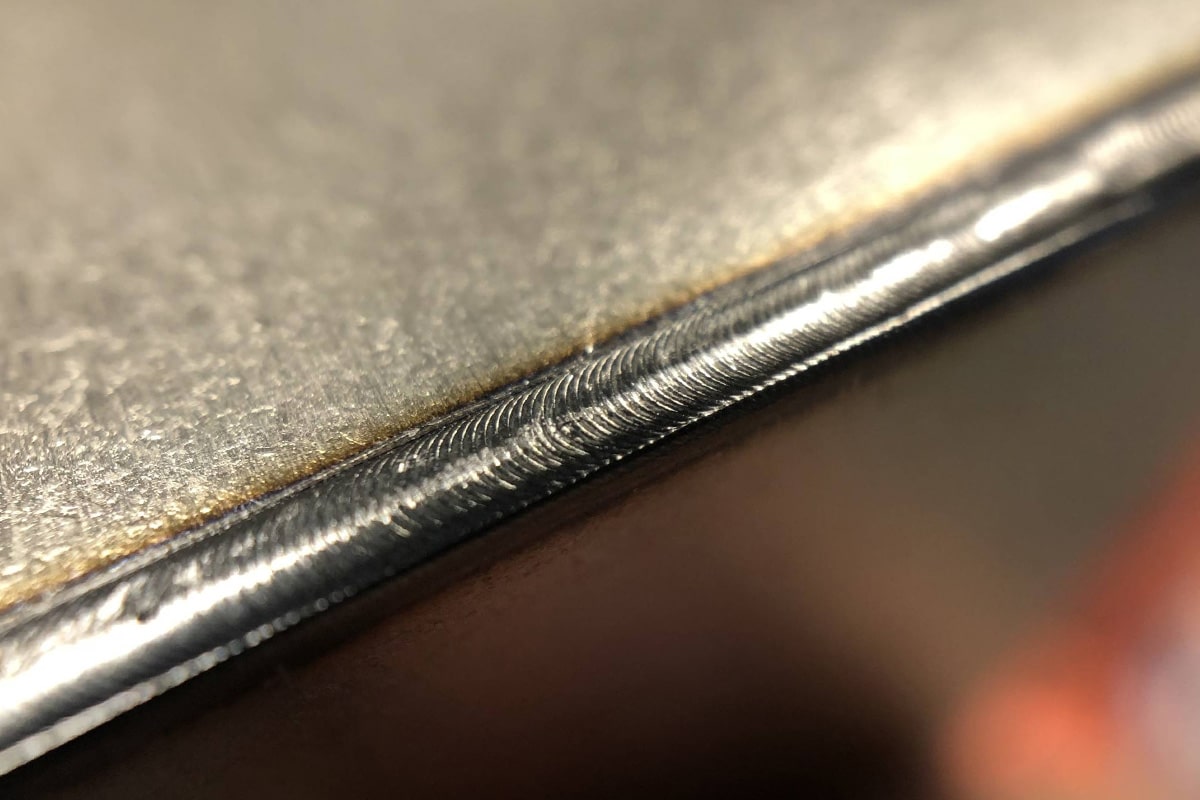
レーザー溶接はどのようにして材料の深部溶融を実現するのでしょうか?
レーザー溶接は、高エネルギー密度、非接触加工、熱影響部が小さいといった利点から、高効率かつ高精度な溶接技術として、自動車、航空宇宙、エレクトロニクスなど多くの業界で広く利用されています。従来の溶接方法と比較して、レーザー溶接は複雑な構造物の接合をより高速に、熱変形が少なく、溶接強度が高いため、特に精密製造や需要の高い工業生産に適しています。
レーザー溶接プロセスにおいて、材料の深溶け込み溶接を実現するには、レーザーパラメータ、材料特性、溶接プロセス制御など、複数の要因を総合的に考慮する必要があります。本稿では、レーザー溶接の基本原理、溶け込み深さに影響を与える主要な要因を深く探究し、深溶け込みの形成メカニズムと最適化戦略を詳細に分析することで、企業がレーザー溶接技術をより適切に活用し、溶接品質と生産効率を向上させるための支援を行います。
目次
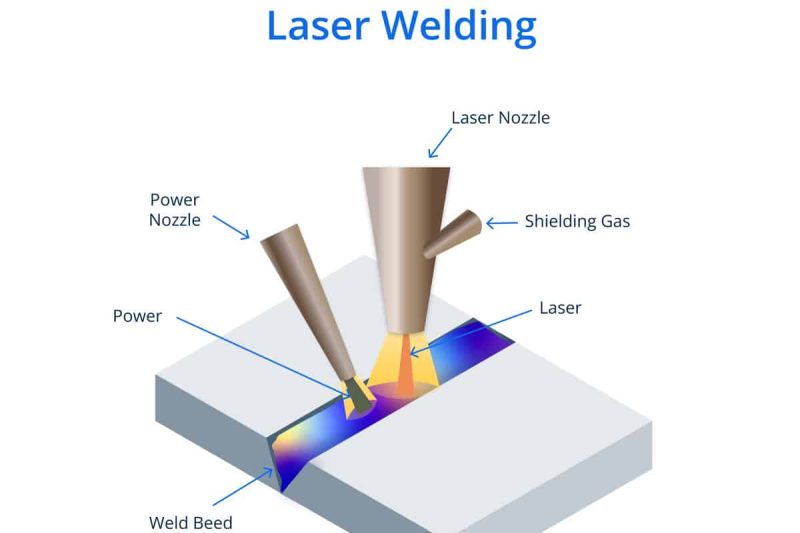
レーザー溶接について学ぶ
定義と根拠
レーザー溶接は、レーザー光を熱源として用い、材料を局所的に融点まで加熱することで溶接を実現するプロセスです。レーザー光を溶接箇所に集束させ、高強度の光エネルギーが材料を急速に加熱・溶融させて溶融池を形成し、冷却後に強固な溶接継手を形成します。レーザー溶接は、高エネルギー密度、高精度、高速溶接といった特徴を有し、精密部品の溶接に適しています。
レーザー溶接プロセスの概要
レーザー溶接プロセスには通常、レーザービームの照射、材料の加熱と溶融、溶融池の形成、冷却と凝固などのステップが含まれます。これらのステップでは、レーザーエネルギーの有効利用と材料の相互作用によって溶接効果、特に深部溶融能力が決まります。
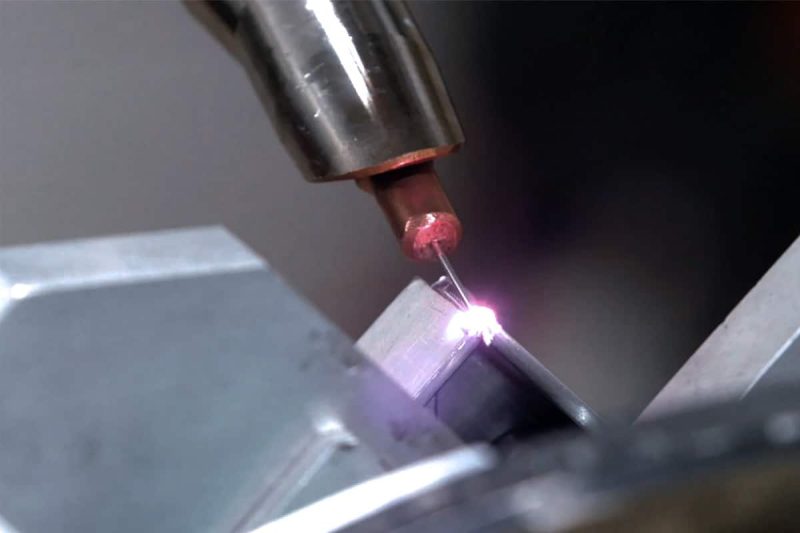
レーザービームと材料の相互作用
レーザー溶接の核心は、レーザービームと材料との相互作用にあり、これが効率的で深い溶け込みの溶接を実現する鍵となります。レーザービームは高エネルギー密度の光源です。材料の表面に照射されると、その一部は材料によって吸収、反射、または透過されます。吸収された光エネルギーは熱エネルギーに変換され、材料は急速に加熱され、溶融または気化状態になり、溶接が完了します。吸収率、熱伝導率、融点など、様々な材料の物理的特性は、レーザー溶接の効率と品質に重要な影響を与えます。したがって、材料によるレーザーエネルギーの吸収と光エネルギーの熱エネルギーへの変換を理解することは、レーザー溶接の効率と品質に不可欠です。 溶接プロセスの最適化.
材料によるレーザーエネルギーの吸収
レーザー溶接における材料の性能は、まずレーザーエネルギーの吸収能力によって左右されます。吸収率は、材料のレーザーエネルギー吸収能力を測定する上で重要なパラメータであり、表面領域におけるレーザーエネルギーの変換効率を決定します。材料によって、異なる波長のレーザーに対する吸収率は異なります。例えば、鉄や銅などの材料は、 ステンレス鋼 ファイバーレーザー発振器(近赤外線帯域)の吸収率が高いため、安定した溶融池を形成しやすい。一方、高反射率の金属、例えば アルミニウム そして 銅 吸収率が低いため、エネルギー損失が大きくなります。吸収率を向上させるには、より高出力のレーザーや特殊な波長(青色レーザーや緑色レーザーなど)が必要です。さらに、材料表面の酸化層、粗さ、温度といった要因もレーザーの吸収効果に影響します。そのため、溶接安定性を向上させるために、通常は溶接前に表面前処理が必要です。
光エネルギーが熱エネルギーに変換される
レーザービームが材料表面に照射されると、吸収された光エネルギーは急速に熱エネルギーに変換され、材料の温度が急上昇します。温度が融点に達すると、材料は溶融状態になり、溶融池を形成します。さらに温度が蒸発温度まで上昇すると、材料の一部が蒸発してピンホール効果を形成し、深溶け込み溶接を実現します。光エネルギーから熱エネルギーへの変換効率は、溶接の深さと品質を直接決定します。エネルギー変換が不十分な場合、溶接が浅くなったり、融合が不良になったり、安定した溶接接続を形成できない可能性があります。過剰なエネルギー入力は、材料の過燃焼、気孔、溶接変形を引き起こす可能性があります。したがって、レーザー出力、ビームモード、溶接速度などのパラメータを適切に制御することで、エネルギー変換プロセスを効果的に最適化し、溶接品質を向上させることができます。
レーザービームと材料との相互作用は、レーザー溶接の核心です。その鍵は、材料によるレーザーエネルギーの吸収と、光エネルギーから熱エネルギーへの効率的な変換にあります。材料ごとの吸収率と熱伝導率は、溶接効果に直接影響します。レーザー波長、出力密度、溶接パラメータを最適化することで、光エネルギーの利用率を向上させ、高品質の深溶け込み溶接を実現できます。これらの相互作用の基本原理を理解することは、溶接プロセスの最適化、溶接部の安定性と強度の向上、そして様々な産業分野の応用要件への対応に役立ちます。
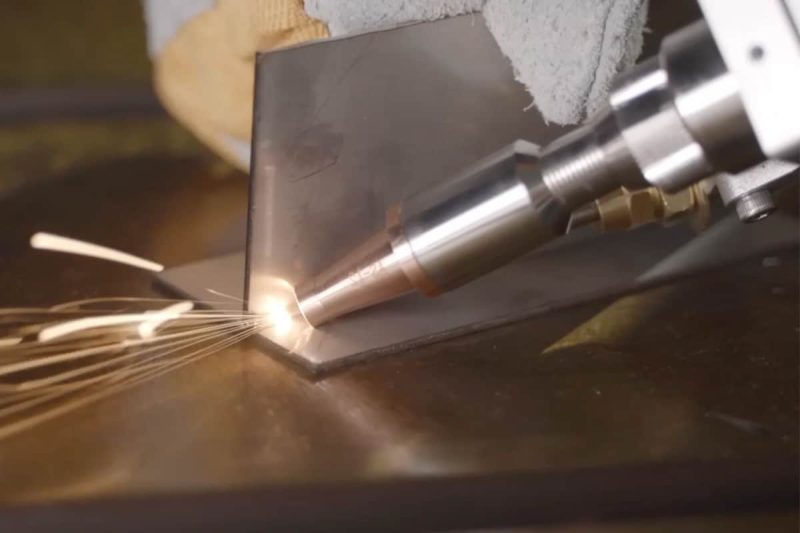
浸透深度に影響を与える主な要因
レーザー溶接の深溶け込み効果は、溶接品質の中核指標の一つです。その溶け込み深さは、溶接部の強度と信頼性に直接影響します。溶接深さは、レーザーパラメータ、材料特性、ワークピースの形状と組み立て、溶接速度など、多くの要因の影響を受けます。これらの要因は相互作用し、溶融池の形成と拡大を決定します。これらのパラメータを適切に最適化することで、溶接深さを効果的に増加させ、溶接部の安定性と一貫性を確保することができます。
レーザーパラメータ
- 出力:レーザー出力は溶接深度に影響を与える主な要因です。レーザー出力が高いほど、より強いエネルギーを供給でき、より深い層で材料を溶融させることができます。一般的に、出力が増加すると溶接深度もそれに応じて増加しますが、出力が高すぎると過度の焼き付きや溶接欠陥が発生する可能性があります。
- ビーム焦点とスポットサイズ:レーザーの焦点サイズはエネルギーの集中度を決定します。焦点が小さいほどエネルギー密度が高くなり、溶接深度を高めることができます。一般的に、焦点位置を正確に調整することで、溶融深度と溶融幅の最適なバランスを実現し、さまざまな溶接ニーズに対応できます。
- パルス幅と周波数:パルスレーザー溶接では、短時間で高いエネルギーを入力することで、材料を素早く加熱し、より深い層まで浸透させることができます。パルスパラメータを適切に調整することで、溶接部の成形品質を最適化し、溶接の安定性を向上させることができます。
材料特性
- 熱伝導率:材料の熱伝導率はレーザーエネルギーの伝播に影響を与えます。熱伝導率の高い材料(銅やアルミニウムなど)は熱を素早く失うため、深部溶融が減少します。熱伝導率の低い材料(ステンレス鋼など)は熱をより効果的に集中させ、より深い浸透深度を実現します。
- 吸収係数:材料のレーザー光の吸収率は、深溶け込みを決定する重要な要素です。吸収係数が高いほどエネルギー利用率が向上し、溶接結果が向上します。反射率の高い材料の場合、通常、特定の波長のレーザーを使用するか、表面を前処理して吸収率を高める必要があります。
ワークピースの形状と組み立て
ワークピースの形状と組み立て方法も、レーザー溶接の深部溶融効果に直接影響を与えます。複雑な幾何学的形状では、レーザービームが目標領域に正確に照射されにくくなり、溶融深度に影響を与える可能性があります。また、ワークピースの組み立てギャップが大きすぎたり、位置決めが不正確だったりすると、溶接ムラが発生し、溶接品質が低下する可能性があります。そのため、レーザービームが溶接領域に安定して作用できるように、溶接前に正確な組み立てと位置決めを行う必要があります。
溶接速度
溶接速度は、材料がレーザーエネルギーを吸収する時間を決定し、溶融池の形成に影響を与えます。通常、溶接速度が遅いほど入熱量が増加し、材料が十分に溶融する時間が得られるため、溶け込み深さが増加します。しかし、溶接速度が遅すぎると、過熱や溶接変形を引き起こす可能性があります。逆に、溶接速度が速いと溶け込み深さが減少し、溶接継手が脆弱になる可能性があります。したがって、実際の作業では、最高の溶接品質を得るために、材料特性と溶接要件に応じて溶接速度を最適化する必要があります。
レーザー溶接の溶け込み深さは多くの要因の影響を受けますが、中でもレーザーパラメータ、材料特性、ワークピースの形状、溶接速度は溶接効果を決定する重要な要素です。レーザー出力、焦点位置、溶接速度などのパラメータを適切に制御し、材料特性と組み合わせることで最適化を図ることで、深溶け込み溶接の安定性と品質を効果的に向上させることができます。これらの要因を総合的に制御することで、溶接プロセスの安定性と信頼性を確保し、さまざまな産業応用シナリオのニーズを満たすことができます。
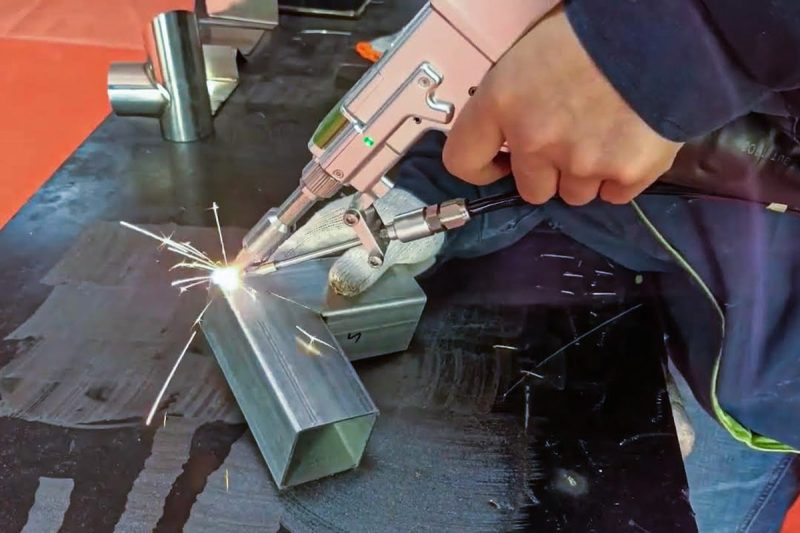
深部浸透制御戦略
レーザー溶接プロセスでは、安定的かつ均一な深い溶け込みを実現することが極めて重要です。溶接深さは、レーザー出力、焦点位置、材料特性、溶接速度など、多くの要因の影響を受けるため、溶接品質と均一性を確保するには、レーザーパラメータの最適化、リアルタイム監視とフィードバックといった戦略が必要です。これらの制御戦略は、溶接強度を向上させるだけでなく、溶接欠陥を低減し、生産効率を向上させることができます。
レーザーパラメータの最適化
深溶け込み溶接には、レーザーパラメータの正確な制御が不可欠です。最適化される主なパラメータは以下のとおりです。
レーザー出力:
- 電力が高ければエネルギー入力も大きくなり、材料がより深く溶けて溶接の深さも増します。
- 電力が高すぎると、材料が過剰に溶解または蒸発し、気孔や亀裂などの溶接欠陥が発生する可能性があります。
- 電力が低すぎると溶け込みが不十分になり、溶接の強度に影響する可能性があります。
フォーカスのサイズと位置:
- 焦点径が小さいとエネルギー密度が増加し、レーザーがより効率的に材料に浸透し、浸透の深さが増します。
- 焦点位置を最適化すると、エネルギーが溶接領域に効果的に集中され、過剰なエネルギー分散や十分な深さのない表面溶融が回避されます。
パルス持続時間と周波数(パルスレーザー溶接の場合):
- 短いパルス時間と高周波を組み合わせることで、十分な浸透を確保しながら熱影響部を減らすことができます。
- パルス時間が長いほど、エネルギーの浸透が深くなりますが、熱影響部が拡大し、溶接精度に影響する可能性があります。
実験とコンピューターシミュレーションを通じて、さまざまな材料と溶接要件に最適なレーザーパラメータの組み合わせを見つけることができ、溶接の深さと品質が最高レベルに達することが保証されます。
リアルタイム監視とフィードバック
溶接プロセス中の溶込みの均一性を維持するためには、溶接パラメータを調整するためのリアルタイム監視およびフィードバックシステムが必要です。これらのシステムは通常、光学センサー、サーマルイメージング装置、レーザー出力モニターなどで構成されており、溶接プロセス中の材料の反応を検知し、そのデータに基づいて溶接パラメータを自動的に調整します。
監視する主なパラメータ:
- 溶融プールの温度: 赤外線カメラまたはスペクトル分析により、溶融プールの温度をリアルタイムで測定し、入熱が適切な範囲内に維持されていることを確認できます。
- 溶融池の形態:溶融池の形状と動的変化を高速カメラで監視し、均一で安定した溶接を保証します。
- レーザー出力変動:装置の不安定さによる溶接品質の変動を防ぐために、レーザー出力を自動で検知・調整します。
フィードバックメカニズム:
- インテリジェント制御システムは、監視データに基づいてレーザーパラメータを自動調整し、発生する可能性のある偏差を補正します。例えば、センサーが貫通不足を検知した場合、システムは自動的にレーザー出力を上げたり、焦点位置を調整したりします。
- 手動調整: 高精度のアプリケーション シナリオでは、オペレーターは監視データに基づいて溶接パラメータを手動で微調整し、溶接品質が要件を満たしていることを確認できます。
レーザー溶接の深溶融効果を確保するには、レーザーパラメータの最適化とリアルタイム監視・フィードバック戦略が必要です。レーザー出力、焦点サイズ、パルス幅などのパラメータを適切に調整することで、溶接深度を効果的に向上させることができます。同時に、高度な監視システムの支援により、溶接プロセス中に重要なパラメータをリアルタイムで検出・調整し、溶融深度の安定性と一貫性を確保できます。これらの制御戦略は、溶接品質を向上させるだけでなく、溶接欠陥の低減と生産効率の向上にもつながり、産業製造におけるレーザー溶接技術の信頼性と効率性を高めます。
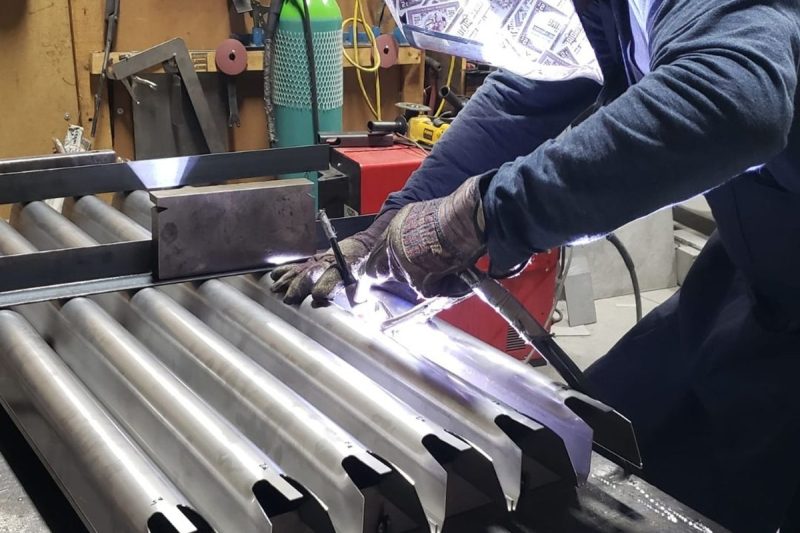
アプリケーションと業界
レーザー溶接技術は、高精度、高効率、そして複雑な材料への適応性から、多くの産業で広く利用されており、特に溶接品質と深度に対する要求が極めて高い分野で顕著です。レーザー溶接の利点は、従来の溶接技術では対応できなかったニーズを解決する理想的な選択肢となります。以下は、現代産業におけるレーザー溶接技術の重要性と幅広い応用を示す代表的な産業分野とその応用分野です。
自動車産業
レーザー溶接は自動車製造において広く利用されており、特に高張力鋼やアルミニウム合金製の車体構造部品の溶接に用いられています。レーザー溶接は深い溶接溶け込みを実現し、車体の強度を確保し、変形を低減します。また、効率的なレーザー溶接は自動化生産ラインにも適しており、生産効率の向上に貢献します。
- 高強度鋼:レーザー溶接は高強度鋼に深溶接を施すことで車体の強度と安全性を確保しながら、使用する材料の量を減らし、軽量設計に貢献します。
- アルミニウム合金 溶接:アルミニウム合金は、現代の自動車製造において広く使用されている軽量素材です。レーザー溶接技術は、精密なエネルギー制御能力により、アルミニウム合金の効率的な深溶接を実現し、接合部の強度と安定性を確保します。
- 自動化生産ライン:レーザー溶接は高速かつ高精度であるため、自動化生産ラインに適しており、生産効率が向上し、手動介入が削減され、大規模生産のニーズを満たします。
航空宇宙
航空宇宙産業では、レーザー溶接は軽量合金や複合材料の精密溶接に用いられています。深溶接能力と高精度という特徴から、レーザー溶接は合金材料や構造部品の理想的な溶接方法となり、過酷な条件下でも部品の信頼性を確保しています。
- 合金材料:航空宇宙用途では、構造部品の製造に合金材料(チタン合金、アルミニウム合金など)が広く使用されています。レーザー溶接は、より深い溶融池とより強力な溶接強度を提供し、過酷な作業条件下でも部品の信頼性を確保します。
- 複合材料の溶接:複合材料は軽量で高強度であることから、航空宇宙分野で広く使用されています。レーザー溶接は、これらの材料を精密に溶接し、構造の完全性を確保します。
- 高精度・高品質:航空宇宙部品の溶接には極めて高い精度と品質が求められます。レーザー溶接は、従来の溶接方法で発生する可能性のある熱影響部や溶接変形を効果的に回避し、溶接部品の強度と耐久性を確保します。
エレクトロニクス産業
電子機器の小型部品は、部品の高い信頼性と安定性を確保するために、レーザー溶接によって精密に溶接されることがよくあります。レーザー溶接は、他の部品への損傷を防ぎながら高精度な深溶接を実現できるため、マイクロエレクトロニクス部品の製造に適しています。
- マイクロエレクトロニクス部品: レーザー溶接は、センサー、バッテリー、集積回路などのマイクロエレクトロニクス部品の溶接によく使用されます。これらの部品には溶接品質に対する要件が非常に高く、レーザー溶接は正確な熱入力を提供して、熱による損傷や部品の変形を回避できます。
- 精密溶接: エレクトロニクス業界では、レーザー溶接技術により、周囲の敏感な部品を損傷することなく、非常に精密な小型部品の接続を完了できます。
- 製品の信頼性を向上: レーザー溶接は、強力で安定した溶接接合部を提供し、長期使用時の電子製品の信頼性と耐久性を保証します。
レーザー溶接技術は、高精度、高効率、複雑な材料への適応性といった特長から、自動車、航空宇宙、エレクトロニクス、医療、精密工具など、多くの産業で広く利用されています。科学技術の進歩に伴い、レーザー溶接はより多くの分野で重要な役割を果たし、現代産業の高品質・高精度溶接のニーズを満たし、様々な産業における製造技術の発展を促進するでしょう。
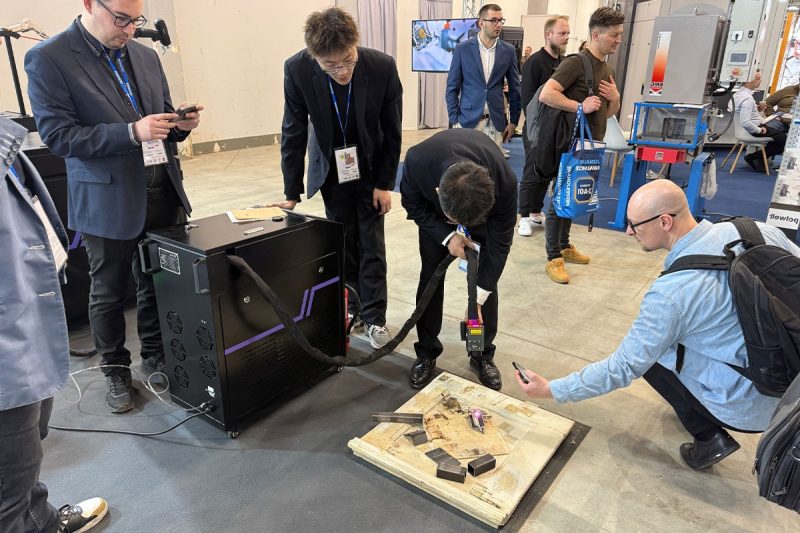
要約する
レーザー溶接による深溶け込みの実現プロセスは複雑かつ精密であり、レーザーと材料の相互作用、複数の主要因子の最適化と制御、そして深溶け込みの複数のメカニズムが絡み合っています。レーザーパラメータの精密制御とリアルタイムモニタリングにより、材料の品質を損なうことなく深溶け込みを実現できます。この技術は多くの産業で広く利用されており、特に自動車、航空宇宙、電子機器といった高精度分野において顕著です。技術の継続的な発展に伴い、レーザー溶接はより多くの産業で独自の優位性を発揮していくでしょう。
上記の内容では、レーザー溶接の原理とプロセスを深く分析し、深溶融を実現する方法と重要な制御戦略に焦点を当てました。業界のリーダーとして、 AccTek レーザー 効率的なレーザー溶接ソリューションを提供することに尽力しています。 レーザー溶接機 様々な業界の高精度・高品質な溶接ニーズにお応えします。ご質問やご要望がございましたら、レーザー溶接に関する専門的なアドバイスやサービスをご提供いたしますので、お気軽にお問い合わせください。
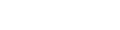
連絡先
- [email protected]
- [email protected]
- +86-19963414011
- No. 3 ゾーン A、Lunzhen 工業地帯、玉城市、山東省。
レーザー ソリューションを入手する