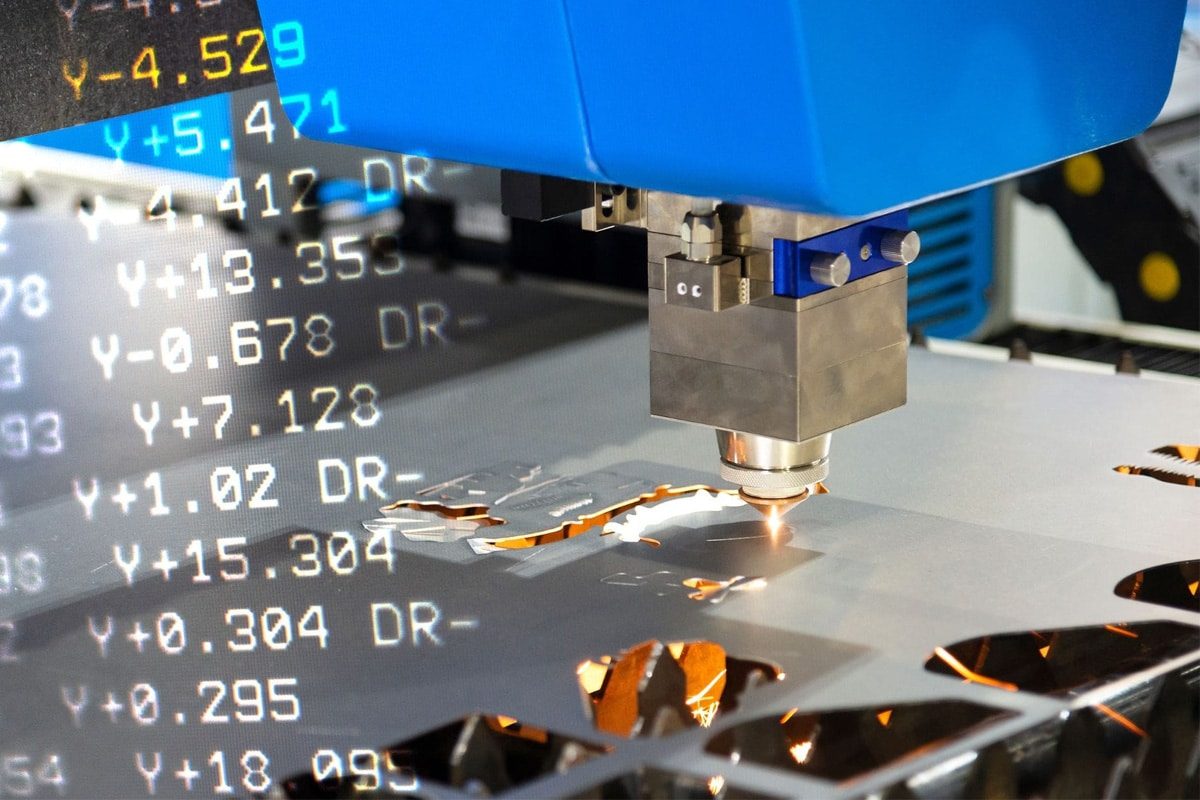
複雑なデザインに対応するファイバーレーザー切断機の機能と限界
精密製造の高度化に伴い、ファイバーレーザー切断機は高効率かつ高精度な加工を実現する代表的な装置となっています。特に、複雑なパターンや高精度が求められる設計課題において、ファイバーレーザー切断技術はその優れた性能から、多くの産業分野で広く利用されています。本稿では、複雑な設計に対応するファイバーレーザー切断機のコア機能と実用上の限界を詳細に検討し、メーカーがファイバーレーザー切断機の有効性を最大限に発揮するための最適化戦略を紹介します。
目次
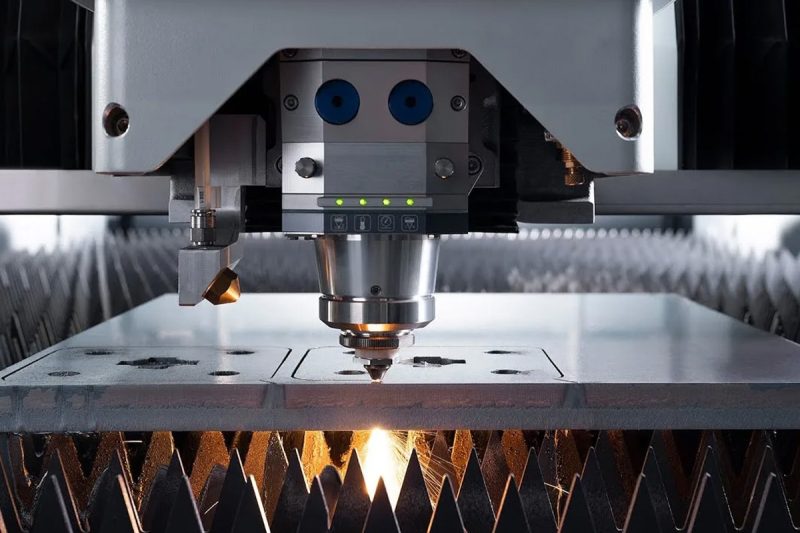
ファイバーレーザー切断機について学ぶ
あ ファイバーレーザー切断機 高エネルギーレーザービームを集束させ、材料表面を精密に溶融することで自動切断を実現するハイエンド設備です。ファイバーレーザージェネレータをレーザー光源として採用し、効率的な光学系と高度なCNCプログラミングと連携することで、ステンレス鋼、炭素鋼、アルミニウム合金、銅板など、様々な金属材料の高速・高品質な切断加工を実現します。精密製造、板金加工、自動車部品、航空構造部品などの業界で広く利用されており、特に切断精度と複雑性に対する要求が高い製品設計に適しています。
コアコンポーネント
レーザー発生器はファイバーレーザー切断機全体の「心臓部」であり、電気エネルギーを高密度のレーザーエネルギーに変換する役割を主に担っています。従来のCO2レーザーやYAGレーザー発生器と比較して、ファイバーレーザー発生器は高い光電変換効率(最大40%以上)、低消費電力、小型、長寿命といった利点を備えています。出力レーザービームは非常に高い輝度と安定性を備えており、高速加工においても継続的で高品質な切断出力を確保できます。
光学系は、主にレーザー光をレーザー発生装置から切断ヘッドへ伝送し、集光レンズでレーザー光を正確に集光する役割を担っています。このプロセスでは、複数の高反射レンズとレンズ群を用いることで、レーザーエネルギーの集中とスポット径の制御性を確保しています。同時に、一部のハイエンド機器には自動集光レンズや防汚レンズも搭載されており、様々な厚さの材料の自動調整ニーズに対応し、全体的な切断効率と切断品質を向上させています。
CNCシステムは精密加工の「頭脳」です。CAD/CAM設計図面を受信して解析することで、複雑な図形を精密な切削パスへと自動的に変換します。最新のファイバーレーザー切断装置を搭載したCNCシステムは、多軸リンク、動的出力調整、リアルタイム速度フィードバックなどの機能をサポートし、複数の面や角度への動的追従切削を実現します。一部のシステムでは、加工パス最適化アルゴリズム、自動エッジ検出、リモートモニタリングなどの機能も統合されており、加工効率とヒューマンマシンコラボレーションエクスペリエンスを大幅に向上させます。
一般的に、ファイバーレーザー切断機が現代産業において重要な地位を占めている理由は、高性能レーザー発生装置、高精度光伝送システム、そしてインテリジェントCNC技術の緊密な連携にあります。これら3つの組み合わせにより、従来の直線切断や円形切断だけでなく、複雑な構造や多数のディテールを持つ金属部品の切断にも対応できます。高効率と高精度を追求する現代の製造企業にとって、ファイバーレーザー切断機は競争力を高めるための重要なツールの一つです。
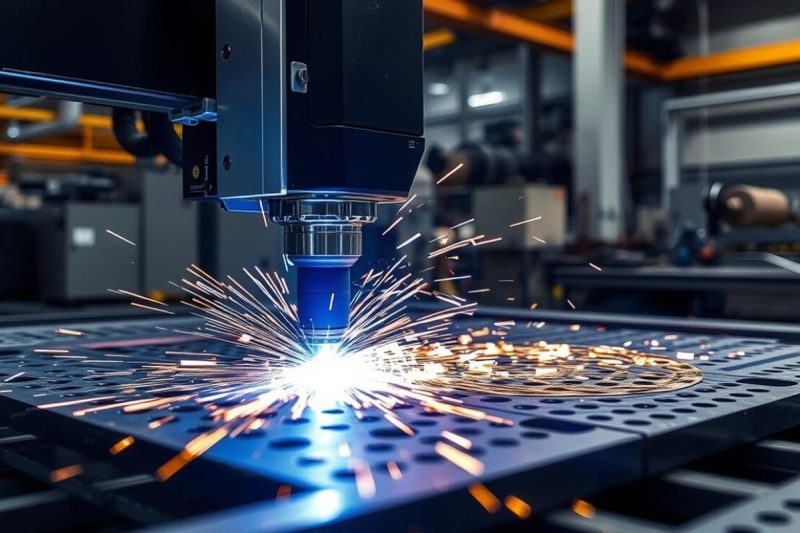
ファイバーレーザー切断機の機能
現代の製造業において、高精度、高効率、多様化といった加工への需要が高まる中、ファイバーレーザー切断機は、安定したレーザー出力、精密な制御システム、そして幅広い材料適応性を備え、精密加工分野において徐々に重要な設備となっています。複雑な構造を持つカスタマイズされたワークピースから、多数の標準化された部品まで、ファイバーレーザー切断技術は迅速かつ高品質なソリューションを実現し、様々な産業のお客様に極めて高い加工柔軟性と効率性の利点を提供します。
主な特徴
ファイバーレーザービームの焦点は極めて小さく、先進的な集光光学部品とCNCシステムを組み合わせることで、ミクロン単位の精密制御を実現しています。スリット幅が狭く、熱影響部が狭いため、加工エッジはきれいに仕上がり、寸法公差制御も優れています。特に電子、医療、金型などの業界において、極めて高い精度が求められる部品の製造に適しており、高い適応性を示しています。
高安定性のレーザービーム制御とインテリジェントなCNCパス最適化により、ファイバーレーザー切断機は様々な複雑な構造の設計要件を容易に満たすことができます。例えば、曲線が交差する部品、急角度の頻繁な変化、密集したパターンなど、CAD図面に基づいて高い忠実度で再現できるため、設計から生産までの変換時間を大幅に短縮できます。
複雑なエッジや不規則な形状を持つ金属ワークピースでも、ファイバーレーザー切断技術は滑らかな切断面を確保し、バリ、スラグ、熱変形を回避します。厚みが不均一な部品や緻密なディテールを持つ部品でも、明確な境界と良好な表面処理効果を維持し、後工程の研磨や二次加工にかかる時間コストを効果的に削減します。
ファイバーレーザー切断機は、従来の切断方法と比較して、特に薄板材料の加工において切断速度が速く、フライングカットモードを実現し、加工効率を大幅に向上させることができます。同時に、自動ローディング・アンローディングシステムや生産ライン統合ソリューションと組み合わせることで、長期無人連続運転を実現し、手動介入を減らし、生産ラインの自動化レベルを向上させることができます。
ファイバーレーザー切断はデジタル制御を採用しています。図面の調整やバージョンアップは、ソフトウェアで切断プログラムを変更するだけで完了します。迅速な校正、小ロットカスタマイズ、複数仕様の注文処理に最適です。製品のアップデートが頻繁に行われる業界では、この柔軟な応答速度が特に重要です。
まとめると、ファイバーレーザー切断機は、高精度、高効率、多材料対応、そして複雑な設計への対応力の高さにより、現代の製造業においてかけがえのない役割を果たしています。製品の品質と生産効率を大幅に向上させるだけでなく、企業が柔軟な製造と多様なカスタマイズを実現するための強力なサポートを提供します。特に、微細加工と迅速な設計反復を必要とする産業用途において、ファイバーレーザー切断技術は徐々にコア設備の第一選択肢になりつつあります。
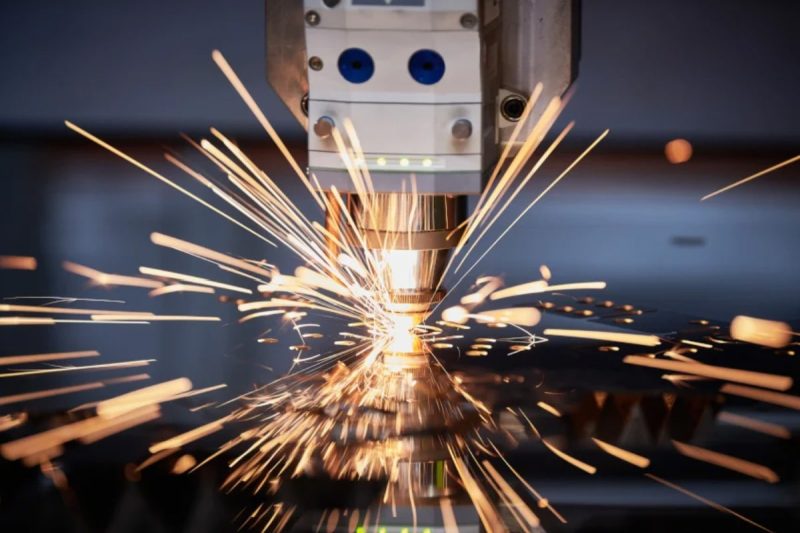
複雑な設計におけるファイバーレーザー切断機の応用分野
製造業における個別対応、複雑な構造、高品質な加工への需要が高まる中、優れた柔軟性と高精度を誇るファイバーレーザー切断技術は、様々な業界で広く導入されています。特に、部品の寸法精度、エッジ品質、細部の複雑さに対する要求が極めて高い産業分野において、ファイバーレーザー切断機はエンジニアリングの実現と製品イノベーションのための重要な基本ツールとなっています。
典型的な産業用途
自動車製造において、ファイバーレーザー切断技術は、ボディパネル、シャーシ構造、排気系部品、内装金属部品の加工に広く利用されています。これらの部品は、曲面形状、補強リブ、取り付け穴などの複雑な構造を持つことが多く、従来の機械加工では精度と効率のバランスを取ることが困難でした。レーザー切断は、成形を一工程で完了できるため、後工程の工数を削減し、構造強度と組立精度を確保しながら、車両全体の組立品質と製造効率を向上させます。
航空宇宙産業では、特にエンジンブラケット、キャビンフレーム、アビオニクスアセンブリなどの金属部品において、軽量性、強度分布、加工精度に対する要求が非常に高くなっています。ファイバーレーザー切断機は、非接触で高精度な加工を実現し、部品のエッジに亀裂や熱変形が生じないようにし、構造強度を維持しながら最小限の重量設計を実現します。チタン合金や高強度アルミニウム合金などの特殊材料に対する優れた加工性能により、航空宇宙産業における適用範囲が大幅に拡大しています。
現代建築は、構造と芸術の融合をますます追求しています。ファイバーレーザー切断技術は、複雑な模様、レリーフスタイル、中空構造といった設計要件を効率的に実現します。金属製カーテンウォール、彫刻された間仕切り、階段の手すり、ステンレス製のアート部品など、レーザー切断は、きれいな切断面、鮮明なグラフィック、そして高い量産安定性を保証します。CAD図面をインポートすることで、設計者は創造性を素早く物理的なオブジェクトに変換し、建築美と構造の実用性を融合させることができます。
電気・電子産業において、小型化と高精度化は、特に民生用電子機器、通信機器、産業用制御機器に使用される筐体構造、コネクタ、シールドシートなどの金属部品における中核的な設計要件です。ファイバーレーザー切断機は、非常に小さなサイズ範囲において高い再現性と切断精度を維持できるため、従来のスタンピング工程でよく見られるバリや変形の問題を効果的に回避し、金型製造コストを削減し、製品開発の柔軟性を向上させます。
医療機器は、加工時の清浄度、微細精度、そして材料エッジ加工に関して極めて厳格な基準を要求されます。ファイバーレーザー切断機は、非接触、高エネルギー密度、そして熱影響部の制御可能性といった特長を活かし、外科用器具、整形外科用インプラント、歯科用部品などの製造工程で広く利用されています。切断面は滑らかで汚染のないだけでなく、部品の寸法誤差や材料疲労を効果的に抑制できるため、医療業界の厳しい品質の一貫性と製品の信頼性に対する要件を満たしています。
ファイバーレーザー切断機は、精密で効率的かつ柔軟な加工方法により、多くの業界における複雑な構造設計にソリューションを提供しています。自動車、航空、建設、エレクトロニクス、医療といったハイエンド製造分野において、製品の品質と生産効率を向上させるだけでなく、新しい構造設計の実現を強力にサポートしています。技術の継続的な進歩に伴い、ファイバーレーザー切断機の応用範囲は拡大し続けており、今後、より精密な製造分野で重要な役割を果たすことになるでしょう。
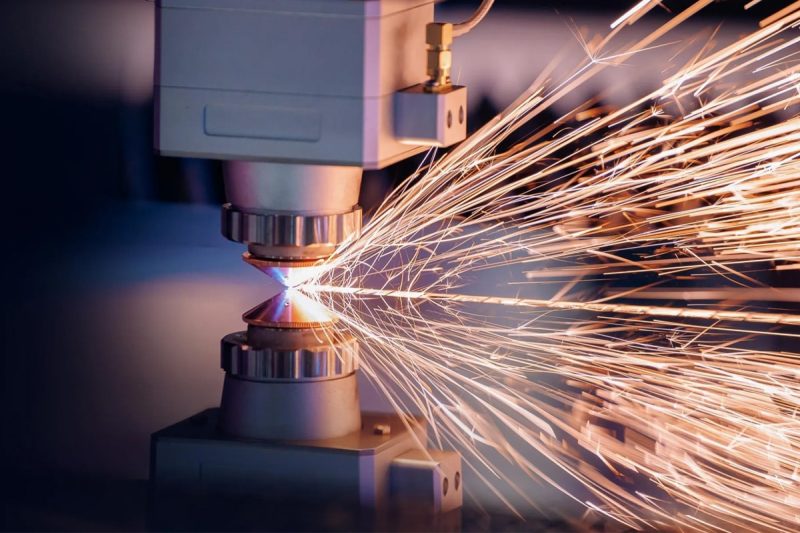
精度と詳細パフォーマンスに影響を与える主な要因
ファイバーレーザー切断機自体は非常に高い加工能力を備えていますが、実際の操作工程においては、完成品の品質は様々な技術パラメータや動作変数の影響を受けます。特に複雑な構造や微細なパターンの切断作業においては、各リンク制御の精度と安定性が、最終製品のディテールの復元度と全体的な一貫性を直接左右します。したがって、これらの重要な要素を深く理解し、操作中に継続的に最適化を行うことが、高品質な出力を保証するための核心となります。
主な影響要因
ビーム品質は、レーザー出力の安定性と集光性能を測る上で重要な指標です。高品質ビームは発散角が小さく、エネルギー集中度が高いため、レーザーを極めて微細な光点に集光することができ、より狭いスリット幅とより精密な軌道制御を実現します。微細パターンや極小部品の切断において、ビームモードの純度は、エッジラインのシャープさと表面仕上げに直接影響を及ぼします。
切断速度の設定は、材料の厚さ、出力密度、ガスアシストなどのパラメータのバランスをとる必要があります。切断速度が速すぎると、レーザーが材料を完全に溶融できず、スラグや未切断現象が発生する可能性があります。一方、速度が遅すぎると、過剰な熱蓄積によりエッジの溶融や拡散、精度の低下を引き起こす可能性があります。異なる材料や厚さのワークピースの場合、効率と品質の両方を確保するために、パラメータデータベースまたは試し切りによって最適な速度範囲を決定する必要があります。
材料によって熱伝導率、反射率、融点が異なり、レーザーの吸収度合いも異なります。例えば、ステンレス鋼はレーザーの吸収率が高く、高速切断に適しています。一方、銅やアルミニウムなどの高反射材料は波長に対する反射率が高く、専用のレーザー発生器と補助光路システムを使用する必要があります。材料が厚くなるほど、エネルギーを透過させ、焦点を維持することが難しくなります。特に厚板切断では、焦点距離の動的調整とガス流場の安定性に細心の注意を払う必要があります。
熱影響部とは、レーザー作用領域の周囲において熱拡散によって微細構造変化が生じる領域を指します。熱影響部が大きすぎると、材料の局所的な硬化、脆化、変形を引き起こし、部品の後続加工や組立性能に影響を及ぼす可能性があります。短パルスレーザーの選択や高周波穿刺モードの使用により、熱拡散範囲を効果的に低減し、加工効率を向上させることで、トリミング領域の材料特性が破壊されることを防ぎます。
ノズルは補助ガス出力経路です。その構造とサイズはガス噴射速度と方向に直接影響し、スラグ排出と切断安定性に影響を与えます。高品質のノズル設計は、安定した保護ガス流を形成し、切断継ぎ目の清浄度を向上させます。同時に、焦点位置の正確な設定は、レーザーエネルギーの利用率を最大限に高める鍵となります。特に特殊形状のワークピースや多層材料の切断では、切断パス全体にわたってエネルギーの一貫性を確保するために、焦点を動的に調整する必要があります。
レーザー切断工程は、CNCシステムの安定性とCAD/CAMプログラムの精度に大きく依存します。最適化された切断パスは、空ストロークを短縮し、過熱箇所の繰り返しを回避できるだけでなく、図形の複雑さに応じて速度と出力を自動調整し、インテリジェントな加工を実現します。プログラムパラメータの設定が不適切だと、切断軌跡のずれ、エッジ焼け、エラー増幅などの問題が発生する可能性があります。そのため、経験豊富なソフトウェアエンジニアと高度な制御プラットフォームは、高品質な製品を安定して生産するための保証となります。
ファイバーレーザー切断の精度と詳細な性能には、機器のハードウェア、動作パラメータ、材料特性、ソフトウェアシステムなど、多岐にわたる要因が影響します。継続的な経験の蓄積、設定の最適化、そして実用化における技術革新を組み合わせることで、複雑な構造物加工におけるレーザー切断機の潜在能力を最大限に発揮し、図面から完成品までの正確な復元を実現し、ハイエンド製造とパーソナライズされた設計に対して安定した信頼性の高い技術サポートを提供することができます。
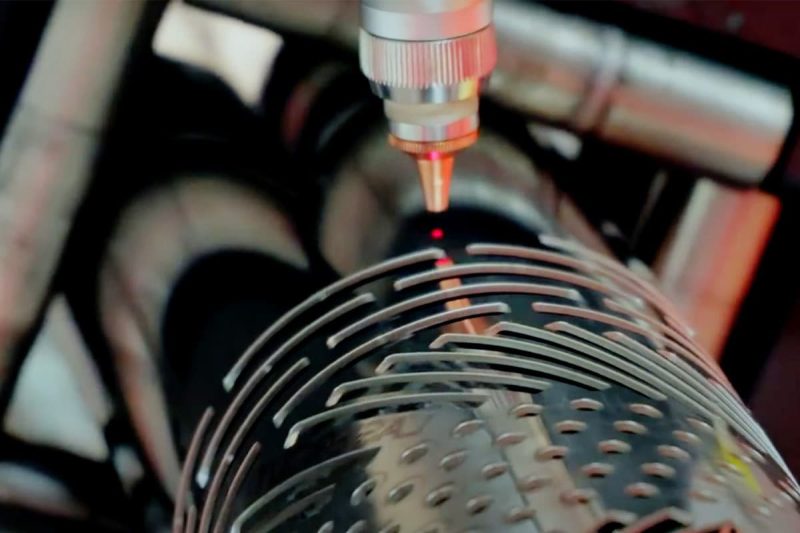
制限を緩和するための戦略
複雑な構造や精密部品のファイバーレーザー切断の実際の応用においては、装置の性能は大幅に向上しているものの、パラメータ設定、材料特性、プログラミングパス、操作経験など、依然として多くの要因によって制限されています。これらの制限を科学的に解決できない場合、切断品質の変動、生産効率の低下、さらには加工不良が発生する可能性が高くなります。そのため、企業は技術の最適化、プロセス管理、人材育成など、複数のレベルで同時に取り組み、プロセス全体のレベルと安定性を体系的に向上させることができます。
効果的な戦略
体系的なパラメータテストと記録メカニズムを通じて、様々な材質、厚さ、グラフィックタイプに対応したパラメータデータベースを段階的に構築することは、切断品質の一貫性を確保するための重要な手段です。パラメータの最適化には、主にレーザー出力、パルス周波数、切断速度、ジェット圧力、焦点位置などのコア変数が含まれます。特に微細な曲線や小さな円形の穴を扱う場合は、試し切り+データ収集とモニタリングシステムによる微調整を組み合わせることをお勧めします。パラメータを微調整することで、エッジ品質と切断継ぎ目の平坦性が大幅に向上することがよくあります。
材料自体の純度、表面の清浄度、平坦度は、レーザー吸収効率と熱分布に直接影響します。加工前には、一般的なブランドの高品質な金属板を使用し、表面脱脂、錆除去、または皮膜保護処理を施すことで、切断欠陥の発生率を大幅に低減することが望ましいです。さらに、異なるバッチの材料に対して予備的なスペクトル検出や物理的特性試験を実施することで、差別化されたパラメータモデルを確立し、より精密な切断制御を実現することも可能です。
高度な設計・プログラミングツールは、初期設計の効率を向上させるだけでなく、加工パス、切断順序、熱分布を効果的に制御できます。特に複雑なグラフィックや高密度パターンをレイアウトする場合、パス最適化、ホットゾーン回避、加工シミュレーション、残留材料識別機能を備えたソフトウェアモジュールにより、無駄を大幅に削減し、歩留まりを向上させることができます。同時に、ソフトウェアインターフェースを使用して、レーザー装置とのパラメータ連携や加工データのフィードバックを実現し、プロセス全体のデジタル閉ループ管理を促進します。
設備とソフトウェアがいかに先進的であっても、熟練したオペレーターと安定したプロセスフローがなければ、長期にわたって一貫した処理結果を確保することは困難です。充実した標準操作手順(SOP)とプロセスマニュアルを確立し、オペレーターへの定期的なトレーニングを実施することが、設備の能力と歩留まりを維持するための核心的な保証となります。優秀なオペレーターは、現場で異常状態を迅速に特定できるだけでなく、実際の操作において経験的な判断を行い、処理パラメータを微調整・最適化することができます。
ますます複雑化する切断要件と精度への課題に直面し、ハードウェア自体の性能のみに頼るだけでは、安定的かつ効率的な生産目標を達成することはもはや不可能です。科学的なパラメータデバッグ手法、高品質な材料管理、効率的なソフトウェアサポート、標準化されたオペレーティングシステム、そしてインテリジェントな補助機器を総合的に活用することで、企業はファイバーレーザー切断機の複雑な設計処理における技術的制約を、ソースから実装まで徹底的に緩和し、より高品質な製品提供と競争力の高い生産能力を実現できます。
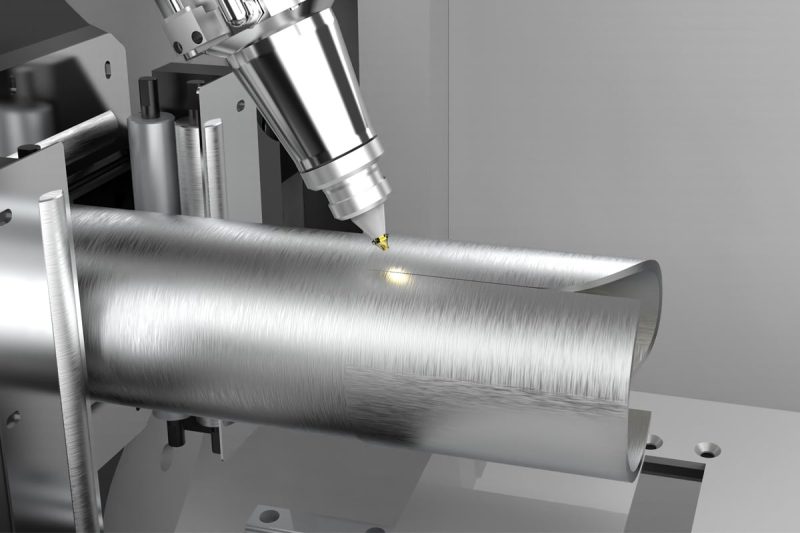
要約する
ハイエンド化、インテリジェント化、カスタマイズ化が加速する現代の製造業において、従来の加工方法では、効率性、精度、柔軟性といった面で絶えず変化する市場ニーズを満たすことができなくなりました。優れたビーム品質、極めて高い位置決め精度、そして様々な複雑なグラフィックへの優れた適応性を備えたファイバーレーザー切断機は、現代の産業システムに欠かせない基幹設備となっています。特に、複雑な構造設計と高精度が求められる加工タスクにおいて、従来のプロセスでは到底及ばない技術的優位性を発揮します。
実際のアプリケーションでは、熱衝撃制御、材料適合性、エッジ品質といった課題に直面する可能性がありますが、高度なパラメータ設定技術、インテリジェントなパス最適化ソフトウェア、精密加工制御システム、そして専門オペレーターの連携によって、これらの問題を効果的に軽減、あるいは完全に解決することができます。ファイバーレーザー切断の技術的限界は絶えず打ち破られており、ハイエンド製造におけるその戦略的地位はますます高まっていくでしょう。
AccTek Laserは、レーザー加工装置分野における深い研究開発と製造の蓄積を持つ専門ブランドとして、「技術主導の価値」という開発理念を常に堅持し、安定性、効率性、そしてインテリジェント性を兼ね備えたファイバーレーザー切断ソリューションの創出に注力してきました。当社の装置は、優れた加工性能と優れた動作安定性を備えているだけでなく、自動車製造、航空宇宙、精密電子機器、建築装飾、医療機器など、多くの業界で広く採用されており、世界中のユーザーから高い評価と高い評価を得ています。
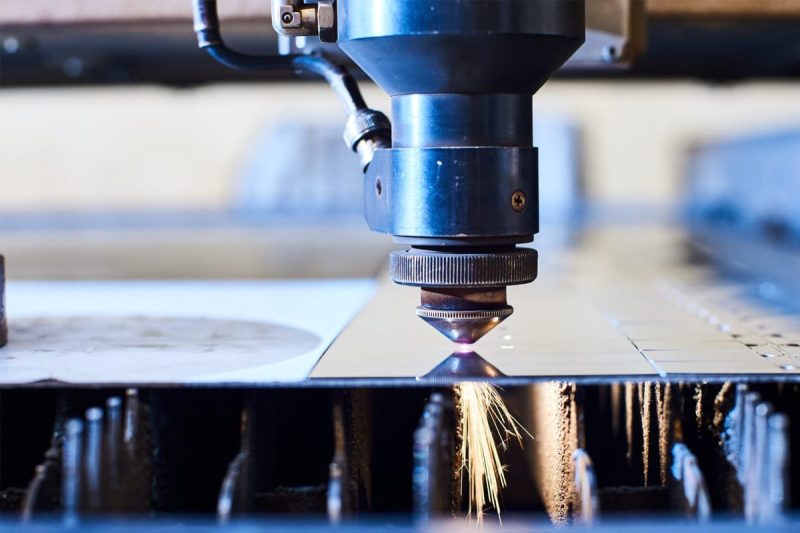
レーザーソリューションを入手
私たちは、あらゆる業界、あらゆるお客様が独自のアプリケーションニーズを持っていることを理解しています。そのため、AccTek Laserは、機器の選定、プロセスのカスタマイズ、設置、試運転からアフターサービスまで、ワンストップサポートを提供し、「お客様の問題を解決し、生産に価値を創造する」というサービスコミットメントを真に実現しています。
複雑な構造設計や難しい加工にも対応できる高性能ファイバーレーザー切断機をお探しの方は、お気軽にお問い合わせください。 お問い合わせ弊社の専門技術チーム、豊富な業界経験、柔軟なカスタマイズ能力により、お客様の実際の生産ニーズに最適なソリューションを提供し、激しい市場競争の中で貴社が際立ち、高品質な発展の新たな段階に進むお手伝いをいたします。
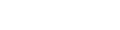
連絡先
- [email protected]
- [email protected]
- +86-19963414011
- No. 3 ゾーン A、Lunzhen 工業地帯、玉城市、山東省。
レーザー ソリューションを入手する