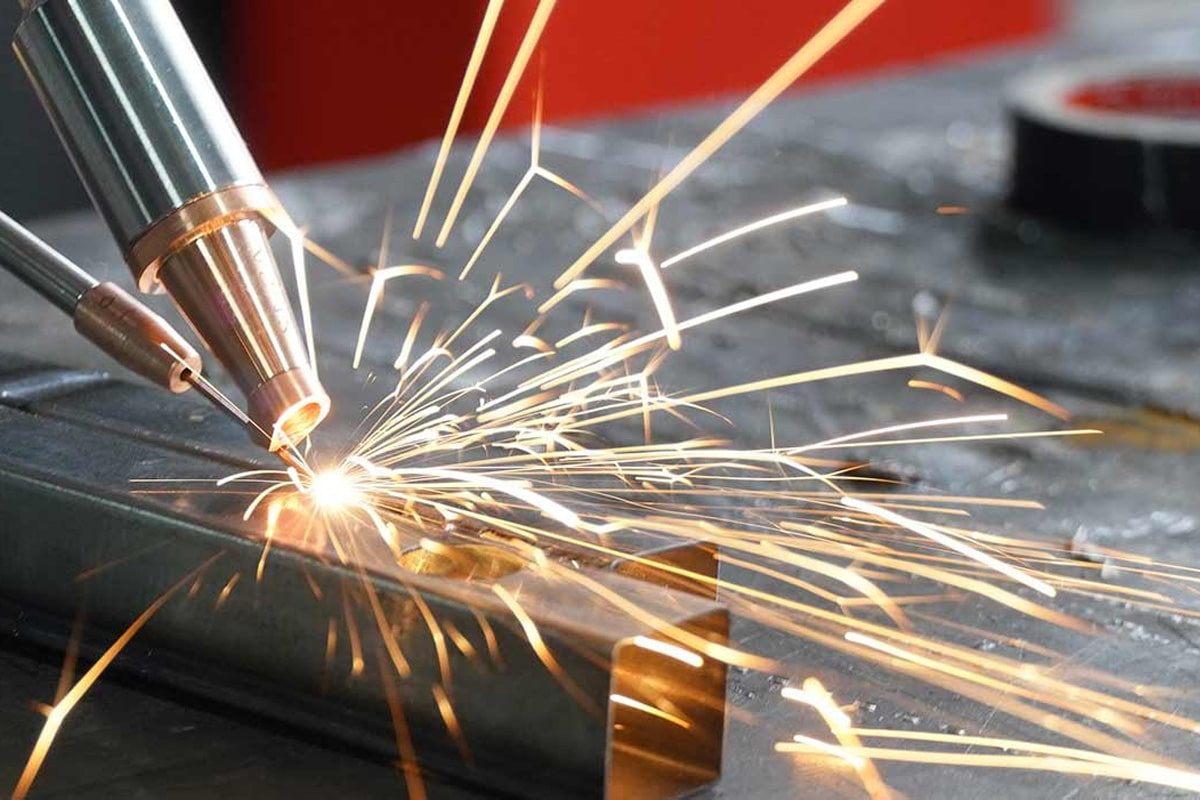
Effect of focal length on laser welding results
In the field of laser welding, focal length is one of the key optical parameters that determine welding quality. Whether in thin plate welding or deep penetration welding, the reasonable selection and adjustment of laser focal length will have a significant impact on the spot size, energy density, penetration depth and final weld appearance. This article will explore the core role of focal length in the laser welding process and provide practical suggestions for focal length selection and optimization to help you achieve high-quality and high-consistency welding results.
目次
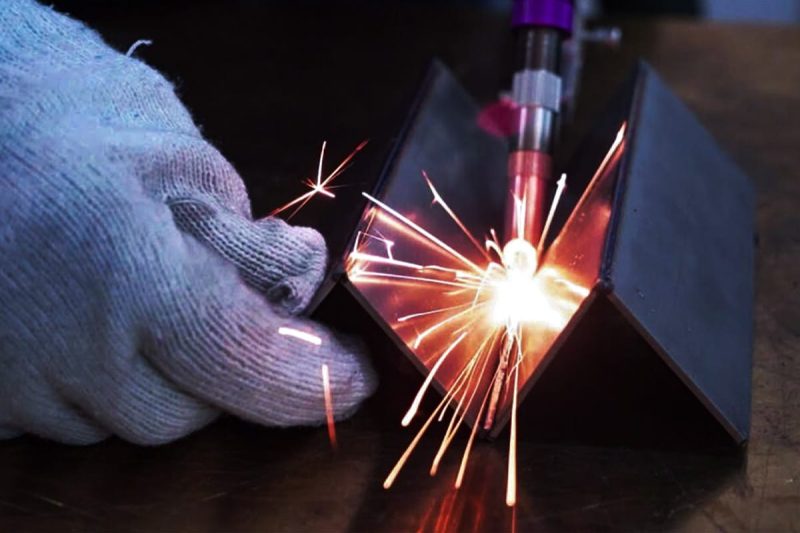
Understanding Focal Length in Laser Welding
In the laser welding system, the focal length is one of the core parameters in the laser optical path, which has a direct impact on the welding quality, depth control, and weld stability. Whether you are using a continuous laser welding machine or a pulsed laser welding machine, correctly understanding and selecting the appropriate focal length is crucial to optimizing the molten pool morphology and achieving high-quality connections.
The laser beam emitted by the laser generator is focused into a high-energy-density spot through the focusing lens (Laser Focusing Lens). In this process, the focal length refers to the distance from the focusing lens to the position of the laser’s minimum spot. Different focal length settings will significantly change the size and energy density of the laser spot, thereby affecting the penetration ability of the welding, the weld shape, and the range of the heat-affected zone.
Common laser focusing lens types and focal length ranges
- Standard Plano-Convex Lens: Commonly used for general welding, the focal length range is usually between 100mm-300mm.
- F-Theta Scan Lens: Suitable for use with scanning systems, it can achieve large-format high-speed welding, and common focal lengths include 160mm, 254mm, etc.
- Long Focus Industrial Lens: The focal length can reach 400mm or longer, and is used for long-distance welding of thick plates or special structural parts.
When selecting each lens type, not only should the laser wavelength and power matching be considered, but also the most suitable focal length parameters should be determined based on the thickness, reflectivity, weld structure, and processing accuracy of the target workpiece.
The Importance of Focal Length Selection
If the focal length is too short, although a smaller focused spot and higher energy density can be achieved, it is easy to cause problems such as too fast beam divergence, insufficient penetration, and heat concentration leading to weld surface ablation; if the focal length is too long, it may cause energy dispersion, insufficient welding depth or unstable molten pool.
Therefore, choosing an appropriate focal length can effectively control the spot size and energy distribution, thereby affecting the depth, width, flatness, and strength stability of the weld. For the welding of precision components, dissimilar metal connections, or heat-sensitive materials, focal length matching is particularly critical and can effectively reduce welding defects (such as undercuts, pores, weld penetration, etc.).
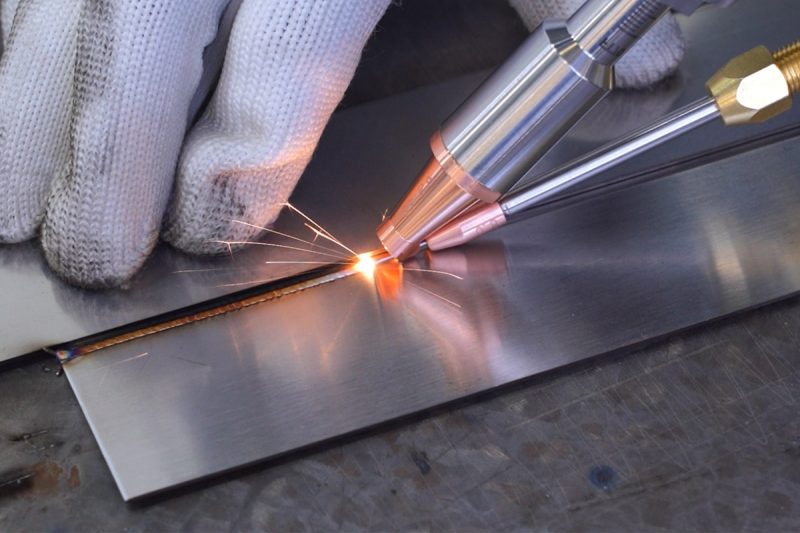
Effect of focal length on welding parameters
In the laser welding process, focal length is not only a basic parameter of optical design, but also directly affects the beam characteristics and various process parameters of the welding results. The energy distribution form, action depth, and molten pool control of the laser system after focusing will change significantly with the change of focal length. Therefore, a deep understanding of the specific impact of focal length on core welding parameters will help achieve higher consistency and controllability in actual processing.
スポットサイズ
The shorter the focal length, the smaller the spot after laser focusing, the more concentrated the laser energy per unit area, and the more detailed and precise heat input control can be achieved. This is especially critical for micro welding, precision electronic device connection, or welding scenes with extremely high edge accuracy requirements. On the contrary, a longer focal length produces a larger spot, which is more suitable for large-area welding workpieces that require higher energy distribution uniformity.
エネルギー密度
In laser welding, energy density = laser power/spot area, which is a key indicator for determining welding depth, speed, and melting state. High energy density formed by short focal length can quickly heat the metal surface, achieve rapid melting and deep welding, and is particularly suitable for laser welding of highly reflective materials (such as アルミニウム そして 銅) or high thermal conductivity materials. Lower energy density is suitable for thin plates and easily deformed materials to avoid damage to the workpiece caused by excessive heat input.
浸透深度
Under the same laser power conditions, the short focal length focused beam has stronger penetration ability and can obtain a deeper molten pool, which is conducive to one-pass welding or thick plate welding. However, due to its concentrated energy, the heat affected zone (HAZ) is relatively small and the cooling rate is fast, which may require higher process stability control. Long focal length has a wider energy distribution and moderate welding depth, which is suitable for processing products with higher requirements for heat effect control.
Welding Quality & Repeatability
Precise focal length matching helps to form a stable molten pool and uniform weld profile. In continuous mass production, maintaining weld size consistency and appearance quality is the core of achieving process standardization. Short focal length is often used for high-precision, high-penetration welding; long focal length is suitable for welding scenes with long continuous trajectories such as thick plate lap joints and pipe circumferential seams, which is convenient for ensuring the uniformity and repeatability of the welding process.
From spot control to energy distribution, to weld depth and appearance consistency, the influence of focal length on laser welding parameters runs through the entire processing process. Reasonable selection of focal length not only determines the stability of the process window, but is also directly related to production efficiency and finished product qualification rate.
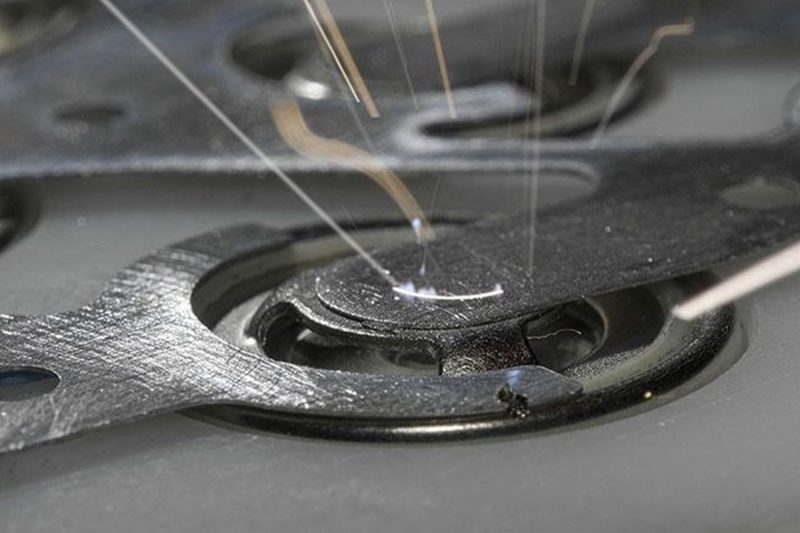
Choosing the Correct Focal Length for Your Welding Application
In the laser welding process, the focal length selection is directly related to the processing depth, heat input control, welding accuracy, and overall stability. A reasonable focal length setting can not only optimize the welding quality but also significantly improve production efficiency. To ensure that the laser welding system is perfectly matched to your specific application, the following core dimensions need to be fully considered:
素材の種類と厚さ
Different materials have different absorption capabilities for laser energy. For example, highly reflective and highly thermally conductive materials such as aluminum and copper require higher energy density and are therefore more suitable for short focal length optical systems to enhance penetration. Materials that absorb lasers well, such as ステンレス鋼 そして 炭素鋼, can achieve stable welding at medium and long focal lengths. For thinner materials, a longer focal length helps avoid burn-through and warping, while for thicker plates, short focal lengths should be prioritized to achieve deep penetration welding.
Joint geometry and assembly
The type of weld joint (lap, butt, T-joint, etc.) and its geometry have an important influence on the choice of focal length. Complex geometries or multi-dimensional weld paths (such as tubular and curved welds) are more suitable for longer focal length lenses, which have a larger depth of field and can better adapt to the height difference of the workpiece surface. High-precision butt welds, especially in automated assembly lines, are usually preferred to use short focal lengths to ensure welding accuracy and stable weld pool control.
Required welding quality and appearance
When the project has high requirements for weld beauty, minimal spatter, clean edges, etc., fine control of focal length is particularly critical. Short focal length can achieve a smaller spot and more concentrated heat input, which helps to form a fine and smooth weld profile; while in situations where the appearance requirements are general but faster speed and greater tolerance are required, using a longer focal length can balance appearance and efficiency.
Production constraints and efficiency targets
Laser welding in industrial environments often faces limitations in terms of space layout, automation equipment matching, and cycle speed. Longer focal length lenses have a greater working distance and fault tolerance, and are suitable for robot welding or large-format platform operations; while short focal length systems have strong focusing capabilities, but have higher requirements for workpiece positioning and stability. According to the production line cycle goals, equipment coordination capabilities, and maintenance convenience, a reasonable choice of focal length will help maximize production output while meeting quality requirements.
Choosing the right laser focal length is not a simple parameter setting, but a systematic project that requires comprehensive consideration of materials, structures, process goals, and equipment environment. Different industries and products have different requirements for laser welding. Only by adapting to local conditions can we achieve ideal welding results.
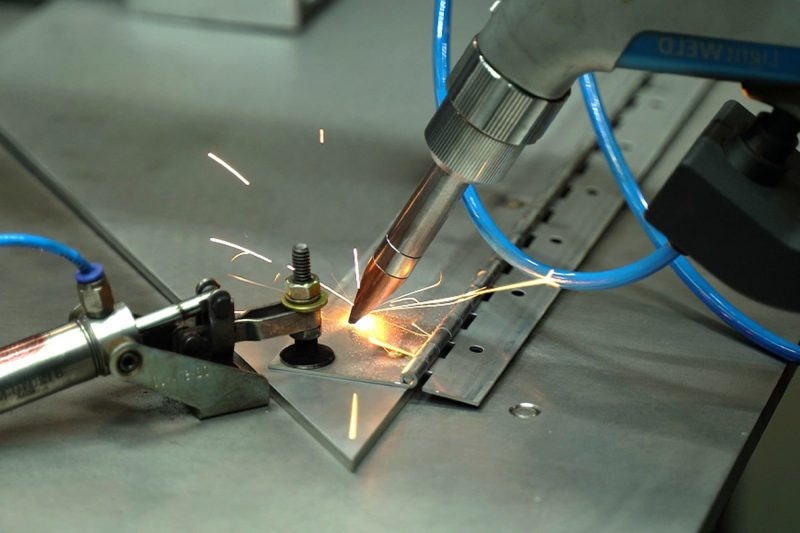
Practical tips for optimizing laser welding focal length
In the actual application of laser welding, even if the theoretically “appropriate” focal length is selected, if it is not finely adjusted in the specific environment, problems such as unstable welding quality, increased spatter, or unsightly welds may still occur. To more effectively play the role of laser focal length in the welding process, the following practical tips can help you accurately optimize the focal length setting at the operational level to achieve more stable and reliable welding quality:
Focus Test
When setting up for the first time or changing different materials and thicknesses, it is recommended to perform a systematic focus test. By fine-tuning the Z-axis height up and down, observing the molten pool width, depth and weld state at different focal lengths, you can find the best focus point. This method helps to intuitively judge the energy concentration area and avoid poor welding caused by focus offset.
Use a focus meter to assist adjustment
To improve focusing efficiency and accuracy, a red light auxiliary system or a dedicated laser focus meter can be used for auxiliary positioning. These tools can accurately indicate whether the current focal length position falls within the focus point of the optical system, thereby significantly improving the accuracy of the first setting, especially in automated or high-frequency switching applications.
Monitoring weld quality feedback
Integrated visual monitoring systems (such as weld trackers and weld pool imaging systems) can help to observe the status feedback of the laser welding process in real time. If the weld width is unstable, spatter increases, or insufficient fusion is found, it may be caused by improper focus setting. By adjusting the focus position in combination with the online feedback system, the welding stability can be dynamically optimized.
Reasonable matching of laser power
There is a close linkage between laser power and focal length. The high energy density brought by shorter focal length requires precise control of power output to prevent over-penetration or burning through, while longer focal length requires increased power to compensate for energy diffusion to maintain stable molten pool formation. During the adjustment process, the spot size and heat input characteristics should be considered simultaneously to ensure power-focal length balance.
Optimizing laser focal length is not a one-time parameter setting, but a process that requires dynamic adjustment based on actual materials, equipment conditions, and welding requirements. Through scientific testing, instrument assistance, visual feedback, and power matching, users can achieve more consistent, high-quality, and efficient welding results in actual production.
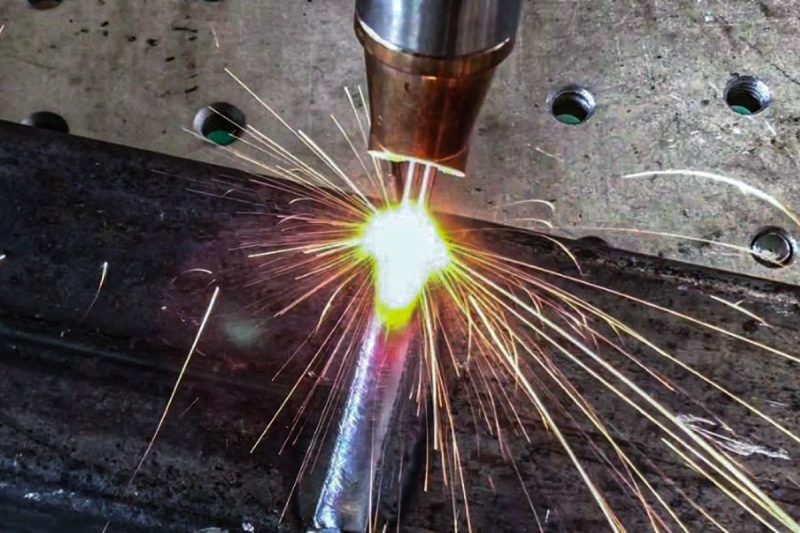
要約する
In the laser welding process, the focal length setting is far more than a simple optical parameter adjustment. It essentially determines the stability of welding quality, the appearance of the weld, and the efficiency and consistency of the entire process. From controlling the laser energy density, adjusting the welding depth, to achieving precise connection of different materials and structures, the selection and optimization of the focal length runs through every key link.
In actual production, ignoring the focal length setting often leads to problems such as unstable welds, increased spatter, insufficient penetration, or overburning. Reasonable focusing can not only improve the quality of weld formation and the consistency of finished products, but also significantly extend the service life of the laser generator and optical system, providing a guarantee for long-term stable operation. Selecting the appropriate focusing lens, matching material properties with welding targets, combining real-time visual monitoring systems and power control strategies, and incorporating focal length optimization into the entire welding process are the keys to achieving efficient, reliable, and automated welding production.
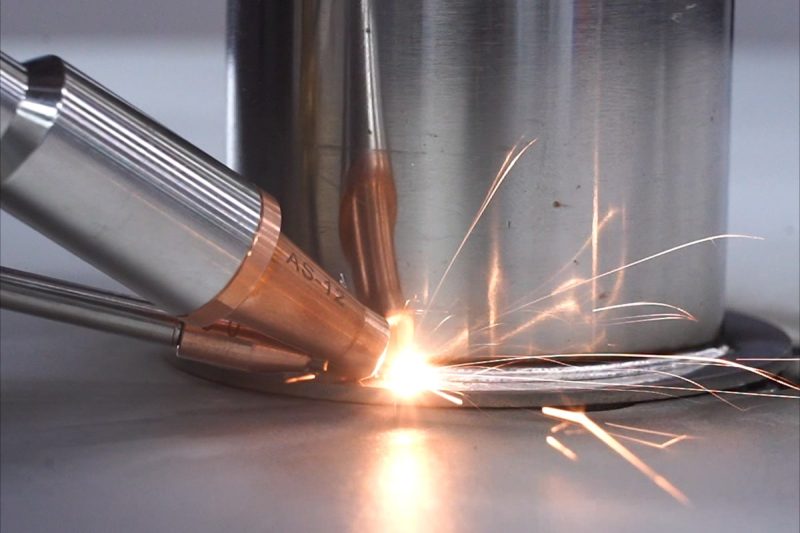
レーザー ソリューションを入手する
If you are looking for a more professional, efficient, and automation-friendly welding solution, welcome to learn more about AccTek Laser’s laser welding machines. We offer a variety of laser focus configurations, including short-focus, high-energy density solutions, and long-focus systems suitable for large-area fusion, supporting integrated intelligent focusing modules, robot control interfaces, and vision guidance units, covering full-scenario applications from manual precision welding to industrial-grade automated welding.
AccTek Laser focuses on laser process innovation and application implementation, and is committed to creating sustainable, high-quality welding solutions for customers. お問い合わせ now to get a personalized technical evaluation and system selection recommendations, and start your high-performance laser welding journey!
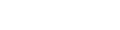
連絡先
- [email protected]
- [email protected]
- +86-19963414011
- No. 3 ゾーン A、Lunzhen 工業地帯、玉城市、山東省。
レーザー ソリューションを入手する