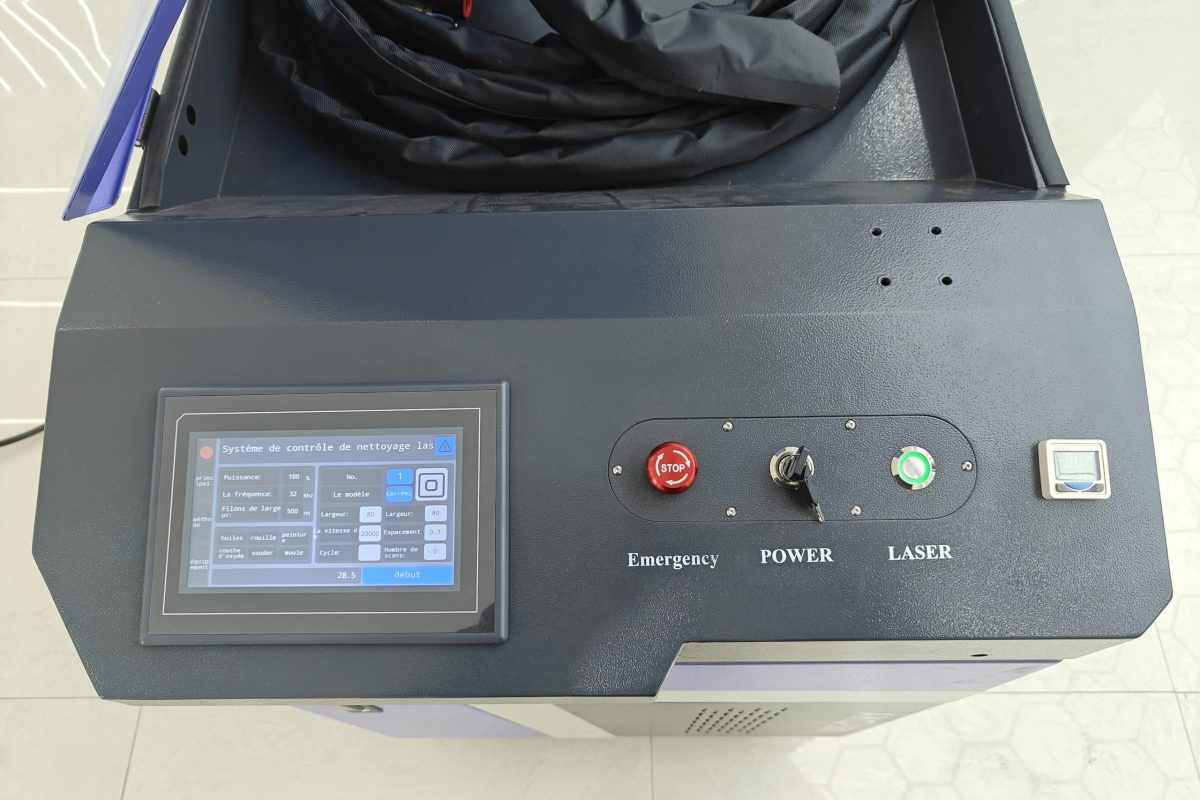
Как настроить импульсный лазерный очиститель?
In recent years, pulse laser cleaning technology has been widely used in industrial surface treatment, cultural relic restoration, mold cleaning, electronic component processing and other fields. Due to its advantages such as high efficiency, environmental protection, no contact with the substrate, and no consumables, it is gradually replacing traditional cleaning methods. Correctly setting up the laser cleaning machine is the key to ensuring the cleaning effect and equipment stability. This guide will systematically explain the entire process of setting up the импульсная лазерная чистящая машина from basic preparation to advanced configuration.
Оглавление
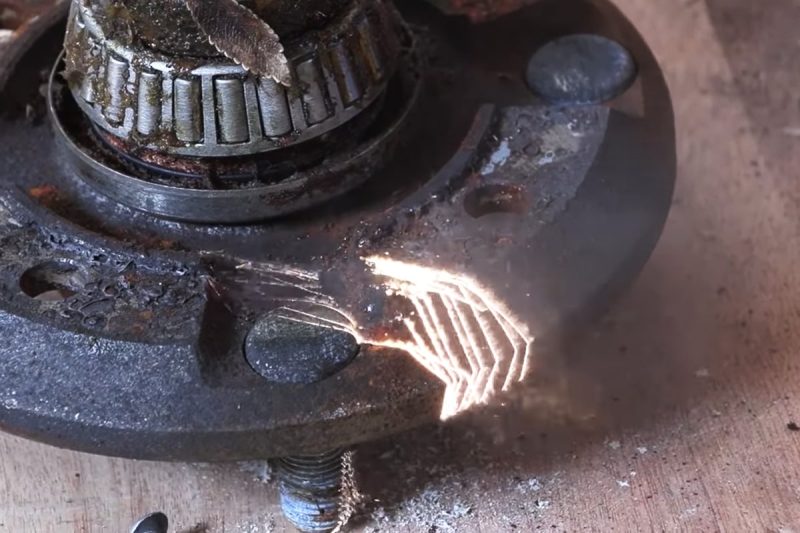
Learn about pulse laser cleaning machine
Pulse laser cleaning is a non-contact cleaning technology that uses short pulse high-energy laser to vaporize, ablate or peel off the contaminated layer. Compared with continuous laser, pulse laser performs better in thermal impact control and fine precision. It is suitable for high-demand scenarios such as laser rust removal, coating stripping, oxide layer removal, etc., and is particularly suitable for cleaning tasks of high-value metals and precision parts.
Initial planning and preparation
Before installing and using pulse laser cleaning equipment, scientific preliminary planning is the key to ensuring cleaning results, improving work efficiency and extending equipment life. Only after fully understanding the cleaning requirements, material types and pollution characteristics can the laser system be reasonably configured to maximize the performance of the equipment. The following systematically introduces the core content of preliminary planning and preparation from two aspects.
Assess cleaning needs
Before formal installation, the specific cleaning conditions should be clarified first to formulate the corresponding process plan. The following aspects should be considered:
- Substrate type: Different materials have different absorption rates for lasers, which will directly affect the cleaning efficiency and safety. Common laser cleaning application materials includecarbon steel, stainless steel, aluminum alloy, copper, titanium, and some non-metallic materials such as stone and polymer plastics.
- Pollutant type: It is necessary to identify the type of pollutant layer on the surface of the cleaning object, such as rust, oxide scale, welding spatter, old paint layer, oil stains, resin, or coating. Different pollutants respond differently to laser energy, so parameters need to be set in a targeted manner.
- Cleaning goal: It should be clear whether the laser cleaning task is to completely remove surface pollutants or only perform surface roughening to improve the adhesion of subsequent spraying, electroplating, or welding. Different goals will determine the value range of parameters such as pulse energy and scanning speed.
Accurate needs assessment is the prerequisite for developing efficient, safe, and cost-controlled laser rust removal or laser surface treatment solutions.
Choosing the right laser system
After clarifying the cleaning requirements, it is necessary to select a suitable laser cleaning system according to the actual application scenario. The following are the main reference parameters:
- Laser type: Currently, laser cleaning equipment mainly uses pulsed fiber laser generators or Nd: YAG laser generators. Among them, pulsed fiber laser generators have become the mainstream choice due to their small size, high stability, no consumables, and low maintenance costs.
- Wavelength selection: The laser wavelength affects the absorption characteristics of the material. The near-infrared wavelength of 1064nm is generally used in industry, which is particularly suitable for cleaning pollutants on metal surfaces, taking into account high energy density and material adaptability.
- Pulse energy and frequency: The peak power and frequency of the pulsed laser determine the energy density of a single pulse. It should be configured according to the thickness of the contamination layer, the cleaning speed and the heat resistance of the substrate to avoid thermal damage to the substrate.
- Power range: Select laser generators of different powers according to the intensity of the cleaning task. The power range of common машины для лазерной очистки is 100W to 2000 For heavy pollution or large-area cleaning needs, higher power equipment (such as 500W or more) can be selected to improve efficiency.
Reasonable selection not only affects the cleaning efficiency but is also directly related to the service life of the equipment and its long-term stable operation capability. It is the core step to ensure the quality of laser cleaning.
Early planning and preparation are not only the prerequisites for the successful use of laser cleaning systems, but also directly related to the stability of equipment operation, the controllability of cleaning quality, and the safety of operators. By scientifically evaluating cleaning needs and selecting appropriate laser generator configurations and parameter combinations, users can fully unleash the potential of pulsed laser cleaning technology while improving production efficiency and achieving true green cleaning and intelligent manufacturing.
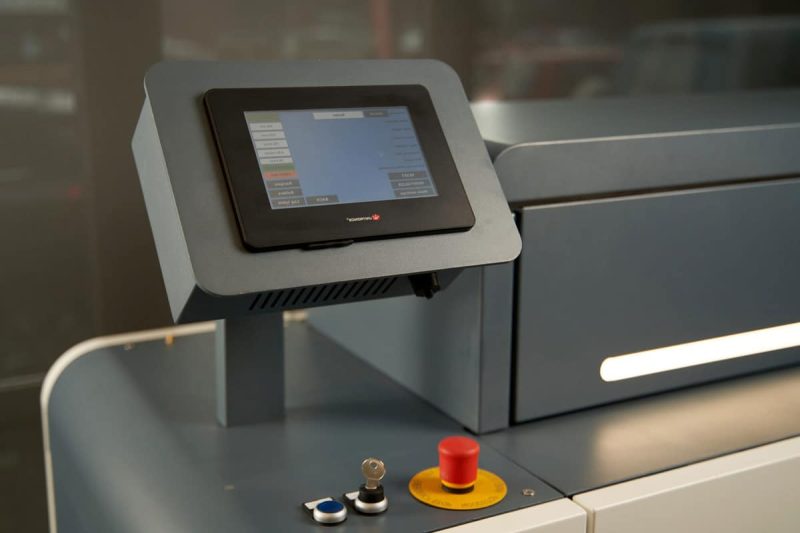
Setting up the laser cleaning machine
After completing the cleaning needs assessment and equipment selection, the next step is to install and debug the laser cleaning system on site. This stage of work is not only related to whether the equipment can run smoothly, but also directly affects the subsequent cleaning efficiency and safety. Scientific and standardized installation and calibration will help the laser rust removal equipment achieve its proper cleaning ability and system stability.
Machine Installation
The installation process of laser cleaning equipment needs to fully consider the adaptability and safety of the operating environment:
- Site preparation: Choose a clean, dry, and well-ventilated industrial plant as the equipment installation location, and reserve enough space for the equipment body, control system, and operation channel to avoid overheating, dust accumulation, and other factors that affect the stable operation of the laser cleaning system.
- Power supply configuration: According to the power requirements of the laser generator, control cabinet, and chiller, a matching industrial power supply (generally 220V or 380V) should be configured, and the voltage should be stable to avoid equipment abnormalities due to voltage fluctuations. It is recommended to equip a voltage stabilizer and dedicated grounding protection.
- Cooling system installation: High-power pulsed laser generators will generate a lot of heat during continuous work, so an efficient industrial chiller must be installed to keep the laser generator temperature within a safe range and extend the service life of the laser module.
- Ventilation and smoke exhaust system: Smoke, odor, and tiny particles will be generated during laser cleaning, and a professional smoke purification system or industrial smoking equipment must be configured. Ensuring a good smoke exhaust effect not only improves the working environment but also meets environmental protection regulations.
Alignment and calibration
After completing the basic hardware installation, the laser system needs to be precisely calibrated to ensure consistent and safe cleaning results:
- Laser beam alignment: Use a positioning device or reference template to accurately align the laser beam with the surface of the workpiece to be cleaned, keep the spot position and angle stable, and avoid offsets that cause uneven cleaning areas or damage to the substrate.
- Laser parameter calibration: According to the material properties and contaminant characteristics, adjust key parameters such as laser power, pulse frequency, scanning speed, and pulse width to match different cleaning task requirements, improve efficiency, and avoid overheating.
- Test run: It is recommended to test samples before batch cleaning. By observing the cleaning effect, surface changes, and heat-affected areas, further fine-tune the parameters to ensure that the pulse laser cleaning process is stable and controllable.
By completing the installation and commissioning of laser cleaning equipment in a scientific and standardized manner, not only can the overall operating efficiency of the equipment be improved, but the equipment life can also be significantly extended, and the maintenance frequency can be reduced. Especially in industrial scenarios of mass production or long-term continuous work, a good initial setting is a key step to ensure the quality and stability of laser cleaning.
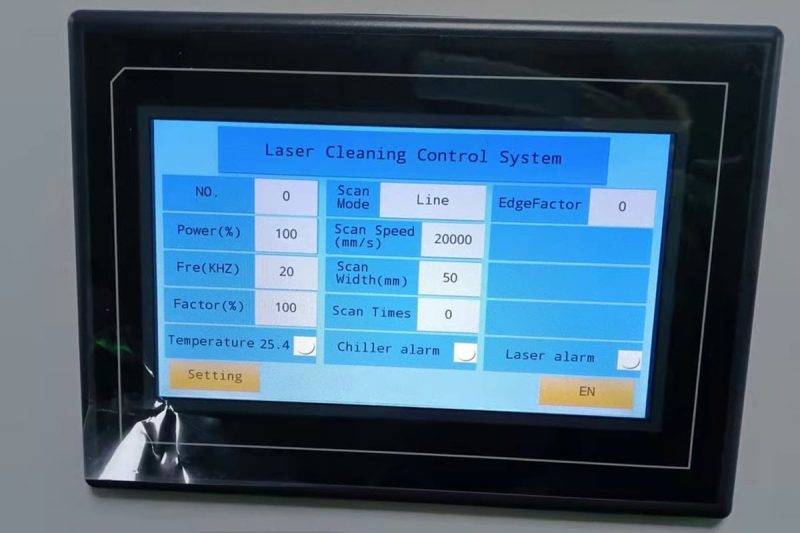
Optimizing laser parameters
After the laser cleaning system is installed and basically debugged, it is crucial to further optimize the laser process parameters. Reasonable setting of various laser parameters can not only improve the efficiency of pollutant removal, but also maximize the protection of the substrate surface to avoid thermal damage and over-processing. Especially in industrial scenarios where diverse materials and complex pollution types coexist, the ability to control parameters determines the adaptability and stability of the laser cleaning system. To achieve the best cleaning effect, it is recommended to focus on the following core parameters:
Длительность импульса
Pulse duration directly affects the action time of the laser and material, and is an important factor in determining cleaning accuracy and heat diffusion range. Shorter pulses (such as nanoseconds and picoseconds) help achieve the “cold processing” effect, which is suitable for surface treatment with high precision requirements and reduces the heat-affected zone of the substrate. In comparison, longer pulses are ideal for efficient stripping of thick and heavy contamination.
Импульсная энергия
The higher the pulse energy, the stronger the peeling ability under the unit laser action, which can effectively destroy the bonding force between the contamination layer and the substrate. However, it must be controlled within a safe range to avoid melting or ablation of the substrate. Usually, it needs to be adjusted step by step according to the thickness of the contamination, the adhesion strength, and the thermal sensitivity of the substrate.
Частота повторений
The laser repetition frequency determines the number of laser pulses per unit time, thereby controlling the cleaning efficiency and heat accumulation. A higher repetition rate can speed up the processing, but if the pulse energy is not properly matched, it may cause problems such as excessive heat accumulation and surface discoloration. The comprehensive balance of frequency and energy is the key to achieving efficient and stable cleaning.
Beam Profile & Focus Spot
The beam shape and focus position of the laser directly affect the energy density per unit area. Good focus control can concentrate the energy on the contaminant layer and enhance the cleaning effect. Usually, a Gaussian beam or a top hat spot design with uniform energy distribution is used, combined with an autofocus function to achieve higher consistency and cleanliness.
In general, the final performance of the laser cleaning system depends not only on the hardware configuration of the equipment itself, but also on the professionalism of parameter debugging and process optimization capabilities. By scientifically setting core parameters such as pulse width, energy, frequency, and spot control, the cleaning efficiency can be significantly improved, the material damage rate can be reduced, and more complex cleaning scenarios can be adapted.
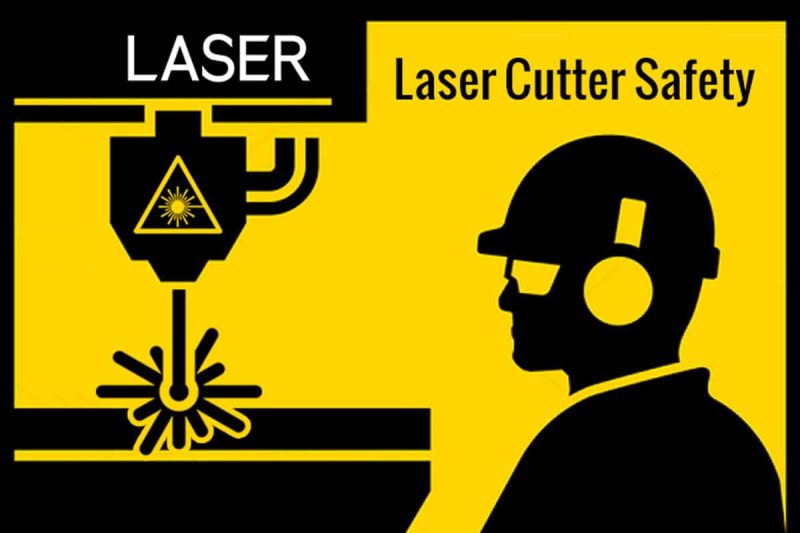
Протокол безопасности
During the use of laser cleaning machines, ensuring the safety of the operating environment and personnel is a basic prerequisite for the stable operation of the equipment and production compliance. Since the laser generator itself has high energy and high focusing characteristics, and harmful smoke and particles may be generated during the cleaning process, if there is a lack of a complete protection mechanism, it will bring potential risks to the health of operators and the surrounding environment. Therefore, when deploying laser cleaning systems, companies must simultaneously implement a complete set of systematic safety protocols.
Laser safety measures
To prevent laser radiation from causing harm to the human body, the following laser protection strategies are recommended:
- Wear laser goggles: Operators must be equipped with goggles that meet the requirements of laser wavelength, such as OD-level goggles for 1064nm wavelength, to ensure that the eyes are not damaged by direct or reflected laser light.
- Configure safety interlock device: Configure an interlock system for the laser generator and the working area. If a protective door is not closed or an abnormal person enters the area, the system should automatically interrupt the laser output to prevent misoperation and accidental triggering.
- Set up warning signs: Hang eye-catching signs such as “Laser Operation Area” and “Wear Goggles” in obvious locations in the working area to remind all personnel entering the area to pay attention to protection.
Smoke and Particle Control
During the laser cleaning process, pollutants will be vaporized, and fine particles and smoke will be released. If not removed in time, it may cause damage to the operator’s respiratory system and the equipment structure:
- Install a fume extractor: Efficiently filter out PM2.5 particles, oil mist, organic gases, etc., to ensure that air cleanliness meets industrial safety standards.
- Ensure that the ventilation system is unobstructed: Especially when working in closed or narrow spaces, industrial exhaust fans or negative pressure ventilation equipment should be equipped to maintain good air flow and exhaust paths to prevent pollutants from depositing on the surface of the equipment or flowing back to the work area.
Обучение и образование
Even if the hardware protection measures are perfect, the standardization of personnel operation is still an important guarantee for safe operation. Therefore, a regular training system should be established:
- Laser safety training: including the principle of laser hazards, emergency response procedures, how to use personal protective equipment, etc., to enhance employees’ safety awareness.
- Operation training: ensure that operators master the basic skills of correct startup, shutdown, parameter adjustment, troubleshooting, etc., of the laser cleaning machine.
- Maintenance training: train relevant technicians to master the daily maintenance process of the equipment, including optical path inspection, filter element replacement, cooling system maintenance, etc., to ensure the long-term stable operation of the equipment.
Overall, while laser cleaning technology brings high efficiency and environmental protection advantages, it also puts forward higher requirements for safety in use. Enterprises should take the safety agreement as the core part of the project launch, and build a safety system that meets industry standards from source risk assessment, equipment selection, to personnel training and environmental protection.
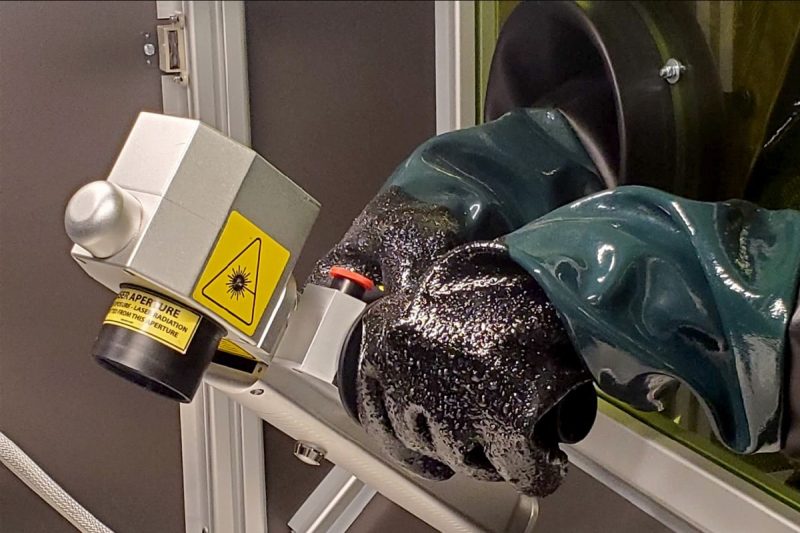
Regular maintenance and troubleshooting
To ensure the continuous, efficient, and stable operation of the laser cleaning machine, the company must establish a systematic daily maintenance mechanism and troubleshooting process. Although the laser system is a non-contact processing equipment, its core components, such as the laser generator, optical system, and cooling system, are still inevitably affected by multiple factors such as the environment and load during long-term operation. If they are not maintained regularly, it will directly affect the cleaning effect, laser power, and even the service life of the equipment.
Routine maintenance items
It is recommended that users develop maintenance plans for different periods such as weekly, monthly, and quarterly according to the frequency of equipment use, and focus on checking the following items:
- Cleaning of laser head and optical lens: Use dust-free cotton swabs and special lens cleaning fluid to regularly wipe the protective lens and focusing lens to prevent laser divergence, power reduction, or mirror ablation due to dust and oil.
- Check the cooling system status: Check daily whether the cooling capacity of the industrial chiller is normal, whether the water channel is unobstructed, and whether the water temperature is kept within the recommended range of the laser generator. Regularly replace pure cooling water and clean the water tank filter to avoid scale accumulation and reduce heat conduction efficiency.
- Replace consumable parts: Regularly replace aging laser optical fiber, power cable, dust cover, protective lens, etc., especially for equipment under heavy load conditions or long-term continuous operation, pay more attention to the life cycle of consumables.
Common troubleshooting
When the laser cleaning equipment runs abnormally, a systematic investigation should be carried out based on the phenomenon to ensure rapid recovery:
- Laser power fluctuation: often caused by poor heat dissipation of the laser generator, unstable power supply voltage, or contaminated optical path. Check the cooling system water temperature, the firmness of the power supply wiring, whether the optical path is blocked, or the lens is contaminated.
- Beam deviation or abnormal cleaning trajectory: usually caused by loose optical lenses, tilted installation, or internal structure deviation of the laser head. It is recommended to re-lock the lens and recalibrate the optical path or replace the focusing component if necessary.
- Abnormal smoke filtration or weak exhaust may be caused by filter blockage or fan damage. Check the saturation of the smoke purifier filter in time, replace the high-efficiency filter if necessary, and confirm that the exhaust duct is not blocked and the fan is operating normally.
Through regular maintenance and standardized troubleshooting processes, users can not only significantly reduce equipment failure rates and extend the service life of the entire machine but also ensure the continuity and consistency of cleaning operations, reduce the risk of production interruptions, and improve overall production capacity.
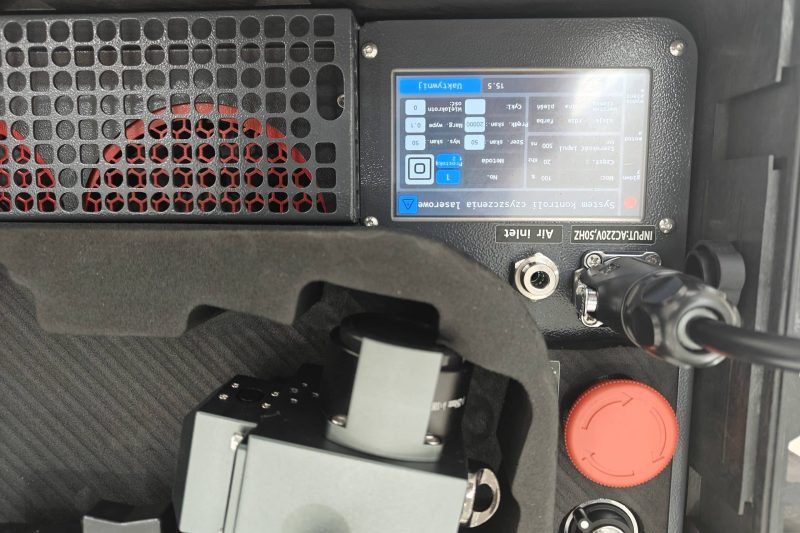
Advanced Settings Notes
With the development of intelligent manufacturing and industrial automation, the application of laser cleaning equipment is not limited to manual operation or simple cleaning scenarios, but tends to be automated, intelligent, and traceable. Especially in high-end manufacturing fields such as automobile manufacturing, precision molds, aerospace, etc., the advanced configuration capabilities and automated integration performance of laser cleaning systems have become the key to improving production line efficiency, reducing labor costs, and ensuring cleaning consistency.
Interfacing with automation systems
Modern laser cleaning equipment generally supports integration with a variety of industrial automation platforms, such as connecting to robot systems, PLC control systems, visual positioning systems, etc., through communication interfaces (EtherCAT, Profinet, Modbus, etc.). It can achieve:
- Robot-assisted Laser Cleaning: The robot arm drives the cleaning head to move precisely, realizing automated cleaning of large quantities of complex curved surfaces.
- Track control and scanning head linkage: With a multi-axis linkage platform or automatic slide rail, the laser scanning path is controlled to achieve efficient and continuous cleaning of large-sized workpieces.
- Remote triggering and safety interlocking mechanism: Ensure operational safety and equipment stability, and support automatic anti-flood and abnormal shutdown mechanisms.
Data recording and analysis
High-end laser cleaning systems are usually equipped with industrial-grade data recording modules to record the core parameters of each cleaning operation, such as power, frequency, pulse width, trajectory time, etc., to facilitate later analysis and quality traceability:
- Cleaning parameter archiving: The cleaning data corresponding to each batch of workpieces is automatically stored, and the cleaning status at each time can be traced.
- Quality analysis: Combined with cleaning effect detection (such as image recognition or sensor feedback), a database is formed for different materials and parameter combinations to assist process optimization.
- Remote diagnosis and system upgrade: Through the cloud platform or industrial server, remote software upgrades and fault diagnosis are supported to improve after-sales response efficiency.
Customized solutions
In response to customers’ special cleaning needs, the laser cleaning system can be flexibly customized with exclusive fixture systems, rotating platforms, roller conveyor lines, automatic loading and unloading systems, etc.:
- Special fixture design: improves fixing efficiency and ensures that the laser beam stably covers the cleaning area.
- Batch automated processing, such as docking with automatic assembly lines to achieve multi-station continuous operation in industrial scenarios;
- Flexible process adjustment: The system supports multi-task process parameter presets, which facilitate quick switching between different cleaning tasks.
Through advanced settings and automated integration, laser cleaning equipment is no longer an isolated stand-alone tool but an important part of the intelligent production line. It not only improves production rhythm and cleaning consistency, but also helps enterprises build a sustainable, highly flexible, and high-standard intelligent manufacturing system.
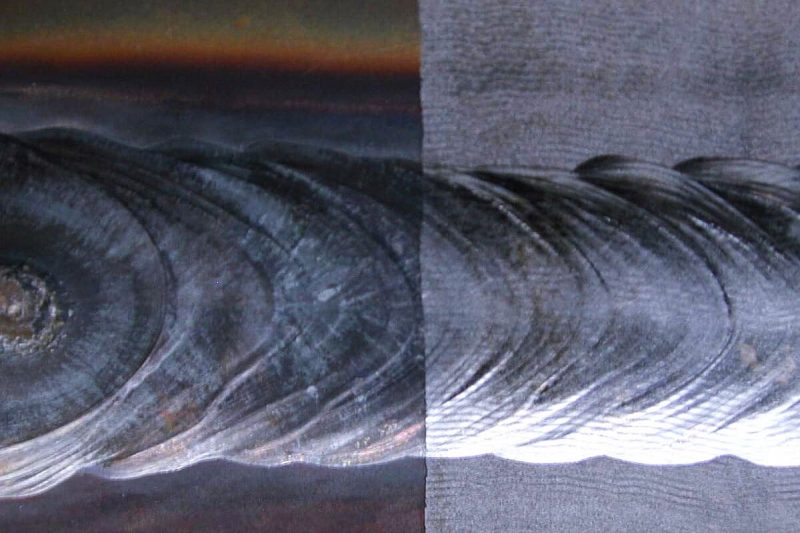
Подведем итог
The outstanding performance of a pulse laser cleaning machine with excellent performance and stable operation depends not only on the high-quality laser generator body, but also on the scientific planning and reasonable configuration of the entire system from setting to application. Whether in complex metal rust cleaning, oxide layer stripping, or high-precision mold surface treatment, to achieve efficient, safe, and controllable cleaning effects, it is necessary to ensure that all process steps are strictly executed:
From the early cleaning condition assessment (including material type, contaminant characteristics, cleaning target), to selecting the appropriate laser generator type and power parameters, matching the appropriate cooling system and exhaust purification equipment, to the later laser beam alignment, parameter debugging, system calibration and safety protection, etc., each link will directly affect the equipment’s work efficiency, cleaning accuracy and service life. A scientific setting process can not only improve cleaning consistency but also significantly reduce operating costs and maintenance frequency, which is the key to ensuring the long-term and efficient operation of the enterprise.
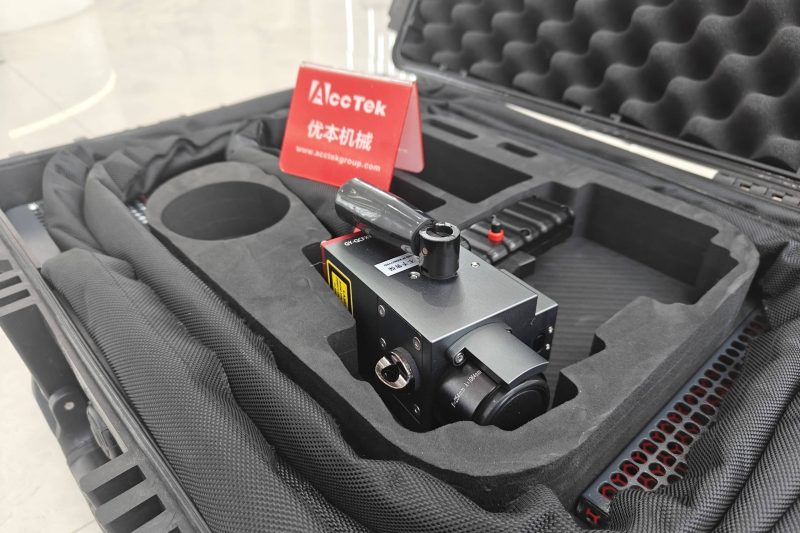
Получить лазерные решения
If you are looking for a truly high-performance, intelligent, and adaptable laser surface treatment solution, Актек Лазер will be your ideal choice. We are committed to providing global customers with pulsed laser cleaning systems covering multiple industries and scenarios. The equipment covers a variety of power levels from 50W to 500W, suitable for all-condition applications from light stain cleaning to heavy pollution rust removal. More importantly, we also support full-process customized services, and can flexibly configure exclusive fixtures, automation systems, and operation interfaces according to your workpiece shape, cleaning needs, and production line environment.
In addition, we have an experienced technical engineering team that can provide customers with one-to-one pre-sales condition assessment, remote installation guidance, operation training, and continuous technical support to ensure that you can use the equipment smoothly, efficiently, and worry-free at every stage of equipment use. Choosing us means choosing professionalism, efficiency, and long-term value. Welcome to связаться с нами for free testing solutions or customized consulting advice.
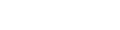
Контактная информация
- [email protected]
- [email protected]
- +86-19963414011
- Зона № 3 А, промышленная зона Лунчжэнь, город Юйчэн, провинция Шаньдун.
Получить лазерные решения