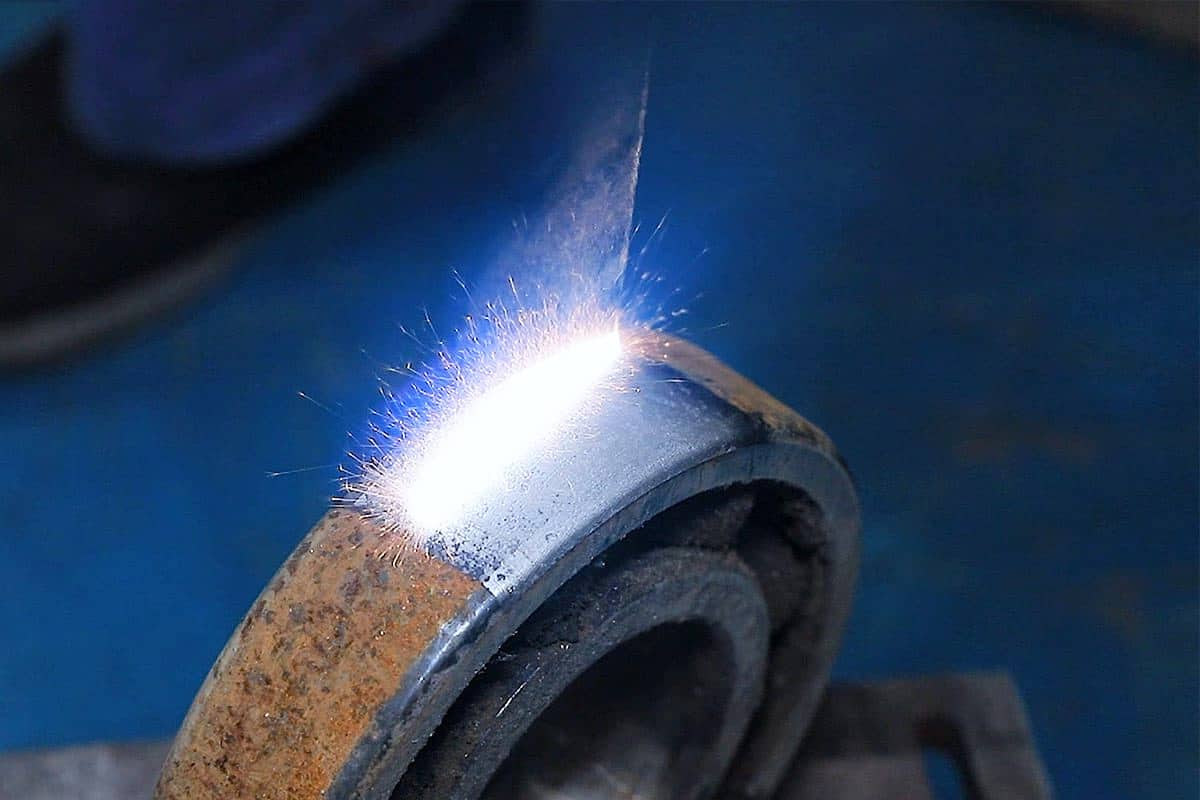
Le nettoyage au laser pulsé endommagera-t-il le substrat ?
Le nettoyage par laser pulsé a gagné en popularité dans des applications telles que la préparation de surface au laser et l'élimination de la rouille par laser à fibre, en raison de sa grande efficacité, de son respect de l'environnement et de son absence de contact. Cependant, une préoccupation majeure demeure pour de nombreux utilisateurs : cette technologie peut-elle endommager le substrat ?
Cet article explore les fondamentaux du nettoyage par laser pulsé, en examinant les effets thermiques, mécaniques et photochimiques potentiels susceptibles d'endommager le substrat selon différents paramètres. Nous examinerons également les principaux facteurs d'influence, tels que la conductivité thermique et le taux d'absorption du matériau, et présenterons des stratégies pratiques, telles que l'optimisation des paramètres, le contrôle multi-impulsions et la surveillance de la température en temps réel, pour minimiser les risques.
Table des matières
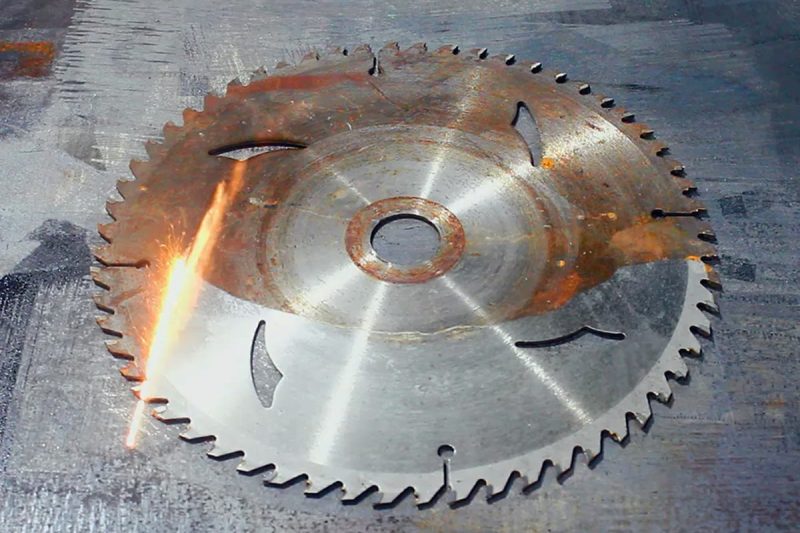
Comprendre le nettoyage au laser pulsé
Le nettoyage laser pulsé est une technologie de traitement de surface efficace, écologique et sans contact, largement utilisée dans des applications telles que l'élimination de la rouille et de la peinture, le nettoyage des couches d'oxyde et la préparation de surface laser pour les moules de précision et les composants électroniques. Son principe de base repose sur des impulsions laser à haute énergie qui vaporisent ou éliminent rapidement les contaminants du substrat sans provoquer d'effets thermiques ni de dommages mécaniques importants.
Dans les applications pratiques, la compréhension et l’optimisation des paramètres clés suivants sont essentielles pour améliorer l’efficacité du nettoyage et garantir la sécurité du substrat :
- Durée d'impulsion : désigne la durée d'une impulsion laser unique, généralement de l'ordre de la nanoseconde, de la picoseconde, voire de la femtoseconde. Des impulsions plus courtes contribuent à réduire la zone affectée thermiquement (ZAT), ce qui les rend idéales pour le nettoyage de précision des matériaux thermosensibles.
- Énergie d'impulsion : représente l'énergie transportée par chaque impulsion laser, affectant directement la capacité de nettoyage. Une énergie d'impulsion plus élevée est efficace pour éliminer les contaminants fortement adhérents, mais elle doit être soigneusement contrôlée pour éviter d'endommager le substrat.
- Taux de répétition : désigne la fréquence des impulsions laser émises par unité de temps. Un taux de répétition plus élevé peut accélérer le nettoyage, mais, s'il n'est pas correctement contrôlé, il peut provoquer une accumulation de chaleur et des dommages thermiques.
- Longueur d'onde : La longueur d'onde du laser détermine son interaction avec différents matériaux. Par exemple, les métaux réagissent généralement mieux à une longueur d'onde laser de 1 064 nm.
- Profil du faisceau : désigne la distribution énergétique du faisceau laser dans l'espace. Un profil de faisceau idéal doit présenter une distribution énergétique uniforme, garantissant un nettoyage stable et efficace, tout en évitant une surchauffe localisée ou un nettoyage irrégulier.
Dans des applications telles que l'élimination de la rouille au laser, le nettoyage au laser des moules ou d'autres utilisations industrielles, une configuration appropriée de ces paramètres améliore non seulement l'efficacité, mais protège également le matériau, ce qui en fait un facteur crucial pour obtenir un nettoyage au laser pulsé de haute qualité.
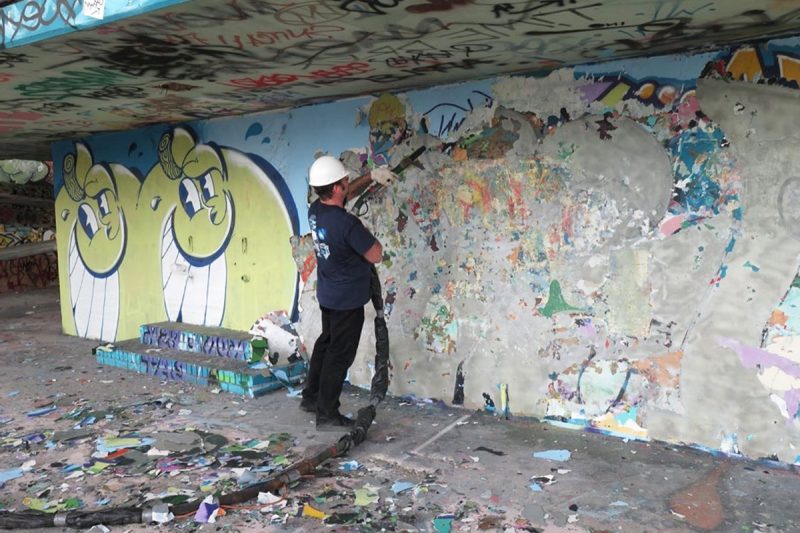
Mécanismes d'endommagement du substrat
Lors du nettoyage par laser pulsé, les substrats peuvent être affectés par divers mécanismes, notamment des effets thermiques, mécaniques et photochimiques. Bien que la technologie de nettoyage par laser pulsé offre une grande efficacité et des avantages environnementaux, ces effets peuvent endommager le substrat dans certaines conditions. Voici les mécanismes d'endommagement spécifiques :
Effets thermiques
- Fusion : Les impulsions laser à haute énergie peuvent chauffer localement le substrat à des températures supérieures au point de fusion, provoquant une fusion localisée. Ce phénomène est particulièrement fréquent lors du nettoyage de surfaces métalliques ou de revêtements. Une énergie laser trop élevée peut entraîner une fusion localisée.
- Contrainte thermique : Un chauffage et un refroidissement rapides pendant le nettoyage laser peuvent provoquer une dilatation thermique irrégulière, générant des contraintes internes dans le matériau. Ces contraintes peuvent entraîner des fissures ou des déformations, en particulier sur les matériaux thermosensibles ou à parois minces.
- Zone affectée thermiquement (ZAT) : La microstructure et les propriétés mécaniques du substrat dans la ZAT peuvent changer. Ce changement peut réduire la résistance mécanique et la durée de vie du substrat, en particulier dans les métaux et alliages, où la ZAT peut entraîner une diminution des performances du matériau.
Effets mécaniques
- Ondes de choc : L'expansion du plasma induite par le laser génère des ondes de choc susceptibles d'endommager mécaniquement la surface du substrat. Ceci est particulièrement vrai pour les matériaux fragiles ou fins, où les ondes de choc peuvent provoquer des fissures superficielles ou un écaillage.
- Pression de vaporisation : La vaporisation rapide des contaminants génère une pression élevée, qui peut être transférée à la surface du substrat, appliquant une charge mécanique supplémentaire. Un nettoyage trop rapide ou une énergie trop élevée peut entraîner des dommages localisés ou une déformation du substrat.
Effets photochimiques
- Modifications chimiques de surface : Les photons à haute énergie émis par le laser peuvent interagir avec la surface du substrat, provoquant des réactions chimiques qui altèrent ses propriétés de surface. Par exemple, certains procédés de nettoyage laser peuvent déclencher une oxydation ou d'autres réactions chimiques, modifiant ainsi la structure et la composition chimique de la surface du substrat.
- Contamination : L'élimination incomplète des contaminants lors du nettoyage peut entraîner le redéposition de matières résiduelles à la surface du substrat, provoquant une nouvelle contamination. Cela peut nuire aux performances du substrat et avoir des effets néfastes à long terme sur son utilisation.
Bien que le nettoyage laser pulsé constitue une méthode très efficace pour éliminer les contaminants de surface, il est essentiel de contrôler soigneusement les paramètres laser, tels que l'énergie, la durée et la fréquence d'impulsion, afin d'éviter que les effets thermiques, mécaniques et photochimiques mentionnés ci-dessus n'endommagent le substrat. Une configuration adéquate des paramètres laser et un contrôle précis sont essentiels pour garantir la sécurité et l'efficacité du processus de nettoyage.
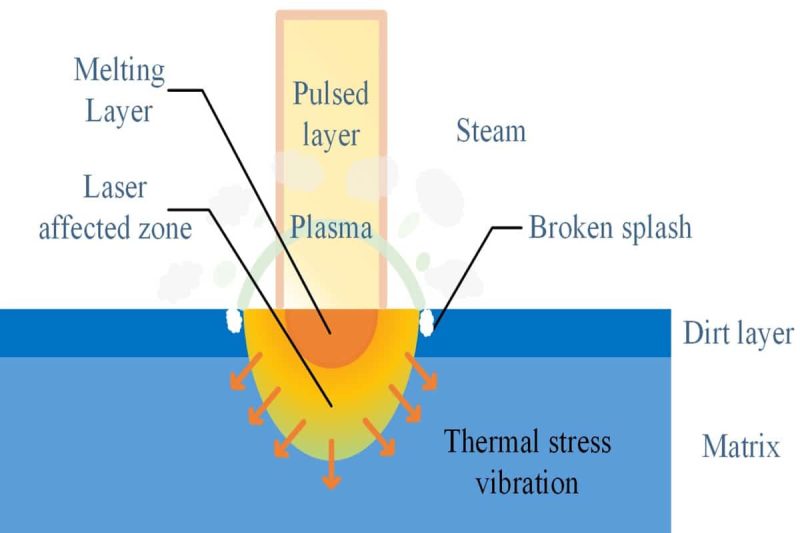
Facteurs influençant les dommages au substrat
Lors du nettoyage par laser pulsé, divers facteurs influencent le degré de dommage potentiel du substrat. Comprendre et optimiser ces facteurs est essentiel pour garantir une élimination efficace des contaminants et la protection du substrat. Voici les principaux facteurs d'influence :
Propriétés matérielles
- Conductivité thermique : Les matériaux à conductivité thermique élevée dissipent la chaleur plus efficacement, réduisant ainsi le risque d'accumulation et de dommages thermiques. Par exemple, les métaux comme le cuivre et l'aluminium sont moins sujets à la dégradation thermique lors du nettoyage laser grâce à leur meilleure dissipation thermique.
- Coefficient d'absorption : Le coefficient d'absorption détermine la quantité d'énergie laser qu'un matériau peut absorber à une longueur d'onde donnée. Un taux d'absorption plus élevé entraîne un échauffement de surface plus rapide, rendant un contrôle précis de la longueur d'onde et de la puissance du laser essentiel pour un nettoyage en toute sécurité.
- Point de fusion : Les matériaux à point de fusion plus bas sont plus susceptibles de fondre sous l'effet d'un laser à haute énergie. Il est essentiel de choisir des paramètres de nettoyage adaptés pour travailler avec des substrats sensibles à la chaleur, comme les plastiques ou les alliages à bas point de fusion.
- Résistance mécanique : Une résistance mécanique plus élevée permet à un matériau de résister aux dommages causés par les ondes de choc ou les contraintes thermiques. Les substrats plus résistants sont moins susceptibles de se fissurer ou de se déformer lors du nettoyage par laser pulsé haute fréquence.
- Composition chimique : La stabilité chimique du substrat influence sa sensibilité aux réactions photochimiques. Certains matériaux peuvent subir des modifications chimiques de surface lorsqu'ils sont exposés à des photons de haute énergie, ce qui peut nuire à leurs performances.
Paramètres laser
- Durée d'impulsion : La durée de chaque impulsion laser affecte directement le transfert de chaleur au substrat. Les impulsions ultracourtes (par exemple, les lasers femtosecondes) peuvent réduire considérablement la zone affectée thermiquement (ZAT), réduisant ainsi le risque de dommages thermiques, en particulier pour les composants délicats ou de précision.
- Énergie d'impulsion : Un réglage précis de l'énergie d'impulsion est essentiel. Une énergie suffisante est nécessaire pour éliminer les contaminants, mais une énergie excessive peut entraîner la fusion ou l'ablation du substrat. L'optimisation de ce paramètre garantit un nettoyage efficace et sûr.
- Fréquence de répétition : Une fréquence de répétition élevée augmente le risque d'accumulation de chaleur. Pour éviter toute accumulation de chaleur et tout dommage potentiel au substrat, la fréquence doit être ajustée en fonction de la tolérance à la chaleur et de la conductivité du matériau.
- Longueur d'onde : Le choix d'une longueur d'onde laser adaptée aux caractéristiques d'absorption des contaminants et du substrat améliore l'efficacité du nettoyage et réduit les dommages. Il s'agit d'une stratégie clé pour optimiser la préparation des surfaces laser.
Conditions environnementales
- Température ambiante : Des températures ambiantes élevées peuvent augmenter la température initiale du substrat, augmentant ainsi le risque de surchauffe pendant le nettoyage. Un contrôle de la température peut être nécessaire pour les applications sensibles.
- Humidité : Une humidité élevée peut entraîner une condensation à la surface du substrat, altérant ainsi l'interaction du laser avec le matériau. Cela peut entraîner des effets thermiques ou chimiques supplémentaires, compromettant potentiellement les performances de nettoyage.
- État de surface : La rugosité de la surface et le type de contaminants présents influencent le résultat du nettoyage. Des surfaces irrégulières ou des contaminants stratifiés peuvent entraîner une répartition inégale de l'énergie, affectant à la fois l'efficacité du nettoyage et la sécurité du substrat.
La réussite du nettoyage par laser pulsé et son impact sur le substrat dépendent non seulement du système laser lui-même, mais aussi des propriétés physiques et chimiques du matériau, des conditions environnementales et de l'état de surface. Pour minimiser les dommages au substrat et maximiser l'efficacité du nettoyage, il est essentiel d'évaluer minutieusement ces facteurs et d'ajuster les paramètres laser en conséquence.
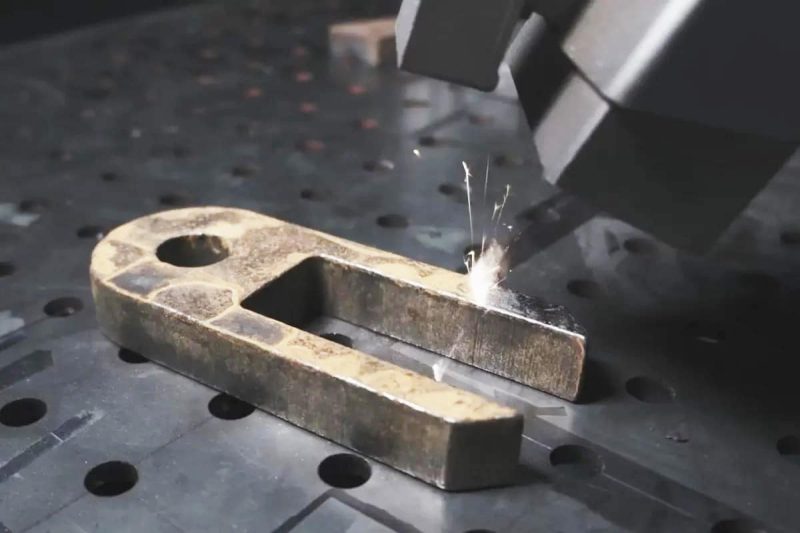
Stratégies pour minimiser les dommages au substrat
Bien que le nettoyage par laser pulsé offre une solution précise et sans contact pour éliminer les contaminants, un mauvais réglage des paramètres peut néanmoins entraîner des dommages irréversibles au substrat sous-jacent. Pour garantir un nettoyage efficace tout en préservant l'intégrité du matériau, il est essentiel d'associer optimisation des paramètres et techniques avancées.
Optimisation des paramètres
- Réglage de la durée d'impulsion : l'utilisation d'impulsions ultracourtes, telles que les lasers femtosecondes, limite considérablement la zone de diffusion thermique, minimisant ainsi efficacement la taille de la zone affectée par la chaleur (HAZ) et réduisant les risques de dommages thermiques.
- Contrôle de l'énergie d'impulsion : le réglage de l'énergie d'impulsion au minimum requis pour l'élimination des contaminants empêche un échauffement ou une fusion excessifs de la surface du substrat, ce qui est crucial pour les matériaux délicats.
- Gestion du taux de répétition : un taux de répétition soigneusement sélectionné garantit un temps de refroidissement adéquat entre les impulsions, contribuant ainsi à prévenir l'accumulation de chaleur pouvant entraîner des déformations, des microfissures ou d'autres problèmes de substrat liés à la chaleur.
- Choisir la bonne longueur d'onde : adapter la longueur d'onde du laser aux caractéristiques d'absorption du substrat et des contaminants améliore la sélectivité du nettoyage, améliore l'efficacité et minimise l'exposition du substrat.
Techniques avancées
- Fonctionnement en mode rafale : en divisant une seule impulsion en une série de sous-impulsions, le mode rafale réduit l'intensité maximale de l'impulsion tout en maintenant l'énergie totale, atténuant ainsi les contraintes thermiques et mécaniques sur la surface.
- Chevauchement multi-impulsions : l'élimination des contaminants en plusieurs passes à l'aide d'impulsions à faible énergie permet une ablation progressive du matériau, réduisant considérablement l'impact sur le substrat.
- Mise en forme du faisceau : l'optique avancée peut distribuer l'énergie laser de manière plus uniforme sur la zone cible, évitant ainsi une surchauffe localisée et garantissant des résultats de préparation de surface laser cohérents.
Suivi et rétroaction
- Surveillance de la température : La température est un facteur clé influençant les dommages thermiques. L'installation de caméras thermiques infrarouges ou de capteurs thermocouples dans la zone de nettoyage permet de suivre en temps réel l'évolution de la température de surface du substrat. Lorsque la température approche du point de fusion ou de la valeur critique de contrainte thermique, le système peut immédiatement réduire l'énergie d'impulsion ou le taux de répétition afin d'empêcher efficacement la fusion, la déformation ou la fissuration thermique du matériau. Ce mécanisme de rétroaction a considérablement amélioré la sécurité et la fiabilité du nettoyage laser dans le domaine de la fabrication de précision.
- Surveillance acoustique : Les technologies de surveillance acoustique, telles que les appareils de mesure d'épaisseur par ultrasons, permettent de suivre efficacement les variations d'épaisseur du substrat pendant le processus de nettoyage. Grâce à la collecte de données en temps réel, le système peut déterminer si un enlèvement de matière excessif a eu lieu, émettre des avertissements à temps et ajuster les paramètres laser. Par exemple, le brevet chinois CN112044874A propose un système de nettoyage laser en temps réel associé à un retour d'information par ultrasons pour prévenir les dommages structurels causés par un nettoyage excessif.
- Rétroaction optique : La tomographie par cohérence optique (OCT) offre une imagerie tridimensionnelle haute résolution de la zone de nettoyage, permettant d'identifier avec précision si les contaminants sont complètement éliminés et si la surface du substrat est endommagée. Comparée aux systèmes visuels traditionnels, l'OCT offre une meilleure pénétration et une plus grande précision, ce qui la rend particulièrement adaptée à l'évaluation de l'efficacité du nettoyage des surfaces de haute précision ou multicouches.
En intégrant un contrôle précis des paramètres laser à des technologies avancées, le risque d'endommagement du substrat lors du nettoyage par laser pulsé peut être considérablement réduit. Ces stratégies sont particulièrement cruciales dans les applications où l'intégrité de surface est primordiale, comme l'aéronautique, la fabrication de semi-conducteurs et la restauration du patrimoine culturel. Une mise en œuvre adéquate améliore non seulement les performances de nettoyage, mais contribue également à la durabilité et à la sécurité des matériaux à long terme.
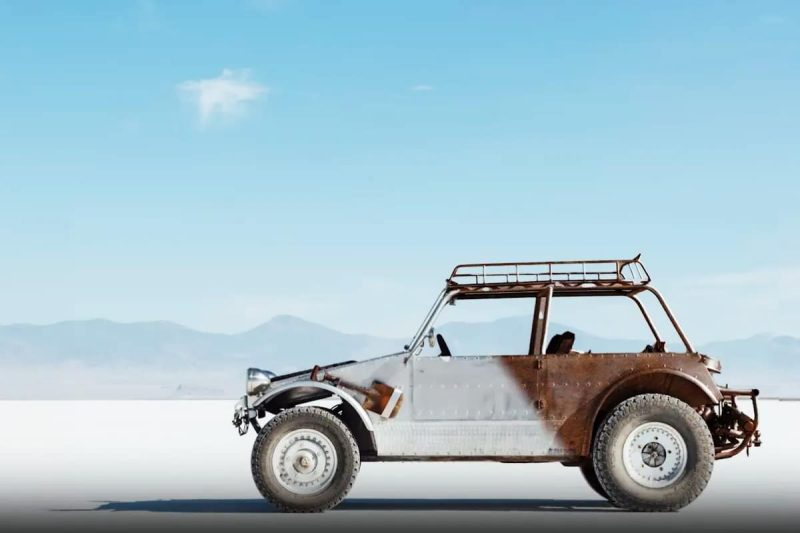
Études de cas et applications
Le nettoyage laser pulsé, grâce à sa nature sans contact, sa haute sélectivité et son fonctionnement sans consommable, est utilisé avec succès dans diverses industries haut de gamme. Ces applications concrètes démontrent la fiabilité et la valeur industrielle de cette technologie pour la gestion de traitements de surface complexes.
Industrie des semi-conducteurs
Dans la fabrication de semi-conducteurs, même une contamination par des particules de l'ordre du micron peut dégrader les performances des puces ou provoquer des pannes de production. Les méthodes de nettoyage traditionnelles peuvent introduire de l'électricité statique ou endommager la surface des plaquettes lors du retrait des particules. Le nettoyage par laser pulsé, notamment avec des impulsions laser femtosecondes (par exemple, 233 fs), utilise des micro-ondes de choc induites par laser pour éliminer avec précision les contaminants des substrats en verre, pratiquement sans impact thermique à l'échelle microscopique. Cette méthode de nettoyage de haute précision et peu dommageable devient progressivement un procédé clé sur les lignes de production de puces avancées.
Industrie automobile
Pour la maintenance des moteurs, la rénovation des aubes de turbine et l'entretien des systèmes hydrauliques, l'élimination efficace de la rouille et des contaminants lourds est cruciale. Le nettoyage par laser pulsé offre un fort couplage énergétique aux couches de contamination des surfaces métalliques, permettant un décapage précis sans affecter la précision dimensionnelle ni l'intégrité de surface des composants critiques. Sa grande répétabilité et sa facilité d'automatisation en font un choix idéal pour les lignes de production industrielles modernes, prolongeant efficacement la durée de vie des pièces et améliorant la fiabilité des équipements.
Conservation du patrimoine culturel
Le nettoyage des objets et bâtiments historiques exige un traitement extrêmement délicat : éliminer les contaminants en profondeur sans endommager le matériau d'origine. La technologie laser pulsé ultrarapide permet un nettoyage en douceur de matériaux tels que la pierre, le métal et la céramique. Elle est couramment utilisée pour éliminer les biofilms, les salissures environnementales et les produits de corrosion. Comparées au nettoyage chimique ou mécanique, les méthodes laser évitent la pollution secondaire et l'abrasion physique et sont largement utilisées dans les musées, les laboratoires de restauration et les projets de conservation du patrimoine du monde entier.
De l'électronique de précision à l'industrie lourde en passant par la préservation du patrimoine culturel, le nettoyage par laser pulsé s'est avéré être une solution de nettoyage moderne hautement efficace, sûre et contrôlable. Avec l'évolution continue de la technologie laser et des systèmes de contrôle intelligents, son champ d'application va encore s'élargir, permettant aux processus de nettoyage de surfaces de tous les secteurs d'activité de répondre à des normes toujours plus strictes.
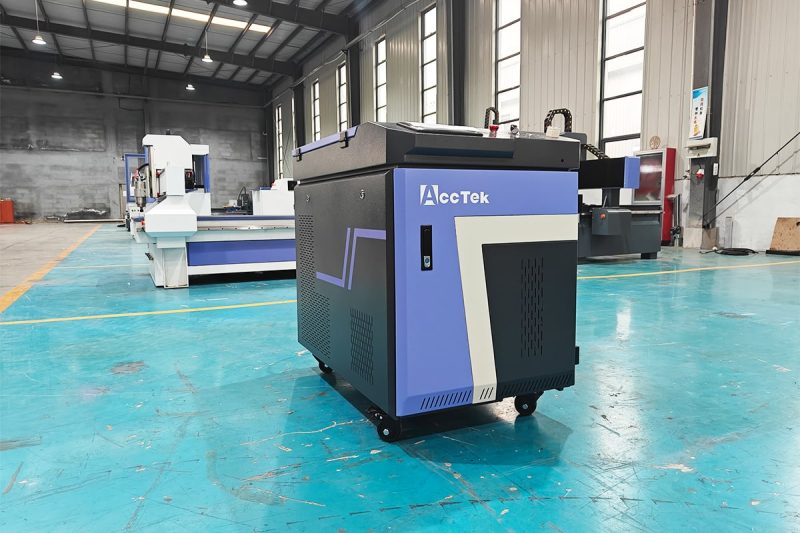
Défis et limites
Malgré les avantages du nettoyage par laser pulsé, tels que le fonctionnement sans contact, la haute précision et le respect de l'environnement, la technologie est encore confrontée à plusieurs défis dans sa mise en œuvre pratique et son adoption plus large dans tous les secteurs :
Coût : Les systèmes de nettoyage laser impliquent généralement des générateurs laser haute performance, des unités de contrôle de précision et des systèmes de refroidissement, et leur investissement initial est relativement important. Pour les PME, le coût d'acquisition et de maintenance à long terme peut constituer le principal obstacle à la promotion. Parallèlement, certains systèmes haut de gamme, tels que les générateurs laser femtoseconde ou picoseconde, présentent des coûts d'équipement et de maintenance plus élevés, et le retour sur investissement doit être évalué.
Compatibilité des matériaux : Certains matériaux à forte réflectivité (comme l'aluminium ou le cuivre) ou à forte transparence (comme le verre ou le plastique) absorbent mal l'énergie laser, ce qui réduit l'efficacité du nettoyage, voire l'empêche de fonctionner. De plus, la longueur d'onde du laser doit être parfaitement adaptée aux caractéristiques d'absorption optique du matériau cible, une exigence particulièrement complexe lors du nettoyage de surfaces composites multi-matériaux.
Bien que des défis financiers et techniques subsistent, le nettoyage par laser pulsé continue de s'imposer comme une solution fiable et avancée pour les applications industrielles haut de gamme. Grâce aux progrès constants en matière de miniaturisation des équipements, de réduction des coûts et de systèmes d'exploitation intelligents, ces limitations devraient s'atténuer avec le temps, ouvrant la voie à une adoption plus large dans divers environnements industriels.
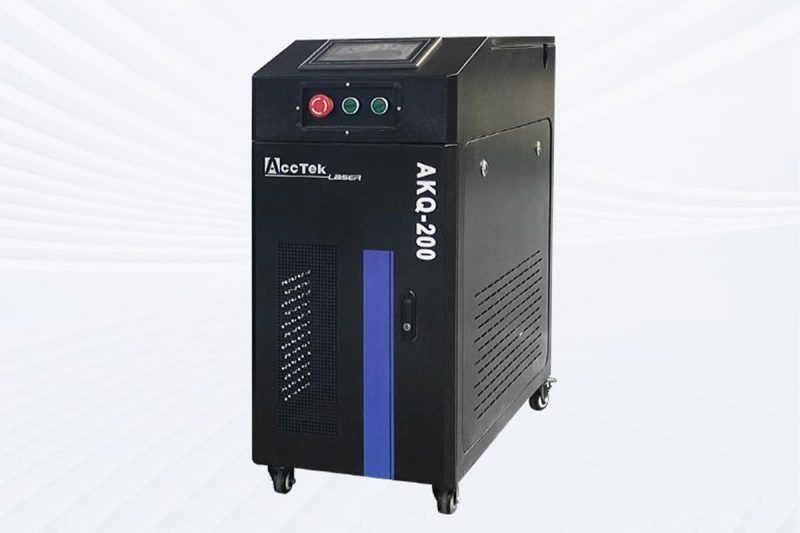
Résumé
La technologie de nettoyage par laser pulsé, avec ses avantages sans contact, sa haute précision et son respect de l'environnement, a démontré un vaste potentiel d'application dans les industries modernes. Grâce à un contrôle précis des paramètres laser tels que la durée, l'énergie et la longueur d'onde de l'impulsion, et à la mise en œuvre de systèmes de surveillance et de rétroaction avancés, cette technologie permet d'éliminer efficacement les contaminants de surface tout en minimisant les dommages au substrat, garantissant ainsi efficacité et sécurité pendant le processus de nettoyage. Ses applications réussies dans des secteurs haut de gamme tels que les semi-conducteurs, l'automobile, l'aérospatiale et la préservation du patrimoine culturel confirment son formidable potentiel et sa fiabilité technique.
Cependant, malgré les résultats positifs obtenus par la technologie de nettoyage par laser pulsé dans de nombreux secteurs, les entreprises doivent encore prendre en compte des facteurs tels que le coût, la complexité opérationnelle et la compatibilité des matériaux avant d'envisager son adoption. L'investissement initial dans un équipement de nettoyage laser est relativement élevé, et les opérateurs doivent suivre une formation technique professionnelle pour garantir le bon fonctionnement du système. De plus, certains matériaux à haute réflectivité ou transparents peuvent nécessiter des longueurs d'onde laser et des paramètres spécifiques. Par conséquent, les entreprises doivent procéder à une évaluation complète de chaque application afin de garantir des résultats de nettoyage optimaux et de minimiser les dommages au substrat.
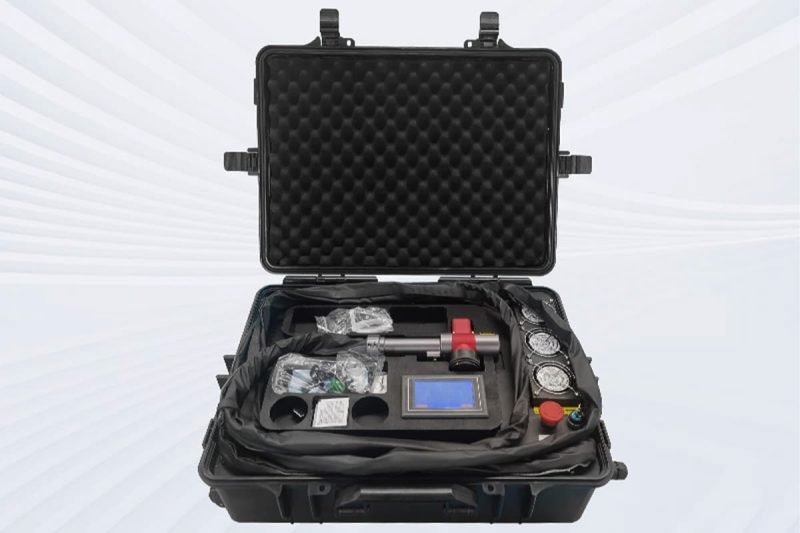
Obtention d'une solution laser
En tant que fabricant leader d'équipements laser, Laser AccTek s'engage à fournir des services de haute qualité machines de nettoyage au laser pulsé Pour aider nos clients à obtenir des résultats de nettoyage efficaces et sûrs et répondre à divers besoins de nettoyage industriel. Qu'il s'agisse de nettoyer des appareils électroniques de précision, l'industrie lourde ou le patrimoine culturel, nous proposons à nos clients des solutions laser personnalisées pour répondre à divers défis de nettoyage.
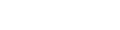
Coordonnées
- [email protected]
- [email protected]
- +86-19963414011
- No. 3 Zone A, zone industrielle de Lunzhen, ville de Yucheng, province du Shandong.
Obtenez des solutions laser