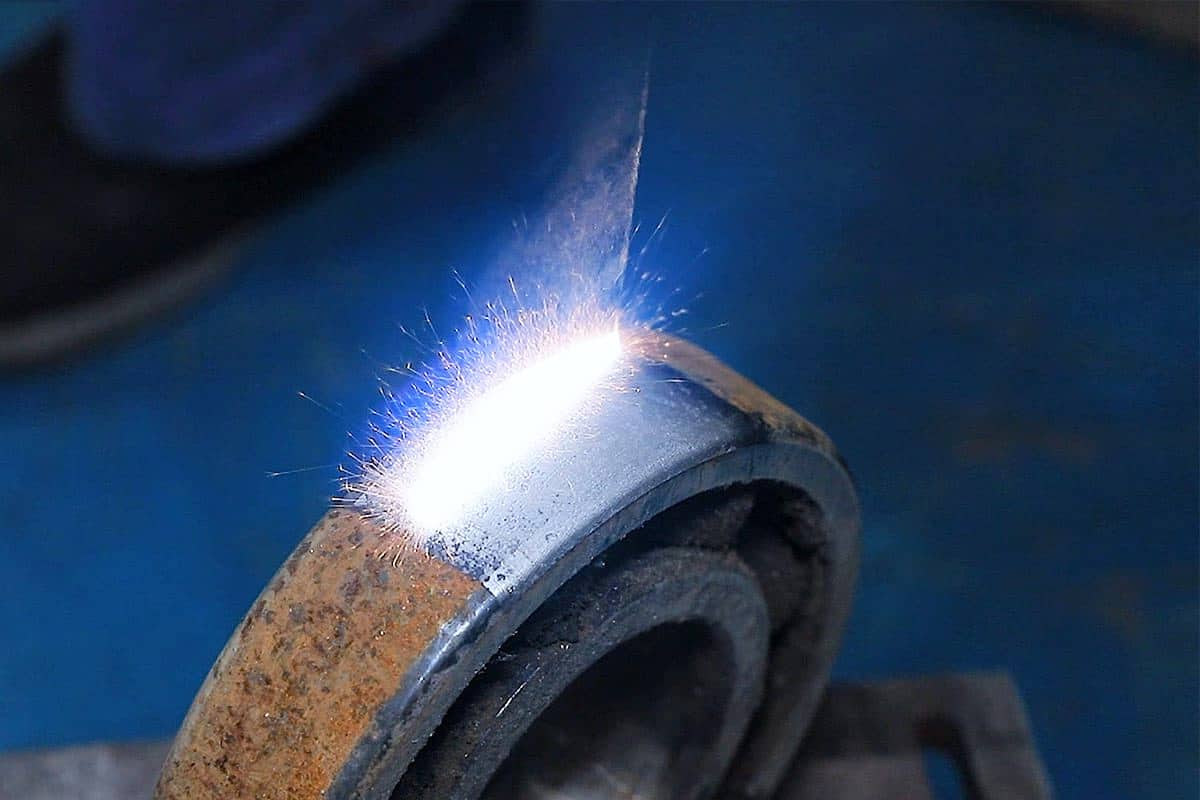
La pulizia laser pulsata danneggia il substrato?
La pulizia laser pulsata ha guadagnato ampia popolarità in applicazioni come la preparazione laser delle superfici e la rimozione della ruggine con laser a fibra, grazie alla sua elevata efficienza, al rispetto dell'ambiente e alla sua natura senza contatto. Tuttavia, permane una preoccupazione critica per molti utenti: questa tecnologia può danneggiare il substrato?
Questo articolo esplora i fondamenti della pulizia laser pulsata, esaminando i potenziali effetti termici, meccanici e fotochimici che potrebbero causare danni al substrato in base a diverse impostazioni dei parametri. Esamineremo anche i principali fattori di influenza, come la conduttività termica e il tasso di assorbimento del materiale, e introdurremo strategie pratiche, come l'ottimizzazione dei parametri, il controllo multi-impulso e il monitoraggio della temperatura in tempo reale, per ridurre al minimo i rischi.
Sommario
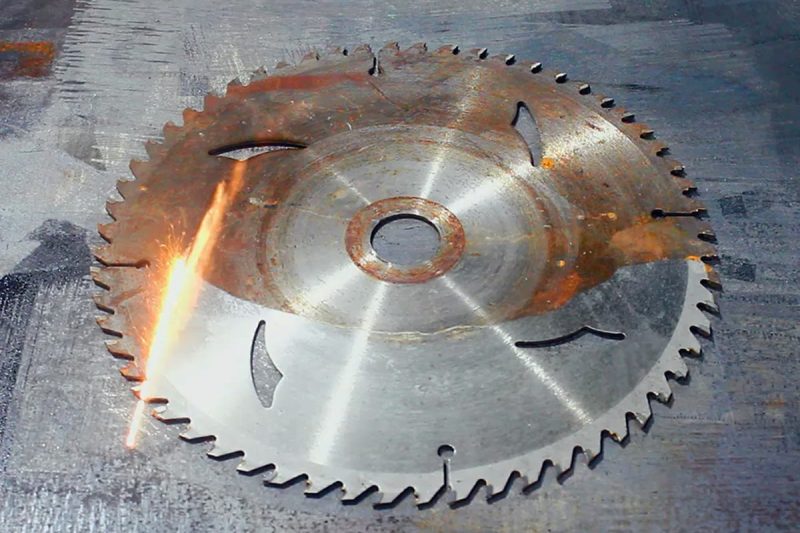
Comprensione della pulizia laser pulsata
La pulizia laser pulsata è una tecnologia di trattamento superficiale efficiente, ecologica e senza contatto, ampiamente utilizzata in applicazioni come la rimozione laser della ruggine, la rimozione della vernice, la pulizia degli strati di ossido e la preparazione laser delle superfici per stampi di precisione e componenti elettronici. Il principio di base prevede impulsi laser ad alta energia che vaporizzano o rimuovono rapidamente i contaminanti dal substrato senza causare effetti termici significativi o danni meccanici al materiale.
Nelle applicazioni pratiche, la comprensione e l'ottimizzazione dei seguenti parametri chiave sono essenziali per migliorare l'efficienza della pulizia e garantire la sicurezza del substrato:
- Durata dell'impulso: si riferisce alla durata di un singolo impulso laser, tipicamente nell'ordine dei nanosecondi, dei picosecondi o persino dei femtosecondi. Impulsi più brevi contribuiscono a ridurre la zona termicamente alterata (ZTA), rendendoli ideali per la pulizia di precisione di materiali sensibili al calore.
- Energia dell'impulso: rappresenta l'energia trasportata da ciascun impulso laser, che influisce direttamente sulla capacità di pulizia. Un'energia dell'impulso più elevata è efficace per rimuovere contaminanti ostinati, ma deve essere attentamente controllata per evitare danni al substrato.
- Frequenza di ripetizione: si riferisce alla frequenza degli impulsi laser emessi per unità di tempo. Una frequenza di ripetizione più elevata può aumentare la velocità di pulizia, ma, se non adeguatamente controllata, può causare accumulo di calore e causare danni termici.
- Lunghezza d'onda: la lunghezza d'onda del laser determina la sua interazione con i diversi materiali. Ad esempio, i metalli rispondono in genere meglio a una lunghezza d'onda laser di 1064 nm.
- Profilo del fascio: si riferisce alla distribuzione dell'energia del raggio laser nello spazio. Un profilo del fascio ideale dovrebbe avere una distribuzione uniforme dell'energia, garantendo una pulizia stabile ed efficiente ed evitando surriscaldamenti localizzati o una pulizia non uniforme.
In applicazioni quali la rimozione della ruggine tramite laser, la pulizia laser degli stampi o altri usi industriali, la corretta configurazione di questi parametri non solo migliora l'efficienza, ma protegge anche il materiale, il che lo rende un fattore cruciale per ottenere una pulizia laser pulsata di alta qualità.
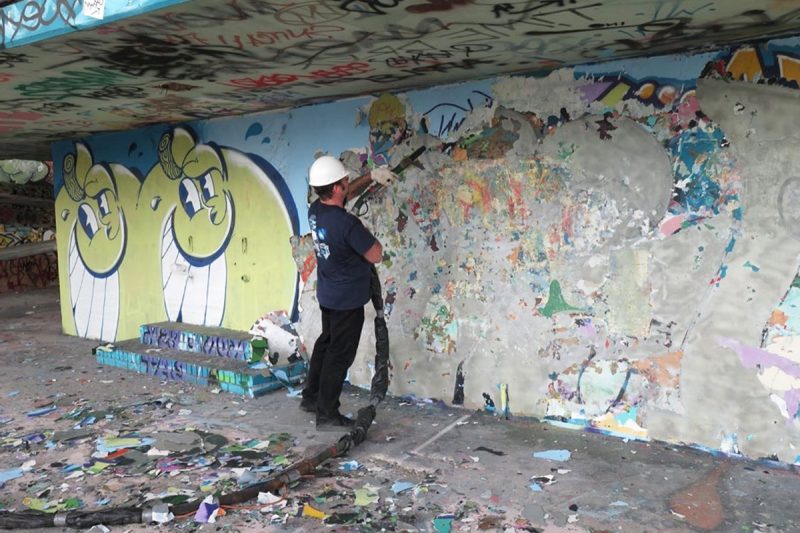
Meccanismi di danno al substrato
Durante il processo di pulizia laser pulsata, i substrati possono essere influenzati da diversi meccanismi, tra cui effetti termici, meccanici ed effetti fotochimici. Sebbene la tecnologia di pulizia laser pulsata offra elevata efficienza e vantaggi ambientali, questi effetti possono danneggiare il substrato in determinate condizioni. Di seguito sono riportati i meccanismi di danneggiamento specifici:
Effetti termici
- Fusione: gli impulsi laser ad alta energia possono riscaldare localmente il substrato a temperature superiori al punto di fusione, causandone la fusione localizzata. Questo fenomeno è particolarmente comune durante la pulizia di superfici metalliche o rivestimenti. Se l'energia laser è troppo elevata, può verificarsi una fusione localizzata.
- Stress termico: il riscaldamento e il raffreddamento rapidi durante il processo di pulizia laser possono causare un'espansione termica irregolare, generando stress interni nel materiale. Questi stress possono causare crepe o deformazioni, soprattutto su materiali sensibili al calore o con pareti sottili.
- Zona termicamente alterata (ZTA): la microstruttura e le proprietà meccaniche del substrato nella zona termicamente alterata (ZTA) possono variare. Questa variazione può ridurre la resistenza meccanica e la durata del substrato, in particolare nei metalli e nelle leghe, dove la ZTA può portare a una riduzione delle prestazioni del materiale.
Effetti meccanici
- Onde d'urto: l'espansione del plasma indotta dal laser genera onde d'urto, che possono causare danni meccanici alla superficie del substrato. Ciò è particolarmente vero per materiali fragili o fini, dove le onde d'urto possono causare crepe superficiali o scheggiature del materiale.
- Pressione di vaporizzazione: la rapida vaporizzazione dei contaminanti genera un'elevata pressione, che può essere trasferita alla superficie del substrato, applicando un carico meccanico aggiuntivo. Se il processo di pulizia è troppo rapido o l'energia utilizzata è troppo elevata, si possono verificare danni localizzati o deformazioni del substrato.
Effetti fotochimici
- Cambiamenti chimici superficiali: i fotoni ad alta energia del laser possono interagire con la superficie del substrato, causando reazioni chimiche che ne alterano le proprietà superficiali. Ad esempio, alcuni processi di pulizia laser possono innescare ossidazione o altre reazioni chimiche, modificando la struttura superficiale e la composizione chimica del substrato.
- Contaminazione: la rimozione incompleta dei contaminanti durante la pulizia può causare il ridepositamento di materiali residui sulla superficie del substrato, causando nuova contaminazione. Ciò può influire negativamente sulle prestazioni del substrato e avere effetti negativi a lungo termine sul suo utilizzo.
Sebbene la pulizia laser pulsata offra un metodo altamente efficiente per la rimozione dei contaminanti superficiali, è fondamentale controllare attentamente i parametri laser, come l'energia dell'impulso, la durata e la frequenza di ripetizione, per evitare che gli effetti termici, meccanici e fotochimici sopra menzionati danneggino il substrato. Una corretta configurazione dei parametri laser e un controllo preciso sono essenziali per garantire sia la sicurezza che l'efficienza del processo di pulizia.
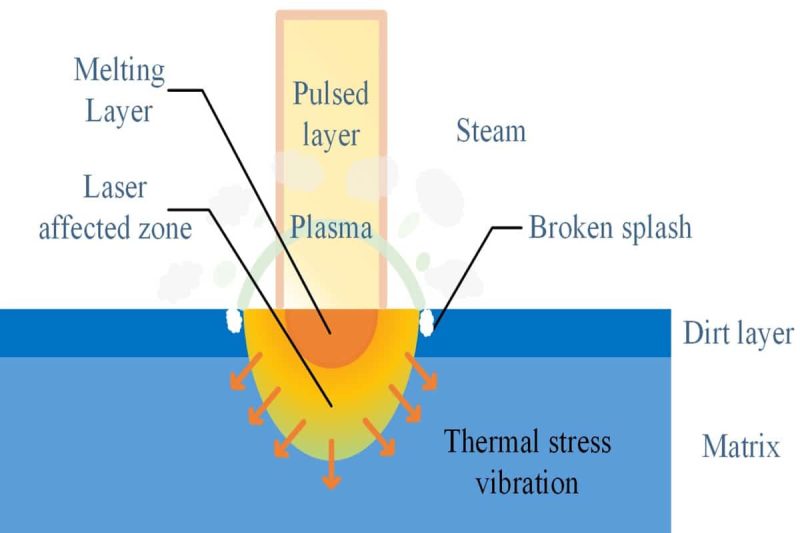
Fattori che influenzano il danno al substrato
Durante la pulizia laser pulsata, diversi fattori influenzano il grado di danno che può verificarsi al substrato. Comprendere e ottimizzare questi fattori è fondamentale per garantire sia un'efficace rimozione dei contaminanti che la protezione del substrato. Di seguito sono riportati i principali fattori che influenzano il processo:
Proprietà dei materiali
- Conduttività termica: i materiali con elevata conduttività termica possono dissipare il calore in modo più efficiente, riducendo il rischio di accumulo termico e danni. Ad esempio, metalli come rame e alluminio sono meno soggetti a degradazione termica durante la pulizia laser grazie alla loro superiore dissipazione del calore.
- Coefficiente di assorbimento: il coefficiente di assorbimento determina la quantità di energia laser che un materiale può assorbire a una specifica lunghezza d'onda. Un tasso di assorbimento più elevato si traduce in un riscaldamento più rapido della superficie, rendendo essenziale il controllo preciso della lunghezza d'onda e della potenza del laser per una pulizia sicura.
- Punto di fusione: i materiali con punti di fusione più bassi sono più suscettibili alla fusione in caso di esposizione laser ad alta energia. La scelta di parametri di pulizia adeguati è essenziale quando si lavora con substrati sensibili al calore come materie plastiche o leghe a basso punto di fusione.
- Resistenza meccanica: una maggiore resistenza meccanica aiuta un materiale a resistere ai danni causati da onde d'urto o stress termico. I substrati più resistenti hanno meno probabilità di subire crepe o deformazioni durante la pulizia laser pulsata ad alta frequenza.
- Composizione chimica: la stabilità chimica del substrato influenza la sua suscettibilità alle reazioni fotochimiche. Alcuni materiali possono subire alterazioni chimiche superficiali se esposti a fotoni ad alta energia, il che potrebbe influire negativamente sulle loro prestazioni.
Parametri laser
- Durata dell'impulso: la durata di ogni impulso laser influenza direttamente il modo in cui il calore viene trasferito al substrato. Gli impulsi ultrabrevi (ad esempio, i laser a femtosecondi) possono ridurre significativamente la zona termicamente alterata (HAZ), riducendo il rischio di danni termici, soprattutto in componenti delicati o di precisione.
- Energia dell'impulso: la corretta regolazione dell'energia dell'impulso è fondamentale. È necessaria un'energia sufficiente per rimuovere i contaminanti, ma un'energia eccessiva può causare la fusione o l'ablazione del substrato. L'ottimizzazione di questo parametro garantisce una pulizia efficiente e sicura.
- Frequenza di ripetizione: un'elevata frequenza di ripetizione aumenta il rischio di accumulo di calore. Per evitare l'accumulo termico e potenziali danni al substrato, la frequenza deve essere regolata in base alla tolleranza al calore e alla conduttività del materiale.
- Lunghezza d'onda: la scelta di una lunghezza d'onda laser che corrisponda alle caratteristiche di assorbimento sia dei contaminanti che del substrato migliora l'efficienza di pulizia e riduce i danni. Questa è una strategia fondamentale per ottimizzare la preparazione laser delle superfici.
Condizioni ambientali
- Temperatura ambiente: temperature ambientali elevate possono aumentare la temperatura iniziale del substrato, aumentando il rischio di surriscaldamento durante il processo di pulizia. Il controllo della temperatura potrebbe essere necessario per applicazioni sensibili.
- Umidità: un'umidità elevata può causare la formazione di condensa sulla superficie del substrato, alterando il modo in cui il laser interagisce con il materiale. Ciò può causare ulteriori effetti termici o chimici, compromettendo potenzialmente le prestazioni di pulizia.
- Condizioni della superficie: la rugosità superficiale e il tipo di contaminanti presenti influenzano l'esito del processo di pulizia. Superfici irregolari o contaminanti stratificati possono causare una distribuzione non uniforme dell'energia, compromettendo sia l'efficacia della pulizia che la sicurezza del substrato.
Il successo della pulizia laser pulsata e il suo impatto sul substrato dipendono non solo dal sistema laser in sé, ma anche dalle proprietà fisiche e chimiche del materiale, dalle condizioni ambientali e dallo stato della superficie. Per ridurre al minimo i danni al substrato e massimizzare l'efficienza della pulizia, è essenziale valutare attentamente questi fattori e regolare di conseguenza i parametri laser.
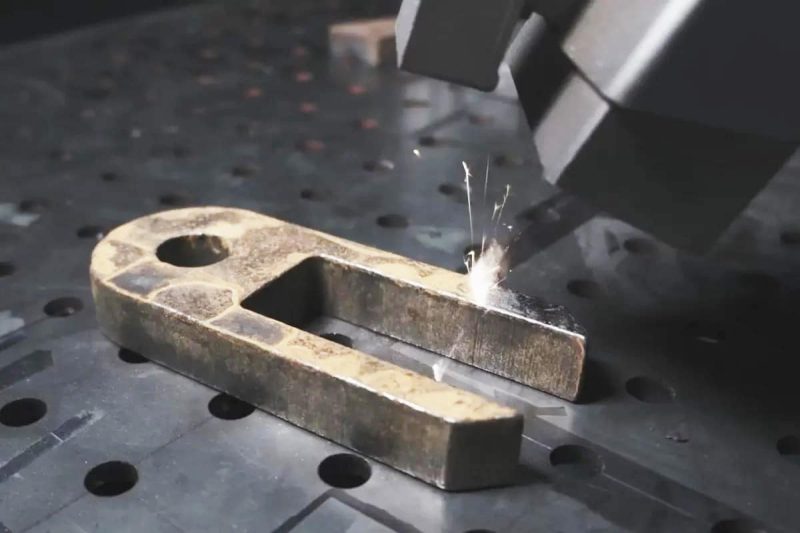
Strategie per minimizzare i danni al substrato
Sebbene la pulizia laser pulsata offra una soluzione precisa e senza contatto per la rimozione dei contaminanti, un'impostazione errata dei parametri può comunque causare danni irreversibili al substrato sottostante. Per garantire una pulizia efficace preservando l'integrità del materiale, è necessario applicare una combinazione di ottimizzazione dei parametri e tecniche avanzate.
Ottimizzazione dei parametri
- Regolazione della durata dell'impulso: l'utilizzo di impulsi ultrabrevi, come i laser a femtosecondi, limita significativamente la zona di diffusione termica, riducendo al minimo le dimensioni della zona termicamente alterata (HAZ) e riducendo i rischi di danni termici.
- Controllo dell'energia degli impulsi: impostando l'energia degli impulsi al minimo necessario per la rimozione dei contaminanti si evita il riscaldamento eccessivo o la fusione della superficie del substrato, fattore fondamentale per i materiali delicati.
- Gestione della frequenza di ripetizione: una frequenza di ripetizione attentamente selezionata garantisce un tempo di raffreddamento adeguato tra gli impulsi, contribuendo a prevenire l'accumulo di calore che può causare deformazioni, microfessure o altri problemi al substrato correlati alla temperatura.
- Scelta della lunghezza d'onda corretta: adattare la lunghezza d'onda del laser alle caratteristiche di assorbimento sia del substrato che dei contaminanti migliora la selettività della pulizia, aumenta l'efficienza e riduce al minimo l'esposizione del substrato.
Tecniche avanzate
- Funzionamento in modalità Burst: suddividendo un singolo impulso in una serie di sottoimpulsi, la modalità Burst riduce l'intensità di picco dell'impulso mantenendo inalterata l'energia totale, mitigando così lo stress termico e meccanico sulla superficie.
- Sovrapposizione multiimpulso: la rimozione dei contaminanti in più passaggi mediante impulsi a bassa energia consente un'ablazione graduale del materiale, riducendo significativamente l'impatto sul substrato.
- Modellazione del raggio: l'ottica avanzata è in grado di distribuire l'energia laser in modo più uniforme sull'area bersaglio, prevenendo il surriscaldamento localizzato e garantendo risultati costanti nella preparazione della superficie laser.
Monitoraggio e feedback
- Monitoraggio della temperatura: la temperatura è un fattore chiave che influenza il danno termico. Installando termocamere a infrarossi o sensori a termocoppia nell'area di pulizia, è possibile rilevare in tempo reale l'andamento variabile della temperatura superficiale del substrato. Quando la temperatura è prossima al punto di fusione o al valore critico di stress termico, il sistema può ridurre immediatamente l'energia dell'impulso o la frequenza di ripetizione per prevenire efficacemente la fusione, la deformazione o la criccatura termica del materiale. Questo meccanismo di feedback ha notevolmente migliorato la sicurezza e l'affidabilità della pulizia laser nel campo della produzione di precisione.
- Monitoraggio acustico: la tecnologia di monitoraggio acustico, come i dispositivi di misurazione dello spessore a ultrasuoni, può monitorare efficacemente le variazioni di spessore del substrato durante il processo di pulizia. Raccogliendo dati in tempo reale, il sistema può determinare se si è verificata un'eccessiva rimozione di materiale, emettere avvisi tempestivi e regolare i parametri laser. Ad esempio, il brevetto cinese CN112044874A propone un sistema di pulizia laser in tempo reale combinato con feedback a ultrasuoni per prevenire danni strutturali causati da una pulizia eccessiva.
- Feedback ottico: la tomografia ottica a coerenza di fase (OCT) offre capacità di imaging tridimensionale ad alta risoluzione per l'area di pulizia, consentendo di identificare con precisione se i contaminanti sono stati completamente rimossi e se la superficie del substrato presenta danni. Rispetto ai sistemi visivi tradizionali, l'OCT offre maggiore penetrazione e precisione ed è particolarmente adatta per valutare l'effetto di pulizia di superfici ad alta precisione o con strutture multistrato.
Integrando un controllo preciso dei parametri laser con tecnologie avanzate, è possibile ridurre notevolmente il rischio di danni al substrato durante la pulizia laser pulsata. Queste strategie sono particolarmente importanti nelle applicazioni in cui l'integrità superficiale è fondamentale, come nel settore aerospaziale, nella fabbricazione di semiconduttori e nel restauro dei beni culturali. Un'implementazione corretta non solo migliora le prestazioni di pulizia, ma contribuisce anche alla durata e alla sicurezza dei materiali a lungo termine.
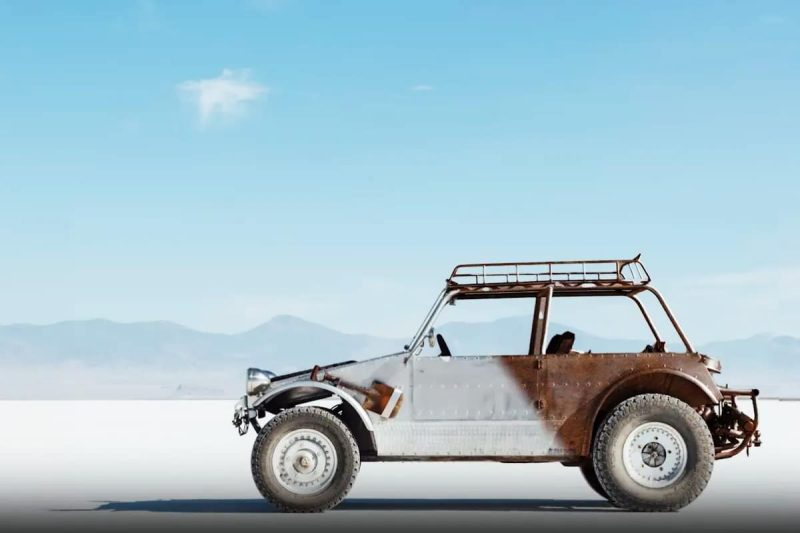
Casi di studio e applicazioni
La pulizia laser pulsata, grazie alla sua natura senza contatto, all'elevata selettività e al funzionamento senza materiali di consumo, è stata applicata con successo in diversi settori industriali di fascia alta. Queste applicazioni concrete dimostrano l'affidabilità e il valore industriale della tecnologia nella gestione di trattamenti superficiali complessi.
industria dei semiconduttori
Nella produzione di semiconduttori, anche la contaminazione da particelle di dimensioni micrometriche può degradare le prestazioni dei chip o causare guasti di produzione. I metodi di pulizia tradizionali possono introdurre elettricità statica o danneggiare la superficie del wafer durante la rimozione delle particelle. La pulizia laser pulsata, in particolare con impulsi laser a femtosecondi (ad esempio, 233 fs), utilizza microonde d'urto indotte dal laser per rimuovere con precisione i contaminanti dai substrati di vetro, praticamente senza alcun impatto termico a livello microscopico. Questo metodo di pulizia ad alta precisione e a basso impatto sta gradualmente diventando un processo chiave nelle linee di produzione di chip avanzate.
Industria automobilistica
Nella manutenzione dei motori, nella rigenerazione delle pale delle turbine e nella manutenzione dei sistemi idraulici, la rimozione efficiente di ruggine e contaminanti pesanti è fondamentale. La pulizia laser pulsata fornisce un forte accoppiamento energetico con gli strati di contaminazione sulle superfici metalliche, consentendo una rimozione precisa senza compromettere la precisione dimensionale o l'integrità superficiale dei componenti critici. L'elevata ripetibilità e la facilità di automazione la rendono la scelta ideale per le moderne linee di produzione industriale, prolungando efficacemente la vita utile dei componenti e migliorando l'affidabilità delle apparecchiature.
Conservazione del patrimonio culturale
La pulitura di manufatti ed edifici storici richiede un trattamento estremamente delicato, che rimuova a fondo i contaminanti senza danneggiare il materiale originale. La tecnologia laser pulsata ultraveloce consente una pulitura "delicata" di materiali come pietra, metallo e ceramica. Viene comunemente utilizzata per rimuovere biofilm, sporco ambientale e prodotti di corrosione. Rispetto alla pulitura chimica o meccanica, i metodi laser evitano l'inquinamento secondario e l'abrasione fisica e sono ampiamente utilizzati in musei, laboratori di restauro e progetti di conservazione del patrimonio culturale in tutto il mondo.
Dall'elettronica di precisione all'industria pesante, fino alla conservazione del patrimonio culturale, la pulizia laser pulsata si è dimostrata una soluzione moderna altamente efficiente, sicura e controllabile. Con la continua evoluzione della tecnologia laser e dei sistemi di controllo intelligenti, il suo ambito di applicazione si espanderà ulteriormente, spingendo i processi di pulizia delle superfici in tutti i settori a soddisfare standard sempre più elevati.
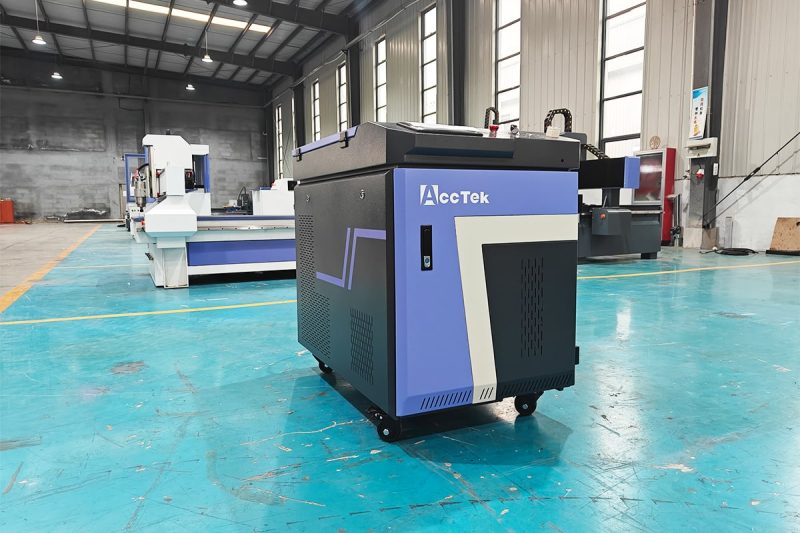
Sfide e limitazioni
Nonostante i vantaggi della pulizia laser pulsata, come il funzionamento senza contatto, l'elevata precisione e il rispetto dell'ambiente, la tecnologia deve ancora affrontare diverse sfide nell'implementazione pratica e nella sua più ampia adozione nei vari settori:
Costo: i sistemi di pulizia laser di solito includono generatori laser ad alte prestazioni, unità di controllo di precisione e sistemi di raffreddamento, e il loro investimento iniziale è relativamente elevato. Per le piccole e medie imprese, il costo di acquisizione e la manutenzione a lungo termine possono rappresentare il principale ostacolo alla promozione. Allo stesso tempo, alcuni sistemi di fascia alta, come i generatori laser a femtosecondi o picosecondi, presentano costi di supporto e manutenzione più elevati, e il ritorno sull'investimento deve essere valutato attentamente.
Compatibilità dei materiali: alcuni materiali ad alta riflettività (come alluminio o rame) o trasparenza (come vetro o plastica) presentano uno scarso assorbimento dell'energia laser, riducendo l'efficacia del processo di pulizia o addirittura compromettendone l'efficacia. Inoltre, la lunghezza d'onda del laser deve essere adattata con precisione alle caratteristiche di assorbimento ottico del materiale target, un requisito particolarmente complesso quando si puliscono superfici composite multimateriale.
Nonostante i costi e le sfide tecniche permangano, la pulizia laser pulsata continua ad affermarsi come una soluzione affidabile e avanzata nelle applicazioni industriali di fascia alta. Grazie ai continui sviluppi nella miniaturizzazione delle apparecchiature, nella riduzione dei costi e nei sistemi operativi intelligenti, si prevede che queste limitazioni si ridurranno nel tempo, aprendo la strada a una più ampia adozione in diversi ambienti industriali.
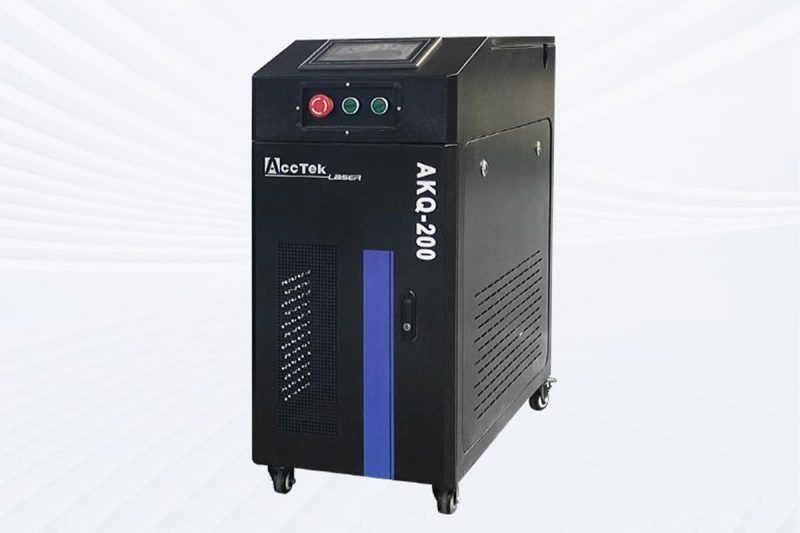
Riepilogo
La tecnologia di pulizia laser pulsata, con i suoi vantaggi senza contatto, ad alta precisione e rispettosa dell'ambiente, ha dimostrato un ampio potenziale applicativo nelle industrie moderne. Grazie al controllo preciso dei parametri laser come durata dell'impulso, energia e lunghezza d'onda, e all'implementazione di sistemi avanzati di monitoraggio e feedback, questa tecnologia è in grado di rimuovere efficacemente i contaminanti superficiali riducendo al minimo i danni al substrato, garantendo efficienza e sicurezza durante il processo di pulizia. Le sue applicazioni di successo in settori di fascia alta come i semiconduttori, l'automotive, l'aerospaziale e la conservazione del patrimonio culturale ne convalidano ulteriormente l'enorme potenziale e l'affidabilità tecnica.
Tuttavia, nonostante i risultati positivi ottenuti dalla tecnologia di pulizia laser pulsata in molti settori, le aziende devono ancora valutare fattori quali costi, complessità operativa e compatibilità dei materiali quando ne valutano l'adozione. L'investimento iniziale in apparecchiature di pulizia laser è relativamente elevato e gli operatori necessitano di una formazione tecnica professionale per garantire l'efficienza del sistema. Inoltre, alcuni materiali altamente riflettenti o trasparenti potrebbero richiedere lunghezze d'onda laser e impostazioni dei parametri specifiche. Pertanto, le aziende devono condurre una valutazione completa per applicazioni specifiche per garantire risultati di pulizia ottimali e danni minimi al substrato.
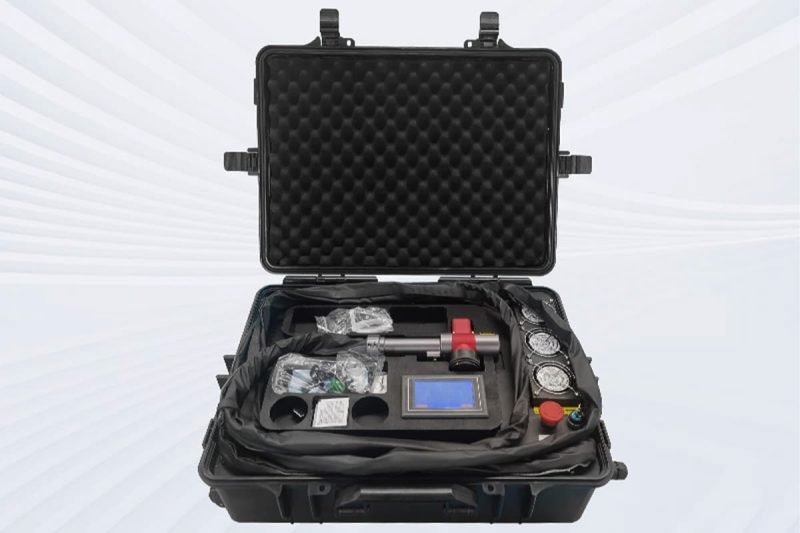
Ottenere la soluzione laser
In qualità di produttore leader di apparecchiature laser, Laser AccTek si impegna a fornire alta qualità macchine per la pulizia laser pulsata Per aiutare i clienti a ottenere risultati di pulizia efficienti e sicuri e a soddisfare le diverse esigenze di pulizia industriale. Che si tratti di pulizia di componenti elettronici di precisione, industria pesante o beni culturali, possiamo fornire ai clienti soluzioni laser personalizzate per affrontare diverse sfide di pulizia.
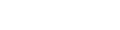
Informazioni sui contatti
- [email protected]
- [email protected]
- +86-19963414011
- N. 3 Zona A, zona industriale di Lunzhen, città di Yucheng, provincia di Shandong.
Ottieni soluzioni laser