ABS Laser Cutting Machine
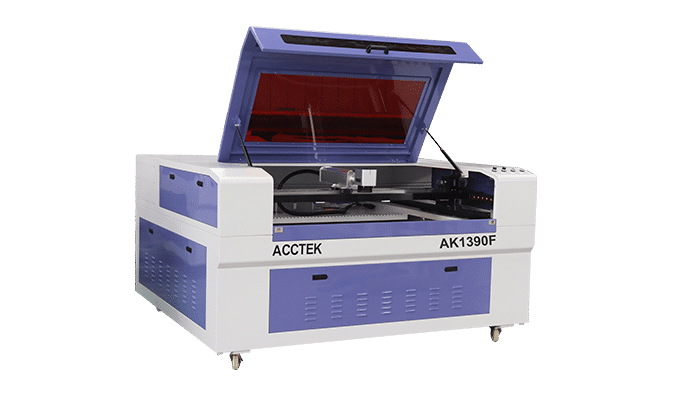
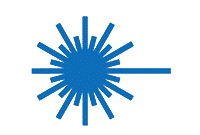
Photoelectric Technology
AccTek Laser focus on designing and manufacturing photoelectric-related system. We provide accurate and exquisite processing quality with leading R&D capability.
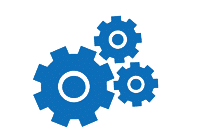
Integration Ability & Experienced
With an experienced, completed, and elite R&D team, customized such as automated, integrated with the robot, system integration, etc. are all available.
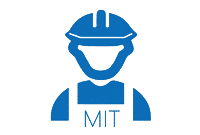
Professional Service
AccTek Laser's laser cutting machine is a professional laser cutting machine designed and manufactured in China. Our elite engineering team provides related service support.
Equipment Features
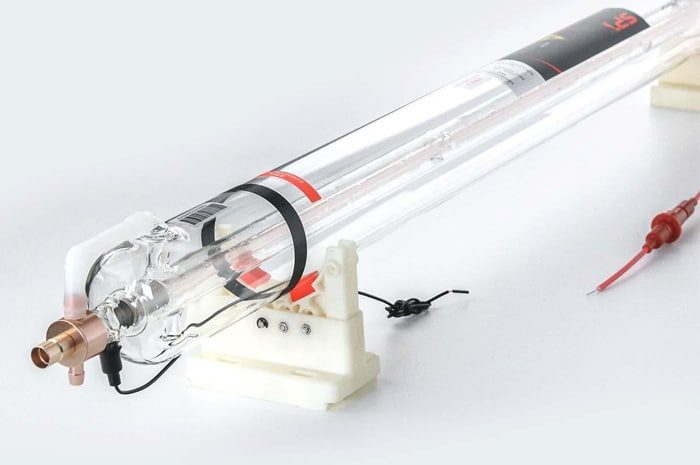
High Power CO2 Laser Tube
The machine is equipped with a powerful CO2 laser tube, which can provide precise and efficient cutting and engraving performance on various materials, including acrylic, wood, leather, fabric, glass, and so on. A high-powered laser tube ensures clean, precise cuts and smooth edges, while also enabling detailed engraving, making it suitable for intricate designs and industrial applications.
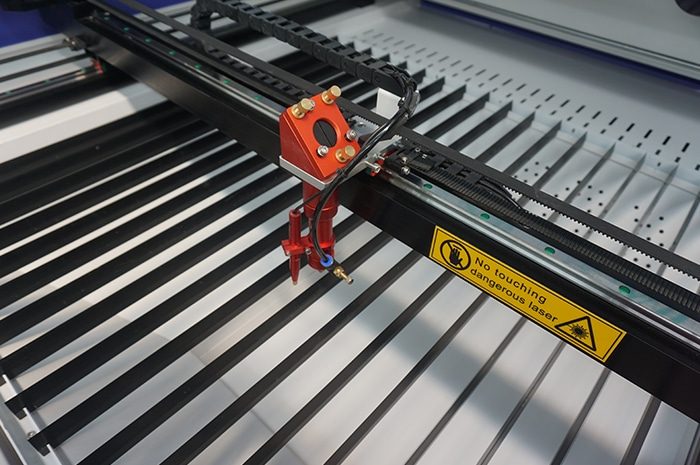
Advanced Motion System
The machine is equipped with an advanced motion system to ensure smooth and accurate movement of the laser head during cutting and engraving. This precise motion control enables clean, sharp cuts while also enabling detailed and intricate engraving on a variety of materials.
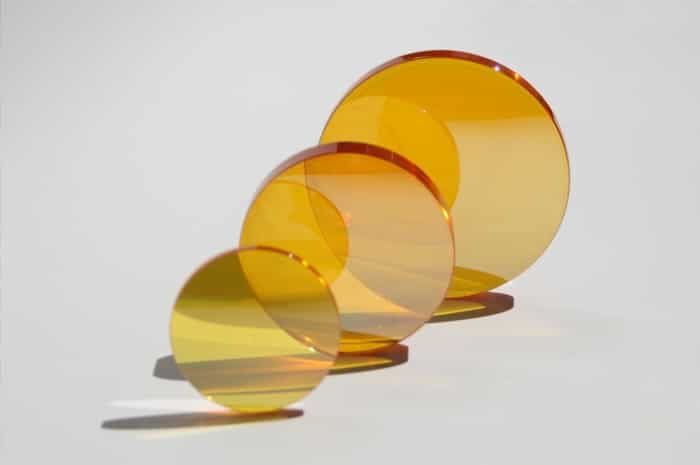
High-Quality Optics
The machine is equipped with high-quality optics capable of producing a narrower, more stable laser beam, ensuring precise cutting paths and cleaner edges even on complex designs and delicate materials. In addition, high-quality optics help reduce beam divergence and losses, thereby improving energy efficiency.
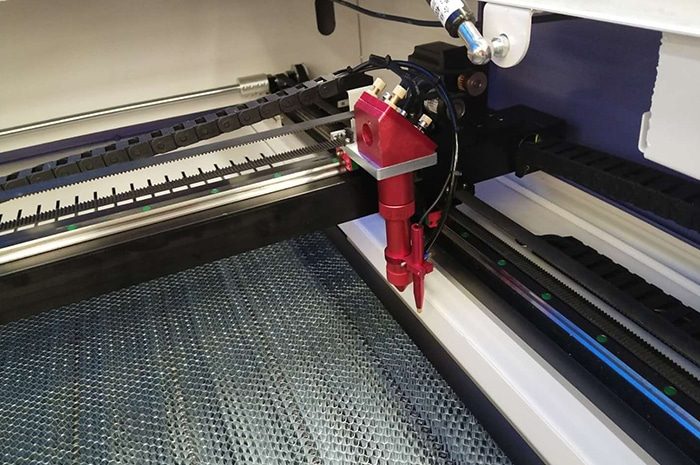
High-Precision CO2 Laser Head
The high-precision CO2 laser head is selected, and it has a red dot positioning function to ensure that the laser beam is precisely aligned with the focusing optics and the nozzle. An accurate laser beam contributes to consistent and uniform cutting results. Additionally, the CO2 laser head is equipped with height control, which ensures consistent focus and compensates for any variations in material thickness or uneven surfaces.
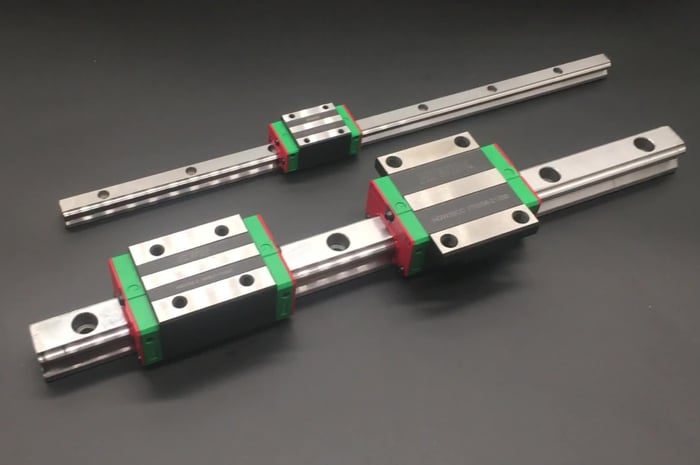
High-Precision HIWIN Rail
The machine is equipped with a Taiwan HIWIN guide rail with excellent precision. HIWIN is manufactured to tight tolerances, ensuring smooth and stable linear motion. This level of precision contributes to accurate and consistent laser cutting, especially when working with intricate designs and fine details. In addition, HIWIN rails are designed to minimize friction, resulting in smooth and quiet movement.
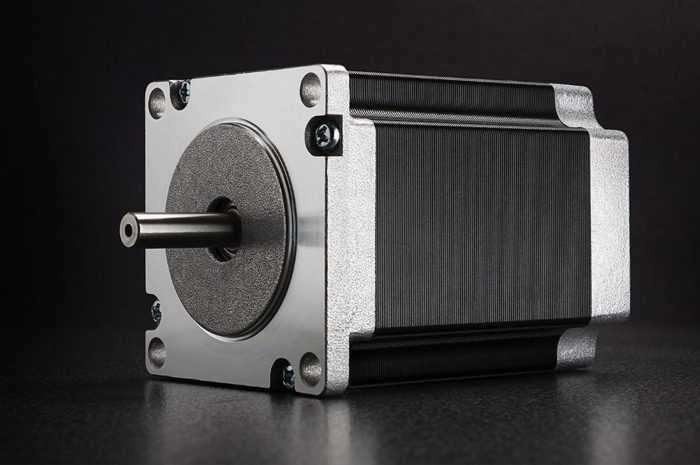
Reliable Stepper Motor
The machine adopts a stepper motor with strong power and reliable performance to ensure the normal operation of the machine. Not only are stepper motors cost-effective, but they also provide precise control of moving parts, ensuring high-quality laser cutting and stable positioning of optical components for reliable, efficient operation.
Technical Specifications
Model | AKJ-6040 | AKJ-6090 | AKJ-1390 | AKJ-1610 | AKJ-1810 | AKJ-1325 | AKJ-1530 |
---|---|---|---|---|---|---|---|
Working Area | 600*400mm | 600*900mm | 1300*900mm | 1600*1000mm | 1800*1000mm | 1300*2500mm | 1500*3000mm |
Laser Medium | CO2 laser | ||||||
Laser Power | 80-300W | ||||||
Power Supply | 220V/50HZ, 110V/60HZ | ||||||
Cutting Speed | 0-20000 mm/min | ||||||
Engraving Speed | 0 - 40000mm/min | ||||||
Min Line Width | ≤0.15mm | ||||||
Position Accuracy | 0.01mm | ||||||
Repetition Accuracy | 0.02mm | ||||||
Cooling System | Water-cooling |
Laser Welding Capacity
Laser Power | Cutting Speed | 3mm | 5mm | 8mm | 10mm | 15mm |
---|---|---|---|---|---|---|
25W | Max Cutting Speed | 15~25mm/s | 8~15mm/s | 3~6mm/s | 1~3mm/s | / |
Optimal Cutting Speed | 10~20mm/s | 5~10mm/s | 2~4mm/s | 0.5~1.5mm/s | / | |
40W | Max Cutting Speed | 20~35mm/s | 10~20mm/s | 4~8mm/s | 2~4mm/s | / |
Optimal Cutting Speed | 15~25mm/s | 8~15mm/s | 3~6mm/s | 1~2.5mm/s | / | |
60W | Max Cutting Speed | 30~50mm/s | 15~30mm/s | 6~12mm/s | 3~6mm/s | / |
Optimal Cutting Speed | 25~40mm/s | 10~20mm/s | 4~8mm/s | 1.5~3.5mm/s | / | |
80W | Max Cutting Speed | 40~70mm/s | 20~40mm/s | 8~16mm/s | 4~8mm/s | / |
Optimal Cutting Speed | 30~50mm/s | 15~30mm/s | 6~12mm/s | 2~4mm/s | / | |
100W | Max Cutting Speed | 50~90mm/s | 25~50mm/s | 10~20mm/s | 5~10mm/s | / |
Optimal Cutting Speed | 40~70mm/s | 20~40mm/s | 8~16mm/s | 3~6mm/s | / | |
130W | Max Cutting Speed | 65~110mm/s | 30~60mm/s | 12~24mm/s | 6~12mm/s | 3~6mm/s |
Optimal Cutting Speed | 50~90mm/s | 25~50mm/s | 10~20mm/s | 4~8mm/s | 1~3mm/s | |
150W | Max Cutting Speed | 75~130mm/s | 35~70mm/s | 14~28mm/s | 7~14mm/s | 3~7mm/s |
Optimal Cutting Speed | 60~100mm/s | 30~60mm/s | 12~24mm/s | 5~10mm/s | 2~4mm/s | |
180W | Max Cutting Speed | 90~150mm/s | 45~90mm/s | 18~36mm/s | 9~18mm/s | 4~9mm/s |
Optimal Cutting Speed | 70~120mm/s | 40~80mm/s | 15~30mm/s | 7~14mm/s | 3~6mm/s | |
200W | Max Cutting Speed | 100~170mm/s | 50~100mm/s | 20~40mm/s | 10~20mm/s | 5~10mm/s |
Optimal Cutting Speed | 80~140mm/s | 45~90mm/s | 18~36mm/s | 8~16mm/s | 4~8mm/s |
Comparison of Different Cutting Methods
Features | Laser Cutting | CNC Routing | Die Cutting | Saw Cutting |
---|---|---|---|---|
Precision | High precision | High precision | Moderate precision | Moderate precision |
Cutting Speed | Fast | Moderate to Fast | Moderate | Moderate |
Heat Affected Zone | Minimal | Moderate | Minimal | High |
Material Thickness Range | Thin to thick | Thin to thick | Thin to medium | Medium to thick |
Edge Quality | Clean and smooth | Clean and smooth | Clean | Rough |
Material Waste | Minimal | Moderate | Moderate | Moderate |
Setup Complexity | Moderate to complex | Moderate to complex | Simple | Simple |
Material Constraints | Versatile | Versatile | Limited by die size | Versatile |
Automation Potential | High potential | High potential | High potential | Limited |
Post-Processing Required | Minimal to none | Minimal | Minimal | Often required |
Tooling Cost | Moderate to high | Moderate to high | Low to moderate | Low to moderate |
Product Features
- The machine is equipped with a high-quality CO2 laser generator, which is very suitable for cutting ABS materials.
- The machine can cut ABS material quickly, which increases productivity.
- The machine provides excellent cutting precision and accuracy, ensuring clean and smooth cuts with minimal material waste.
- The machine can handle ABS sheets of various thicknesses and can also cut other materials such as wood, plastic, and certain metals.
- The laser beam does not physically touch the material, minimizing the risk of material damage or contamination.
- The machine has auto-focus and height adjustment functions to get the best cutting performance on different thicknesses of ABS.
- An intuitive control panel or user interface allows the operator to set cutting parameters, adjust laser power, and control machine motion.
- The machine can be integrated with various design software to realize the seamless transfer of cutting designs.
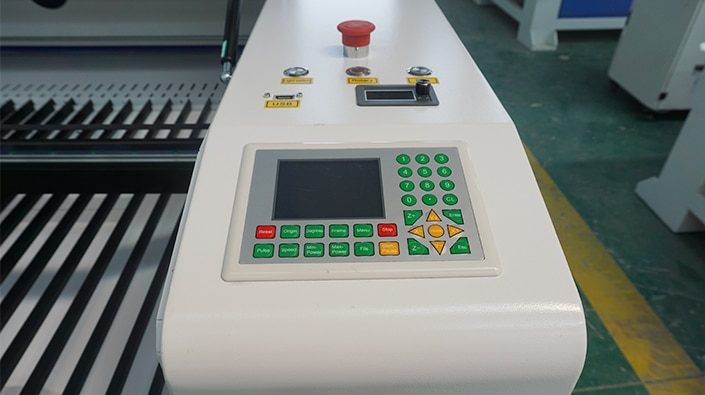
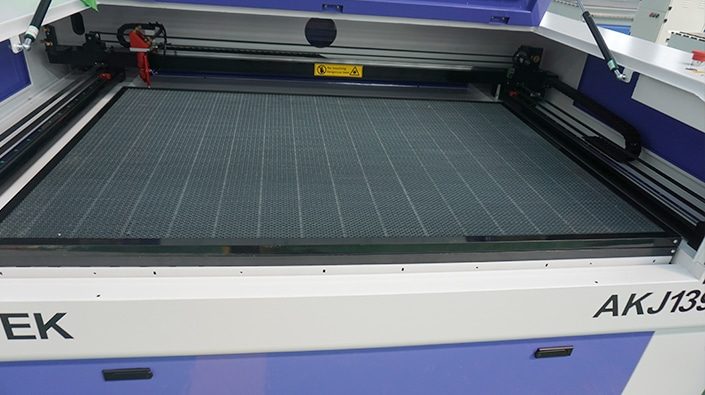
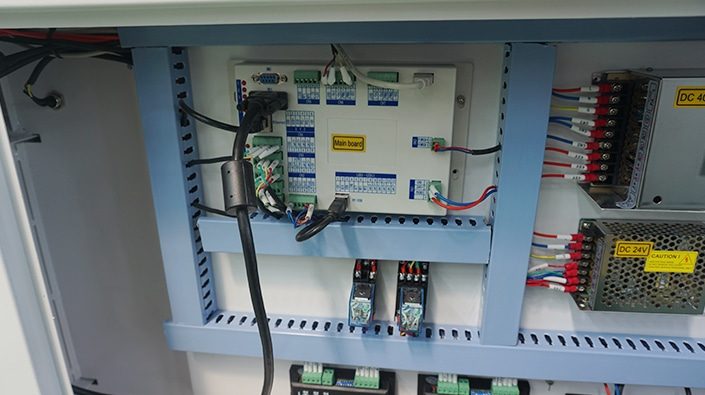
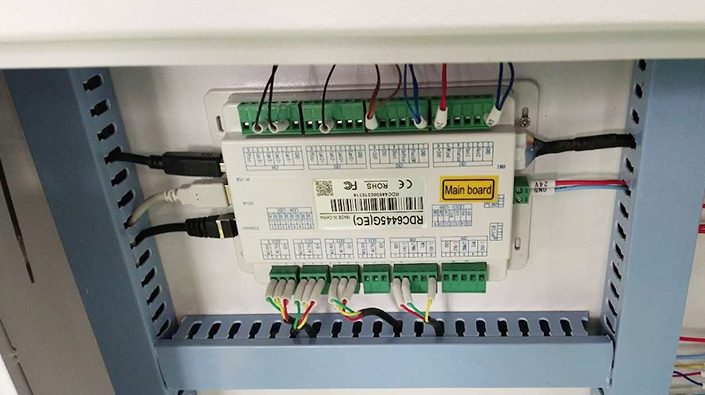
Product Application
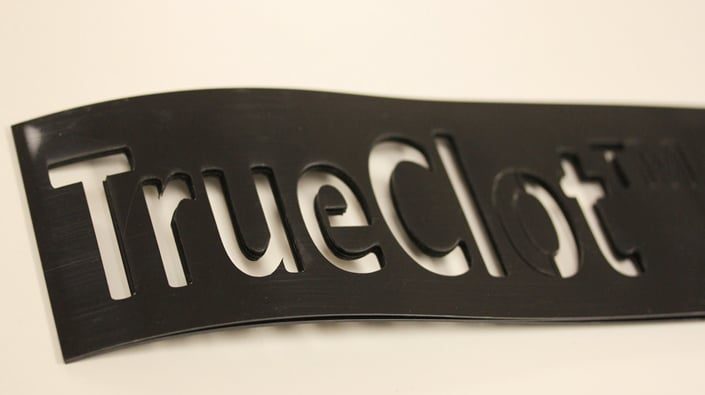
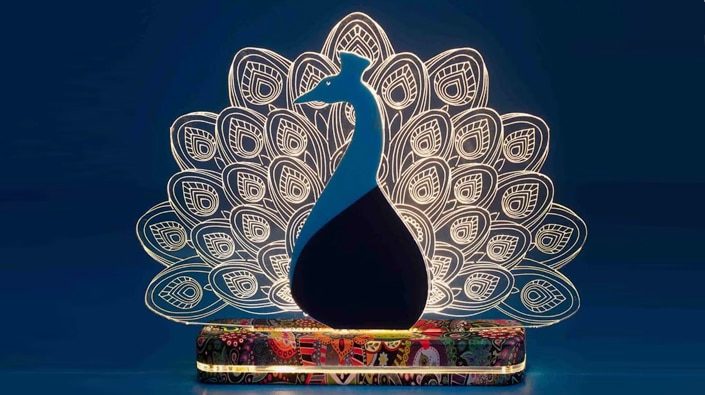
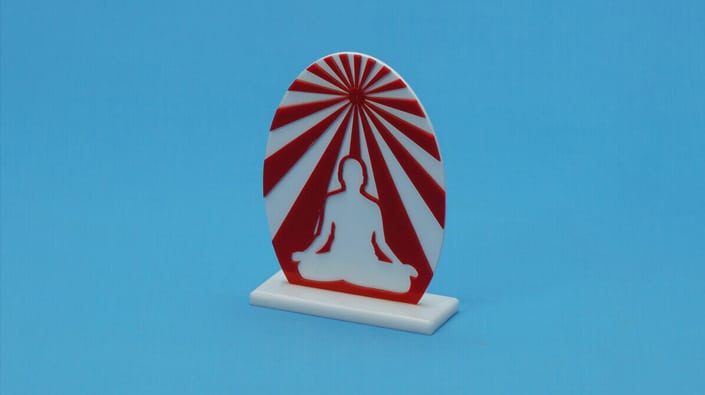
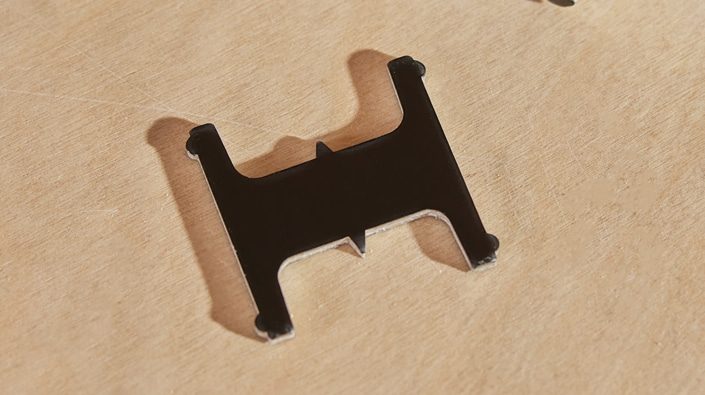
Equipment Selection
High Configuration CO2 Laser Cutting Machine
CO2 Laser Cutting Machine With CCD Camera
CO2 Laser Cutting Machine With Electric Lift Table
Fully Enclosed CO2 Laser Cutting Machine
Double Head CO2 Laser Cutting Machine
CO2 Laser Cutting Machine With Automatic Feeding Device
Large-Size CO2 Laser Cutting Machine
Double Head Large Size CO2 Laser Cutting Machine
Why Choose AccTek?
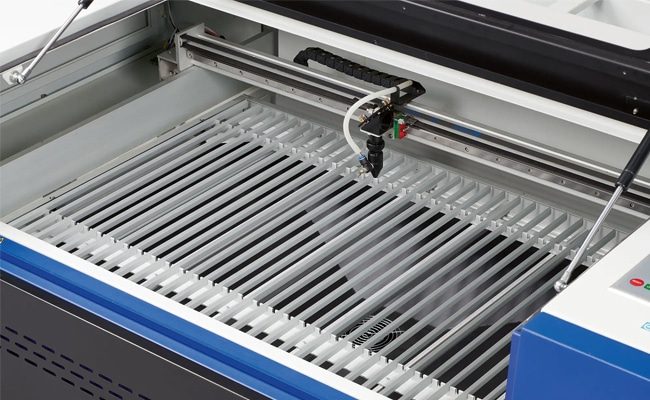
Impeccable Precision
Unrivaled Quality
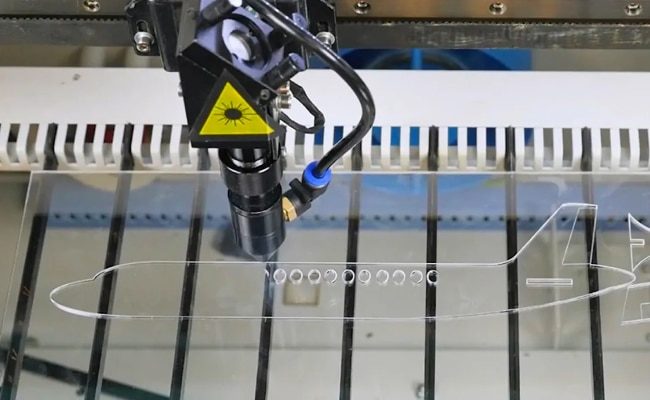
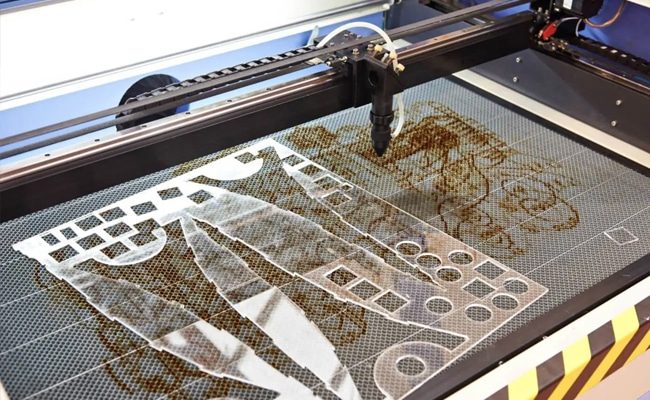
Customized Solutions
Excellent Customer Support
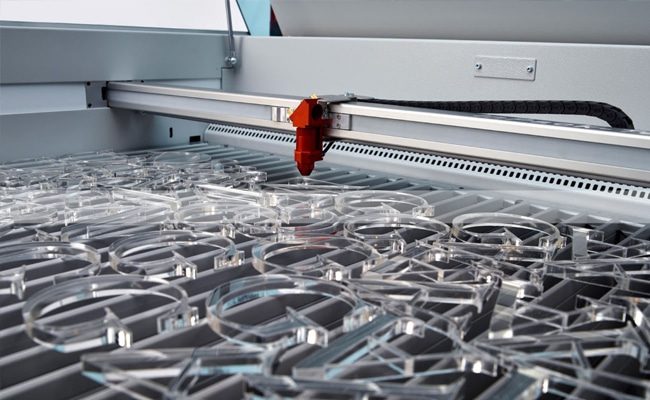
Frequently Asked Questions
- Acrylonitrile: This monomer provides ABS with chemical resistance and hardness. It helps improve the material’s resistance to oil, chemicals, and heat.
- Butadiene: Butadiene gives ABS impact resistance and toughness. This helps the material withstand shocks and shocks without cracking.
- Styrene: Styrene contributes to the rigidity, ease of processing, and surface finish of the material. It also affects the overall appearance and smoothness of the material.
- Ventilation: Lasers release fumes when cutting ABS plastic, which may contain harmful gases and particles. Adequate ventilation helps ensure that these fumes are properly removed from the work area. A well-ventilated space with an exhaust system or smoke extractor can help minimize exposure to fumes.
- Material Composition: Different ABS formulations may contain additives, dyes, or fillers that affect how the material responds to laser cutting. Some additives may emit toxic fumes or have unexpected reactions when exposed to a laser beam. It is recommended to obtain a Material Safety Data Sheet (MSDS) for the specific ABS material being used and to do a small test before cutting larger parts.
- Personal Protective Equipment: Operators and workers should wear appropriate personal protective equipment (PPE), including safety glasses or goggles, to protect eyes from laser radiation and potential debris. Gloves and a lab coat or coverall can help protect the skin.
- Fire Safety: Laser cutting generates heat, which can cause ABS plastic to catch fire if the laser power is too high or the material is not secured properly. Make sure that fire suppression equipment is readily available and that the work area is free of any fire hazards.
- Laser Parameters: Appropriate laser parameters, such as power and speed settings, should be selected to minimize melting, charring, or other undesirable effects during cutting. Optimizing these parameters helps ensure a clean, accurate cut.
- Training: Operators should receive proper training in laser cutting techniques, safety protocols, and emergency procedures. They should be aware of the potential risks associated with laser cutting ABS plastic and know how to respond appropriately.
- Regulations And Guidelines: Depending on your location and industry, there may be regulations or guidelines related to laser cutting and the use of specific materials. Make sure to follow these rules to maintain a safe work environment.
- Work Area Segregation: Keep work spaces clean and tidy to reduce the risk of fire or accidents. Keep flammable materials away from the laser cutter and follow best practices for laser equipment safety.
- Material Preparation: Make sure your ABS material is clean and free of debris, dust, or oil as these can affect cut quality.
- Prepare work area: Install the laser cutter in a well-ventilated area or under a fume extraction system to ensure the removal of potentially harmful fumes.
- Laser Power: Use a laser power setting appropriate for the thickness of the ABS material. Start with a lower power setting and gradually increase until you can achieve a clean cut. Avoid using too much power as it may cause melting or burning.
- Cutting Speed: Adjust the cutting speed to find the best balance between speed and cut quality. Because faster speeds may result in cleaner cuts, it is recommended that you test different speeds to determine the best results for your particular setup.
- Focusing: Correctly focuses the laser beam on the material surface for precise and consistent cuts. An out-of-focus laser can cause uneven or burnt cuts.
- Use Proper Ventilation: Make sure your workspace is well-ventilated to prevent the buildup of smoke and toxic fumes and to maintain good air quality. Consider using a fume extraction system to remove potentially harmful fumes from the cutting process.
- Test Cuts: Between cutting operations, it is recommended to make test cuts on ABS scrap to determine the best laser settings. This helps you find the right balance between cutting speed and laser power.
- Monitor And Adjust: Throughout the laser cutting process, observe cut quality and adjust laser settings as needed.
- Cutting Path: Optimize the cutting path in the design software to achieve the desired shape or pattern, ensuring the path is continuous and smooth to prevent unnecessary stops and starts during the cutting process.
- Post-Cutting Treatment: After the cutting is completed, wait for the workpiece to cool down before processing to avoid deformation or warping due to residual heat. Inspect the workpiece edges and surfaces to ensure a clean cut with no visible burn marks.
- Fire Safety: Be prepared for potential ignition at all times, especially when laser power is set too high. Have fire fighting equipment ready and follow fire safety procedures.
- Personal Protective Equipment (PPE): Wear appropriate personal protective equipment, including goggles, gloves, and respiratory protection, to minimize exposure to fumes and particulate matter.
- Proper Training: Make sure operators are trained in laser safety procedures, machine operation, and material handling techniques.
- Melting Point And Thermal Properties: Compared with PVC, ABS has a lower melting point. This means that when laser cutting ABS, there is a higher chance of localized melting if the laser power or cutting speed is too high. PVC is more heat resistant, which makes it easier to cut without over-melting.
- Fumes And Odors: Lasers release fumes and odors when cutting ABS and PVC. However, the fumes when cutting ABS tend to be more pungent and the smell may be more intense than PVC. Proper ventilation and fume extraction are required when cutting both materials, but more stringent measures may be required when cutting ABS due to its more intense fumes.
- Additives And Ingredients: ABS is generally easier to cut than PVC because it has a lower melting temperature and produces less harmful fumes. But the ease of cutting also depends on the additives, fillers, and specific components of ABS and PVC, because this will affect the material’s response to laser cutting. Certain ABS formulations may contain additives that affect the cutting process, while certain PVC formulations may produce more corrosive or noxious fumes when cut.
- Cutting Speed And Power: Achieving a clean cut depends on finding the right balance of laser power and cutting speed for each material. ABS may require a slightly higher laser power and slower cutting speed to ensure a clean cut, whereas laser-cutting PVC at the same power may cut faster.
- Cut quality: Because ABS has a low melting point, achieving a clean cut of ABS may require more precise laser settings and slower cutting speeds to avoid melting or burning. PVC, on the other hand, has a lower melting point, allowing for faster, cleaner cuts, but the right settings can help avoid charring.
- Safety Considerations: Both materials require similar safety precautions, including proper ventilation, personal protective equipment (PPE), and fire safety measures. The fumes of ABS may be more irritating, but both materials produce potentially harmful by-products during the laser-cutting process.
- Charring: PVC is more prone to charring than ABS during laser cutting. This can affect the quality of the cut edge and may require additional post-processing to achieve the desired finish.
- Optimizing Laser Settings: The laser cutting process involves using a high-intensity laser beam to melt or vaporize the material. If the laser power, speed, and focus settings are not suitable for the specific thickness and type of ABS, excessive heat may be generated, causing localized melting or weakening of the material, which may lead to cracking.
- Material Thickness: Thicker ABS sheets are generally more resistant to cracking than thinner sheets. Thinner sheets are more prone to cracking due to reduced structural integrity. If possible, choose a thicker ABS sheet for laser cutting.
- Use Cooling Technology: Adequate cooling and airflow during laser cutting help dissipate heat and reduce the risk of localized overheating that can lead to cracks. If the material gets too hot and doesn’t have a chance to cool, it can crack more easily.
- Design And Geometry: The shape and complexity of the design being cut can also affect the likelihood of cracking. Sharp corners, tight curves, and intricate details can create points of stress concentration that can lead to cracking.
- Sample Material Testing: Before cutting your final project, it is best to test different laser settings on scrap ABS material to determine the best settings for your particular material and design. This allows you to identify and resolve any issues before they affect the actual project.
- Material Quality: The quality and composition of the ABS material itself can affect its propensity to crack during laser cutting. Higher-quality ABS may have better heat resistance and toughness than lower-grade or impure materials, reducing the likelihood of cracking.
- Post-Processing: After laser cutting Depending on the application requirements, you may need to perform post-processing steps such as sanding or smoothing to reduce the possibility of cracks after laser cutting. In addition, it is recommended to allow the ABS material to cool gradually to room temperature before handling, as rapid cooling or exposure to temperature fluctuations may cause cracks.
- Material Thickness: Thinner ABS sheets are generally easier to laser cut than thicker sheets. Thicker sheets may require higher laser power settings and slower cutting speeds, which may increase the risk of melting or scorching the material.
- Laser Power And Speed Settings: Finding the proper balance between laser power and cutting speed is critical. Too much power or a cutting speed that is too slow can cause excessive melting, scorching, or even the material catching fire. Correctly adjusting these settings will help you achieve a clean, precise cut.
- Fumes And Ventilation: ABS emits fumes and potentially dangerous gases when laser cutting. Adequate ventilation and fume extraction systems are essential to ensure a safe working environment and prevent the accumulation of harmful by-products.
- Cutting Design: The complexity of the design being cut will affect the ease of laser cutting. Simple geometric shapes and straight lines are often easier to cut than complex and detailed designs.
- Material Quality: The quality and composition of the ABS material will affect the results of laser cutting. High-quality ABS with consistent properties will generally provide more predictable results than lower-grade or impure materials.
- Cooling And Airflow: Proper cooling and airflow during laser cutting help dissipate heat and prevent localized overheating that could lead to melting or charring.