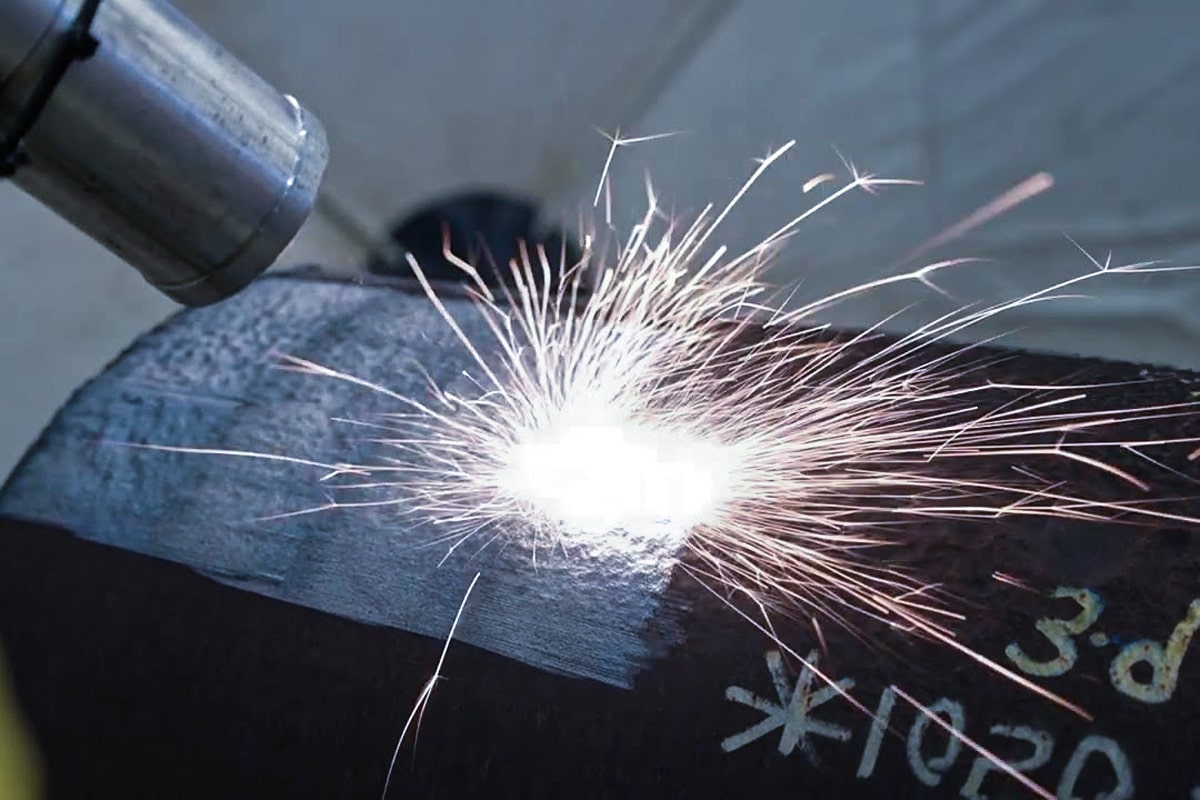
How Do Pulse Frequency and Repetition Rate Affect Laser Cleaning Efficiency?
In laser cleaning technology, pulse frequency and repetition rate are key parameters affecting cleaning efficiency. They determine the transmission mode of laser energy and directly affect material removal rate, surface quality, and cleaning speed. They also play an important role in heat-affected zone (HAZ) and substrate damage. Reasonable adjustment of these two parameters can optimize the cleaning effect in different application scenarios, improve production efficiency, ensure that the cleaning process is both efficient and safe, and reduce substrate damage caused by laser action, to meet the needs of different industrial fields.
Índice
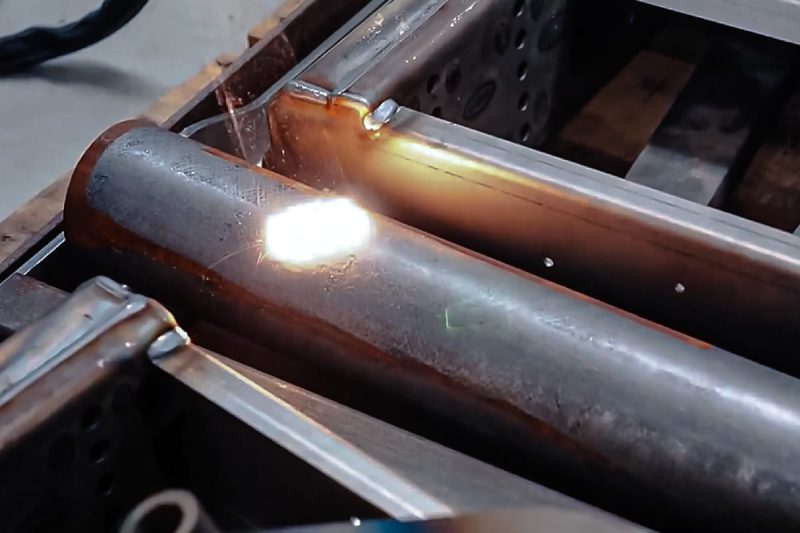
Understanding Pulse Frequency and Repetition Rate
In laser cleaning technology, pulse frequency and repetition rate are two crucial parameters, that directly affect the energy transmission mode of the laser, and thus determine the cleaning efficiency, material removal effect, and impact on the substrate. Reasonable adjustment of these two parameters can optimize the cleaning process, improve production efficiency, reduce damage to the substrate, and ensure a uniform and stable cleaning effect.
Pulse frequency
Pulse frequency refers to the number of pulses emitted by the laser per unit time, usually in Hertz (Hz) or kilohertz (kHz). For example, 10kHz means that the laser generator emits 10,000 pulses per second.
- High pulse frequency (>50kHz): Suitable for cleaning thinner oxide layers, paints, or pollutants, can provide more uniform energy distribution and reduce thermal shock to the substrate.
- Low pulse frequency (<10kHz): Suitable for cleaning thicker rust layers, coatings, or stubborn pollutants such as carbon deposits, can provide higher single pulse energy and improve removal efficiency.
Different materials and contaminants have different sensitivities to pulse frequency. Therefore, in practical applications, the pulse frequency needs to be adjusted according to the characteristics of the cleaning object to obtain the best cleaning effect.
Repetition rate
Repetition rate is often used interchangeably with pulse frequency, which indicates the number of pulses emitted by the laser generator per second. In the laser cleaning process, the repetition rate determines the scanning density of the laser beam, which has an important impact on the cleaning speed and material removal efficiency.
- High repetition rate: provides more intensive laser pulses, increases cleaning speed, and is suitable for cleaning large areas, but if the energy density is insufficient, it may not effectively remove thick contaminants.
- Low repetition rate: Suitable for applications that require higher single pulse energy, such as removing thicker rust layers or strongly attached contaminants, but may result in a decrease in cleaning speed.
In practical applications, the selection of pulse frequency and repetition rate needs to be adjusted according to the cleaning object, material characteristics, and process requirements. For example, when removing the oxide layer, a higher frequency (20-50kHz) is usually used, while when removing heavy pollutants or thick coatings, a lower frequency (<10kHz) is preferred to increase the single pulse energy and achieve more effective material removal. In addition, these parameters need to be coordinated with factors such as pulse energy, scanning speed, and spot size to obtain the best cleaning effect.
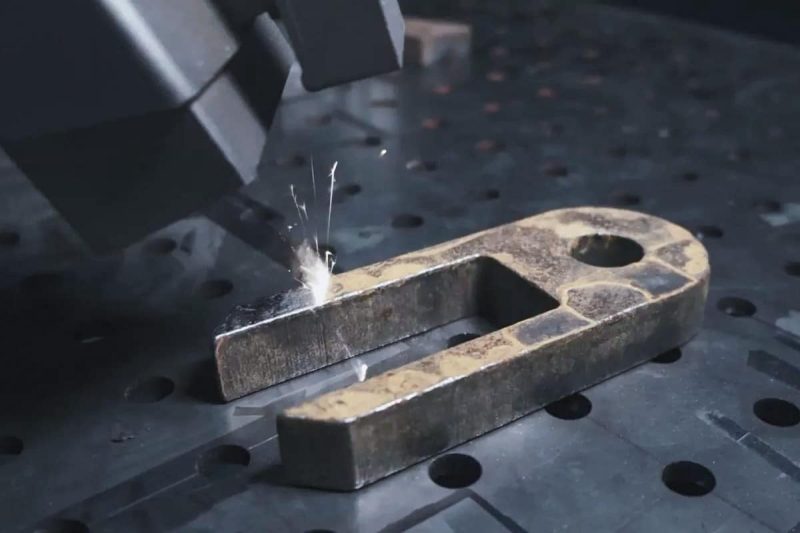
The physical mechanism of laser cleaning
Laser cleaning is an efficient, non-contact cleaning technology that is widely used in metal rust removal, surface treatment, microelectronics processing, and other fields. Its core principle relies on the interaction between laser and contaminants, using high-energy laser beams to accurately remove dirt, oxide layer, or other unwanted coatings without damaging the substrate. The main physical mechanisms of laser cleaning can be summarized as follows:
Photothermal ablation
principle:
Photothermal ablation uses the thermal effect of a laser to remove pollutants. When a high-energy laser beam irradiates the surface of the contaminated layer, the material absorbs the light energy and rapidly heats up, causing local thermal expansion of the contaminated layer, thereby generating thermal stress, causing the contaminant layer to crack, peel off, or directly evaporate.
Características:
- Suitable for highly absorptive contaminants such as metal oxides, paint, oil, etc.
- Effective for removing highly adherent contaminant layers such as aged coatings or heavy rust.
- There may be some thermal impact on the substrate, and the laser parameters need to be controlled to prevent discoloration or melting of the material.
Optimization parameters:
- Lower pulse frequency (<20kHz): provides higher single pulse energy, improves thermal effect, and is suitable for the removal of heavy pollutants.
- Appropriately increase pulse width: increase energy input, so that the polluted layer can fully absorb heat and improve cleaning efficiency.
Photomechanical ablation
principle:
Photomechanical ablation uses the instantaneous energy release of high-power pulsed lasers to form a plasma or gasification effect on the surface of the contamination layer, generating a violent shock wave that shatters and peels off the contaminants.
Características:
- Suitable for removing hard contaminants such as thick rust, metal oxides, coatings, or particulate deposits.
- It has less impact on the substrate and is particularly suitable for precision parts cleaning, such as in the aerospace and microelectronics industries.
- Due to its reliance on instantaneous shock waves, shorter pulse durations (NS or PS levels) are usually required.
Optimization parameters:
- High-power short pulses (nanosecond or picosecond): increase shock wave intensity and enhance the contaminant stripping effect.
- Higher repetition rate (>30kHz): improve cleaning efficiency and ensure uniform surface removal.
Photochemical ablation
principle:
Photochemical ablation relies on lasers of specific wavelengths (such as ultraviolet lasers) acting on the molecular structure of contaminants, breaking their chemical bonds and causing them to decompose or volatilize without causing thermal or mechanical damage to the substrate.
Características:
- Suitable for temperature-sensitive materials such as plastics, rubber, glass, or composite materials.
- Mainly used to remove organic pollutants such as oil, resin residues, adhesives, etc.
- Since no obvious thermal effect is produced, the impact on precision devices (such as semiconductor chips, and LCD screens) is minimal.
Optimization parameters:
- Select appropriate wavelength (such as 355nm UV laser): enhance chemical reaction efficiency and improve cleaning accuracy.
- Use shorter pulses (picosecond or femtosecond): to avoid thermal effects and improve molecular destruction efficiency.
Reasonable adjustment of pulse frequency, pulse energy, and scanning speed can optimize the cleaning effect in different application scenarios, improve production efficiency, and reduce damage to the substrate, thereby achieving accurate, efficient, and safe cleaning operations.
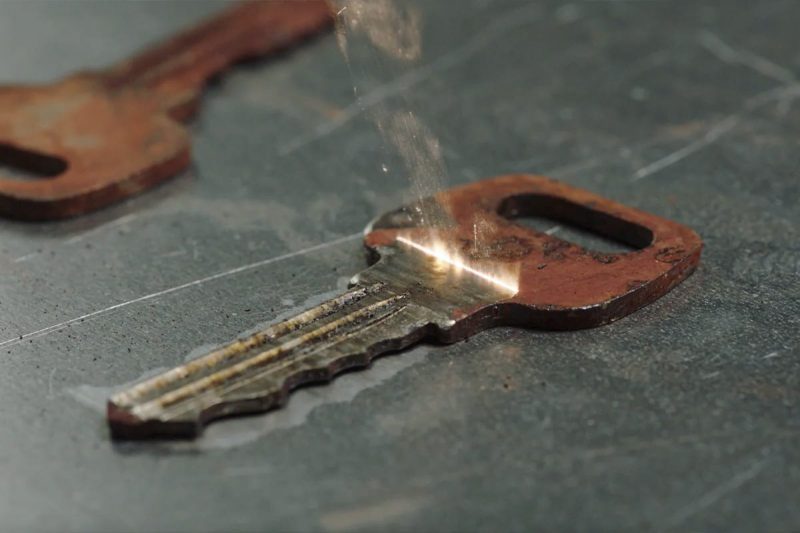
Effect of pulse frequency and repetition rate on cleaning efficiency
In the laser cleaning process, the selection of pulse frequency and repetition rate plays a vital role in cleaning efficiency, substrate protection, and final processing effect. Different parameter combinations not only affect the material removal rate but also determine the thermal effect, surface quality, and cleaning speed. Therefore, according to the specific application requirements, the pulse frequency and repetition rate can be reasonably adjusted to optimize the cleaning effect, improve production efficiency, and reduce damage to the substrate.
Efeitos térmicos
High repetition rate (>50kHz): Since the laser beam releases a large number of pulses per unit time, the heat accumulates quickly, causing the surface temperature of the material to continue to rise. For materials with high thermal stability (such as most metals), this heat accumulation can accelerate the decomposition and removal of pollutants and improve cleaning efficiency. However, if the heat accumulates excessively, it may cause a heat-affected zone (HAZ) in the substrate, or even melting or structural changes, affecting surface properties.
Low repetition rate (<10kHz): There is a long cooling time between each pulse, and the substrate can fully dissipate heat, thereby reducing damage caused by heat accumulation. Suitable for heat-sensitive materials such as organics, rubbers, plastics, or coatings to avoid burning, discoloration, or deformation due to excessive temperature. When cleaning precision parts or electronic components, a lower repetition rate helps reduce side effects and maintain material integrity.
Material removal rate
High repetition rate (>30kHz): Since the laser energy is evenly distributed over a larger area, it is suitable for removing thin and uniform contamination layers, such as oxide layers, slight oil stains or coating residues. The cleaning process is relatively stable, which can obtain better surface quality and reduce the need for subsequent cleaning processes (such as polishing and grinding). It is suitable for applications with high requirements for surface finish, such as high-end manufacturing, automotive parts cleaning, medical device processing, etc.
Low repetition rate (<10kHz): The energy of a single pulse is higher, which can provide a stronger impact force to crack and peel off the contamination layer, so it is more suitable for removing thicker contaminants, such as heavy rust, carbon deposits, resin deposits or multi-layer coatings. For scenes that require deep cleaning (such as rust removal on metal surfaces and weld cleaning), a low repetition rate can improve the removal efficiency of a single cleaning and reduce the number of laser scans. However, it is necessary to control the laser power to avoid damage to the substrate or excessive surface roughness due to excessive single pulse energy.
Surface roughness and damage
High repetition rate (>50kHz): Due to the short interval between laser pulses, the energy is evenly distributed, and the surface after cleaning is smoother, which is suitable for processes with high requirements on surface quality, such as cleaning of precision mechanical parts, semiconductor manufacturing, etc. However, if the power is too high, it may cause partial melting of the material surface, affecting subsequent processes, such as the adhesion performance of coating or welding.
Low repetition rate (<10kHz): Due to the high energy of a single pulse, the impact force formed on the surface is greater, which may produce microstructures or increase roughness on the material surface. Suitable for applications that require improved surface adhesion, such as pre-coating treatment, and surface treatment before painting or bonding. Through moderate surface roughening, the bonding force of the material can be enhanced and the durability and quality of the final product can be improved.
Pulse frequency and repetition rate are important parameters that affect laser cleaning efficiency. A high repetition rate is suitable for removing thin layers of contaminants and can maintain a high surface finish, but may cause more heat accumulation. A low repetition rate is suitable for removing thicker contaminants and provides a high removal rate, but may increase surface roughness. Therefore, in different application scenarios, these two parameters need to be reasonably adjusted according to the substrate type, contaminant thickness, and surface quality requirements to achieve the best cleaning effect.
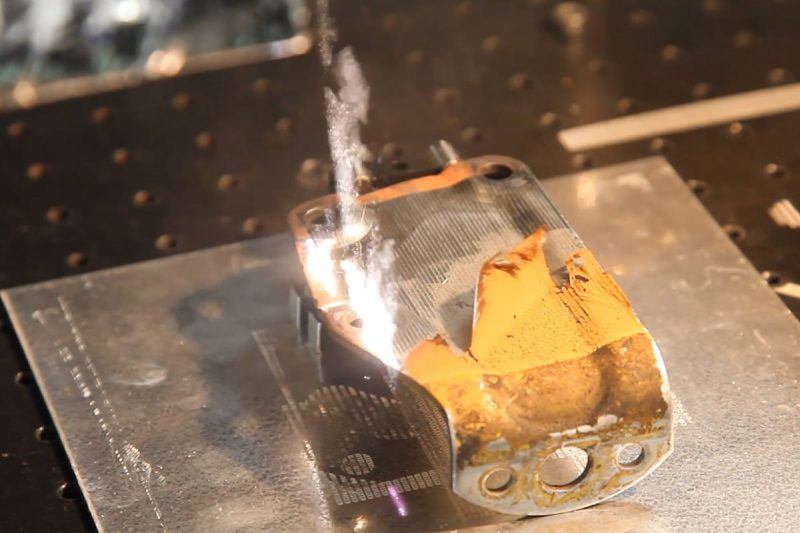
Optimization strategy for pulse frequency and repetition rate
In the laser cleaning process, the reasonable adjustment of pulse frequency and repetition rate is crucial to improve cleaning efficiency, protect the substrate, and achieve the best cleaning effect. Different application scenarios require different optimization strategies to ensure that while effectively removing pollutants, no unnecessary damage to the material is caused. In addition, the selection of pulse energy, duration, beam profile, and wavelength are also important factors in optimizing the cleaning process. The following are optimization strategies for different application scenarios to help users adjust laser parameters according to specific needs to achieve the best cleaning effect.
Application-specific adjustments
- Metal cleaning: Choose medium to high repetition rates (20-50kHz) to ensure stable removal of oxide layers and contaminants while reducing thermal effects to avoid melting or structural changes on the material surface.
- Semiconductor cleaning: Use low repetition rates (<10kHz) to reduce heat accumulation to avoid damage to delicate structures while maintaining high cleaning accuracy.
- Cultural heritage protection: Use low pulse frequencies combined with lower power to ensure that there is no irreversible damage to the surface of cultural relics. It is suitable for cleaning fragile materials such as stone carvings, murals, and ancient books.
Adjustment of pulse energy and duration
- High pulse energy + low repetition rate (<10kHz): suitable for removing thicker contamination layers, such as severe rust, carbon deposits, or thick coatings, but may increase the risk of surface damage, so it is necessary to combine appropriate scanning methods to reduce substrate damage.
- Low pulse energy + high repetition rate (>50kHz): suitable for fine cleaning, such as removing minor contamination, or processing materials with high surface finish requirements, such as aerospace parts or precision instruments.
Choice of beam profile and wavelength
Uniform beam profile (Top-Hat): Suitable for uniform cleaning of large areas, providing consistent energy distribution, and improving cleaning efficiency, while reducing surface damage caused by local overheating.
Wavelength matching: Different materials have different absorption rates for lasers, and choosing the right wavelength can improve the cleaning effect:
- Metal materials: A 1064nm fiber laser generator works best and can efficiently remove rust, oil, and oxide layers.
- Organic matter and polymers: A 355nm UV laser has a high absorption rate for organic materials and is suitable for cleaning plastics, rubber, and paint to reduce thermal effects.
- Glass and ceramics: 532nm green laser can provide more precise processing and reduce the risk of micro cracks.
The optimization of pulse frequency and repetition rate is a key link that cannot be ignored in the laser cleaning process. According to different application requirements, adjusting pulse parameters, energy distribution, beam shape, and laser wavelength can protect the substrate to the greatest extent while ensuring cleaning efficiency and reducing unnecessary damage. By rationally selecting appropriate cleaning strategies, the laser cleaning effect in industrial production, precision manufacturing, and cultural relics protection can be greatly improved, providing better solutions for different application scenarios.
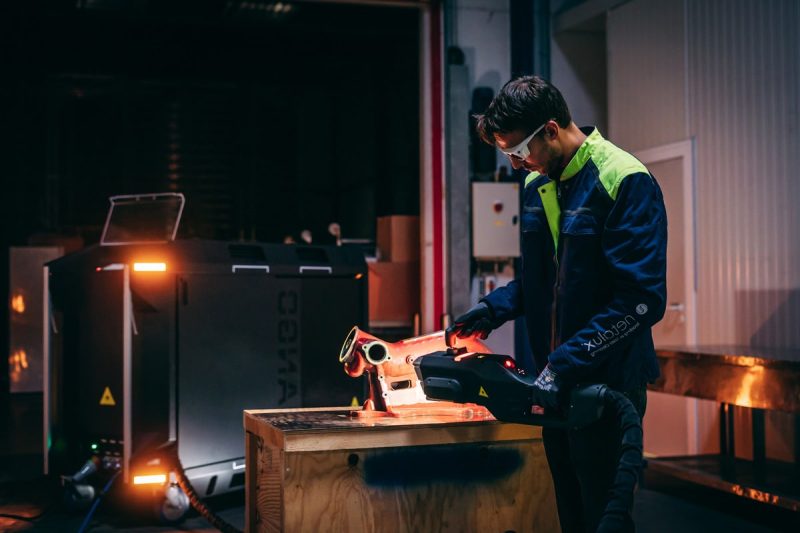
Considerações ambientais e de segurança
While optimizing laser cleaning parameters to improve efficiency, safety, and environmental factors should not be ignored. The laser cleaning process involves multiple aspects such as high-energy laser beams, smoke and dust emissions, and equipment protection. If not handled properly, it may pose potential risks to operators and the environment. Therefore, when formulating a cleaning process, the following key safety measures should be considered to ensure a safe and efficient cleaning process.
- Smoke extraction and air quality control: The laser cleaning process generates a large amount of smoke, particles, and vapors that may contain harmful substances, such as metal oxides or paint-burning residues. To ensure the health of operators and the cleanliness of the working environment, it is necessary to equip efficient smoke extraction and filtration systems, such as HEPA filters or activated carbon filters, to effectively remove pollutants in the air and prevent the spread of harmful substances.
- Equipment and personnel safety protection: Due to the high energy density of laser beams, direct irradiation or reflection may cause damage to personnel and equipment. Therefore, operators should wear laser protective glasses that meet the laser wavelength protection standards, and set up protective covers or shielding devices in the cleaning area to prevent accidental reflection of laser beams. In addition, keep surrounding flammable materials away from the working area to reduce the risk of fire.
- Regulatory compliance and standard certification: In the manufacture, sale, and use of laser cleaning equipment, it should be ensured that international and local safety regulations are complied with, such as EU CE certification, US FDA laser safety certification, ISO11553 (safety requirements for laser processing equipment), etc. In particular, when exporting equipment, it is necessary to follow the laws and regulations of the target market and conduct relevant safety tests to ensure that the equipment meets the standards of various countries and reduces trade risks.
By implementing strict safety management measures, we can not only ensure the health and safety of operators but also ensure the stable operation of equipment and the sustainability of the environment, providing a solid guarantee for the efficient application of laser cleaning technology.
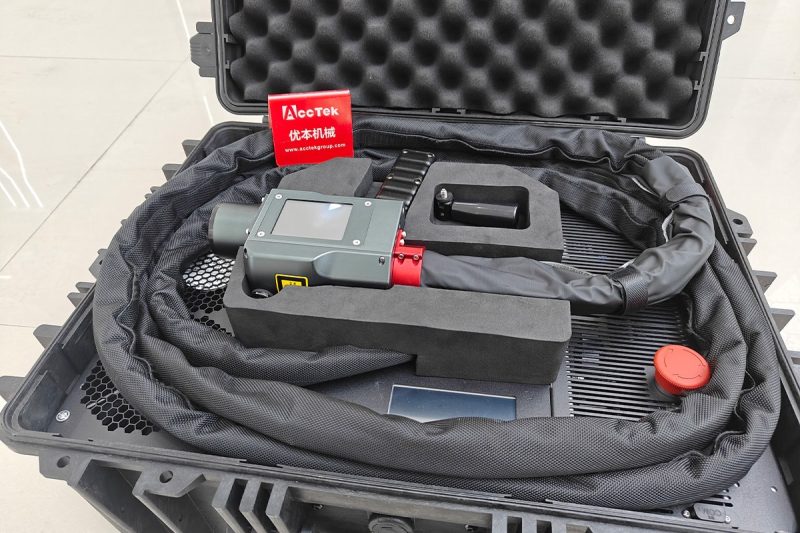
Resumir
Pulse frequency and repetition rate are the core parameters that affect laser cleaning efficiency. Reasonable adjustment can optimize processing speed, reduce substrate damage, and improve overall process stability while ensuring a cleaning effect. For different application scenarios, such as metal cleaning, semiconductor cleaning, and cultural heritage protection, it is necessary to select the best pulse parameters according to material properties and pollutant types. In addition, with appropriate beam profile and wavelength matching, cleaning efficiency can be further improved to ensure the best process effect.
When choosing laser cleaning equipment, Laser AccTek offers a variety of máquinas de limpeza a laser with adjustable pulse parameters, suitable for a variety of industrial and precision applications. If you have any needs for laser cleaning solutions, please contact our professional team to provide you with customized technical support!
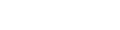
Informações de contato
- [email protected]
- [email protected]
- +86-19963414011
- No. 3 Zona A, Zona Industrial de Lunzhen, Cidade de Yucheng, Província de Shandong.
Obtenha soluções a laser