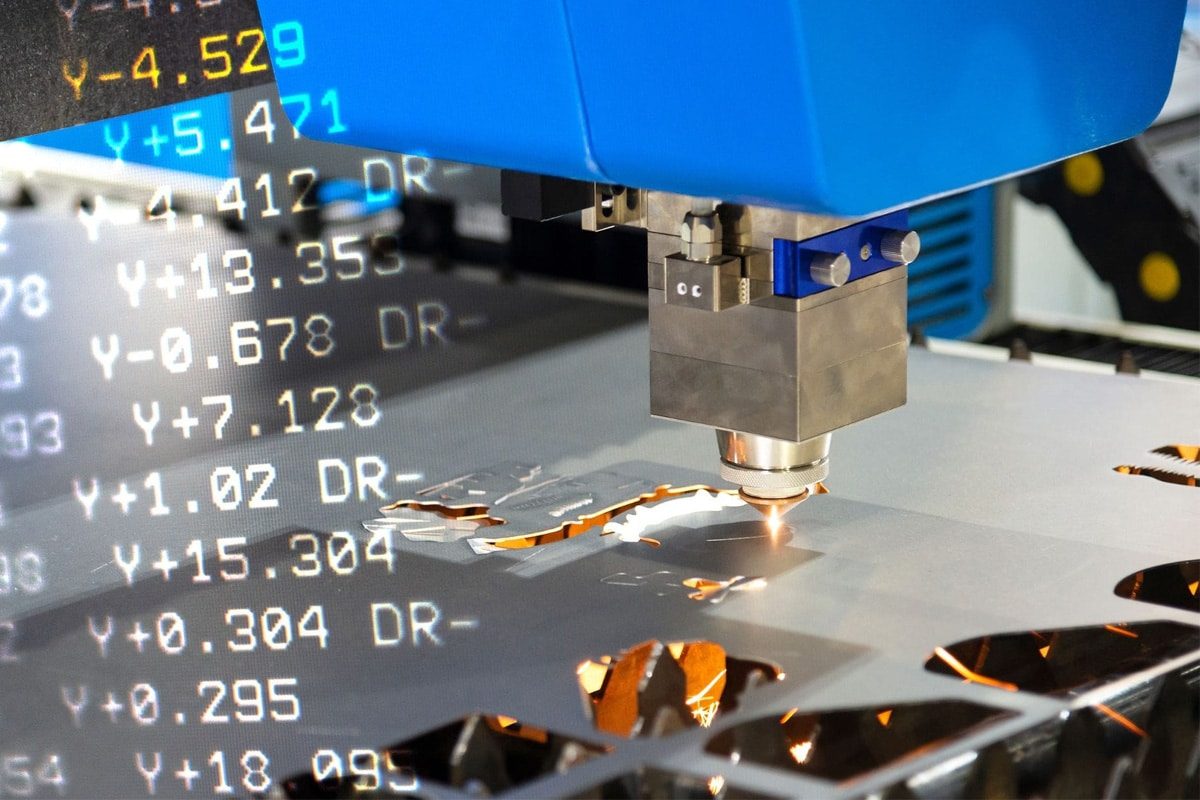
Karmaşık Tasarımlar İçin Fiber Lazer Kesim Makinelerinin Yetenekleri ve Sınırlamaları
As precision manufacturing continues to upgrade, fiber laser cutting machines have become a representative device for efficient and high-precision processing. Especially in dealing with design tasks with complex patterns and high precision requirements, fiber laser cutting technology is widely used in many industrial fields due to its excellent performance. This article will explore in depth the core capabilities and practical limitations of fiber laser cutting machines in dealing with complex designs, and provide optimization strategies to help manufacturers give full play to their effectiveness.
İçindekiler
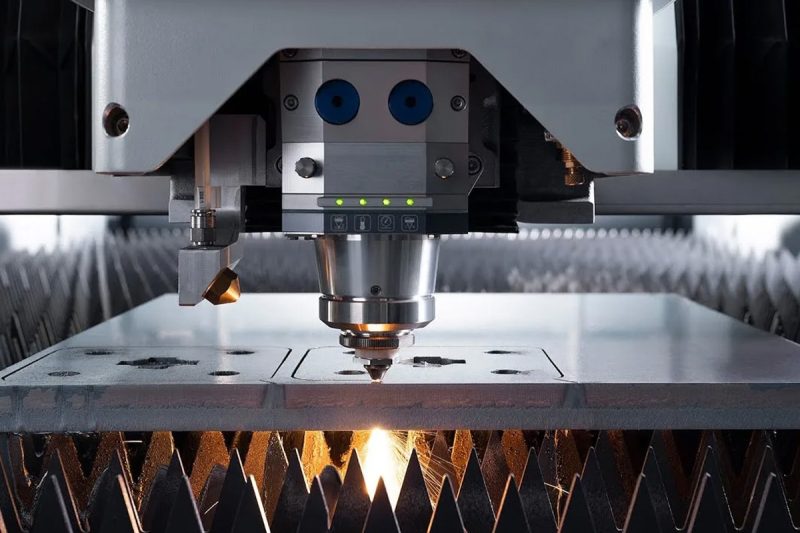
Learn about fiber laser cutting machine
A fiber lazer kesim makinesi is high-end equipment that can achieve automatic cutting by focusing a laser beam with high energy, precisely melting the surface of materials. It uses a fiber laser generator as a laser source, cooperates with an efficient optical system and advanced CNC programming, and can achieve high-speed and high-quality cutting processing of various metal materials, including stainless steel, carbon steel, aluminum alloy, copper plate, etc. It is widely used in precision manufacturing, sheet metal processing, automotive parts, aviation structural parts, and other industries, and is particularly suitable for product design with high requirements for cutting accuracy and complexity.
Core components
The laser generator is the “heart” of the entire fiber laser cutting machine, and is mainly responsible for converting electrical energy into high-density laser energy. Compared with traditional CO2 or YAG laser generators, fiber laser generators have the advantages of high photoelectric conversion efficiency (up to more than 40%), low energy consumption, small size, and long life. The output laser beam has extremely high brightness and stability, which can ensure continuous and high-quality cutting output during high-speed processing.
The optical system is mainly responsible for transmitting the laser beam from the laser generator to the cutting head and accurately focusing the laser at the focusing lens. This process involves multiple high-reflectivity lenses and lens groups to ensure that the laser energy is concentrated and the spot diameter is controllable. At the same time, some high-end equipment is also equipped with automatic focusing lenses and anti-pollution protection lenses to meet the automatic adjustment needs of materials of different thicknesses, thereby improving the overall cutting efficiency and cutting quality.
The CNC system is the “brain” for precision machining. It automatically converts complex graphics into precise cutting paths by receiving and parsing CAD/CAM design drawings. The CNC system, equipped with modern fiber laser cutting equipment, supports multi-axis linkage, dynamic power adjustment, real-time speed feedback, and other functions, and can achieve dynamic follow-up cutting of multiple surfaces and angles. Some systems also integrate machining path optimization algorithms, automatic edge finding, remote monitoring, and other functions, which greatly improve machining efficiency and the human-machine collaboration experience.
In general, the reason why fiber laser cutting machines can occupy an important position in modern industry is due to the deep collaboration between high-performance laser generators, precise optical transmission systems, and intelligent CNC technology. The combination of the three enables the equipment to not only handle conventional straight or circular cutting tasks, but also to handle cutting tasks of metal parts with complex structures and numerous details. For modern manufacturing companies that pursue high efficiency and high precision, fiber laser cutting equipment is one of the key tools to enhance competitiveness.
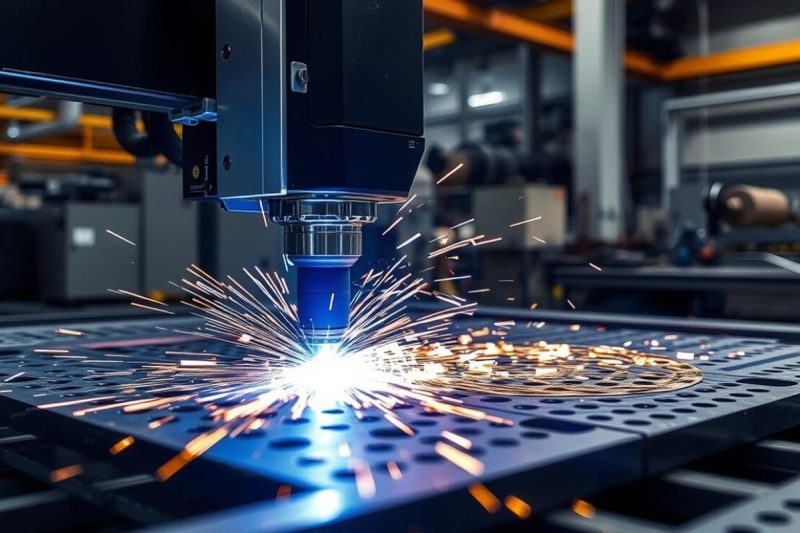
Functions of fiber laser cutting machine
With the growing demand for high-precision, high-efficiency, and diversified processing in modern manufacturing, fiber laser cutting machines have gradually become important equipment in the field of precision processing with their stable laser output, precise control system, and wide range of material adaptability. Whether it is a customized workpiece with complex structure or a large number of standardized parts, fiber laser cutting technology can achieve fast and high-quality solutions, providing various industrial customers with extremely high processing flexibility and efficiency advantages.
Key features
The focal point of the fiber laser beam is extremely small, and combined with advanced focusing optical components and CNC systems, precise control can be achieved within the micron range. The small slit width and narrow heat-affected zone make the processed edges neat and clean, and the dimensional tolerance control is excellent. It is suitable for the production of parts with extremely high precision requirements, especially in the electronics, medical, mold, and other industries, showing strong adaptability.
Fiber laser cutting machines can effectively cut a variety of metal materials, including karbon çeliği, paslanmaz çelik, alüminyum alaşımı, bakır, galvanizli sheet, titanium alloy, etc. The reflectivity, thermal conductivity, and thickness of different materials have different requirements for laser performance, but by adjusting parameters such as power, focus position, and cutting speed, high-quality cutting effects can be achieved, greatly improving the versatility of the equipment and return on investment.
With high-stability laser beam control and intelligent CNC path optimization, fiber laser cutting machines can easily meet the design requirements of various complex structures. For example, parts with interlaced curves, frequent sharp angle changes, and dense patterns can be restored with high fidelity according to CAD drawings, greatly shortening the conversion time from design to production.
For metal workpieces with complicated edges or irregular shapes, fiber laser cutting technology can still ensure a smooth cut surface, avoiding burrs, slag and thermal deformation. Even on parts with uneven thickness or dense details, it can maintain clear boundaries and good surface treatment effects, effectively reducing the time cost of subsequent grinding and secondary processing.
Compared with traditional cutting methods, fiber laser cutting machines have faster cutting speeds, especially in thin plate material processing, which can achieve flying cutting mode and greatly improve processing efficiency. At the same time, combined with automatic loading and unloading systems or production line integration solutions, it can achieve long-term unmanned continuous operation, reduce manual intervention, and improve the level of production line automation.
Fiber laser cutting uses digital control. Drawing adjustments and version upgrades can be completed by simply modifying the cutting program through software. It is very suitable for rapid proofing, small batch customization, or multi-specification order processing. In industries with frequent product updates, this flexible response speed is particularly critical.
In summary, fiber laser cutting machines play an irreplaceable role in modern manufacturing through their high precision, high efficiency, multi-material adaptability, and strong ability to cope with complex designs. It not only significantly improves product quality and production efficiency, but also provides strong support for enterprises to achieve flexible manufacturing and diversified customization. Especially in industrial applications that require fine detail processing and rapid design iteration, fiber laser cutting technology is gradually becoming the first choice for core equipment.
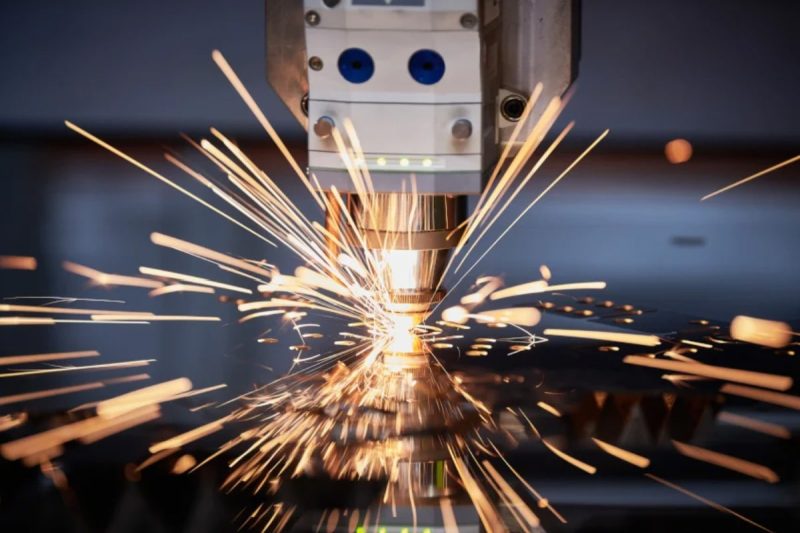
Application areas of fiber laser cutting machines in complex designs
As the manufacturing industry’s demand for personalized, complex structures and high-quality processing continues to rise, fiber laser cutting technology has been widely deployed in multiple industries with its excellent flexibility and high precision. Especially in the industrial field with extremely high requirements for part dimensional accuracy, edge quality, and detail complexity, fiber laser cutting machines have become an important basic tool for engineering realization and product innovation.
Typical industry applications
In automobile manufacturing, fiber laser cutting technology is widely used in the processing of body panels, chassis structures, exhaust system parts, and interior metal parts. These parts often contain complex structures such as curved contours, reinforcing ribs, and mounting holes. Traditional mechanical processing finds it difficult to balance precision and efficiency. Laser cutting can complete the forming in one go, reducing the number of post-finishing steps, while ensuring structural strength and assembly matching, and improving the assembly quality and manufacturing efficiency of the entire vehicle.
The aerospace industry places extremely high demands on the lightweight, strength distribution, and processing accuracy of metal components, especially on engine brackets, cabin frames, avionics assemblies, and other parts. Fiber laser cutting machines can achieve high-precision processing in a non-contact manner, ensuring that there are no cracks or thermal deformation on the edges of parts, and achieving a minimum weight design while maintaining structural strength. Its good processing performance on special materials such as titanium alloys and high-strength aluminum alloys has greatly expanded its scope of application in the industry.
Modern architecture is increasingly pursuing the combination of structure and art. Fiber laser cutting technology can efficiently achieve design requirements such as complex patterns, relief styles, and hollow structures. Whether it is a metal curtain wall, carved partition, stair handrail, or stainless steel art component, laser cutting can ensure neat cutting edges, clear graphics, and high consistency in mass production. By importing CAD drawings, designers can quickly transform their creativity into physical objects, helping to unify architectural aesthetics and structural practicality.
In the electrical and electronics industry, miniaturization and precision are the core design requirements, especially for metal parts such as housing structures, connectors, shielding sheets, etc., used in consumer electronics, communication equipment, and industrial control. Fiber laser cutting machines can maintain high repeatability and cutting cleanliness within a very small size range, effectively avoiding the burrs and deformation problems common in traditional stamping processes, while reducing mold manufacturing costs and improving product development flexibility.
Medical equipment has extremely strict standards for processing cleanliness, micro-precision, and material edge processing. Fiber laser cutting machines are widely used in the manufacturing process of surgical instruments, orthopedic implants, dental components, etc., with their non-contact, high energy density, and controllable heat-affected zone. Not only are the cutting edges smooth and pollution-free, but they can also effectively control component dimensional errors and material fatigue, meeting the medical industry’s strict requirements for quality consistency and product reliability.
Fiber laser cutting machines provide solutions for complex structural designs in many industries through precise, efficient and flexible processing methods. In high-end manufacturing fields such as automobiles, aviation, construction, electronics and medical care, they not only improve product quality and production efficiency, but also provide strong support for the implementation of new structural designs. With the continuous advancement of technology, the application boundaries of fiber laser cutting machines are still expanding, and they will play a key role in more precision manufacturing fields in the future.
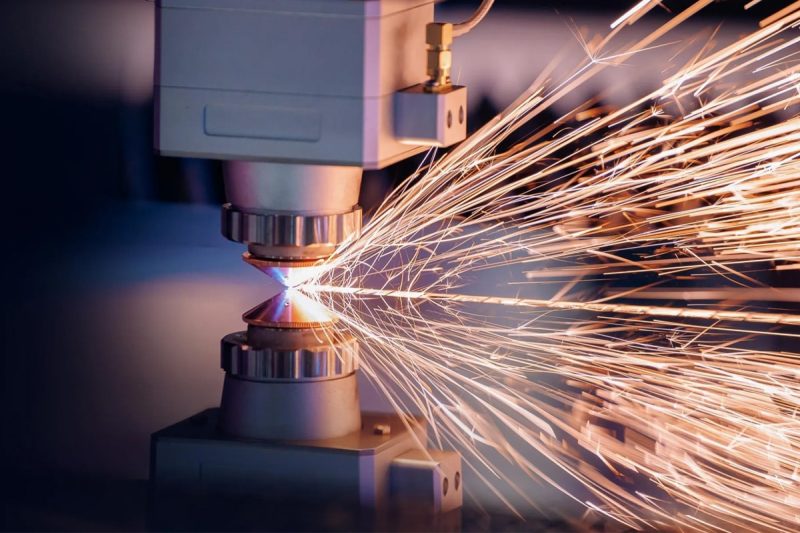
Key factors affecting accuracy and detail performance
Although the fiber laser cutting machine itself has extremely high processing capabilities, in the actual operation process, the quality of the finished product is still affected by a series of technical parameters and operating variables. Especially when facing complex structures or fine pattern cutting tasks, the accuracy and stability of each link control directly determine the degree of detail restoration and overall consistency of the final product. Therefore, an in-depth understanding of these key factors and continuous optimization during operation are the core guarantees for ensuring high-quality output.
Main influencing factors
Beam quality is the core indicator for measuring laser output stability and focusing performance. High-quality beams have smaller divergence angles and higher energy concentration, allowing the laser to be focused into an extremely fine light spot, thereby achieving a narrower slit width and more precise trajectory control. In the cutting of fine patterns or tiny parts, the purity of the beam mode is directly related to the sharpness of the edge lines and the surface finish.
The setting of cutting speed needs to achieve a balance between parameters such as material thickness, power density, and gas assist. Too fast a cutting speed may cause the laser to fail to fully melt the material, resulting in slag or uncut phenomenon; while too slow a speed may cause excessive heat accumulation, causing edge melting and diffusion, and loss of precision. For workpieces of different materials and thicknesses, the optimal speed range should be determined through a parameter database or trial cutting to ensure both efficiency and quality.
Different materials have different thermal conductivity, reflectivity, and melting points, and the degree of absorption of lasers varies accordingly. For example, stainless steel absorbs lasers better and is suitable for high-speed cutting, while highly reflective materials such as copper and aluminum have high reflectivity to wavelengths and require the use of dedicated laser generators and auxiliary optical path systems. The thicker the material, the more difficult it is to penetrate the energy and maintain the focus, especially in thick plate cutting, where more attention should be paid to the dynamic adjustment of the focal length and stability of the gas flow field.
The heat-affected zone refers to the area around the laser action area where microstructural changes occur due to heat diffusion. If the heat-affected zone is too large, it may cause local hardening, embrittlement, or deformation of the material, thereby affecting the subsequent processing or assembly performance of the parts. By selecting short-pulse lasers or using high-frequency puncture mode, the heat diffusion range can be effectively reduced while improving processing efficiency, thereby ensuring that the material properties of the trimming area are not destroyed.
The nozzle is the channel for auxiliary gas output. Its structure and size will directly affect the gas injection speed and direction, thereby affecting the slag discharge and cutting stability. High-quality nozzle design can form a stable protective gas flow and improve the cleanliness of the cutting seam. At the same time, accurate setting of the focus position is the key to maximizing the utilization of laser energy. Especially in the cutting of special-shaped workpieces or multi-layer materials, the focus must be adjusted dynamically to ensure energy consistency along the entire cutting path.
The laser cutting process is highly dependent on the stability of the CNC system and the accuracy of the CAD/CAM program. The optimized cutting path can not only reduce the empty stroke and avoid repeated overheating areas, but also automatically adjust the speed and power output according to the complexity of the graphics to achieve intelligent processing. Improper setting of program parameters will cause the cutting track to deviate, edge burn, or error amplification. Therefore, experienced software engineers and advanced control platforms are the guarantee for stable output of high-quality products.
Many factors affect the precision and detail performance of fiber laser cutting, covering multiple dimensions such as equipment hardware, operating parameters, material properties, and software systems. Only by constantly accumulating experience, optimizing settings and combining technological evolution in practical applications can we give full play to the potential of laser cutting machines in complex structure processing, achieve accurate restoration from drawings to finished products, and provide stable and reliable technical support for high-end manufacturing and personalized design.
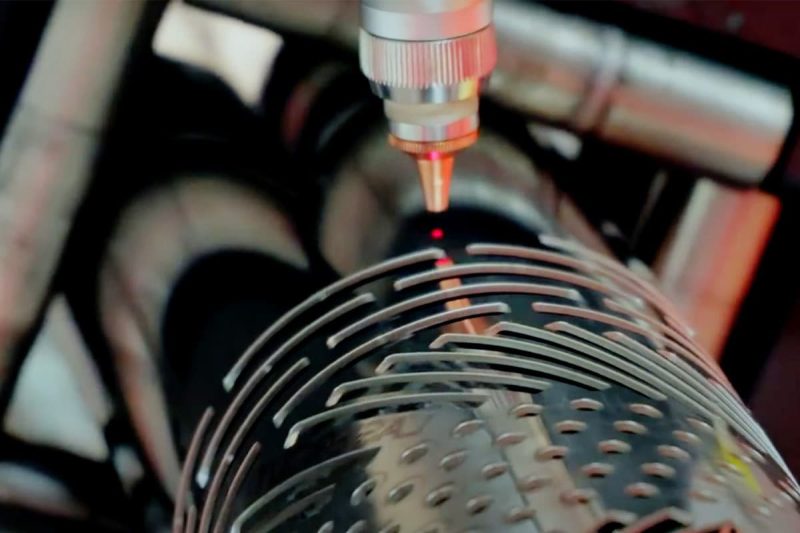
Strategies to ease restrictions
In the actual application of fiber laser cutting of complex structures or precision components, although the performance of the equipment has been greatly improved, it is still restricted by many factors such as parameter settings, material properties, programming paths, operating experience, etc. If these limitations cannot be dealt with scientifically, it is very easy to cause fluctuations in cutting quality, reduced production efficiency, and even processing failure. To this end, enterprises can make simultaneous efforts from multiple levels, such as technology optimization, process management, and personnel training, to systematically improve the overall process level and stability.
Effective strategies
Through a systematic parameter testing and recording mechanism, gradually establishing a parameter database for different materials, thicknesses, and graphic types is an important means to ensure the consistency of cutting quality. Parameter optimization mainly includes core variables such as laser power, pulse frequency, cutting speed, jet pressure, and focal position. It is recommended to use the method of trial cutting + data collection, combined with the monitoring system for fine adjustment, especially when dealing with fine curves or small circular holes. Fine-tuning a parameter can often significantly improve the edge quality and cut seam flatness.
The purity, surface cleanliness and flatness of the material itself directly affect the laser absorption efficiency and heat distribution. It is preferred to use high-quality metal sheets from regular brands and perform surface degreasing, rust removal or film protection treatment before processing to significantly reduce the incidence of cutting defects. In addition, preliminary spectral detection or physical property testing of different batches of materials can also help establish a differentiated parameter model to achieve more precise cutting control.
Advanced design and programming tools can not only improve the efficiency of early design but also effectively control the processing path, cutting sequence, and heat distribution. Especially when laying out complex graphics or high-density patterns, software modules with path optimization, hot zone avoidance, processing simulation, and residual material identification functions can significantly reduce waste and improve the yield rate. At the same time, the software interface can be used to realize parameter linkage and processing data feedback with the laser equipment, promoting digital closed-loop management of the entire process.
Even if the equipment and software are advanced, it is difficult to ensure consistent processing results in the long term without professional operators and stable process flows. Establishing a complete standard operating instruction (SOP) and process manual, and regularly organizing operator training, is the core guarantee for maintaining equipment capacity and yield. Excellent operators can not only quickly identify abnormal conditions on site, but also make empirical judgments in actual operations and fine-tune and optimize processing parameters.
Faced with increasingly complex cutting requirements and precision challenges, relying solely on the performance of the hardware itself is no longer sufficient to achieve stable and efficient production goals. By comprehensively using scientific parameter debugging methods, high-quality material management, efficient software support, standardized operating systems and intelligent auxiliary equipment, companies can fully alleviate the technical limitations of fiber laser cutting machines in complex design processing from the source to the implementation, thereby achieving higher quality product delivery and more competitive production capabilities.
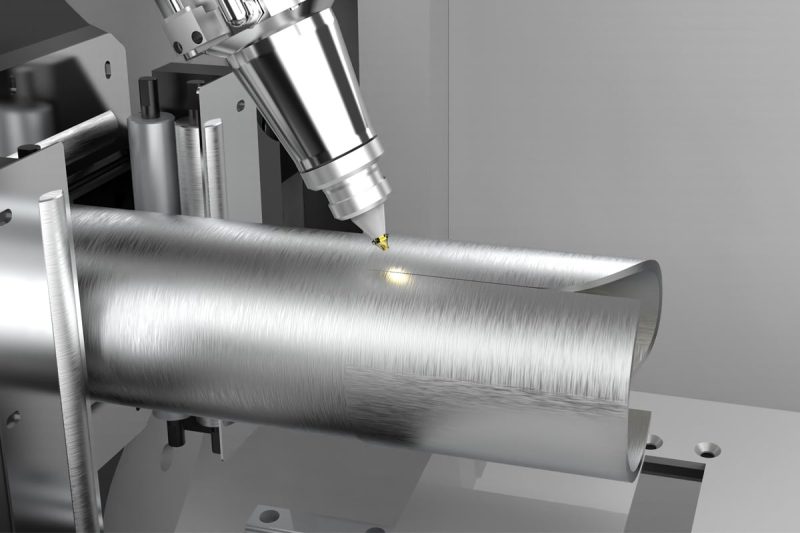
özetle
In the context of the current manufacturing industry accelerating towards high-end, intelligent, and customized development, traditional processing methods can no longer meet the ever-changing market needs in terms of efficiency, precision, and flexibility. The fiber laser cutting machine, with its excellent beam quality, extremely high positioning accuracy, and excellent adaptability to a variety of complex graphics, has become an indispensable key equipment in the modern industrial system. Especially in processing tasks involving complex structural design and high-precision requirements, it shows technical advantages that are difficult to match with traditional processes.
Although challenges such as heat impact control, material compatibility, and edge quality may still be faced in actual applications, these problems can be effectively alleviated or even completely solved through advanced parameter setting technology, intelligent path optimization software, precision processing control systems, and the coordination of professional operators. The technical boundaries of fiber laser cutting are constantly being broken, and its strategic position in high-end manufacturing will become increasingly prominent.
As a professional brand with deep R&D and manufacturing accumulation in the field of laser processing equipment, AccTek Laser has always adhered to the development concept of “technology-driven value” and focused on creating stable, efficient, and intelligent fiber laser cutting solutions. Our equipment not only has superior processing performance and excellent operating stability, but is also widely used in many industries such as automobile manufacturing, aerospace, precision electronics, architectural decoration, medical equipment, etc., and has won a good reputation and high praise from users around the world.
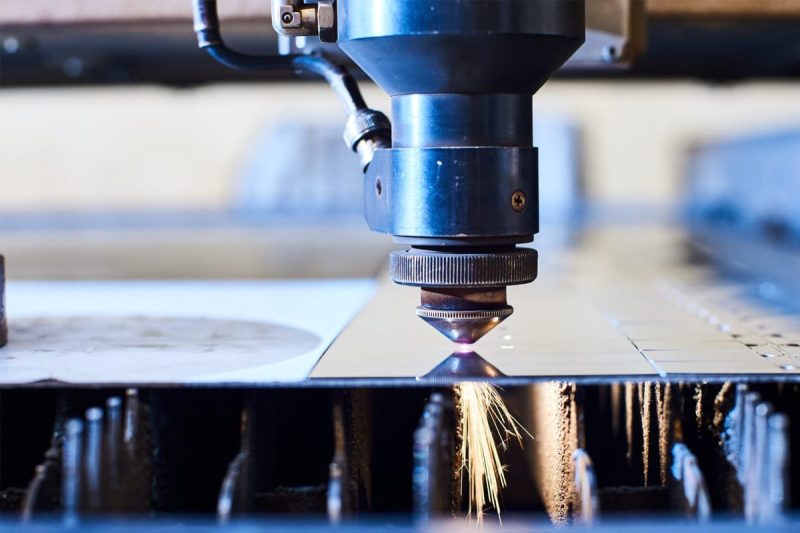
Get laser solutions
We know that every industry and every customer has unique application needs. Therefore, AccTek Laser provides one-stop support from equipment selection, process customization, installation, and commissioning to after-sales service, truly realizing the service commitment of “solving problems for customers and creating value for production”.
If you are looking for a high-performance fiber laser cutting machine that can cope with complex structural design and difficult processing tasks, please feel free to bize Ulaşın. With our professional technical team, rich industry experience and flexible customization capabilities, we will provide you with the solution that best meets your actual production needs, helping your company stand out in the fierce market competition and move towards a new stage of high-quality development.
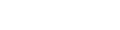
İletişim bilgileri
- [email protected]
- [email protected]
- +86-19963414011
- 3 Bölge A, Lunzhen Sanayi Bölgesi, Yucheng Şehri, Shandong Eyaleti.
Lazer Çözümleri Alın