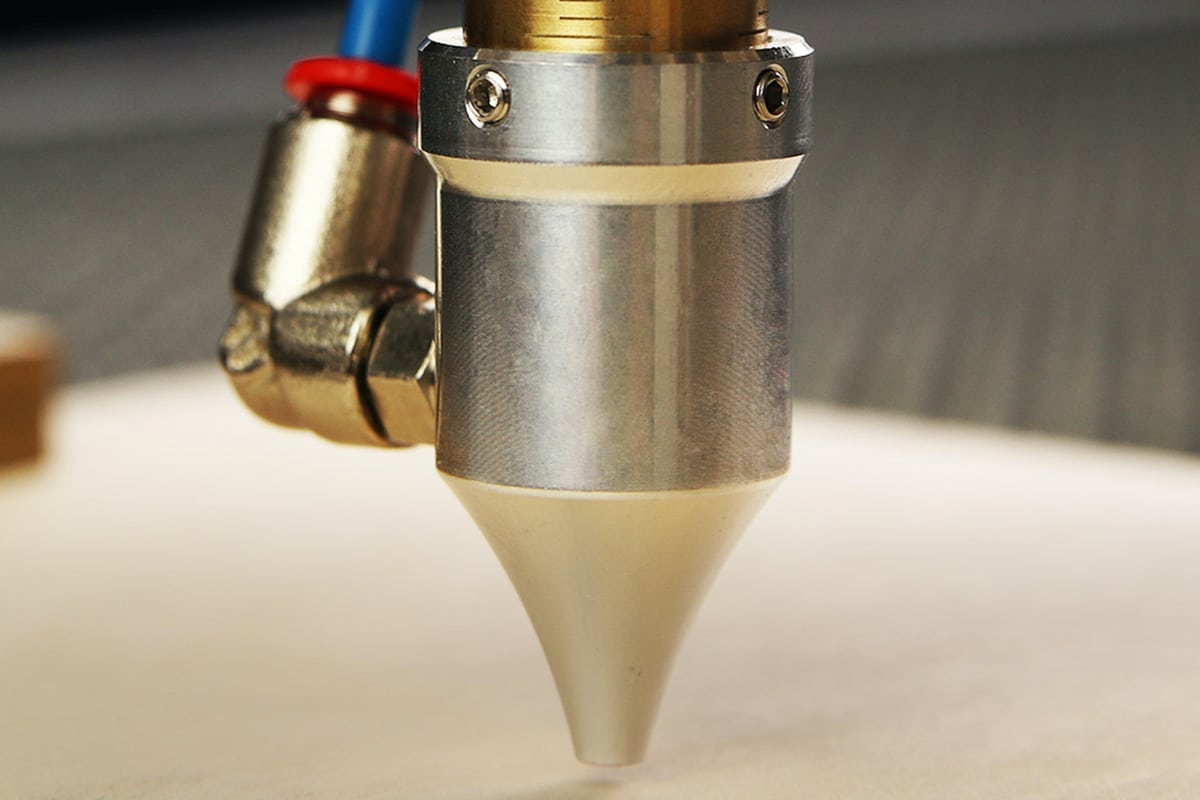
Common Defects in CO2 Laser Cutting and Their Mitigation Methods
CO2 laser cutting is a high-precision processing technology widely used in the processing of metal and non-metal materials. It uses a high-energy-density CO2 laser beam to heat the material, causing it to melt, vaporize, or be blown away by auxiliary gas to achieve efficient cutting. Although CO2 laser cutting machines has advantages such as high precision and smooth cutting surface, in actual operation, it may still be affected by factors such as material properties, cutting parameters, and equipment conditions, resulting in processing defects. This article will introduce the basic principles of CO2 laser cutting, common defects, and their mitigation methods.
İçindekiler
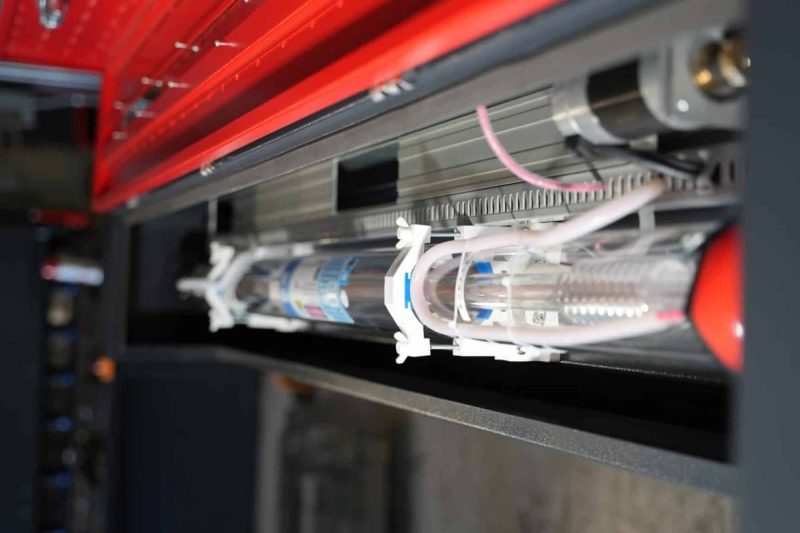
CO2 Laser Cutting Principle
A CO2 laser generator is a gas laser generator that mainly uses CO2 gas as the gain medium. When the electric current excites the CO2 gas, the gas molecules are stimulated to emit photons, forming a high-power infrared laser beam (wavelength 10.6μm). After the laser beam is focused by the optical system, the energy density is extremely high, which can quickly heat and melt or vaporize the material. Under the action of auxiliary gas (such as oxygen, nitrogen, or air), the melt is blown away to form an incision.
Different gas types can affect cutting quality, for example:
- Oxygen: promotes combustion and increases cutting speed but easily oxidizes the surface of the material.
- Nitrogen: prevents oxidation and is suitable for high-quality cutting of materials such as stainless steel.
- Air: has a lower cost but may affect cutting quality and is suitable for non-critical workpiece processing.
CO2 laser cutting relies on the synergy of high-energy infrared laser beam and auxiliary gas to achieve efficient material processing. The selection of different auxiliary gases directly affects the cutting quality and efficiency. Enterprises should choose the appropriate gas type according to material characteristics and processing requirements to optimize cutting effects and improve production stability.
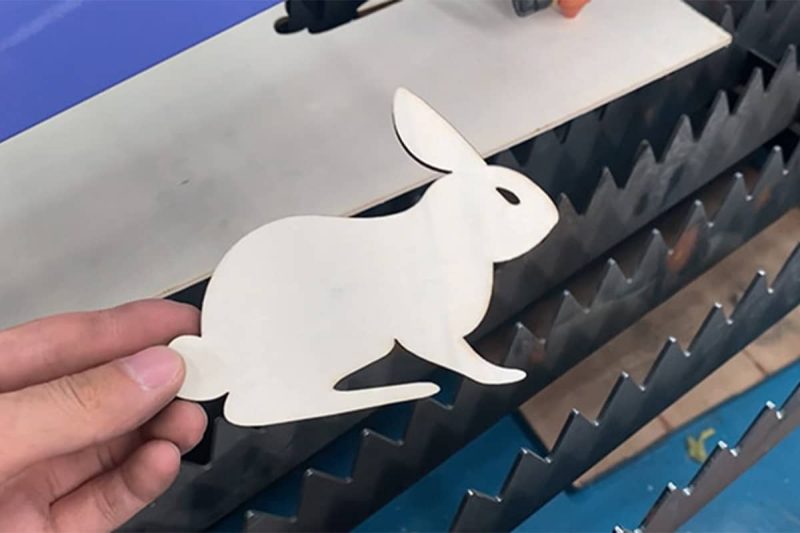
Common Defects in CO2 Laser Cutting and Solutions
Although CO2 laser cutting has the advantages of high precision and high efficiency, different types of defects may occur during the processing due to various factors. These defects will not only affect the cutting quality but may also reduce production efficiency and increase material waste. Therefore, in-depth understanding of the causes of common problems and taking corresponding optimization measures are the keys to improving cutting quality and equipment stability. The following will analyze the common defects in the CO2 laser cutting process and provide mitigation methods.
The cutting surface is rough and has obvious stripes
Causes:
This issue is mainly caused by cutting speed, laser power, and unstable auxiliary gas flow. If the cutting speed is too fast, molten material cannot be fully expelled, resulting in noticeable striations on the cut surface. Conversely, if the speed is too slow, heat accumulation can affect cutting quality. Additionally, insufficient power or unstable gas flow direction can further exacerbate the problem.
Çözümler:
- Adjust the cutting speed appropriately to ensure timely removal of molten material and achieve a smooth cut surface.
- Increase laser power to enhance energy density and ensure complete penetration of the material.
- Use high-purity auxiliary gas and optimize the nozzle angle to stabilize the airflow and effectively remove slag.
Severe Slag Adherence
Causes:
This is mainly caused by factors such as low gas pressure, mismatched nozzle size, and improper focus position. Insufficient auxiliary gas pressure may not effectively blow away the molten metal, causing slag to adhere to the cutting surface. In addition, inappropriate nozzle design may affect the uniformity of gas flow and reduce the cleanliness of the cutting area.
Çözümler:
- Increase auxiliary gas pressure to ensure quick removal of slag and reduce adherence.
- Choose the appropriate nozzle size to ensure uniform gas distribution and improve cutting quality.
- Readjust the focal position to evenly distribute laser beam energy and enhance cutting stability.
Excessive Heat-Affected Zone (HAZ)
Causes:
Excessive laser power or slow cutting speed can cause heat accumulation, leading to a larger heat-affected zone. This can impact cutting precision and may result in edge melting or deformation.
Çözümler:
- Reduce laser power appropriately to minimize unnecessary heat input and prevent excessive HAZ.
- Increase cutting speed to reduce the material’s exposure to high temperatures and minimize thermal effects.
- Use pulsed laser cutting to reduce continuous heating effects on the material and optimize processing quality.
Decreased Cutting Precision
Causes:
Machine vibration, optical path misalignment, and contamination of optical lenses can all lead to reduced cutting precision. Vibrations affect laser beam stability, optical path deviations may cause incorrect focal positioning, and contaminated lenses can weaken laser energy transmission.
Çözümler:
- Regularly maintain the machine to minimize mechanical looseness and reduce vibration impact.
- Recalibrate the optical path to ensure the laser beam remains accurately focused.
- Clean and replace optical lenses to prevent dust or oil contamination from affecting laser transmission.
Poor Perforation Quality
Causes:
Excessive perforation time, unstable auxiliary gas flow, or exceeding the machine’s cutting capacity can lead to poor perforation quality. This may result in irregular holes or excessive heat-affected zones.
Çözümler:
- Use stepwise or pulsed perforation techniques to minimize heat accumulation and optimize hole shape.
- Ensure stable auxiliary gas flow for consistent and reliable perforation quality.
- Adjust laser power and beam size according to material thickness to match different processing needs.
Oxidized and Discolored Edges
Causes:
When using oxygen as an auxiliary gas, the high cutting temperature accelerates oxidation reactions, causing edge discoloration. This oxidation layer not only affects appearance but may also reduce the material’s corrosion resistance.
Çözümler:
- Use nitrogen or other inert gases instead of oxygen to reduce oxidation reactions.
- Lower cutting temperature to minimize oxidation layer formation and improve surface quality.
Common CO2 laser cutting defects are mainly related to cutting parameters, gas flow, and equipment maintenance. By optimizing cutting parameters, selecting the right auxiliary gases, and maintaining equipment regularly, businesses can effectively reduce defects and improve cutting quality.

CO2 Lazer Kesimin Avantajları
While CO2 laser cutting has some common limitations, it also offers unique advantages. With its well-established process and stable performance, CO2 laser cutting technology is widely used across various industries. Compared to other cutting methods, it provides the following benefits:
- High Cutting Quality: CO2lasers offer excellent beam quality with a fine focal point, enabling high-precision cutting. This makes them ideal for applications requiring smooth edges, such as automotive manufacturing and precision electronics.
- Wide range of applicable materials: CO2 laser is not only suitable for thin metal materials, but can also be used to cut non-metal materials (such as odun, akrilik, plexiglass, etc.), so it is also widely used in advertising, decoration and furniture industries.
- Mature Technology & Cost Efficiency: With years of development, CO2laser cutting technology is highly refined, and both equipment and maintenance costs are relatively manageable, making it suitable for mass production.
Thanks to these advantages, CO2 laser cutting remains competitive across multiple industries, particularly for manufacturers that require versatile material processing solutions.
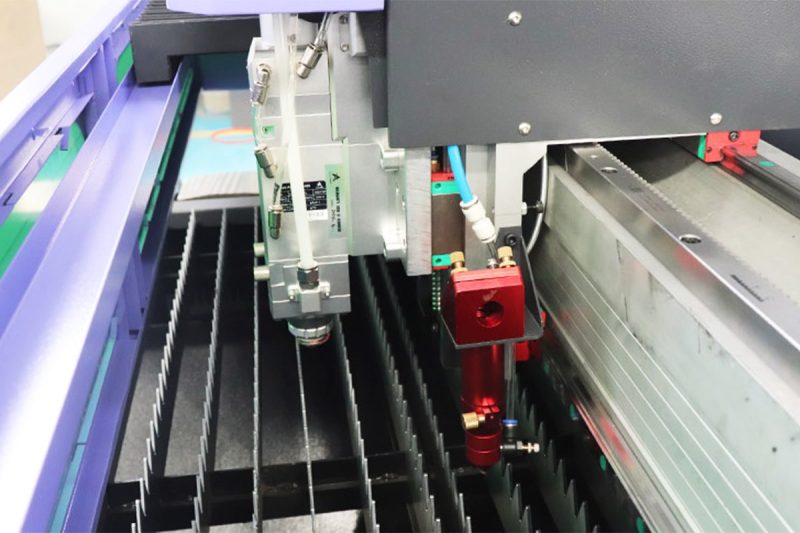
özetle
CO2 laser cutting plays a vital role in industrial manufacturing due to its well-established process and broad application scope. However, because of equipment characteristics and processing parameter limitations, some common defects may occur during production, such as rough cutting surfaces, slag adhesion, and excessive heat-affected zones. To improve processing quality, companies can implement various optimization measures, including adjusting cutting speed and laser power, selecting suitable assist gases, precisely controlling focal positions, and regularly maintaining the optical system and mechanical components. Additionally, using high-quality CO2 laser generators, optimizing airflow control, and upgrading CNC systems can effectively enhance cutting stability and production efficiency.
As the manufacturing industry shifts towards efficiency, environmental sustainability, and precision machining, CO2 laser cutting continues to offer unique advantages, particularly in thick plate processing, non-metal cutting, and specialized industry applications. By continuously refining processing techniques and integrating advanced auxiliary technologies, businesses can maximize the benefits of CO2 laser cutting—achieving high precision and superior quality while reducing operational costs and minimizing environmental impact.
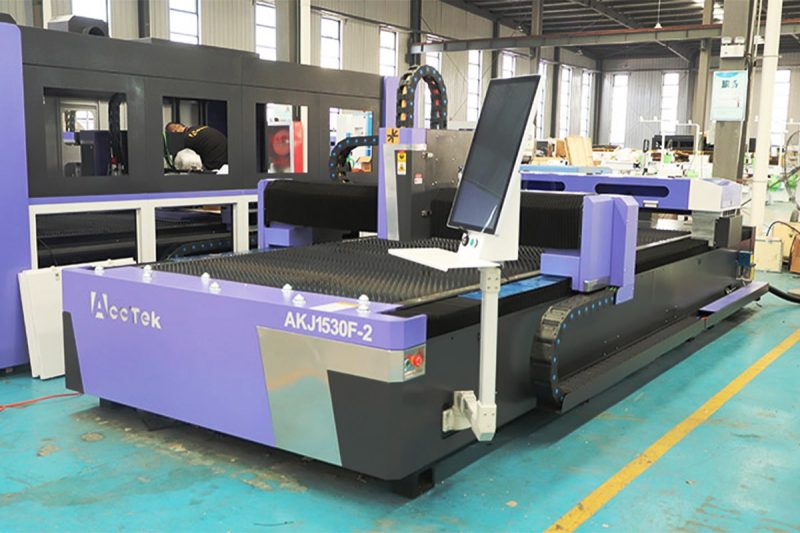
Get Your Laser Solution
AccTek Lazer is committed to delivering high-efficiency and reliable CO2 laser cutting solutions to meet diverse industrial processing needs. Our equipment features advanced laser sources, high-precision control systems, and intelligent cutting software, ensuring stable cutting quality, low operational costs, and broad material compatibility. Whether for metal processing, non-metal cutting, or industry-specific applications, we provide professional technical support and customized optimization solutions to help businesses enhance productivity and competitiveness.
If your are looking for high-performance, cost-effective CO2 laser cutting equipment, feel free to bize Ulaşın to learn more about CO2 laser cutting applications and optimization strategies. Let’s work together to create a future of efficient and precise manufacturing!
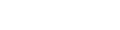
İletişim bilgileri
- [email protected]
- [email protected]
- +86-19963414011
- 3 Bölge A, Lunzhen Sanayi Bölgesi, Yucheng Şehri, Shandong Eyaleti.
Lazer Çözümleri Alın