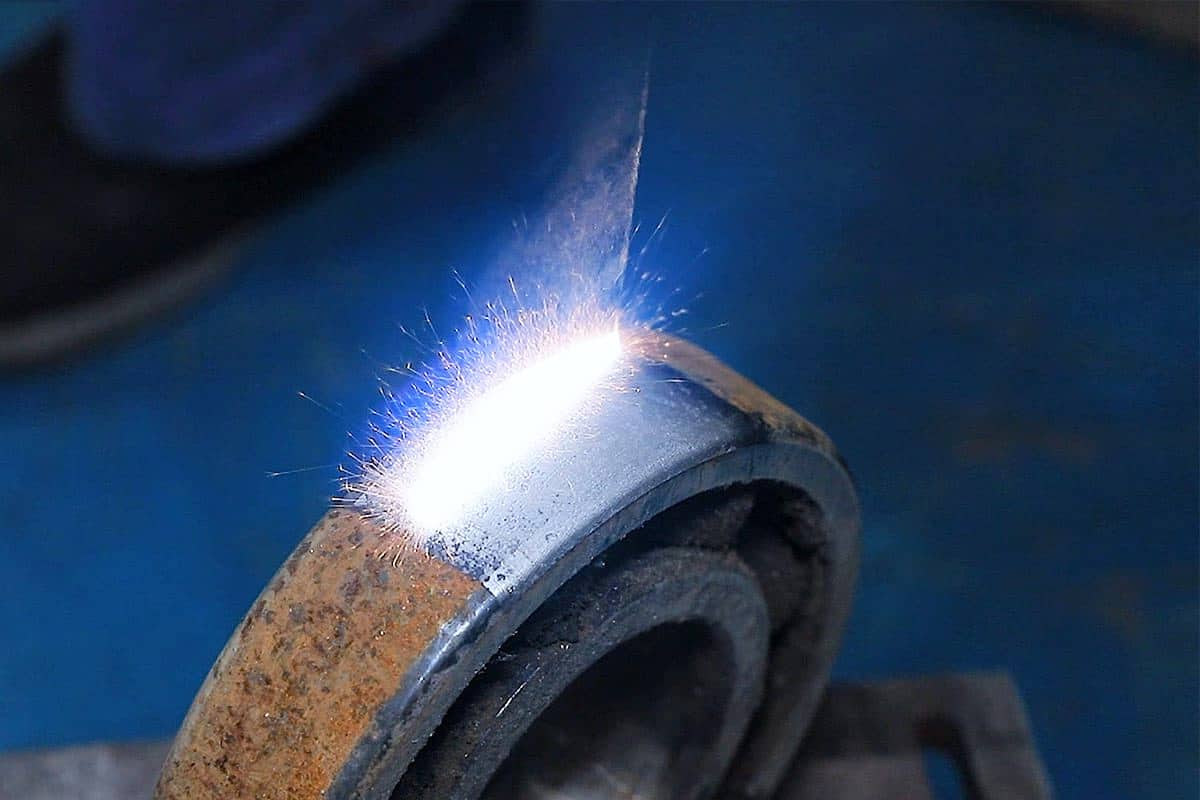
Darbeli Lazer Temizleme Alt Tabakaya Zarar Verir Mi?
Darbeli lazer temizleme, yüksek verimliliği, çevre dostu olması ve temassız yapısı nedeniyle lazer yüzey hazırlama ve fiber lazer pas giderme gibi uygulamalarda yaygın bir popülerlik kazanmıştır. Ancak, birçok kullanıcı için kritik bir endişe devam etmektedir: Bu teknoloji alt tabakaya zarar verebilir mi?
Bu makale, darbeli lazer temizliğinin temellerini ele alarak çeşitli parametre ayarları altında alt tabaka hasarına yol açabilecek olası termal, mekanik ve fotokimyasal etkileri inceler. Ayrıca, malzemenin termal iletkenliği ve emilim oranı gibi temel etki faktörlerine bakacağız ve riski en aza indirmek için parametre optimizasyonu, çoklu darbe kontrolü ve gerçek zamanlı sıcaklık izleme gibi pratik stratejiler sunacağız.
İçindekiler
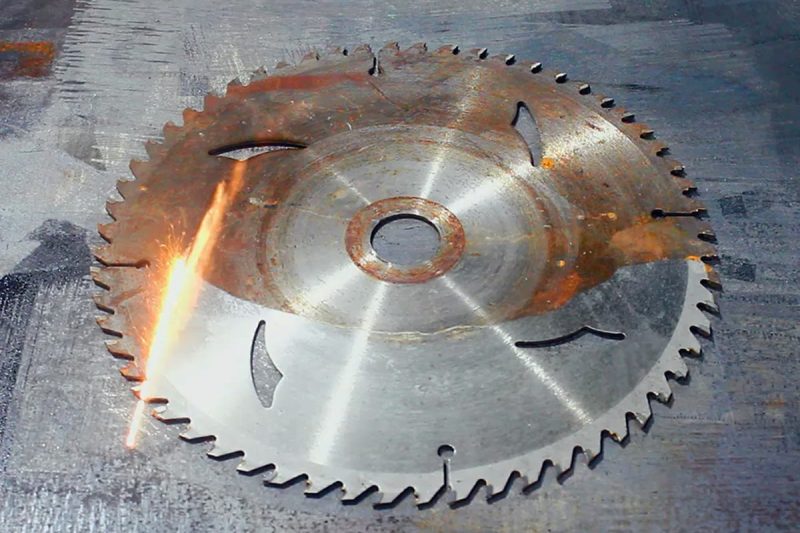
Darbeli Lazer Temizliğini Anlamak
Darbeli lazer temizleme, lazer pas giderme, boya giderme, oksit tabakası temizleme ve hassas kalıplar ve elektronik bileşenler için lazer yüzey hazırlama gibi uygulamalarda yaygın olarak kullanılan etkili, çevre dostu ve temassız bir yüzey işleme teknolojisidir. Temel prensip, malzemeye önemli termal etkiler veya mekanik hasar vermeden alt tabakadan kirleticileri hızla buharlaştıran veya temizleyen yüksek enerjili lazer darbelerini içerir.
Pratik uygulamalarda, temizleme verimliliğini artırmak ve alt tabaka güvenliğini sağlamak için aşağıdaki temel parametrelerin anlaşılması ve optimize edilmesi önemlidir:
- Darbe Süresi: Genellikle nanosaniye, pikosaniye veya hatta femtosaniye aralığında olan tek bir lazer darbesinin süresini ifade eder. Daha kısa darbeler ısıdan etkilenen bölgeyi (HAZ) azaltmaya yardımcı olur ve bu da onları ısıya duyarlı malzemelerin hassas temizliği için ideal hale getirir.
- Darbe Enerjisi: Her lazer darbesinin taşıdığı enerjiyi temsil eder ve temizleme kabiliyetini doğrudan etkiler. Daha yüksek darbe enerjisi, güçlü bir şekilde yapışmış kirleticileri gidermek için etkilidir, ancak alt tabaka hasarını önlemek için dikkatlice kontrol edilmelidir.
- Tekrarlama Oranı: Birim zaman başına yayılan lazer darbelerinin frekansını ifade eder. Daha yüksek bir tekrarlama oranı temizleme hızını artırabilir ancak düzgün bir şekilde kontrol edilmezse ısı birikmesine ve termal hasara yol açabilir.
- Dalga boyu: Lazerin dalga boyu, farklı malzemelerle etkileşimini belirler. Örneğin, metaller genellikle 1064 nm lazer dalga boyuna daha iyi yanıt verir.
- Işın Profili: Uzaydaki lazer ışınının enerji dağılımını ifade eder. İdeal bir ışın profili, yerel aşırı ısınma veya düzensiz temizlemeyi önlerken istikrarlı ve verimli temizlik sağlayan düzgün bir enerji dağılımına sahip olmalıdır.
Lazer pas giderme, lazerle kalıp temizleme veya diğer endüstriyel kullanımlar gibi uygulamalarda, bu parametrelerin düzgün şekilde yapılandırılması yalnızca verimliliği artırmakla kalmaz, aynı zamanda malzemeyi de korur ve bu da yüksek kaliteli darbeli lazer temizliği elde etmede önemli bir faktör haline gelir.
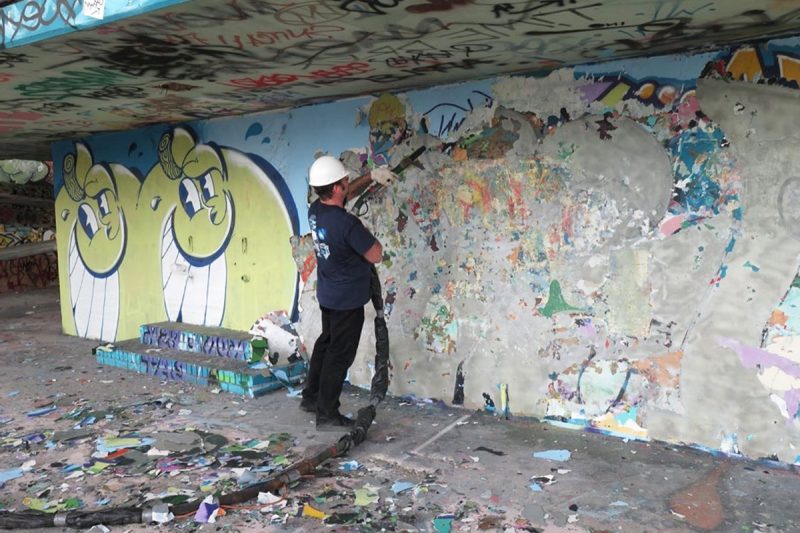
Alt Tabaka Hasar Mekanizmaları
Darbeli lazer temizleme işlemi sırasında, alt tabakalar termal etkiler, mekanik etkiler ve fotokimyasal etkiler dahil olmak üzere çeşitli mekanizmalardan etkilenebilir. Darbeli lazer temizleme teknolojisi yüksek verimlilik ve çevresel faydalar sunarken, bu etkiler belirli koşullar altında alt tabakaya zarar verebilir. Aşağıda belirli hasar mekanizmaları verilmiştir:
Termal Etkiler
- Erime: Yüksek enerjili lazer darbeleri, substratı erime noktasını aşan sıcaklıklara kadar yerel olarak ısıtabilir ve bu da yerel erimeye neden olabilir. Bu fenomen özellikle metal yüzeyleri veya kaplamaları temizlerken yaygındır. Lazer enerjisi çok yüksekse, yerel erime meydana gelebilir.
- Termal Stres: Lazer temizleme işlemi sırasında hızlı ısıtma ve soğutma, malzemede iç stresler oluşturarak düzensiz termal genleşmeye neden olabilir. Bu stresler, özellikle ısıya duyarlı veya ince duvarlı malzemelerde çatlaklara veya deformasyona neden olabilir.
- Isıdan Etkilenen Bölge (HAZ): Isıdan etkilenen bölgedeki (HAZ) alt tabakanın mikro yapısı ve mekanik özellikleri değişebilir. Bu değişiklik, özellikle HAZ'ın malzeme performansında düşüşe yol açabileceği metallerde ve alaşımlarda alt tabakanın mekanik mukavemetini ve ömrünü azaltabilir.
Mekanik Etkiler
- Şok dalgaları: Lazer tarafından oluşturulan plazma genleşmesi, alt tabaka yüzeyinde mekanik hasara neden olabilecek şok dalgaları üretir. Bu, özellikle şok dalgalarının yüzey çatlaklarına veya malzeme dökülmesine yol açabileceği kırılgan veya ince malzemeler için geçerlidir.
- Buharlaşma Basıncı: Kirleticilerin hızlı buharlaşması, alt tabaka yüzeyine aktarılabilen ve ek mekanik yük uygulayabilen yüksek basınç üretir. Temizleme işlemi çok hızlıysa veya enerji çok yüksekse, alt tabakada lokal hasara veya deformasyona neden olabilir.
Fotokimyasal Etkiler
- Yüzey Kimyasal Değişimleri: Lazerden gelen yüksek enerjili fotonlar, alt tabaka yüzeyiyle etkileşime girerek yüzey özelliklerini değiştiren kimyasal reaksiyonlara neden olabilir. Örneğin, bazı lazer temizleme işlemleri oksidasyonu veya diğer kimyasal reaksiyonları tetikleyerek alt tabakanın yüzey yapısını ve kimyasal bileşimini değiştirebilir.
- Kirlenme: Temizlik sırasında kirleticilerin eksik bir şekilde çıkarılması, artık maddelerin alt tabaka yüzeyinde yeniden birikmesine ve yeni kirlenmeye neden olabilir. Bu, alt tabakanın performansını olumsuz etkileyebilir ve kullanımında uzun vadeli olumsuz etkilere neden olabilir.
Darbeli lazer temizleme, yüzey kirleticilerinin giderilmesi için oldukça etkili bir yöntem sunarken, yukarıda belirtilen termal, mekanik ve fotokimyasal etkilerin alt tabakaya zarar vermesini önlemek için darbe enerjisi, süre ve tekrarlama oranı gibi lazer parametrelerini dikkatlice kontrol etmek çok önemlidir. Uygun lazer parametre yapılandırması ve hassas kontrol, hem temizleme sürecinin güvenliğini hem de verimliliğini sağlamak için önemlidir.
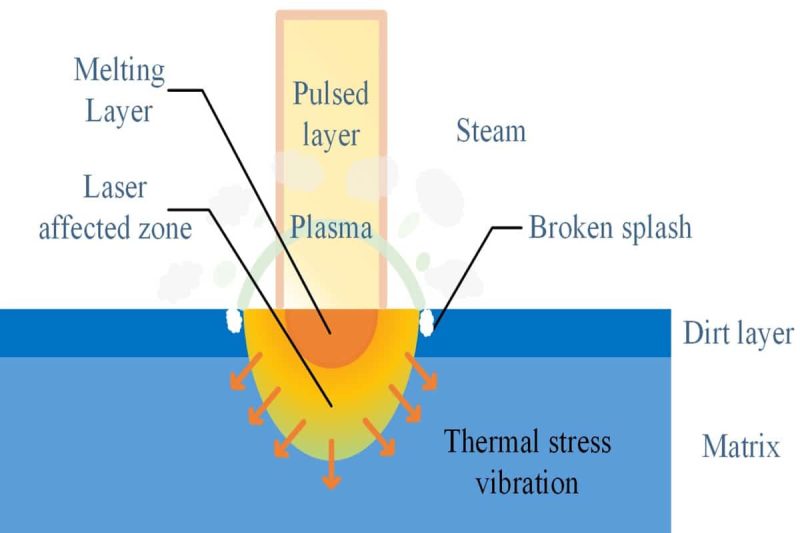
Alt tabaka hasarını etkileyen faktörler
Darbeli lazer temizliği sırasında, çeşitli faktörler alt tabakada meydana gelebilecek hasarın derecesini etkiler. Bu faktörleri anlamak ve optimize etmek hem etkili kirletici madde giderimi hem de alt tabaka koruması sağlamak için çok önemlidir. Aşağıda ana etki eden unsurlar verilmiştir:
Malzeme özellikleri
- Isıl İletkenlik: Yüksek ısıl iletkenliğe sahip malzemeler ısıyı daha verimli bir şekilde dağıtabilir ve bu da ısı birikimi ve hasar riskini azaltır. Örneğin, bakır ve alüminyum gibi metaller, üstün ısı dağılımı nedeniyle lazer temizliği sırasında termal bozulmaya daha az eğilimlidir.
- Emilim Katsayısı: Emilim katsayısı, bir malzemenin belirli bir dalga boyunda ne kadar lazer enerjisi emebileceğini belirler. Daha yüksek emilim oranı daha hızlı yüzey ısınmasıyla sonuçlanır ve bu da güvenli temizlik için lazer dalga boyu ve gücünün hassas bir şekilde kontrol edilmesini gerekli kılar.
- Erime Noktası: Daha düşük erime noktalarına sahip malzemeler, yüksek enerjili lazer maruziyeti altında erimeye daha yatkındır. Plastikler veya düşük erime noktalı alaşımlar gibi ısıya duyarlı alt tabakalarla çalışırken uygun temizlik parametrelerini seçmek önemlidir.
- Mekanik Dayanıklılık: Daha yüksek mekanik dayanıklılık, bir malzemenin şok dalgalarından veya termal stresten kaynaklanan hasara direnmesine yardımcı olur. Daha güçlü alt tabakaların yüksek frekanslı darbeli lazer temizliği sırasında çatlama veya deformasyona uğrama olasılığı daha düşüktür.
- Kimyasal Bileşim: Substratın kimyasal kararlılığı, fotokimyasal reaksiyonlara olan duyarlılığını etkiler. Bazı malzemeler, yüksek enerjili fotonlara maruz kaldığında yüzey kimyası değişimlerine uğrayabilir ve bu da performanslarını olumsuz etkileyebilir.
Lazer Parametreleri
- Darbe Süresi: Her lazer darbesinin süresi, ısının alt tabakaya nasıl aktarıldığını doğrudan etkiler. Ultra kısa darbeler (örneğin, femtosaniye lazerler) ısıdan etkilenen bölgeyi (HAZ) önemli ölçüde en aza indirerek, özellikle hassas veya hassas bileşenlerde termal hasar riskini azaltır.
- Darbe Enerjisi: Darbe enerjisinin uygun şekilde ayarlanması kritik öneme sahiptir. Kirleticileri gidermek için yeterli enerjiye ihtiyaç vardır, ancak aşırı enerji alt tabakanın erimesine veya ablasyonuna yol açabilir. Bu parametrenin optimize edilmesi verimli ancak güvenli bir temizlik sağlar.
- Tekrar Oranı: Yüksek tekrar oranı ısı birikimi riskini artırır. Isı birikimini ve olası alt tabaka hasarını önlemek için, frekans malzemenin ısı toleransına ve iletkenliğine göre ayarlanmalıdır.
- Dalga boyu: Hem kirleticilerin hem de alt tabakanın emilim özelliklerine uyan bir lazer dalga boyu seçmek temizleme verimliliğini artırır ve hasarı azaltır. Bu, lazer yüzey hazırlığını optimize etmede önemli bir stratejidir.
Çevre koşulları
- Ortam Sıcaklığı: Yükseltilmiş ortam sıcaklıkları, alt tabakanın başlangıç sıcaklığını yükselterek temizleme işlemi sırasında aşırı ısınma olasılığını artırabilir. Hassas uygulamalar için sıcaklık kontrolü gerekebilir.
- Nem: Yüksek nem, alt tabaka yüzeyinde nemin yoğunlaşmasına neden olarak lazerin malzemeyle etkileşimini değiştirebilir. Bu, ek termal veya kimyasal etkilere yol açabilir ve potansiyel olarak temizleme performansını tehlikeye atabilir.
- Yüzey Durumu: Yüzey pürüzlülüğü ve mevcut kirleticilerin türü, temizleme işleminin sonucunu etkiler. Düzensiz yüzeyler veya katmanlı kirleticiler, hem temizleme verimliliğini hem de alt tabakanın güvenliğini etkileyen eşit olmayan enerji dağılımına yol açabilir.
Darbeli lazer temizliğinin başarısı ve alt tabaka üzerindeki etkisi yalnızca lazer sisteminin kendisine değil, aynı zamanda malzemenin fiziksel ve kimyasal özelliklerine, çevre koşullarına ve yüzey durumuna da bağlıdır. Alt tabaka hasarını en aza indirmek ve temizleme verimliliğini en üst düzeye çıkarmak için bu faktörleri kapsamlı bir şekilde değerlendirmek ve lazer parametrelerini buna göre ayarlamak esastır.
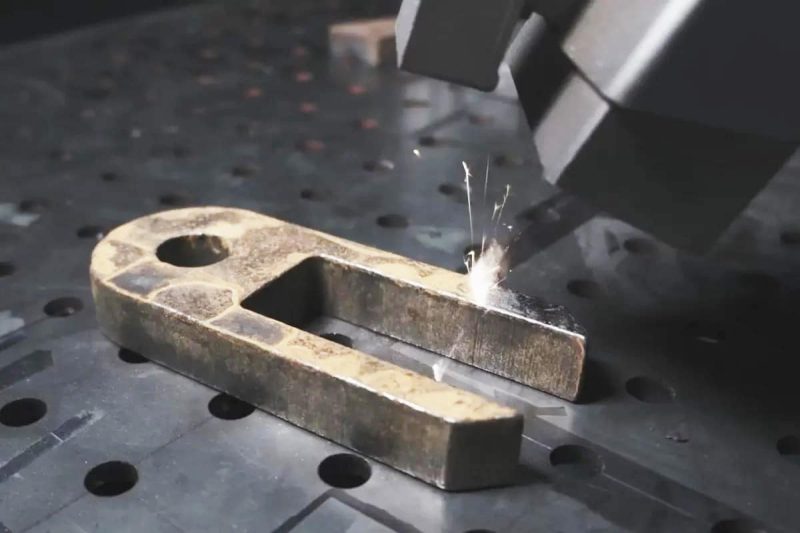
Alt tabaka hasarını en aza indirmeye yönelik stratejiler
Darbeli lazer temizleme, kirleticileri gidermek için hassas, temassız bir çözüm sunarken, uygunsuz parametre ayarları yine de alttaki alt tabakaya geri döndürülemez hasar verebilir. Malzeme bütünlüğünü korurken etkili bir temizlik sağlamak için, parametre optimizasyonu ve gelişmiş tekniklerin bir kombinasyonu uygulanmalıdır.
Parametre Optimizasyonu
- Darbe Süresinin Ayarlanması: Femtosaniye lazerler gibi ultra kısa darbelerin kullanılması, termal difüzyon bölgesini önemli ölçüde sınırlandırır, ısıdan etkilenen bölgenin (HAZ) boyutunu etkili bir şekilde en aza indirir ve termal hasar risklerini azaltır.
- Darbe Enerjisinin Kontrolü: Kirletici maddelerin giderilmesi için gereken minimum darbe enerjisinin ayarlanması, hassas malzemeler için hayati önem taşıyan alt tabaka yüzeyinin aşırı ısınmasını veya erimesini önler.
- Tekrar Oranının Yönetimi: Dikkatle seçilmiş bir tekrar oranı, darbeler arasında yeterli soğutma süresini garanti ederek, eğilmeye, mikro çatlaklara veya diğer termal kaynaklı alt tabaka sorunlarına yol açabilecek ısı birikimini önlemeye yardımcı olur.
- Doğru Dalga Boyunun Seçilmesi: Lazer dalga boyunun hem alt tabakanın hem de kirleticilerin emilim özelliklerine uyması, temizleme seçiciliğini artırır, verimliliği yükseltir ve alt tabaka maruziyetini en aza indirir.
İleri Teknikler
- Patlama Modu Çalışması: Tek bir darbeyi bir dizi alt darbeye bölerek, patlama modu toplam enerjiyi korurken tepe darbe yoğunluğunu azaltır ve böylece yüzeydeki termal ve mekanik stresi hafifletir.
- Çoklu Darbe Üst Üste Binme: Düşük enerjili darbeler kullanılarak kirleticilerin birden fazla geçişte çıkarılması, malzemenin kademeli olarak aşındırılmasına olanak tanır ve alt tabaka üzerindeki etkiyi önemli ölçüde azaltır.
- Işın Şekillendirme: Gelişmiş optikler, lazer enerjisini hedef alan boyunca daha eşit bir şekilde dağıtabilir, böylece lokal aşırı ısınma önlenir ve tutarlı lazer yüzey hazırlama sonuçları sağlanır.
İzleme ve geri bildirim
- Sıcaklık izleme: Sıcaklık, termal hasarı etkileyen önemli bir faktördür. Temizleme alanına kızılötesi termal görüntüleyiciler veya termokupl sensörleri yerleştirerek, alt tabaka yüzey sıcaklığının değişen eğilimi gerçek zamanlı olarak kavranabilir. Sıcaklık erime noktasına veya termal stresin kritik değerine yakın olduğunda, sistem darbe enerjisini hemen azaltabilir veya tekrarlama oranını düşürerek malzemenin erimesini, deforme olmasını veya termal çatlamasını etkili bir şekilde önleyebilir. Bu geri bildirim mekanizması, hassas üretim alanında lazer temizliğinin güvenliğini ve güvenilirliğini büyük ölçüde iyileştirmiştir.
- Akustik izleme: Ultrasonik kalınlık ölçüm cihazları gibi akustik izleme teknolojisi, temizleme işlemi sırasında alt tabakanın kalınlık değişikliklerini etkili bir şekilde izleyebilir. Sistem, gerçek zamanlı olarak veri toplayarak aşırı malzeme çıkarımının olup olmadığını belirleyebilir, zamanında uyarılar verebilir ve lazer parametrelerini ayarlayabilir. Örneğin, Çin patenti CN112044874A, aşırı temizlemeden kaynaklanan yapısal hasarı önlemek için ultrasonik geri bildirimle birleştirilmiş gerçek zamanlı bir lazer temizleme sistemi önermektedir.
- Optik geri bildirim: Optik koherens tomografi (OCT), kirleticilerin tamamen giderilip giderilmediğini ve alt tabaka yüzeyinde hasar olup olmadığını doğru bir şekilde belirleyebilen temizleme alanı için yüksek çözünürlüklü üç boyutlu görüntüleme yetenekleri sağlar. Geleneksel görsel sistemlerle karşılaştırıldığında, OCT daha güçlü penetrasyona ve doğruluğa sahiptir ve özellikle yüksek hassasiyetli veya çok katmanlı yapı yüzeylerinin temizleme etkisini değerlendirmek için uygundur.
Hassas lazer parametre kontrolünü gelişmiş teknolojilerle entegre ederek, darbeli lazer temizliği sırasında alt tabaka hasarı riski büyük ölçüde azaltılabilir. Bu stratejiler, havacılık, yarı iletken üretimi ve kültürel miras restorasyonu gibi yüzey bütünlüğünün çok önemli olduğu uygulamalarda özellikle kritik öneme sahiptir. Doğru uygulama yalnızca temizleme performansını artırmakla kalmaz, aynı zamanda uzun vadeli malzeme dayanıklılığını ve güvenliğini de destekler.
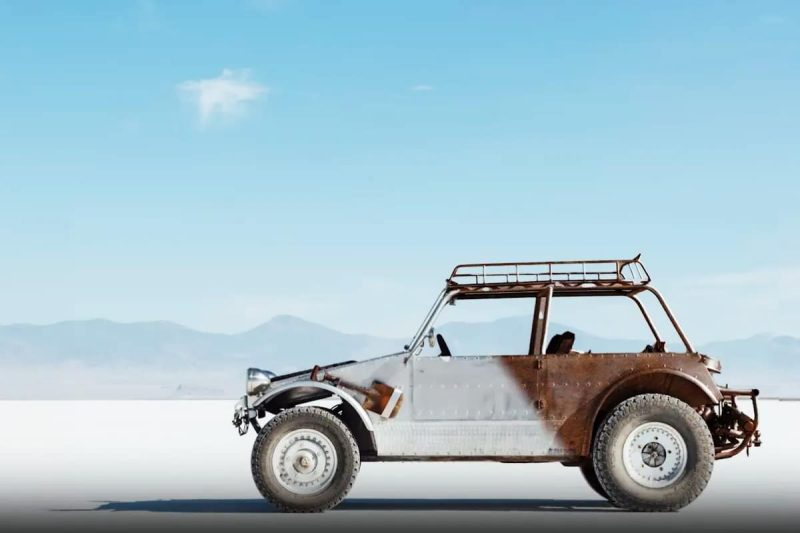
Vaka Çalışmaları ve Uygulamalar
Temassız yapısı, yüksek seçiciliği ve sarf malzemesi içermeyen çalışmasıyla darbeli lazer temizleme, çeşitli üst düzey endüstrilerde başarıyla uygulanmıştır. Bu gerçek dünya uygulamaları, teknolojinin karmaşık yüzey işlemlerini ele almadaki güvenilirliğini ve endüstriyel değerini göstermektedir.
Yarıiletken Endüstrisi
Yarı iletken üretiminde, mikron boyutundaki parçacık kontaminasyonu bile çip performansını düşürebilir veya üretim hatalarına neden olabilir. Geleneksel temizleme yöntemleri, parçacık giderme sırasında statik elektrik oluşturabilir veya gofret yüzeyine zarar verebilir. Darbeli lazer temizleme (özellikle femtosaniye lazer darbeleriyle (örneğin, 233 fs)) lazer kaynaklı mikro şok dalgalarını kullanarak mikroskobik düzeyde neredeyse hiç termal etki olmadan cam alt tabakalardan kirleticileri hassas bir şekilde temizler. Bu yüksek hassasiyetli ve düşük hasarlı temizleme yöntemi, gelişmiş çip üretim hatlarında giderek önemli bir süreç haline geliyor.
Otomotiv endüstrisi
Motor bakımı, türbin kanat yenilemesi ve hidrolik sistem servisinde pas ve ağır kirleticilerin etkili bir şekilde çıkarılması hayati önem taşır. Darbeli lazer temizleme, metal yüzeylerdeki kirletici katmanlarına güçlü enerji bağlantısı sağlayarak, kritik bileşenlerin boyutsal doğruluğunu veya yüzey bütünlüğünü etkilemeden hassas sıyırma sağlar. Yüksek tekrarlanabilirliği ve otomasyon kolaylığı, onu modern endüstriyel üretim hatları için ideal bir seçim haline getirir, parçaların hizmet ömrünü etkili bir şekilde uzatır ve ekipman güvenilirliğini artırır.
Kültürel Mirasın Korunması
Tarihi eserleri ve binaları temizlemek son derece hassas bir işlem gerektirir; orijinal malzemeye zarar vermeden kirleticileri tamamen temizler. Ultra hızlı darbeli lazer teknolojisi, taş, metal ve seramik gibi malzemelerin "yumuşak" bir şekilde temizlenmesini sağlar. Genellikle biyofilmleri, çevresel kiri ve korozyon ürünlerini temizlemek için kullanılır. Kimyasal veya mekanik temizlemeye kıyasla, lazer yöntemleri ikincil kirliliği ve fiziksel aşınmayı önler ve dünya çapında müzelerde, restorasyon laboratuvarlarında ve miras koruma projelerinde yaygın olarak kullanılır.
Hassas elektronikten ağır sanayiye ve kültürel mirasın korunmasına kadar, darbeli lazer temizliğinin son derece verimli, güvenli ve kontrol edilebilir bir modern temizlik çözümü olduğu kanıtlanmıştır. Lazer teknolojisi ve akıllı kontrol sistemleri gelişmeye devam ettikçe, uygulama kapsamı daha da genişleyecek ve endüstriler genelinde yüzey temizleme süreçlerinin giderek daha yüksek standartları karşılamasını sağlayacaktır.
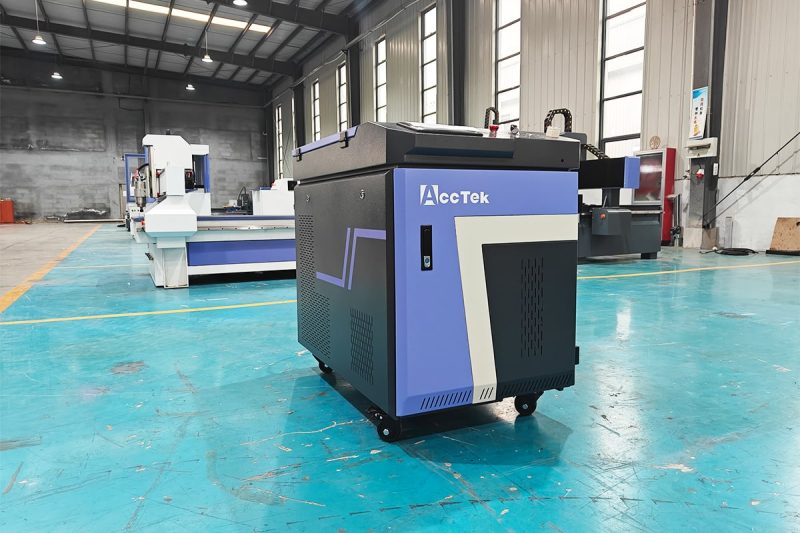
Zorluklar ve Sınırlamalar
Temassız çalışma, yüksek hassasiyet ve çevre dostu olma gibi avantajlarına rağmen, darbeli lazer temizliğinin pratikte uygulanması ve endüstriler genelinde daha geniş bir şekilde benimsenmesi konusunda hala bazı zorluklarla karşı karşıya olduğu görülmektedir:
Maliyet: Lazer temizleme sistemleri genellikle yüksek performanslı lazer jeneratörleri, hassas kontrol üniteleri ve soğutma sistemleri içerir ve ilk yatırımları nispeten büyüktür. Küçük ve orta ölçekli işletmeler için, edinim maliyeti ve uzun vadeli bakım, tanıtımın önündeki en büyük engel olabilir. Aynı zamanda, femtosaniye veya pikosaniye lazer jeneratörleri gibi bazı üst düzey sistemler daha yüksek destekleyici ekipman ve bakım maliyetlerine sahiptir ve yatırım getirisinin tartılması gerekir.
Malzeme Uyumluluğu: Yüksek yansıtıcılığa sahip (alüminyum veya bakır gibi) veya şeffaflığa sahip (cam veya plastik gibi) belirli malzemeler lazer enerjisini zayıf bir şekilde emer, bu da temizleme işleminin etkinliğini azaltır veya başarısız olmasına neden olur. Dahası, lazer dalga boyu hedef malzemenin optik emilim özelliklerine tam olarak uymalıdır; bu, çok malzemeli kompozit yüzeyleri temizlerken özellikle karmaşık bir gerekliliktir.
Maliyet ve teknik zorluklar devam ederken, darbeli lazer temizleme, üst düzey endüstriyel uygulamalarda güvenilir ve gelişmiş bir çözüm olarak kendini kanıtlamaya devam ediyor. Ekipman minyatürleştirme, maliyet düşürme ve akıllı işletim sistemlerindeki devam eden gelişmelerle, bu sınırlamaların zamanla azalması ve çeşitli endüstriyel ortamlarda daha geniş bir şekilde benimsenmesinin önünü açması bekleniyor.
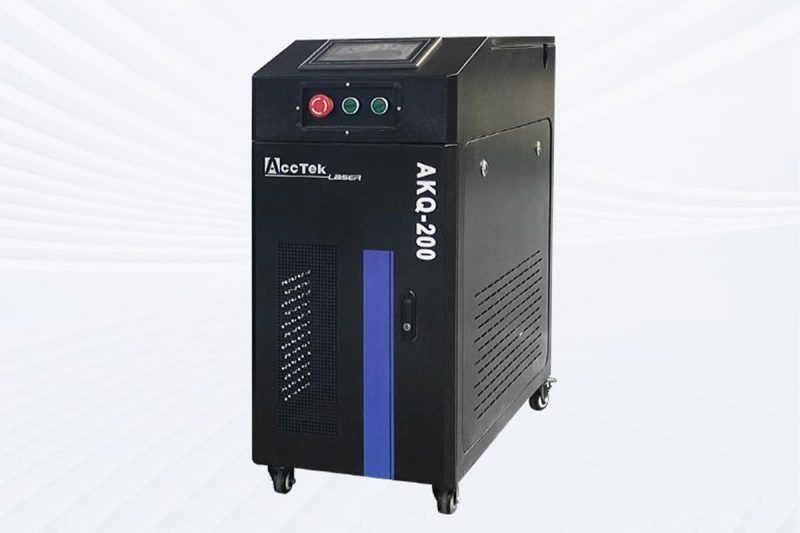
Özet
Temassız, yüksek hassasiyetli ve çevre dostu avantajlarıyla darbeli lazer temizleme teknolojisi, modern endüstrilerde geniş uygulama potansiyeli göstermiştir. Darbe süresi, enerji ve dalga boyu gibi lazer parametrelerini hassas bir şekilde kontrol ederek ve gelişmiş izleme ve geri bildirim sistemleri uygulayarak, bu teknoloji, alt tabakaya verilen hasarı en aza indirirken yüzey kirleticilerini etkili bir şekilde giderebilir ve temizleme işlemi sırasında hem verimliliği hem de güvenliği sağlayabilir. Yarı iletkenler, otomotiv, havacılık ve kültürel mirasın korunması gibi üst düzey alanlardaki başarılı uygulamaları, muazzam potansiyelini ve teknik güvenilirliğini daha da doğrulamaktadır.
Ancak, darbeli lazer temizleme teknolojisinin birçok sektörde elde ettiği olumlu sonuçlara rağmen, işletmelerin benimsemeyi değerlendirirken maliyet, operasyonel karmaşıklık ve malzeme uyumluluğu gibi faktörleri hala göz önünde bulundurmaları gerekir. Lazer temizleme ekipmanına yapılan ilk yatırım nispeten yüksektir ve operatörlerin sistemin verimli bir şekilde çalışmasını sağlamak için profesyonel teknik eğitime ihtiyaçları vardır. Ek olarak, belirli yüksek yansıtıcı veya şeffaf malzemeler özel lazer dalga boyları ve parametre ayarları gerektirebilir. Bu nedenle, işletmelerin optimum temizleme sonuçları ve minimum alt tabaka hasarı sağlamak için belirli uygulamalarda kapsamlı bir değerlendirme yapmaları gerekir.
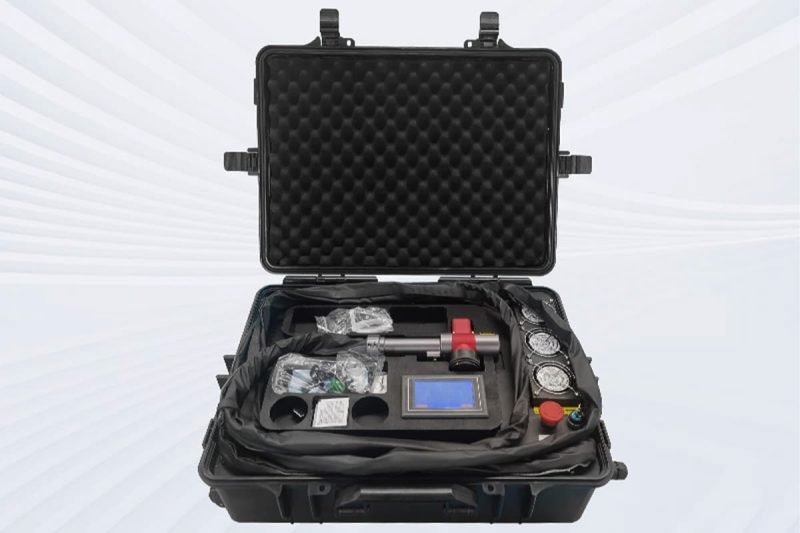
Lazer Çözümü Elde Etme
Önde gelen bir lazer ekipmanı üreticisi olarak, AccTek Lazer yüksek kalite sağlamaya kendini adamıştır darbeli lazer temizleme makineleri Müşterilerin verimli ve güvenli temizlik sonuçları elde etmelerine ve çeşitli endüstriyel temizlik ihtiyaçlarını karşılamalarına yardımcı olmak. İster hassas elektronikler, ister ağır sanayi veya kültürel miras olsun, müşterilere çeşitli temizlik zorluklarını karşılamak için özelleştirilmiş lazer çözümleri sağlayabiliriz.
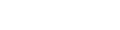
İletişim bilgileri
- [email protected]
- [email protected]
- +86-19963414011
- 3 Bölge A, Lunzhen Sanayi Bölgesi, Yucheng Şehri, Shandong Eyaleti.
Lazer Çözümleri Alın