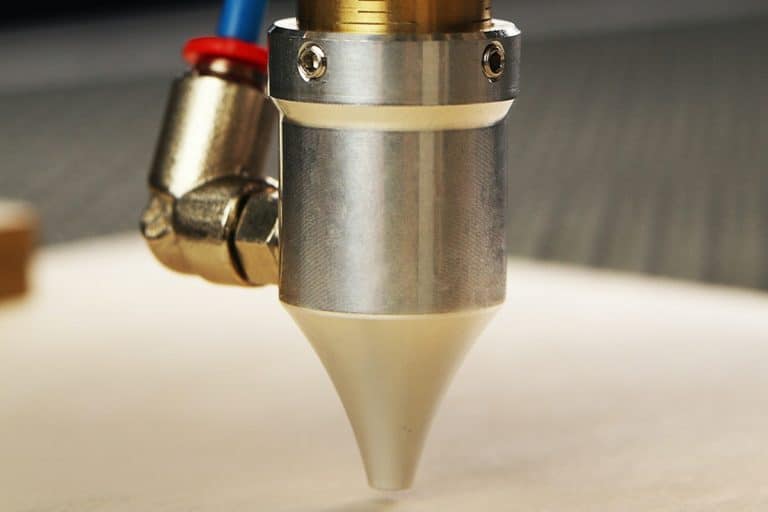
Common Defects in CO2 Laser Cutting and Their Mitigation Methods
This article mainly introduces the principles, common defects, and optimization measures of CO2 laser cutting to improve processing quality and stability.
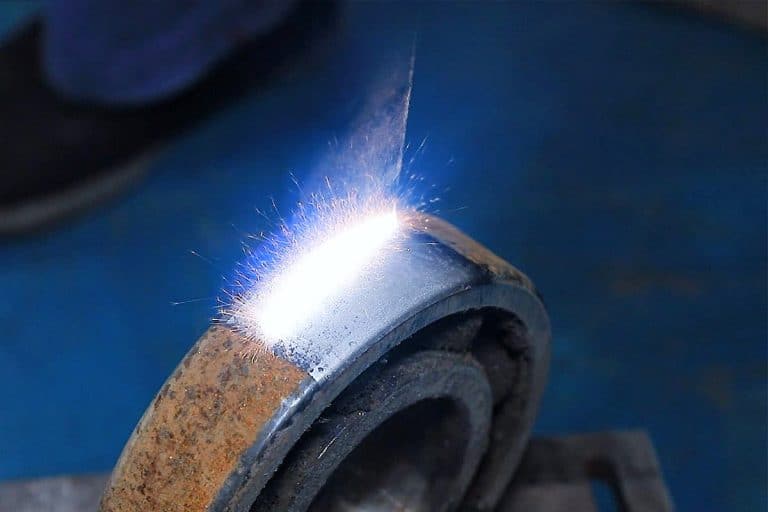
Will Pulsed Laser Cleaning Damage the Substrate?
This article provides a comprehensive overview of how pulsed laser cleaning works, the mechanisms that may cause substrate damage, influencing factors, and effective strategies to ensure safe and efficient cleaning across various industries.
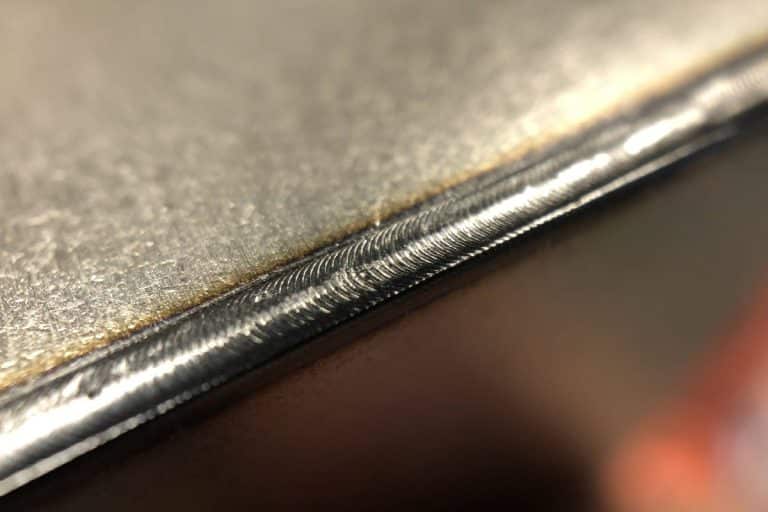
How Does Laser Welding Achieve Deep Melting of Materials?
This article mainly discusses how laser welding can achieve deep melting of materials, including its basic principles, key factors affecting penetration depth, the formation mechanism of deep penetration, and optimization control strategies to improve welding quality and production efficiency.
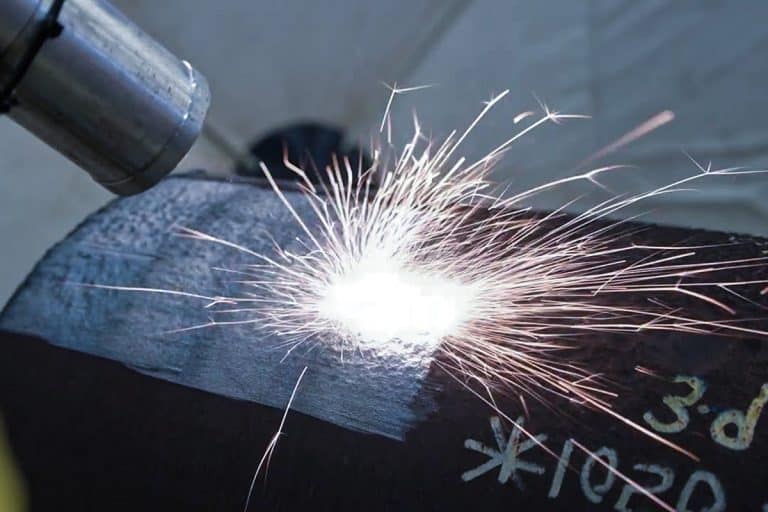
How Do Pulse Frequency and Repetition Rate Affect Laser Cleaning Efficiency?
This article will explore in depth the effects of pulse frequency and repetition rate on laser cleaning efficiency and provide optimization strategies for different applications.
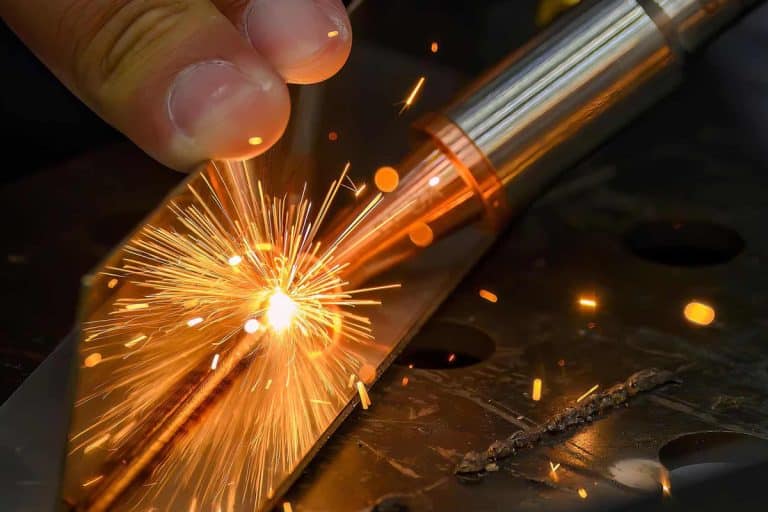
What Are the Challenges of Laser Welding Thin Materials?
This article will explore the challenges and response strategies of thin materials laser welding to help manufacturers master this technology and improve production efficiency and product quality.
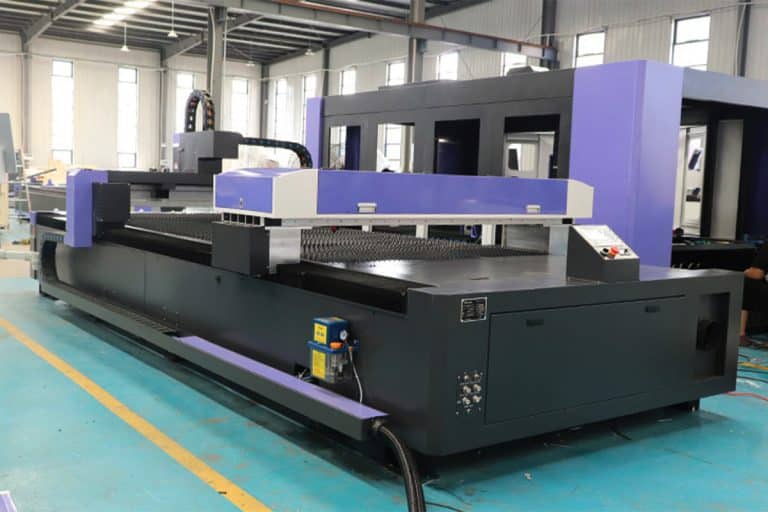
How to Achieve the Minimum Incision Width in CO2 Laser Cutting?
This article will analyze the key factors affecting the kerf width of CO2 laser cutting and provide optimization strategies to help manufacturers improve accuracy, and production efficiency, reduce material waste, and improve economic benefits.
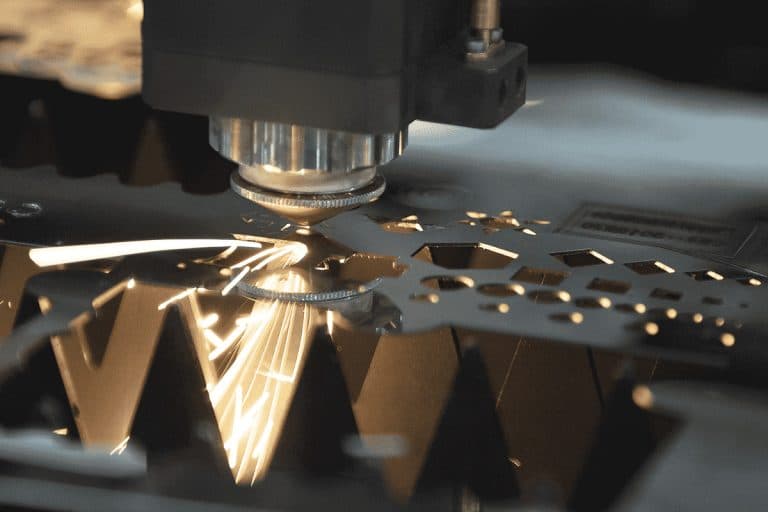
The Influence of Autofocus on the Cutting Accuracy of Fiber Laser Cutting Machine
This article discusses the definition and types of autofocus technology and its impact on fiber laser cutting accuracy and analyzes the challenges and optimization solutions it faces to improve production efficiency and processing quality.
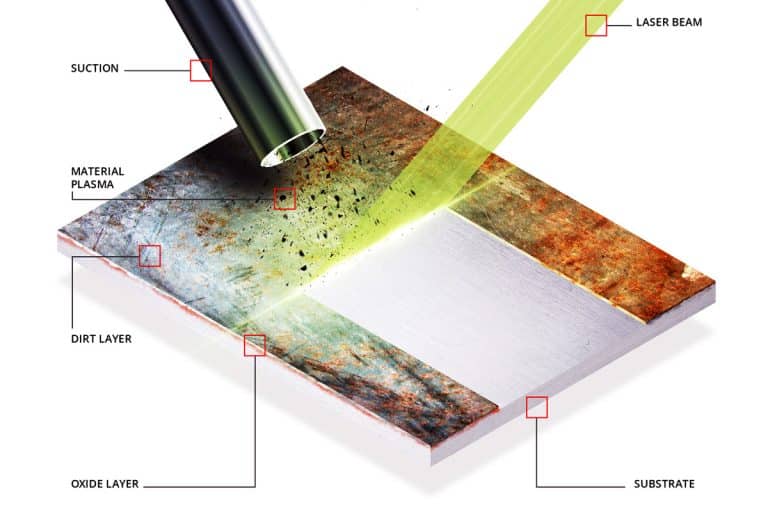
A Comprehensive Guide to Evaluating Surfaces After Laser Cleaning
This article will explore in depth the cleanliness assessment methods after laser cleaning to help companies ensure that the cleaning effect meets industry standards while optimizing production efficiency and costs.
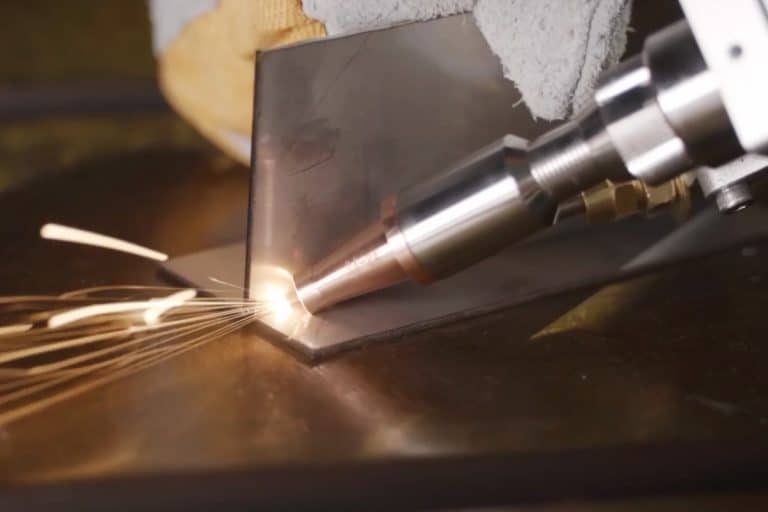
Laser Welding Joint Design
This paper mainly discusses the basic principles, influencing factors, and optimization strategies of laser welding joint design to improve welding quality, optimize production efficiency, and ensure the integrity and strength of the weld.
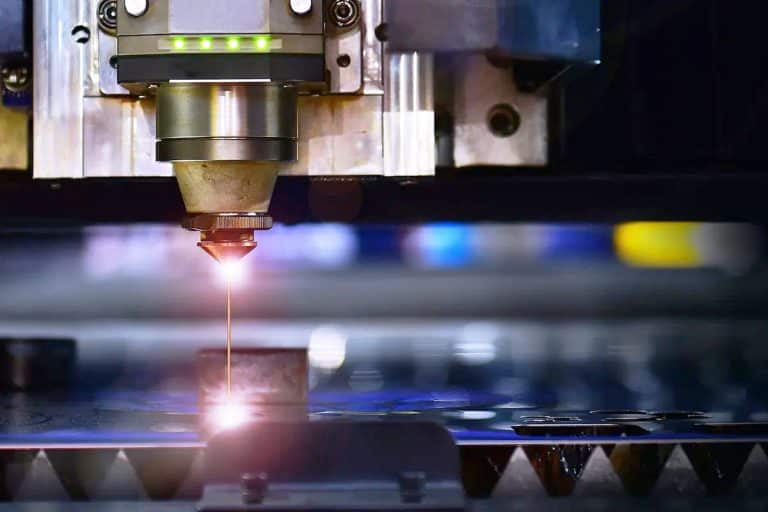
The Influence of Fiber Laser Beam Quality on Cutting Accuracy and Quality
The quality of fiber laser beam has an important influence on the accuracy, efficiency and surface quality of laser cutting. Optimizing the beam quality can significantly improve the cutting effect and production efficiency.
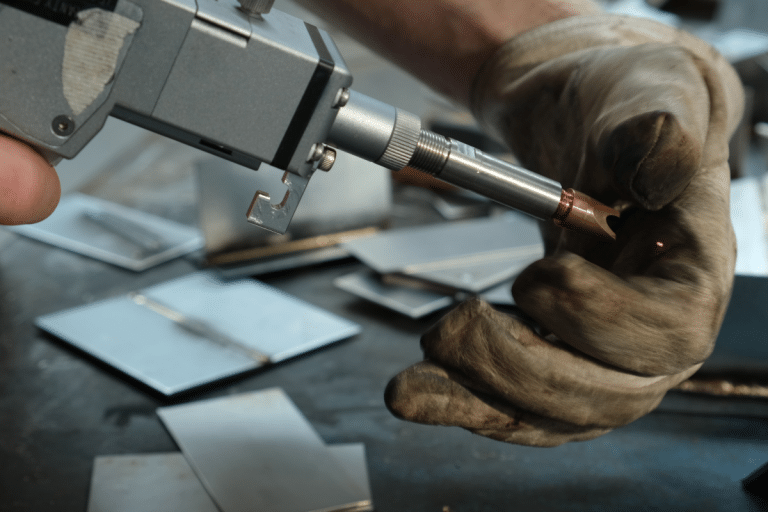
Affordable Laser Welding Machine Buying Guide
his article will analyze the many factors that contribute to the high price of laser welding machines and provide some suggestions on how to obtain an affordable and high-performance laser welding machine while meeting manufacturing needs.
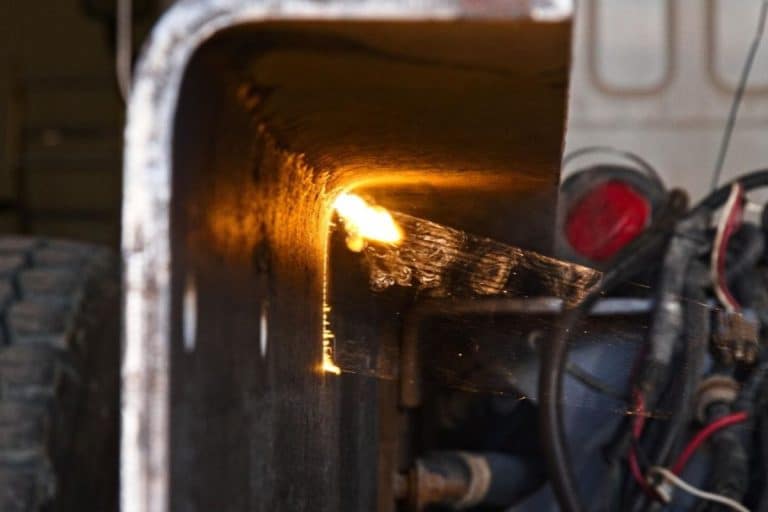
How to Maintain The Cooling System of The Laser Cleaning Machine?
This article will explain the working principle of laser cleaning machines, several common cooling system types, specific maintenance methods of laser cleaning machine cooling systems, and the importance of cooling systems, so as to ensure the efficient performance of laser cleaning machines during operation.
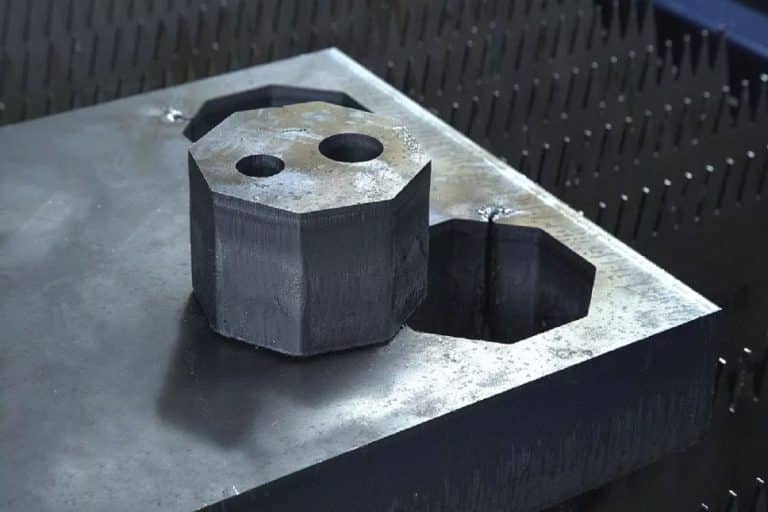
Decoding Laser Cutting Costs: Key Considerations Unveiled
This article discusses the cost-effectiveness of laser cutting, explores the cost considerations related to laser cutting, and conducts a comparative analysis of laser cutting costs and benefits.
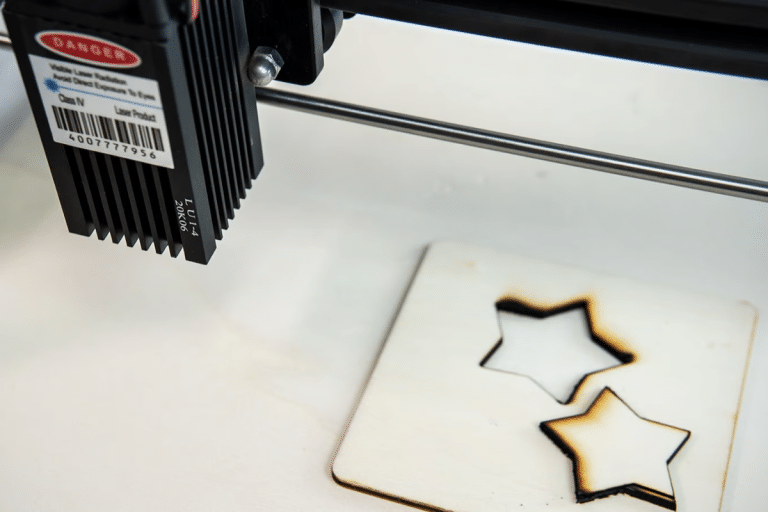
Safety Precautions When Using CO2 Laser Cutting Machine
This article will discuss in detail the specific safety precautions when using a CO2 laser cutting machine to ensure the safety of the operator and the efficient operation of the equipment.
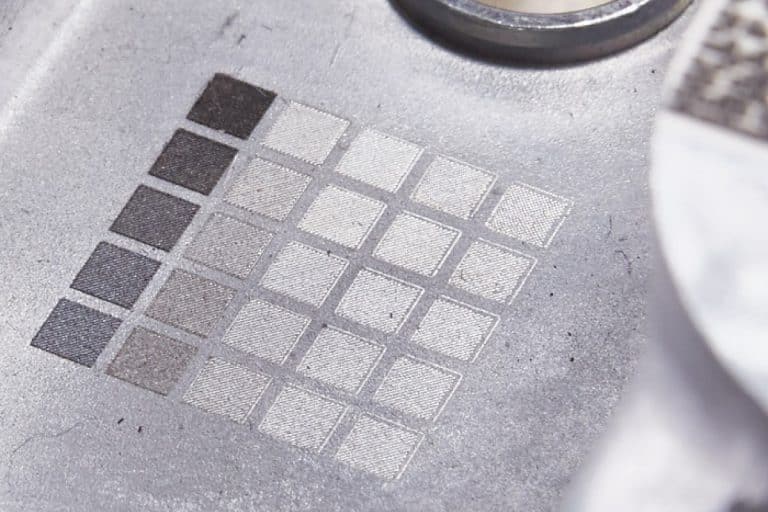
Revealing the Depth of Laser Marking: Discovering Maximum Laser Marking Depth
Laser marking is a versatile and precise technology, and marking depth is a key parameter that determines the longevity, visibility, and functionality of the marked material. This article will fully reveal the complexities of laser marking maximum depth.
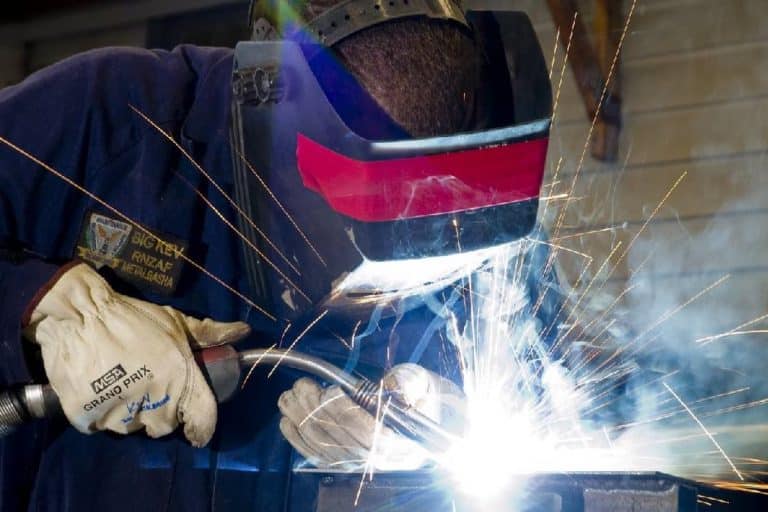
Welding Methods Comparison: Unveiling Optimal Performance
This article will compare several common welding methods, including laser welding, tungsten inert gas welding, metal inert gas welding, shielded metal arc welding, submerged arc welding, and resistance spot welding, to understand their working principles and discuss which welding method has The most outstanding performance.
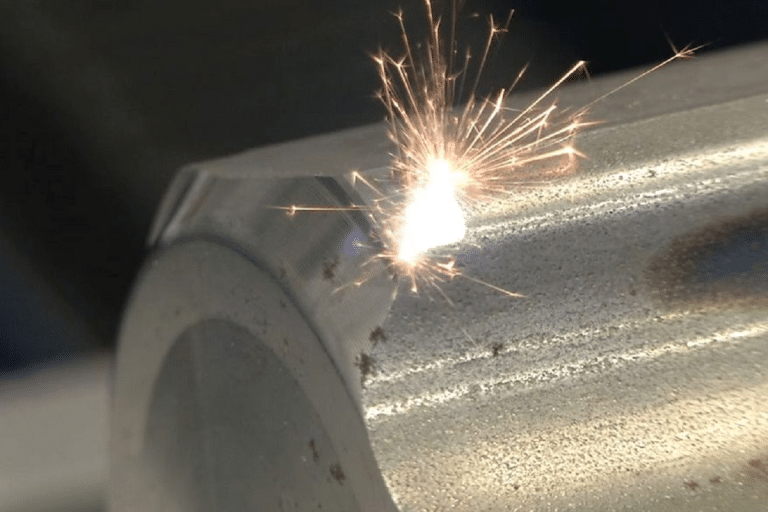
Laser Cleaning: Eco-Friendly Assessment
This article will delve into the working principles and advantages of laser cleaning, the potential impacts on the environment caused by the use of laser cleaning machines, and environmentally friendly measures.
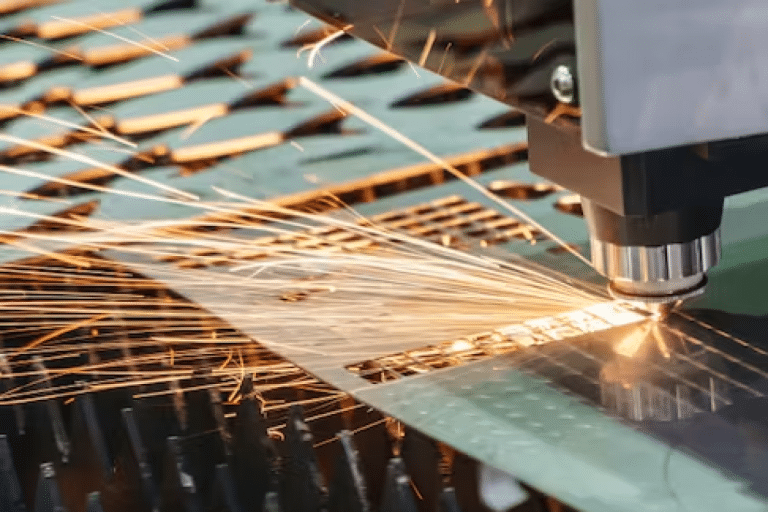
Laser Cutting VS Sawing
This article will take an in-depth look at two mainstream cutting technologies – sawing and laser cutting, understand how they work, and compare their advantages and disadvantages in the field of material processing to help readers better choose the cutting method that suits their needs.
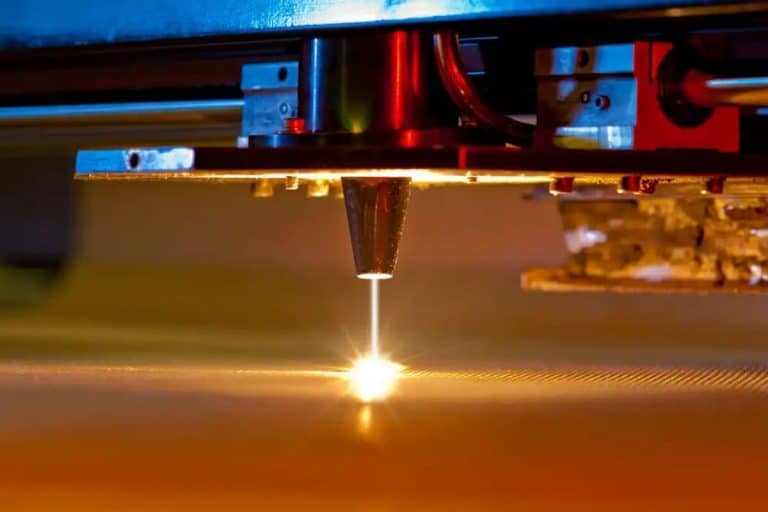
Mastering CO2 Laser Cutting: Essential Skills And Training
This article will discuss the necessary skills and training to operate a CO2 laser cutting machine, explain the potential risks when using a CO2 laser cutting machine, and understand the specific safety operation requirements to better ensure that operators can use CO2 laser cutting machines safely and efficiently.
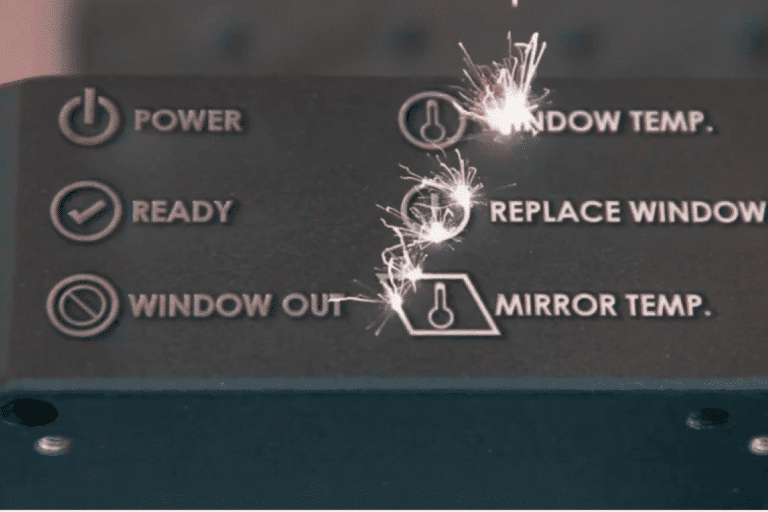
How Accurate is Laser Marking?
Laser marking provides a highly precise and efficient method of adding permanent marks to a variety of materials. Let’s take a look at how accurate laser marking is and what factors affect laser marking accuracy.
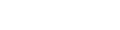
- [email protected]
- [email protected]
- +86-19963414011
- No. 3 Zone A, Lunzhen Industrial Zone,Yucheng City , Shandong Province.