Pulse Laser Cleaning Machine
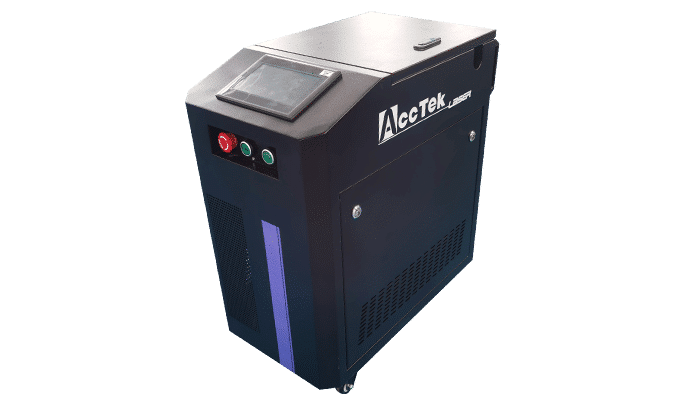
Product Range
-
Pulse Laser Cleaning Machine
Rated 4.75 out of 5$5,900.00 – $65,300.00 Select options This product has multiple variants. The options may be chosen on the product page -
Luggage Pulse Laser Cleaning Machine
Rated 4.75 out of 5$6,500.00 – $16,800.00 Select options This product has multiple variants. The options may be chosen on the product page -
Backpack Pulse Laser Cleaning Machine
Rated 4.75 out of 5$6,800.00 – $9,100.00 Select options This product has multiple variants. The options may be chosen on the product page
Optional Pulse Laser Cleaning Machine Power
Materials and Surfaces That Can Be Cleaned
Laser Cleaning VS. Other Methods
Laser Cleaning vs. Sandblasting
Sandblasting involves abrasive materials that can damage surfaces and cause wear over time. Laser cleaning, on the other hand, is a non-contact method that eliminates the risk of surface abrasion. It also reduces waste and eliminates the need for disposal of cleaning media, making it a more environmentally friendly option for industrial cleaning.
Laser Cleaning vs. Chemical Cleaning
Chemical cleaning typically requires the use of hazardous solvents, which can be harmful to the environment and human health. Laser cleaning is a solvent-free process, reducing environmental impact while ensuring precise, effective removal of contaminants without leaving any chemical residues. This makes it a safer, cleaner, and more sustainable choice.
Laser Cleaning vs. High-Pressure Water Cleaning
High-pressure water cleaning can cause damage to sensitive parts and is not always effective on tough contaminants like rust or coatings. Laser cleaning, however, uses focused laser pulses that precisely target contaminants without affecting the underlying surface. It’s a dry, efficient method that eliminates the need for water, drying time, or messy cleanup.
Why Choose AccTek Laser
Advanced Laser Technology
We use the latest laser technology to provide precise, efficient, and reliable cleaning solutions. Our machines are engineered for high-performance cleaning, ensuring superior results across a wide range of materials and contaminants.
Environmentally Friendly
AccTek Laser machines offer a sustainable cleaning solution. With no chemicals, no abrasive materials, and minimal waste, our technology reduces environmental impact while maintaining the highest cleaning standards.
Cost-Effective Solutions
By eliminating the need for consumables such as chemicals, abrasives, or solvents, our laser cleaning machines help you cut costs in the long term. The durability and low maintenance of our machines further enhance cost-effectiveness.
Versatility Across Industries
Whether in automotive, aerospace, manufacturing, or any other industry, our laser cleaning machines are designed for versatile use. They can handle a variety of materials and contaminants, making them ideal for a wide array of applications.
Precision and Safety
AccTek Laser's machines ensure a non-contact, precise cleaning process, reducing the risk of damage to delicate surfaces. The user-friendly design and safety features ensure your operators can work with confidence and efficiency.
Exceptional Customer Support
We provide comprehensive customer support before, during, and after the sale. Our dedicated team offers expert guidance on machine selection, operation, and maintenance, ensuring your investment performs at its best.
Frequently Asked Questions
How Do Pulse Laser Cleaning Machines Work?
- Laser Generation: The machine generates laser pulses using a laser source. These pulses are characterized by their high peak power and very short duration, typically in the nanosecond to picosecond range.
- Laser Beam Delivery: The laser beam is delivered to the surface through a series of optical components, including mirrors and lenses, which focus the beam to a precise spot on the target material.
- Surface Interaction: When the focused laser pulses hit the surface, they rapidly heat and vaporize the contaminants or unwanted materials, such as rust, paint, or coatings. This process occurs in a localized area, allowing for precise cleaning.
- Material Removal: The vaporized material is ejected from the surface in the form of tiny particles. This process, known as ablation, removes the contaminants without damaging the underlying substrate.
- Non-Contact Cleaning: Since the laser beam does not physically touch the surface, there is no mechanical abrasion or wear on the material being cleaned. This makes pulse laser cleaning suitable for delicate and sensitive surfaces.
- Controlled Operation: The machine’s parameters, such as pulse duration, energy, repetition rate, and scan speed, can be precisely controlled to optimize the cleaning process for different materials and contamination levels.
- Safe and Eco-Friendly: The process eliminates the need for chemical solvents or abrasive materials, making it an environmentally friendly and safe cleaning method.
How Does Pulse Laser Cleaning Compare to Traditional Cleaning Methods?
- Precision and Control
- Pulse Laser Cleaning: Delivers exceptional precision, allowing for selective removal of contaminants without damaging the underlying material.
- Traditional Methods: Often lack this level of control, which can result in surface damage, especially with abrasive techniques.
- Non-Contact Cleaning
- Pulse Laser Cleaning: Utilizes a non-contact process that prevents mechanical wear and tear on the surface.
- Traditional Methods: Involve physical contact, leading to potential abrasion and surface degradation over time.
- Environmental Impact
- Pulse Laser Cleaning: Eco-friendly, as it eliminates the need for harmful chemicals and reduces waste production.
- Traditional Methods: Frequently involve chemical solvents that can be hazardous to the environment and require special disposal.
- Versatility
- Pulse Laser Cleaning: Effective on a wide range of materials and contaminants, including rust, paint, and delicate coatings.
- Traditional Methods: Often require different techniques and chemicals for different types of contaminants and surfaces.
- Safety
- Pulse Laser Cleaning: Generally safer for operators, minimizing exposure to harmful chemicals and reducing the risk of physical injury.
- Traditional Methods: Can expose workers to hazardous chemicals and necessitate protective gear to mitigate risks.
- Efficiency and Speed
- Pulse Laser Cleaning: Often more efficient, capable of quickly cleaning surfaces and reducing downtime.
- Traditional Methods: This can be time-consuming, especially when multiple steps or repeated applications are needed.
- Maintenance and Operating Costs
- Pulse Laser Cleaning: Lower maintenance costs due to its non-contact nature and reduced need for consumables.
- Traditional Methods: Higher operating costs due to the need for consumables (chemicals, abrasive materials) and frequent equipment maintenance.
- Residue and Cleanliness
- Pulse Laser Cleaning: Leaves minimal residue, ensuring a clean surface post-treatment.
- Traditional Methods: Can leave residues that require additional cleaning steps.
- Adaptability to Complex Shapes
- Pulse Laser Cleaning: Highly adaptable to cleaning complex geometries and hard-to-reach areas.
- Traditional Methods: May struggle with intricate shapes, often requiring manual effort for thorough cleaning.
How Do You Choose The Appropriate Power for Specific Cleaning Tasks?
- Type of Contaminant
- Light Contaminants: For light contaminants like dust, thin oxides, or light surface rust, lower power settings (100W-200W) are usually sufficient.
- Heavy Contaminants: For heavy rust, thick paint layers, or more stubborn residues, higher power settings (500W-1000W) may be necessary to effectively remove the material.
- Material of the Substrate
- Delicate Materials: For delicate surfaces like historical artifacts, thin metals, or sensitive materials, using a lower power setting (100W-200W) is advisable to avoid damaging the substrate.
- Robust Materials: For more robust materials such as steel, cast iron, or heavily corroded surfaces, higher power levels (500W-1000W) can be used.
- Surface Area and Cleaning Speed
- Small Areas or Precision Cleaning: For small, detailed areas or tasks requiring high precision, lower power settings combined with slower scan speeds allow for careful control.
- Large Areas or Quick Cleaning: For larger surfaces or tasks where speed is critical, higher power settings with faster scan speeds can expedite the process.
- Desired Finish
- Smooth Finish: Lower power settings can help achieve a smoother finish without pitting or over-roughening the surface.
- Aggressive Cleaning: Higher power settings can be used for aggressive cleaning tasks where the finish is less critical, and thorough contaminant removal is the priority.
- Testing and Calibration
- Initial Tests: Conduct small-scale tests on a less critical part of the surface to determine the appropriate power setting. Start with lower power and gradually increase until the desired cleaning effect is achieved.
- Adjustments: Continuously monitor the cleaning process and adjust the power settings as needed based on real-time observations and results.
- Manufacturer Guidelines
- Consult Documentation: Refer to the manufacturer’s guidelines and documentation for recommendations on power settings for various materials and contaminants.
- Technical Support: Utilize the manufacturer’s technical support for advice on setting adjustments for specific tasks.
- Experience and Expertise
- Operator Experience: Experienced operators can make informed decisions based on past projects and familiarity with the equipment.
- Training: Ensure that operators are well-trained in adjusting power settings and understanding the effects on different surfaces.
What Training Is Necessary For Operating Pulse Laser Cleaning Machines?
- Understanding the Equipment
- Machine Components: Familiarize with all parts of the pulse laser cleaning machine, including the laser source, control panel, optics, and safety features.
- Operational Principles: Learn how the laser pulses interact with different materials and contaminants.
- Safety Training
- Laser Safety: Comprehensive training on laser safety standards, including understanding laser classes, potential hazards, and safety protocols.
- Protective Gear: Proper use of personal protective equipment (PPE) such as laser safety glasses, gloves, and appropriate clothing.
- Safety Interlocks: Knowledge of safety interlocks and emergency shutoff procedures.
- Basic Laser Physics
- Laser Fundamentals: Basic understanding of how lasers work, including concepts like wavelength, pulse duration, and energy.
- Material Interaction: How different materials respond to laser exposure, including absorption and reflection.
- Machine Operation
- Start-Up and Shutdown Procedures: Step-by-step instructions on safely starting and shutting down the machine.
- Control Settings: How to adjust power settings, pulse frequency, scan speed, and focus for different cleaning tasks.
- Calibration: Procedures for calibrating the machine for specific materials and contaminants.
- Maintenance and Troubleshooting
- Routine Maintenance: Regular maintenance tasks to keep the machine in optimal working condition.
- Common Issues: Identifying and troubleshooting common operational issues.
- Service Schedules: Understanding when and how to schedule professional servicing.
- Application Techniques
- Surface Preparation: Preparing surfaces before cleaning.
- Cleaning Techniques: Best practices for effective cleaning, including beam path planning and managing overlap.
- Result Assessment: Evaluating the effectiveness of the cleaning process and making necessary adjustments.
- Software Training
- User Interface: Navigating the machine’s software interface.
- Data Input: Entering and adjusting cleaning parameters.
- Data Analysis: Using software tools to analyze cleaning results and optimize settings.
- Health and Environmental Considerations
- Ventilation: Ensuring adequate ventilation to remove fumes and particles generated during the cleaning process.
- Waste Management: Proper disposal of any waste materials by environmental regulations.
- Hands-On Practice
- Supervised Operation: Initial supervised operation of the machine under the guidance of an experienced operator.
- Real-World Scenarios: Practicing various materials and contaminant types to gain confidence and experience.
- Certification and Continuing Education
- Certification: Obtaining certification from the machine manufacturer or an accredited training provider.
- Continuing Education: Regularly updating skills and knowledge to keep up with advancements in laser cleaning technology.
What Is The Environmental Impact of Pulse Laser Cleaning?
- Reduction of Chemical Use
- No Hazardous Chemicals: Pulse laser cleaning eliminates the need for harsh chemical solvents, which are often used in traditional cleaning methods. This reduces the risk of chemical spills and contamination.
- Eco-Friendly Process: By avoiding chemicals, pulse laser cleaning contributes to a cleaner and safer environment.
- Minimal Waste Production
- Reduced Waste: Traditional methods, such as sandblasting, generate significant amounts of waste, including used abrasives and contaminated water. Pulse laser cleaning produces minimal waste, primarily in the form of small particles or dust, which are easier to manage and dispose of safely.
- Cleaner Disposal: The small amount of residue produced by laser cleaning can often be collected with simple filtration systems, reducing the environmental burden.
- Energy Efficiency
- Targeted Cleaning: Laser cleaning is highly efficient, focusing energy precisely where it is needed. This reduces overall energy consumption compared to processes that require extensive manual labor or multiple cleaning steps.
- Lower Carbon Footprint: The efficiency of the laser cleaning process contributes to a lower carbon footprint, as less energy is required for operation and waste disposal.
- Reduced Water Use
- Waterless Process: Unlike methods such as hydro blasting, which use large volumes of water, pulse laser cleaning is a dry process. This conserves water resources and reduces the need for water treatment and disposal systems.
- No Contaminated Water: By not using water, there is no risk of creating contaminated runoff that can pollute local water sources.
- Less Environmental Disturbance
- Noise and Dust Control: Laser cleaning is generally quieter and produces less dust than abrasive methods. This reduces noise pollution and the spread of airborne contaminants.
- Localized Impact: The precise nature of laser cleaning means that it has a localized impact, minimizing disruption to surrounding areas and ecosystems.
- Health and Safety Benefits
- Reduced Exposure to Toxins: Operators are not exposed to toxic chemicals or heavy metals, which are common in traditional cleaning methods. This improves workplace safety and reduces health risks.
- Safer Work Environment: The improved safety profile of laser cleaning translates to less environmental contamination from accidental spills or mishandling of hazardous materials.
- Long-Term Sustainability
- Extended Lifespan of Materials: By preserving the integrity of the cleaned surfaces, pulse laser cleaning can extend the lifespan of materials, reducing the need for replacements and conserving resources.
- Promotes Green Practices: The adoption of pulse laser cleaning supports broader environmental sustainability goals and encourages the use of green technologies in industrial processes.
Are There Any Limitations to Using Pulse Laser Cleaning Machines?
- Initial Cost
- High Purchase Price: The initial investment for pulse laser cleaning machines can be significant compared to traditional cleaning methods, which may be a barrier for small businesses or low-budget projects.
- Specificity of Use
- Material Limitations: Not all materials respond well to laser cleaning. Some plastics and reflective surfaces can be challenging to clean effectively without causing damage or inefficient cleaning results.
- Surface Preparation: Certain surfaces may require pre-treatment or specific conditions to be suitable for laser cleaning.
- Technical Expertise Required
- Training Needs: Operating a pulse laser cleaning machine requires specialized training to ensure safe and effective use. This can involve a steep learning curve and additional training costs.
- Maintenance Knowledge: Regular maintenance and troubleshooting require a good understanding of the equipment, which might necessitate hiring or training skilled personnel.
- Speed of Cleaning
- Slower for Large Areas: While pulse laser cleaning is efficient for precise and small-scale tasks, it can be slower for cleaning large areas compared to some traditional methods like sandblasting.
- Surface Finish
- Potential Surface Changes: In some cases, laser cleaning can alter the surface finish, especially at higher power settings. This might not be desirable for all applications, particularly where the original surface finish needs to be preserved.
- Energy Consumption
- Power Requirements: High-powered laser cleaning machines can have substantial energy requirements, which may lead to higher operational costs, especially in areas with expensive electricity.
- Limited Accessibility
- Complex Geometries: While laser cleaning is adaptable, it may struggle with very complex geometries or deep recesses that require the laser beam to penetrate hard-to-reach areas.
- Health and Safety Concerns
- Laser Safety Risks: Operators must follow stringent safety protocols to prevent accidents, as exposure to high-intensity laser beams can cause serious injuries, including burns or eye damage.
- Fume Management: The process can generate hazardous fumes or particulate matter, requiring adequate ventilation and fume extraction systems to ensure a safe working environment.
- Environmental Conditions
- Operational Environment: The effectiveness of laser cleaning can be influenced by environmental conditions such as ambient temperature and humidity. This might require controlled environments for optimal performance.
- Surface Damage Potential
- Over-Exposition Risks: If not properly controlled, the laser can cause surface damage, such as micro-cracking or excessive heating, particularly on sensitive materials.
- Availability of Spare Parts
- Component Replacement: Sourcing and replacing specific components for the laser system can be expensive and time-consuming, especially for high-tech parts that require specialized suppliers.
- Regulatory Compliance
- Regulatory Restrictions: Some regions may have stringent regulations regarding the use of high-powered lasers, requiring additional compliance measures and possibly limiting their usage.
What Are The Safety Considerations When Using Pulse Laser Cleaning Machines?
- Laser Safety
- Laser Classification: Understand the laser class of your machine (usually Class 4, which is the highest risk category) and follow specific safety guidelines for that class.
- Beam Control: Ensure that the laser beam is properly enclosed or directed to prevent accidental exposure. Use beam stops and barriers where necessary.
- Personal Protective Equipment (PPE)
- Laser Safety Glasses: Wear appropriate laser safety glasses that match the wavelength of the laser being used to protect against eye injuries.
- Protective Clothing: Use flame-resistant clothing to protect against potential exposure to laser radiation and other hazards.
- Gloves and Face Shields: Wear gloves to protect hands and face shields for additional face protection if needed.
- Access Control
- Restricted Access: Limit access to the area where the laser cleaning machine is operating. Use signs and barriers to keep unauthorized personnel out.
- Interlock Systems: Install interlock systems on doors and windows of the operating area to automatically shut off the laser if the area is breached.
- Training and Certification
- Operator Training: Ensure that all operators are properly trained in using the machine, and understanding laser safety, and emergency procedures.
- Certification: Obtain necessary certifications for operators as required by local regulations and standards.
- Ventilation and Fume Extraction
- Fume Extraction: Install adequate fume extraction systems to remove hazardous fumes and particles generated during the cleaning process.
- Ventilation: Ensure proper ventilation to maintain air quality and prevent the buildup of harmful substances.
- Emergency Procedures
- Emergency Shutoff: Familiarize operators with the location and use of emergency shutoff buttons and procedures.
- First Aid: Have first aid kits and trained personnel available to respond to laser-related injuries or other emergencies.
- Regular Maintenance and Inspection
- Routine Checks: Perform regular maintenance and safety inspections of the laser cleaning machine to ensure it is operating correctly and safely.
- Component Integrity: Check the integrity of safety interlocks, beam enclosures, and protective barriers regularly.
- Operational Environment
- Controlled Environment: Operate the machine in a controlled environment to minimize external factors that could affect safety, such as excessive dust or moisture.
- Stable Setup: Ensure that the laser cleaning machine is securely positioned and stable during operation to prevent accidents.
- Hazard Awareness
- Warning Signs: Use clear and visible warning signs to indicate the presence of laser radiation and other potential hazards.
- Awareness Training: Conduct regular training sessions to keep operators aware of potential hazards and updates in safety protocols.
- Compliance with Regulations
- Regulatory Standards: Comply with all relevant local, national, and international safety regulations and standards related to laser equipment and operation.
- Documentation: Maintain thorough documentation of safety procedures, training records, and equipment maintenance for compliance and audit purposes.
- Health Monitoring
- Exposure Limits: Monitor operator exposure to laser radiation and hazardous substances to ensure it remains within safe limits.
- Medical Surveillance: Implement a medical surveillance program for operators who are regularly exposed to laser radiation.
What Maintenance Is Required for Pulse Laser Cleaning Machines?
- Regular Cleaning
- Optical Components: Clean lenses, mirrors, and protective windows regularly to prevent contamination and ensure optimal laser transmission.
- Machine Exterior: Wipe down the machine’s exterior surfaces to remove dust and debris that could affect operation.
- Inspection of Laser Source
- Laser Tube or Diode: Check the laser tube or diode for signs of wear or damage. Ensure it is operating within the manufacturer’s specified parameters.
- Cooling System: Inspect and maintain the cooling system (air or water-cooled) to prevent overheating. Check for leaks, and ensure coolant levels are adequate.
- Alignment Checks
- Beam Alignment: Regularly verify the alignment of the laser beam to ensure it is properly focused and directed. Misalignment can reduce efficiency and damage components.
- Optical Path: Ensure all mirrors and lenses are correctly positioned and aligned.
- Calibration
- Power Calibration: Periodically calibrate the laser power output to ensure it matches the required settings for different cleaning tasks.
- Focus Adjustment: Adjust the focal length as needed to maintain optimal cleaning performance for various surfaces and contaminants.
- Software Updates
- Firmware and Software: Keep the machine’s firmware and control software up to date with the latest versions provided by the manufacturer.
- Backup Settings: Regularly back up machine settings and parameters to prevent data loss.
- Component Replacement
- Wear Parts: Replace consumable parts such as protective windows, filters, and seals according to the manufacturer’s recommended schedule.
- Laser Source: Depending on usage and the type of laser, the laser source (tube or diode) may need replacement after a certain number of hours of operation.
- Cooling System Maintenance
- Coolant Replacement: Replace the coolant periodically to prevent degradation and maintain effective cooling.
- Filter Cleaning: Clean or replace filters in the cooling system to ensure efficient operation.
- Safety Systems Check
- Interlocks and Safety Switches: Test all safety interlocks and emergency shutoff switches regularly to ensure they are functioning correctly.
- Protective Barriers: Inspect protective barriers and enclosures for integrity and proper function.
- Electrical System
- Wiring Inspection: Check for any loose or damaged wiring connections and secure or replace them as needed.
- Power Supply: Ensure the power supply is stable and within the specifications required for the machine.
- Fume Extraction and Ventilation
- Filter Replacement: Replace filters in fume extraction and ventilation systems as recommended to maintain air quality.
- System Inspection: Regularly inspect the fume extraction system for blockages or damage.
- Documentation and Record Keeping
- Maintenance Logs: Keep detailed records of all maintenance activities, including inspections, cleaning, part replacements, and calibration.
- Service Reports: Document any issues encountered and the corrective actions taken.
- Training and Updates
- Operator Training: Ensure operators are trained in routine maintenance procedures and aware of the machine’s maintenance schedule.
- Manufacturer Updates: Stay informed about any maintenance updates or advisories issued by the manufacturer.
Related Resources
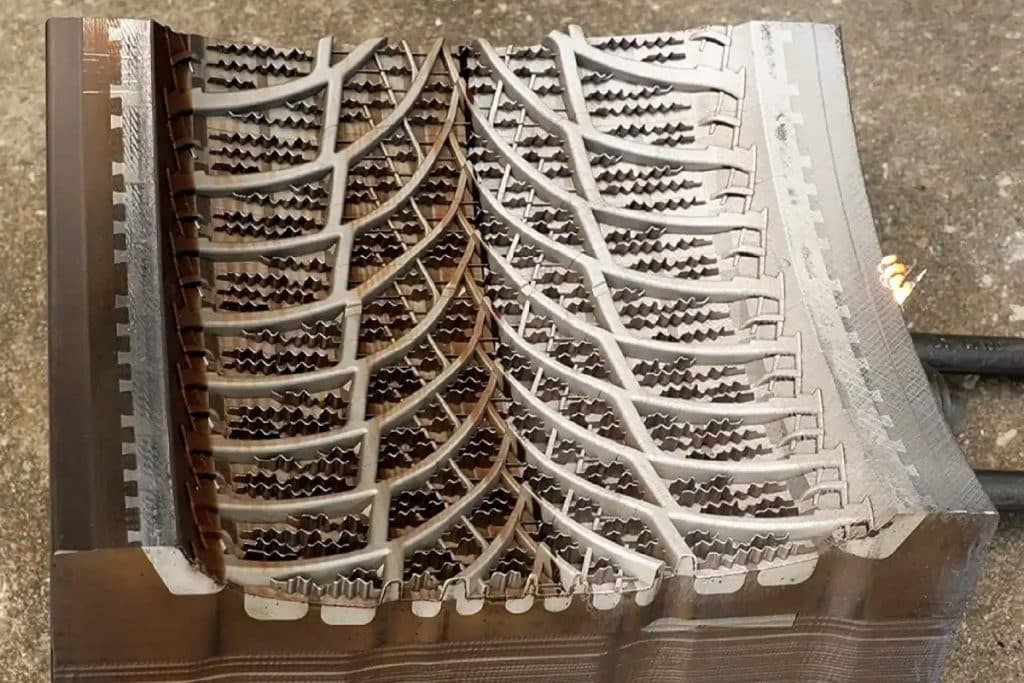
Why Are Pulsed Lasers More Powerful?
This article mainly discusses the scientific principles, advantages, design considerations, application areas, and challenges of pulsed lasers and deeply explores their high peak power and versatility.
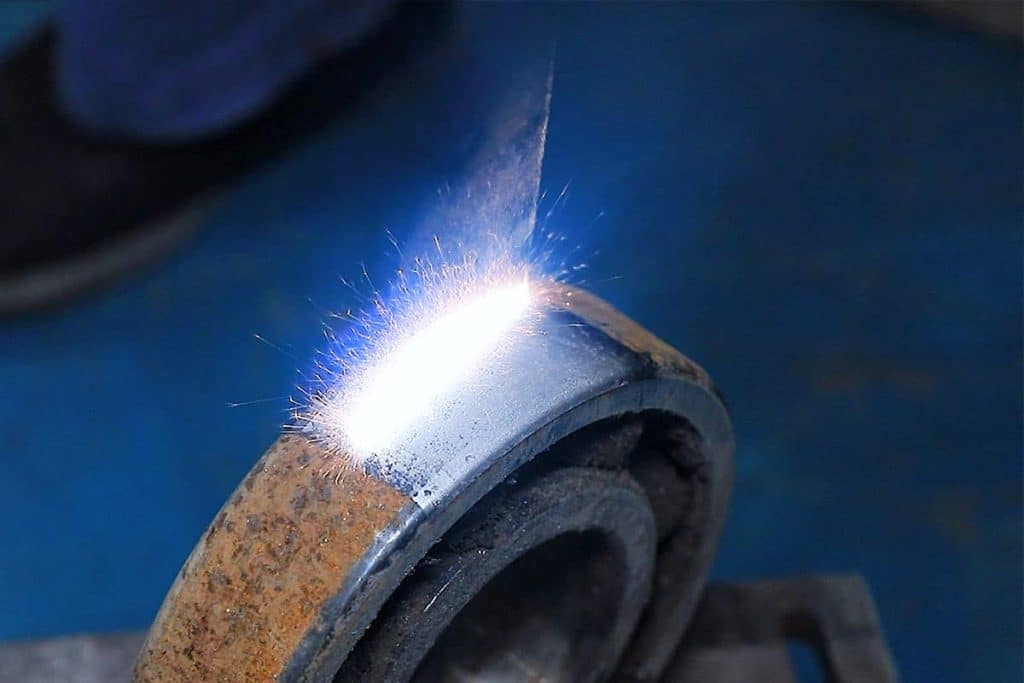
Will Pulsed Laser Cleaning Damage the Substrate?
This article provides a comprehensive overview of how pulsed laser cleaning works, the mechanisms that may cause substrate damage, influencing factors, and effective strategies to ensure safe and efficient cleaning
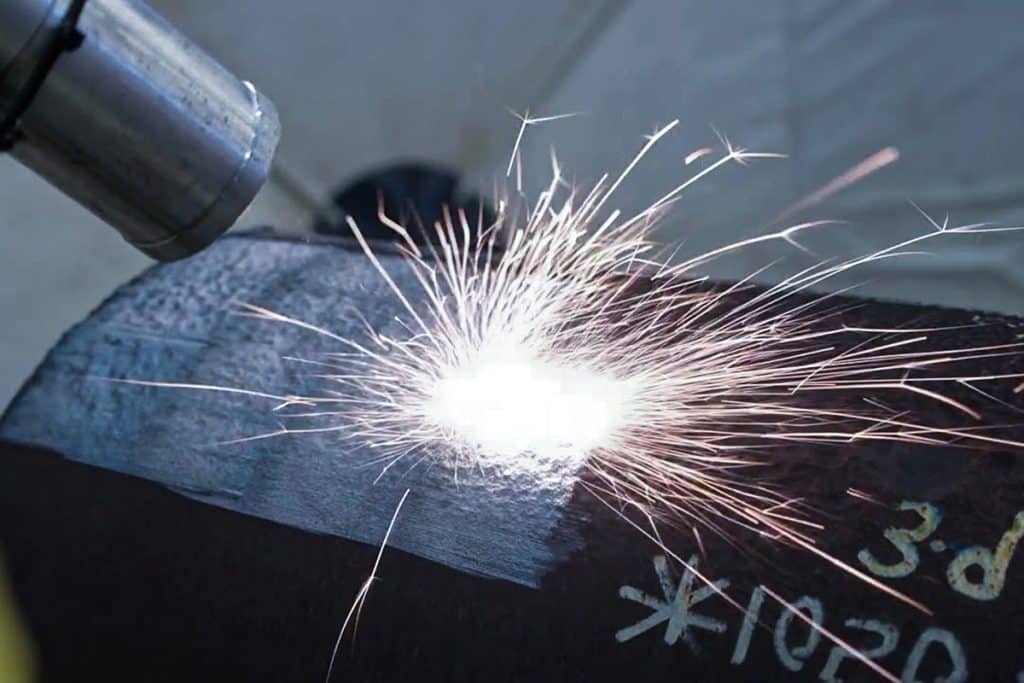
How Do Pulse Frequency and Repetition Rate Affect Laser Cleaning Efficiency?
This article will explore in depth the effects of pulse frequency and repetition rate on laser cleaning efficiency and provide optimization strategies for different applications.