金属レーザー溶接機
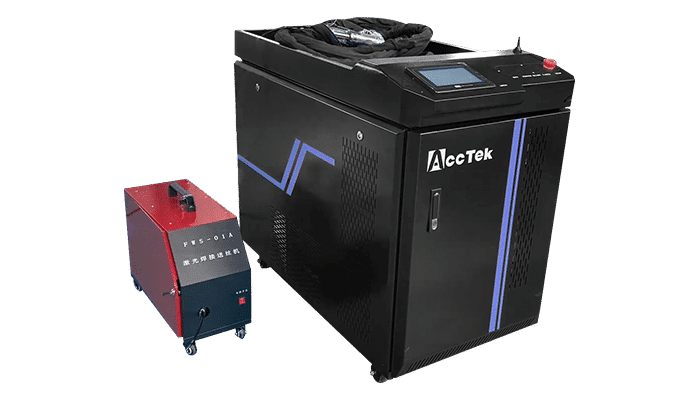
製品ラインナップ
-
ステンレス鋼レーザー溶接機
5段階中5.00の評価$4,000.00 – $8,700.00 オプションを選択 この商品には複数のバリエーションがあります。 オプションは商品ページから選択できます -
炭素鋼レーザー溶接機
5段階中5.00の評価$4,000.00 – $8,700.00 オプションを選択 この商品には複数のバリエーションがあります。 オプションは商品ページから選択できます -
アルミニウムレーザー溶接機
5段階中5.00の評価$4,000.00 – $8,700.00 オプションを選択 この商品には複数のバリエーションがあります。 オプションは商品ページから選択できます -
銅レーザー溶接機
5段階中4.75の評価$4,000.00 – $8,700.00 オプションを選択 この商品には複数のバリエーションがあります。 オプションは商品ページから選択できます -
真鍮レーザー溶接機
5段階中5.00の評価$4,000.00 – $8,700.00 オプションを選択 この商品には複数のバリエーションがあります。 オプションは商品ページから選択できます
レーザー溶接 VS. その他の方法
レーザー溶接とMIG溶接
MIG 溶接は厚い材料や高速生産によく使われる方法ですが、熱や歪みが増加する可能性があります。レーザー溶接は熱を最小限に抑えながら精度を高め、特に薄い金属部品や複雑な金属部品の溶接をよりきれいに、より強くできるため、繊細な作業や高精度の作業に最適です。
レーザー溶接とTIG溶接
TIG 溶接は高品質の溶接を実現し、薄い材料に適していますが、速度が遅く、オペレーターのスキルも必要になります。レーザー溶接はより高速で自動化されており、熱による歪みが少なく、優れた精度を実現し、大量生産や薄い材料の複雑な溶接に最適です。
レーザー溶接とスポット溶接
スポット溶接は薄い金属板を接合するのに最適ですが、溶接のサイズと材料の厚さによって制限されます。レーザー溶接はより汎用性が高く、より広範囲の材料と厚さを高精度で溶接できるため、さまざまな用途でより強力で一貫した結果を得ることができます。
AccTekレーザーを選ぶ理由
業界をリードするテクノロジー
当社では最新のレーザー技術を採用し、比類のない精度、速度、効率を機械が実現できるようにしています。AccTek レーザー溶接機は、さまざまな材料に対して熱による歪みを最小限に抑え、溶接強度を最大限に高め、高品質の結果を提供するように作られています。
カスタマイズ可能なソリューション
当社のレーザー溶接機は、カスタマイズ可能な出力設定、レーザーの種類、制御システムを備えており、お客様の特定のニーズに合わせて機器をカスタマイズできます。繊細な部品を扱う場合でも、高負荷のアプリケーションを扱う場合でも、当社はあらゆるプロジェクトに柔軟なソリューションを提供します。
優れた品質
AccTek レーザー マシンは、耐久性と長期的なパフォーマンスを実現するように設計されています。高品質の材料と高度なエンジニアリングで構築された当社のマシンは、厳しい生産環境に耐えるように設計されており、最小限のメンテナンスで信頼性の高い動作を保証します。
精度と精度
AccTek レーザー溶接機は、その優れた精度で知られており、毎回きれいで正確な溶接を保証します。当社の高度な制御システムにより、繊細で複雑な材料でも、厳しい許容差と複雑な溶接形状を簡単に実現できます。
優れた顧客サポート
当社は、最初の相談から設置、アフターサービスまで、優れたカスタマー サポートを提供できることに誇りを持っています。当社の専門家チームが、機械のセットアップ、トレーニング、トラブルシューティングをサポートし、お客様が投資を最大限に活用できるようにします。
競争力のある価格
AccTek Laser では、高性能のレーザー溶接機を競争力のある価格で提供しています。当社は、品質を犠牲にすることなくコスト効率の高いソリューションの必要性を理解しており、当社の機械はあらゆる規模の企業にとって優れた価値を提供します。
よくある質問
金属レーザー溶接機は動作しますか?
金属レーザー溶接機の価格はいくらですか?
レーザー溶接機の運用コストはいくらですか?
- 電力消費: レーザー溶接機は、レーザー光源だけでなく、冷却ユニット、ポンプ、制御システムなどの補助システムにも電力を必要とします。電力消費量は、レーザーの定格電力と動作時間によって異なります。
- レーザー光源のメンテナンス: レーザー溶接機のレーザー光源は、清掃、位置合わせ調整、ミラーやレンズなどの部品の交換など、定期的なメンテナンスが必要になる場合があります。メンテナンスの頻度と範囲は、使用するレーザー技術の種類とメーカーの推奨事項によって異なります。
- ガス消費量: 一部のレーザー溶接プロセスでは、溶接部を大気汚染から保護するために、アルゴンやヘリウムなどのシールド ガスを使用する必要があります。これらのガスのコストは、使用するガスの種類、流量、溶接作業の継続時間によって異なります。
- 消耗品: レーザー溶接機には、保護レンズ カバー、ノズル チップ、電極アセンブリなどの消耗部品が必要になる場合があります。これらの消耗品の交換頻度とコストは、使用する特定のコンポーネントと溶接作業の強度によって異なります。
- 保守契約: 一部のメーカーは、レーザー溶接機の保守契約またはサービス契約を提供しており、定期的な検査、修理、技術サポートをカバーできます。これらの契約の費用は、提供されるサービスのレベルと契約期間によって異なります。
- オペレーターのトレーニングと人件費: レーザー溶接機を適切に操作するには、レーザーの安全手順と溶接技術のトレーニングを受けた熟練したオペレーターが必要です。オペレーターのトレーニングと賃金に関連する人件費は、全体的な運用費用に影響します。
金属レーザー溶接機はどのような金属を溶接できますか?
- 鋼: これにはさまざまな種類の炭素鋼、ステンレス鋼、工具鋼が含まれます。レーザー溶接は、自動車、航空宇宙、建設業界で鋼部品の溶接によく使用されます。
- アルミニウム: アルミニウムとその合金は、レーザー溶接機を使用して頻繁に溶接されます。自動車製造、航空宇宙、電子機器などの業界では、アルミニウム部品の接合にレーザー溶接が使用されています。
- 銅および銅合金: レーザー溶接は、銅およびその合金 (真鍮や青銅など) の接合に使用できます。これらの材料は、電気および電子アプリケーションでよく使用されます。
- チタン: チタンとその合金は、反応性が高く、汚染されやすいため、従来の方法で溶接するのは困難です。レーザー溶接は、航空宇宙、医療、工業用途で使用されるチタン部品の正確でクリーンな溶接プロセスを実現します。
- ニッケル合金: レーザー溶接は、強度と耐腐食性が高いため、航空宇宙、石油化学、発電業界で一般的に使用されているニッケルベースの合金の溶接に適しています。
- 貴金属: レーザー溶接は、金、銀、プラチナなどの貴金属の溶接に使用できます。これらの材料は、ジュエリー作りや電子機器の製造によく使用されます。
- 特殊合金: レーザー溶接機は、航空宇宙、化学処理、海洋工学などの業界で高温および腐食環境で一般的に使用されるインコネル、ハステロイ、モネルなどの特殊合金も溶接できます。
金属のレーザー溶接にはガスが必要ですか?
- 不活性ガス: アルゴンやヘリウムなどの不活性ガスは、レーザー溶接のシールドガスとしてよく使用されます。これらのガスは化学的に不活性で、溶融金属や周囲の大気と反応しません。アルゴンは鋼、ステンレス鋼、チタンなどの材料の溶接によく使用され、ヘリウムはアルミニウムやその他の非鉄金属の溶接に使用されます。不活性ガスは、溶接部の周りに安定した一貫した環境を作り出し、気孔のリスクを減らし、溶接品質を向上させます。
- 活性ガス: 酸素や窒素などの活性ガスも、特に特定の用途や材料ではレーザー溶接のシールドガスとして使用できます。これらのガスは溶融金属と反応して、溶接部の化学組成を変えたり、浸透を改善したりします。たとえば、炭素鋼のレーザー溶接では、溶接深さを増やして溶接プロセスを高速化するために酸素が使用されることがあります。ただし、活性ガスは過度の酸化やその他の望ましくない影響を防ぐために慎重に制御する必要があります。
- 混合ガス: 不活性ガスと活性ガスを組み合わせたガス混合物は、特定の溶接要件に合わせて調整でき、溶接品質の向上、生産性の向上、運用コストの削減などの利点が得られます。ガス混合物には、用途に応じて、アルゴン、ヘリウム、酸素、窒素、またはその他のガスをさまざまな割合で組み合わせて含めることができます。
金属をレーザー溶接するには溶接ワイヤーが必要ですか?
- 隙間を埋める: 隙間があったり、ジョイントのフィットアップにばらつきがある場合は、隙間を埋めて完全な溶接を確実にするために充填材を追加することがあります。
- 合金化または強化: フィラー材料は、特定の用途に合わせて合金元素や強化材を追加するなど、溶接接合部の化学組成や機械的特性を変更するために使用される場合があります。
- ビルドアップ溶接: レーザー溶接は、摩耗または損傷した部品を修復するためにベース金属表面に追加の材料を堆積させるビルドアップ溶接にも使用できます。この場合、フィラーワイヤまたは粉末を使用して、溶接プールに材料を追加できます。
レーザー溶接の歪みと割れを軽減するにはどうすればいいですか?
- 熱入力の制御: レーザー溶接では熱入力を正確に制御できるため、歪みやひび割れを最小限に抑えることができます。レーザー出力、溶接速度、焦点位置などのパラメータを調整することで、ワークピースに適用される熱量を調整し、過熱や歪みのリスクを軽減できます。
- 予熱と溶接後の熱処理: 溶接前にワークピースを予熱すると、熱勾配と応力の蓄積が軽減され、歪みや割れを最小限に抑えることができます。さらに、応力緩和焼鈍などの溶接後の熱処理プロセスは、溶接部の残留応力を軽減し、溶接構造の全体的な安定性を向上させるのに役立ちます。
- ジョイント設計: 適切なジョイント設計により、レーザー溶接の変形や割れを最小限に抑えることができます。鋭角を避け、ジョイントの隙間を減らし、適切なフィットアップ許容値を使用すると、均一な熱分布が確保され、歪みや割れにつながる応力集中点のリスクが軽減されます。
- 固定とクランプ: ワークピースを適切に固定してクランプすると、溶接中の動きや歪みを最小限に抑えることができます。固定具やジグを使用して部品をしっかりと固定すると、位置合わせと安定性が維持され、歪みや割れの可能性が減ります。
- 溶接順序: 溶接プロセスを計画する際には、溶接順序を考慮してください。熱勾配と歪みを最小限に抑える順序で溶接すると、歪みや割れが発生する可能性を減らすことができます。たとえば、中心から外側に向かって溶接したり、バックステップ技法を使用したりすると、熱がより均等に分散され、歪みを減らすことができます。
- 材料の選択: 適切な材料とフィラー メタルを選択すると、レーザー溶接の歪みや割れを軽減できます。熱膨張係数が類似する材料を選択し、材料の厚さの差を最小限に抑えると、応力の蓄積や歪みを軽減できます。さらに、適切な機械的特性とベース材料との適合性を備えたフィラー メタルを使用すると、溶接品質が向上し、割れのリスクを軽減できます。
レーザー溶接中にワークピースが過熱するのを防ぐにはどうすればよいでしょうか?
- レーザー パラメータの最適化: 出力、パルス持続時間、周波数、ビーム焦点などのレーザー パラメータを調整して、ワークピースへの熱入力を制御します。レーザー出力を下げるか、パルス持続時間を調整すると、過熱を軽減できます。パルス レーザー溶接技術を使用して、ワークピースへの熱伝達を制御し、全体的な熱入力を最小限に抑えます。
- 制御された熱入力: レーザー ビームのワークピースへの滞留時間を制御することで、急速な加熱と冷却のサイクルが実現します。レーザー ビームの照射時間を制限することで、過度の加熱を防止できます。動的レーザー出力変調技術を使用して、ワークピースの熱応答に応じてレーザー出力をリアルタイムで調整し、一貫した熱入力を確保します。
- 冷却戦略: 溶接プロセス中にワークピースから余分な熱を放散するには、空冷や水冷などのアクティブ冷却技術を使用します。溶接前にワークピースを特定の温度範囲まで予冷または予熱して、熱勾配を最小限に抑え、過熱のリスクを軽減します。
- 固定具の設計: 効率的な固定具の設計を使用して、溶接プロセス中にワークピースを適切にサポートし、熱を放散します。適切な固定具の設計は、熱の蓄積を最小限に抑え、局所的な過熱を防ぐのに役立ちます。ワークピース内の熱の蓄積を防ぐために、溶接エリアの周囲で適切な換気と熱放散を確保します。
- 材料の選択: 溶接中の過熱のリスクを軽減するために、熱伝導性と放熱性に優れた材料を選択してください。また、溶接熱による歪みや熱応力を最小限に抑えるために、熱膨張係数の低い材料を選択してください。
- 溶接シーケンス: 大きな溶接部分を小さなセクションに分割し、順番に溶接することで熱をより均等に分散し、局所的な過熱を防ぎます。冷却間隔を制御した断続溶接技術を実装して、溶接パス間でワークピースの熱を放散できるようにします。
- プロセス監視: リアルタイムの温度監視およびフィードバック制御システムを実装して、溶接中のワークピースの過熱を検出して防止します。熱画像または赤外線温度検知技術を使用して、ワークピースの温度分布を監視し、それに応じて溶接パラメータを調整します。
関連リソース
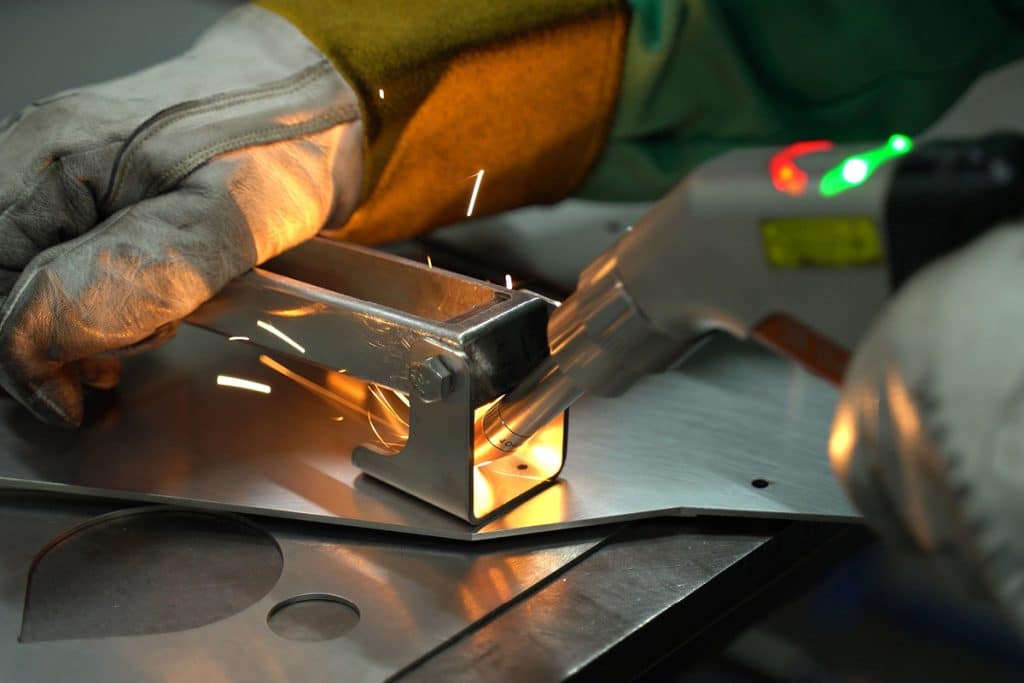
レーザー溶接機を使用する際には、どのような環境上の配慮が必要ですか?
この記事では、レーザー溶接機を使用する際に考慮すべき環境問題とそれに対する対策について説明します。
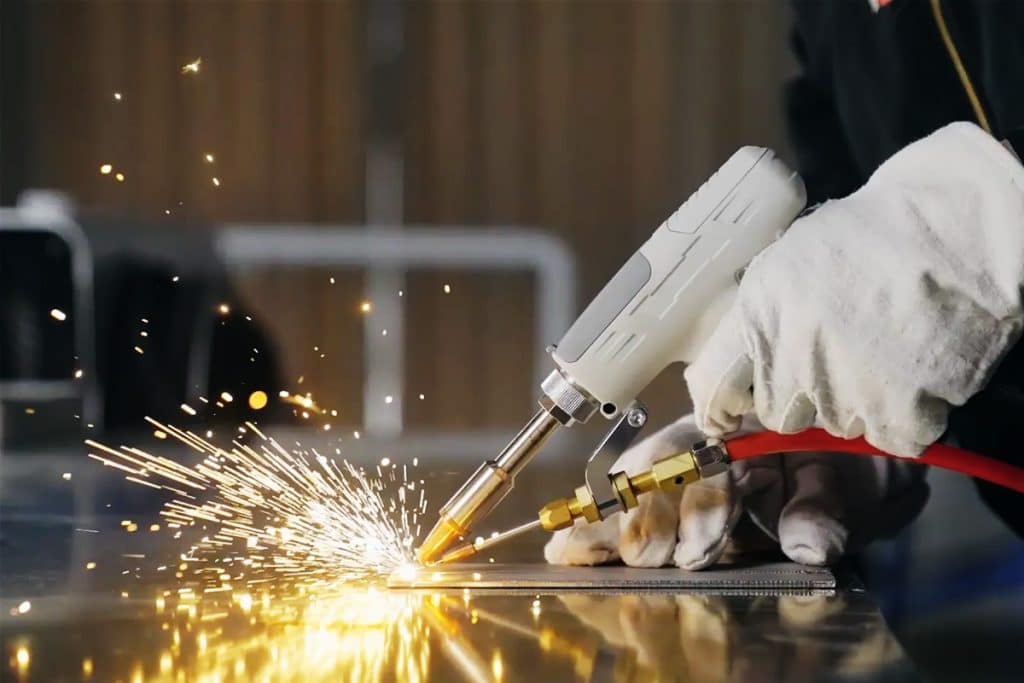
溶接に最適なレーザージェネレータはどれですか?
この記事では主に CO2 レーザー ジェネレータ、ファイバー レーザー ジェネレータ、Nd: YAG レーザー ジェネレータを比較し、ユーザーが溶接のニーズに基づいて科学的な選択を行えるようにします。
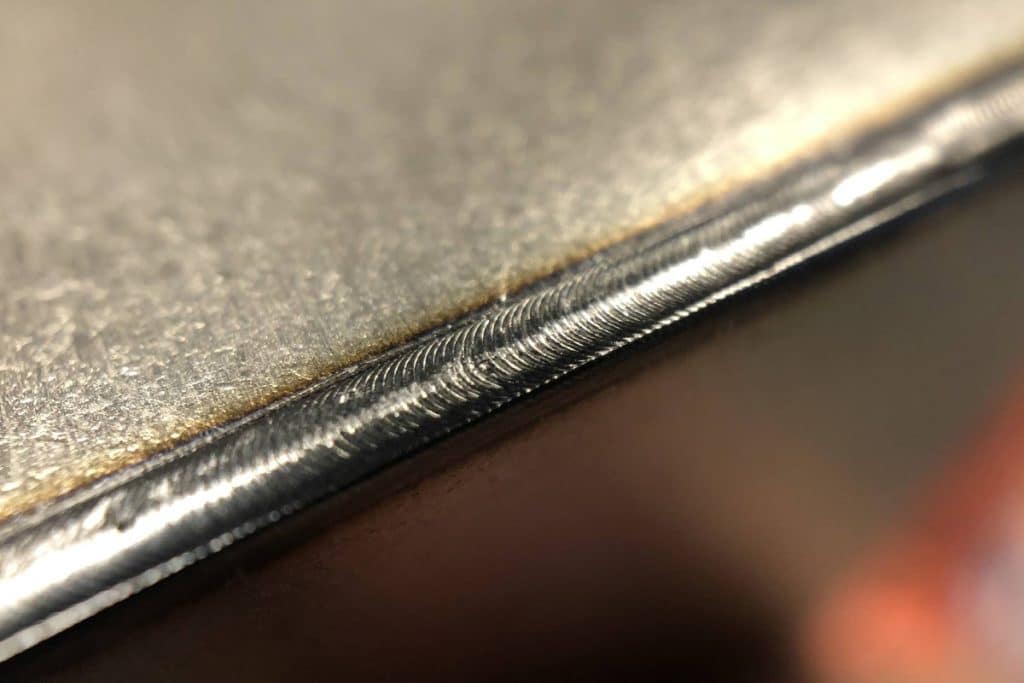
レーザー溶接はどのようにして材料の深部溶融を実現するのでしょうか?
この記事では、レーザー溶接がどのようにして材料の深溶融を実現するか、その基本原理、浸透深さに影響を与える主な要因、深浸透の形成メカニズム、最適化などについて主に説明します。