Metal Lazer Kaynak Makinesi
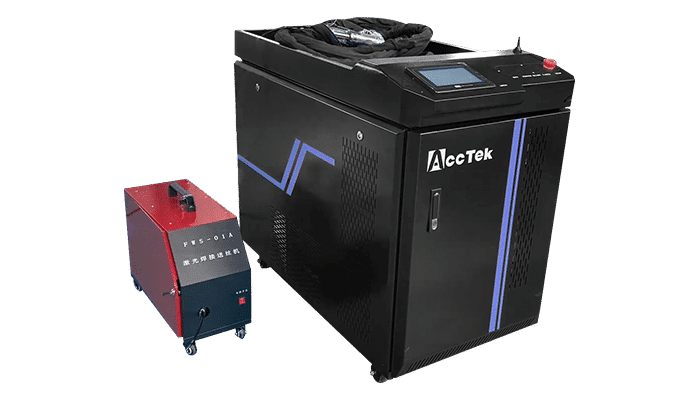
Ürün Yelpazesi
-
Paslanmaz Çelik Lazer Kaynak Makinesi
5 üzerinden 5.00 oy aldı$4,000.00 – $8,700.00 Seçenekler Bu ürünün birden fazla varyasyonu var. Seçenekler ürün sayfasından seçilebilir -
Karbon Çelik Lazer Kaynak Makinesi
5 üzerinden 5.00 oy aldı$4,000.00 – $8,700.00 Seçenekler Bu ürünün birden fazla varyasyonu var. Seçenekler ürün sayfasından seçilebilir -
Alüminyum Lazer Kaynak Makinesi
5 üzerinden 5.00 oy aldı$4,000.00 – $8,700.00 Seçenekler Bu ürünün birden fazla varyasyonu var. Seçenekler ürün sayfasından seçilebilir -
Bakır Lazer Kaynak Makinesi
5 üzerinden 4.75 oy aldı$4,000.00 – $8,700.00 Seçenekler Bu ürünün birden fazla varyasyonu var. Seçenekler ürün sayfasından seçilebilir -
Pirinç Lazer Kaynak Makinesi
5 üzerinden 5.00 oy aldı$4,000.00 – $8,700.00 Seçenekler Bu ürünün birden fazla varyasyonu var. Seçenekler ürün sayfasından seçilebilir
Lazer kaynak Karşılaştır. Diğer Yöntemler
Lazer Kaynak ve MIG Kaynak
MIG kaynak, kalın malzemeler ve yüksek hızlı üretim için popüler bir yöntemdir, ancak artan ısıya ve bozulmaya yol açabilir. Lazer kaynak, minimum ısıyla daha fazla hassasiyet sunarak, özellikle ince veya karmaşık metal bileşenler için daha temiz, daha güçlü kaynaklar elde edilmesini sağlar ve hassas veya yüksek hassasiyetli işler için idealdir.
Lazer Kaynak ve TIG Kaynak
TIG kaynak, yüksek kaliteli kaynaklar üretir ve daha ince malzemeler için uygundur, ancak daha yavaştır ve daha fazla operatör becerisi gerektirir. Lazer kaynak daha hızlıdır ve daha otomatiktir, daha az ısı bozulmasıyla üstün hassasiyet sunar, yüksek hacimli uygulamalar ve ince malzemeler üzerindeki karmaşık kaynaklar için idealdir.
Lazer Kaynak ve Nokta Kaynak
Nokta kaynağı, ince metal levhaları birleştirmek için idealdir, ancak kaynak boyutu ve malzeme kalınlığı ile sınırlıdır. Lazer kaynak daha çok yönlüdür ve daha geniş bir malzeme ve kalınlık aralığını daha yüksek hassasiyetle kaynaklayabilir, çeşitli uygulamalarda daha güçlü ve daha tutarlı sonuçlar sağlar.
Neden AccTek Lazer'i Seçmelisiniz?
Sektör Lideri Teknoloji
Makinelerimizin eşsiz hassasiyet, hız ve verimlilik sağlamasını sağlamak için en son lazer teknolojisini kullanıyoruz. AccTek Lazer kaynak makineleri, çok çeşitli malzemeler için ısı bozulmasını en aza indirerek ve kaynak mukavemetini en üst düzeye çıkararak yüksek kaliteli sonuçlar sağlamak için üretilmiştir.
Özelleştirilebilir Çözümler
Lazer kaynak makinelerimiz, ekipmanı özel ihtiyaçlarınıza göre uyarlamanıza olanak tanıyan özelleştirilebilir güç ayarları, lazer türleri ve kontrol sistemleri sunar. İster hassas bileşenlerle ister ağır hizmet uygulamalarıyla çalışın, her proje için esnek çözümler sunuyoruz.
Olağanüstü Yapı Kalitesi
AccTek Lazer makineleri dayanıklılık ve uzun süreli performans için tasarlanmıştır. Yüksek kaliteli malzemeler ve gelişmiş mühendislikle üretilen makinelerimiz, zorlu üretim ortamlarına dayanacak şekilde tasarlanmıştır ve minimum bakımla güvenilir çalışma sağlar.
Hassasiyet ve doğruluk
AccTek Lazer kaynak makineleri, her seferinde temiz ve doğru kaynaklar sağlayarak olağanüstü hassasiyetleriyle bilinir. Gelişmiş kontrol sistemlerimiz, hassas veya karmaşık malzemelerde bile sıkı toleranslar ve karmaşık kaynak geometrileri elde etmenizi sağlar.
Mükemmel Müşteri Desteği
İlk danışmanlıktan kuruluma ve satış sonrası hizmete kadar olağanüstü müşteri desteği sunmaktan gurur duyuyoruz. Uzman ekibimiz, makine kurulumu, eğitim ve sorun giderme konusunda yardımcı olmak için hazırdır ve yatırımınızdan en iyi şekilde yararlanmanızı sağlar.
Rekabetçi Fiyatlandırma
AccTek Laser'da rekabetçi fiyatlarla yüksek performanslı lazer kaynak makineleri sunuyoruz. Kaliteyi tehlikeye atmadan uygun maliyetli çözümlere olan ihtiyacı anlıyoruz ve bu da makinelerimizi her ölçekteki işletme için mükemmel bir değer haline getiriyor.
Sıkça Sorulan Sorular
Metal Lazer Kaynak Makinaları Çalışır mı?
Metal Lazer Kaynak Makinelerinin Maliyeti Ne Kadardır?
Lazer Kaynak Makinalarının İşletme Maliyetleri Nelerdir?
- Elektrik Tüketimi: Lazer kaynak makineleri, lazer kaynağına güç sağlamak için elektriğin yanı sıra soğutma üniteleri, pompalar ve kontrol sistemleri gibi yardımcı sistemlere de ihtiyaç duyar. Elektrik tüketimi lazerin güç oranına ve çalışma süresine bağlı olacaktır.
- Lazer Kaynağı Bakımı: Lazer kaynak makinelerindeki lazer kaynağı, temizlik, hizalama ayarlamaları veya aynalar veya lensler gibi bileşenlerin değiştirilmesi gibi periyodik bakım gerektirebilir. Bakım sıklığı ve kapsamı, kullanılan lazer teknolojisinin türüne ve üreticinin önerilerine bağlı olarak değişecektir.
- Gaz Tüketimi: Bazı lazer kaynak işlemleri, kaynak bölgesini atmosferik kirlenmeden korumak için argon veya helyum gibi koruyucu gazların kullanılmasını gerektirir. Bu gazların maliyeti kullanılan gazın türüne, akış hızına ve kaynak işlemlerinin süresine bağlı olacaktır.
- Sarf malzemeleri: Lazer kaynak makineleri, koruyucu lens kapakları, nozül uçları veya elektrot düzenekleri gibi sarf malzemelerine ihtiyaç duyabilir. Bu sarf malzemelerinin değiştirme sıklığı ve maliyeti, kullanılan spesifik bileşenlere ve kaynak işlemlerinin yoğunluğuna bağlı olacaktır.
- Bakım Sözleşmeleri: Bazı üreticiler, lazer kaynak makineleri için periyodik denetimleri, onarımları ve teknik desteği kapsayabilen bakım sözleşmeleri veya servis sözleşmeleri sunmaktadır. Bu sözleşmelerin maliyeti, sağlanan hizmetin düzeyine ve sözleşmenin süresine bağlı olacaktır.
- Operatör Eğitimi ve İşçilik Maliyetleri: Lazer kaynak makinelerinin düzgün çalışması, lazer güvenlik prosedürleri ve kaynak teknikleri konusunda eğitim almış yetenekli operatörler gerektirir. Operatör eğitimi ve ücretlerle ilişkili işçilik maliyetleri, genel işletme giderlerine katkıda bulunur.
Metal Lazer Kaynak Makineleri Hangi Metalleri Kaynak Yapabilir?
- Çelik: Buna çeşitli karbon çeliği, paslanmaz çelik ve takım çeliği dahildir. Lazer kaynağı genellikle otomotiv, havacılık ve inşaat endüstrilerinde çelik bileşenlerin kaynaklanması için kullanılır.
- Alüminyum: Alüminyum ve alaşımları sıklıkla lazer kaynak makineleri kullanılarak kaynaklanır. Otomotiv üretimi, havacılık ve elektronik gibi endüstriler, alüminyum parçaların birleştirilmesi için lazer kaynağına güvenmektedir.
- Bakır ve Bakır Alaşımları: Lazer kaynağı, bakırı ve pirinç ve bronz gibi alaşımlarını birleştirmek için kullanılabilir. Bu malzemeler elektrik ve elektronik uygulamalarda yaygın olarak kullanılmaktadır.
- Titanyum: Titanyum ve alaşımlarının, yüksek reaktiviteleri ve kirlenmeye karşı duyarlılıkları nedeniyle geleneksel yöntemler kullanılarak kaynak yapılması zordur. Lazer kaynağı, havacılık, tıp ve endüstriyel uygulamalarda kullanılan titanyum bileşenler için hassas ve temiz bir kaynak işlemi sağlar.
- Nikel Alaşımları: Lazer kaynağı, yüksek mukavemeti ve korozyon direnci nedeniyle havacılık, petrokimya ve enerji üretim endüstrilerinde yaygın olarak kullanılan nikel bazlı alaşımların kaynağına uygundur.
- Değerli Metaller: Lazer kaynağı altın, gümüş ve platin gibi değerli metallerin kaynağında kullanılabilir. Bu malzemeler genellikle mücevher yapımında ve elektronik üretiminde kullanılır.
- Özel Alaşımlar: Lazer kaynak makineleri ayrıca havacılık, kimyasal işleme ve denizcilik mühendisliği gibi endüstrilerde yüksek sıcaklık ve aşındırıcı ortamlarda yaygın olarak kullanılan Inconel, Hastelloy ve Monel gibi özel alaşımları da kaynaklayabilir.
Lazer Kaynak Metalinin Gaza İhtiyacı Var mı?
- İnert Gazlar: Argon ve helyum gibi inert gazlar, lazer kaynağında koruyucu gaz olarak yaygın olarak kullanılır. Bu gazlar kimyasal olarak inerttir ve erimiş metalle veya çevredeki atmosferle reaksiyona girmez. Argon genellikle çelik, paslanmaz çelik ve titanyum gibi malzemelerin kaynaklanmasında tercih edilirken, helyum alüminyum ve diğer demir dışı metallerin kaynağında kullanılır. İnert gazlar kaynak bölgesi çevresinde sabit ve tutarlı bir ortam oluşturarak gözeneklilik riskini azaltır ve kaynak kalitesini artırır
- Aktif Gazlar: Oksijen veya nitrojen gibi aktif gazlar, özellikle belirli uygulamalar veya malzemeler için lazer kaynağında koruyucu gaz olarak da kullanılabilir. Bu gazlar, kaynağın kimyasal bileşimini değiştirmek veya nüfuziyeti arttırmak için erimiş metalle reaksiyona girebilir. Örneğin, karbon çeliklerinin lazer kaynağında kaynak derinliğini arttırmak ve kaynak işlemini hızlandırmak için bazen oksijen kullanılır. Ancak aktif gazlar, aşırı oksidasyonu veya diğer istenmeyen etkileri önlemek için dikkatli kontrol gerektirir.
- Karışık Gazlar: İnert ve aktif gazların bir kombinasyonunu içeren gaz karışımları, özel kaynak gereksinimlerine göre uyarlanabilir ve iyileştirilmiş kaynak kalitesi, artan üretkenlik veya azaltılmış işletme maliyetleri gibi faydalar sunar. Gaz karışımları, uygulamaya bağlı olarak değişen oranlarda argon, helyum, oksijen, nitrojen veya diğer gazların kombinasyonlarını içerebilir.
Lazer Kaynak Metaline Kaynak Teline İhtiyacım Var mı?
- Boşlukların Doldurulması: Birleşim yeri kurulumunda boşlukların veya değişikliklerin olduğu durumlarda, boşluğu kapatmak ve tam bir kaynak sağlamak için dolgu malzemesi eklenebilir.
- Alaşımlama veya Takviye: Dolgu malzemesi, belirli uygulamalar için alaşım elementleri veya takviye eklemek gibi, kaynak bağlantısının kimyasal bileşimini veya mekanik özelliklerini değiştirmek için kullanılabilir.
- Yapı Kaynağı: Lazer kaynağı, aşınmış veya hasar görmüş bileşenleri eski haline getirmek için ana metal yüzeyine ek malzemenin biriktirildiği yapı kaynağı için de kullanılabilir. Bu durumda kaynak havuzuna malzeme eklemek için dolgu teli veya tozu kullanılabilir.
Lazer Kaynak Bozulması ve Çatlama Nasıl Azaltılır?
- Kontrollü Isı Girişi: Lazer kaynak, ısı girişi üzerinde hassas kontrol sağlar, bu da bozulma ve çatlamayı en aza indirmeye yardımcı olabilir. Lazer gücü, kaynak hızı ve odak konumu gibi parametrelerin ayarlanması, iş parçasına uygulanan ısı miktarının düzenlenmesine yardımcı olarak aşırı ısınma ve bozulma riskini azaltabilir.
- Ön Isıtma ve Kaynak Sonrası Isıl İşlem: Kaynaktan önce iş parçasının ön ısıtılması, termal değişimlerin ve gerilim oluşumunun azaltılmasına, distorsiyon ve çatlamanın en aza indirilmesine yardımcı olabilir. Ek olarak, gerilim giderme tavlaması gibi kaynak sonrası ısıl işlem süreçleri, kaynak bölgesindeki artık gerilimlerin hafifletilmesine yardımcı olarak kaynaklı yapının genel stabilitesini artırabilir.
- Bağlantı Tasarımı: Uygun bağlantı tasarımı, lazer kaynakta deformasyonu ve çatlamayı en aza indirebilir. Keskin açılardan kaçınmak, bağlantı boşluklarını azaltmak ve uygun montaj toleranslarını kullanmak, eşit ısı dağılımının sağlanmasına ve bozulma ve çatlamaya yol açabilecek gerilim yoğunlaşma noktaları riskinin azaltılmasına yardımcı olabilir.
- Fikstürleme ve Kenetleme: İş parçasının uygun şekilde fikstürle bağlanması ve kelepçelenmesi, kaynak sırasında hareket ve distorsiyonun en aza indirilmesine yardımcı olabilir. Parçaların sabitleme elemanları veya aparatlarla güvenli bir şekilde yerinde tutulması, hizalamanın ve stabilitenin korunmasına yardımcı olarak bozulma ve çatlama olasılığını azaltabilir.
- Kaynak Sırası: Kaynak işlemini planlarken kaynak sırasını dikkate alın. Termal değişimleri ve distorsiyonu en aza indiren bir sırayla kaynak yapmak, distorsiyon ve çatlama olasılığının azaltılmasına yardımcı olabilir. Örneğin merkezden dışarıya doğru kaynak yapmak veya geri adım atma tekniği kullanmak, ısının daha eşit şekilde dağıtılmasına ve bozulmanın azaltılmasına yardımcı olabilir.
- Malzeme Seçimi: Uygun malzeme ve dolgu metalinin seçilmesi, lazer kaynağında bozulma ve çatlamanın azaltılmasına da yardımcı olabilir. Benzer termal genleşme katsayılarına sahip malzemelerin seçilmesi ve malzeme kalınlıkları arasındaki farkın en aza indirilmesi, gerilim oluşumunun ve bozulmanın azaltılmasına yardımcı olabilir. Ek olarak, uygun mekanik özelliklere sahip ve ana malzemeyle uyumlu dolgu metallerinin kullanılması, kaynak kalitesinin iyileştirilmesine ve çatlama riskinin azaltılmasına yardımcı olabilir.
Lazer Kaynak Sırasında İş Parçasının Aşırı Isınması Nasıl Önlenir?
- Lazer Parametrelerini Optimize Edin: İş parçasına ısı girişini kontrol etmek için güç, darbe süresi, frekans ve ışın odağı gibi lazer parametrelerini ayarlayın. Lazer gücünü azaltmak veya darbe süresini ayarlamak aşırı ısınmanın azaltılmasına yardımcı olabilir. İş parçasına ısı transferini kontrol etmek ve genel ısı girişini en aza indirmek için darbeli lazer kaynak teknolojisini kullanın.
- Kontrollü Isı Girişi: Lazer ışınının iş parçasında kalma süresinin kontrol edilmesiyle hızlı ısıtma ve soğutma döngüleri elde edilir. Lazer ışınına maruz kalma süresinin sınırlandırılması aşırı ısınmayı önlemeye yardımcı olur. Dinamik lazer güç modülasyon teknolojisi, tutarlı ısı girişi sağlamak için iş parçasının termal tepkisine göre lazer gücünü gerçek zamanlı olarak ayarlamak için kullanılır.
- Soğutma Stratejisi: Kaynak işlemi sırasında iş parçasındaki fazla ısıyı dağıtmak için havayla soğutma veya suyla soğutma gibi aktif soğutma tekniklerini kullanın. Termal değişimleri en aza indirmek ve aşırı ısınma riskini azaltmak için kaynak yapmadan önce iş parçasını belirli bir sıcaklık aralığına kadar önceden soğutun veya önceden ısıtın.
- Fikstür Tasarımı: Kaynak işlemi sırasında iş parçasına yeterli destek ve ısı dağılımı sağlamak için verimli bir fikstür tasarımı kullanın. Doğru fikstür tasarımı, ısı oluşumunu en aza indirmeye ve bölgesel aşırı ısınmayı önlemeye yardımcı olur. İş parçasında ısı birikmesini önlemek için kaynak alanı çevresinde uygun havalandırma ve ısı dağılımı olduğundan emin olun.
- Malzeme Seçimi: Kaynak sırasında aşırı ısınma riskini azaltmak için ısı iletkenliği ve ısı dağıtma özellikleri iyi olan malzemeleri seçin. Ayrıca kaynak ısısının neden olduğu distorsiyonu ve termal gerilimi en aza indirmek için daha düşük termal genleşme katsayılarına sahip malzemeleri seçin.
- Kaynak Sırası: Büyük kaynakları daha küçük bölümlere ayırın ve ısıyı daha eşit dağıtmak ve yerel aşırı ısınmayı önlemek için bunları sırayla kaynaklayın. İş parçasının kaynak pasoları arasında ısıyı dağıtmasını sağlamak için kontrollü soğutma aralıklarıyla aralıklı kaynak teknikleri uygulayın.
- Proses İzleme: Kaynak sırasında iş parçasının aşırı ısınmasını tespit etmek ve önlemek için gerçek zamanlı sıcaklık izleme ve geri bildirim kontrol sistemlerini uygulayın. İş parçasının sıcaklık dağılımını izlemek ve kaynak parametrelerini buna göre ayarlamak için termal görüntüleme veya kızılötesi sıcaklık algılama teknolojisini kullanın.
İlgili Kaynaklar
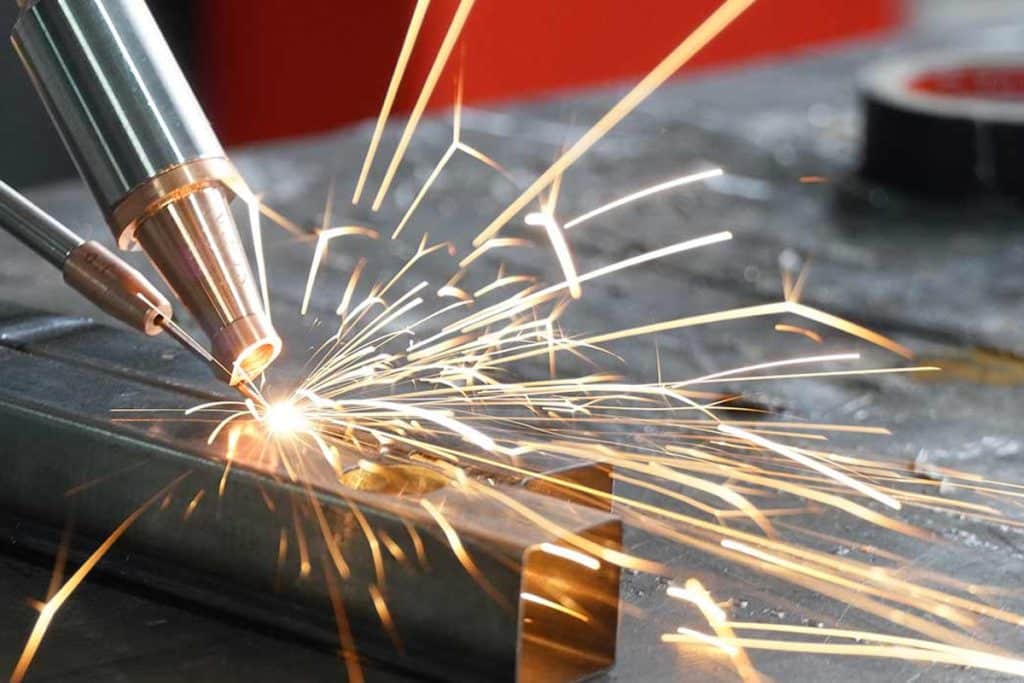
Odak uzaklığının lazer kaynak sonuçlarına etkisi
Bu makalede esas olarak lazer kaynakta odak uzaklığının önemi ve kaynak etkisine etkisi ele alınmakta ve pratik optimizasyon önerileri sunulmaktadır.
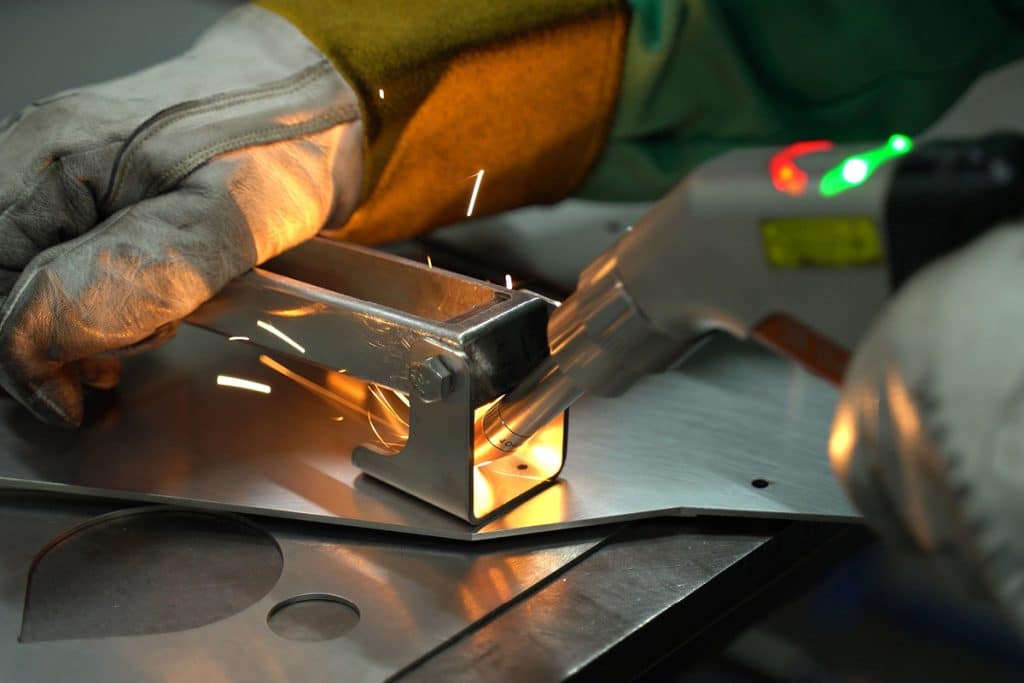
Lazer Kaynak Makineleri Kullanılırken Hangi Çevresel Hususlara Dikkat Edilmelidir?
Bu makalede lazer kaynak makinelerinin kullanımı sırasında ortaya çıkan çevresel sorunlar ve alınması gereken önlemler ele alınmaktadır.
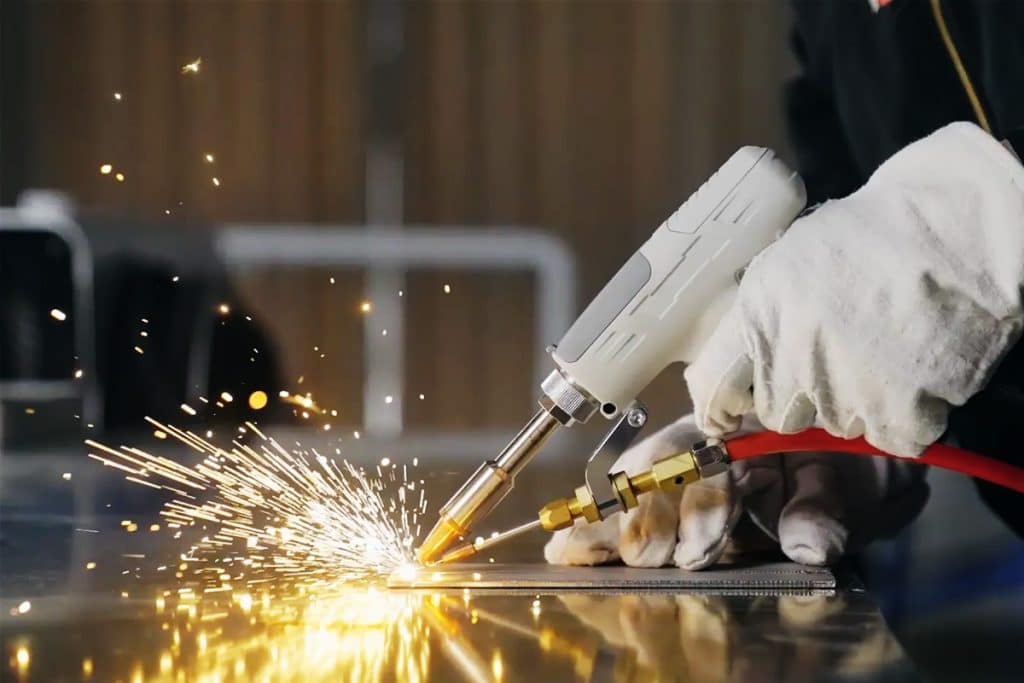
Kaynak İçin Hangi Lazer Jeneratörü En İyisidir?
Bu makale, kullanıcıların kaynak ihtiyaçlarına göre bilimsel seçimler yapmalarına yardımcı olmak için esas olarak CO2 lazer jeneratörlerini, fiber lazer jeneratörlerini ve Nd: YAG lazer jeneratörlerini karşılaştırmaktadır.