Metal Laser Welding Machine
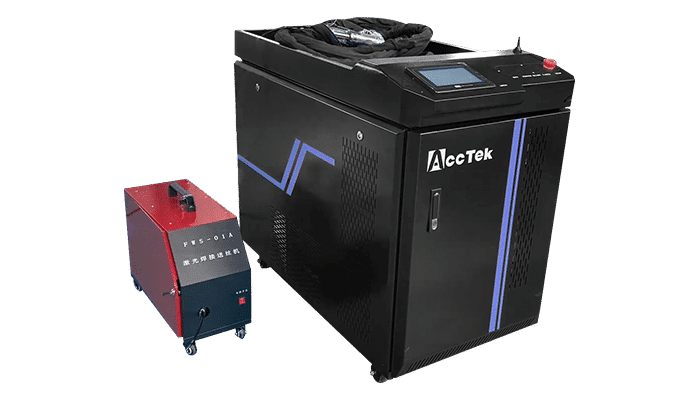
Product Range
-
Stainless Steel Laser Welding Machine
Rated 5.00 out of 5$4,000.00 – $8,700.00 Select options This product has multiple variants. The options may be chosen on the product page -
Carbon Steel Laser Welding Machine
Rated 5.00 out of 5$4,000.00 – $8,700.00 Select options This product has multiple variants. The options may be chosen on the product page -
Aluminum Laser Welding Machine
Rated 5.00 out of 5$4,000.00 – $8,700.00 Select options This product has multiple variants. The options may be chosen on the product page -
Copper Laser Welding Machine
Rated 4.75 out of 5$4,000.00 – $8,700.00 Select options This product has multiple variants. The options may be chosen on the product page -
Brass Laser Welding Machine
Rated 5.00 out of 5$4,000.00 – $8,700.00 Select options This product has multiple variants. The options may be chosen on the product page
Laser Welding VS. Other Methods
Laser Welding vs. MIG Welding
MIG welding is a popular method for thick materials and high-speed production, but it can lead to increased heat and distortion. Laser welding offers greater precision with minimal heat, resulting in cleaner, stronger welds, especially for thin or complex metal components, making it ideal for delicate or high-precision work.
Laser Welding vs. TIG Welding
TIG welding produces high-quality welds and is suitable for thinner materials, but it is slower and requires more operator skill. Laser welding is faster and more automated, offering superior precision with less heat distortion, ideal for high-volume applications and intricate welds on thin materials.
Laser Welding vs. Spot Welding
Spot welding is ideal for joining thin sheets of metal, but it is limited by the size of the weld and material thickness. Laser welding is more versatile, and capable of welding a broader range of materials and thicknesses with higher precision, providing stronger and more consistent results across diverse applications.
Why Choose AccTek Laser
Industry-Leading Technology
We use the latest laser technology to ensure our machines deliver unmatched precision, speed, and efficiency. AccTek Laser welding machines are built to provide high-quality results, minimizing heat distortion and maximizing weld strength for a wide range of materials.
Customizable Solutions
Our laser welding machines offer customizable power settings, laser types, and control systems, allowing you to tailor the equipment to your specific needs. Whether you're working with delicate components or heavy-duty applications, we provide flexible solutions for every project.
Exceptional Build Quality
AccTek Laser machines are engineered for durability and long-lasting performance. Built with high-quality materials and advanced engineering, our machines are designed to withstand rigorous production environments, ensuring reliable operation with minimal maintenance.
Precision and Accuracy
AccTek Laser welding machines are known for their exceptional precision, ensuring clean, accurate welds every time. Our advanced control systems allow you to achieve tight tolerances and complex weld geometries with ease, even on delicate or intricate materials.
Excellent Customer Support
We pride ourselves on offering outstanding customer support, from initial consultation to installation and after-sales service. Our team of experts is available to assist with machine setup, training, and troubleshooting, ensuring you get the most out of your investment.
Competitive Pricing
At AccTek Laser, we offer high-performance laser welding machines at competitive prices. We understand the need for cost-effective solutions without compromising on quality, making our machines an excellent value for businesses of all sizes.
Frequently Asked Questions
Do Metal Laser Welding Machines Work?
How Much Does Metal Laser Welding Machines Cost?
What Are The Operating Costs of Laser Welding Machines?
- Electricity Consumption: Laser welding machines require electricity to power the laser source, as well as auxiliary systems such as cooling units, pumps, and control systems. The electricity consumption will depend on the power rating of the laser and the duration of operation.
- Laser Source Maintenance: The laser source in laser welding machines may require periodic maintenance, such as cleaning, alignment adjustments, or replacement of components like mirrors or lenses. The frequency and extent of maintenance will vary depending on the type of laser technology used and the manufacturer’s recommendations
- Gas Consumption: Some laser welding processes require the use of shielding gases, such as argon or helium, to protect the weld zone from atmospheric contamination. The cost of these gases will depend on the type of gas used, the flow rate, and the duration of welding operations.
- Consumables: Laser welding machines may require consumable parts such as protective lens covers, nozzle tips, or electrode assemblies. The frequency of replacement and the cost of these consumables will depend on the specific components used and the intensity of welding operations.
- Maintenance Contracts: Some manufacturers offer maintenance contracts or service agreements for laser welding machines, which can cover periodic inspections, repairs, and technical support. The cost of these contracts will depend on the level of service provided and the duration of the agreement.
- Operator Training and Labor Costs: Proper operation of laser welding machines requires skilled operators who are trained in laser safety procedures and welding techniques. Labor costs associated with operator training and wages contribute to the overall operating expenses.
What Metals Can Metal Laser Welding Machines Weld?
- Steel: This includes various types of carbon steel, stainless steel, and tool steel. Laser welding is often used in the automotive, aerospace, and construction industries for welding steel components
- Aluminum: Aluminum and its alloys are frequently welded using laser welding machines. Industries such as automotive manufacturing, aerospace, and electronics rely on laser welding for joining aluminum parts.
- Copper and Copper Alloys: Laser welding can be used to join copper and its alloys, such as brass and bronze. These materials are commonly used in electrical and electronic applications.
- Titanium: Titanium and its alloys are challenging to weld using conventional methods due to their high reactivity and susceptibility to contamination. Laser welding provides a precise and clean welding process for titanium components used in aerospace, medical, and industrial applications.
- Nickel Alloys: Laser welding is suitable for welding nickel-based alloys, which are commonly used in aerospace, petrochemical, and power generation industries due to their high strength and corrosion resistance.
- Precious Metals: Laser welding can be used for welding precious metals such as gold, silver, and platinum. These materials are often used in jewelry making and electronics manufacturing.
- Specialty Alloys: Laser welding machines can also weld specialty alloys such as Inconel, Hastelloy, and Monel, which are commonly used in high-temperature and corrosive environments in industries like aerospace, chemical processing, and marine engineering
Does Laser Welding Metal Need Gas?
- Inert Gases: Inert gases such as argon and helium are commonly used as shielding gases in laser welding. These gases are chemically inert and do not react with the molten metal or the surrounding atmosphere. Argon is often preferred for welding materials such as steel, stainless steel, and titanium, while helium is used for welding aluminum and other non-ferrous metals. Inert gases create a stable and consistent environment around the weld zone, reducing the risk of porosity and improving weld quality
- Active Gases: Active gases such as oxygen or nitrogen can also be used as shielding gases in laser welding, especially for certain applications or materials. These gases can react with the molten metal to alter the chemical composition of the weld or improve penetration. For example, oxygen is sometimes used in laser welding of carbon steels to enhance the weld depth and speed up the welding process. However, active gases require careful control to prevent excessive oxidation or other undesirable effects.
- Mixed Gases: Gas mixtures containing a combination of inert and active gases can be tailored to specific welding requirements, offering benefits such as improved weld quality, increased productivity, or reduced operating costs. Gas mixtures may include combinations of argon, helium, oxygen, nitrogen, or other gases in varying proportions, depending on the application.
Do I Need Welding Wire To Laser Weld Metal?
- Filling Gaps: In cases where there are gaps or variations in joint fit-up, filler material may be added to bridge the gap and ensure a complete weld.
- Alloying or Reinforcement: Filler material may be used to modify the chemical composition or mechanical properties of the weld joint, such as adding alloying elements or reinforcement for specific applications.
- Build-Up Welding: Laser welding can also be used for build-up welding, where additional material is deposited onto the base metal surface to restore worn or damaged components. In this case, a filler wire or powder may be used to add material to the weld pool.
How To Mitigate Laser Weld Distortion And Cracking?
- Controlled Heat Input: Laser welding allows for precise control over heat input, which can help minimize distortion and cracking. Adjusting parameters such as laser power, welding speed, and focal position can help regulate the amount of heat applied to the workpiece, reducing the risk of overheating and distortion.
- Preheating and Post-Weld Heat Treatment: Preheating the workpiece before welding can help reduce thermal gradients and stress buildup, minimizing distortion and cracking. Additionally, post-weld heat treatment processes such as stress relief annealing can help relieve residual stresses in the weld zone, improving the overall stability of the welded structure.
- Joint Design: Proper joint design can minimize deformation and cracking in laser welding. Avoiding sharp angles, reducing joint gaps, and using appropriate fit-up tolerances can help ensure uniform heat distribution and reduce the risk of stress concentration points that can lead to distortion and cracking.
- Fixturing and Clamping: Proper fixturing and clamping of the workpiece can help minimize movement and distortion during welding. Securely holding the parts in place with fixtures or jigs can help maintain alignment and stability, reducing the likelihood of distortion and cracking.
- Weld Sequence: Consider the welding sequence when planning the welding process. Welding in a sequence that minimizes thermal gradients and distortion can help reduce the likelihood of distortion and cracking. For example, welding from the center outward or using a back-stepping technique can help distribute heat more evenly and reduce distortion.
- Material Selection: Choosing the appropriate material and filler metal can also help mitigate distortion and cracking in laser welding. Selecting materials with similar thermal expansion coefficients and minimizing the difference in material thicknesses can help reduce stress buildup and distortion. Additionally, using filler metals with suitable mechanical properties and compatibility with the base material can help improve weld quality and reduce the risk of cracking.
How To Prevent The Workpiece From Overheating During Laser Welding?
- Optimize Laser Parameters: Adjust laser parameters such as power, pulse duration, frequency, and beam focus to control heat input to the workpiece. Reducing laser power or adjusting pulse duration can help reduce overheating. Use pulsed laser welding technology to control heat transfer to the workpiece and minimize overall heat input.
- Controlled Heat Input: Rapid heating and cooling cycles are achieved by controlling the dwell time of the laser beam on the workpiece. Limiting the exposure time to the laser beam helps prevent excessive heating. Dynamic laser power modulation technology is used to adjust the laser power in real time according to the thermal response of the workpiece to ensure consistent heat input.
- Cooling Strategy: Use active cooling techniques, such as air cooling or water cooling, to dissipate excess heat from the workpiece during the welding process. Precool or preheat the workpiece to a specific temperature range before welding to minimize thermal gradients and reduce the risk of overheating.
- Fixture Design: Use an efficient fixture design to provide adequate support and heat dissipation for the workpiece during the welding process. Proper fixture design helps minimize heat build-up and prevent localized overheating. Ensure proper ventilation and heat dissipation around the welding area to prevent heat build-up within the workpiece.
- Material Selection: Choose materials with good thermal conductivity and heat dissipation properties to reduce the risk of overheating during welding. Additionally, choose materials with lower coefficients of thermal expansion to minimize distortion and thermal stress caused by welding heat.
- Welding Sequence: Divide large welds into smaller sections and weld them sequentially to distribute heat more evenly and prevent local overheating. Implement intermittent welding techniques with controlled cooling intervals to allow the workpiece to dissipate heat between weld passes.
- Process Monitoring: Implement real-time temperature monitoring and feedback control systems to detect and prevent workpiece overheating during welding. Use thermal imaging or infrared temperature sensing technology to monitor the temperature distribution of the workpiece and adjust welding parameters accordingly.
Related Resources
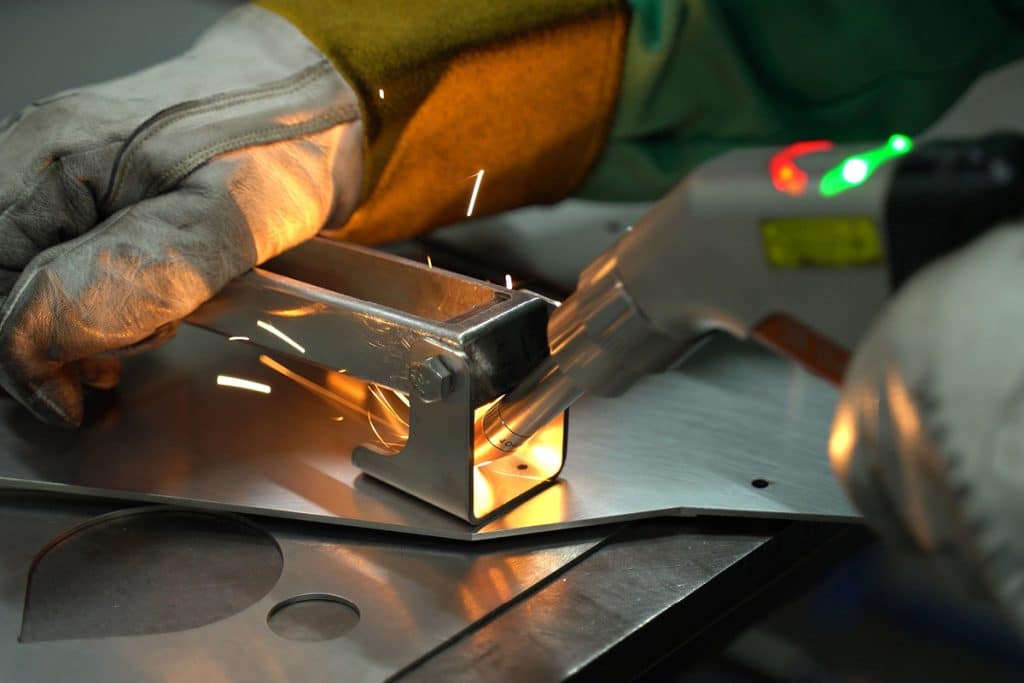
What Environmental Considerations Should Be Taken When Using Laser Welding Machines?
This article discusses the environmental issues and corresponding measures to be taken when using laser welding machines.
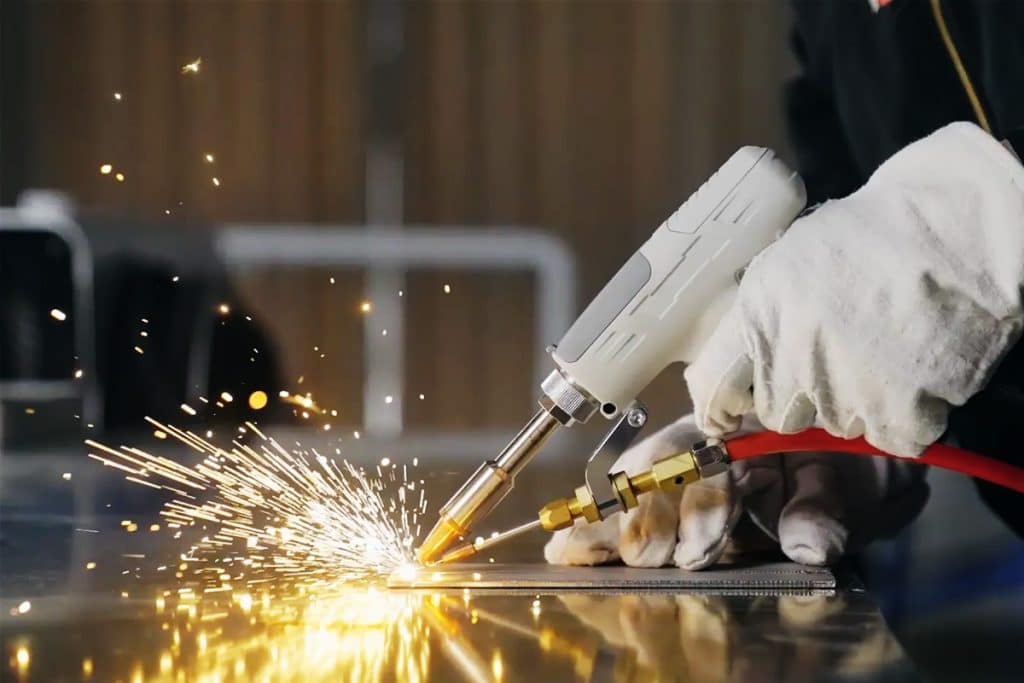
Which Laser Generator Is Best for Welding?
This article mainly compares CO2 laser generators, fiber laser generators, and Nd: YAG laser generators to help users make scientific selections based on their welding needs.
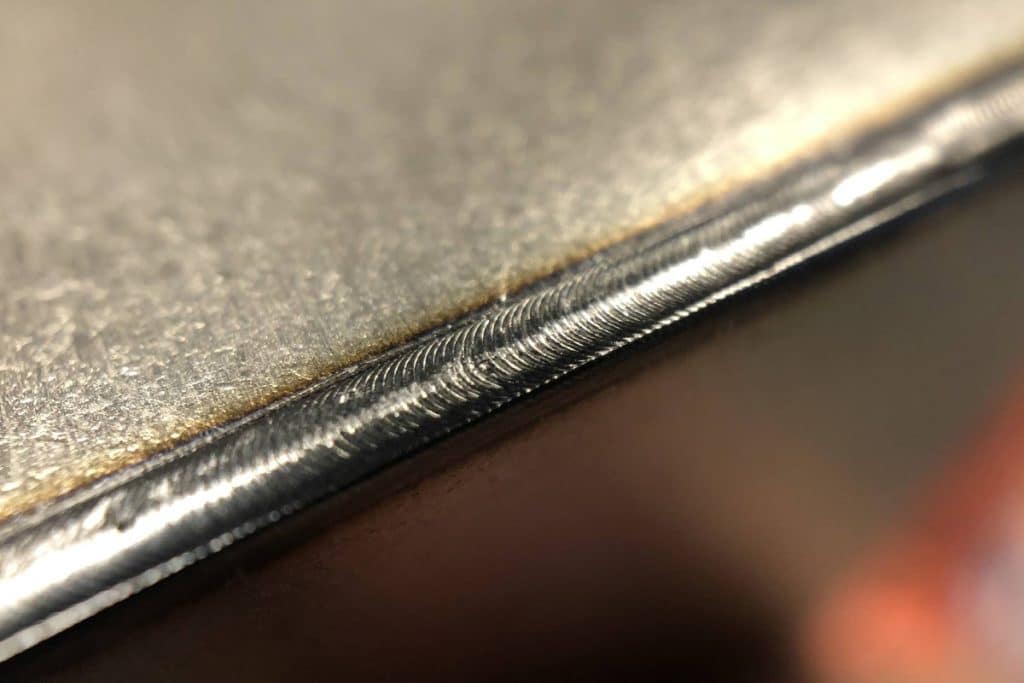
How Does Laser Welding Achieve Deep Melting of Materials?
This article mainly discusses how laser welding can achieve deep melting of materials, including its basic principles, key factors affecting penetration depth, the formation mechanism of deep penetration, and optimization