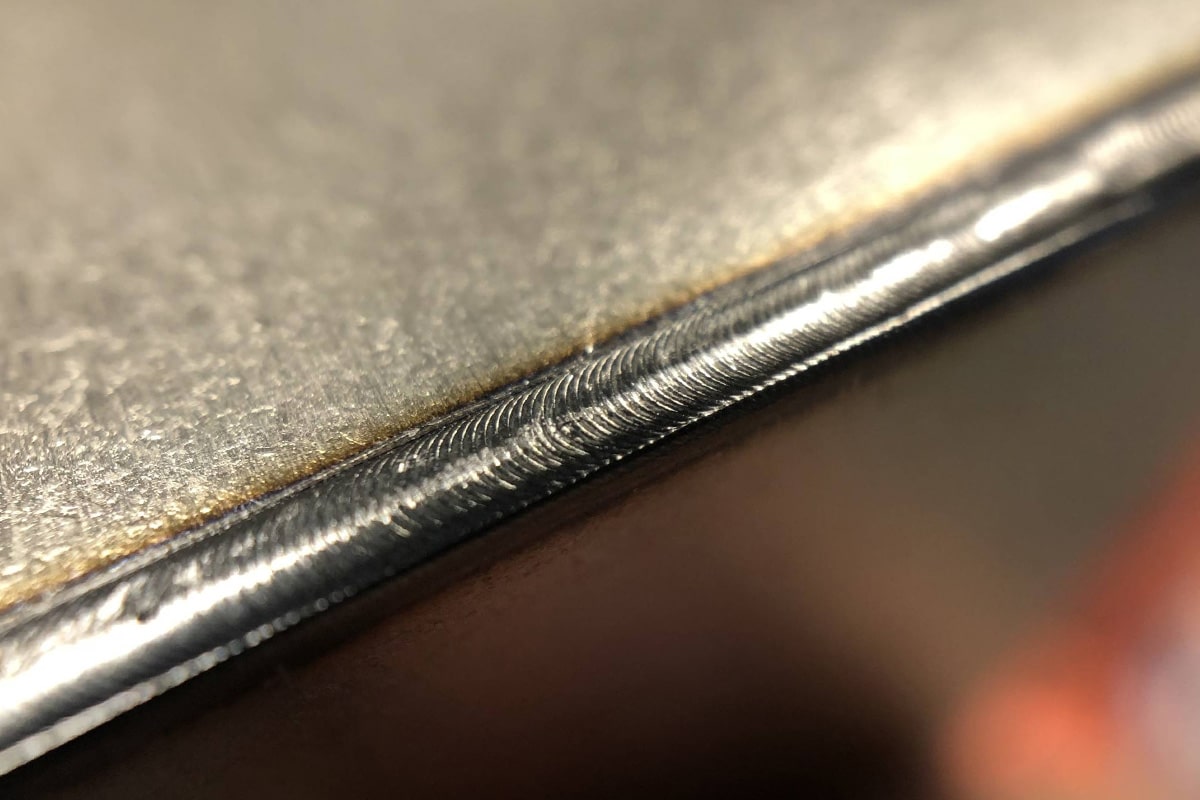
Lazer Kaynak, Malzemelerin Derin Erimesini Nasıl Sağlar?
Verimli ve hassas bir kaynak teknolojisi olarak lazer kaynak, yüksek enerji yoğunluğu, temassız işleme ve küçük ısıdan etkilenen bölge avantajları nedeniyle otomobil, havacılık ve elektronik gibi birçok endüstride yaygın olarak kullanılmaktadır. Geleneksel kaynak yöntemleriyle karşılaştırıldığında, lazer kaynak karmaşık yapıların bağlantısını daha hızlı bir hızda, daha az termal deformasyon ve daha yüksek kaynak mukavemetiyle tamamlayabilir ve özellikle hassas üretim ve yüksek talepli endüstriyel üretim senaryoları için uygundur.
Lazer kaynak işleminde, malzemelerin derin penetrasyon kaynağının elde edilmesi, lazer parametreleri, malzeme özellikleri ve kaynak işlemi kontrolü gibi birden fazla faktörün kapsamlı bir şekilde değerlendirilmesini gerektirir. Bu makale, lazer kaynağının temel prensiplerini, penetrasyon derinliğini etkileyen temel faktörleri derinlemesine inceleyecek ve işletmelerin lazer kaynak teknolojisini daha iyi uygulamalarına ve kaynak kalitesini ve üretim verimliliğini artırmalarına yardımcı olmak için derin penetrasyonun oluşum mekanizmasını ve optimizasyon stratejisini ayrıntılı olarak analiz edecektir.
İçindekiler
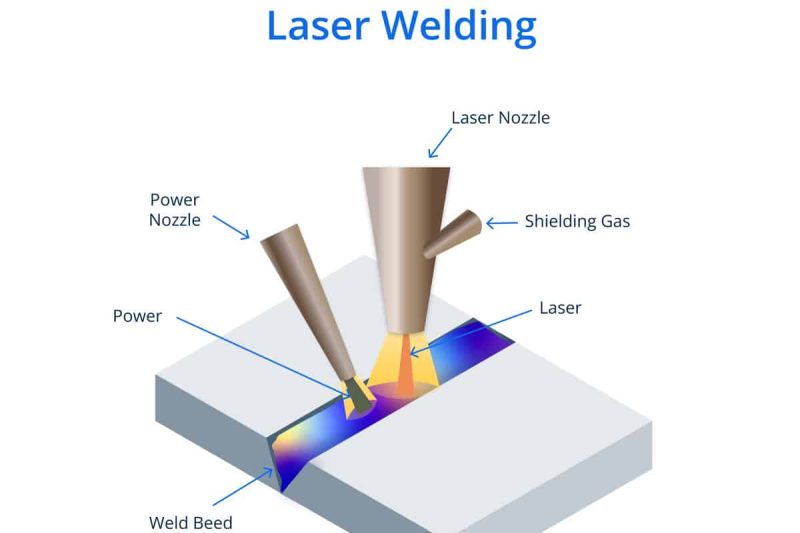
Lazer kaynak hakkında bilgi edinin
Tanım ve Gerekçe
Lazer kaynak, kaynak işlemini gerçekleştirmek için malzemeyi yerel olarak erime noktasına ısıtmak amacıyla bir lazer ışınını ısı kaynağı olarak kullanan bir işlemdir. Lazer ışını kaynak alanına odaklanır ve yüksek yoğunluklu ışık enerjisi, soğuduktan sonra güçlü bir kaynaklı bağlantı oluşturan erimiş bir havuz oluşturmak için malzemeyi hızla ısıtır ve eritir. Lazer kaynak, yüksek enerji yoğunluğu, yüksek hassasiyet ve yüksek kaynak hızı özelliklerine sahiptir ve hassas parçaları kaynaklamak için uygundur.
Lazer Kaynak İşlemine Genel Bakış
Lazer kaynak işlemi genellikle lazer ışınımı, malzemenin ısıtılması ve eritilmesi, erimiş havuz oluşumu, soğutulması ve katılaştırılması vb. adımları içerir. Bu adımlarda lazer enerjisinin etkili kullanımı ve malzemelerin etkileşimi, özellikle derin erime kabiliyeti olmak üzere kaynak etkisini belirler.
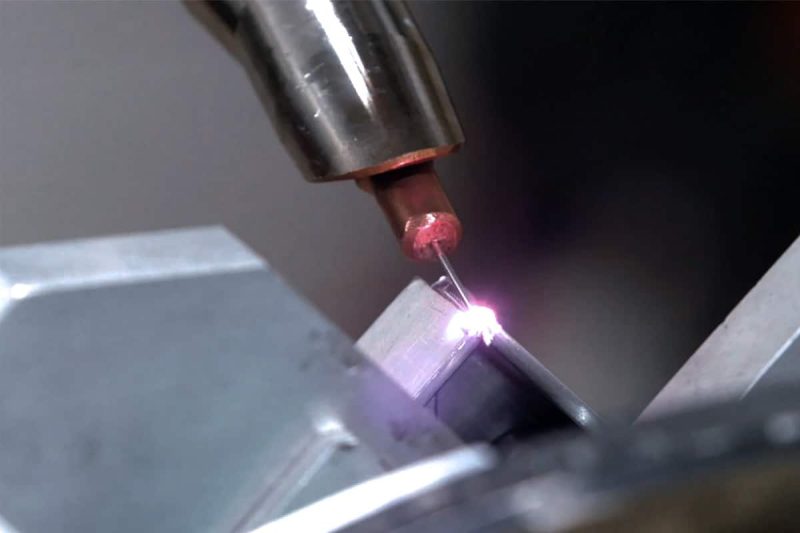
Lazer ışınının malzemelerle etkileşimi
Lazer kaynağının özü, lazer ışını ile malzeme arasındaki etkileşimde yatar ve bu, verimli ve derin nüfuzlu kaynak elde etmenin anahtarıdır. Lazer ışını, yüksek enerji yoğunluklu bir ışık kaynağıdır. Bir malzemenin yüzeyini ışınladığında, malzeme tarafından kısmen emilir, yansıtılır veya iletilir. Emilen ışık enerjisi daha sonra ısı enerjisine dönüştürülür ve malzemenin hızla ısınmasına ve erimiş veya buharlaşmış bir duruma girmesine neden olur, böylece kaynak tamamlanır. Farklı malzemelerin emicilik, termal iletkenlik ve erime noktası gibi fiziksel özellikleri, lazer kaynağının verimliliği ve kalitesi üzerinde önemli bir etkiye sahiptir. Bu nedenle, malzemenin lazer enerjisini emmesini ve ışık enerjisinin ısı enerjisine dönüşümünü anlamak, kaynak sürecini optimize etmek.
Lazer enerjisinin malzemeler tarafından emilmesi
Bir malzemenin lazer kaynaktaki performansı ilk olarak lazer enerjisini emme yeteneğinden etkilenir. Emilim, malzemenin lazer enerjisini emme yeteneğini ölçmek için önemli bir parametredir ve bu da yüzey alanındaki lazer enerjisinin dönüşüm verimliliğini belirler. Farklı malzemelerin farklı dalga boylarındaki lazerler için farklı emilim oranları vardır. Örneğin, demir ve paslanmaz çelik fiber lazer jeneratörleri için yüksek bir emilim oranına sahiptir (yakın kızılötesi bant), bu nedenle kararlı bir erimiş havuz oluşturmak kolaydır. Öte yandan, yüksek yansıtıcılığa sahip metaller gibi alüminyum Ve bakır düşük emilim oranına sahiptir ve bu da büyük enerji kaybına neden olur. Emilim oranını iyileştirmek için daha yüksek güçlü lazerler veya özel dalga boyları (mavi veya yeşil lazerler gibi) gerekir. Ayrıca, malzemenin yüzeyindeki oksit tabakası, pürüzlülük ve sıcaklık gibi faktörler de lazerin emilim etkisini etkileyecektir. Bu nedenle, kaynak stabilitesini iyileştirmek için genellikle kaynaktan önce yüzey ön işlemi gerekir.
Işık enerjisinin ısı enerjisine dönüşmesi
Lazer ışını malzemenin yüzeyini ışınladığında, emilen ışık enerjisi hızla ısı enerjisine dönüşür ve bu da malzeme sıcaklığının hızla yükselmesine neden olur. Sıcaklık erime noktasına ulaştığında, malzeme erimiş bir duruma girer ve erimiş bir havuz oluşturur; sıcaklık buharlaşma sıcaklığına daha da yükseltilirse, malzemenin bir kısmı buharlaşarak iğne deliği etkisi oluşturur ve böylece derin penetrasyon kaynağı elde edilir. Işık enerjisinin ısı enerjisine dönüşüm verimliliği, doğrudan kaynak derinliğini ve kalitesini belirler. Enerji dönüşümü yetersizse, sığ kaynaklara, zayıf füzyona veya hatta kararlı bir kaynak bağlantısı oluşturulamamasına neden olabilir. Aşırı enerji girişi, malzemenin aşırı yanmasına, gözeneklere veya kaynak deformasyonuna neden olabilir. Bu nedenle, lazer gücü, ışın modu ve kaynak hızı gibi parametrelerin makul bir şekilde kontrol edilmesi, enerji dönüşüm sürecini etkili bir şekilde optimize edebilir ve kaynak kalitesini artırabilir.
Lazer ışını ile malzeme arasındaki etkileşim, lazer kaynağının özünü oluşturur. Anahtar, malzemenin lazer enerjisini emmesi ve ışık enerjisinin ısı enerjisine verimli bir şekilde dönüştürülmesinde yatar. Farklı malzemelerin emilim oranı ve ısıl iletkenlik özellikleri, kaynak etkisini doğrudan etkiler. Lazer dalga boyu, güç yoğunluğu ve kaynak parametreleri optimize edilerek, ışık enerjisinin kullanım oranı iyileştirilebilir ve böylece yüksek kaliteli derin penetrasyonlu kaynak elde edilebilir. Bu etkileşimlerin temel prensiplerinin anlaşılması, kaynak sürecini optimize etmeye, kaynağın kararlılığını ve mukavemetini iyileştirmeye ve farklı endüstriyel alanların uygulama gereksinimlerini karşılamaya yardımcı olacaktır.
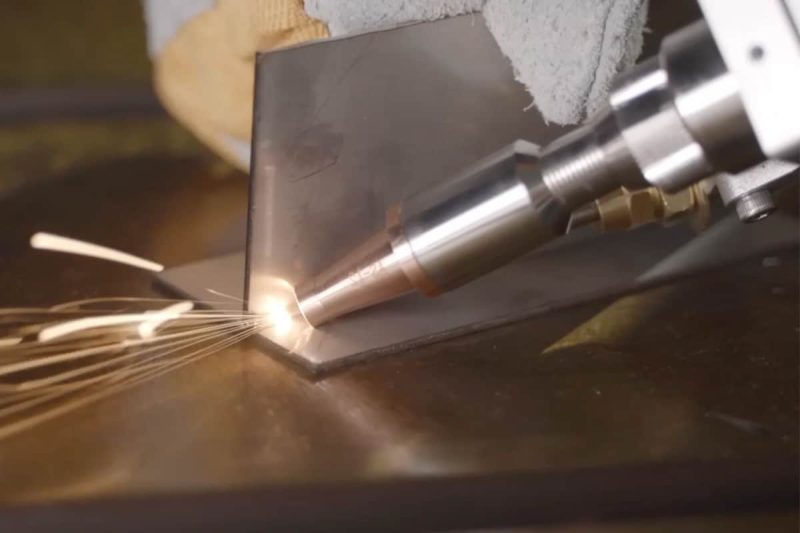
Penetrasyon derinliğini etkileyen temel faktörler
Lazer kaynağının derin penetrasyon etkisi, kaynak kalitesinin temel göstergelerinden biridir. Penetrasyon derinliği, kaynağın mukavemetini ve güvenilirliğini doğrudan etkiler. Kaynak derinliği, lazer parametreleri, malzeme özellikleri, iş parçası geometrisi ve montajı ve kaynak hızı dahil olmak üzere birçok faktörden etkilenir. Bu faktörler, erimiş havuzun oluşumunu ve genişlemesini belirlemek için etkileşime girer. Bu parametrelerin makul bir şekilde optimize edilmesi, kaynak derinliğini etkili bir şekilde artırabilir ve kaynağın kararlılığını ve tutarlılığını sağlayabilir.
Lazer parametreleri
- Güç: Lazer gücü, kaynak derinliğini etkileyen ana faktördür. Daha yüksek lazer gücü, malzemeyi daha derin bir seviyede eritmek için daha güçlü enerji sağlayabilir. Genellikle, güç arttıkça kaynak derinliği de buna göre artacaktır, ancak çok yüksek güç aşırı yanmaya veya kaynak kusurlarına neden olabilir.
- Işın odağı ve nokta boyutu: Lazer odağının boyutu enerjinin konsantrasyonunu belirler. Daha küçük bir odak daha yüksek enerji yoğunluğu sağlayabilir ve böylece kaynak derinliğini artırabilir. Genellikle, odak konumunu doğru bir şekilde ayarlayarak, farklı kaynak ihtiyaçlarını karşılamak için erime derinliği ve erime genişliği arasında en iyi denge sağlanabilir.
- Darbe süresi ve frekansı: Darbeli lazer kaynağı için, kısa sürede yüksek enerji girişi, malzemenin hızla ısınmasına ve daha derin bir seviyeye nüfuz etmesine yardımcı olur. Darbe parametrelerinin makul bir şekilde ayarlanması, kaynağın şekillendirme kalitesini optimize edebilir ve kaynak stabilitesini iyileştirebilir.
Malzeme özellikleri
- Isıl iletkenlik: Bir malzemenin ısıl iletkenliği lazer enerjisinin yayılmasını etkiler. Yüksek ısıl iletkenliğe sahip malzemeler (bakır ve alüminyum gibi) ısıyı hızla kaybeder ve bu da derin erimenin azalmasına neden olur. Düşük ısıl iletkenliğe sahip malzemeler (paslanmaz çelik gibi) ısıyı daha etkili bir şekilde yoğunlaştırabilir ve daha büyük bir penetrasyon derinliğine ulaşabilir.
- Emilim katsayısı: Malzemenin lazer ışığını emme yeteneği, derin penetrasyonu belirlemede önemli bir faktördür. Daha yüksek bir emilim katsayısı enerji kullanımını iyileştirebilir ve böylece kaynak sonuçlarını geliştirebilir. Yüksek yansıtıcı malzemeler için genellikle belirli bir dalga boyunda lazer kullanmak veya emilimi artırmak için yüzeyi önceden işlemek gerekir.
İş parçası geometrisi ve montajı
İş parçasının şekli ve montaj yöntemi de lazer kaynağının derin erime etkisi üzerinde doğrudan bir etkiye sahiptir. Karmaşık geometrik şekiller, lazer ışınının hedef alanı doğru bir şekilde ışınlamasını zorlaştırabilir ve erime derinliğini etkileyebilir. Ayrıca, iş parçasının montaj boşluğu çok büyükse veya konumlandırma yanlışsa, düzensiz kaynaklamaya neden olabilir ve kaynak kalitesini düşürebilir. Bu nedenle, lazer ışınının kaynak alanı üzerinde stabil bir şekilde etki edebilmesini sağlamak için kaynaktan önce hassas montaj ve konumlandırma gerekir.
Kaynak hızı
Kaynak hızı, malzemenin lazer enerjisini emdiği zamanı belirler ve böylece erimiş havuzun oluşumunu etkiler. Daha yavaş kaynak hızları genellikle ısı girişini artırır, malzemeye erimesi için yeterli zaman verir ve böylece penetrasyon derinliğini artırır. Ancak hız çok yavaşsa, aşırı ısınmaya veya kaynak deformasyonuna neden olabilir. Tersine, daha hızlı kaynak hızları penetrasyon derinliğini azaltabilir ve kaynak bağlantısını zayıflatabilir. Bu nedenle, gerçek operasyonda, en iyi kaynak kalitesini elde etmek için kaynak hızının malzeme özelliklerine ve kaynak gereksinimlerine göre optimize edilmesi gerekir.
Lazer kaynağının nüfuz derinliği birçok faktörden etkilenir, bunların arasında lazer parametreleri, malzeme özellikleri, iş parçası geometrisi ve kaynak hızı kaynak etkisini belirlemede temel faktörlerdir. Lazer gücü, odak konumu, kaynak hızı ve optimizasyon gibi parametrelerin makul kontrolü, malzeme özellikleriyle birleştirildiğinde derin nüfuz kaynağının kararlılığını ve kalitesini etkili bir şekilde iyileştirebilir. Bu faktörlerin kapsamlı bir şekilde düzenlenmesiyle, kaynak işleminin kararlı ve güvenilir olması sağlanabilir ve farklı endüstriyel uygulama senaryolarının ihtiyaçları karşılanabilir.
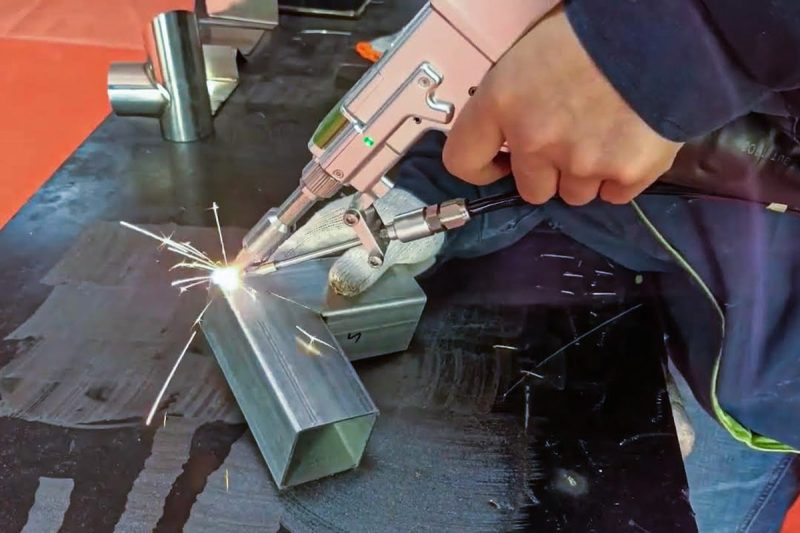
Derin penetrasyon kontrol stratejisi
Lazer kaynak işleminde, istikrarlı ve tutarlı derin penetrasyon elde etmek çok önemlidir. Kaynak derinliği, lazer gücü, odak konumu, malzeme özellikleri ve kaynak hızı gibi birçok faktörden etkilendiğinden, kaynak kalitesini ve tutarlılığını sağlamak için lazer parametrelerini optimize etme ve gerçek zamanlı izleme ve geri bildirim gibi stratejilere ihtiyaç vardır. Bu kontrol stratejileri yalnızca kaynak mukavemetini iyileştirmekle kalmaz, aynı zamanda kaynak kusurlarını azaltabilir ve üretim verimliliğini artırabilir.
Lazer parametre optimizasyonu
Derin penetrasyonlu kaynak için lazer parametrelerinin hassas kontrolü çok önemlidir. Optimize edilmiş ana parametreler şunlardır:
Lazer gücü:
- Daha yüksek güç, daha fazla enerji girişi sağlayarak malzemenin daha derin erimesine ve dolayısıyla kaynak derinliğinin artmasına neden olabilir.
- Çok yüksek güç, malzemenin aşırı erimesine veya buharlaşmasına neden olarak gözenek veya çatlak gibi kaynak kusurlarının oluşmasına yol açabilir.
- Çok düşük güç yetersiz penetrasyona neden olabilir ve kaynak mukavemetini etkileyebilir.
Odak boyutu ve konumu:
- Küçük odak çapı enerji yoğunluğunu artırarak lazerin malzemeye daha etkili bir şekilde nüfuz etmesini sağlar ve böylece penetrasyon derinliği artar.
- Odak pozisyonunun optimize edilmesi, enerjinin kaynak alanında etkili bir şekilde yoğunlaşmasını sağlayarak, aşırı enerji dağılımının veya yeterli derinlik olmadan yüzey erimesinin önlenmesini sağlar.
Darbe süresi ve frekansı (darbeli lazer kaynağı için):
- Kısa darbe süresi yüksek frekansla birleştirildiğinde, yeterli penetrasyon sağlanırken ısıdan etkilenen bölge azaltılabilmektedir.
- Daha uzun darbe süresi enerjinin daha derinlere nüfuz etmesine yardımcı olur ancak ısıdan etkilenen bölgeyi artırarak kaynak doğruluğunu etkileyebilir.
Deneyler ve bilgisayar simülasyonları yoluyla, farklı malzeme ve kaynak gereksinimleri için lazer parametrelerinin optimum kombinasyonu bulunarak, kaynak derinliğinin ve kalitesinin en iyi seviyeye ulaşması sağlanabilir.
Gerçek zamanlı izleme ve geri bildirim
Kaynak işlemi sırasında tutarlı penetrasyonu korumak için, kaynak parametrelerini ayarlamak üzere gerçek zamanlı izleme ve geri bildirim sistemleri gereklidir. Bu sistemler genellikle optik sensörler, termal görüntüleyiciler, lazer güç monitörleri vb. içerir ve bunlar kaynak işlemi sırasında malzemenin tepkisini algılayabilir ve verilere göre kaynak parametrelerini otomatik olarak ayarlayabilir.
İzlenecek temel parametreler:
- Erimiş havuz sıcaklığı: Kızılötesi kamera veya spektral analiz yoluyla, erimiş havuz sıcaklığı gerçek zamanlı olarak ölçülebilir ve böylece ısı girişinin makul bir aralıkta kaldığından emin olunabilir.
- Erimiş havuz morfolojisi: Erimiş havuzun şekli ve dinamik değişimleri, homojen ve kararlı kaynaklamayı garantilemek için yüksek hızlı bir kamera ile izlenir.
- Lazer gücü dalgalanması: Ekipman dengesizliği nedeniyle kaynak kalitesindeki dalgalanmaları önlemek için lazer gücünü otomatik olarak algılar ve ayarlar.
Geri Bildirim Mekanizması:
- Akıllı kontrol sistemi, olası sapmaları telafi etmek için izleme verilerine göre lazer parametrelerini otomatik olarak ayarlayabilir. Örneğin, sensör yetersiz penetrasyon tespit ettiğinde, sistem lazer gücünü otomatik olarak artırabilir veya odak konumunu ayarlayabilir.
- Manuel ayarlama: Yüksek hassasiyetli uygulama senaryolarında, operatörler kaynak kalitesinin gereksinimleri karşıladığından emin olmak için izleme verilerine dayanarak kaynak parametrelerini manuel olarak ince ayarlayabilir.
Lazer kaynağının derin erime etkisini sağlamak için lazer parametre optimizasyonu ve gerçek zamanlı izleme ve geri bildirim stratejileri gereklidir. Lazer gücü, odak boyutu ve darbe süresi gibi parametreleri makul bir şekilde ayarlayarak kaynak derinliği etkili bir şekilde iyileştirilebilir. Aynı zamanda, gelişmiş izleme sistemlerinin yardımıyla, kaynak işlemi sırasında temel parametreler gerçek zamanlı olarak tespit edilebilir ve ayarlanabilir, böylece erime derinliğinin kararlılığı ve tutarlılığı sağlanır. Bu kontrol stratejileri yalnızca kaynak kalitesini iyileştirmekle kalmaz, aynı zamanda kaynak kusurlarını azaltabilir ve üretim verimliliğini artırabilir, böylece lazer kaynak teknolojisi endüstriyel üretimde daha güvenilir ve verimli hale gelir.
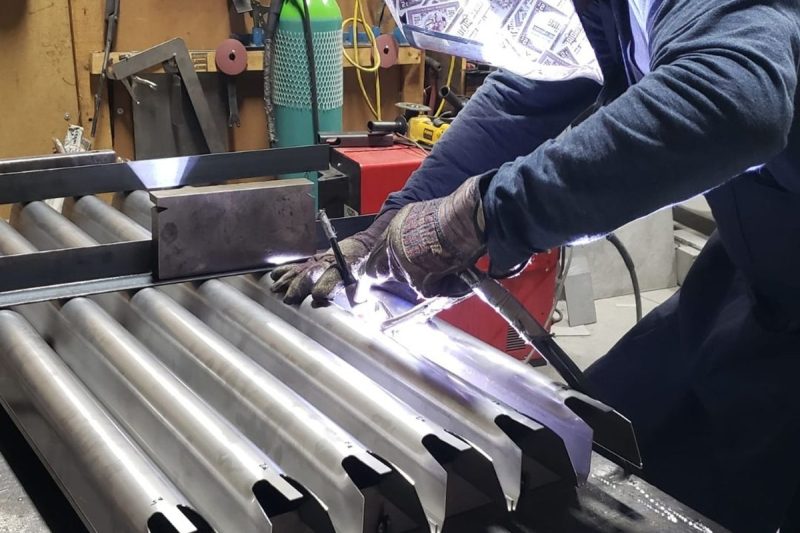
Uygulamalar ve Endüstriler
Lazer kaynak teknolojisi, yüksek hassasiyeti, yüksek verimliliği ve karmaşık malzemelere uyarlanabilirliği nedeniyle birçok endüstride yaygın olarak kullanılmaktadır, özellikle kaynak kalitesi ve derinliği için son derece yüksek gereksinimleri olan alanlarda. Lazer kaynak teknolojisinin avantajları, onu geleneksel kaynak teknolojisinin karşılayamadığı ihtiyaçları çözmek için ideal bir seçim haline getirir. Aşağıda, modern endüstride lazer kaynak teknolojisinin önemini ve geniş uygulamasını gösteren bazı tipik endüstriler ve uygulama alanları verilmiştir.
otomotiv endüstrisi
Lazer kaynak, özellikle yüksek mukavemetli çelik ve alüminyum alaşımlı gövde yapısal parçalarının kaynaklanmasında otomobil üretiminde yaygın olarak kullanılır. Lazer kaynak, derin kaynak penetrasyonu sağlayabilir, gövdenin mukavemetini garanti altına alabilir ve deformasyonu azaltabilir. Verimli lazer kaynak, üretim verimliliğini artırmak için otomatik üretim hatları için de uygundur.
- Yüksek mukavemetli çelik: Lazer kaynak, kullanılan malzeme miktarını azaltırken, araç gövdesinin mukavemetini ve güvenliğini sağlamak için yüksek mukavemetli çelik üzerinde derin kaynak yapabilir; bu da hafif tasarıma katkıda bulunur.
- Alüminyum alaşım kaynak: Alüminyum alaşımı, modern otomobil üretiminde yaygın olarak kullanılan hafif bir malzemedir. Lazer kaynak teknolojisi, hassas enerji kontrol yeteneği sayesinde alüminyum alaşımının etkili derin kaynağını elde edebilir ve bağlantının mukavemetini ve kararlılığını garanti edebilir.
- Otomatik üretim hattı: Lazer kaynağının yüksek hızı ve yüksek hassasiyeti, üretim verimliliğini artıran ve manuel müdahaleyi azaltan otomatik üretim hatları için uygun hale getirir ve büyük ölçekli üretimin ihtiyaçlarını karşılar.
Havacılık ve Uzay
Havacılık endüstrisinde lazer kaynak, hafif alaşımların ve kompozit malzemelerin hassas kaynaklanması için kullanılır. Derin kaynak kabiliyeti ve yüksek hassasiyeti nedeniyle lazer kaynak, alaşımlı malzemeler ve yapısal bileşenler için ideal bir kaynak yöntemi haline gelmiş olup, aşırı koşullar altında bileşenlerin güvenilirliğini garanti altına almaktadır.
- Alaşımlı malzemeler: Havacılık uygulamalarında, alaşımlı malzemeler (titanyum alaşımları, alüminyum alaşımları vb.) yapısal bileşenleri üretmek için yaygın olarak kullanılır. Lazer kaynak, aşırı çalışma koşullarında bileşenlerin güvenilirliğini sağlamak için daha derin bir erimiş havuz ve daha güçlü kaynak mukavemeti sağlayabilir.
- Kompozit malzeme kaynağı: Kompozit malzemeler hafif ve yüksek mukavemetli olmaları nedeniyle havacılık alanında yaygın olarak kullanılır. Lazer kaynak, yapının bütünlüğünü sağlamak için bu malzemelerin hassas bir şekilde kaynaklanmasını sağlayabilir.
- Yüksek hassasiyet ve yüksek kalite gereksinimleri: Havacılık parçalarının kaynaklanması son derece yüksek hassasiyet ve kalite gerektirir. Lazer kaynak, geleneksel kaynak yöntemlerinde oluşabilecek ısıdan etkilenen bölgeyi ve kaynak deformasyonunu etkili bir şekilde önleyebilir ve kaynaklı parçaların mukavemetini ve dayanıklılığını garanti eder.
Elektronik Sanayi
Elektronik cihazlardaki küçük bileşenler, bileşenlerin yüksek güvenilirliğini ve kararlılığını sağlamak için genellikle lazer kaynakla hassas bir şekilde kaynaklanır. Lazer kaynak, diğer bileşenlere zarar vermemek için yüksek hassasiyetli derin kaynak sağlayabilir ve bu da onu mikroelektronik bileşenlerin üretimi için uygun hale getirir.
- Mikroelektronik bileşenler: Lazer kaynağı genellikle sensörler, piller, entegre devreler vb. gibi mikroelektronik bileşenlerin kaynağında kullanılır. Bu bileşenlerin kaynak kalitesi için çok yüksek gereksinimleri vardır ve lazer kaynağı, termal hasarı ve bileşen deformasyonunu önlemek için hassas ısı girişi sağlayabilir.
- Hassas kaynak: Elektronik sektöründe lazer kaynak teknolojisi, çevredeki hassas bileşenlere zarar vermeden çok hassas küçük bileşen bağlantılarını tamamlayabilir.
- Ürün güvenilirliğini artırın: Lazer kaynak, uzun süreli kullanımda elektronik ürünlerin güvenilirliğini ve dayanıklılığını garanti ederek güçlü ve sağlam kaynaklı bağlantılar sağlayabilir.
Lazer kaynak teknolojisi, yüksek hassasiyeti, yüksek verimliliği ve karmaşık malzemelere uyarlanabilirliği nedeniyle otomobil, havacılık, elektronik, tıbbi, hassas aletler vb. gibi birçok endüstride yaygın olarak kullanılmaktadır. Bilim ve teknolojinin ilerlemesiyle birlikte lazer kaynak daha fazla alanda önemli bir rol oynayacak, modern endüstrinin yüksek kaliteli ve yüksek hassasiyetli kaynak ihtiyacını karşılayacak ve çeşitli endüstrilerde üretim teknolojisinin gelişimini teşvik edecektir.
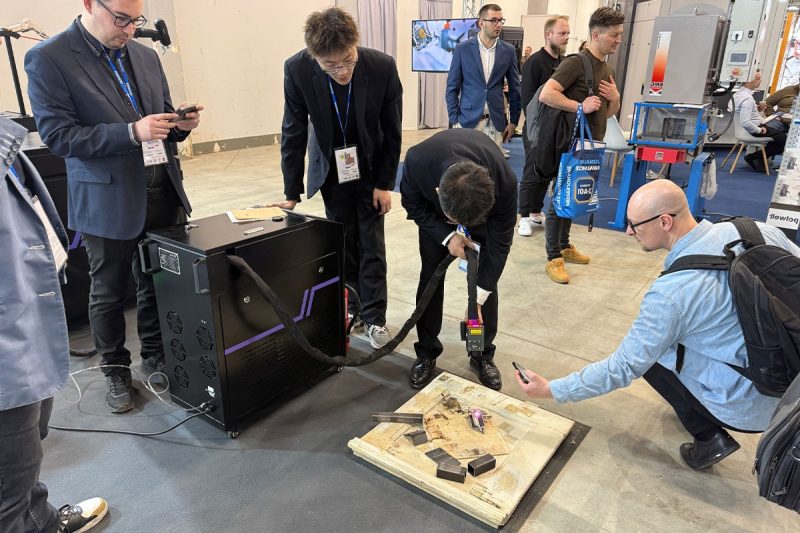
özetle
Lazer kaynakla derin penetrasyon elde etme süreci karmaşık ve hassastır, lazer ve malzeme arasındaki etkileşimi, birden fazla temel faktörün optimizasyonunu ve kontrolünü ve birden fazla derin penetrasyon mekanizmasını içerir. Lazer parametrelerinin hassas kontrolü ve gerçek zamanlı izleme yoluyla, malzeme kalitesinden ödün vermeden derin kaynak elde edilebilir. Bu teknoloji birçok endüstride, özellikle otomobiller, havacılık ve elektronik gibi yüksek hassasiyetli alanlarda yaygın olarak kullanılmaktadır. Teknolojinin sürekli gelişmesiyle, lazer kaynak daha fazla endüstride benzersiz avantajlarını gösterecektir.
Yukarıdaki içerikte, lazer kaynaklama prensiplerini ve süreçlerini derinlemesine analiz ettik ve derin erime ve temel kontrol stratejilerine nasıl ulaşılacağına odaklandık. Bir endüstri lideri olarak, AccTek Lazer verimli lazer kaynak çözümleri sunmaya kendini adamıştır. lazer kaynak makineleri çeşitli endüstrilerin yüksek hassasiyetli ve yüksek kaliteli kaynak ihtiyaçlarını karşılayabilir. Herhangi bir sorunuz veya ihtiyacınız varsa, lazer kaynak konusunda daha profesyonel tavsiyeler ve hizmetler için lütfen bizimle iletişime geçin.
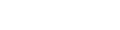
İletişim bilgileri
- [email protected]
- [email protected]
- +86-19963414011
- 3 Bölge A, Lunzhen Sanayi Bölgesi, Yucheng Şehri, Shandong Eyaleti.
Lazer Çözümleri Alın