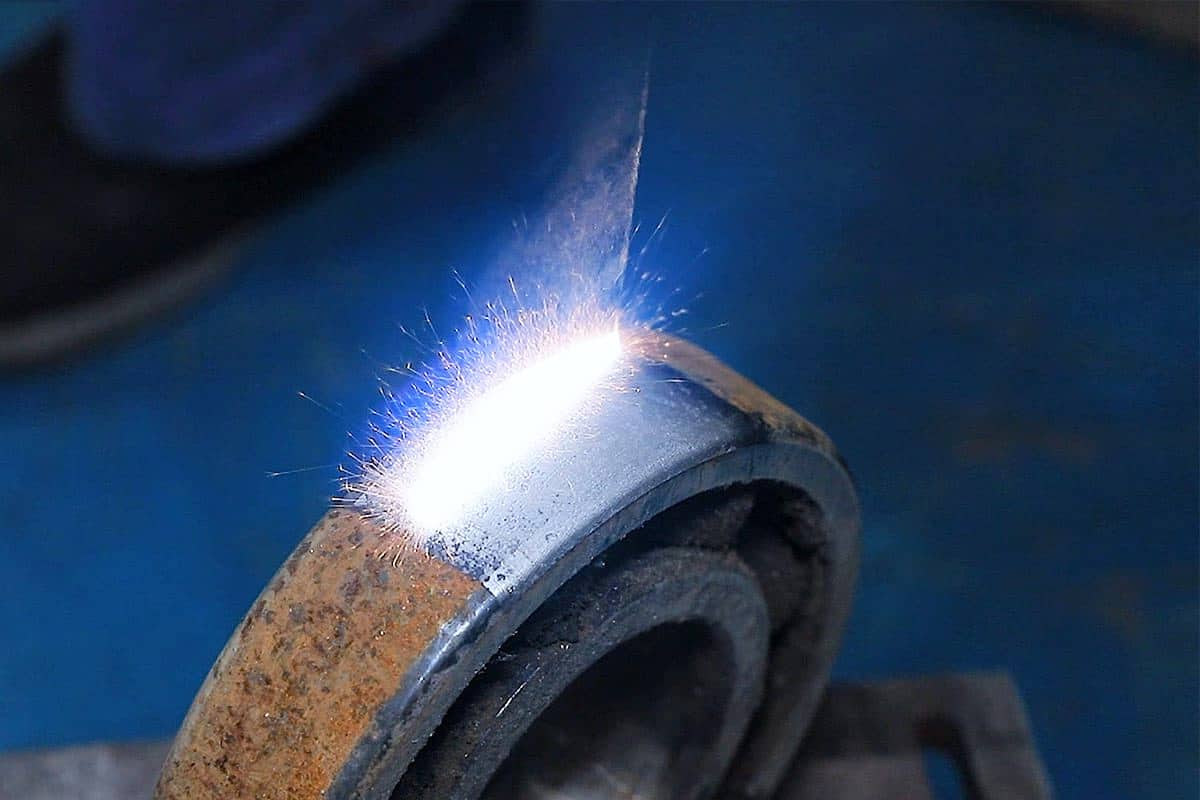
Will Pulsed Laser Cleaning Damage the Substrate?
Pulsed laser cleaning has gained widespread popularity in applications such as laser surface preparation and fiber laser rust removal due to its high efficiency, eco-friendliness, and non-contact nature. However, one critical concern remains for many users: Can this technology damage the substrate?
This article explores the fundamentals of pulsed laser cleaning, examining potential thermal, mechanical, and photochemical effects that could lead to substrate damage under various parameter settings. We’ll also look into key influencing factors, such as thermal conductivity and absorption rate of the material, and introduce practical strategies—like parameter optimization, multi-pulse control, and real-time temperature monitoring—to minimize risk.
Table of Contents
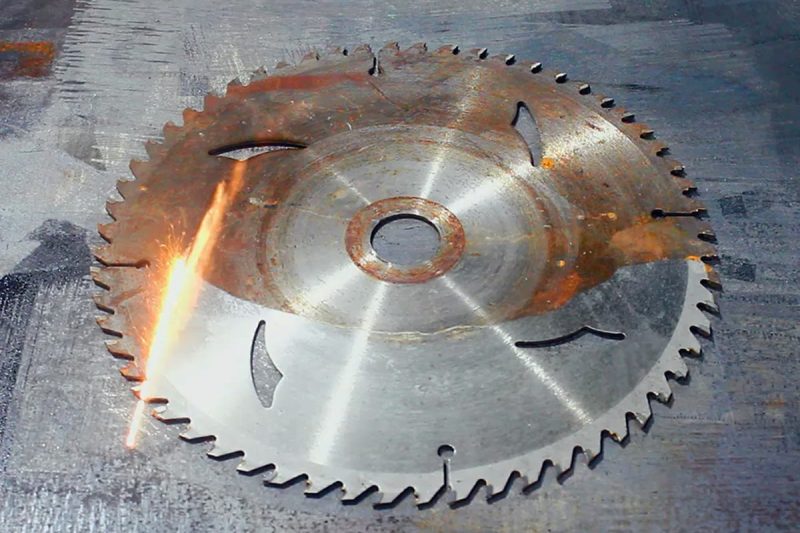
Understanding Pulsed Laser Cleaning
Pulsed laser cleaning is an efficient, eco-friendly, and non-contact surface treatment technology widely used in applications such as laser rust removal, paint removal, oxide layer cleaning, and laser surface preparation for precision molds and electronic components. The core principle involves high-energy laser pulses that rapidly vaporize or remove contaminants from the substrate without causing significant thermal effects or mechanical damage to the material.
In practical applications, understanding and optimizing the following key parameters is essential for improving cleaning efficiency and ensuring substrate safety:
- Pulse Duration: Refers to the duration of a single laser pulse, typically in the nanosecond, picosecond, or even femtosecond range. Shorter pulses help reduce the heat-affected zone (HAZ), making them ideal for precision cleaning of heat-sensitive materials.
- Pulse Energy: Represents the energy carried by each laser pulse, directly affecting the cleaning capability. Higher pulse energy is effective for removing strongly adhered contaminants, but it must be carefully controlled to prevent substrate damage.
- Repetition Rate: Refers to the frequency of laser pulses emitted per unit time. A higher repetition rate can increase cleaning speed but, if not properly controlled, may cause heat accumulation and lead to thermal damage.
- Wavelength: The wavelength of the laser determines its interaction with different materials. For example, metals typically respond better to a 1064nm laser wavelength.
- Beam Profile: Refers to the energy distribution of the laser beam in space. An ideal beam profile should have uniform energy distribution, ensuring stable and efficient cleaning while avoiding localized overheating or uneven cleaning.
In applications such as laser rust removal, laser cleaning molds, or other industrial uses, properly configuring these parameters not only improves efficiency but also protects the material, making it a crucial factor in achieving high-quality pulsed laser cleaning.
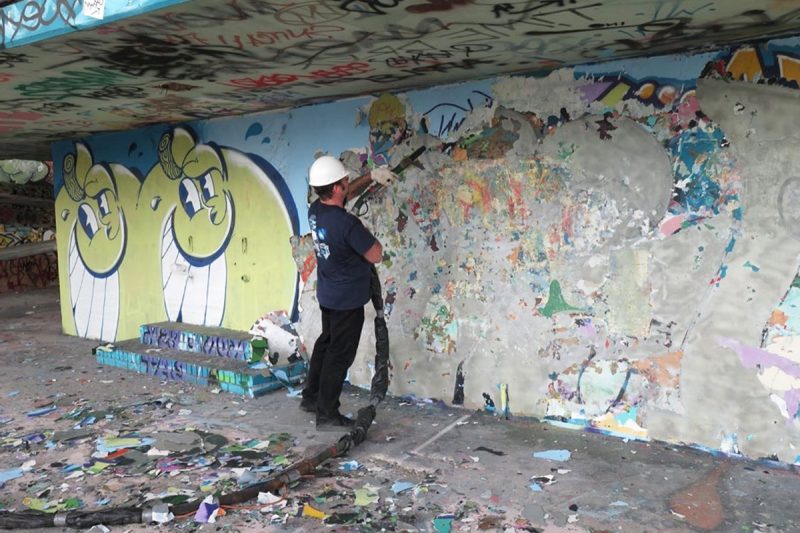
Substrate Damage Mechanismsg
During the pulsed laser cleaning process, substrates may be affected by various mechanisms, including thermal effects, mechanical effects, and photochemical effects. While pulsed laser cleaning technology offers high efficiency and environmental benefits, these effects can cause damage to the substrate under certain conditions. Below are the specific damage mechanisms:
Thermal Effects
- Melting: High-energy laser pulses may heat the substrate locally to temperatures exceeding the melting point, causing localized melting. This phenomenon is particularly common when cleaning metal surfaces or coatings. If the laser energy is too high, localized melting can occur.
- Thermal Stress: Rapid heating and cooling during the laser cleaning process can cause uneven thermal expansion, generating internal stresses in the material. These stresses may result in cracks or deformation, especially on heat-sensitive or thin-walled materials.
- Heat-Affected Zone (HAZ): The microstructure and mechanical properties of the substrate in the heat-affected zone (HAZ) may change. This change can reduce the substrate’s mechanical strength and lifespan, particularly in metals and alloys, where the HAZ can lead to a decrease in material performance.
Mechanical Effects
- Shockwaves: Plasma expansion induced by the laser generates shockwaves, which may cause mechanical damage to the substrate surface. This is particularly true for brittle or fine materials, where shockwaves can lead to surface cracks or material spalling.
- Vaporization Pressure: The rapid vaporization of contaminants generates high pressure, which can be transferred to the substrate surface, applying additional mechanical load. If the cleaning process is too fast or the energy too high, it may cause localized damage or deformation of the substrate.
Photochemical Effects
- Surface Chemical Changes: High-energy photons from the laser may interact with the substrate surface, causing chemical reactions that alter its surface properties. For example, some laser cleaning processes can trigger oxidation or other chemical reactions, changing the substrate’s surface structure and chemical composition.
- Contamination: Incomplete removal of contaminants during cleaning may lead to residual materials redepositing on the substrate surface, causing new contamination. This can negatively affect the substrate’s performance and may have long-term adverse effects on its use.
While pulsed laser cleaning offers a highly efficient method for surface contaminant removal, it is crucial to carefully control the laser parameters, such as pulse energy, duration, and repetition rate, to prevent the above-mentioned thermal, mechanical, and photochemical effects from damaging the substrate. Proper laser parameter configuration and precise control are essential for ensuring both the safety and efficiency of the cleaning process.
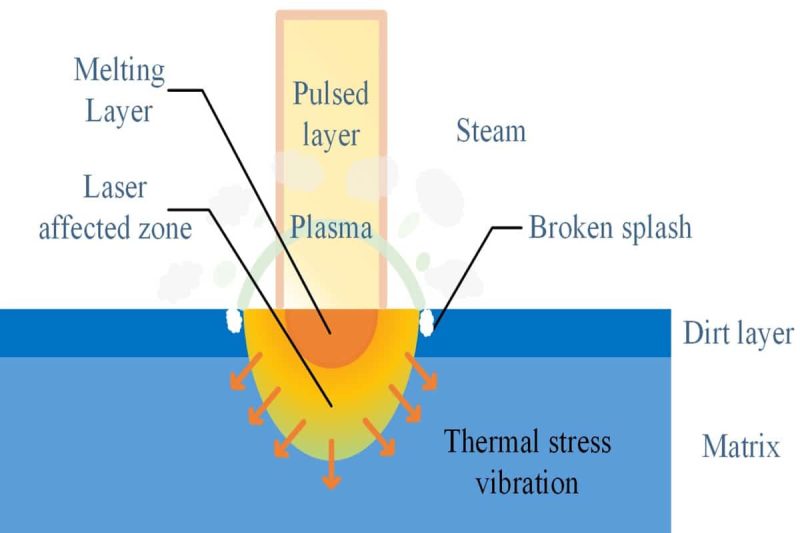
Factors Influencing Substrate Damage
During pulsed laser cleaning, various factors influence the degree of damage that may occur to the substrate. Understanding and optimizing these factors is crucial to ensure both effective contaminant removal and substrate protection. Below are the main influencing elements:
Material Properties
- Thermal Conductivity: Materials with high thermal conductivity can dissipate heat more efficiently, reducing the risk of thermal accumulation and damage. For example, metals like copper and aluminum are less prone to thermal degradation during laser cleaning due to their superior heat dissipation.
- Absorption Coefficient: The absorption coefficient determines how much laser energy a material can absorb at a specific wavelength. A higher absorption rate results in quicker surface heating, making precise control of laser wavelength and power essential for safe cleaning.
- Melting Point: Materials with lower melting points are more susceptible to melting under high-energy laser exposure. Choosing suitable cleaning parameters is essential when working with heat-sensitive substrates like plastics or low-melting-point alloys.
- Mechanical Strength: Higher mechanical strength helps a material resist damage from shockwaves or thermal stress. Stronger substrates are less likely to suffer from cracking or deformation during high-frequency pulsed laser cleaning.
- Chemical Composition: The chemical stability of the substrate influences its susceptibility to photochemical reactions. Some materials may undergo surface chemistry changes when exposed to high-energy photons, which could negatively impact their performance.
Laser Parameters
- Pulse Duration: The duration of each laser pulse directly affects how heat is transferred to the substrate. Ultra-short pulses (e.g., femtosecond lasers) can significantly minimize the heat-affected zone (HAZ), reducing the risk of thermal damage—especially in delicate or precision components.
- Pulse Energy: Proper adjustment of pulse energy is critical. Sufficient energy is needed to remove contaminants, but excessive energy may lead to substrate melting or ablation. Optimizing this parameter ensures efficient yet safe cleaning.
- Repetition Rate: A high repetition rate increases the risk of heat buildup. To avoid thermal accumulation and potential substrate damage, the frequency must be adjusted based on the material’s heat tolerance and conductivity.
- Wavelength: Selecting a laser wavelength that matches the absorption characteristics of both the contaminants and the substrate enhances cleaning efficiency and reduces damage. This is a key strategy in optimizing laser surface preparation.
Environmental Conditions
- Ambient Temperature: Elevated environmental temperatures can raise the substrate’s initial temperature, increasing the chance of overheating during the cleaning process. Temperature control may be necessary for sensitive applications.
- Humidity: High humidity may cause moisture to condense on the substrate surface, altering how the laser interacts with the material. This can result in additional thermal or chemical effects, potentially compromising cleaning performance.
- Surface Condition: The surface roughness and the type of contaminants present influence the outcome of the cleaning process. Irregular surfaces or layered contaminants can lead to uneven energy distribution, affecting both the cleaning efficiency and the substrate’s safety.
The success of pulsed laser cleaning and its impact on the substrate depend not only on the laser system itself but also on the material’s physical and chemical properties, environmental conditions, and surface status. To minimize substrate damage and maximize cleaning efficiency, it is essential to comprehensively evaluate these factors and adjust the laser parameters accordingly.
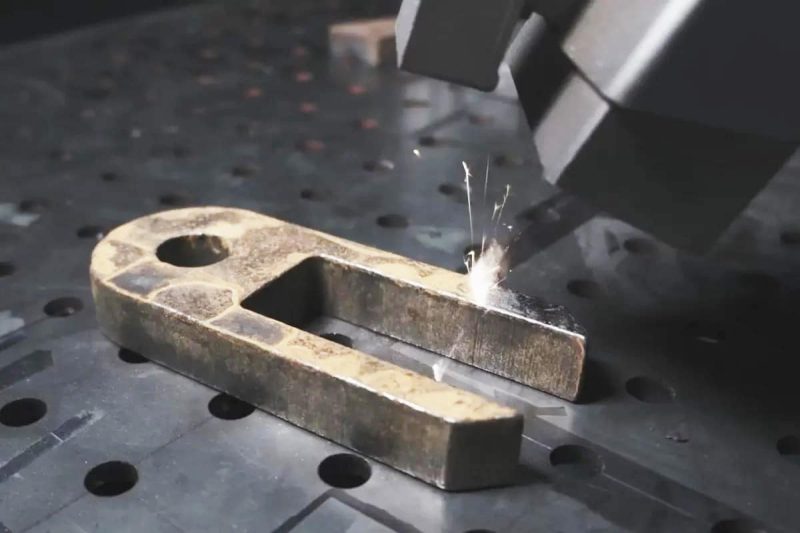
Strategies to Minimize Substrate Damage
While pulsed laser cleaning offers a precise, non-contact solution for removing contaminants, improper parameter settings can still lead to irreversible damage to the underlying substrate. To ensure effective cleaning while preserving material integrity, a combination of parameter optimization and advanced techniques should be applied.
Parameter Optimization
- Adjusting Pulse Duration: Utilizing ultrashort pulses, such as femtosecond lasers, significantly limits the thermal diffusion zone, effectively minimizing the size of the heat-affected zone (HAZ) and reducing thermal damage risks.
- Controlling Pulse Energy: Setting the pulse energy to the minimum required for contaminant removal prevents excessive heating or melting of the substrate surface, which is crucial for delicate materials.
- Managing Repetition Rate: A carefully selected repetition rate ensures adequate cooling time between pulses, helping to prevent heat accumulation that can lead to warping, microcracks, or other thermal-related substrate issues.
- Choosing the Right Wavelength: Matching the laser wavelength to the absorption characteristics of both the substrate and the contaminants enhances cleaning selectivity, improves efficiency, and minimizes substrate exposure.
Advanced Techniques
- Burst Mode Operation: By splitting a single pulse into a series of sub-pulses, burst mode reduces peak pulse intensity while maintaining total energy, thereby mitigating thermal and mechanical stress on the surface.
- Multipulse Overlapping: Removing contaminants in multiple passes using lower-energy pulses allows for gradual material ablation, significantly lowering the impact on the substrate.
- Beam Shaping: Advanced optics can distribute laser energy more uniformly across the target area, preventing localized overheating and ensuring consistent laser surface preparation results.
Monitoring and feedback
- Temperature monitoring: Temperature is a key factor affecting thermal damage. By arranging infrared thermal imagers or thermocouple sensors in the cleaning area, the changing trend of the substrate surface temperature can be grasped in real time. When the temperature is close to the melting point or the critical value of thermal stress, the system can immediately reduce the pulse energy or reduce the repetition rate to effectively prevent the material from melting, deforming, or thermal cracking. This feedback mechanism has greatly improved the safety and reliability of laser cleaning in the field of precision manufacturing.
- Acoustic monitoring: Acoustic monitoring technology, such as ultrasonic thickness measurement devices, can effectively track the thickness changes of the substrate during the cleaning process. By collecting data in real time, the system can determine whether excessive material removal has occurred, issue warnings in time, and adjust laser parameters. For example, Chinese patent CN112044874A proposes a real-time laser cleaning system combined with ultrasonic feedback to prevent structural damage caused by excessive cleaning.
- Optical feedback: Optical coherence tomography (OCT) provides high-resolution three-dimensional imaging capabilities for the cleaning area, which can accurately identify whether contaminants are completely removed and whether there is damage on the substrate surface. Compared with traditional visual systems, OCT has stronger penetration and accuracy and is particularly suitable for evaluating the cleaning effect of high-precision or multi-layer structure surfaces.
By integrating precise laser parameter control with advanced technologies, the risk of substrate damage during pulsed laser cleaning can be greatly reduced. These strategies are especially critical in applications where surface integrity is paramount, such as in aerospace, semiconductor fabrication, and cultural heritage restoration. Proper implementation not only enhances cleaning performance but also supports long-term material durability and safety.
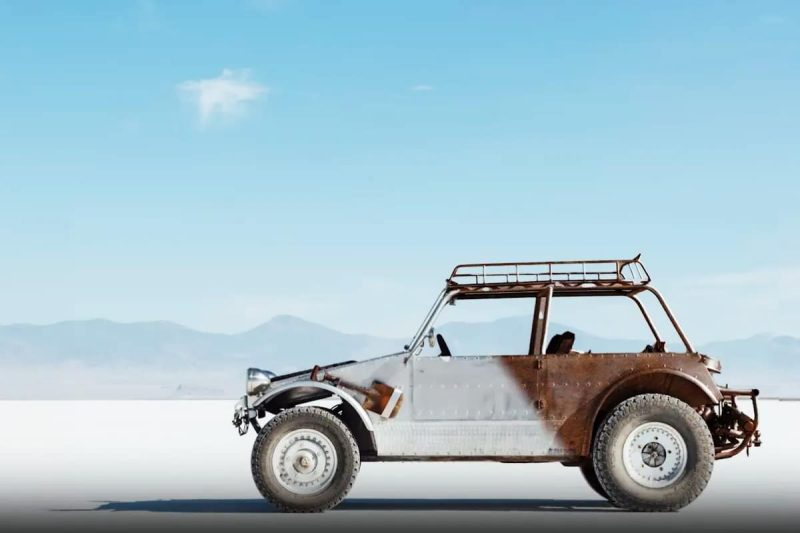
Case Studies and Applications
Pulsed laser cleaning, with its non-contact nature, high selectivity, and consumable-free operation, has been successfully applied across various high-end industries. These real-world applications demonstrate the technology’s reliability and industrial value in handling complex surface treatments.
Semiconductor Industry
In semiconductor manufacturing, even micron-sized particle contamination can degrade chip performance or cause production failures. Traditional cleaning methods may introduce static electricity or damage the wafer surface during particle removal. Pulsed laser cleaning—particularly with femtosecond laser pulses (e.g., 233 fs)—utilizes laser-induced micro shock waves to precisely remove contaminants from glass substrates with virtually no thermal impact at the microscopic level. This high-precision and low-damage cleaning method is gradually becoming a key process in advanced chip production lines.
Automotive Industry
In engine maintenance, turbine blade refurbishment, and hydraulic system servicing, efficient removal of rust and heavy contaminants is crucial. Pulsed laser cleaning provides strong energy coupling to contamination layers on metal surfaces, enabling precise stripping without affecting the dimensional accuracy or surface integrity of critical components. Its high repeatability and ease of automation make it an ideal choice for modern industrial production lines, effectively extending the service life of parts and improving equipment reliability.
Cultural Heritage Conservation
Cleaning historical artifacts and buildings requires extremely delicate treatment—removing contaminants thoroughly without damaging the original material. Ultrafast pulsed laser technology enables “gentle” cleaning of materials such as stone, metal, and ceramics. It is commonly used to remove biofilms, environmental grime, and corrosion products. Compared to chemical or mechanical cleaning, laser methods avoid secondary pollution and physical abrasion, and are widely used in museums, restoration labs, and heritage conservation projects around the world.
From precision electronics and heavy industry to cultural heritage preservation, pulsed laser cleaning has proven to be a highly efficient, safe, and controllable modern cleaning solution. As laser technology and intelligent control systems continue to evolve, the scope of its application will further expand—driving surface cleaning processes across industries to meet ever-higher standards.
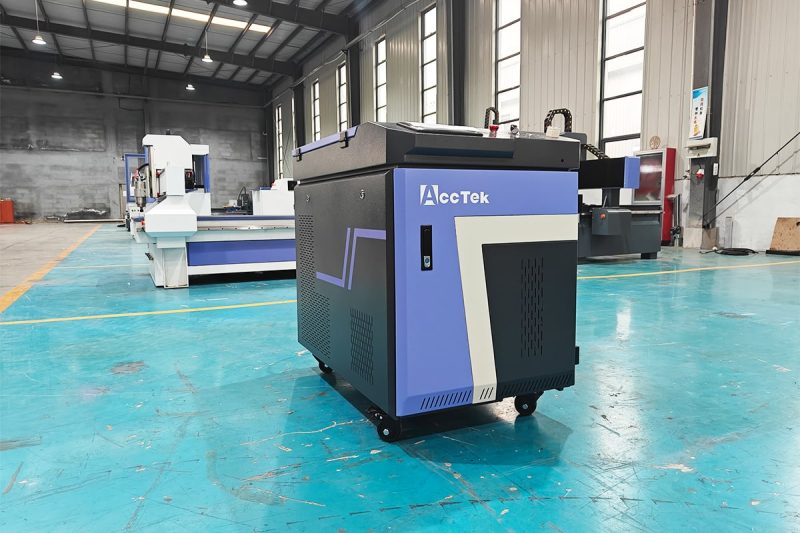
Challenges and Limitations
Despite the advantages of pulsed laser cleaning—such as non-contact operation, high precision, and environmental friendliness—the technology still faces several challenges in practical implementation and broader adoption across industries:
Cost: Laser cleaning systems usually involve high-performance laser generators, precision control units, and cooling systems, and their initial investment is relatively large. For small and medium-sized enterprises, the cost of acquisition and long-term maintenance may become the main obstacle to promotion. At the same time, some high-end systems such as femtosecond or picosecond laser generators have higher supporting equipment and maintenance costs, and the return on investment needs to be weighed.
Material Compatibility: Certain materials with high reflectivity (such as aluminum or copper) or transparency (such as glass or plastic) exhibit poor absorption of laser energy, reducing the effectiveness of the cleaning process or causing it to fail. Furthermore, the laser wavelength must be precisely matched to the optical absorption characteristics of the target material—an especially complex requirement when cleaning multi-material composite surfaces.
While cost and technical challenges remain, pulsed laser cleaning continues to establish itself as a reliable and advanced solution in high-end industrial applications. With ongoing developments in equipment miniaturization, cost reduction, and intelligent operation systems, these limitations are expected to diminish over time, paving the way for wider adoption in diverse industrial environments.
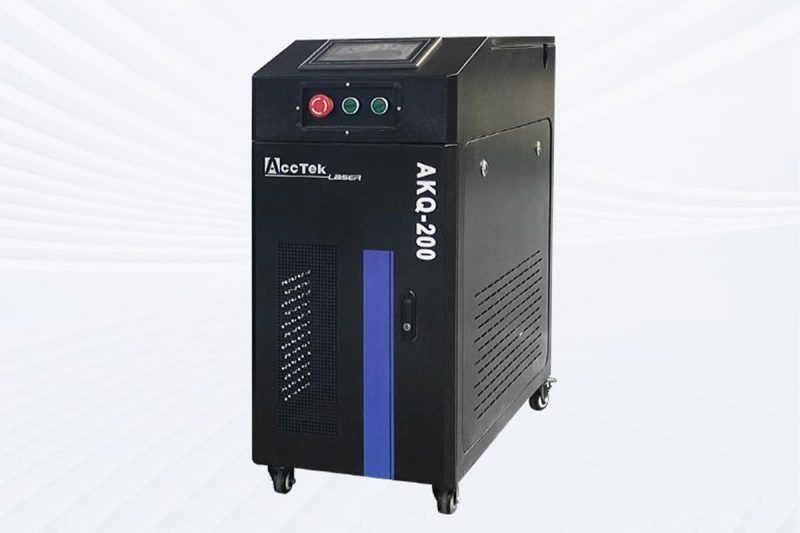
Summary
Pulsed laser cleaning technology, with its non-contact, high precision, and environmentally friendly advantages, has demonstrated broad application potential in modern industries. By precisely controlling laser parameters such as pulse duration, energy, and wavelength, and implementing advanced monitoring and feedback systems, this technology can effectively remove surface contaminants while minimizing damage to the substrate, ensuring both efficiency and safety during the cleaning process. Its successful applications in high-end fields such as semiconductors, automotive, aerospace, and cultural heritage preservation further validate its tremendous potential and technical reliability.
However, despite the positive results that pulsed laser cleaning technology has achieved in many industries, businesses still need to weigh factors such as cost, operational complexity, and material compatibility when considering its adoption. The initial investment in laser cleaning equipment is relatively high, and operators require professional technical training to ensure the system operates efficiently. Additionally, certain high-reflectivity or transparent materials may require special laser wavelengths and parameter settings. Therefore, businesses need to conduct a comprehensive evaluation in specific applications to ensure optimal cleaning results and minimal substrate damage.
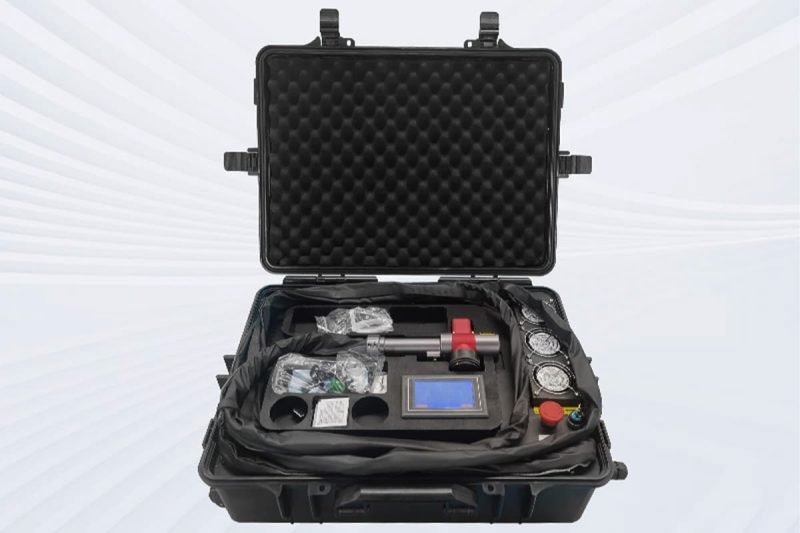
Obtaining Laser Solution
As a leading laser equipment manufacturer, AccTek Laser is committed to providing high-quality pulsed laser cleaning machines to help customers achieve efficient and safe cleaning results and meet various industrial cleaning needs. Whether it is for cleaning precision electronics, heavy industry or cultural heritage, we can provide customers with customized laser solutions to meet diverse cleaning challenges.
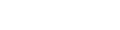
Contact information
- [email protected]
- [email protected]
- +86-19963414011
- No. 3 Zone A, Lunzhen Industrial Zone,Yucheng City , Shandong Province.
Get Laser Solutions