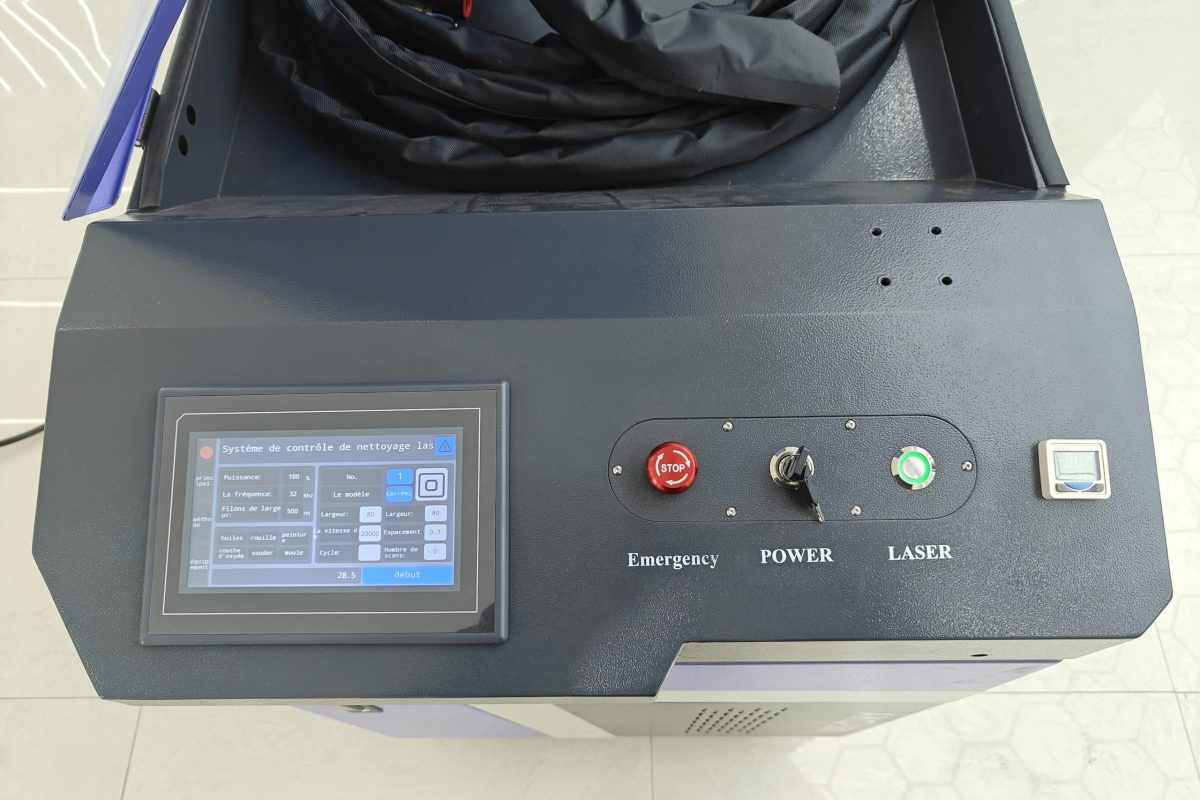
Wie richte ich eine Pulslaser-Reinigungsmaschine ein?
In den letzten Jahren hat die Pulslaserreinigungstechnologie breite Anwendung in der industriellen Oberflächenbehandlung, der Restaurierung kultureller Relikte, der Formenreinigung, der Bearbeitung elektronischer Bauteile und anderen Bereichen gefunden. Dank ihrer Vorteile wie hoher Effizienz, Umweltschutz, fehlendem Kontakt mit dem Substrat und dem Verzicht auf Verbrauchsmaterialien ersetzt sie zunehmend traditionelle Reinigungsmethoden. Die korrekte Einrichtung der Laserreinigungsmaschine ist entscheidend für die Reinigungswirkung und die Anlagenstabilität. Diese Anleitung erklärt systematisch den gesamten Einrichtungsprozess. Pulslaser-Reinigungsmaschine von der Grundvorbereitung bis zur erweiterten Konfiguration.
Inhaltsverzeichnis
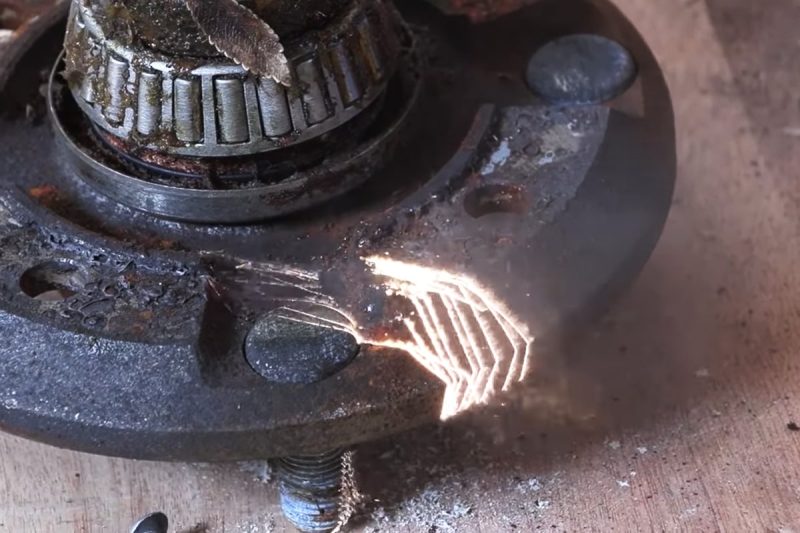
Erfahren Sie mehr über die Pulslaser-Reinigungsmaschine
Die Pulslaserreinigung ist eine berührungslose Reinigungstechnologie, die mit kurzpulsigen Hochenergielasern die kontaminierte Schicht verdampft, abträgt oder ablöst. Im Vergleich zu kontinuierlichen Lasern bietet der Pulslaser eine bessere Wärmeeinflusskontrolle und höhere Präzision. Er eignet sich für anspruchsvolle Anwendungen wie Laser-Rostentfernung, Entschichtung und Oxidschichtentfernung und ist besonders für die Reinigung hochwertiger Metalle und Präzisionsteile geeignet.
Erste Planung und Vorbereitung
Vor der Installation und Inbetriebnahme von Pulslaser-Reinigungsgeräten ist eine fundierte Vorplanung entscheidend für optimale Reinigungsergebnisse, verbesserte Arbeitseffizienz und längere Gerätelebensdauer. Erst nach umfassendem Verständnis der Reinigungsanforderungen, Materialarten und Verschmutzungseigenschaften kann das Lasersystem optimal konfiguriert werden, um die Leistung des Geräts zu maximieren. Im Folgenden werden die Kerninhalte der Vorplanung und Vorbereitung systematisch aus zwei Blickwinkeln vorgestellt.
Reinigungsbedarf ermitteln
Vor der offiziellen Installation sollten zunächst die spezifischen Reinigungsbedingungen geklärt und der entsprechende Prozessplan erstellt werden. Folgende Aspekte sollten berücksichtigt werden:
- Substrattyp: Verschiedene Materialien haben unterschiedliche Absorptionsraten für Laser, was sich direkt auf die Reinigungseffizienz und -sicherheit auswirkt. Zu den gängigen Materialien für die Laserreinigung gehören Kohlenstoffstahl, Edelstahl, Aluminiumlegierungen, Kupfer, Titan und einige nichtmetallische Materialien wie Stein und Polymerkunststoffe.
- Schadstoffart: Es ist notwendig, die Art der Schadstoffschicht auf der Oberfläche des Reinigungsobjekts zu identifizieren, z. B. Rost, Oxidschicht, Schweißspritzer, alte Farbschicht, Ölflecken, Harz oder Beschichtung. Verschiedene Schadstoffe reagieren unterschiedlich auf Laserenergie, daher müssen die Parameter gezielt eingestellt werden.
- Reinigungsziel: Es sollte klar sein, ob die Laserreinigungsaufgabe darin besteht, Oberflächenverunreinigungen vollständig zu entfernen oder lediglich die Oberfläche aufzurauen, um die Haftung für nachfolgendes Sprühen, Galvanisieren oder Schweißen zu verbessern. Unterschiedliche Ziele bestimmen den Wertebereich von Parametern wie Pulsenergie und Scangeschwindigkeit.
Eine genaue Bedarfsanalyse ist die Voraussetzung für die Entwicklung effizienter, sicherer und kostenkontrollierter Lösungen zur Laser-Rostentfernung oder Laser-Oberflächenbehandlung.
Die Wahl des richtigen Lasersystems
Nach der Klärung der Reinigungsanforderungen ist es notwendig, ein geeignetes Laserreinigungssystem entsprechend dem tatsächlichen Anwendungsszenario auszuwählen. Im Folgenden sind die wichtigsten Referenzparameter aufgeführt:
- Lasertyp: Laserreinigungsgeräte verwenden derzeit hauptsächlich gepulste Faserlasergeneratoren oder Nd:YAG-Lasergeneratoren. Gepulste Faserlasergeneratoren haben sich aufgrund ihrer geringen Größe, hohen Stabilität, des Verzichts auf Verbrauchsmaterial und der geringen Wartungskosten als gängige Wahl etabliert.
- Wellenlängenauswahl: Die Laserwellenlänge beeinflusst die Absorptionseigenschaften des Materials. In der Industrie wird üblicherweise die Nahinfrarotwellenlänge von 1064 nm verwendet, die sich aufgrund ihrer hohen Energiedichte und Materialanpassungsfähigkeit besonders zur Reinigung von Schadstoffen auf Metalloberflächen eignet.
- Pulsenergie und -frequenz: Die Spitzenleistung und Frequenz des gepulsten Lasers bestimmen die Energiedichte eines einzelnen Pulses. Sie sollte entsprechend der Dicke der Kontaminationsschicht, der Reinigungsgeschwindigkeit und der Hitzebeständigkeit des Substrats konfiguriert werden, um thermische Schäden am Substrat zu vermeiden.
- Leistungsbereich: Wählen Sie Lasergeneratoren unterschiedlicher Leistung entsprechend der Intensität der Reinigungsaufgabe. Der Leistungsbereich gängiger Laserreinigungsmaschinen beträgt 100 W bis 2000. Bei starker Verschmutzung oder Reinigungsbedarf für große Flächen können Geräte mit höherer Leistung (z. B. 500 W oder mehr) ausgewählt werden, um die Effizienz zu verbessern.
Eine sinnvolle Auswahl beeinflusst nicht nur die Reinigungseffizienz, sondern steht auch in direktem Zusammenhang mit der Lebensdauer des Geräts und seiner langfristigen stabilen Betriebsfähigkeit. Sie ist der zentrale Schritt zur Sicherstellung der Qualität der Laserreinigung.
Frühzeitige Planung und Vorbereitung sind nicht nur Voraussetzung für den erfolgreichen Einsatz von Laserreinigungssystemen, sondern stehen auch in direktem Zusammenhang mit der Betriebsstabilität der Anlage, der Kontrollierbarkeit der Reinigungsqualität und der Sicherheit der Bediener. Durch die wissenschaftliche Bewertung des Reinigungsbedarfs und die Auswahl geeigneter Lasergeneratorkonfigurationen und Parameterkombinationen können Anwender das Potenzial der gepulsten Laserreinigungstechnologie voll ausschöpfen, die Produktionseffizienz steigern und eine wirklich umweltfreundliche Reinigung sowie intelligente Fertigung erreichen.
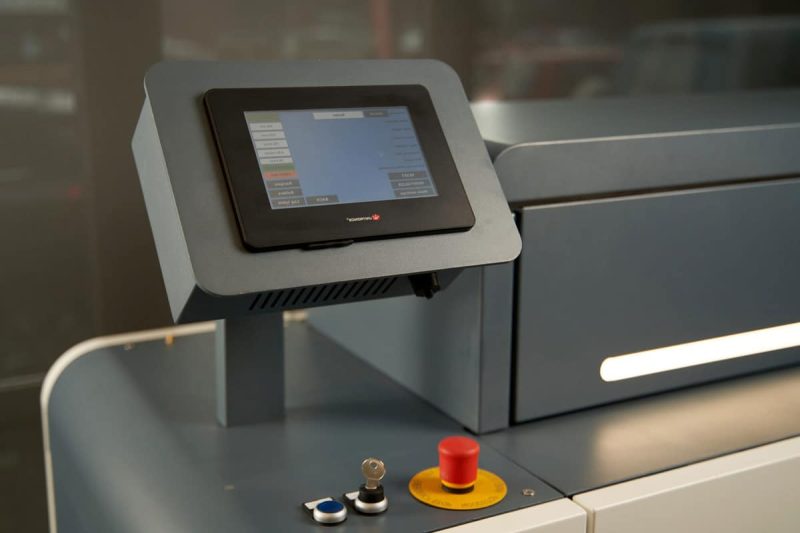
Einrichten der Laserreinigungsmaschine
Nach Abschluss der Reinigungsbedarfsermittlung und der Geräteauswahl besteht der nächste Schritt in der Installation und Fehlerbehebung des Laserreinigungssystems vor Ort. Dieser Arbeitsschritt bestimmt nicht nur den reibungslosen Betrieb der Anlage, sondern wirkt sich auch direkt auf die nachfolgende Reinigungseffizienz und -sicherheit aus. Eine wissenschaftlich fundierte und standardisierte Installation und Kalibrierung trägt dazu bei, dass die Laser-Rostentfernungsanlage ihre optimale Reinigungsleistung und Systemstabilität erreicht.
Maschineninstallation
Bei der Installation von Laserreinigungsgeräten müssen die Anpassungsfähigkeit und Sicherheit der Betriebsumgebung umfassend berücksichtigt werden:
- Standortvorbereitung: Wählen Sie als Installationsort für die Geräte eine saubere, trockene und gut belüftete Industrieanlage und lassen Sie ausreichend Platz für das Gerätegehäuse, das Steuerungssystem und den Betriebskanal, um Überhitzung, Staubansammlungen und andere Faktoren zu vermeiden, die den stabilen Betrieb des Laserreinigungssystems beeinträchtigen.
- Stromversorgungskonfiguration: Je nach Leistungsbedarf von Lasergenerator, Schaltschrank und Kühler sollte eine passende Industriestromversorgung (in der Regel 220 V oder 380 V) konfiguriert werden. Die Spannung sollte stabil sein, um Gerätestörungen durch Spannungsschwankungen zu vermeiden. Es wird empfohlen, einen Spannungsstabilisator und einen speziellen Erdungsschutz einzusetzen.
- Installation des Kühlsystems: Hochleistungs-Impulslasergeneratoren erzeugen im Dauerbetrieb viel Wärme. Daher muss ein effizienter Industriekühler installiert werden, um die Temperatur des Lasergenerators in einem sicheren Bereich zu halten und die Lebensdauer des Lasermoduls zu verlängern.
- Belüftungs- und Rauchabzugssystem: Bei der Laserreinigung entstehen Rauch, Gerüche und winzige Partikel. Daher ist ein professionelles Rauchreinigungssystem oder eine industrielle Rauchabzugsanlage erforderlich. Eine gute Rauchabzugswirkung verbessert nicht nur das Arbeitsumfeld, sondern erfüllt auch die Umweltschutzvorschriften.
Ausrichtung und Kalibrierung
Nach Abschluss der grundlegenden Hardwareinstallation muss das Lasersystem präzise kalibriert werden, um konsistente und sichere Reinigungsergebnisse zu gewährleisten:
- Laserstrahlausrichtung: Verwenden Sie ein Positionierungsgerät oder eine Referenzschablone, um den Laserstrahl genau auf die Oberfläche des zu reinigenden Werkstücks auszurichten, die Punktposition und den Winkel stabil zu halten und Versätze zu vermeiden, die zu unebenen Reinigungsbereichen oder Schäden am Substrat führen.
- Kalibrierung der Laserparameter: Passen Sie wichtige Parameter wie Laserleistung, Pulsfrequenz, Scangeschwindigkeit und Pulsbreite entsprechend den Materialeigenschaften und Verschmutzungsmerkmalen an, um sie an unterschiedliche Reinigungsaufgabenanforderungen anzupassen, die Effizienz zu verbessern und eine Überhitzung zu vermeiden.
- Testlauf: Es wird empfohlen, vor der Chargenreinigung Proben zu testen. Durch Beobachtung der Reinigungswirkung, Oberflächenveränderungen und wärmebeeinflusster Bereiche können die Parameter weiter optimiert werden, um sicherzustellen, dass der Pulslaser-Reinigungsprozess stabil und kontrollierbar ist.
Durch die wissenschaftliche und standardisierte Installation und Inbetriebnahme von Laserreinigungsanlagen lässt sich nicht nur die Gesamtbetriebseffizienz der Anlage verbessern, sondern auch deren Lebensdauer deutlich verlängern und die Wartungshäufigkeit reduzieren. Insbesondere in industriellen Szenarien der Massenproduktion oder im Langzeitbetrieb ist eine gute Anfangseinstellung ein entscheidender Schritt, um die Qualität und Stabilität der Laserreinigung zu gewährleisten.
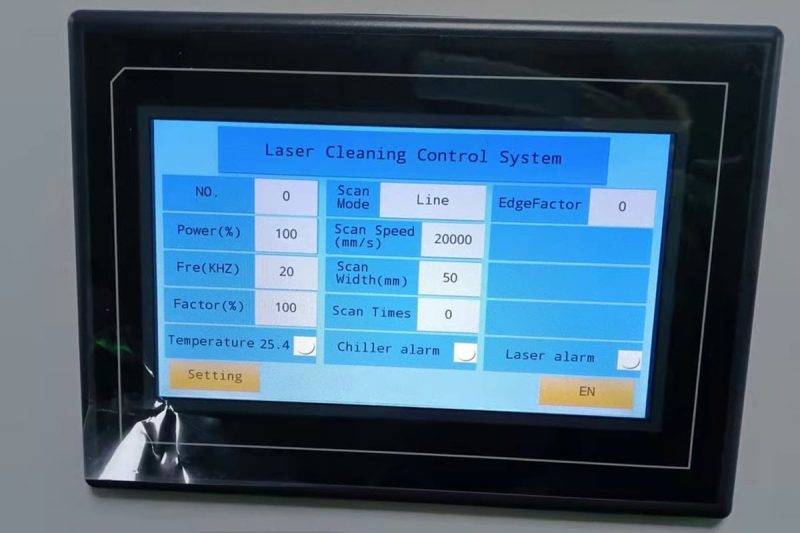
Optimierung der Laserparameter
Nach der Installation und grundlegenden Fehlerbehebung des Laserreinigungssystems ist es entscheidend, die Laserprozessparameter weiter zu optimieren. Eine sinnvolle Einstellung verschiedener Laserparameter verbessert nicht nur die Effizienz der Schadstoffentfernung, sondern schützt auch die Substratoberfläche optimal, um thermische Schäden und Überbearbeitung zu vermeiden. Insbesondere in industriellen Umgebungen mit unterschiedlichen Materialien und komplexen Verschmutzungsarten ist die Parameterkontrolle entscheidend für die Anpassungsfähigkeit und Stabilität des Laserreinigungssystems. Für eine optimale Reinigungswirkung empfiehlt es sich, sich auf die folgenden Kernparameter zu konzentrieren:
Impulsdauer
Die Pulsdauer beeinflusst direkt die Einwirkzeit von Laser und Material und ist ein wichtiger Faktor für die Reinigungsgenauigkeit und den Wärmediffusionsbereich. Kürzere Pulse (z. B. Nanosekunden und Pikosekunden) ermöglichen den „Kaltbearbeitungseffekt“, der sich für die Oberflächenbehandlung mit hohen Präzisionsanforderungen eignet und die Wärmeeinflusszone des Substrats reduziert. Längere Pulse eignen sich dagegen ideal für die effiziente Entfernung dicker und schwerer Verunreinigungen.
Pulsenergie
Je höher die Pulsenergie, desto stärker ist die Ablösefähigkeit durch die Laserwirkung, wodurch die Bindungskraft zwischen der Kontaminationsschicht und dem Substrat effektiv zerstört werden kann. Die Energie muss jedoch in einem sicheren Bereich gehalten werden, um ein Schmelzen oder Abtragen des Substrats zu vermeiden. In der Regel muss die Energie schrittweise an die Dicke der Kontamination, die Haftfestigkeit und die thermische Empfindlichkeit des Substrats angepasst werden.
Wiederholungsrate
Die Laserwiederholfrequenz bestimmt die Anzahl der Laserpulse pro Zeiteinheit und steuert dadurch die Reinigungseffizienz und den Wärmestau. Eine höhere Wiederholfrequenz kann die Bearbeitung beschleunigen, eine nicht optimal abgestimmte Pulsenergie kann jedoch zu Problemen wie übermäßigem Wärmestau und Oberflächenverfärbungen führen. Das ausgewogene Verhältnis von Frequenz und Energie ist der Schlüssel zu einer effizienten und stabilen Reinigung.
Strahlprofil und Fokuspunkt
Strahlform und Fokusposition des Lasers beeinflussen direkt die Energiedichte pro Flächeneinheit. Eine gute Fokussteuerung kann die Energie auf die Schmutzschicht konzentrieren und so die Reinigungswirkung verbessern. Üblicherweise wird ein Gauß-Strahl oder ein Top-Hat-Spot-Design mit gleichmäßiger Energieverteilung verwendet, kombiniert mit einer Autofokusfunktion, um eine höhere Konsistenz und Sauberkeit zu erreichen.
Generell hängt die Leistung des Laserreinigungssystems nicht nur von der Hardwarekonfiguration des Geräts selbst ab, sondern auch von der Professionalität des Parameter-Debuggings und der Prozessoptimierung. Durch die gezielte Einstellung von Kernparametern wie Pulsbreite, Energie, Frequenz und Punktsteuerung kann die Reinigungseffizienz deutlich verbessert, die Materialschadensrate reduziert und komplexere Reinigungsszenarien angepasst werden.
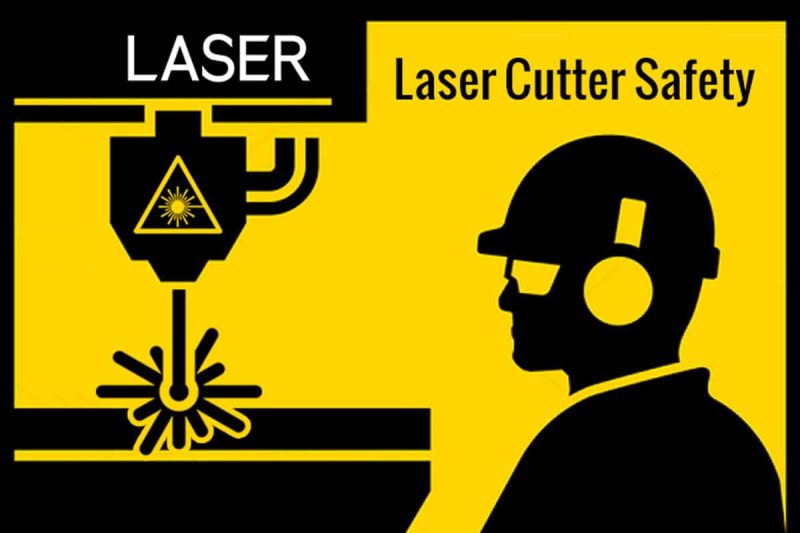
Sicherheitsprotokoll
Beim Einsatz von Laserreinigungsanlagen ist die Sicherheit der Betriebsumgebung und des Personals eine Grundvoraussetzung für einen stabilen Anlagenbetrieb und die Einhaltung der Produktionsvorschriften. Da der Lasergenerator selbst über eine hohe Energie und hohe Fokussierungseigenschaften verfügt und während des Reinigungsvorgangs schädlicher Rauch und Partikel entstehen können, birgt ein fehlender umfassender Schutzmechanismus potenzielle Risiken für die Gesundheit der Bediener und die Umgebung. Daher müssen Unternehmen beim Einsatz von Laserreinigungssystemen gleichzeitig umfassende, systematische Sicherheitsprotokolle implementieren.
Laser-Sicherheitsmaßnahmen
Um zu verhindern, dass Laserstrahlung dem menschlichen Körper schadet, werden folgende Laserschutzstrategien empfohlen:
- Tragen Sie eine Laserschutzbrille: Die Bediener müssen eine Schutzbrille tragen, die den Anforderungen der Laserwellenlänge entspricht, z. B. eine Schutzbrille der OD-Klasse für eine Wellenlänge von 1064 nm, um sicherzustellen, dass die Augen nicht durch direktes oder reflektiertes Laserlicht geschädigt werden.
- Sicherheitsverriegelung konfigurieren: Konfigurieren Sie ein Verriegelungssystem für den Lasergenerator und den Arbeitsbereich. Wenn eine Schutztür nicht geschlossen ist oder eine unzulässige Person den Bereich betritt, sollte das System die Laserleistung automatisch unterbrechen, um Fehlbedienungen und versehentliches Auslösen zu verhindern.
- Bringen Sie Warnschilder an: Hängen Sie auffällige Schilder wie „Laser-Einsatzbereich“ und „Schutzbrille tragen“ an gut sichtbaren Stellen im Arbeitsbereich auf, um alle Mitarbeiter, die den Bereich betreten, daran zu erinnern, auf die Schutzmaßnahmen zu achten.
Rauch- und Partikelkontrolle
Während der Laserreinigung werden Schadstoffe verdampft und Feinstaub sowie Rauch freigesetzt. Werden diese nicht rechtzeitig entfernt, können die Atemwege des Bedieners und die Gerätestruktur beschädigt werden:
- Installieren Sie einen Rauchabzug: Filtern Sie PM2,5-Partikel, Ölnebel, organische Gase usw. effizient heraus, um sicherzustellen, dass die Luftreinheit den industriellen Sicherheitsstandards entspricht.
- Stellen Sie sicher, dass das Belüftungssystem frei ist: Insbesondere bei Arbeiten in geschlossenen oder engen Räumen sollten industrielle Abluftventilatoren oder Unterdruckbelüftungsgeräte so ausgestattet sein, dass ein guter Luftstrom und gute Abluftwege gewährleistet sind, um zu verhindern, dass sich Schadstoffe auf der Oberfläche des Geräts ablagern oder in den Arbeitsbereich zurückfließen.
Aus-und Weiterbildung
Auch wenn die Hardware-Schutzmaßnahmen perfekt sind, ist die Standardisierung der Personalbedienung eine wichtige Garantie für einen sicheren Betrieb. Daher sollte ein regelmäßiges Schulungssystem etabliert werden:
- Schulung zur Lasersicherheit: einschließlich der Grundsätze zu Lasergefahren, Notfallmaßnahmen, Verwendung persönlicher Schutzausrüstung usw., um das Sicherheitsbewusstsein der Mitarbeiter zu stärken.
- Schulung zur Bedienung: Stellen Sie sicher, dass die Bediener die grundlegenden Fähigkeiten zum korrekten Starten, Herunterfahren, Anpassen der Parameter, zur Fehlerbehebung usw. der Laserreinigungsmaschine beherrschen.
- Wartungsschulung: Schulen Sie die entsprechenden Techniker im täglichen Wartungsablauf der Geräte, einschließlich der Inspektion des optischen Pfads, des Austauschs von Filterelementen, der Wartung des Kühlsystems usw., um einen langfristig stabilen Betrieb der Geräte sicherzustellen.
Insgesamt bietet die Laserreinigungstechnologie zwar hohe Effizienz und Vorteile im Umweltschutz, stellt aber auch höhere Anforderungen an die Sicherheit im Einsatz. Unternehmen sollten die Sicherheitsvereinbarung als Kernbestandteil des Projektstarts betrachten und ein Sicherheitssystem aufbauen, das den Branchenstandards entspricht – von der Risikobewertung der Quelle über die Geräteauswahl bis hin zur Personalschulung und zum Umweltschutz.
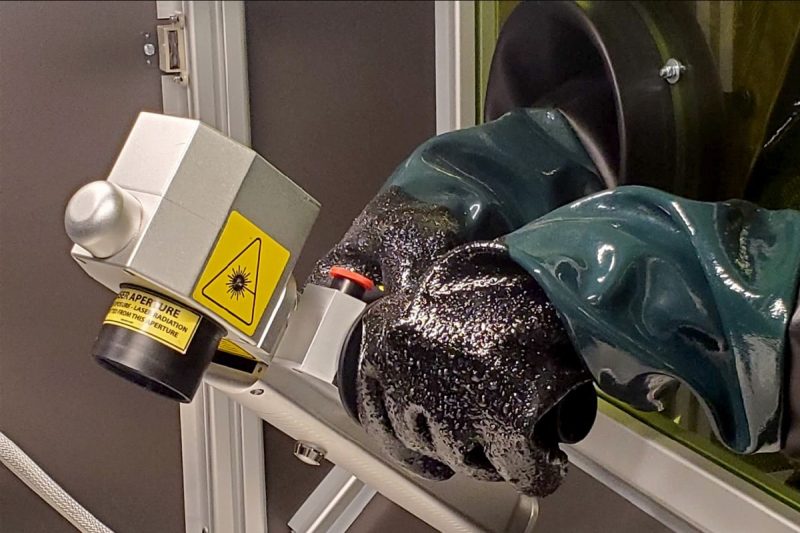
Regelmäßige Wartung und Fehlerbehebung
Um einen kontinuierlichen, effizienten und stabilen Betrieb der Laserreinigungsmaschine zu gewährleisten, muss das Unternehmen einen systematischen täglichen Wartungsmechanismus und Fehlerbehebungsprozess etablieren. Obwohl es sich bei dem Lasersystem um ein berührungsloses Bearbeitungsgerät handelt, werden seine Kernkomponenten wie Lasergenerator, optisches System und Kühlsystem im Langzeitbetrieb zwangsläufig von verschiedenen Faktoren wie Umgebung und Belastung beeinflusst. Werden sie nicht regelmäßig gewartet, wirkt sich dies direkt auf die Reinigungswirkung, die Laserleistung und sogar die Lebensdauer des Geräts aus.
Routinemäßige Wartungsarbeiten
Es wird empfohlen, dass Benutzer Wartungspläne für unterschiedliche Zeiträume, z. B. wöchentlich, monatlich und vierteljährlich, entsprechend der Häufigkeit der Gerätenutzung entwickeln und sich auf die Überprüfung der folgenden Punkte konzentrieren:
- Reinigung des Laserkopfes und der optischen Linse: Wischen Sie die Schutzlinse und die Fokussierlinse regelmäßig mit staubfreien Wattestäbchen und einer speziellen Linsenreinigungsflüssigkeit ab, um Laserdivergenz, Leistungsreduzierung oder Spiegelablation durch Staub und Öl zu verhindern.
- Überprüfen Sie den Zustand des Kühlsystems: Überprüfen Sie täglich, ob die Kühlleistung des Industriekühlers normal ist, ob der Wasserkanal frei ist und ob die Wassertemperatur im empfohlenen Bereich des Lasergenerators liegt. Wechseln Sie regelmäßig reines Kühlwasser und reinigen Sie den Wassertankfilter, um Kalkablagerungen und eine verringerte Wärmeleitfähigkeit zu vermeiden.
- Ersetzen Sie Verbrauchsmaterialien: Ersetzen Sie regelmäßig alte Laserlichtwellenleiter, Netzkabel, Staubschutzkappen, Schutzlinsen usw. Achten Sie insbesondere bei Geräten unter hoher Belastung oder im Dauerbetrieb besonders auf die Lebensdauer der Verbrauchsmaterialien.
Allgemeine Fehlerbehebung
Wenn die Laserreinigungsanlage nicht normal läuft, sollte eine systematische Untersuchung basierend auf dem Phänomen durchgeführt werden, um eine schnelle Wiederherstellung sicherzustellen:
- Schwankungen der Laserleistung: Häufig verursacht durch schlechte Wärmeableitung des Lasergenerators, instabile Versorgungsspannung oder verunreinigten optischen Pfad. Überprüfen Sie die Wassertemperatur des Kühlsystems, die Festigkeit der Stromversorgungsverkabelung und ob der optische Pfad blockiert oder die Linse verunreinigt ist.
- Strahlabweichung oder anormale Reinigungsbahn: In der Regel verursacht durch lose optische Linsen, schiefe Installation oder Abweichungen in der internen Struktur des Laserkopfes. Es wird empfohlen, die Linse erneut zu fixieren und den optischen Pfad neu zu kalibrieren oder gegebenenfalls die Fokussierungskomponente auszutauschen.
- Eine abnormale Rauchfilterung oder ein schwacher Abzug können durch eine Filterverstopfung oder einen Lüfterschaden verursacht werden. Überprüfen Sie rechtzeitig die Sättigung des Rauchreinigerfilters, ersetzen Sie gegebenenfalls den Hochleistungsfilter und stellen Sie sicher, dass der Abluftkanal nicht verstopft ist und der Lüfter normal funktioniert.
Durch regelmäßige Wartung und standardisierte Fehlerbehebungsprozesse können Benutzer nicht nur die Ausfallrate der Geräte erheblich senken und die Lebensdauer der gesamten Maschine verlängern, sondern auch die Kontinuität und Konsistenz der Reinigungsvorgänge sicherstellen, das Risiko von Produktionsunterbrechungen verringern und die Gesamtproduktionskapazität verbessern.
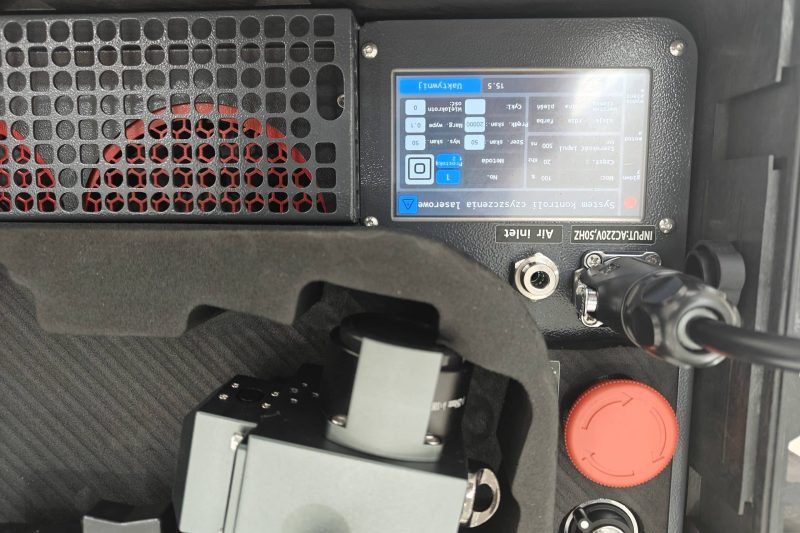
Hinweise zu erweiterten Einstellungen
Mit der Entwicklung intelligenter Fertigung und industrieller Automatisierung beschränkt sich der Einsatz von Laserreinigungsanlagen nicht mehr auf manuelle Bedienung oder einfache Reinigungsszenarien, sondern wird zunehmend automatisiert, intelligent und nachverfolgbar. Insbesondere in anspruchsvollen Fertigungsbereichen wie dem Automobilbau, dem Präzisionsformenbau, der Luft- und Raumfahrt usw. sind die erweiterten Konfigurationsmöglichkeiten und die automatisierte Integrationsleistung von Laserreinigungssystemen entscheidend für die Effizienzsteigerung von Produktionslinien, die Senkung der Arbeitskosten und die Gewährleistung einer konsistenten Reinigung.
Schnittstelle zu Automatisierungssystemen
Moderne Laserreinigungsanlagen unterstützen in der Regel die Integration in eine Vielzahl industrieller Automatisierungsplattformen, z. B. die Anbindung an Robotersysteme, SPS-Steuerungen, visuelle Positionierungssysteme usw. über Kommunikationsschnittstellen (EtherCAT, Profinet, Modbus usw.). Sie ermöglichen:
- Robotergestützte Laserreinigung: Der Roboterarm sorgt für präzise Bewegungen des Reinigungskopfes und ermöglicht so die automatisierte Reinigung großer Mengen komplexer gekrümmter Oberflächen.
- Bahnsteuerung und Scankopf-Anbindung: Mit einer mehrachsigen Anbindungsplattform oder einer automatischen Gleitschiene wird der Laser-Scanpfad gesteuert, um eine effiziente und kontinuierliche Reinigung großer Werkstücke zu erreichen.
- Fernauslösung und Sicherheitsverriegelungsmechanismus: Gewährleisten Sie die Betriebssicherheit und Gerätestabilität und unterstützen Sie automatische Überflutungs- und Abschaltmechanismen.
Datenerfassung und -analyse
Hochwertige Laserreinigungssysteme sind in der Regel mit Datenaufzeichnungsmodulen in Industriequalität ausgestattet, um die Kernparameter jedes Reinigungsvorgangs wie Leistung, Frequenz, Impulsbreite, Flugzeit usw. aufzuzeichnen und so eine spätere Analyse und Qualitätsrückverfolgbarkeit zu erleichtern:
- Archivierung der Reinigungsparameter: Die Reinigungsdaten jeder Werkstückcharge werden automatisch gespeichert und der Reinigungsstatus ist jederzeit nachvollziehbar.
- Qualitätsanalyse: In Kombination mit der Erkennung von Reinigungseffekten (z. B. Bilderkennung oder Sensorfeedback) wird eine Datenbank für verschiedene Materialien und Parameterkombinationen erstellt, die die Prozessoptimierung unterstützt.
- Ferndiagnose und Systemaktualisierung: Über die Cloud-Plattform oder den Industrieserver werden Fernsoftwareaktualisierungen und Fehlerdiagnosen unterstützt, um die Reaktionseffizienz nach dem Verkauf zu verbessern.
Maßgeschneiderte Lösungen
Um den speziellen Reinigungsanforderungen der Kunden gerecht zu werden, kann das Laserreinigungssystem flexibel mit exklusiven Vorrichtungssystemen, Drehplattformen, Rollenbahnlinien, automatischen Be- und Entladesystemen usw. angepasst werden:
- Spezielles Vorrichtungsdesign: Verbessert die Befestigungseffizienz und stellt sicher, dass der Laserstrahl den Reinigungsbereich stabil abdeckt.
- Automatisierte Stapelverarbeitung, wie z. B. das Andocken an automatische Montagelinien, um einen kontinuierlichen Betrieb mehrerer Stationen in industriellen Szenarien zu erreichen;
- Flexible Prozessanpassung: Das System unterstützt Multitasking-Prozessparameter-Voreinstellungen, die einen schnellen Wechsel zwischen verschiedenen Reinigungsaufgaben ermöglichen.
Dank erweiterter Einstellungen und automatisierter Integration ist die Laserreinigungsanlage kein isoliertes Einzelwerkzeug mehr, sondern ein wichtiger Bestandteil intelligenter Produktionslinien. Sie verbessert nicht nur den Produktionsrhythmus und die Reinigungskonsistenz, sondern unterstützt Unternehmen auch beim Aufbau eines nachhaltigen, hochflexiblen und hochwertigen intelligenten Fertigungssystems.
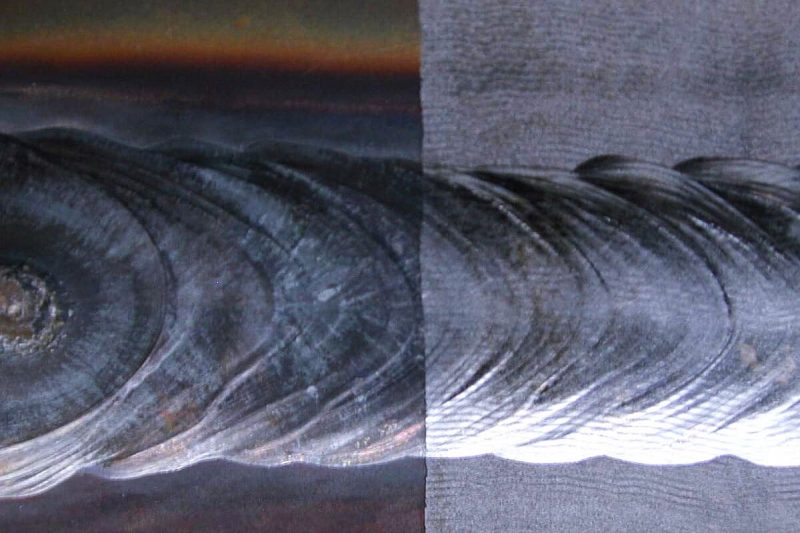
Zusammenfassen
Die herausragende Leistung einer Pulslaser-Reinigungsmaschine mit hervorragender Leistung und stabilem Betrieb hängt nicht nur vom hochwertigen Lasergeneratorgehäuse ab, sondern auch von der wissenschaftlichen Planung und sinnvollen Konfiguration des gesamten Systems von der Einstellung bis zur Anwendung. Ob bei der komplexen Metallrostreinigung, der Oxidschichtentfernung oder der hochpräzisen Formoberflächenbehandlung – um effiziente, sichere und kontrollierbare Reinigungseffekte zu erzielen, ist die strikte Ausführung aller Prozessschritte erforderlich:
Von der frühzeitigen Beurteilung der Reinigungsbedingungen (einschließlich Materialtyp, Schadstoffeigenschaften und Reinigungsziel) über die Auswahl des geeigneten Lasergeneratortyps und der Leistungsparameter, die Anpassung des passenden Kühlsystems und der Abgasreinigungsanlage bis hin zur späteren Laserstrahlausrichtung, Parameter-Debugging, Systemkalibrierung und Sicherheitsvorkehrungen usw. wirkt sich jeder Schritt direkt auf die Arbeitseffizienz, Reinigungsgenauigkeit und Lebensdauer der Anlage aus. Ein wissenschaftlich fundierter Einstellungsprozess kann nicht nur die Reinigungskonsistenz verbessern, sondern auch die Betriebskosten und die Wartungshäufigkeit deutlich senken, was der Schlüssel zu einem langfristigen und effizienten Betrieb des Unternehmens ist.
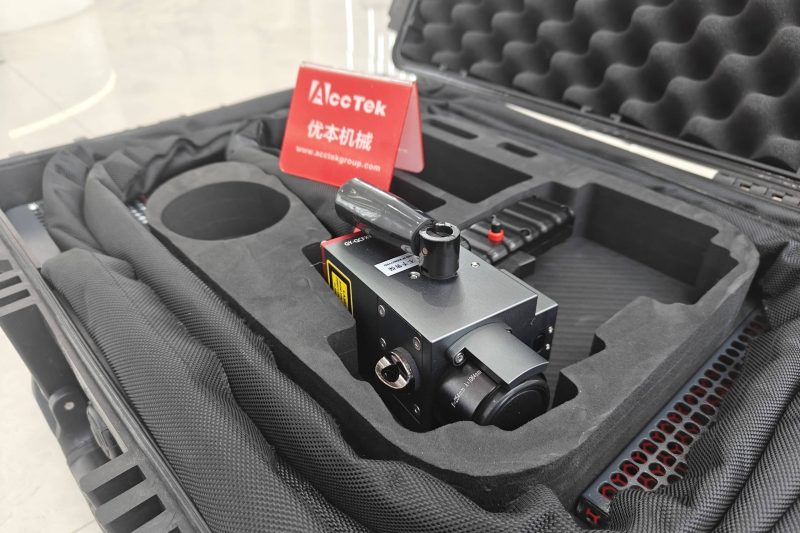
Holen Sie sich Laserlösungen
Wenn Sie nach einer wirklich leistungsstarken, intelligenten und anpassungsfähigen Lösung zur Laser-Oberflächenbehandlung suchen, AccTek-Laser ist die ideale Wahl für Sie. Wir bieten unseren Kunden weltweit gepulste Laserreinigungssysteme für verschiedenste Branchen und Anwendungsbereiche. Die Geräte decken verschiedene Leistungsstufen von 50 W bis 500 W ab und eignen sich für alle Anwendungen, von der leichten Fleckenreinigung bis zur Entfernung von starkem Rost. Darüber hinaus bieten wir maßgeschneiderte Komplettservices und können exklusive Vorrichtungen, Automatisierungssysteme und Bedienoberflächen flexibel an Ihre Werkstückform, Ihre Reinigungsanforderungen und Ihre Produktionsumgebung anpassen.
Darüber hinaus verfügen wir über ein erfahrenes technisches Team, das Kunden vor dem Verkauf individuelle Zustandsbewertungen, Ferninstallationsanleitungen, Bedienerschulungen und kontinuierlichen technischen Support bietet, um sicherzustellen, dass Sie die Geräte in jeder Phase reibungslos, effizient und sorgenfrei nutzen können. Wenn Sie sich für uns entscheiden, entscheiden Sie sich für Professionalität, Effizienz und langfristigen Wert. Willkommen bei kontaktiere uns für kostenlose Testlösungen oder individuelle Beratung.
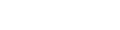
Kontaktinformationen
- [email protected]
- [email protected]
- +86-19963414011
- Nr. 3 Zone A, Industriegebiet Lunzhen, Stadt Yucheng, Provinz Shandong.
Holen Sie sich Laserlösungen