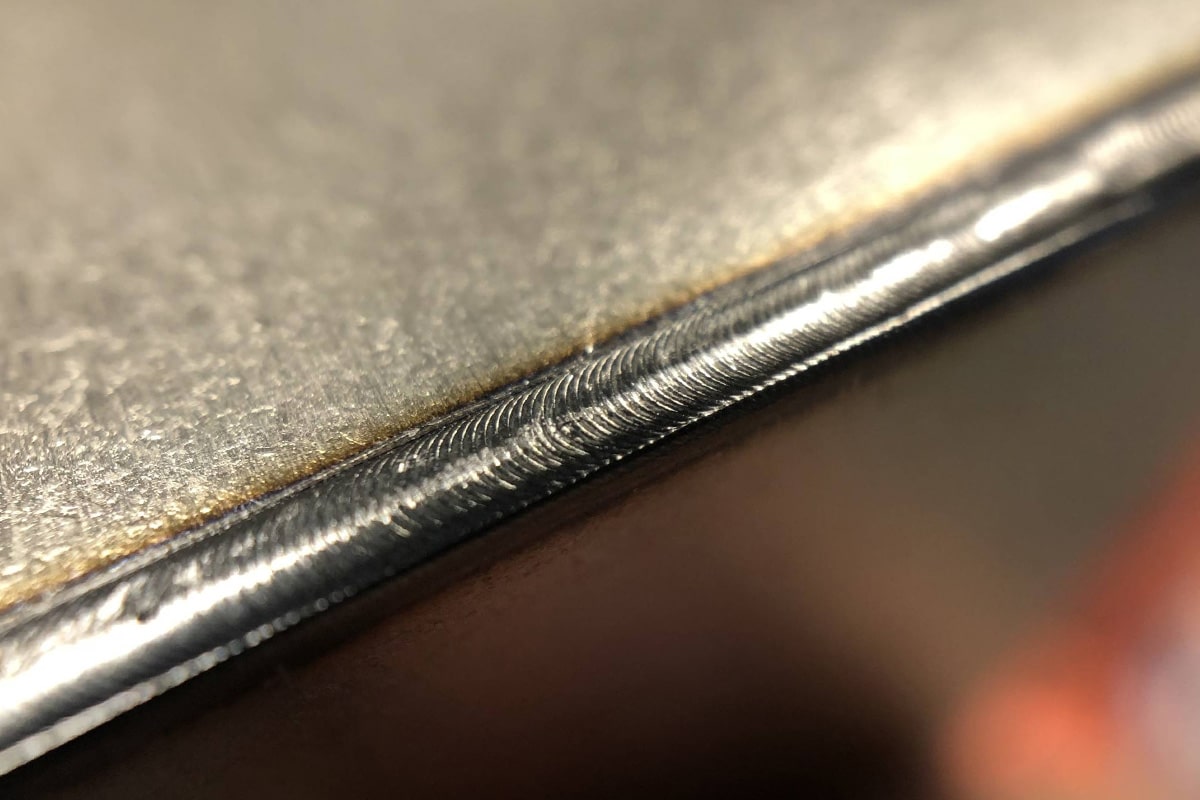
Wie erreicht man durch Laserschweißen ein tiefes Schmelzen von Materialien?
Als effiziente und präzise Schweißtechnologie hat sich das Laserschweißen aufgrund seiner Vorteile wie hoher Energiedichte, berührungsloser Verarbeitung und kleiner Wärmeeinflusszone in vielen Branchen wie der Automobil-, Luft- und Raumfahrt- und Elektronikindustrie etabliert. Im Vergleich zu herkömmlichen Schweißverfahren ermöglicht das Laserschweißen die Verbindung komplexer Strukturen schneller, mit geringerer thermischer Verformung und höherer Schweißfestigkeit. Es eignet sich besonders für die Präzisionsfertigung und anspruchsvolle industrielle Produktionsszenarien.
Um beim Laserschweißen eine tiefe Eindringtiefe zu erreichen, müssen verschiedene Faktoren wie Laserparameter, Materialeigenschaften und Schweißprozesssteuerung umfassend berücksichtigt werden. Dieser Artikel erläutert die Grundprinzipien des Laserschweißens, die wichtigsten Einflussfaktoren auf die Eindringtiefe und analysiert detailliert den Entstehungsmechanismus und die Optimierungsstrategie für die tiefe Eindringtiefe. So können Unternehmen die Laserschweißtechnologie besser anwenden und die Schweißqualität sowie die Produktionseffizienz verbessern.
Inhaltsverzeichnis
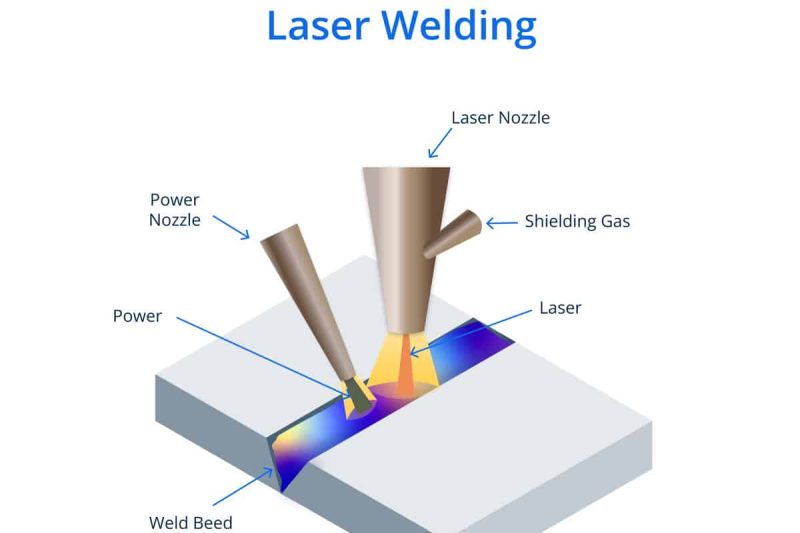
Erfahren Sie mehr über Laserschweißen
Definition und Begründung
Laserschweißen ist ein Verfahren, bei dem ein Laserstrahl als Wärmequelle das Material lokal bis zum Schmelzpunkt erhitzt und so das Schweißen ermöglicht. Der Laserstrahl wird auf den Schweißbereich fokussiert, und die hochintensive Lichtenergie erhitzt und schmilzt das Material schnell zu einem Schmelzbad, das nach dem Abkühlen eine feste Schweißverbindung bildet. Laserschweißen zeichnet sich durch hohe Energiedichte, hohe Präzision und hohe Schweißgeschwindigkeit aus und eignet sich zum Schweißen von Präzisionsteilen.
Übersicht über den Laserschweißprozess
Der Laserschweißprozess umfasst üblicherweise die Schritte Laserbestrahlung, Erhitzen und Schmelzen des Materials, Bildung eines Schmelzbades, Abkühlen und Erstarren usw. In diesen Schritten bestimmen die effektive Nutzung der Laserenergie und die Wechselwirkung der Materialien den Schweißeffekt, insbesondere die Fähigkeit zum Tiefschmelzen.
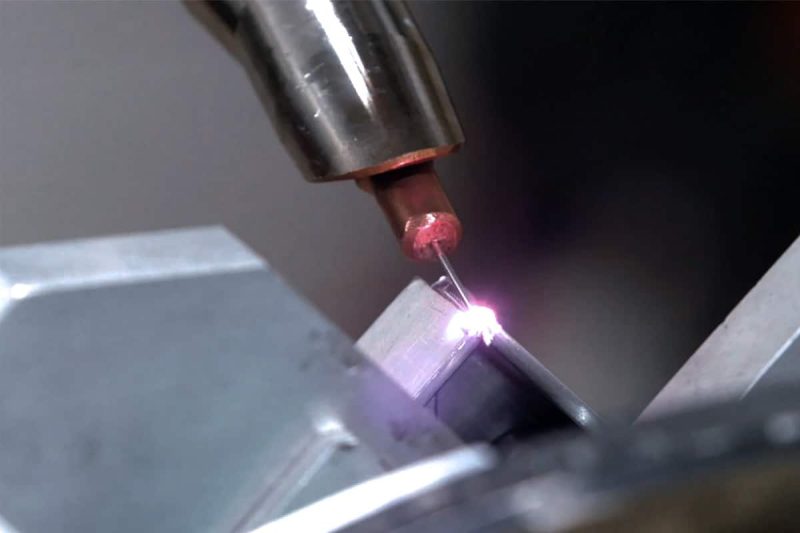
Wechselwirkung von Laserstrahlen mit Materialien
Der Kern des Laserschweißens liegt in der Wechselwirkung zwischen Laserstrahl und Material, die den Schlüssel zu effizientem und tiefem Schweißen darstellt. Der Laserstrahl ist eine Lichtquelle mit hoher Energiedichte. Trifft er auf die Oberfläche eines Materials, wird er teilweise absorbiert, reflektiert oder transmittiert. Die absorbierte Lichtenergie wird in Wärmeenergie umgewandelt, wodurch sich das Material schnell erwärmt und in einen geschmolzenen oder verdampften Zustand übergeht, wodurch das Schweißen abgeschlossen wird. Die physikalischen Eigenschaften verschiedener Materialien, wie Absorptionsgrad, Wärmeleitfähigkeit und Schmelzpunkt, beeinflussen maßgeblich die Effizienz und Qualität des Laserschweißens. Daher ist das Verständnis der Absorption von Laserenergie durch das Material und der Umwandlung von Lichtenergie in Wärmeenergie entscheidend für Optimierung des Schweißprozesses.
Absorption von Laserenergie durch Materialien
Die Leistung eines Materials beim Laserschweißen wird in erster Linie durch seine Fähigkeit zur Absorption von Laserenergie beeinflusst. Die Absorption ist ein wichtiger Parameter zur Messung der Absorptionsfähigkeit des Materials und bestimmt die Umwandlungseffizienz der Laserenergie in der Oberfläche. Verschiedene Materialien weisen unterschiedliche Absorptionsraten für Laser unterschiedlicher Wellenlängen auf. Beispielsweise können Materialien wie Eisen und Edelstahl haben eine hohe Absorptionsrate für Faserlasergeneratoren (nahes Infrarotband), sodass sich leicht ein stabiles Schmelzbad bilden kann. Andererseits können hochreflektierende Metalle wie Aluminium Und Kupfer haben eine geringe Absorptionsrate, was zu einem hohen Energieverlust führt. Um die Absorptionsrate zu verbessern, sind Laser mit höherer Leistung oder spezielle Wellenlängen (wie blaue oder grüne Laser) erforderlich. Darüber hinaus beeinflussen Faktoren wie die Oxidschicht, die Rauheit und die Temperatur der Materialoberfläche die Absorptionswirkung des Lasers. Daher ist vor dem Schweißen in der Regel eine Oberflächenvorbehandlung erforderlich, um die Schweißstabilität zu verbessern.
Umwandlung von Lichtenergie in Wärmeenergie
Trifft der Laserstrahl auf die Materialoberfläche, wird die absorbierte Lichtenergie schnell in Wärmeenergie umgewandelt, wodurch die Materialtemperatur stark ansteigt. Erreicht die Temperatur den Schmelzpunkt, schmilzt das Material und bildet ein Schmelzbad. Steigt die Temperatur weiter bis zur Verdampfungstemperatur, verdampft ein Teil des Materials sogar, wodurch ein Nadelsticheffekt entsteht und eine tiefe Durchschweißung erreicht wird. Die Umwandlungseffizienz von Lichtenergie in Wärmeenergie bestimmt direkt die Tiefe und Qualität der Schweißung. Eine unzureichende Energieumwandlung kann zu oberflächlichen Schweißnähten, schlechter Verschmelzung oder sogar zum Versagen einer stabilen Schweißverbindung führen. Zu hoher Energieeintrag kann zu Materialüberbrennungen, Porenbildung oder Schweißdeformationen führen. Daher kann eine sinnvolle Steuerung von Parametern wie Laserleistung, Strahlmodus und Schweißgeschwindigkeit den Energieumwandlungsprozess effektiv optimieren und die Schweißqualität verbessern.
Die Wechselwirkung zwischen Laserstrahl und Material ist der Kern des Laserschweißens. Der Schlüssel liegt in der Absorption der Laserenergie durch das Material und der effizienten Umwandlung von Lichtenergie in Wärmeenergie. Die Absorptionsrate und die Wärmeleitfähigkeit verschiedener Materialien beeinflussen den Schweißeffekt direkt. Durch Optimierung der Laserwellenlänge, der Leistungsdichte und der Schweißparameter kann die Ausnutzung der Lichtenergie verbessert und so hochwertiges Tiefschweißen erreicht werden. Das Verständnis der Grundprinzipien dieser Wechselwirkungen trägt dazu bei, den Schweißprozess zu optimieren, die Stabilität und Festigkeit der Schweißnaht zu verbessern und den Anwendungsanforderungen verschiedener Industriebereiche gerecht zu werden.
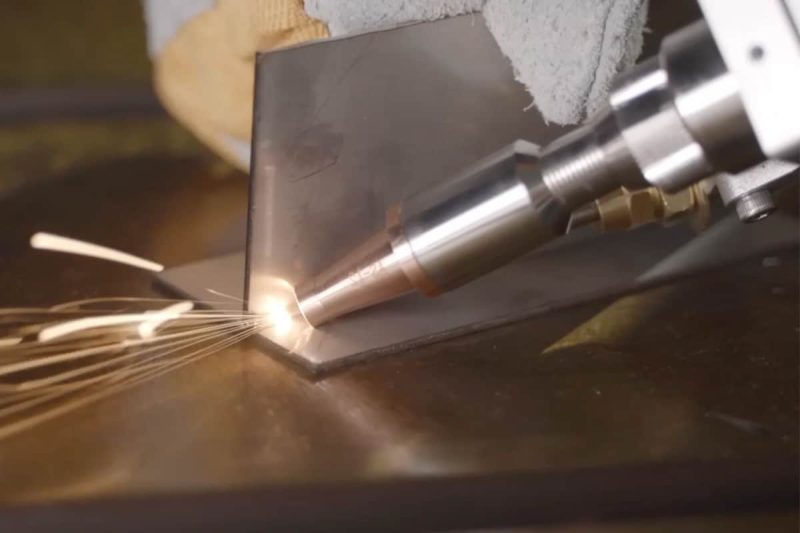
Schlüsselfaktoren, die die Eindringtiefe beeinflussen
Die Tiefenwirkung des Laserschweißens ist einer der wichtigsten Indikatoren für die Schweißqualität. Ihre Eindringtiefe beeinflusst direkt die Festigkeit und Zuverlässigkeit der Schweißnaht. Die Schweißtiefe wird von vielen Faktoren beeinflusst, darunter Laserparameter, Materialeigenschaften, Werkstückgeometrie und -montage sowie Schweißgeschwindigkeit. Diese Faktoren beeinflussen im Zusammenspiel die Bildung und Ausdehnung des Schmelzbades. Eine sinnvolle Optimierung dieser Parameter kann die Schweißtiefe effektiv erhöhen und die Stabilität und Konsistenz der Schweißnaht gewährleisten.
Laserparameter
- Leistung: Die Laserleistung ist der Hauptfaktor, der die Schweißtiefe beeinflusst. Eine höhere Laserleistung kann mehr Energie liefern, um das Material tiefer zu schmelzen. Generell gilt: Mit zunehmender Leistung erhöht sich auch die Schweißtiefe. Zu hohe Leistung kann jedoch zu Überhitzung oder Schweißfehlern führen.
- Strahlfokus und Punktgröße: Die Größe des Laserfokus bestimmt die Energiekonzentration. Ein kleinerer Fokus kann eine höhere Energiedichte und damit eine größere Schweißtiefe liefern. Durch die präzise Einstellung der Fokusposition lässt sich im Allgemeinen das optimale Gleichgewicht zwischen Schmelztiefe und Schmelzbreite erreichen, um unterschiedlichen Schweißanforderungen gerecht zu werden.
- Pulsdauer und -frequenz: Beim gepulsten Laserschweißen sorgt eine hohe Energiezufuhr in kurzer Zeit dafür, dass sich das Material schnell erwärmt und tiefer eindringt. Eine sinnvolle Anpassung der Pulsparameter kann die Formqualität der Schweißnaht optimieren und die Schweißstabilität verbessern.
Materialeigenschaften
- Wärmeleitfähigkeit: Die Wärmeleitfähigkeit eines Materials beeinflusst die Ausbreitung der Laserenergie. Materialien mit hoher Wärmeleitfähigkeit (wie Kupfer und Aluminium) verlieren schnell Wärme, was zu einer geringeren Schmelztiefe führt. Materialien mit geringer Wärmeleitfähigkeit (wie Edelstahl) können die Wärme effektiver konzentrieren und so eine größere Eindringtiefe erreichen.
- Absorptionskoeffizient: Die Fähigkeit des Materials, Laserlicht zu absorbieren, ist ein entscheidender Faktor für die Eindringtiefe. Ein höherer Absorptionskoeffizient kann die Energieausnutzung verbessern und somit die Schweißergebnisse verbessern. Bei stark reflektierenden Materialien ist es in der Regel erforderlich, einen Laser mit einer bestimmten Wellenlänge zu verwenden oder die Oberfläche vorzubehandeln, um die Absorption zu erhöhen.
Werkstückgeometrie und -montage
Auch die Form und Montagemethode des Werkstücks haben einen direkten Einfluss auf den Tiefschmelzeffekt des Laserschweißens. Komplexe geometrische Formen können die präzise Bestrahlung des Zielbereichs durch den Laserstrahl erschweren und so die Schmelztiefe beeinträchtigen. Ein zu großer Montagespalt des Werkstücks oder eine ungenaue Positionierung kann zudem zu ungleichmäßigem Schweißen und einer verminderten Schweißqualität führen. Daher sind vor dem Schweißen eine präzise Montage und Positionierung erforderlich, um eine stabile Einwirkung des Laserstrahls auf den Schweißbereich zu gewährleisten.
Schweißgeschwindigkeit
Die Schweißgeschwindigkeit bestimmt die Zeit, die das Material die Laserenergie absorbiert, und beeinflusst somit die Bildung des Schmelzbades. Niedrigere Schweißgeschwindigkeiten erhöhen in der Regel die Wärmezufuhr, geben dem Material genügend Zeit zum Schmelzen und erhöhen dadurch die Eindringtiefe. Eine zu niedrige Geschwindigkeit kann jedoch zu Überhitzung oder Schweißdeformation führen. Umgekehrt können höhere Schweißgeschwindigkeiten die Eindringtiefe verringern und die Schweißverbindung schwächen. Daher muss die Schweißgeschwindigkeit im praktischen Einsatz entsprechend den Materialeigenschaften und Schweißanforderungen optimiert werden, um eine optimale Schweißqualität zu erzielen.
Die Eindringtiefe beim Laserschweißen wird von vielen Faktoren beeinflusst. Laserparameter, Materialeigenschaften, Werkstückgeometrie und Schweißgeschwindigkeit sind dabei die entscheidenden Faktoren für den Schweißeffekt. Eine sinnvolle Steuerung von Parametern wie Laserleistung, Fokusposition, Schweißgeschwindigkeit und Optimierung in Kombination mit den Materialeigenschaften kann die Stabilität und Qualität des Tiefschweißens effektiv verbessern. Durch die umfassende Regulierung dieser Faktoren kann ein stabiler und zuverlässiger Schweißprozess gewährleistet werden, der den Anforderungen verschiedener industrieller Anwendungsszenarien gerecht wird.
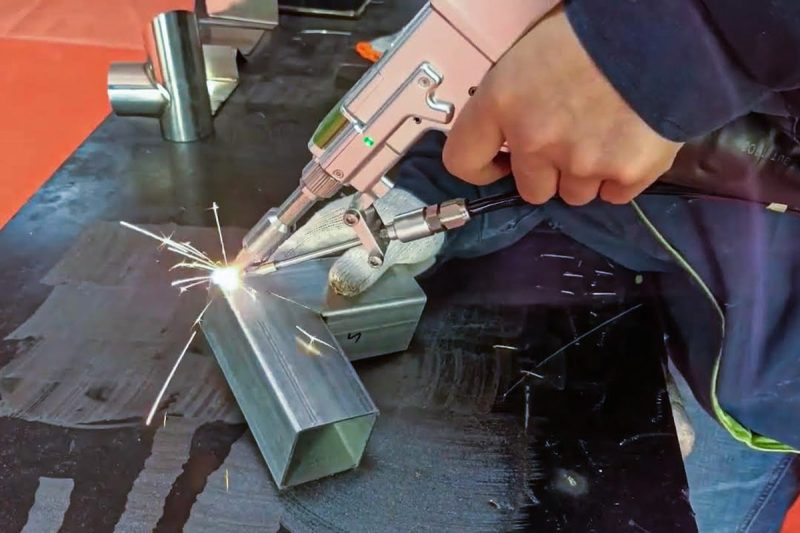
Strategie zur Kontrolle tiefer Penetration
Beim Laserschweißen ist eine stabile und gleichmäßige Eindringtiefe entscheidend. Da die Schweißtiefe von vielen Faktoren wie Laserleistung, Fokusposition, Materialeigenschaften und Schweißgeschwindigkeit beeinflusst wird, sind Strategien wie die Optimierung der Laserparameter sowie Echtzeitüberwachung und -rückmeldung erforderlich, um die Schweißqualität und -konsistenz sicherzustellen. Diese Steuerungsstrategien können nicht nur die Schweißfestigkeit verbessern, sondern auch Schweißfehler reduzieren und die Produktionseffizienz steigern.
Optimierung der Laserparameter
Die präzise Steuerung der Laserparameter ist für das Tiefschweißen entscheidend. Zu den wichtigsten optimierten Parametern gehören:
Laserleistung:
- Durch höhere Leistung kann ein größerer Energieeintrag erzielt werden, der das Material tiefer aufschmilzt und somit die Schweißtiefe erhöht.
- Eine zu hohe Leistung kann zu übermäßigem Schmelzen oder Verdampfen des Materials führen und so Schweißfehler wie Poren oder Risse bilden.
- Eine zu geringe Leistung kann zu einer unzureichenden Durchdringung führen und die Festigkeit der Schweißnaht beeinträchtigen.
Fokusgröße und -position:
- Ein kleiner Fokusdurchmesser erhöht die Energiedichte, sodass der Laser das Material effektiver durchdringen kann und somit die Eindringtiefe erhöht.
- Durch die Optimierung der Fokusposition wird sichergestellt, dass die Energie effektiv im Schweißbereich konzentriert wird, wodurch eine übermäßige Energiestreuung oder ein Oberflächenschmelzen ohne ausreichende Tiefe vermieden wird.
Pulsdauer und Frequenz (beim gepulsten Laserschweißen):
- Eine kurze Impulsdauer in Kombination mit einer hohen Frequenz kann die Wärmeeinflusszone verringern und gleichzeitig eine ausreichende Durchdringung gewährleisten.
- Eine längere Impulsdauer ermöglicht eine tiefere Energiedurchdringung, kann jedoch die Wärmeeinflusszone vergrößern und so die Schweißgenauigkeit beeinträchtigen.
Durch Experimente und Computersimulationen kann die optimale Kombination von Laserparametern für verschiedene Materialien und Schweißanforderungen gefunden werden, um sicherzustellen, dass die Tiefe und Qualität der Schweißung das beste Niveau erreichen.
Echtzeitüberwachung und Feedback
Um eine gleichmäßige Durchdringung während des Schweißprozesses zu gewährleisten, sind Echtzeit-Überwachungs- und Feedbacksysteme zur Anpassung der Schweißparameter erforderlich. Diese Systeme umfassen üblicherweise optische Sensoren, Wärmebildkameras, Laserleistungsmonitore usw., die die Reaktion des Materials während des Schweißprozesses erfassen und die Schweißparameter anhand der Daten automatisch anpassen können.
Wichtige zu überwachende Parameter:
- Schmelzbadtemperatur: Durch eine Infrarotkamera oder Spektralanalyse kann die Schmelzbadtemperatur in Echtzeit gemessen werden, um sicherzustellen, dass die Wärmezufuhr in einem angemessenen Bereich bleibt.
- Morphologie des Schmelzbads: Die Form und die dynamischen Veränderungen des Schmelzbads werden durch eine Hochgeschwindigkeitskamera überwacht, um ein gleichmäßiges und stabiles Schweißen zu gewährleisten.
- Schwankungen der Laserleistung: Automatische Erkennung und Anpassung der Laserleistung, um Schwankungen der Schweißqualität aufgrund von Geräteinstabilitäten zu vermeiden.
Feedback-Mechanismus:
- Das intelligente Steuerungssystem kann die Laserparameter basierend auf den Überwachungsdaten automatisch anpassen, um mögliche Abweichungen auszugleichen. Wenn der Sensor beispielsweise eine unzureichende Eindringtiefe erkennt, kann das System automatisch die Laserleistung erhöhen oder die Fokusposition anpassen.
- Manuelle Anpassung: In hochpräzisen Anwendungsszenarien können Bediener die Schweißparameter basierend auf Überwachungsdaten manuell feinabstimmen, um sicherzustellen, dass die Schweißqualität den Anforderungen entspricht.
Um den tiefen Schmelzeffekt des Laserschweißens zu gewährleisten, sind Optimierung der Laserparameter sowie Echtzeit-Überwachungs- und Feedbackstrategien erforderlich. Durch die sinnvolle Anpassung von Parametern wie Laserleistung, Fokusgröße und Pulsdauer lässt sich die Schweißtiefe effektiv verbessern. Gleichzeitig können mithilfe moderner Überwachungssysteme wichtige Parameter während des Schweißprozesses in Echtzeit erfasst und angepasst werden, um die Stabilität und Konstanz der Schmelztiefe zu gewährleisten. Diese Steuerungsstrategien verbessern nicht nur die Schweißqualität, sondern reduzieren auch Schweißfehler und steigern die Produktionseffizienz. Dadurch wird die Laserschweißtechnologie in der industriellen Fertigung zuverlässiger und effizienter.
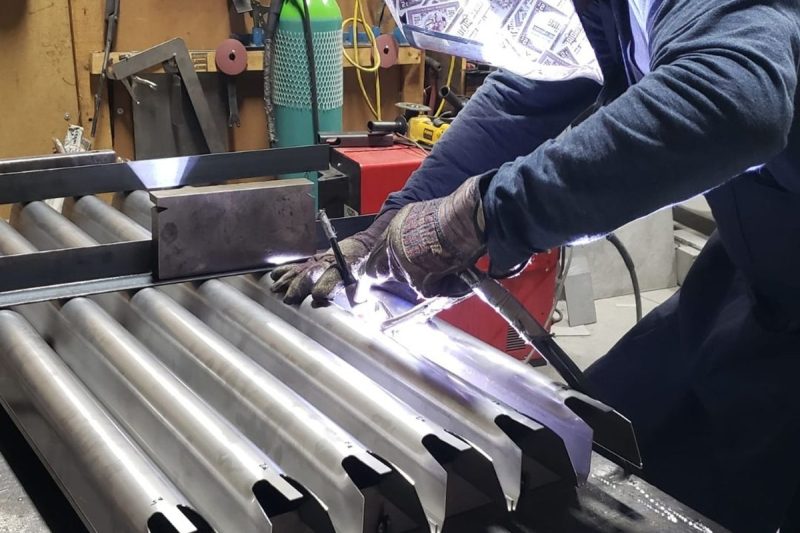
Anwendungen und Branchen
Die Laserschweißtechnologie ist aufgrund ihrer hohen Präzision, Effizienz und Anpassungsfähigkeit an komplexe Materialien in vielen Branchen weit verbreitet, insbesondere in Bereichen mit extrem hohen Anforderungen an Schweißqualität und -tiefe. Die Vorteile des Laserschweißens machen es zur idealen Lösung für Anforderungen, die herkömmliche Schweißtechnologien nicht erfüllen können. Im Folgenden werden einige typische Branchen und Anwendungsfelder vorgestellt, die die Bedeutung und breite Anwendung der Laserschweißtechnologie in der modernen Industrie verdeutlichen.
Automobilindustrie
Laserschweißen wird im Automobilbau häufig eingesetzt, insbesondere beim Schweißen von Karosseriestrukturteilen aus hochfestem Stahl und Aluminiumlegierungen. Laserschweißen ermöglicht eine tiefe Einschweißung, sichert die Festigkeit der Karosserie und reduziert Verformungen. Effizientes Laserschweißen eignet sich auch für automatisierte Produktionslinien zur Verbesserung der Produktionseffizienz.
- Hochfester Stahl: Durch Laserschweißen können bei hochfestem Stahl Tiefschweißungen durchgeführt werden, um die Festigkeit und Sicherheit der Karosserie zu gewährleisten und gleichzeitig den Materialeinsatz zu reduzieren, was dem Leichtbau förderlich ist.
- Aluminiumlegierung Schweißen: Aluminiumlegierungen sind ein häufig verwendetes Leichtbaumaterial im modernen Automobilbau. Dank der präzisen Energiesteuerung ermöglicht die Laserschweißtechnologie ein effizientes Tiefschweißen von Aluminiumlegierungen und gewährleistet so die Festigkeit und Stabilität der Verbindung.
- Automatisierte Produktionslinie: Aufgrund der hohen Geschwindigkeit und Präzision des Laserschweißens eignet es sich für automatisierte Produktionslinien, was die Produktionseffizienz verbessert und manuelle Eingriffe reduziert und so den Anforderungen der Großserienproduktion gerecht wird.
Luft- und Raumfahrt
In der Luft- und Raumfahrtindustrie wird Laserschweißen zum Präzisionsschweißen von Leichtmetalllegierungen und Verbundwerkstoffen eingesetzt. Dank seiner tiefen Schweißfähigkeit und hohen Präzision hat sich das Laserschweißen zu einem idealen Schweißverfahren für Legierungswerkstoffe und Strukturbauteile entwickelt und gewährleistet die Zuverlässigkeit der Komponenten unter extremen Bedingungen.
- Legierungsmaterialien: In der Luft- und Raumfahrt werden Legierungsmaterialien (wie Titanlegierungen, Aluminiumlegierungen usw.) häufig zur Herstellung von Strukturkomponenten verwendet. Laserschweißen ermöglicht ein tieferes Schmelzbad und eine höhere Schweißfestigkeit, um die Zuverlässigkeit der Komponenten unter extremen Arbeitsbedingungen zu gewährleisten.
- Schweißen von Verbundwerkstoffen: Verbundwerkstoffe werden aufgrund ihres geringen Gewichts und ihrer hohen Festigkeit häufig in der Luft- und Raumfahrt eingesetzt. Durch Laserschweißen können diese Materialien präzise verschweißt werden, um die Integrität der Struktur zu gewährleisten.
- Hohe Präzision und hohe Qualitätsanforderungen: Das Schweißen von Luft- und Raumfahrtteilen erfordert extrem hohe Präzision und Qualität. Laserschweißen kann die Wärmeeinflusszone und Schweißverformungen, die bei herkömmlichen Schweißverfahren auftreten können, wirksam vermeiden und so die Festigkeit und Haltbarkeit der geschweißten Teile gewährleisten.
Elektronikindustrie
Kleine Bauteile in elektronischen Geräten werden häufig präzise per Laserschweißen verschweißt, um eine hohe Zuverlässigkeit und Stabilität der Bauteile zu gewährleisten. Laserschweißen ermöglicht hochpräzises Tiefschweißen, ohne andere Bauteile zu beschädigen. Daher eignet es sich für die Herstellung mikroelektronischer Bauteile.
- Mikroelektronische Komponenten: Laserschweißen wird häufig zum Schweißen mikroelektronischer Komponenten wie Sensoren, Batterien, integrierten Schaltkreisen usw. verwendet. Diese Komponenten stellen sehr hohe Anforderungen an die Schweißqualität und das Laserschweißen kann eine präzise Wärmezufuhr gewährleisten, um thermische Schäden und Komponentenverformungen zu vermeiden.
- Präzisionsschweißen: In der Elektronikindustrie können mithilfe der Laserschweißtechnologie sehr präzise Verbindungen kleiner Komponenten hergestellt werden, ohne die umliegenden empfindlichen Komponenten zu beschädigen.
- Verbessern Sie die Produktzuverlässigkeit: Durch Laserschweißen können starke und stabile Schweißverbindungen hergestellt werden, die die Zuverlässigkeit und Haltbarkeit elektronischer Produkte bei langfristiger Nutzung gewährleisten.
Die Laserschweißtechnologie wird aufgrund ihrer hohen Präzision, Effizienz und Anpassungsfähigkeit an komplexe Materialien in vielen Branchen wie der Automobilindustrie, der Luft- und Raumfahrt, der Elektronik, der Medizintechnik und der Präzisionsindustrie eingesetzt. Mit dem Fortschritt von Wissenschaft und Technologie wird das Laserschweißen in weiteren Bereichen eine wichtige Rolle spielen, den Bedarf der modernen Industrie an hochwertigem und hochpräzisem Schweißen decken und die Entwicklung der Fertigungstechnologie in verschiedenen Branchen fördern.
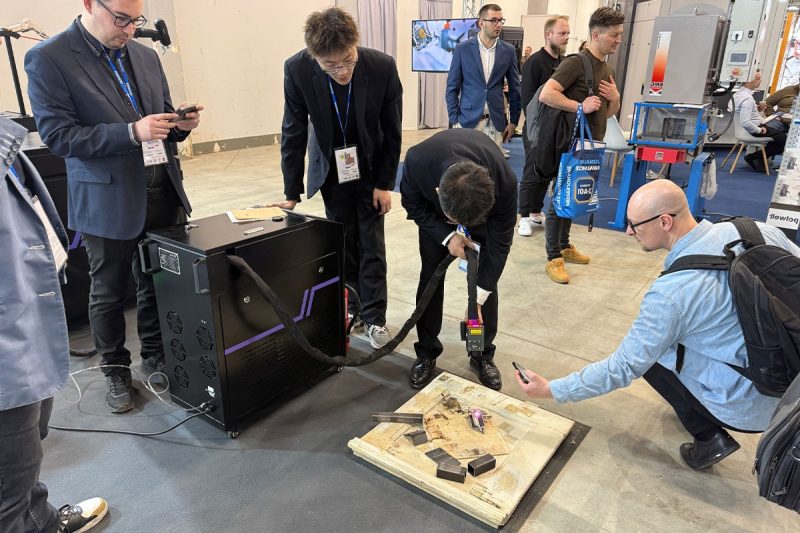
Zusammenfassen
Der Prozess des Tiefschweißens mittels Laserschweißen ist komplex und präzise. Er umfasst die Interaktion zwischen Laser und Material, die Optimierung und Kontrolle mehrerer Schlüsselfaktoren sowie verschiedene Mechanismen des Tiefschweißens. Durch präzise Steuerung der Laserparameter und Echtzeitüberwachung kann Tiefschweißen ohne Beeinträchtigung der Materialqualität erreicht werden. Diese Technologie ist in vielen Branchen weit verbreitet, insbesondere in hochpräzisen Bereichen wie der Automobil-, Luft- und Raumfahrt- und Elektronikindustrie. Mit der kontinuierlichen technologischen Weiterentwicklung wird das Laserschweißen seine einzigartigen Vorteile in weiteren Branchen ausspielen.
Im obigen Inhalt haben wir die Prinzipien und Prozesse des Laserschweißens eingehend analysiert und uns dabei auf das Erreichen von tiefem Schmelzen und wichtige Kontrollstrategien konzentriert. Als Branchenführer, AccTek-Laser ist bestrebt, effiziente Laserschweißlösungen anzubieten. Unsere Laserschweißmaschinen kann die hochpräzisen und hochwertigen Schweißanforderungen verschiedener Branchen erfüllen. Bei Fragen oder Wünschen kontaktieren Sie uns bitte für weitere professionelle Beratung und Dienstleistungen zum Laserschweißen.
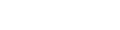
Kontaktinformationen
- [email protected]
- [email protected]
- +86-19963414011
- Nr. 3 Zone A, Industriegebiet Lunzhen, Stadt Yucheng, Provinz Shandong.
Holen Sie sich Laserlösungen