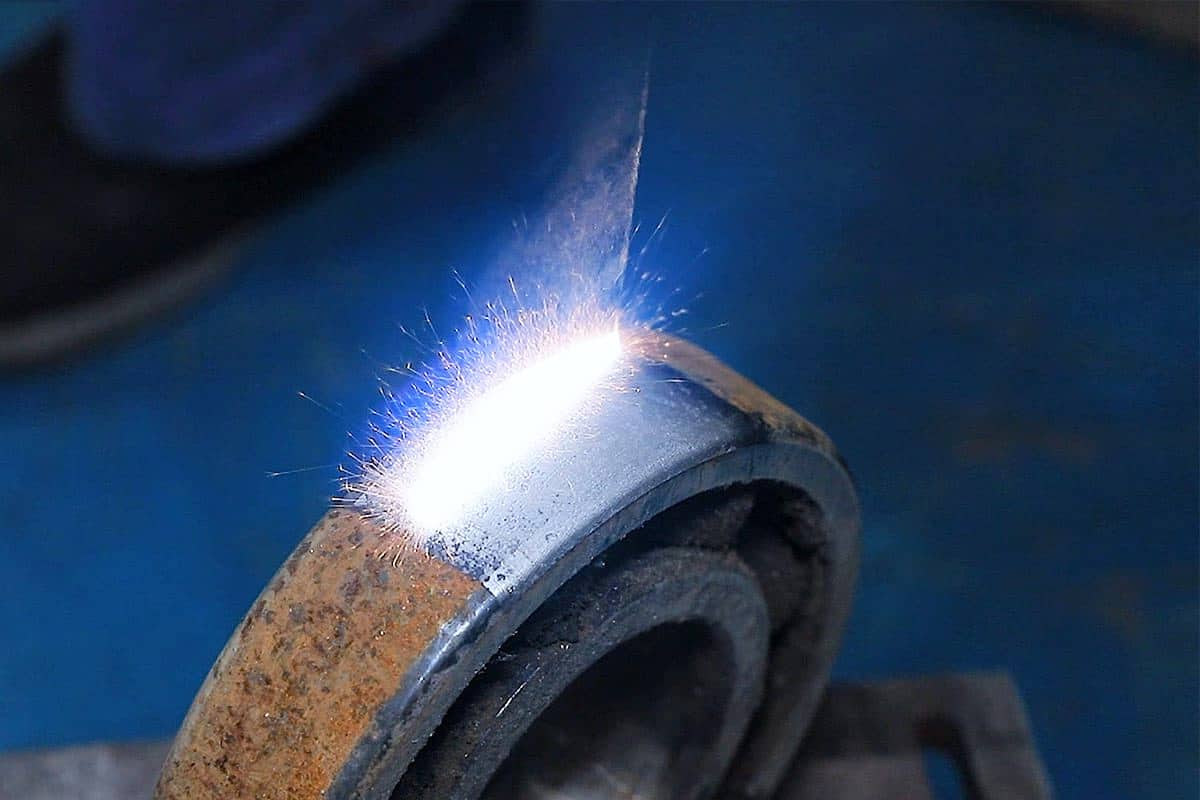
Wird das Substrat durch die Reinigung mit gepulsten Lasern beschädigt?
Die Reinigung mit gepulsten Lasern erfreut sich aufgrund ihrer hohen Effizienz, Umweltfreundlichkeit und berührungslosen Funktionsweise großer Beliebtheit in Anwendungen wie der Oberflächenvorbereitung und der Rostentfernung mit Faserlasern. Viele Anwender haben jedoch weiterhin Bedenken: Kann diese Technologie das Substrat beschädigen?
Dieser Artikel untersucht die Grundlagen der gepulsten Laserreinigung und untersucht mögliche thermische, mechanische und photochemische Effekte, die unter verschiedenen Parametereinstellungen zu Substratschäden führen können. Wir gehen außerdem auf wichtige Einflussfaktoren wie Wärmeleitfähigkeit und Absorptionsrate des Materials ein und stellen praktische Strategien zur Risikominimierung vor – wie Parameteroptimierung, Mehrpulssteuerung und Echtzeit-Temperaturüberwachung.
Inhaltsverzeichnis
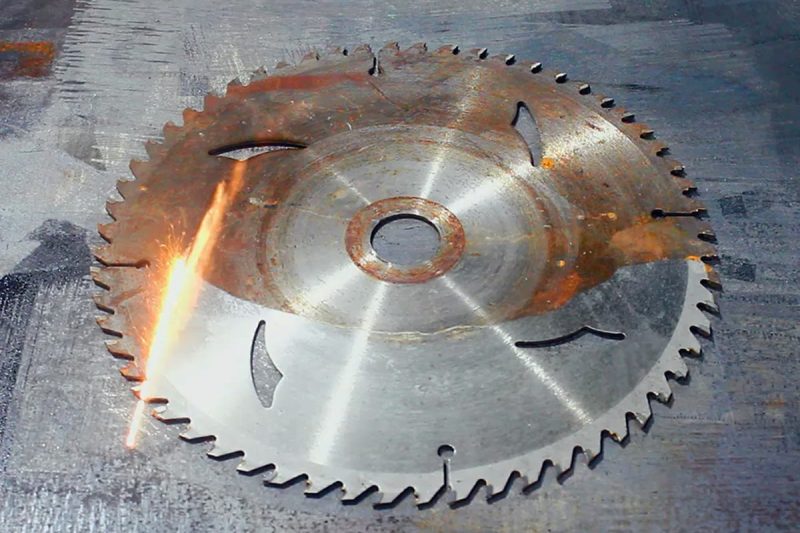
Grundlegendes zur Reinigung mit gepulsten Lasern
Die gepulste Laserreinigung ist eine effiziente, umweltfreundliche und berührungslose Oberflächenbehandlungstechnologie, die häufig in Anwendungen wie der Laser-Rostentfernung, der Lackentfernung, der Oxidschichtreinigung und der Laser-Oberflächenvorbereitung für Präzisionsformen und elektronische Bauteile eingesetzt wird. Das Kernprinzip besteht darin, dass hochenergetische Laserpulse Verunreinigungen schnell verdampfen oder vom Substrat entfernen, ohne nennenswerte thermische Effekte oder mechanische Schäden am Material zu verursachen.
In der Praxis ist das Verständnis und die Optimierung der folgenden Schlüsselparameter von entscheidender Bedeutung, um die Reinigungseffizienz zu verbessern und die Substratsicherheit zu gewährleisten:
- Pulsdauer: Bezeichnet die Dauer eines einzelnen Laserpulses, typischerweise im Nanosekunden-, Pikosekunden- oder sogar Femtosekundenbereich. Kürzere Pulse tragen zur Reduzierung der Wärmeeinflusszone (WEZ) bei und eignen sich daher ideal für die Präzisionsreinigung wärmeempfindlicher Materialien.
- Pulsenergie: Stellt die Energie jedes Laserpulses dar und beeinflusst direkt die Reinigungsleistung. Eine höhere Pulsenergie entfernt effektiv stark anhaftende Verunreinigungen, muss aber sorgfältig kontrolliert werden, um eine Beschädigung des Substrats zu vermeiden.
- Wiederholungsrate: Bezeichnet die Frequenz der pro Zeiteinheit abgegebenen Laserimpulse. Eine höhere Wiederholungsrate kann die Reinigungsgeschwindigkeit erhöhen, kann aber bei unsachgemäßer Steuerung zu einem Hitzestau und damit zu thermischen Schäden führen.
- Wellenlänge: Die Wellenlänge des Lasers bestimmt seine Wechselwirkung mit verschiedenen Materialien. Beispielsweise reagieren Metalle typischerweise besser auf eine Laserwellenlänge von 1064 nm.
- Strahlprofil: Bezeichnet die Energieverteilung des Laserstrahls im Raum. Ein ideales Strahlprofil sollte eine gleichmäßige Energieverteilung aufweisen, um eine stabile und effiziente Reinigung zu gewährleisten und gleichzeitig lokale Überhitzung oder ungleichmäßige Reinigung zu vermeiden.
Bei Anwendungen wie der Laser-Rostentfernung, der Laser-Reinigung von Formen oder anderen industriellen Anwendungen verbessert die richtige Konfiguration dieser Parameter nicht nur die Effizienz, sondern schützt auch das Material und ist somit ein entscheidender Faktor für die Erzielung einer qualitativ hochwertigen Reinigung mit gepulsten Lasern.
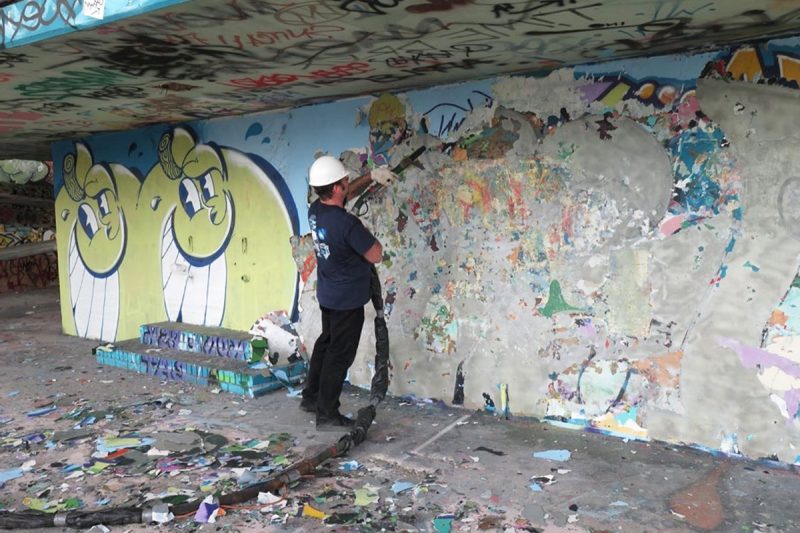
Substratschädigungsmechanismen
Während der Reinigung mit gepulsten Lasern können Substrate durch verschiedene Mechanismen beeinflusst werden, darunter thermische, mechanische und photochemische Effekte. Die Reinigung mit gepulsten Lasern bietet zwar eine hohe Effizienz und ist umweltfreundlich, diese Effekte können jedoch unter bestimmten Bedingungen zu Schäden am Substrat führen. Nachfolgend sind die spezifischen Schadensmechanismen aufgeführt:
Thermische Effekte
- Schmelzen: Hochenergetische Laserpulse können das Substrat lokal über den Schmelzpunkt erhitzen und so lokales Schmelzen verursachen. Dieses Phänomen tritt insbesondere beim Reinigen von Metalloberflächen oder Beschichtungen häufig auf. Bei zu hoher Laserenergie kann es zu lokalem Schmelzen kommen.
- Thermische Spannung: Schnelles Erhitzen und Abkühlen während der Laserreinigung kann zu einer ungleichmäßigen Wärmeausdehnung und damit zu inneren Spannungen im Material führen. Diese Spannungen können insbesondere bei wärmeempfindlichen oder dünnwandigen Materialien zu Rissen oder Verformungen führen.
- Wärmeeinflusszone (WEZ): Die Mikrostruktur und die mechanischen Eigenschaften des Substrats in der Wärmeeinflusszone (WEZ) können sich verändern. Diese Veränderung kann die mechanische Festigkeit und Lebensdauer des Substrats verringern, insbesondere bei Metallen und Legierungen, bei denen die WEZ zu einer Verschlechterung der Materialleistung führen kann.
Mechanische Effekte
- Stoßwellen: Die durch den Laser induzierte Plasmaexpansion erzeugt Stoßwellen, die mechanische Schäden an der Substratoberfläche verursachen können. Dies gilt insbesondere für spröde oder feine Materialien, bei denen Stoßwellen zu Oberflächenrissen oder Materialabplatzungen führen können.
- Verdampfungsdruck: Durch die schnelle Verdampfung von Verunreinigungen entsteht hoher Druck, der auf die Substratoberfläche übertragen werden kann und zusätzliche mechanische Belastung erzeugt. Ein zu schneller Reinigungsprozess oder zu hohe Energie kann zu lokalen Schäden oder Verformungen des Substrats führen.
Photochemische Effekte
- Chemische Veränderungen der Oberfläche: Hochenergetische Photonen des Lasers können mit der Substratoberfläche interagieren und chemische Reaktionen auslösen, die deren Oberflächeneigenschaften verändern. Beispielsweise können einige Laserreinigungsprozesse Oxidation oder andere chemische Reaktionen auslösen, die die Oberflächenstruktur und chemische Zusammensetzung des Substrats verändern.
- Kontamination: Unvollständige Entfernung von Verunreinigungen während der Reinigung kann dazu führen, dass sich Rückstände auf der Substratoberfläche ablagern und neue Verunreinigungen verursachen. Dies kann die Leistung des Substrats beeinträchtigen und langfristig negative Auswirkungen auf dessen Nutzung haben.
Die gepulste Laserreinigung ist eine hocheffiziente Methode zur Entfernung von Oberflächenverunreinigungen. Allerdings ist eine sorgfältige Kontrolle der Laserparameter wie Pulsenergie, -dauer und -wiederholrate unerlässlich, um zu verhindern, dass die oben genannten thermischen, mechanischen und photochemischen Effekte das Substrat beschädigen. Die richtige Konfiguration der Laserparameter und eine präzise Steuerung sind unerlässlich für die Sicherheit und Effizienz des Reinigungsprozesses.
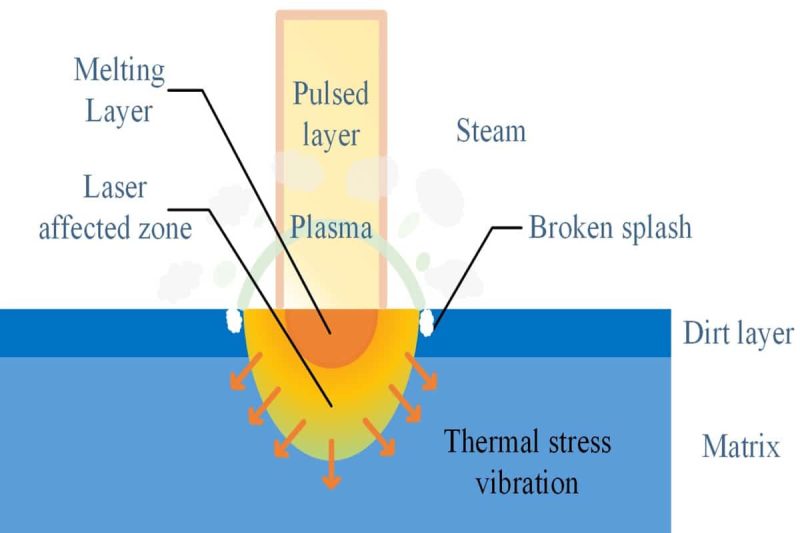
Einflussfaktoren auf Substratschäden
Bei der Reinigung mit gepulsten Lasern beeinflussen verschiedene Faktoren den Grad der Beschädigung des Substrats. Das Verständnis und die Optimierung dieser Faktoren ist entscheidend, um sowohl eine effektive Entfernung von Verunreinigungen als auch den Schutz des Substrats zu gewährleisten. Die wichtigsten Einflussfaktoren sind:
Materialeigenschaften
- Wärmeleitfähigkeit: Materialien mit hoher Wärmeleitfähigkeit können Wärme effizienter ableiten und so das Risiko von Wärmestaus und -schäden verringern. Beispielsweise sind Metalle wie Kupfer und Aluminium aufgrund ihrer besseren Wärmeableitung weniger anfällig für thermische Zersetzung bei der Laserreinigung.
- Absorptionskoeffizient: Der Absorptionskoeffizient bestimmt, wie viel Laserenergie ein Material bei einer bestimmten Wellenlänge absorbieren kann. Eine höhere Absorptionsrate führt zu einer schnelleren Oberflächenerwärmung. Daher ist eine präzise Steuerung der Laserwellenlänge und -leistung für eine sichere Reinigung unerlässlich.
- Schmelzpunkt: Materialien mit niedrigerem Schmelzpunkt neigen bei hochenergetischer Laserbestrahlung eher zum Schmelzen. Die Wahl geeigneter Reinigungsparameter ist bei der Arbeit mit wärmeempfindlichen Substraten wie Kunststoffen oder niedrigschmelzenden Legierungen entscheidend.
- Mechanische Festigkeit: Eine höhere mechanische Festigkeit hilft einem Material, Schäden durch Stoßwellen oder thermische Belastung zu widerstehen. Stärkere Substrate neigen bei der Reinigung mit hochfrequenten gepulsten Lasern weniger zu Rissen oder Verformungen.
- Chemische Zusammensetzung: Die chemische Stabilität des Substrats beeinflusst seine Anfälligkeit für photochemische Reaktionen. Bei einigen Materialien kann es bei Einwirkung hochenergetischer Photonen zu chemischen Veränderungen der Oberflächenbeschaffenheit kommen, was sich negativ auf ihre Leistung auswirken kann.
Laserparameter
- Pulsdauer: Die Dauer jedes Laserpulses beeinflusst direkt die Wärmeübertragung auf das Substrat. Ultrakurze Pulse (z. B. Femtosekundenlaser) können die Wärmeeinflusszone (WEZ) deutlich minimieren und so das Risiko thermischer Schäden – insbesondere bei empfindlichen oder Präzisionsbauteilen – verringern.
- Pulsenergie: Die richtige Einstellung der Pulsenergie ist entscheidend. Ausreichend Energie ist erforderlich, um Verunreinigungen zu entfernen. Zu viel Energie kann jedoch zum Schmelzen oder Abtragen des Substrats führen. Die Optimierung dieses Parameters gewährleistet eine effiziente und sichere Reinigung.
- Wiederholungsrate: Eine hohe Wiederholungsrate erhöht das Risiko eines Hitzestaus. Um einen Wärmestau und mögliche Substratschäden zu vermeiden, muss die Frequenz an die Wärmetoleranz und Leitfähigkeit des Materials angepasst werden.
- Wellenlänge: Die Wahl einer Laserwellenlänge, die den Absorptionseigenschaften sowohl der Verunreinigungen als auch des Substrats entspricht, verbessert die Reinigungseffizienz und reduziert Schäden. Dies ist eine Schlüsselstrategie zur Optimierung der Laseroberflächenvorbereitung.
Umweltbedingungen
- Umgebungstemperatur: Erhöhte Umgebungstemperaturen können die Ausgangstemperatur des Substrats erhöhen und so die Gefahr einer Überhitzung während des Reinigungsvorgangs erhöhen. Bei empfindlichen Anwendungen kann eine Temperaturregelung erforderlich sein.
- Luftfeuchtigkeit: Hohe Luftfeuchtigkeit kann dazu führen, dass sich Feuchtigkeit auf der Substratoberfläche niederschlägt und die Interaktion des Lasers mit dem Material verändert. Dies kann zusätzliche thermische oder chemische Effekte zur Folge haben und die Reinigungsleistung beeinträchtigen.
- Oberflächenbeschaffenheit: Die Oberflächenrauheit und die Art der vorhandenen Verunreinigungen beeinflussen das Ergebnis des Reinigungsvorgangs. Unregelmäßige Oberflächen oder schichtweise Verunreinigungen können zu einer ungleichmäßigen Energieverteilung führen, was sowohl die Reinigungsleistung als auch die Sicherheit des Substrats beeinträchtigt.
Der Erfolg der gepulsten Laserreinigung und ihre Auswirkungen auf das Substrat hängen nicht nur vom Lasersystem selbst, sondern auch von den physikalischen und chemischen Eigenschaften des Materials, den Umgebungsbedingungen und dem Oberflächenzustand ab. Um Substratschäden zu minimieren und die Reinigungseffizienz zu maximieren, ist es wichtig, diese Faktoren umfassend zu bewerten und die Laserparameter entsprechend anzupassen.
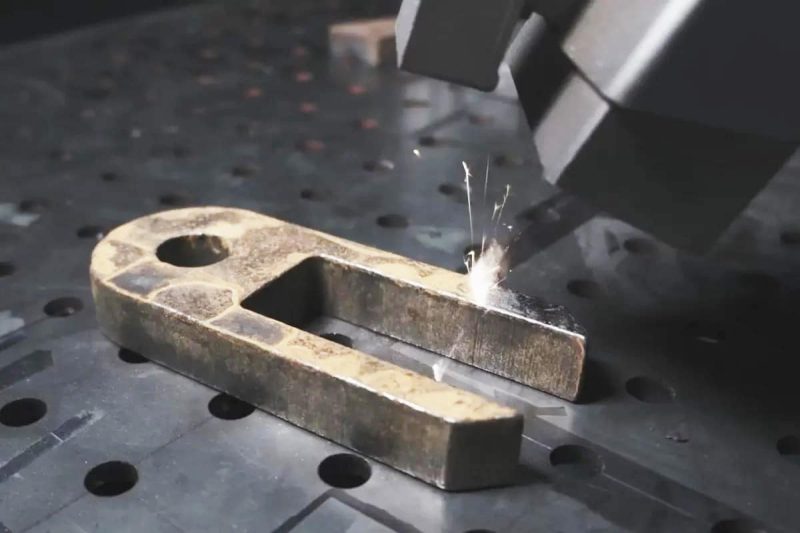
Strategien zur Minimierung von Substratschäden
Die gepulste Laserreinigung bietet zwar eine präzise, berührungslose Lösung zur Entfernung von Verunreinigungen, falsche Parametereinstellungen können jedoch zu irreversiblen Schäden am darunterliegenden Substrat führen. Um eine effektive Reinigung bei gleichzeitiger Wahrung der Materialintegrität zu gewährleisten, sollte eine Kombination aus Parameteroptimierung und fortschrittlichen Techniken angewendet werden.
Parameteroptimierung
- Anpassen der Impulsdauer: Durch die Verwendung ultrakurzer Impulse, beispielsweise von Femtosekundenlasern, wird die thermische Diffusionszone erheblich eingeschränkt, wodurch die Größe der Wärmeeinflusszone (WEZ) effektiv minimiert und das Risiko thermischer Schäden verringert wird.
- Steuerung der Impulsenergie: Durch Einstellen der Impulsenergie auf das zum Entfernen von Verunreinigungen erforderliche Minimum wird eine übermäßige Erhitzung oder ein Schmelzen der Substratoberfläche verhindert, was bei empfindlichen Materialien von entscheidender Bedeutung ist.
- Verwaltung der Wiederholungsrate: Eine sorgfältig ausgewählte Wiederholungsrate gewährleistet eine ausreichende Abkühlzeit zwischen den Impulsen und hilft, einen Wärmestau zu verhindern, der zu Verformungen, Mikrorissen oder anderen thermisch bedingten Substratproblemen führen kann.
- Auswahl der richtigen Wellenlänge: Durch die Anpassung der Laserwellenlänge an die Absorptionseigenschaften des Substrats und der Verunreinigungen wird die Reinigungsselektivität verbessert, die Effizienz gesteigert und die Belastung des Substrats minimiert.
Fortgeschrittene Techniken
- Betrieb im Burst-Modus: Durch die Aufteilung eines einzelnen Impulses in eine Reihe von Unterimpulsen reduziert der Burst-Modus die Spitzenimpulsintensität bei gleichbleibender Gesamtenergie und mildert so die thermische und mechanische Belastung der Oberfläche.
- Überlappung mehrerer Impulse: Das Entfernen von Verunreinigungen in mehreren Durchgängen mithilfe von Impulsen niedrigerer Energie ermöglicht einen schrittweisen Materialabtrag, wodurch die Auswirkungen auf das Substrat erheblich verringert werden.
- Strahlformung: Durch moderne Optik kann die Laserenergie gleichmäßiger über den Zielbereich verteilt werden, wodurch eine lokale Überhitzung verhindert und konsistente Ergebnisse bei der Laseroberflächenvorbereitung gewährleistet werden.
Überwachung und Feedback
- Temperaturüberwachung: Die Temperatur ist ein entscheidender Faktor für thermische Schäden. Durch die Platzierung von Infrarot-Wärmebildkameras oder Thermoelementsensoren im Reinigungsbereich lässt sich die Temperaturentwicklung der Substratoberfläche in Echtzeit erfassen. Nähert sich die Temperatur dem Schmelzpunkt oder dem kritischen Wert der thermischen Spannung, kann das System die Pulsenergie oder die Wiederholungsrate sofort reduzieren, um Schmelzen, Verformungen oder thermische Risse im Material wirksam zu verhindern. Dieser Rückkopplungsmechanismus hat die Sicherheit und Zuverlässigkeit der Laserreinigung in der Präzisionsfertigung deutlich verbessert.
- Akustische Überwachung: Akustische Überwachungstechnologien, wie beispielsweise Ultraschall-Dickenmessgeräte, können die Dickenänderungen des Substrats während des Reinigungsvorgangs effektiv verfolgen. Durch die Echtzeit-Datenerfassung kann das System feststellen, ob übermäßiger Materialabtrag stattgefunden hat, rechtzeitig Warnungen ausgeben und die Laserparameter anpassen. Beispielsweise schlägt das chinesische Patent CN112044874A ein Echtzeit-Laserreinigungssystem mit Ultraschall-Feedback vor, um Strukturschäden durch übermäßige Reinigung zu verhindern.
- Optisches Feedback: Die optische Kohärenztomografie (OCT) bietet hochauflösende dreidimensionale Bildgebungsmöglichkeiten für den Reinigungsbereich. So lässt sich präzise feststellen, ob Verunreinigungen vollständig entfernt wurden und ob Schäden auf der Substratoberfläche vorliegen. Im Vergleich zu herkömmlichen visuellen Systemen bietet die OCT eine höhere Durchdringung und Genauigkeit und eignet sich besonders zur Beurteilung der Reinigungswirkung hochpräziser oder mehrschichtiger Oberflächen.
Durch die Integration präziser Laserparametersteuerung mit fortschrittlichen Technologien lässt sich das Risiko von Substratschäden bei der gepulsten Laserreinigung deutlich reduzieren. Diese Strategien sind besonders wichtig in Anwendungen, bei denen die Oberflächenintegrität von größter Bedeutung ist, wie beispielsweise in der Luft- und Raumfahrt, der Halbleiterfertigung und der Restaurierung von Kulturerbe. Die fachgerechte Umsetzung verbessert nicht nur die Reinigungsleistung, sondern trägt auch zur langfristigen Haltbarkeit und Sicherheit des Materials bei.
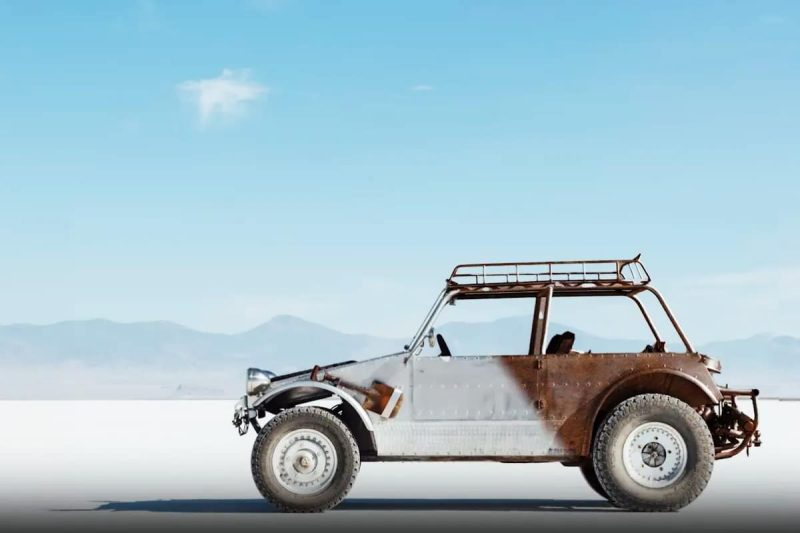
Fallstudien und Anwendungen
Die gepulste Laserreinigung mit ihrem berührungslosen Verfahren, ihrer hohen Selektivität und dem verbrauchsmaterialfreien Betrieb wird bereits erfolgreich in verschiedenen High-End-Industrien eingesetzt. Diese Praxisanwendungen demonstrieren die Zuverlässigkeit und den industriellen Nutzen der Technologie bei komplexen Oberflächenbehandlungen.
Halbleiterindustrie
In der Halbleiterfertigung können selbst mikrometergroße Partikelverunreinigungen die Chipleistung beeinträchtigen oder Produktionsausfälle verursachen. Herkömmliche Reinigungsmethoden können bei der Partikelentfernung statische Elektrizität erzeugen oder die Waferoberfläche beschädigen. Die gepulste Laserreinigung – insbesondere mit Femtosekunden-Laserpulsen (z. B. 233 fs) – nutzt laserinduzierte Mikrostoßwellen, um Verunreinigungen präzise und nahezu ohne thermische Auswirkungen auf mikroskopischer Ebene von Glassubstraten zu entfernen. Dieses hochpräzise und schonende Reinigungsverfahren entwickelt sich zunehmend zu einem Schlüsselprozess in modernen Chip-Produktionslinien.
Automobilindustrie
Bei der Triebwerkswartung, der Überholung von Turbinenschaufeln und der Wartung von Hydrauliksystemen ist die effiziente Entfernung von Rost und starken Verunreinigungen entscheidend. Die Reinigung mittels gepulster Laserstrahlung ermöglicht eine starke Energiekopplung mit den Schmutzschichten auf Metalloberflächen und damit ein präzises Abtragen, ohne die Maßgenauigkeit oder Oberflächenintegrität kritischer Komponenten zu beeinträchtigen. Die hohe Wiederholgenauigkeit und die einfache Automatisierung machen sie zur idealen Wahl für moderne industrielle Produktionslinien. Sie verlängert effektiv die Lebensdauer von Teilen und verbessert die Anlagenzuverlässigkeit.
Erhaltung des kulturellen Erbes
Die Reinigung historischer Artefakte und Gebäude erfordert äußerste Sorgfalt – sie muss Verunreinigungen gründlich entfernen, ohne das Originalmaterial zu beschädigen. Ultrakurzpulslasertechnologie ermöglicht eine schonende Reinigung von Materialien wie Stein, Metall und Keramik. Sie wird häufig zur Entfernung von Biofilmen, Umweltverschmutzung und Korrosionsprodukten eingesetzt. Im Vergleich zur chemischen oder mechanischen Reinigung vermeiden Lasermethoden Sekundärverschmutzung und physischen Abrieb und werden weltweit häufig in Museen, Restaurierungslaboren und Denkmalschutzprojekten eingesetzt.
Von der Präzisionselektronik über die Schwerindustrie bis hin zur Denkmalpflege hat sich die gepulste Laserreinigung als hocheffiziente, sichere und kontrollierbare moderne Reinigungslösung erwiesen. Mit der Weiterentwicklung der Lasertechnologie und intelligenter Steuerungssysteme wird sich ihr Anwendungsbereich weiter erweitern und Oberflächenreinigungsprozesse branchenübergreifend immer höheren Standards gerecht werden.
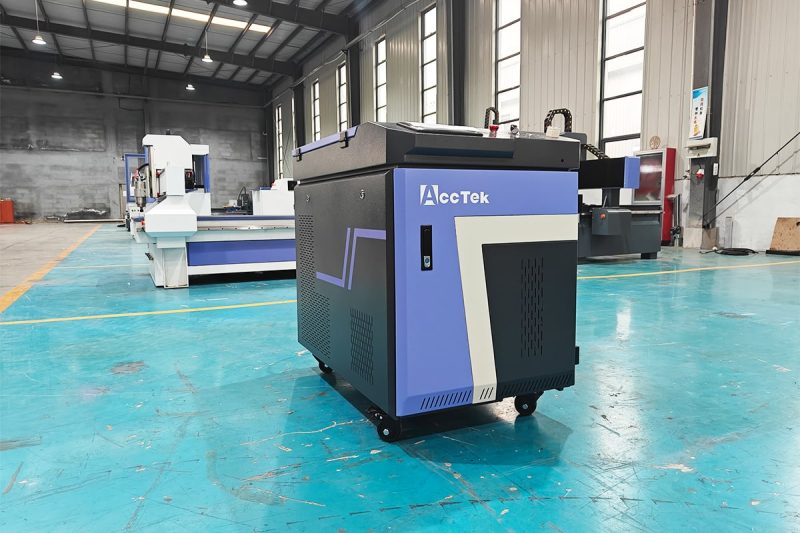
Herausforderungen und Einschränkungen
Trotz der Vorteile der Reinigung mit gepulsten Lasern – wie berührungsloser Betrieb, hohe Präzision und Umweltfreundlichkeit – steht die Technologie bei der praktischen Umsetzung und breiteren Verbreitung in verschiedenen Branchen noch vor mehreren Herausforderungen:
Kosten: Laserreinigungssysteme bestehen in der Regel aus Hochleistungslasergeneratoren, Präzisionssteuereinheiten und Kühlsystemen. Die Anfangsinvestition ist relativ hoch. Für kleine und mittlere Unternehmen können die Anschaffungs- und Wartungskosten zum größten Hindernis werden. Gleichzeitig verursachen einige High-End-Systeme wie Femtosekunden- oder Pikosekundenlasergeneratoren höhere Kosten für die Ausrüstung und Wartung, sodass die Kapitalrendite abgewogen werden muss.
Materialverträglichkeit: Bestimmte Materialien mit hoher Reflektivität (wie Aluminium oder Kupfer) oder Transparenz (wie Glas oder Kunststoff) absorbieren Laserenergie schlecht, was die Wirksamkeit des Reinigungsvorgangs mindert oder zum Scheitern führt. Darüber hinaus muss die Laserwellenlänge präzise auf die optischen Absorptionseigenschaften des Zielmaterials abgestimmt sein – eine besonders komplexe Anforderung bei der Reinigung von Verbundoberflächen aus mehreren Materialien.
Obwohl Kosten und technische Herausforderungen bestehen bleiben, etabliert sich die gepulste Laserreinigung zunehmend als zuverlässige und fortschrittliche Lösung in anspruchsvollen Industrieanwendungen. Mit der fortschreitenden Entwicklung von Miniaturisierung, Kostensenkung und intelligenten Betriebssystemen dürften diese Einschränkungen mit der Zeit abnehmen und den Weg für eine breitere Anwendung in unterschiedlichen Industrieumgebungen ebnen.
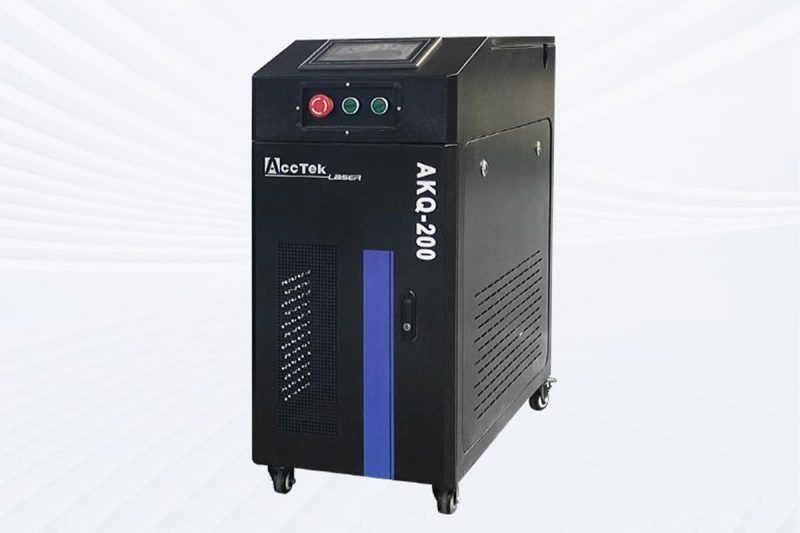
Zusammenfassung
Die gepulste Laserreinigungstechnologie mit ihren berührungslosen, hochpräzisen und umweltfreundlichen Vorteilen hat ein breites Anwendungspotenzial in der modernen Industrie bewiesen. Durch die präzise Steuerung von Laserparametern wie Pulsdauer, Energie und Wellenlänge sowie die Implementierung fortschrittlicher Überwachungs- und Feedbacksysteme kann diese Technologie Oberflächenverunreinigungen effektiv entfernen und gleichzeitig die Beschädigung des Substrats minimieren. Dies gewährleistet sowohl Effizienz als auch Sicherheit während des Reinigungsvorgangs. Erfolgreiche Anwendungen in High-End-Bereichen wie der Halbleiterindustrie, der Automobilindustrie, der Luft- und Raumfahrt und der Denkmalpflege bestätigen ihr enormes Potenzial und ihre technische Zuverlässigkeit.
Trotz der positiven Ergebnisse, die die gepulste Laserreinigungstechnologie in vielen Branchen erzielt hat, müssen Unternehmen bei der Einführung Faktoren wie Kosten, Betriebskomplexität und Materialverträglichkeit abwägen. Die Anfangsinvestition in Laserreinigungsgeräte ist relativ hoch, und die Bediener benötigen eine professionelle technische Schulung, um einen effizienten Betrieb des Systems zu gewährleisten. Darüber hinaus können bestimmte hochreflektierende oder transparente Materialien spezielle Laserwellenlängen und Parametereinstellungen erfordern. Daher müssen Unternehmen bei spezifischen Anwendungen eine umfassende Bewertung durchführen, um optimale Reinigungsergebnisse und minimale Substratschäden zu gewährleisten.
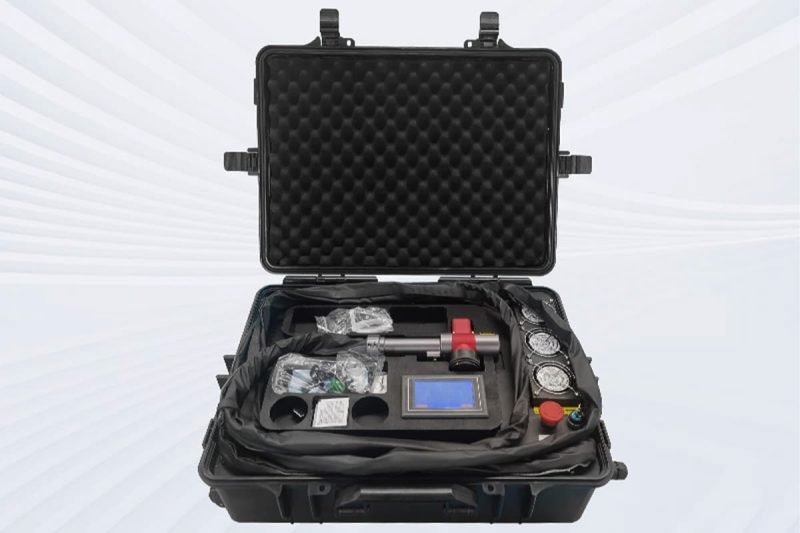
Erhalt der Laserlösung
Als führender Hersteller von Lasergeräten AccTek-Laser ist bestrebt, qualitativ hochwertige gepulste Laserreinigungsmaschinen Wir helfen unseren Kunden, effiziente und sichere Reinigungsergebnisse zu erzielen und verschiedene industrielle Reinigungsanforderungen zu erfüllen. Ob für die Reinigung von Präzisionselektronik, der Schwerindustrie oder des kulturellen Erbes – wir bieten unseren Kunden maßgeschneiderte Laserlösungen für die unterschiedlichsten Reinigungsherausforderungen.
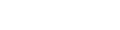
Kontaktinformationen
- [email protected]
- [email protected]
- +86-19963414011
- Nr. 3 Zone A, Industriegebiet Lunzhen, Stadt Yucheng, Provinz Shandong.
Holen Sie sich Laserlösungen