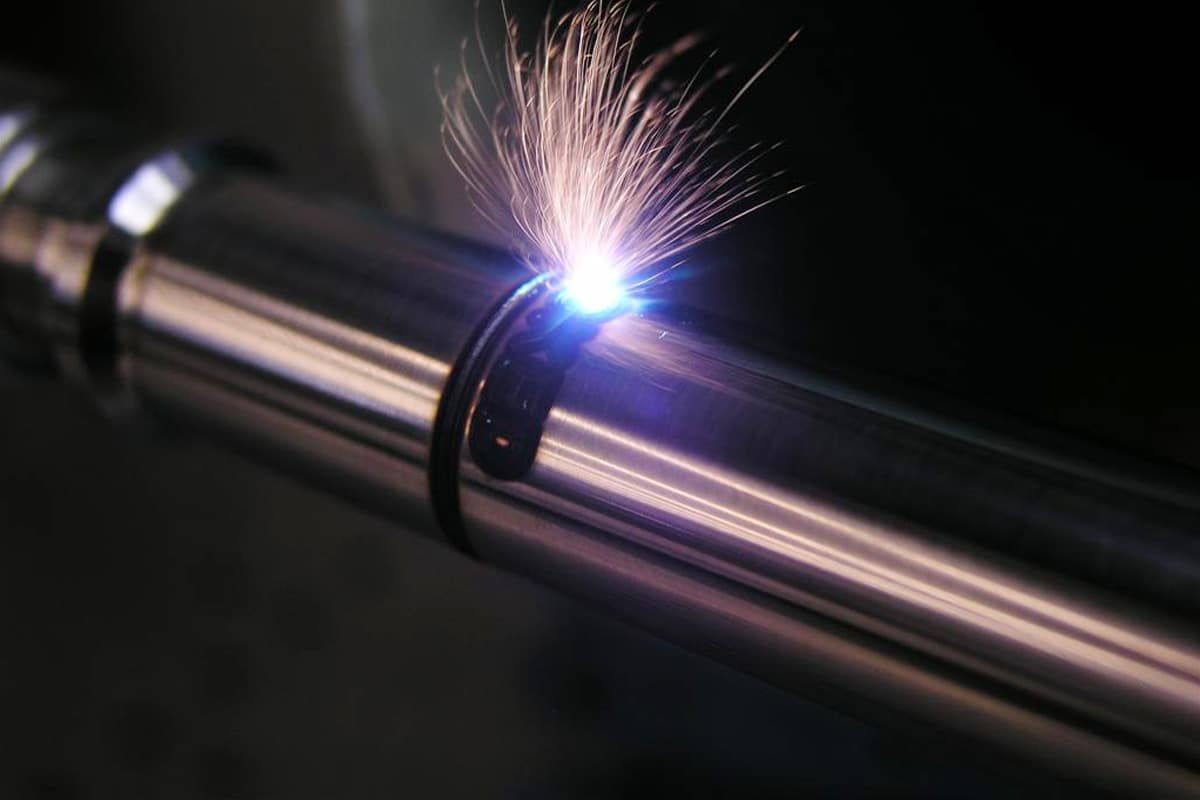
Design Considerations And Limitations Of Laser Marking
The wide application of laser marking technology has become an indispensable part of modern industrial production. However, despite its high degree of accuracy and flexibility in marking and engraving, in practical applications, designers need to carefully consider various factors to ensure the best results. From material selection to laser parameter adjustment, as well as safety considerations, they are all key factors that need to be paid attention to when designing laser marking. At the same time, laser marking technology also has some limitations, such as the unsuitability of specific materials and restrictions on surface treatment requirements.
This article will explore these design considerations and limitations and also include an overview of the fundamentals of laser marking technology, methods, and innovations to address these limitations to help readers better understand and apply laser marking technology.
Table of Contents
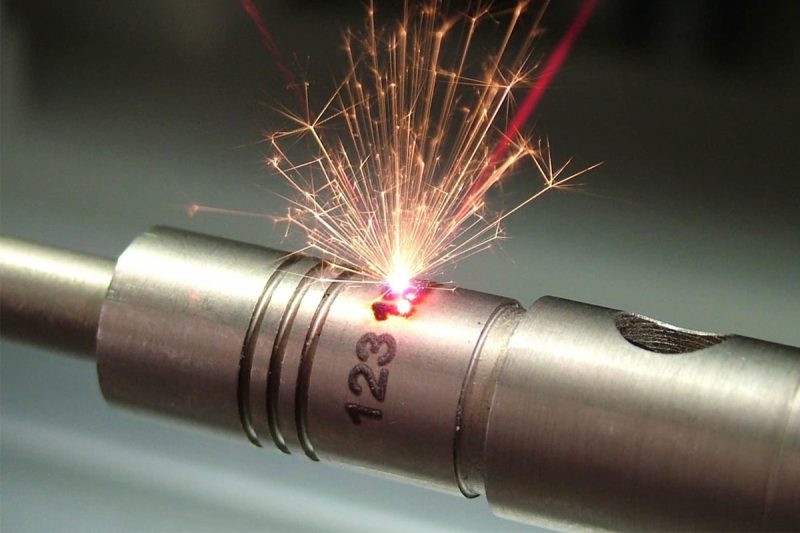
Basic Principles Of Laser Marking Technology
Laser marking technology is a processing method that uses laser beams to etch, mark, or cut the surface of materials. The basic principle is as follows:
- Laser generation: Laser marking systems usually use gas laser generators, solid laser generators, or semiconductor laser generators as laser sources. These laser generators produce highly focused laser beams.
- Focusing of the laser beam: Focusing the laser beam through optical elements such as lenses or mirrors to a very small focus to form a high energy density spot.
- The role of laser energy: When the laser beam irradiates the surface of the material, its high energy density will cause the material to locally heat, reach the temperature of melting or vaporization, and cause etching or evaporation.
- Material reaction: Different materials react differently to laser light. Metals usually have high absorptivity and are prone to evaporation or oxidation on the surface, while non-metallic materials may undergo thermochemical reactions or ablation.
- Control system: The laser marking system is equipped with a sophisticated control system, which can control the position, power, and movement path of the laser beam according to the design document to achieve precise marking or cutting.
- Marking effect: Laser marking can produce permanent, high-definition, and high-precision marks, which are suitable for processing various materials and complex patterns.
Through the above steps, laser marking technology achieves precise processing of material surfaces and is widely used in industrial production, medical equipment, and electronic equipment.
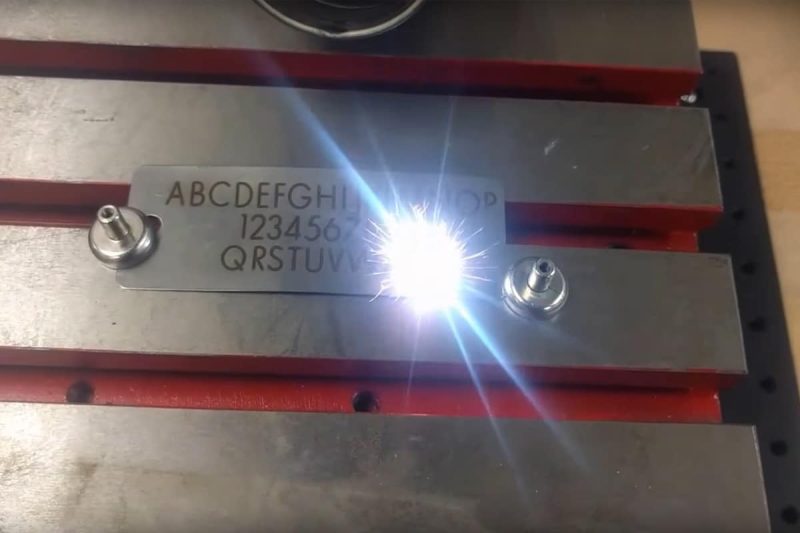
Specific Design Considerations In Laser Marking
Laser marking technology is a high-precision processing technology that is widely used in industrial production and other fields. However, when using laser marking technology, designers need to pay attention to some specific design considerations to ensure mark quality, safety, and efficiency. The following are specific design considerations in laser marking:
Material Selection And Compatibility
When selecting materials suitable for laser marking, the absorption and reflection properties of the material need to be considered. Some materials such as metals generally have high absorptivity and are suitable for laser marking. For some non-metallic materials (such as plastic or glass), which have higher reflectivity, higher-power lasers may be required to produce good results. In addition, some special materials such as organic materials may produce toxic gases during the laser marking process, so additional protective measures are required.
Adjustment Of Laser Parameters
The effect of laser marking is affected by laser parameters, including laser power, frequency, pulse width, and focal length. Appropriate adjustment of these parameters can achieve the best marking effect. Too low a power may result in unclear markings, while too high a power may cause the material to melt or be damaged. Adjustments to frequency and marking speed also affect final mark quality and speed.
Surface Treatment Requirements
Laser marking usually requires a certain temperature or chemical reaction on the material surface to achieve the marking effect. Therefore, before laser marking, the material surface needs to be properly treated, such as removing oil stains, oxide layers, or coatings, to ensure the best marking effect. In addition, for some materials, pre-treatment may be required, such as applying a special marking agent to enhance marking contrast.
Security Issues
The laser radiation produced by laser marking equipment is harmful to the human body and the environment, so safety regulations must be strictly followed when using laser marking equipment. Staff should receive professional training and use appropriate protective equipment, such as laser safety glasses and protective shields, to reduce the damage to the human body caused by laser radiation. In addition, laser marking equipment should be set up in a dedicated operating area and equipped with emergency stop buttons and safety warning signs to deal with unexpected events.
Design File Preparation
Before laser marking, the designer needs to prepare the design files and ensure that it is compatible with laser marking equipment. The correct design file format and parameter settings can ensure the quality and accuracy of the final mark. In addition, the patterns and text in the design document should have a certain size and proportion to ensure that they can be visible during the laser marking process.
Subsequent Processing And Inspection
After laser marking is completed, subsequent processing and inspection of the mark is usually required. Follow-up treatment may include cleaning and dusting, as well as applying a protective coating or surface treatment to the marking to enhance its durability. Inspection can be carried out through visual inspection or using equipment such as optical microscopes to ensure that the mark quality and accuracy meet the requirements.
To sum up, laser marking has important application value in industrial production, but designers need to pay attention to some specific design matters when using laser marking technology to ensure the final marking quality, safety, and efficiency. High-quality laser marking processing can be achieved through reasonable selection of materials, adjustment of laser parameters, surface treatment, strict compliance with safety regulations, and preparation of appropriate design documents.
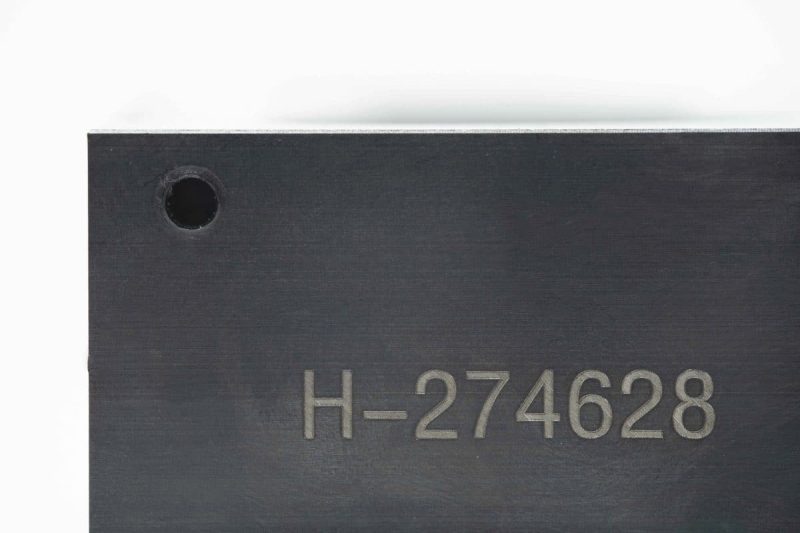
Specific Design Limitations In Laser Marking
The range of applicable materials for laser marking is subject to certain restrictions. Although laser marking is suitable for many common materials, such as metals, plastics, glass, and ceramics, for some special materials, such as certain high-reflectivity metals, transparent materials, or optical glass, the absorption and reflection of laser energy may not be sufficient. ideal, making it difficult to achieve clear marking effects.
Material Restrictions
The range of applicable materials for laser marking is subject to certain restrictions. Although laser marking is suitable for many common materials, such as metals, plastics, glass, and ceramics, for some special materials, such as certain high-reflectivity metals, transparent materials, or optical glass, the absorption and reflection of laser energy may not be sufficient. ideal, making it difficult to achieve clear marking effects.
Surface Treatment Requirements
Laser marking usually requires appropriate treatment of the material surface to ensure the marking effect. Certain material surfaces may require the removal of oxide layers, coatings, or other contaminants to enhance laser interaction with the material. However, surface treatments can increase production costs and complexity, especially in high-volume production.
Marking Size And Depth Limit
The size and depth of laser marking are limited. Because laser marks are labeled through local heating on the surface of the material, the depth of the mark is usually lighter, and it is difficult to achieve deep processing. In addition, the focus size and focus depth of the laser beam will also limit the minimum size and accuracy of the marked marker.
Complex Patterns And Details
Although laser marking can achieve high -precision marking effects, there may be certain limitations when processing complex patterns and details. For example, when processing patterns with tiny size or complex structures, laser marking may be limited by beam focusing and control accuracy, resulting in unsatisfactory labeling effects.
Production Efficiency Limit
Although laser marking is usually considered an efficient processing method, it may face production efficiency restrictions when dealing with large quantities. Laser marking speed is affected by factors such as laser power, material characteristics, and marking depth. Therefore, the relationship between the quality and production efficiency may be required in practical applications.
In summary, although laser marking technology has many advantages, there are some specific design and limitations in practical applications. Designers need to fully consider these limitations and take corresponding measures in the design and production process to maximize the advantages of laser marking technology and solve possible problems.
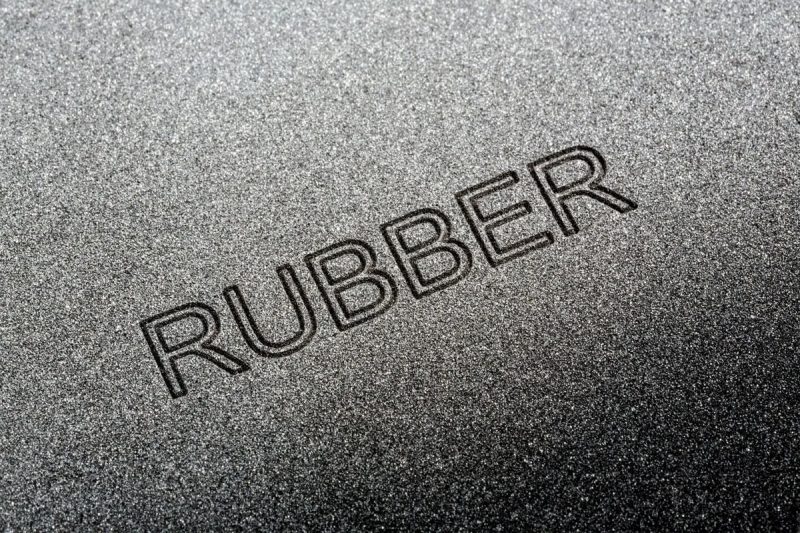
Solution And Innovation
For specific design precautions and limitations in laser marks, the following solutions and innovations can be adopted:
Material Adaptability Innovation
- Develop a new laser marking machine or additive to enhance the interaction between laser and specific materials and improve the marking effect.
- Explore the use of multi-wavelength laser systems to adapt to the absorption characteristics of different materials on the absorption of laser wavelengths, and expand the scope of materials for laser marking.
- Developing surface treatment technology, improving the absorption and reflection of the surface of the material, and improving the efficiency and accuracy of laser marks.
Laser Parameter Optimization Innovation
- Utilize advanced laser control technology to realize dynamic adjustment and optimization of laser parameters to adapt to different materials and marking requirements.
- Explore the use of deep learning and artificial intelligence technology to automatically optimize laser parameter settings and improve the efficiency and accuracy of laser marking.
- Develop multi-beam or composite laser systems to achieve simultaneous control of multiple parameters and improve the flexibility and diversity of laser marking.
Security Protection Innovation
- Design and use intelligent safety devices, such as laser beam monitoring systems and automatic emergency stop devices, to promptly detect and avoid hazards caused by laser radiation.
- Develop more efficient and comfortable laser safety protective equipment, such as more comfortable laser safety glasses and better breathable protective clothing.
- Develop stricter safety standards and operating procedures, strengthen training and supervision of laser marking operators, and improve workplace safety and environmental protection levels.
Mark Quality Optimization Innovation
- Develop high-power, high-stability laser devices, and optical systems to increase the energy density and stability of laser marking and improve marking quality and consistency.
- Optical imaging and three-dimensional scanning technology are used to realize real-time monitoring and feedback of the marking process, timely discover and correct problems in the marking process, and improve marking quality and accuracy.
- Explore the use of new laser marking technologies, such as femtosecond laser marking and ultra-fast laser processing, to achieve ultra-high precision and micro-nano-scale marking of specific materials.
Production Efficiency Improvement Innovation
- Design and apply intelligent laser marking systems to achieve automated production and efficient processing, improving production efficiency and cost-effectiveness.
- Use laser marking technology to achieve mass-customized production, adjust production parameters and marking patterns in real-time according to customer needs, and improve production flexibility and response speed.
- Develop integrated solutions for laser marking and other processing technologies, such as laser cutting and laser welding, to achieve multi-process joint processing and improve production efficiency and processing quality.
Through continuous innovation and improvement of laser marking technology and related equipment and processes, specific design considerations and limitations in laser marking can be effectively addressed, and the application scope, efficiency, and quality of laser marking can be improved.
Summarize
In the application of laser marking technology, certain design considerations and limitations need to be taken seriously. From material selection to laser parameter adjustment to safety considerations, these factors directly affect the effectiveness and safety of laser marking. Designers need to constantly seek methods and technological innovation to overcome these limitations and promote the development and application of laser marking technology. By deeply understanding the characteristics of laser marking technology and combining it with innovative solutions, we can further expand the application fields of laser marking and improve production efficiency and product quality.
Therefore, although laser marking has certain design considerations and limitations, as long as we continue to strive for innovation and improvement, laser marking technology will still become an important tool in modern industrial production, bringing more possibilities to all walks of life. and development opportunities. Need more information about laser marking and laser engraving processes? Contact the experts at AccTek Laser!
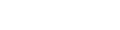
Contact information
- [email protected]
- [email protected]
- +86-19963414011
- No. 3 Zone A, Lunzhen Industrial Zone,Yucheng City , Shandong Province.
Get Laser Solutions