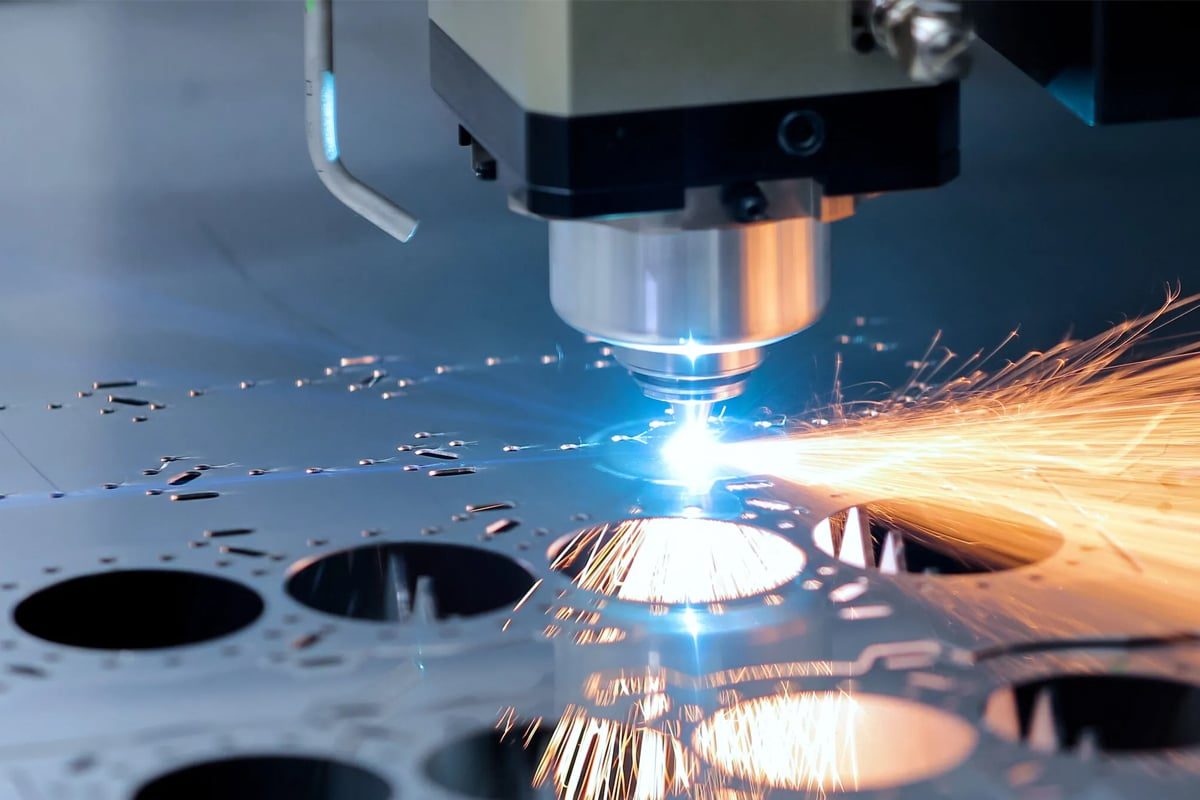
Challenges And Responses To Laser Cutting Technology
In today’s booming manufacturing industry, laser cutting technology has become an indispensable and important tool. Its high precision, high efficiency, and wide applicability make it widely used in metal processing, automobile manufacturing, aerospace, and other fields. However, just like any other technology, laser cutting technology comes with its own set of challenges and limitations. From material characteristics to equipment operating costs, from cutting speed to safety precautions, these challenges not only affect cutting quality and efficiency but also affect the continuous innovation and improvement of technology.
In the following articles, we will delve into the various challenges faced by laser-cutting technology and propose corresponding strategies to further promote the development and application of laser-cutting technology.
Table of Contents
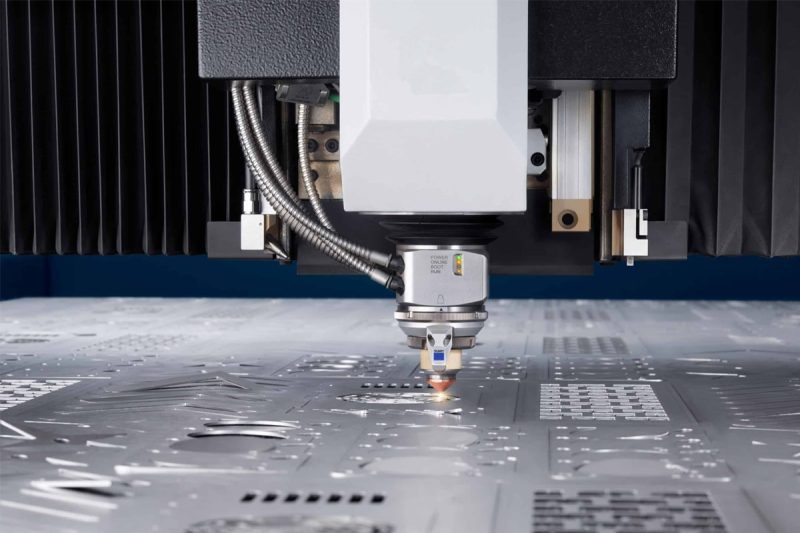
Basic Principles Of Laser Cutting Technology
Laser-cutting technology is a high-precision processing method. Its basic principle is to use laser beams to thermally process the surface of the workpiece. The high-energy-density laser beam locally heats the material to achieve cutting, engraving, or drilling of the material. Purpose. The basic principles of laser cutting technology can be briefly summarized as follows:
- Laser generator produces laser: The key component in the laser cutting system is the laser generator, which can produce high-energy, high-density, and high-monochromatic laser beams.
- Focused laser beam: By using optical elements such as lenses or mirrors, the laser beam is focused onto a small point on the surface of the workpiece to form a spot with high energy density.
- Material absorbs laser energy: The surface of the irradiated material absorbs the laser energy and converts it into heat energy.
- Material heating and melting: The high energy density of the laser beam causes the material to locally heat, eventually reaching the melting point or vaporization point of the material.
- Jet and airflow assistance: During the cutting process, airflow assistance is usually used to blow away the melted material and speed up the cutting process.
- Cut formation: As the laser beam moves across the surface of the workpiece, the material is cut into the desired shape or profile.
However, while laser cutting technology offers many advantages, it also faces some challenges and limitations, including limitations in material type and thickness. Therefore, in response to these challenges, continuous technological innovation and improvement are needed to improve the performance and scope of the application of laser cutting technology.
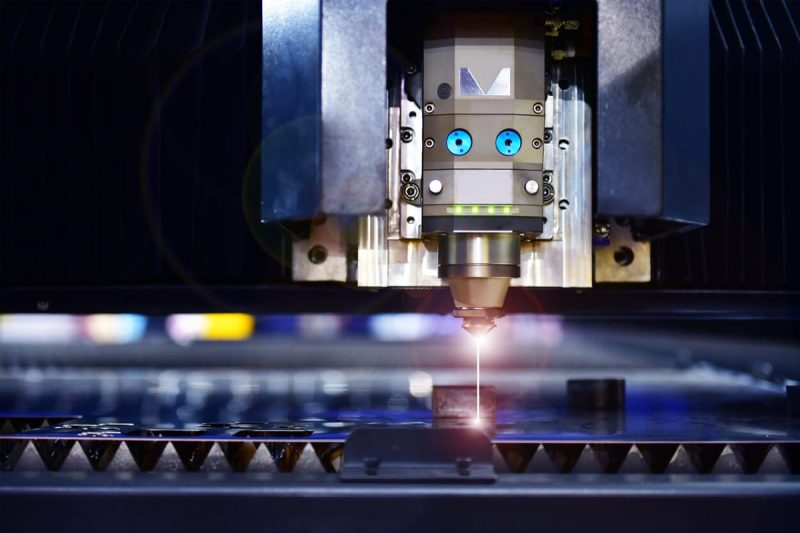
Existing Technical Limitations Of Laser Cutting
Laser-cutting technology is widely used in various fields, but there are also some technical limitations, which involve material and thickness limitations, cutting speed and energy efficiency, initial equipment cost and maintenance operation cost, edge quality and material deformation, line of sight restrictions, etc.
Material And Thickness Limitations
Laser-cutting technology has certain limitations when it comes to processing certain types of materials. For example, for transparent materials or materials with high reflectivity, laser energy is difficult to effectively penetrate or absorb, so good cutting effects cannot be achieved. In addition, the cutting of certain special alloys or composite materials may also be restricted. In addition, the thickness of different materials also has a great impact on laser cutting. Materials that are too thick or too thin may result in reduced cutting quality or even inability to complete the cutting task.
Cutting Speed And Energy Efficiency
The speed of laser cutting is usually limited by energy density and beam power. Increasing cutting speed often requires increasing laser power, which increases energy consumption. This results in reduced energy efficiency and increased processing costs. Therefore, while pursuing higher cutting speeds, energy efficiency and processing quality must be balanced to achieve economical and reasonable production costs.
Initial Equipment Cost And Maintenance Operation Cost
Laser-cutting equipment is relatively expensive to purchase, especially for larger equipment that requires a high-power laser source. In addition, the maintenance and operating costs of the equipment cannot be ignored, including laser generator maintenance, optical system cleaning and calibration, gas and cooling system operation, etc. These costs not only increase the production cost, but also require professional and technical personnel for maintenance and operation, so they also place certain requirements on the company’s capital and human resources.
Edge Quality And Material Deformation
During the laser cutting process, due to the thermal effect of the laser beam, a heat-affected zone may be generated, resulting in a decrease in the quality of the cutting edge, and even defects such as slag and burrs. At the same time, some materials will undergo thermal deformation under high temperatures, affecting processing accuracy and quality. These problems need to be solved by optimizing cutting parameters and controlling laser power and focal length.
Line Of Sight Restrictions And Safety Precautions
In some cases, laser cutting requires precise positioning and alignment of the material. However, the smoke, gas, and slag generated during the processing may affect the penetration and visibility of the laser beam, resulting in line-of-sight restrictions. In addition, the heat generated during laser cutting may also cause material deformation, further affecting processing quality and accuracy.
In general, although laser cutting technology has advantages in many aspects, it still faces many technical limitations. In response to these limitations, continuous technological innovation and improvement are needed to improve the performance and scope of the application of laser cutting technology and meet the processing needs of different industries.
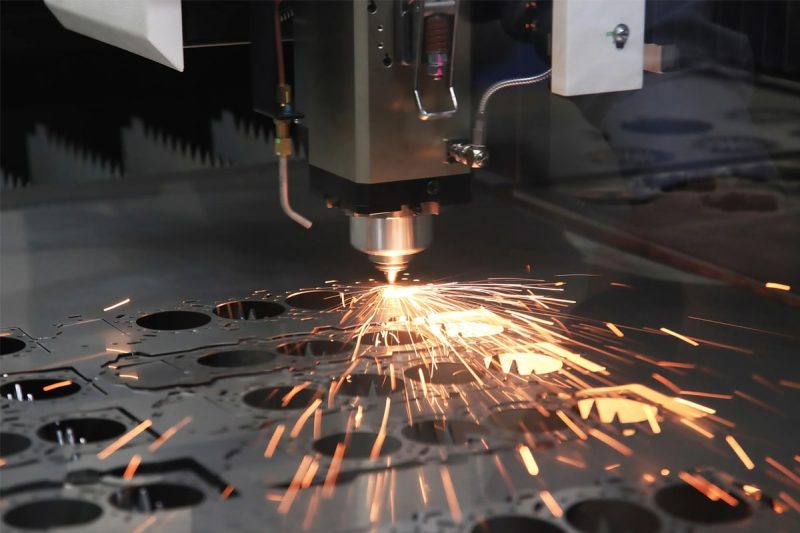
Strategies To Deal With Limitations Of Laser Cutting Technology
Given the various limitations of laser cutting technology, various strategies, and measures can be adopted to improve processing efficiency, reduce costs, and improve processing quality. Here are strategies for targeting the limitations of laser-cutting technology:
Material And Thickness Restrictions
- Technological improvement and adaptability improvement: Carry out continuous research and development and innovation of laser cutting technology, and develop processing techniques suitable for different types of materials based on their characteristics. For example, for transparent materials or materials with high reflectivity, laser parameters can be optimized or special processing methods can be used to improve the cutting effect.
- Multi-wavelength laser application: The use of multi-wavelength laser technology can better adapt to the characteristics of different materials, and improve the material’s absorption rate and processing efficiency, thereby expanding the applicable scope of laser cutting technology.
Cutting Speed And Energy Efficiency
- Laser power optimization: For materials of different thicknesses and types, by reasonably adjusting parameters such as laser power and focal length, the cutting speed and processing efficiency are optimized to achieve faster production speeds.
- Efficient optical system design: Optimize the design and adjustment of the optical system to reduce beam loss and scattering, and improve beam quality and energy density, thereby increasing cutting speed and energy utilization.
- Application of energy-saving technology: Promote energy-saving laser generators and optical components, adopt energy-saving cooling systems and gas supply systems, reduce energy consumption and operating costs, and improve energy efficiency.
Initial Equipment Cost And Maintenance Operating Cost
- Equipment performance optimization: Continuously improve the design and manufacturing process of laser cutting equipment, improve the stability, durability, and performance indicators of the equipment, and reduce initial equipment costs and operation and maintenance costs.
- Regular maintenance and upkeep: Establish a complete equipment maintenance and upkeep system, conduct regular equipment inspections, cleaning, and calibration, promptly discover and repair equipment faults, and extend the service life and stability of the equipment.
- Shared platform and outsourcing services: Use shared platforms or outsourcing services and adopt equipment leasing or sharing models to reduce enterprises’ equipment investment and operating costs and improve resource utilization efficiency.
Edge Quality And Material Deformation
- Optimize processing parameters: By adjusting parameters such as laser power, focal length, and cutting speed, the heat-affected zone and thermal deformation during the cutting process are optimized to improve cutting-edge quality and processing accuracy.
- Auxiliary processing technology: Combined with auxiliary processing technologies such as airflow assistance and liquid cooling, the heat-affected zone and material deformation are controlled to improve cutting quality and processing stability.
- Advanced optical system application: Introduce advanced optical systems and intelligent control technology to achieve precise control and adjustment of laser beams, improving processing accuracy and edge quality.
Line Of Sight Restrictions And Material Deformation
- Online monitoring and control: Introduce real-time monitoring and feedback control technology to monitor and control the entire cutting process, and promptly discover and adjust the line of sight restrictions and material deformation problems during the processing.
- Optical system optimization: Optimize the design and layout of the optical system, reduce the scattering and interference of the beam, improve the visibility and penetration of the laser beam, and improve the line of sight restriction problem.
- Automated positioning and alignment: Introduce automated positioning and alignment technology to improve the accuracy and stability of processing equipment and reduce the impact of manual intervention and line-of-sight restrictions on processing efficiency.
In summary, for the various restrictions of laser cutting technology, it can be cope with technological innovation, process optimization, equipment upgrades and intelligence to improve the cutting efficiency, quality and applicable range. With the continuous development and improvement of technology, it is believed that laser cutting technology will be widely used and developed in the future.
Summarize
In the development and application of laser cutting technology, we are undeniably faced with various challenges and limitations. From material selection and cutting speed to equipment cost and maintenance, every aspect poses challenges to the widespread application of laser-cutting technology. However, through technological innovation, process optimization, and equipment upgrading, we can effectively overcome these challenges. It is these challenges that prompt us to continue to innovate and improve, improve the applicability and competitiveness of laser cutting technology, and promote the progress of laser cutting technology.
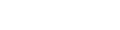
Contact information
- [email protected]
- [email protected]
- +86-19963414011
- No. 3 Zone A, Lunzhen Industrial Zone,Yucheng City , Shandong Province.
Get Laser Solutions