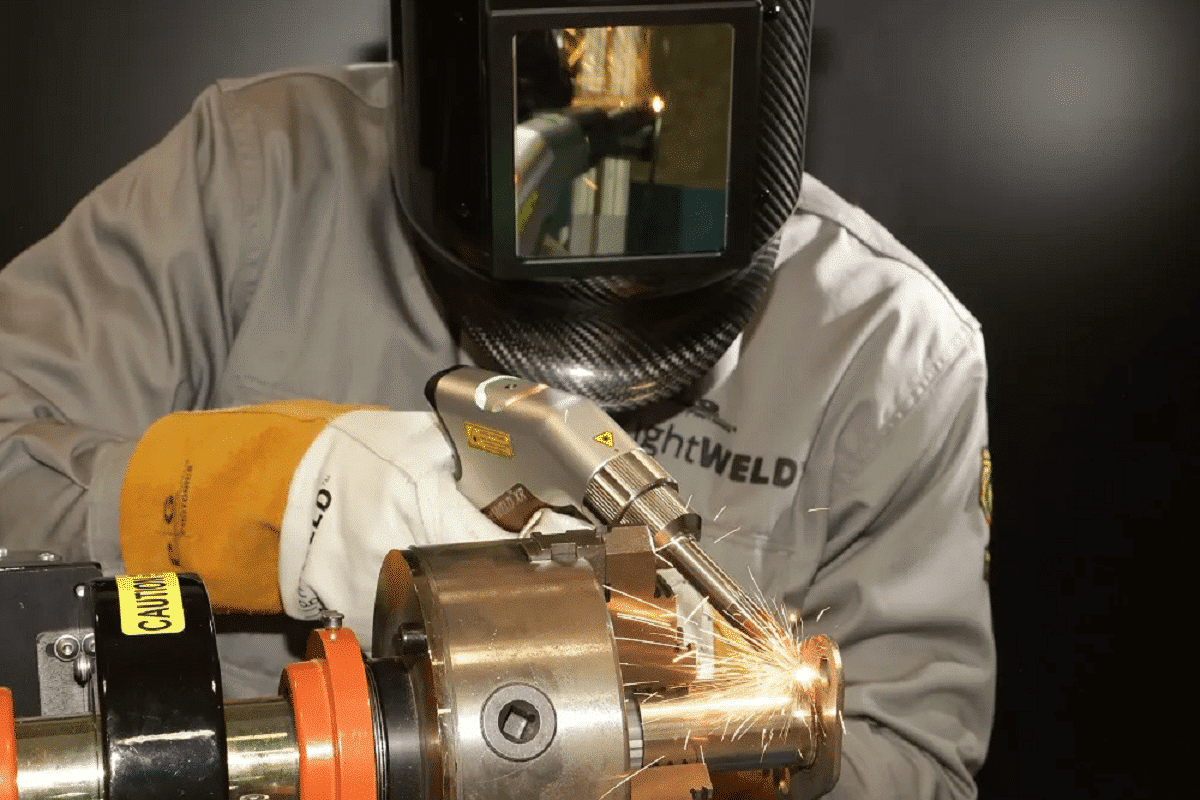
How to Choose a Laser Welding Machine?
Laser welding technology is rapidly gaining popularity in various industries due to its precision, efficiency, and versatility. Whether you are in manufacturing, automotive, aerospace, or any other industry that requires welding, choosing the right laser welder can help ensure project success.
In this article, we will guide you in choosing the perfect laser welding machine to meet your specific needs and preferences. We’ll cover a variety of factors including material type, thickness, application, machine type, power output, and more. Additionally, we will discuss the pros and cons of laser welding machines and provide an approximate price range to help you make an informed decision.
Table of Contents
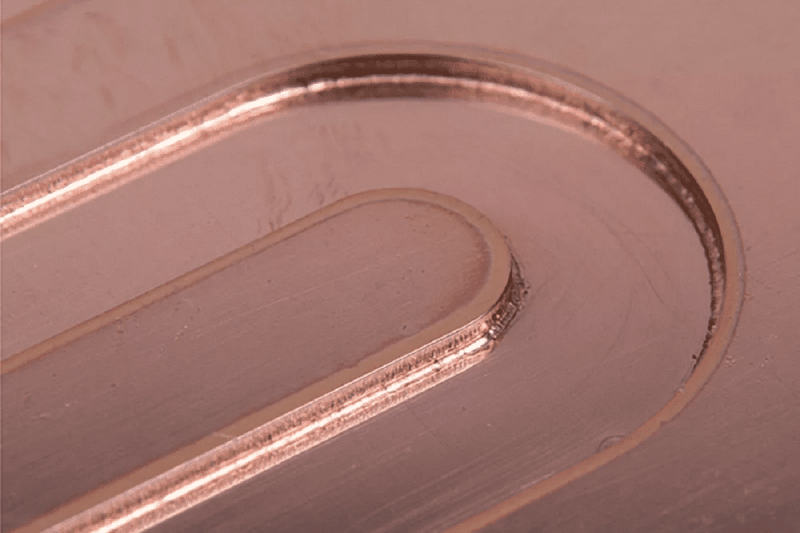
What is a laser welding machine?
Before we delve into the selection process, let’s first understand what a laser welding machine is. The laser welding machine is a highly specialized piece of equipment that uses a focused laser beam to melt and fuse materials together. It works by directing a high-intensity laser beam onto the surfaces to be joined, creating a precise and controlled heat source that creates strong, clean welds. Laser welding machines are used in a variety of industries and can perform tasks ranging from micro-welding on precision medical equipment to heavy-duty welding in the automotive and aerospace sectors.
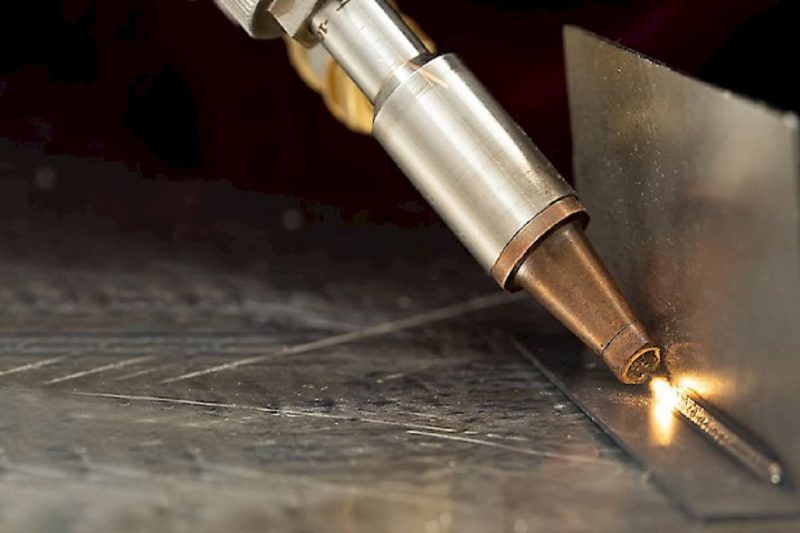
How to choose a laser welding machine?
Choosing the right laser welding machine helps achieve high-quality welding efficiently and effectively. Choosing a laser welding machine is a significant investment and a complex decision. To help you make an informed choice, here’s a detailed look at the various aspects you should consider when choosing a laser welding machine:
Material compatibility
The first thing you need to do is determine the material you need to weld. For example, fiber laser welding machines are mainly used to join metals, including steel, aluminum, copper, and their alloys. Make sure the machine you choose is compatible with the specific materials you will be using.
Material thickness
Consider the range of material thicknesses you will be working with as this will affect the laser power required. Different welding applications may require different power levels. Thicker materials generally require higher laser power for adequate penetration. The following is a reference for laser welding capabilities:
Laser Welding Capability Reference Table | |||||
---|---|---|---|---|---|
Material Type | Thickness | 1000W Laser Welding Speed | 1500W Laser Welding Speed | 2000W Laser Welding Speed | 3000W Laser Welding Speed |
Carbon Steel (Q235B) | 0.5mm | 70~80mm/s | 80~90mm/s | 90~100mm/s | 100~110mm/s |
1mm | 50~60mm/s | 70~80mm/s | 80~90mm/s | 90~100mm/s | |
1.5mm | 30~40mm/s | 50~60mm/s | 60~70mm/s | 70~80mm/s | |
2mm | 20~30mm/s | 30~40mm/s | 40~50mm/s | 60~70mm/s | |
3mm | / | 20~30mm/s | 30~40mm/s | 50~60mm/s | |
4mm | / | 15~20mm/s | 20~30mm/s | 40~50mm/s | |
5mm | / | / | / | 30~40mm/s | |
6mm | / | / | / | 20~30mm/s | |
Stainless Steel (SUS304) | 0.5mm | 80~90mm/s | 90~100mm/s | 100~110mm/s | 110~120mm/s |
1mm | 60~70mm/s | 80~90mm/s | 90~100mm/s | 100~110mm/s | |
1.5mm | 40~50mm/s | 60~70mm/s | 60~70mm/s | 90~100mm/s | |
2mm | 30~40mm/s | 40~50mm/s | 50~60mm/s | 80~90mm/s | |
3mm | / | 30~40mm/s | 40~50mm/s | 70~80mm/s | |
4mm | / | 20~30mm/s | 30~40mm/s | 60~70mm/s | |
5mm | / | / | / | 40~50mm/s | |
6mm | / | / | / | 30~40mm/s | |
Brass | 0.5mm | 55~65mm/s | 70~80mm/s | 80~90mm/s | 90~100mm/s |
1mm | 40~55mm/s | 50~60mm/s | 60~70mm/s | 80~90mm/s | |
1.5mm | 20~30mm/s | 40~50mm/s | 50~60mm/s | 70~80mm/s | |
2mm | / | 20~30mm/s | 30~40mm/s | 60~70mm/s | |
3mm | / | / | 20~30mm/s | 50~60mm/s | |
4mm | / | / | / | 30~40mm/s | |
5mm | / | / | / | 20~30mm/s | |
1-3 Series Aluminum Alloys | 0.5mm | 70~80mm/s | 80~90mm/s | 90~100mm/s | 100~110mm/s |
1mm | 50~60mm/s | 70~80mm/s | 80~90mm/s | 90~100mm/s | |
1.5mm | 30~40mm/s | 50~60mm/s | 70~80mm/s | 80~90mm/s | |
2mm | 20~30mm/s | 30~40mm/s | 40~50mm/s | 70~80mm/s | |
3mm | / | 10~20mm/s | 20~30mm/s | 40~50mm/s | |
4mm | / | / | / | 20~30mm/s | |
4-7 Series Aluminum Alloys | 0.5mm | 45~55mm/s | 60~65mm/s | 70~80mm/s | 80~90mm/s |
1mm | 35~45mm/s | 40~50mm/s | 60~70mm/s | 70~80mm/s | |
1.5mm | 20~30mm/s | 30~40mm/s | 40~50mm/s | 60~70mm/s | |
2mm | / | 20~30mm/s | 30~40mm/s | 40~50mm/s | |
3mm | / | / | / | 30~40mm/s |
Note:
- In the welding data, the core diameter of the 1000w-3000w laser output fiber is 50 microns.
- This welding data adopts a Raytools welding head (swing welding head is used for copper welding), and the optical ratio is 100/200 (collimation/focus lens focal length).
- Welding shielding gas: Argon (purity 99.99%).
- Due to the differences in equipment configuration and welding process used by different customers, this data is for reference only.
Welding applications
Determine your welding application as this will affect the configuration and functionality of the machine. Common welding applications include spot welding, seam welding, and 3D welding, as well as more specialized tasks such as remote laser welding. Different applications may have unique requirements, such as specialized beam delivery systems and automation capabilities.
Laser welding machine selection
Choose the right machine based on your specific welding application. The following is a brief introduction to some laser welding machines:
- Automated laser welding robots: Automated welding robots are ideal for mass production and can provide high precision and welding consistency, making them suitable for industries such as automotive and electronics.
- 3D 5-axis laser welding machine: This machine is very versatile and can handle complex welding tasks with ease. It is typically used in welding applications that require coordinated motion in multiple axes.
- Handheld laser welding machine: The flexibility and portability of handheld devices make them ideal for small projects and repair jobs.
Power and energy output
Calculate the required laser power based on material thickness, welding speed, and penetration depth, and select a machine with appropriate power output. Generally, higher-power laser generators can weld thicker materials and provide faster welding speeds.
Pulse duration and frequency
Pulse duration and frequency settings allow you to easily control the quality and efficiency of your welding process. Short pulses are ideal for minimizing the heat-affected zone and achieving precise, high-quality welding results. While longer pulses may be suitable for deeper penetration.
Beam delivery system
Choose between fixed optics and galvanometer-based scanning systems. Galvanometer systems provide flexibility for welding complex geometries, allow for rapid beam positioning, and can be advantageous for certain applications. Also, make sure the machine can cut the necessary beam diameter to achieve the welding results you want.
Cooling system
Make sure the machine is equipped with an efficient cooling system and that it can operate efficiently and reliably. A well-designed cooling system helps maintain the stable operation of the laser generator and prolongs its service life.
Ease of use and user interface
User-friendliness is important, especially for operators with different experience levels. Users evaluate the machine, including its control interface and software. The intuitive interface simplifies setup, programming, and operation, shortening the operator learning curve and helping to achieve consistent and accurate welds.
Maintenance and service
Consider maintenance ease and accessibility of key components of the equipment. Ask about service and support options offered by the manufacturer or dealer, including maintenance contracts and technical assistance. AccTek Laser As a leading laser welding machine manufacturer, we provide comprehensive maintenance and service. Our expert technicians provide excellent customer support. Your satisfaction is our top priority.
Security features
Safety should always be a top priority, verify that machines have basic safety features such as interlocks, housing systems, and emergency stop mechanisms. These features protect the operator and prevent accidents.
Budget and ROI
Create a comprehensive budget that considers the initial purchase price, operating costs (including power consumption), and potential return on investment over the machine’s lifetime. Consider long-term cost savings through increased productivity and productivity.
Brand and manufacturer reputation
Research the manufacturer’s reputation and track record. Well-known and reputable companies generally offer better quality, reliability, and customer support. Customer reviews and industry reputation can provide valuable insights. AccTek Laser is synonymous with excellence in laser welding technology. With a reputation built over the years for delivering cutting-edge technology and exceptional customer satisfaction, we will be your partner of choice for precision laser welding solutions.
Warranty and support
Check the warranty and after-sales support provided by the manufacturer. A comprehensive warranty and responsive customer support give you peace of mind. Your peace of mind matters to us. With our laser welding machines, you receive not only cutting-edge technology but also complete warranty coverage and unwavering customer support. We’re here to ensure your satisfaction and success, offering dependable service and assistance whenever you need it.
Demonstration and testing
Request a demo and perform welding tests with the machine to evaluate its performance in real-life welding scenarios. This allows you to verify that the machine meets your specific welding needs. AccTek Laser provides free demonstration and testing services. You can experience the powerful performance and precision of our laser welding machines first-hand through our demonstration and testing services. We invite you to witness the unparalleled capabilities of our technology and ensure it’s exactly what you need before you commit.
Seek expert advice
If you are unsure about some technical aspects or features, you can consult an expert or engineer with experience in laser welding machines. Their insights can provide valuable guidance in making the right decisions. At AccTek Laser, we don’t just sell machines, we provide expertise. Our dedicated team of experts is on hand to provide you with personalized advice and guide you to the ideal laser welding solution for your unique needs. Trust our knowledge and experience to improve your welding capabilities and achieve outstanding results.
By thoroughly considering every aspect and conducting extensive research, you can choose a laser welding machine that perfectly matches your welding requirements, budget constraints, and long-term goals. Making smart choices will help improve welding quality, productivity, and operational cost-effectiveness.
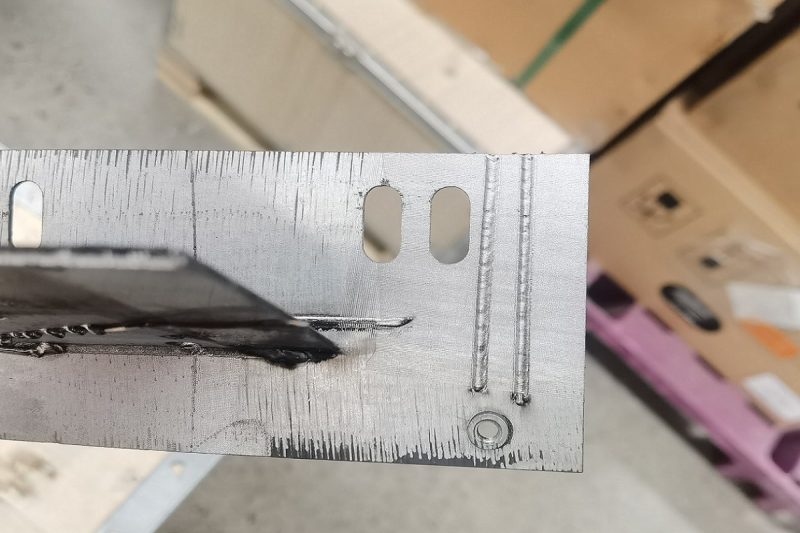
Advantages and disadvantages of laser welding machines
Now that we’ve delved into the selection process, let’s take a look at the advantages and disadvantages of laser welding machines so you can determine if a laser welding machine is right for your specific application and requirements. The following is an analysis of the advantages and disadvantages of laser welding machines:
Advantages of laser welding machine
- Precision and quality: Laser welding provides superior precision and accuracy to create fine, complex welds and minimize the heat-affected zone (HAZ). This accuracy is ideal for applications requiring tight tolerances.
- Minimal distortion: Compared to traditional welding methods such as arc welding, laser welding produces minimal distortion in the workpiece, reducing the need for post-weld corrections or additional processing. This is particularly useful when working with thin or heat-sensitive materials.
- High-speed welding: Laser welding is known for its high welding speed, making it suitable for mass production and high-volume manufacturing. It can significantly increase productivity compared to other welding processes.
- Versatility: Laser welding can be used on a variety of metal materials, including stainless steel, carbon steel, copper, brass, aluminum, and more. Due to its adaptability, it is suitable for various industries including automotive, aerospace, electronics, and medical devices.
- Reduced material waste: Laser welding minimizes material waste because it focuses energy exactly where it’s needed and produces cleaner, narrower welds. This efficiency can lead to cost savings over time.
- Non-contact welding process: Laser welding is a non-contact process, which means there is no physical contact between the welding tool and the workpiece, reducing the risk of contamination and damage to sensitive components. This is advantageous for delicate or sensitive materials that cannot withstand traditional welding methods.
- Remote operation: The laser welding machine can be operated remotely, allowing operators to weld in dangerous or hard-to-reach areas, improving operator safety.
- Automation compatibility: Laser welding can be easily integrated into automated manufacturing processes, increasing welding efficiency and consistency and reducing the need for manual labor.
- Joining dissimilar materials: Laser welding can successfully join dissimilar materials with different melting points and thermal properties, expanding its application range.
Disadvantages of laser welding machine
- High initial investment: Compared with traditional welding equipment, the purchase cost of laser welding machines is relatively high, which may become a barrier to entry for some companies.
- Professional training: Operating a laser welding machine requires specialized training and expertise. Operators need to understand laser safety protocols and how to optimize machine settings for different materials and applications, which can result in additional costs.
- Reflective materials: Laser welding can be less effective on highly reflective materials such as copper or aluminum because these materials tend to reflect the laser beam rather than absorb it.
- Maintenance costs: Laser welding machines require regular maintenance to ensure optimal performance. Maintenance costs, including the replacement of consumable parts such as nozzles and optics, add up over time.
- Environmental considerations: Laser welding produces fumes and emissions that need to be properly managed. Depending on the materials being welded, ventilation or filtration systems may be required to maintain a safe working environment.
- Limited penetration depth: While laser welding is great for many applications, it may not be the best choice for deep penetration welding of thick materials. In this case, other welding methods, such as electron beam welding or arc welding, may be more suitable for such tasks.
- Initial setup time: Laser welding is sensitive to changes in material thickness, so setting up a laser welding machine for a specific application may require time and adjustments to achieve optimal parameters.
- Power consumption: Laser welding machines consume a lot of power when welding, which can lead to high operating costs.
Laser welding machines offer many advantages, including accuracy, speed, and versatility, but they also have some disadvantages, such as initial investment, operator training requirements, and limitations when working with certain materials. Evaluating your specific welding needs and understanding these advantages and disadvantages can help you determine whether laser welding is the right choice for your application.
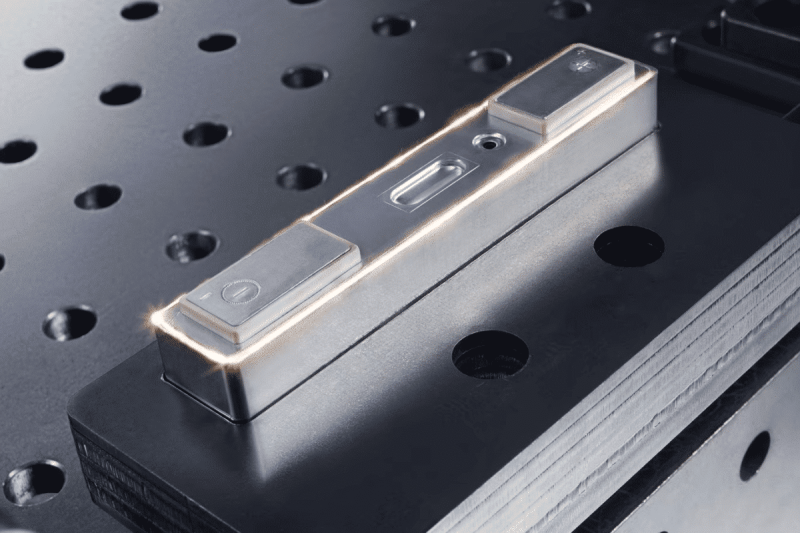
How much does a laser welding machine cost?
Let’s take a look at the price range of laser welding machines to help you make a better decision. Here’s a detailed breakdown of the approximate price ranges for different types of laser welding machines, including handheld, 3D 5-axis, and laser welding robots:
Handheld laser welding machine
- Price range: $6,000 to $30,000
- Handheld laser welding machines are the most affordable of the three options. It is designed for portability and versatility for smaller applications, repairs, and fieldwork. These machines typically use manual controls for welding. Prices may vary based on power output and additional features such as integrated cooling systems or ergonomics.
3D 5-axis laser welding machine
- Price range: $15,000 to $60,000
- 3D 5-axis laser welding machines are more advanced and versatile than handheld devices. It is capable of welding complex geometries and is commonly used for intricate work in industries such as aerospace and automotive. These machines offer greater precision and can steer the laser beam in multiple directions to reach hard-to-reach areas. Prices vary widely depending on the size, features, and brand of the machine.
Laser welding robot
- Price range: $30,000 to $300,000
- Automated laser welding robots are the most advanced and expensive option in laser welding. These systems integrate industrial robots with laser welding technology to provide unparalleled flexibility and automation capabilities. Automated systems are commonly used in high-volume production lines and in industries such as automotive manufacturing, aerospace, and electronics. The price range for automated laser welding systems can vary greatly depending on factors such as robot brand, laser generator, and customization options.
Summarize
Choosing the right laser welding machine is a critical decision that can significantly impact your productivity and weld quality. By carefully considering factors such as material type, application, machine type, power, and budget, you can make an informed choice. Additionally, understanding the pros, cons, and price range of laser welding machines will help you choose the perfect tool for your specific needs. Ultimately, investing in the right laser welding machine can increase the efficiency and long-term success of your industry.
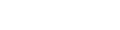
Contact information
- [email protected]
- [email protected]
- +86-19963414011
- No. 3 Zone A, Lunzhen Industrial Zone,Yucheng City , Shandong Province.
Get Laser Solutions