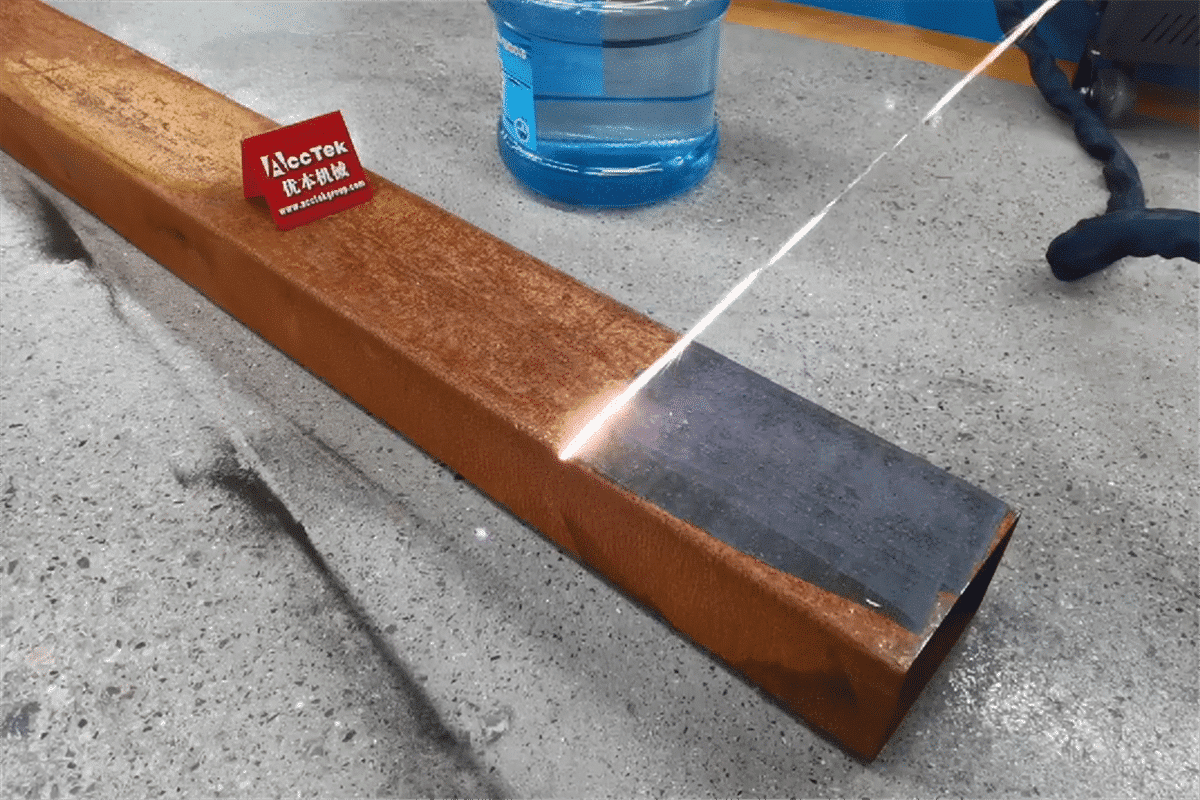
Laser Rust Removal VS Traditional Rust Removal
Laser welding is a high-precision welding method that uses a laser beam to melt the material of the workpiece and then forms a weld after cooling. In laser welding, gas plays a key role. The protective gas not only affects the welding seam formation, welding seam quality, welding seam penetration, and penetration width but also directly affects the quality and efficiency of laser welding. What gases are needed for laser welding? This article will take an in-depth look at the importance of laser welding gases, the gases used, and what they do.
Table of Contents
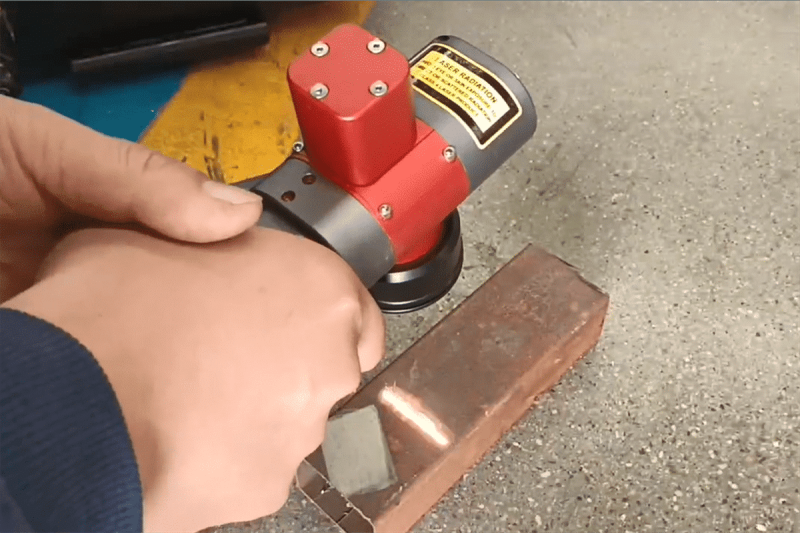
What is laser rust removal?
Laser rust removal is a non-contact cleaning process that uses a laser beam to remove rust and oxides from various metal surfaces. The concept of laser rust removal dates back to the 1980s when lasers were first used to clean delicate surfaces in the aerospace industry. Since then, laser cleaning technology has continued to be refined and used in a variety of industrial and commercial applications. In recent years, laser rust removal machines have become widely popular due to their efficient cleaning ability and non-damage to the substrate.
The working principle of laser rust removal is to emit high-power laser beams to the surface of metal materials. Here, the laser beam interacts with the rust on the material’s surface, which absorbs energy and rapidly raises its temperature until it reaches its ablation threshold, the point at which molecular bonds break. This causes rust particles to be ejected from the substrate, or the rust layer to completely vaporize.
The parameters of the laser rust remover (i.e. power, wavelength, repetition rate, scanning speed, and beam diameter) are carefully selected so that only the ablation threshold of the rust layer is reached and not that of the substrate itself. This targeting of the correct ablation threshold, combined with the fact that laser rust removal can be controlled with micron-level precision, ensures that the underlying substrate is not damaged or is damaged very little. The process of scanning the laser beam is repeated until all rust is removed and the metal surface is clean.
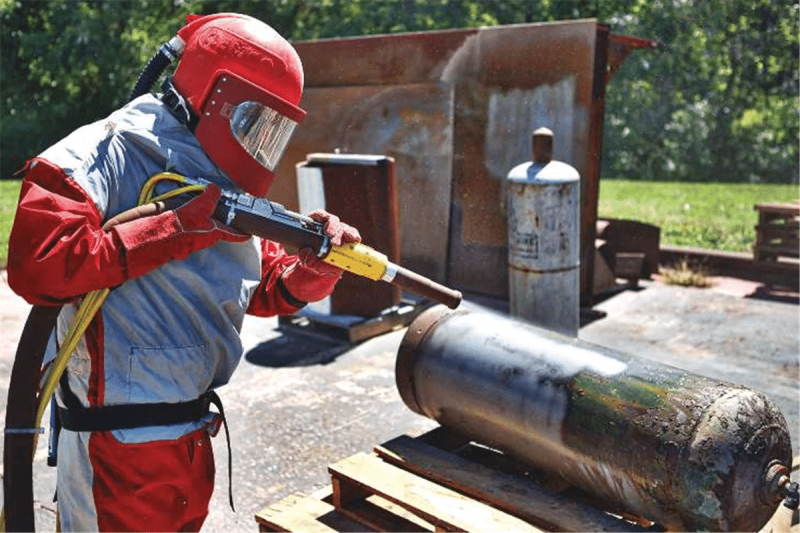
What are the common traditional rust removal methods?
Before laser rust removal appeared or was not widely used, the following traditional rust removal methods were widely used in the field of metal cleaning:
Sandblasting rust removal
Sandblasting uses high pressure to push the medium flow, and sprays angular, hard sand and gravel at high speed through the nozzle onto the metal surface to forcefully remove contaminants on the surface of the object. The most common medium of this kind is a sand mixture, including copper ore sand, quartz sand, emery, iron sand, etc. The advantage of sandblasting is that it is most effective on very large rusted areas and can remove rust from metal surfaces faster than other cleaning methods. In addition, sandblasting can clean thicker rusty substrates. Because sandblasting uses high pressure to force the removal of contaminants, it can effectively blast through thicker layers of rust, removing it from the substrate.
Dry ice blast rust removal
Dry ice blasting is also called cold blasting. Its rust removal method has similar characteristics to sandblasting. The medium it uses is solid carbon dioxide. The principle of dry ice rust removal is to use the physical properties of dry ice to sublimate and absorb heat. When dry ice particles are sprayed onto the surface of rust spots, an instantaneous high-temperature and low-temperature reaction will occur, destroying the connection between rust and metal surfaces, and generating strong explosive force. This will peel off the rust. At the same time, dry ice cleaning will also spray dry ice onto the rust surface through high-pressure airflow to isolate the rust particles from each other and prevent rust from re-growing. The advantage of dry ice cleaning is that it does not leave any residue during the rust removal process and is more environmentally friendly.
Chemical rust removal
Chemical rust removal uses pickling to chemically react with rust to dissolve the rust and oxide layer on the metal surface to achieve the purpose of rust removal. Commonly used cleaning media for this method include sulfuric acid, hydrochloric acid, nitric acid, phosphoric acid, hydrofluoric acid, amino sulfuric acid, etc., so it is also called pickling. For rust removal of large steel structures, sulfuric acid and hydrochloric acid are mainly used. This strong acid cleaning efficiency is high, fast, and cheap. For mechanical workpieces or fine parts, phosphoric acid is mainly used to prevent excessive corrosion and reduce damage to the surface of the workpiece.
Mechanical rust removal
Mechanical rust removal is a method that uses mechanical power to remove rust through friction. Common mechanical rust removal tools include grinding wheels, sandpaper, grinding wheels, etc. These tools can be operated manually or electrically. By mechanically grinding the rust layer on the metal surface, they can effectively remove the rust on the surface. Mechanical rust removal is a simple and effective rust removal method, but it can only remove rust on the metal surface and has no obvious effect on deep-seated rust.
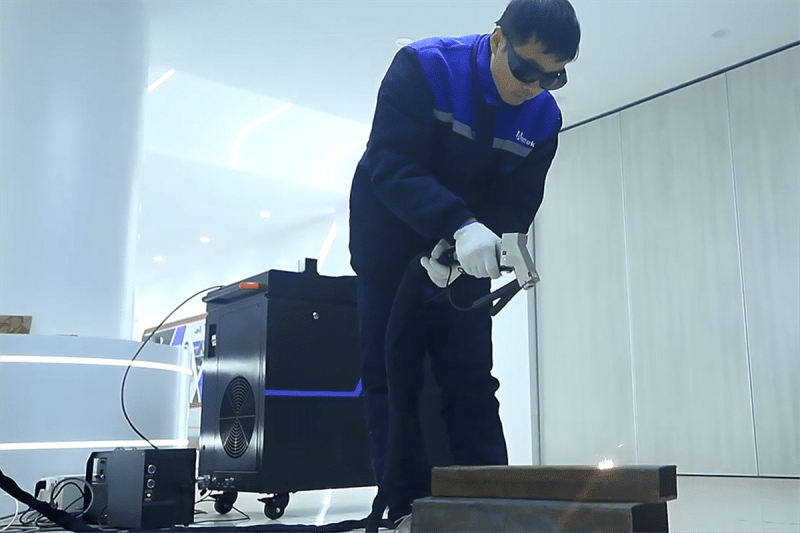
Laser rust removal VS traditional rust removal
Laser rust removal has been welcomed by many companies since its emergence because it has advantages over traditional rust removal in many aspects. Here, we compare laser rust removal with traditional rust removal. The following is a detailed analysis of various rust removal methods:
Cleaning effect and impact on the metal surface
- Sandblasting and rust removal can remove thicker rusty base materials. However, since this method relies on the impact and friction of the edges and corners of sand grains to remove rust and oxide scale on the metal surface, the surface of the material after sandblasting and rust removal will be Very rough. This will cause great damage to the metal surface and is not conducive to long-term use.
- Dry ice cleaning can remove rust to a certain extent without scratching or damaging the surface of the substrate, but the removal effect is affected by factors such as the type and thickness of the rust. It has a good cleaning effect on metal surfaces with thin rust layers but cannot clean deep and heavy rust well.
- The effect of mechanical rust removal is similar to that of sandblasting. Since rust removal relies on mechanical friction, the surface of the base material will be very rough. In addition, mechanical rust removal is not effective for deep-seated rust.
- When using chemicals to remove rust, different pickling solutions have different effects. The strong acid rust removal effect is obvious, but it is prone to excessive corrosion of the base material’s surface. If the cleaning is incomplete, the remaining acid will cause rust to return.
- Laser cleaning has good effects on rust removal of precision parts and large steel structures. There are currently two types of laser cleaning: pulse laser cleaning and continuous laser cleaning. Pulse laser rust removal can better control the heat input while cleaning the rust layer on the surface of the material while preventing micro-dissolution caused by the excessive temperature of the base material, and the cleaning effect is good. This method is usually used in precision instruments, medical equipment, molds, and other applications that require no damage to the surface of the substrate. The maximum power of continuous laser cleaning can reach 3000W. This high-power laser cleaning method is usually used in application scenarios of large heat sinks such as automobiles, pipelines, and large steel structures. Continuous laser cleaning has a good cleaning effect on very large rusty areas or thick rusty substrates, and due to the non-contact cleaning method, there is no rough surface on the substrate like sandblasting and mechanical rust removal.
Machine operating costs
- Sandblasting and rust removal require the use of a large amount of spray media, which results in large consumption and high cost.
- Dry ice rust removal requires the use of dry ice as the cleaning medium. On the one hand, the cost of dry ice itself is high; on the other hand, due to the particularity of dry ice, its transportation and storage costs are much higher than other media.
- Chemical rust removal requires the use of a large amount of acid to clean the substrate, which also has a large consumption, long-term use, and high operating costs.
- Mechanical rust removal uses grinding wheels, sandpaper, grinding wheels and other tools to remove rust. Compared with the above three rust removal methods, the cost is much lower, but it still has high losses and needs to be replaced in time after the tools are worn.
- Laser rust removal does not require cleaning media and can be used when powered on. It only consumes a small amount of electrical energy and has low operating costs. Using a laser cleaning machine also requires regular replacement of protective lenses according to usage conditions, but these consumables have a very low cost compared to the losses of other rust removal methods.
Safety precautions
- When sandblasting and rust removal, operators need to wear strict protective clothing, including a tight helmet, to protect themselves from the hazards of the spray material.
- Dry ice rust removal will cause the accumulation of a large amount of CO2, so a well-ventilated space is required, otherwise it will be dangerous to the operator. Additionally, when using dry ice blasting for rust removal, operators are required to wear multiple layers of protection, including gloves, cotton clothing, and earmuffs to ensure their warmth and safety.
- When chemical rust is removed, the operator needs to wear acid-resistant protective clothing to avoid burns due to acid splashing on the skin during the operation. In addition, the process of chemical rust removal will produce acidic gases. To reduce the corrosion of acidic gases on equipment and harm to the human body, the rust removal site should have good ventilation equipment.
- Mechanical rust removal, whether hand-held or using power tools, is a highly labor-intensive method of rust removal. This rust removal method is simple to operate, but it requires a lot of physical strength. The operator should pay attention to rest and cannot work for a long time to avoid causing damage to the body.
- Laser rust removal is an easier and safer way to remove rust. There is no flying debris during the entire cleaning process. The operator does not need to wear heavy protective clothing. He only needs to wear laser-protective glasses to directly start the metal rust removal work. Moreover, there are no special ventilation requirements for fiber laser rust removal. You only need to ensure that there is a ventilation distance of more than 20cm from the front and rear of the fuselage. This is to ensure that the machine can dissipate heat normally. Although laser cleaning is safer, you should still be careful not to point the laser cleaning head at people and eyes during the rust removal process.
Environmental impact
- On the one hand, sandblasting and rust removal equipment will produce noise, and measures need to be taken to reduce the noise to reduce the impact of noise on workers and the environment; on the other hand, the sandblasting and rust removal process will produce a large amount of dust, causing pollution and harm to the environment. Corresponding measures need to be taken for protection. After sandblasting and rust removal, the used sand and gravel need to be cleaned.
- Dry ice cleaning technology does not leave any residue during the rust removal process and is a more environmentally friendly method of rust removal.
- When chemical agents are used to remove rust, the waste liquid after pickling seriously pollutes the environment and needs to be treated before being discharged. The waste liquid after cleaning needs to be processed by the requirements of the Environmental Protection Law and must not be discharged to the outside at will.
- Laser rust removal is a new environmentally friendly cleaning process. Since the cleaning process does not use cleaning media such as chemicals, it does not produce pollutants and is more environmentally friendly.
Summarize
Laser cleaning has proven to be an effective and safe method of maintaining metal surfaces and extending their service life. As a highly advanced rust removal tool, laser cleaning machines are beginning to gradually replace traditional cleaning processes because they can remove rust more accurately and reduce the additional capital required, resulting in lower overall costs. Laser rust removal is also the most effective process for reducing environmental harm. Its emergence has revolutionized metal surface cleaning methods and is becoming more and more popular in industrial cleaning.
At AccTek Laser, we provide users with suitable laser rust removal equipment, including 100-500W pulse laser cleaning machines and 1000-3000 continuous laser cleaning machines, to meet the rust removal needs of different application scenarios. To learn more about our laser cleaning solutions, contact us today.
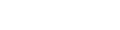
Contact information
- [email protected]
- [email protected]
- +86-19963414011
- No. 3 Zone A, Lunzhen Industrial Zone,Yucheng City , Shandong Province.
Get Laser Solutions