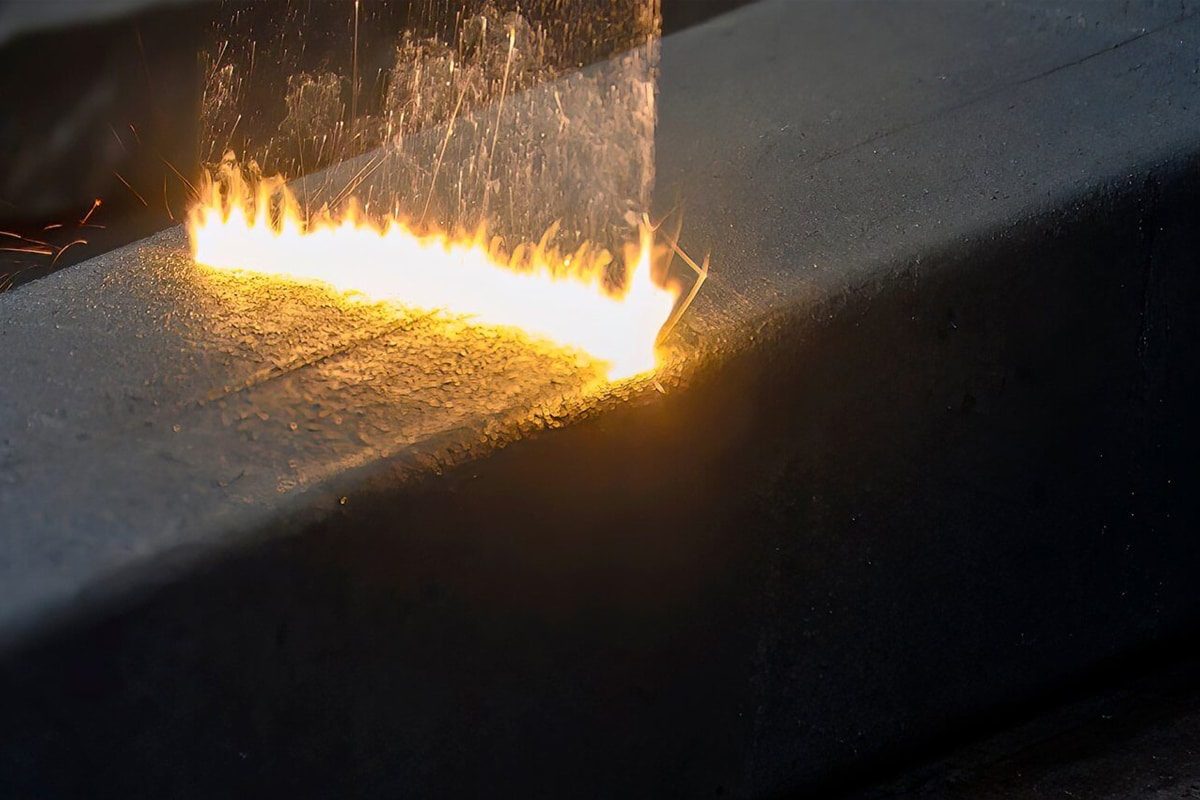
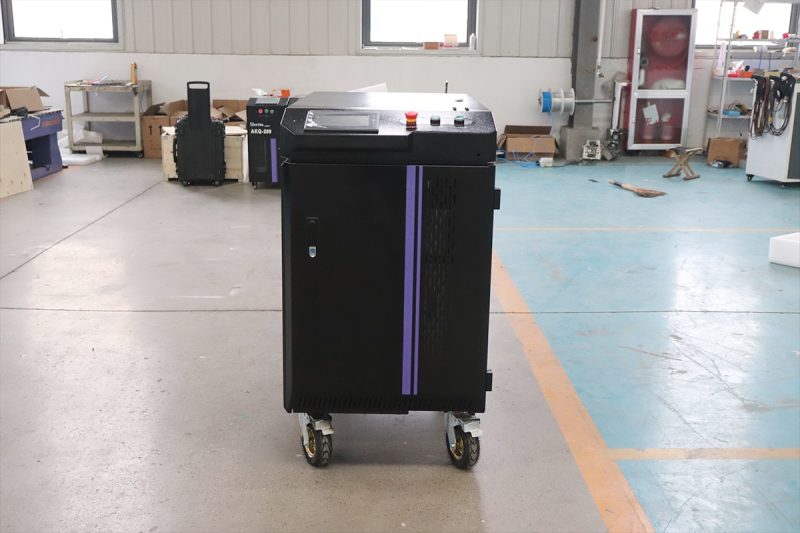
Understanding Laser Cleaning Machines
What is Laser Cleaning?
How Do Laser Cleaning Machines Work?
Laser cleaning machines operate by delivering a controlled laser beam onto the surface of the material to be cleaned. Here’s a step-by-step breakdown of how they work:
- Laser Beam Generation: The machine generates a laser beam at a specific wavelength and power level based on the type of material and contaminant to be cleaned.
- Targeting the Contaminant Layer: The contaminants absorb the laser energy faster than the substrate due to differences in thermal properties and reflectivity.
- Thermal and Photomechanical Effects: The laser energy heats the contaminants, causing them to vaporize, break apart, or peel off from the surface. Some lasers also generate a small shockwave that detaches particles.
- Debris Removal: The removed particles are either vaporized or blown away by air or vacuum systems integrated into the machine.
- Minimal Substrate Damage: The laser’s precision ensures the substrate remains intact, even when cleaning delicate or intricate surfaces.
Types of Laser Cleaning Machines
Advantages:
- Higher average power for faster cleaning of thick contaminants.
- Suitable for removing rust, paint, and coatings over broad surfaces.
- More cost-effective for industrial cleaning applications.
Limitations:
- Can generate more heat, posing a risk of damaging heat-sensitive substrates.
- Less suitable for intricate or selective cleaning tasks.
Advantages:
- Ideal for delicate surfaces where heat damage must be avoided.
- Provides precise control for selective cleaning of small or complex areas.
- Effective for removing thin films, oxidation, or light residues.
Limitations:
- Generally more expensive than continuous wave lasers.
- Requires careful parameter control to achieve optimal results.
Benefits of Laser Cleaning Machines
Laser cleaning offers a range of advantages over traditional cleaning methods:
- Non-Contact Cleaning: No direct contact with the surface, reducing the risk of wear or mechanical damage to sensitive components.
- Environmentally Friendly: Eliminates the need for chemicals, abrasives, and solvents, reducing hazardous waste and promoting a cleaner work environment.
- Precise and Selective Cleaning: Capable of targeting specific areas without affecting the surrounding material, making it ideal for intricate parts and delicate surfaces.
- Versatile Applications: Effective on a wide variety of materials, including metals, ceramics, composites, and stone.
- Minimal Maintenance: With fewer moving parts, laser cleaning machines require less maintenance compared to traditional equipment.
- Cost-Effective in the Long Run: Although the initial investment may be higher, reduced maintenance, labor, and material costs make laser cleaning a cost-effective solution.
- Improved Safety: Reduces the need for abrasive blasting or chemical exposure, improving safety for operators.
- High Efficiency and Speed: Laser cleaning processes are quick, reducing downtime and enhancing productivity in industrial environments.
- Automation Capability: Laser cleaning systems can be integrated into production lines, enabling automated cleaning for high-volume operations.
- Consistent Results: Laser cleaning ensures repeatable and uniform results across different surfaces, enhancing product quality.
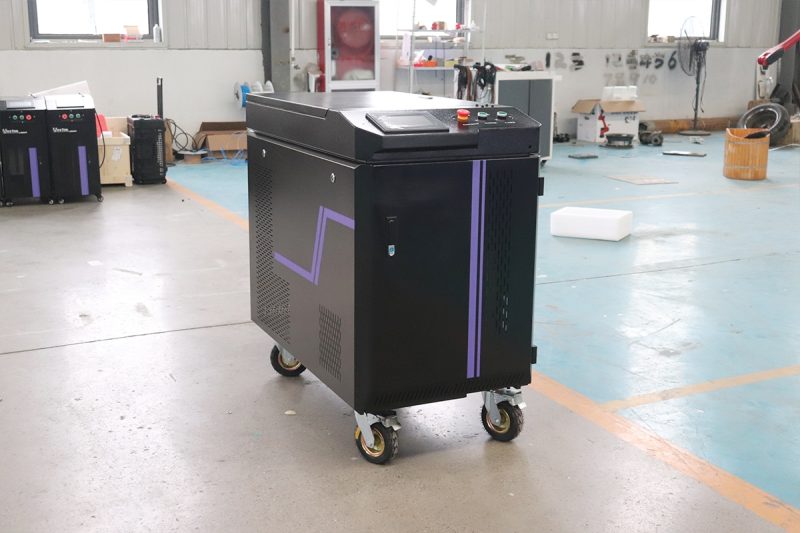
Why Choosing the Right Laser Cleaning Machine Matters
Selecting the right laser cleaning machine helps ensure optimal cleaning results, operational efficiency, and long-term value. The wrong choice can lead to inefficiencies, surface damage, and increased costs, especially in industries where precision, safety, and productivity are critical. Below are the key reasons why choosing the right laser cleaning machine is crucial for your operations.
- Ensures Optimal Cleaning Performance: Different materials and contaminants react differently to laser energy. Choosing a machine with the correct laser power, wavelength, and beam parameters ensures the thorough removal of contaminants without damaging the underlying surface. For example, higher-power lasers are ideal for removing heavy rust, while pulsed lasers are better suited for delicate surfaces or precision cleaning.
- Prevents Substrate Damage: Using a laser cleaning machine with improper settings can overheat or burn the substrate, leading to costly material loss or damage. Machines with customizable parameters allow for precise energy control, protecting sensitive surfaces such as plastic components, thin metals, or historical artifacts.
- Improves Productivity and Efficiency: The right laser cleaning machine enhances workflow by minimizing downtime and increasing cleaning speed. Machines that match the cleaning task—whether it’s batch cleaning in a production line or portable field cleaning—help businesses achieve consistent results with minimal effort. Automated systems also reduce labor requirements, freeing operators for other tasks.
- Reduces Operational Costs: While the initial investment for a laser cleaning machine may be significant, selecting the correct machine reduces operational costs in the long run. Properly chosen machines consume less energy, require fewer repairs, and minimize waste, contributing to a lower total cost of ownership (TCO). Efficient cleaning also reduces the need for rework, saving valuable time and resources.
- Maximizes Safety and Compliance: Laser cleaning eliminates the need for abrasive blasting or chemical solvents, improving workplace safety. However, the wrong machine—especially one lacking safety features like interlock systems or enclosures—can pose risks to operators. Selecting a machine with the appropriate safety measures ensures compliance with industry regulations and protects workers from laser exposure hazards.
- Enhances Application Versatility: Different industries and applications require specialized laser cleaning solutions. For example, the automotive industry may need continuous-wave lasers for large-scale cleaning, while aerospace or electronics industries may benefit from pulsed lasers for precision cleaning. Selecting the appropriate machine ensures that it can meet diverse application requirements, whether in heavy industries or delicate restoration projects.
- Supports Future Scalability and Growth: Investing in the right laser cleaning machine today ensures that it aligns with your future needs. Some machines offer modular designs or support software upgrades, enabling businesses to scale their operations as demand grows. Machines with broader functionality, such as portable units or automated systems, provide flexibility for evolving operational requirements.
- Protects Your Investment: Purchasing a laser cleaning machine is a significant investment. Choosing the wrong one may result in frequent maintenance, unexpected repairs, or even replacement costs. By carefully evaluating your needs and selecting a machine with the right specifications, you protect your investment and ensure long-term reliability.
- Improves Surface Preparation and Downstream Processes: Proper cleaning plays a critical role in preparing surfaces for subsequent processes, such as welding, painting, or coating. Choosing the correct laser cleaning machine ensures surfaces are clean and free from contaminants, improving the adhesion and quality of downstream operations.
- Builds Competitive Advantage: Companies that select the right laser cleaning equipment can offer higher-quality products and services, meet tighter deadlines, and reduce operational risks. This provides a competitive edge in the market, allowing businesses to enhance customer satisfaction and build long-term partnerships.
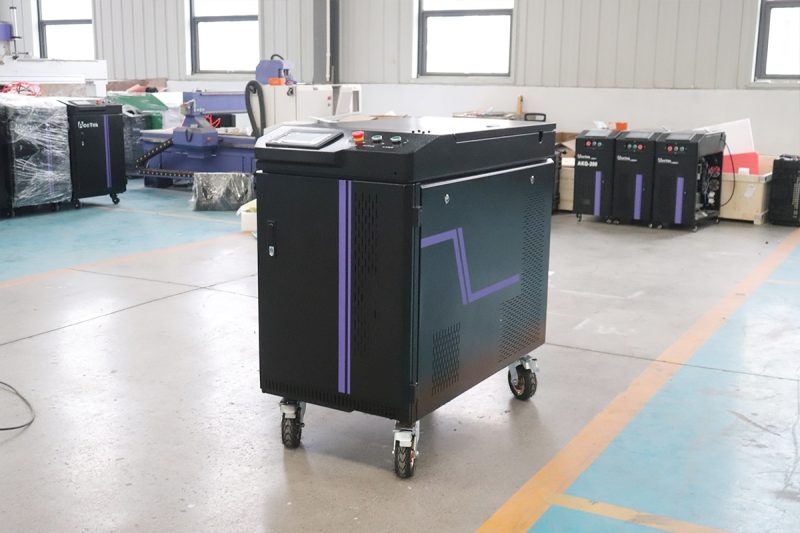
Factors to Consider When Choosing a Laser Cleaning Machine
Material Type
The substrate or material being cleaned significantly influences the choice of laser cleaning machine. Metals, plastics, ceramics, and composites each respond differently to laser energy due to variations in absorption, reflectivity, and thermal conductivity. For instance:
- Metals: Typically require higher power lasers due to their reflective nature.
- Delicate Materials: Plastics or softer materials need lower power settings to avoid damage.
- Stone or Wood: In cultural heritage applications, the laser needs to be finely tuned to avoid affecting the underlying surface.
Contaminant Type
The nature and thickness of the contaminant to be removed—rust, paint, oxide layers, oil, or organic residues—will also dictate the machine’s specifications.
- Heavy Rust and Thick Coatings: Higher power and slower scanning speeds may be required for efficient removal.
- Thin Films and Light Residue: Lower-power lasers with faster pulse durations may be more appropriate for precision cleaning.
Surface Requirements
Understanding the surface finish required after cleaning is critical. Laser cleaning can either remove contaminants while preserving surface texture or prepare a surface for additional processes like welding or coating.
- Sensitive Surfaces: For delicate surfaces that require minimal heat exposure, pulsed lasers with short pulse durations may be ideal.
- Rough or Industrial Surfaces: Continuous wave lasers with higher power might be needed for large-scale cleaning and preparation.
Laser Power and Energy
Laser power, typically measured in watts (W), determines the energy available for cleaning. The choice of power depends on the material and the contaminants to be removed.
- Low Power (100W-300W): Suitable for light cleaning, such as removing light contaminants or delicate surfaces.
- Medium Power (500W-1000W): Ideal for general-purpose cleaning in industries such as automotive or aerospace.
- High Power (1500W and above): Required for heavy-duty applications like industrial rust removal or large-scale cleaning.
Wavelength
The laser wavelength determines how well the laser beam interacts with the material and contaminants. Different wavelengths are absorbed more effectively by different materials:
- 1064 nm (Near-Infrared): Commonly used for metal surfaces and general cleaning applications.
- 532 nm (Green Wavelength): Useful for materials that are highly reflective of infrared wavelengths.
Pulse Duration
The pulse duration, or how long the laser beam interacts with the surface, can greatly impact the precision and effectiveness of cleaning.
- Short Pulses: Ideal for removing thin layers of contaminants and for applications requiring high precision, such as in electronics or delicate surface cleaning.
- Longer Pulses or Continuous Wave: Suitable for removing thicker contaminants, as they provide more energy over a longer period, allowing for deeper cleaning.
Beam Delivery Systems
Laser cleaning machines are equipped with various beam delivery systems to ensure optimal control over the laser’s interaction with the surface.
- Handheld Systems: Offer flexibility and precision for small or hard-to-reach areas.
- Automated or Robotic Systems: Provide consistent cleaning in industrial settings where precision and speed are critical.
Cooling Methods
Laser cleaning machines generate significant heat during operation, which requires effective cooling systems to maintain performance and extend equipment life.
- Air Cooling: Suitable for low to medium-power machines that do not produce excessive heat.
- Water Cooling: Necessary for higher power lasers, ensuring better heat dissipation and maintaining consistent cleaning performance over long periods.
Mobility and Portability
Depending on your operational needs, consider whether a portable or stationary machine is more suitable:
- Portable Machines: Ideal for fieldwork or on-site maintenance, especially in industries like construction, shipbuilding, or restoration.
- Stationary Systems: Typically used in industrial environments with high production volumes, where the machine can be integrated into a fixed location.
Control Systems and Software
User-friendly control systems and advanced software make operating laser cleaning machines easier and more efficient.
- Programmable Parameters: Machines with customizable settings allow users to adjust laser power, pulse duration, and cleaning speed for different applications.
- Monitoring and Diagnostics: Advanced systems can offer real-time monitoring and diagnostics, ensuring optimal performance and quick troubleshooting.
Automation Level
The degree of automation required depends on the scale and complexity of your operations.
- Manual or Handheld Systems: Ideal for flexible, small-scale applications where portability and operator control are important.
- Semi-Automated Systems: Offer a balance between manual control and automated features for repeatable results.
- Fully Automated Systems: Best for large-scale, high-volume operations where consistency, speed, and minimal manual intervention are required.
Cost and Budget
While the initial investment in a laser cleaning machine may be high, it’s important to consider the total cost of ownership, which includes operational costs, energy consumption, and maintenance.
- Budget-Friendly Options: Lower-power, handheld machines can be cost-effective for smaller-scale applications.
- High-End Systems: More expensive machines offer greater automation, power, and efficiency, making them suitable for industries that require heavy-duty cleaning.
Safety Features
Laser cleaning machines require built-in safety features to protect operators and the environment from harmful exposure.
- Safety Enclosures: Prevent accidental exposure to laser radiation.
- Interlock Systems: Automatically shut off the machine if a safety breach occurs.
- Personal Protective Equipment (PPE): Ensure the availability of laser safety goggles and other necessary protective gear for operators.
Maintenance and Service
Regular maintenance helps keep your laser cleaning machine running efficiently. Consider machines from manufacturers that offer:
- Comprehensive Warranty: Ensures the machine is protected from defects and failures.
- Readily Available Spare Parts: Reduces downtime by ensuring that components can be quickly replaced.
- After-Sales Support: Access to technical support and training programs helps operators maximize machine efficiency and reduces operational disruptions.
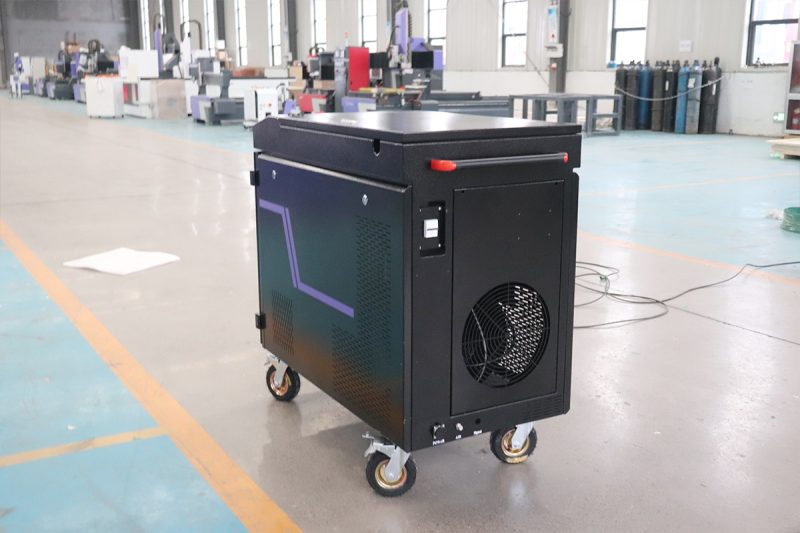
Applications and Industries
Automotive Industry
In the automotive sector, precision and cleanliness are critical to ensuring the quality and longevity of components. Laser cleaning machines are widely used to prepare metal surfaces for welding, bonding, and painting.
- Rust and Oxide Removal: Essential for preparing car body parts and chassis for welding and coating.
- Pre-Welding Surface Preparation: Ensures clean surfaces for high-quality welds, preventing defects.
- Paint Stripping and Reworking: Removes old paint layers without damaging the underlying metal.
- Cleaning of Engine Components: Removes carbon deposits and oil residues from cylinder heads, pistons, and other parts to enhance engine performance.
Aerospace Industry
The aerospace industry demands precision and reliability, and laser cleaning provides a non-invasive way to maintain components and systems.
- Coating Removal: Eliminates coatings from aircraft parts for maintenance and reapplication without damaging critical components.
- Surface Preparation for Bonding: Ensures adhesives and coatings adhere properly by thoroughly cleaning composite surfaces.
- Engine Part Cleaning: Removes carbon, oxide, and fuel residues from turbine blades and other engine components.
- Maintenance of Critical Parts: Provides precise cleaning for sensors, connectors, and other delicate parts without compromising functionality.
Shipbuilding Industry
Laser cleaning technology plays a crucial role in shipbuilding and marine maintenance by offering fast, effective solutions for removing rust and other contaminants.
- Rust Removal from Large Surfaces: Ensures metal surfaces are clean and ready for welding or painting, critical for hull construction.
- Surface Preparation for Coatings: Prepares metal surfaces to ensure better adhesion of protective paints and coatings.
- Marine Equipment Maintenance: Cleans propellers, valves, and other metal parts exposed to seawater, preventing corrosion and extending their lifespan.
- Non-Destructive Cleaning: Removes contaminants from sensitive marine instruments without affecting performance.
Cultural Heritage Restoration
Laser cleaning offers a delicate and precise method for restoring historical artifacts, sculptures, and architectural monuments without causing damage.
- Sculpture and Stone Cleaning: Safely removes dirt, pollution, and biological growth from sculptures and monuments without abrasion.
- Restoration of Frescoes and Paintings: Removes overpainting or varnish without disturbing the original artwork.
- Cleaning of Archaeological Finds: Carefully eliminate dirt and corrosion from ancient artifacts to preserve them for study and display.
- Non-Invasive Technology: Laser cleaning’s precision makes it ideal for delicate surfaces that cannot withstand chemical or abrasive cleaning.
Mold Cleaning
Laser cleaning is widely used in the plastic, rubber, and food industries to maintain molds, ensuring consistent product quality and extending mold life.
- Non-Damaging Cleaning: Removes residues from molds without damaging their surface or geometry.
- Quick and Efficient: Reduces downtime by cleaning molds quickly during production cycles.
- No Residue Left Behind: Cleans without leaving abrasive particles or chemicals, ensuring hygienic standards in food and pharmaceutical molds.
- Improves Product Quality: Ensures molds remain in optimal condition, preventing defects in finished products.
Other Industries
Laser cleaning machines are also making inroads into other industries, offering versatile and effective solutions across various applications.
- Electronics Industry: Removes oxides and contaminants from connectors, circuit boards, and delicate components without causing damage.
- Manufacturing and Maintenance: Prepares surfaces for coating and bonding and cleans machinery parts for optimal operation.
- Energy Sector: Removes corrosion and contaminants from turbines, pipelines, and industrial equipment used in power plants.
- Medical Industry: Cleans surgical tools and medical devices with precision, ensuring they meet strict hygiene standards.
- Railway Industry: Removes rust and paint from train tracks and components, ensuring durability and operational efficiency.
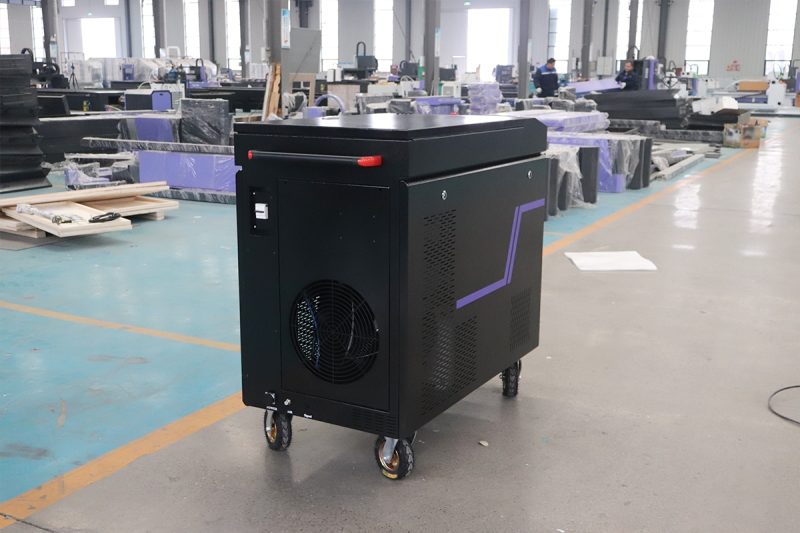
Regulatory and Safety Considerations
Laser Safety Classes
Laser safety classifications, as defined by international standards like IEC 60825-1, categorize lasers based on their potential to cause harm to the eyes or skin. Selecting the appropriate class ensures safe operation, especially in different industrial environments.
- Class 1: These lasers are considered safe under normal conditions because they are enclosed, preventing exposure to the laser beam. Machines integrated into automated systems often fall under this category.
- Class 2: Low-power visible lasers (e.g., up to 1 mW) are included in this class. Brief exposure is generally safe, but operators should avoid prolonged eye contact.
- Class 3: Higher power lasers with the potential to cause damage if viewed directly. Class 3 lasers require protective equipment, such as safety goggles, and controlled work areas.
- Class 4: These are high-power lasers that can cause severe damage to the eyes and skin. Most industrial laser cleaning machines fall under Class 4, necessitating strict safety measures, including enclosed workstations, interlocks, and protective gear.
Operator Training
Proper training ensures the safe and efficient use of laser cleaning machines, especially high-power systems. Well-trained operators ensure that cleaning processes are effective while minimizing the risk of accidents.
- Understanding Laser Parameters: Operators must learn how to adjust laser power, pulse frequency, and speed based on the material and contaminant type.
- Equipment Handling: Training ensures that operators can safely handle handheld devices, portable units, and automated systems.
- Safety Protocols: Operators must be familiar with safety protocols, including the use of personal protective equipment (PPE) such as laser goggles and gloves.
- Emergency Procedures: Training should include steps for responding to equipment malfunctions, safety breaches, or accidental laser exposure.
- Compliance and Documentation: Operators should also understand how to comply with regulatory standards, document cleaning processes, and perform routine maintenance.
Environmental Impact
Laser cleaning is considered an environmentally friendly alternative to traditional cleaning methods, as it eliminates the need for hazardous chemicals, abrasive materials, and excessive water usage. However, businesses must still consider the environmental aspects associated with laser cleaning systems.
- Waste Reduction: Laser cleaning produces minimal waste, with most contaminants vaporized or collected as dust. Machines with integrated vacuum systems help prevent the release of particles into the air.
- Energy Consumption: Machines with higher power levels may consume significant energy. Selecting energy-efficient models and using appropriate power settings can minimize electricity usage.
- Emission Control: Though laser cleaning generates less pollution than chemical methods, it can produce fumes, especially when removing paint or coatings. Proper ventilation or filtration systems should be in place to manage emissions.
- Noise Pollution: While quieter than abrasive cleaning methods, some laser cleaning machines may generate operational noise. Noise control measures should be considered, especially in confined or indoor environments.
- Sustainability Goals: Businesses can align their laser cleaning practices with sustainability initiatives by reducing chemical waste, improving energy efficiency, and minimizing environmental impact.
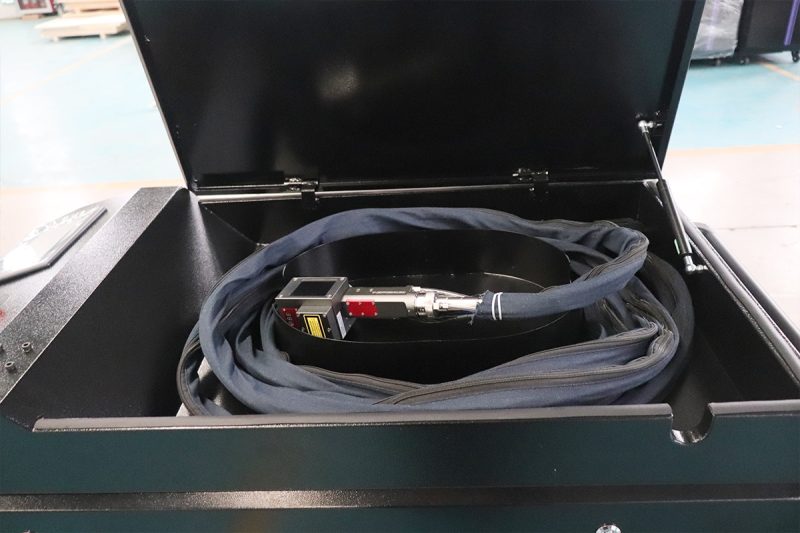
Evaluating Manufacturers and Suppliers
Reputation and Experience
The reputation and experience of a manufacturer reflect their reliability and the quality of their products.
- Industry Expertise: Look for manufacturers with a proven track record in producing laser cleaning machines, such as AccTek Laser, known for expertise in a wide range of laser solutions.
- Customer Reviews and Case Studies: Feedback from existing customers offers insight into product performance and customer satisfaction. Case studies showcasing past projects can highlight the manufacturer’s experience in your specific industry.
- Certifications and Standards Compliance: Manufacturers that adhere to international standards, such as ISO certifications, demonstrate a commitment to quality and safety.
- Global Presence: Suppliers with a global network of customers or partners often have a broader experience and stronger support systems.
Customization Options
Not all laser cleaning requirements are the same, and having the flexibility to customize machines ensures they align perfectly with your operational needs.
- Tailored Solutions: A good manufacturer should offer various options for power levels, wavelengths, and beam delivery systems to meet specific cleaning tasks.
- Modular Designs: Look for machines with modular components that allow easy upgrades, giving you the flexibility to scale operations.
- Special Features: Some manufacturers offer additional customization, such as integrating vacuum systems, cooling solutions, or automated control interfaces.
- Adaptability for Future Growth: A supplier offering a range of compatible products makes it easier to expand or upgrade your operations over time.
Technical Support and Training
Effective technical support ensures smooth installation, operation, and troubleshooting. Proper operator training maximizes the machine’s efficiency and safety.
- Installation and Setup Support: Manufacturers should assist in the installation phase to ensure the machine operates optimally.
- Training Programs: Look for suppliers that offer in-depth operator training on equipment handling, safety protocols, and optimizing laser parameters for different cleaning tasks.
- Ongoing Technical Assistance: Ensure the manufacturer provides remote or on-site support to resolve operational issues quickly.
- Software Updates and Upgrades: Regular updates to control systems and software enhance the machine’s performance and extend its lifespan.
Warranty and Maintenance Services
Reliable warranty and maintenance services protect your investment and minimize downtime, ensuring consistent operations.
- Comprehensive Warranty: A good manufacturer should offer warranties covering parts and labor, with clear terms and conditions.
- Maintenance Plans: Regular preventive maintenance helps avoid unexpected breakdowns and keeps the machine performing at peak efficiency.
- Spare Parts Availability: Quick access to genuine spare parts ensures repairs can be completed without delays.
- After-Sales Service Network: Look for manufacturers with a well-established service network, ensuring fast response times for technical issues and repairs.
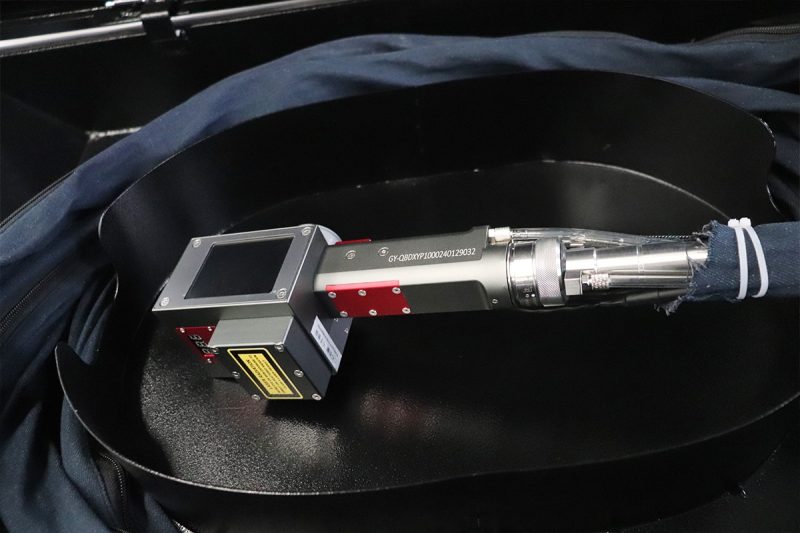
Summary
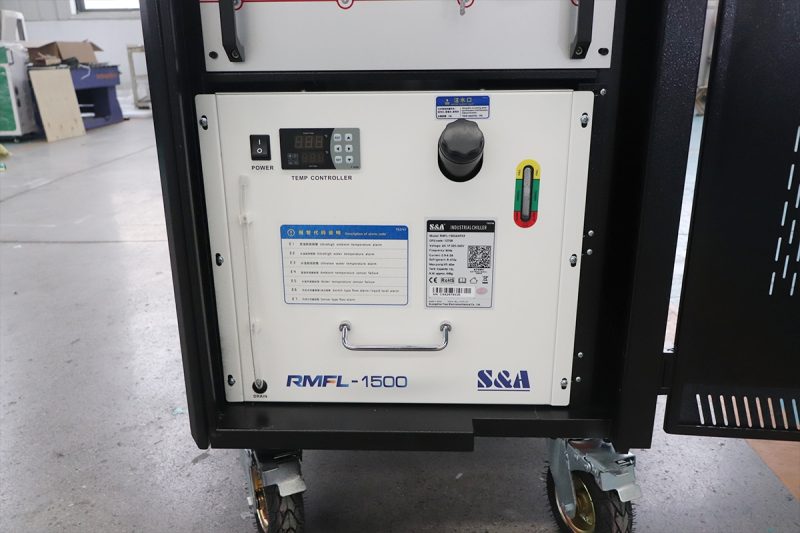
Get Laser Cleaning Solutions
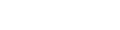
- [email protected]
- [email protected]
- +86-19963414011
- No. 3 Zone A, Lunzhen Industrial Zone,Yucheng City , Shandong Province.