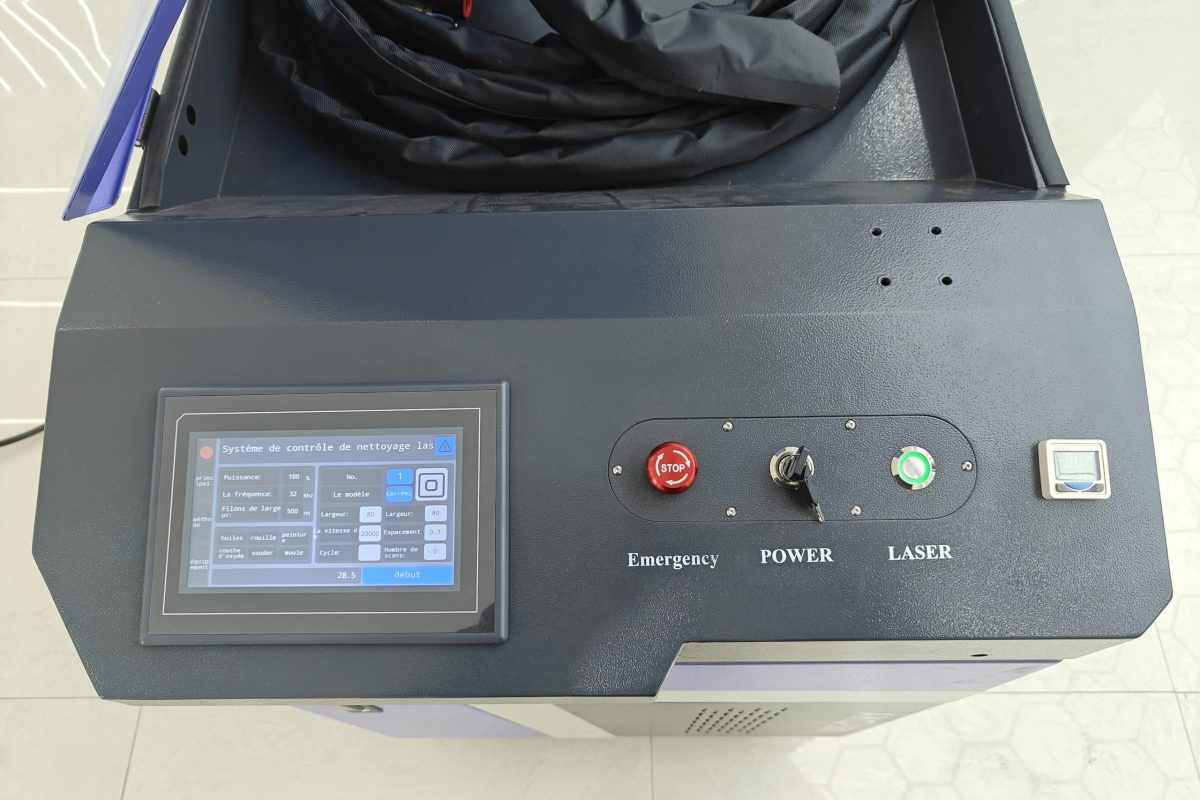
Come installare una macchina per la pulizia laser a impulsi?
Negli ultimi anni, la tecnologia di pulizia laser a impulsi è stata ampiamente utilizzata nel trattamento superficiale industriale, nel restauro di reperti culturali, nella pulizia di stampi, nella lavorazione di componenti elettronici e in altri settori. Grazie ai suoi vantaggi, come l'elevata efficienza, la tutela dell'ambiente, l'assenza di contatto con il substrato e l'assenza di materiali di consumo, sta gradualmente sostituendo i metodi di pulizia tradizionali. La corretta configurazione della macchina per la pulizia laser è fondamentale per garantire l'efficacia della pulizia e la stabilità dell'apparecchiatura. Questa guida spiegherà in modo sistematico l'intero processo di configurazione. macchina per la pulizia laser a impulsi dalla preparazione di base alla configurazione avanzata.
Sommario
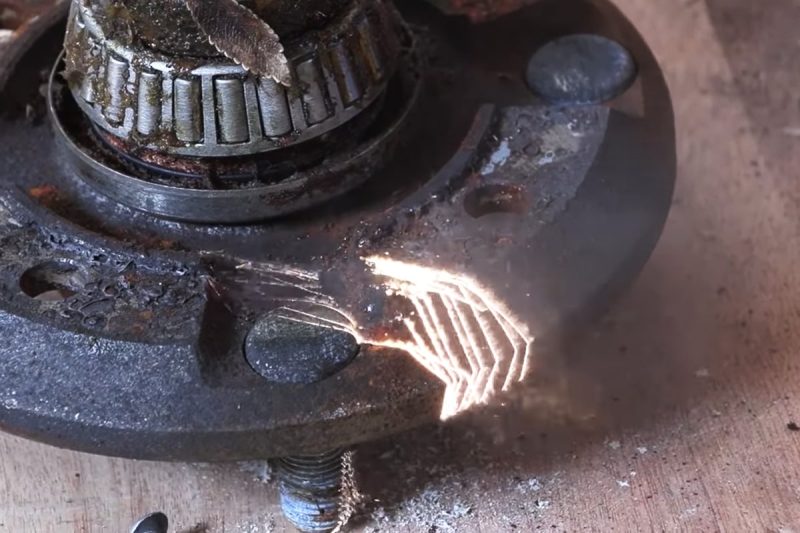
Scopri di più sulla macchina per la pulizia laser a impulsi
La pulizia laser a impulsi è una tecnologia di pulizia senza contatto che utilizza un laser ad alta energia a impulsi brevi per vaporizzare, ablare o rimuovere lo strato contaminato. Rispetto al laser continuo, il laser a impulsi offre prestazioni migliori nel controllo dell'impatto termico e nella massima precisione. È adatto a scenari ad alta richiesta come la rimozione laser della ruggine, la sverniciatura dei rivestimenti, la rimozione dello strato di ossido, ecc., ed è particolarmente indicato per la pulizia di metalli di alto valore e componenti di precisione.
Pianificazione e preparazione iniziale
Prima di installare e utilizzare l'apparecchiatura di pulizia laser a impulsi, una pianificazione preliminare scientifica è fondamentale per garantire risultati di pulizia ottimali, migliorare l'efficienza operativa e prolungare la durata dell'apparecchiatura. Solo dopo aver compreso appieno i requisiti di pulizia, i tipi di materiali e le caratteristiche di inquinamento, è possibile configurare il sistema laser in modo razionale per massimizzare le prestazioni dell'apparecchiatura. Di seguito vengono presentati in modo sistematico i concetti fondamentali della pianificazione e della preparazione preliminare, analizzando due aspetti.
Valutare le esigenze di pulizia
Prima dell'installazione formale, è necessario chiarire le condizioni specifiche di pulizia per formulare il piano di processo corrispondente. È necessario considerare i seguenti aspetti:
- Tipo di substrato: materiali diversi presentano diversi tassi di assorbimento dei raggi laser, il che influisce direttamente sull'efficienza e sulla sicurezza della pulizia. I materiali più comuni per la pulizia laser includono acciaio al carbonio, acciaio inossidabile, lega di alluminio, rame, titanio e alcuni materiali non metallici come pietra e polimeri plastici.
- Tipo di inquinante: è necessario identificare il tipo di strato di inquinante presente sulla superficie dell'oggetto da pulire, come ruggine, ossido, schizzi di saldatura, vecchio strato di vernice, macchie d'olio, resina o rivestimento. Diversi inquinanti reagiscono in modo diverso all'energia laser, quindi i parametri devono essere impostati in modo mirato.
- Obiettivo della pulizia: è necessario chiarire se l'operazione di pulizia laser mira a rimuovere completamente gli inquinanti superficiali o a irruvidire la superficie per migliorare l'adesione di successivi trattamenti di spruzzatura, galvanica o saldatura. Obiettivi diversi determineranno l'intervallo di valori di parametri come l'energia dell'impulso e la velocità di scansione.
Una valutazione accurata delle esigenze è il prerequisito per sviluppare soluzioni efficienti, sicure e convenienti per la rimozione della ruggine tramite laser o per il trattamento superficiale tramite laser.
Scegliere il sistema laser giusto
Dopo aver chiarito i requisiti di pulizia, è necessario selezionare un sistema di pulizia laser adatto allo scenario applicativo specifico. Di seguito sono riportati i principali parametri di riferimento:
- Tipo di laser: attualmente, le apparecchiature di pulizia laser utilizzano principalmente generatori laser a fibra pulsata o generatori laser Nd:YAG. Tra questi, i generatori laser a fibra pulsata sono diventati la scelta più diffusa grazie alle dimensioni ridotte, all'elevata stabilità, all'assenza di materiali di consumo e ai bassi costi di manutenzione.
- Selezione della lunghezza d'onda: la lunghezza d'onda del laser influenza le caratteristiche di assorbimento del materiale. La lunghezza d'onda del vicino infrarosso di 1064 nm è generalmente utilizzata in ambito industriale, ed è particolarmente adatta per la pulizia di inquinanti su superfici metalliche, tenendo conto dell'elevata densità energetica e dell'adattabilità del materiale.
- Energia e frequenza dell'impulso: la potenza di picco e la frequenza del laser pulsato determinano la densità di energia di un singolo impulso. Deve essere configurata in base allo spessore dello strato di contaminazione, alla velocità di pulizia e alla resistenza al calore del substrato per evitare danni termici al substrato.
- Gamma di potenza: selezionare generatori laser di diversa potenza in base all'intensità dell'attività di pulizia. La gamma di potenza dei comuni macchine per la pulizia laser da 100 W a 2000 Per esigenze di pulizia di grandi superfici o in caso di inquinamento intenso, è possibile selezionare apparecchiature con potenza maggiore (ad esempio da 500 W o più) per migliorare l'efficienza.
Una scelta ponderata non influisce solo sull'efficienza della pulizia, ma è anche direttamente correlata alla durata utile dell'apparecchiatura e alla sua stabilità operativa a lungo termine. È il passaggio fondamentale per garantire la qualità della pulizia laser.
Una pianificazione e una preparazione tempestive non sono solo i prerequisiti per un utilizzo efficace dei sistemi di pulizia laser, ma sono anche direttamente correlate alla stabilità operativa delle apparecchiature, alla controllabilità della qualità della pulizia e alla sicurezza degli operatori. Valutando scientificamente le esigenze di pulizia e selezionando le configurazioni e le combinazioni di parametri più appropriate per il generatore laser, gli utenti possono sfruttare appieno il potenziale della tecnologia di pulizia laser pulsata, migliorando al contempo l'efficienza produttiva e realizzando una pulizia realmente ecologica e una produzione intelligente.
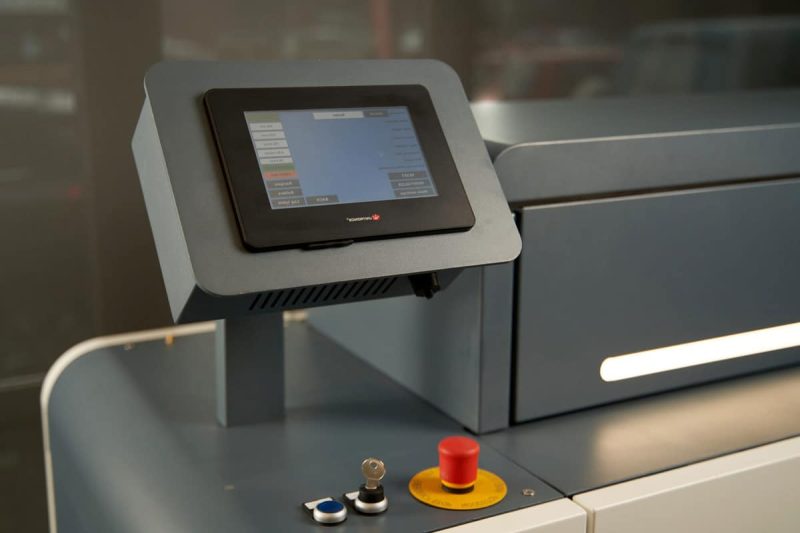
Impostazione della macchina per la pulizia laser
Dopo aver completato la valutazione delle esigenze di pulizia e la selezione dell'attrezzatura, il passo successivo è l'installazione e il debug del sistema di pulizia laser in loco. Questa fase di lavoro non è solo correlata al corretto funzionamento dell'attrezzatura, ma influisce anche direttamente sull'efficienza e sulla sicurezza della pulizia successiva. Un'installazione e una calibrazione scientifiche e standardizzate aiuteranno l'attrezzatura per la rimozione della ruggine laser a raggiungere la corretta capacità di pulizia e la stabilità del sistema.
Installazione della macchina
Il processo di installazione delle apparecchiature di pulizia laser deve tenere in debita considerazione l'adattabilità e la sicurezza dell'ambiente operativo:
- Preparazione del sito: scegliere un impianto industriale pulito, asciutto e ben ventilato come luogo di installazione dell'apparecchiatura e riservare spazio sufficiente per il corpo dell'apparecchiatura, il sistema di controllo e il canale operativo per evitare surriscaldamento, accumulo di polvere e altri fattori che influiscono sul funzionamento stabile del sistema di pulizia laser.
- Configurazione dell'alimentatore: in base ai requisiti di alimentazione del generatore laser, del quadro elettrico e del refrigeratore, è necessario configurare un alimentatore industriale adeguato (generalmente 220 V o 380 V) e la tensione deve essere stabile per evitare anomalie dell'apparecchiatura dovute a fluttuazioni di tensione. Si consiglia di installare uno stabilizzatore di tensione e una protezione di messa a terra dedicata.
- Installazione del sistema di raffreddamento: i generatori laser pulsati ad alta potenza generano molto calore durante il funzionamento continuo, pertanto è necessario installare un efficiente refrigeratore industriale per mantenere la temperatura del generatore laser entro un intervallo sicuro e prolungare la durata utile del modulo laser.
- Sistema di ventilazione e aspirazione fumi: durante la pulizia laser vengono generati fumo, odori e particelle minuscole; è quindi necessario predisporre un sistema di depurazione fumi professionale o un'apparecchiatura per l'affumicatura industriale. Garantire un buon sistema di aspirazione fumi non solo migliora l'ambiente di lavoro, ma soddisfa anche le normative sulla tutela ambientale.
Allineamento e calibrazione
Dopo aver completato l'installazione hardware di base, il sistema laser deve essere calibrato con precisione per garantire risultati di pulizia costanti e sicuri:
- Allineamento del raggio laser: utilizzare un dispositivo di posizionamento o un modello di riferimento per allineare con precisione il raggio laser con la superficie del pezzo da pulire, mantenere stabili la posizione e l'angolazione del punto ed evitare offset che causano aree di pulizia irregolari o danni al substrato.
- Calibrazione dei parametri laser: in base alle proprietà del materiale e alle caratteristiche dei contaminanti, regola parametri chiave quali potenza laser, frequenza degli impulsi, velocità di scansione e larghezza degli impulsi per soddisfare i diversi requisiti delle attività di pulizia, migliorare l'efficienza ed evitare il surriscaldamento.
- Esecuzione di prova: si consiglia di testare i campioni prima della pulizia in lotti. Osservando l'effetto di pulizia, le variazioni superficiali e le aree interessate dal calore, è possibile perfezionare ulteriormente i parametri per garantire che il processo di pulizia laser a impulsi sia stabile e controllabile.
Completando l'installazione e la messa in servizio delle apparecchiature di pulizia laser in modo scientifico e standardizzato, non solo è possibile migliorarne l'efficienza operativa complessiva, ma anche prolungarne significativamente la durata e ridurre la frequenza di manutenzione. Soprattutto in scenari industriali di produzione di massa o di lavoro continuo a lungo termine, una buona impostazione iniziale è fondamentale per garantire la qualità e la stabilità della pulizia laser.
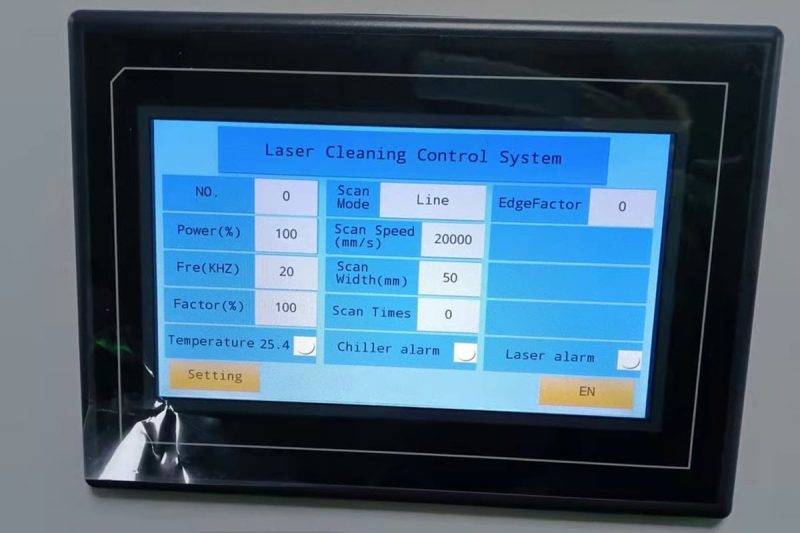
Ottimizzazione dei parametri laser
Dopo l'installazione e il debug del sistema di pulizia laser, è fondamentale ottimizzare ulteriormente i parametri del processo laser. Un'impostazione ponderata dei diversi parametri laser può non solo migliorare l'efficienza della rimozione degli inquinanti, ma anche massimizzare la protezione della superficie del substrato, evitando danni termici e sovra-processazione. Soprattutto in scenari industriali in cui coesistono materiali diversi e tipi di inquinamento complessi, la capacità di controllare i parametri determina l'adattabilità e la stabilità del sistema di pulizia laser. Per ottenere il miglior effetto di pulizia, si consiglia di concentrarsi sui seguenti parametri chiave:
Durata dell'impulso
La durata dell'impulso influenza direttamente il tempo di azione del laser e del materiale, ed è un fattore importante nel determinare la precisione della pulizia e l'intervallo di diffusione del calore. Impulsi più brevi (come nanosecondi e picosecondi) contribuiscono a ottenere l'effetto "cold processing", adatto per trattamenti superficiali con elevati requisiti di precisione e che riduce la zona termicamente alterata del substrato. Al contrario, impulsi più lunghi sono ideali per la rimozione efficiente di contaminanti spessi e pesanti.
Energia impulsiva
Maggiore è l'energia dell'impulso, maggiore è la capacità di distacco sotto l'azione del laser, che può effettivamente distruggere la forza di legame tra lo strato di contaminazione e il substrato. Tuttavia, è necessario controllarla entro un intervallo di sicurezza per evitare la fusione o l'ablazione del substrato. Solitamente, è necessario regolarla gradualmente in base allo spessore della contaminazione, alla forza di adesione e alla sensibilità termica del substrato.
Frequenza di ripetizione
La frequenza di ripetizione del laser determina il numero di impulsi laser per unità di tempo, controllando così l'efficienza di pulizia e l'accumulo di calore. Una frequenza di ripetizione più elevata può accelerare il processo, ma se l'energia dell'impulso non è correttamente calibrata, può causare problemi come un eccessivo accumulo di calore e scolorimento della superficie. Il perfetto equilibrio tra frequenza ed energia è la chiave per ottenere una pulizia efficiente e stabile.
Profilo del fascio e punto focale
La forma del fascio laser e la posizione di messa a fuoco influiscono direttamente sulla densità di energia per unità di superficie. Un buon controllo della messa a fuoco può concentrare l'energia sullo strato di contaminante e migliorare l'effetto di pulizia. Solitamente, si utilizza un fascio gaussiano o un design a spot "top hat" con distribuzione uniforme dell'energia, combinato con una funzione di messa a fuoco automatica per ottenere una maggiore uniformità e pulizia.
In generale, le prestazioni finali del sistema di pulizia laser dipendono non solo dalla configurazione hardware dell'apparecchiatura stessa, ma anche dalla professionalità del debug dei parametri e dalle capacità di ottimizzazione del processo. Impostando in modo scientifico parametri fondamentali come la durata dell'impulso, l'energia, la frequenza e il controllo spot, è possibile migliorare significativamente l'efficienza di pulizia, ridurre il tasso di danneggiamento dei materiali e adattarsi a scenari di pulizia più complessi.
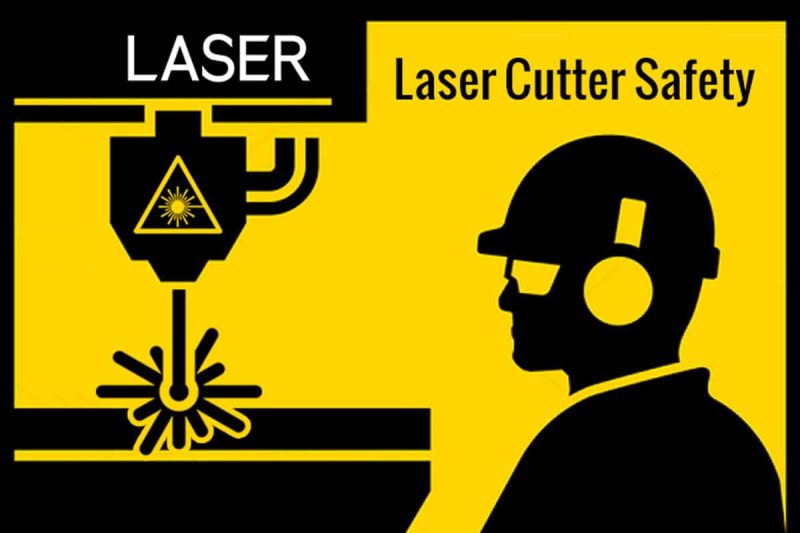
Protocollo di sicurezza
Durante l'utilizzo di macchine per la pulizia laser, garantire la sicurezza dell'ambiente operativo e del personale è un prerequisito fondamentale per il funzionamento stabile dell'apparecchiatura e la conformità della produzione. Poiché il generatore laser stesso presenta elevate caratteristiche di energia e focalizzazione, e durante il processo di pulizia possono essere generati fumo e particelle nocive, la mancanza di un meccanismo di protezione completo può comportare potenziali rischi per la salute degli operatori e dell'ambiente circostante. Pertanto, quando si implementano sistemi di pulizia laser, le aziende devono implementare contemporaneamente un set completo di protocolli di sicurezza sistematici.
Misure di sicurezza laser
Per evitare che le radiazioni laser causino danni al corpo umano, si raccomandano le seguenti strategie di protezione laser:
- Indossare occhiali protettivi laser: gli operatori devono essere dotati di occhiali protettivi che soddisfino i requisiti della lunghezza d'onda laser, come occhiali protettivi di livello OD per lunghezza d'onda di 1064 nm, per garantire che gli occhi non vengano danneggiati dalla luce laser diretta o riflessa.
- Configurazione del dispositivo di interblocco di sicurezza: configurare un sistema di interblocco per il generatore laser e l'area di lavoro. Se una porta di protezione non è chiusa o una persona anomala entra nell'area, il sistema interromperà automaticamente l'emissione laser per evitare malfunzionamenti e attivazioni accidentali.
- Installare cartelli di avvertimento: appendere cartelli accattivanti come "Area operativa laser" e "Indossare occhiali protettivi" in punti evidenti nell'area di lavoro per ricordare a tutto il personale che entra nell'area di prestare attenzione alle misure di protezione.
Controllo del fumo e delle particelle
Durante il processo di pulizia laser, gli inquinanti vengono vaporizzati e vengono rilasciati particelle fini e fumo. Se non rimossi in tempo, possono causare danni all'apparato respiratorio dell'operatore e alla struttura dell'apparecchiatura:
- Installare un aspiratore di fumi: filtrare efficacemente le particelle PM2.5, le nebbie oleose, i gas organici, ecc., per garantire che la purezza dell'aria soddisfi gli standard di sicurezza industriale.
- Assicurarsi che il sistema di ventilazione non sia ostruito: soprattutto quando si lavora in spazi chiusi o ristretti, è necessario installare ventilatori di scarico industriali o apparecchiature di ventilazione a pressione negativa per mantenere un buon flusso d'aria e percorsi di scarico per impedire che gli inquinanti si depositino sulla superficie dell'apparecchiatura o rifluiscano nell'area di lavoro.
Formazione e istruzione
Anche se le misure di protezione hardware sono perfette, la standardizzazione delle operazioni del personale è comunque una garanzia importante per la sicurezza operativa. Pertanto, è necessario istituire un sistema di formazione regolare:
- Formazione sulla sicurezza laser: comprendente il principio dei rischi laser, le procedure di risposta alle emergenze, come utilizzare i dispositivi di protezione individuale, ecc., per migliorare la consapevolezza dei dipendenti in materia di sicurezza.
- Formazione operativa: assicurarsi che gli operatori acquisiscano le competenze di base per il corretto avvio, arresto, regolazione dei parametri, risoluzione dei problemi, ecc. della macchina per la pulizia laser.
- Formazione sulla manutenzione: formare i tecnici competenti per padroneggiare il processo di manutenzione giornaliera dell'apparecchiatura, tra cui l'ispezione del percorso ottico, la sostituzione dell'elemento filtrante, la manutenzione del sistema di raffreddamento, ecc., per garantire il funzionamento stabile a lungo termine dell'apparecchiatura.
Nel complesso, sebbene la tecnologia di pulizia laser offra elevati vantaggi in termini di efficienza e tutela ambientale, impone anche requisiti più elevati in termini di sicurezza d'uso. Le aziende dovrebbero considerare l'accordo di sicurezza come parte fondamentale del lancio del progetto e sviluppare un sistema di sicurezza che soddisfi gli standard di settore, dalla valutazione del rischio alla selezione delle apparecchiature, fino alla formazione del personale e alla tutela ambientale.
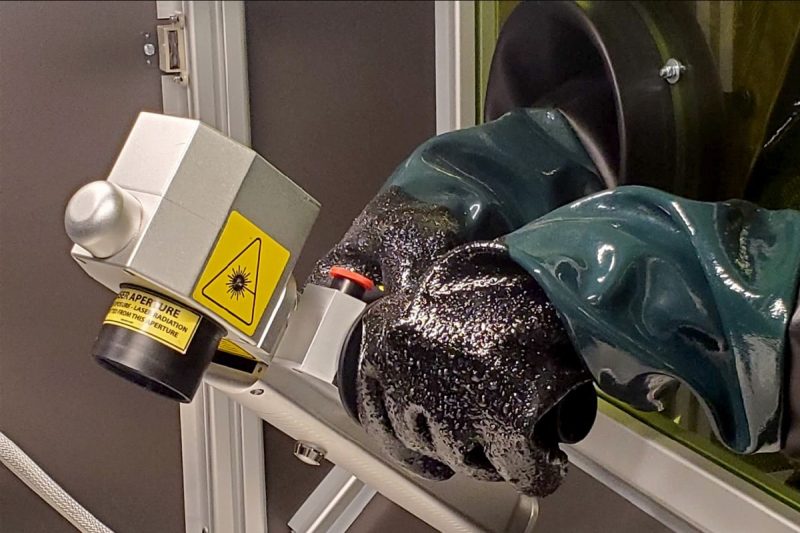
Manutenzione ordinaria e risoluzione dei problemi
Per garantire il funzionamento continuo, efficiente e stabile della macchina per la pulizia laser, l'azienda deve implementare un meccanismo sistematico di manutenzione giornaliera e un processo di risoluzione dei problemi. Sebbene il sistema laser sia un'apparecchiatura di lavorazione senza contatto, i suoi componenti principali, come il generatore laser, il sistema ottico e il sistema di raffreddamento, sono comunque inevitabilmente influenzati da molteplici fattori, come l'ambiente e il carico, durante il funzionamento a lungo termine. La mancata manutenzione regolare comprometterà direttamente l'efficacia della pulizia, la potenza del laser e persino la durata utile dell'apparecchiatura.
Articoli di manutenzione ordinaria
Si consiglia agli utenti di sviluppare piani di manutenzione per periodi diversi, ad esempio settimanali, mensili e trimestrali, in base alla frequenza di utilizzo dell'attrezzatura, e di concentrarsi sul controllo dei seguenti elementi:
- Pulizia della testina laser e delle lenti ottiche: utilizzare tamponi di cotone privi di polvere e un liquido speciale per la pulizia delle lenti per pulire regolarmente la lente protettiva e la lente di messa a fuoco, per evitare divergenze laser, riduzioni di potenza o ablazione dello specchio dovute a polvere e olio.
- Controllare lo stato del sistema di raffreddamento: verificare quotidianamente che la capacità di raffreddamento del refrigeratore industriale sia normale, che il canale dell'acqua sia libero da ostruzioni e che la temperatura dell'acqua sia mantenuta entro l'intervallo raccomandato per il generatore laser. Sostituire regolarmente l'acqua di raffreddamento pura e pulire il filtro del serbatoio dell'acqua per evitare l'accumulo di calcare e ridurre l'efficienza di conduzione del calore.
- Sostituzione delle parti consumabili: sostituire regolarmente la fibra ottica laser, il cavo di alimentazione, la copertura antipolvere, la lente protettiva, ecc., invecchiati, in particolare per le apparecchiature sottoposte a carichi pesanti o a un funzionamento continuo a lungo termine; prestare maggiore attenzione al ciclo di vita dei materiali di consumo.
Risoluzione dei problemi comuni
Quando l'apparecchiatura di pulizia laser funziona in modo anomalo, è necessario eseguire un'indagine sistematica in base al fenomeno per garantire un rapido ripristino:
- Fluttuazione della potenza del laser: spesso causata da una scarsa dissipazione del calore del generatore laser, da una tensione di alimentazione instabile o da un percorso ottico contaminato. Controllare la temperatura dell'acqua del sistema di raffreddamento, la solidità del cablaggio dell'alimentatore, l'eventuale presenza di ostruzioni nel percorso ottico o di contaminazione della lente.
- Deviazione del raggio o traiettoria di pulizia anomala: solitamente causata da lenti ottiche allentate, installazione inclinata o deviazione della struttura interna della testa laser. Si consiglia di bloccare nuovamente la lente e ricalibrare il percorso ottico o sostituire il componente di messa a fuoco, se necessario.
- Una filtrazione anomala del fumo o uno scarico debole possono essere causati da un'ostruzione del filtro o da un danno alla ventola. Controllare tempestivamente la saturazione del filtro purificatore del fumo, sostituire il filtro ad alta efficienza se necessario e verificare che il condotto di scarico non sia ostruito e che la ventola funzioni normalmente.
Grazie a una manutenzione regolare e a processi standardizzati di risoluzione dei problemi, gli utenti possono non solo ridurre significativamente i tassi di guasto delle apparecchiature e prolungare la durata utile dell'intera macchina, ma anche garantire la continuità e la coerenza delle operazioni di pulizia, ridurre il rischio di interruzioni della produzione e migliorare la capacità produttiva complessiva.
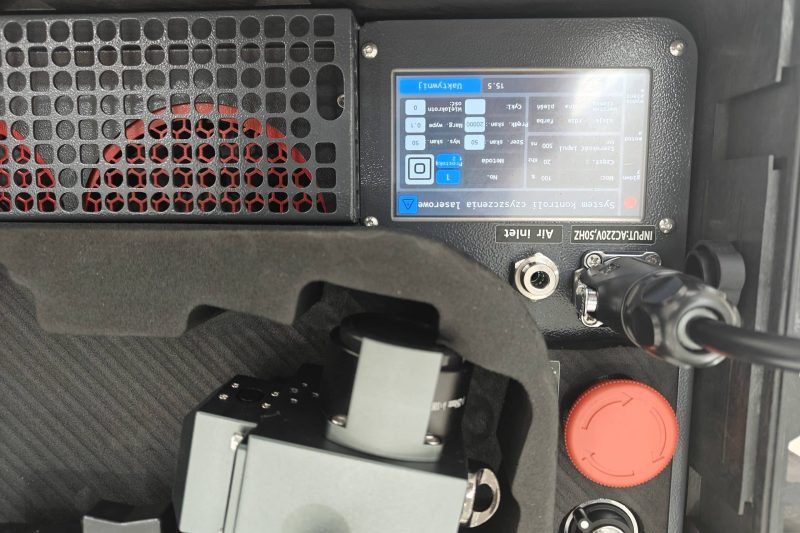
Note sulle impostazioni avanzate
Con lo sviluppo della produzione intelligente e dell'automazione industriale, l'applicazione delle apparecchiature di pulizia laser non si limita al funzionamento manuale o a semplici scenari di pulizia, ma tende a essere automatizzata, intelligente e tracciabile. Soprattutto nei settori manifatturieri di fascia alta come l'industria automobilistica, gli stampi di precisione, l'industria aerospaziale, ecc., le capacità di configurazione avanzate e le prestazioni di integrazione automatizzata dei sistemi di pulizia laser sono diventate la chiave per migliorare l'efficienza delle linee di produzione, ridurre i costi di manodopera e garantire l'uniformità della pulizia.
Interfacciamento con sistemi di automazione
Le moderne apparecchiature di pulizia laser generalmente supportano l'integrazione con una varietà di piattaforme di automazione industriale, come la connessione a sistemi robotici, sistemi di controllo PLC, sistemi di posizionamento visivo, ecc., tramite interfacce di comunicazione (EtherCAT, Profinet, Modbus, ecc.). Possono raggiungere:
- Pulizia laser assistita da robot: il braccio robotico aziona la testina di pulizia per movimenti precisi, realizzando la pulizia automatizzata di grandi quantità di superfici curve complesse.
- Controllo del percorso e collegamento della testa di scansione: con una piattaforma di collegamento multiasse o una guida di scorrimento automatica, il percorso di scansione laser viene controllato per ottenere una pulizia efficiente e continua di pezzi di grandi dimensioni.
- Meccanismo di attivazione remota e di interblocco di sicurezza: garantiscono la sicurezza operativa e la stabilità delle apparecchiature e supportano meccanismi automatici anti-allagamento e di arresto anomalo.
Registrazione e analisi dei dati
I sistemi di pulizia laser di fascia alta sono solitamente dotati di moduli di registrazione dati di livello industriale per registrare i parametri principali di ogni operazione di pulizia, come potenza, frequenza, larghezza di impulso, tempo di traiettoria, ecc., per facilitare l'analisi successiva e la tracciabilità della qualità:
- Archiviazione dei parametri di pulizia: i dati di pulizia corrispondenti a ciascun lotto di pezzi vengono memorizzati automaticamente ed è possibile tracciare lo stato della pulizia in ogni momento.
- Analisi della qualità: in combinazione con il rilevamento dell'effetto di pulizia (ad esempio tramite riconoscimento delle immagini o feedback dei sensori), viene creato un database per diverse combinazioni di materiali e parametri, che agevola l'ottimizzazione del processo.
- Diagnosi remota e aggiornamento del sistema: tramite la piattaforma cloud o il server industriale, vengono supportati gli aggiornamenti software da remoto e la diagnosi dei guasti per migliorare l'efficienza della risposta post-vendita.
Soluzioni personalizzate
In risposta alle particolari esigenze di pulizia dei clienti, il sistema di pulizia laser può essere personalizzato in modo flessibile con sistemi di fissaggio esclusivi, piattaforme rotanti, linee di trasporto a rulli, sistemi di carico e scarico automatici, ecc.:
- Speciale design del dispositivo di fissaggio: migliora l'efficienza del fissaggio e garantisce che il raggio laser copra stabilmente l'area da pulire.
- Elaborazione automatizzata in batch, come l'aggancio a linee di assemblaggio automatiche per ottenere un funzionamento continuo multi-stazione in scenari industriali;
- Regolazione flessibile del processo: il sistema supporta preimpostazioni dei parametri di processo multi-task, che facilitano il passaggio rapido tra diverse attività di pulizia.
Grazie a impostazioni avanzate e all'integrazione automatizzata, le apparecchiature di pulizia laser non sono più uno strumento isolato e autonomo, ma una parte fondamentale della linea di produzione intelligente. Non solo migliorano il ritmo di produzione e l'uniformità della pulizia, ma aiutano anche le aziende a costruire un sistema di produzione intelligente sostenibile, altamente flessibile e di alto livello.
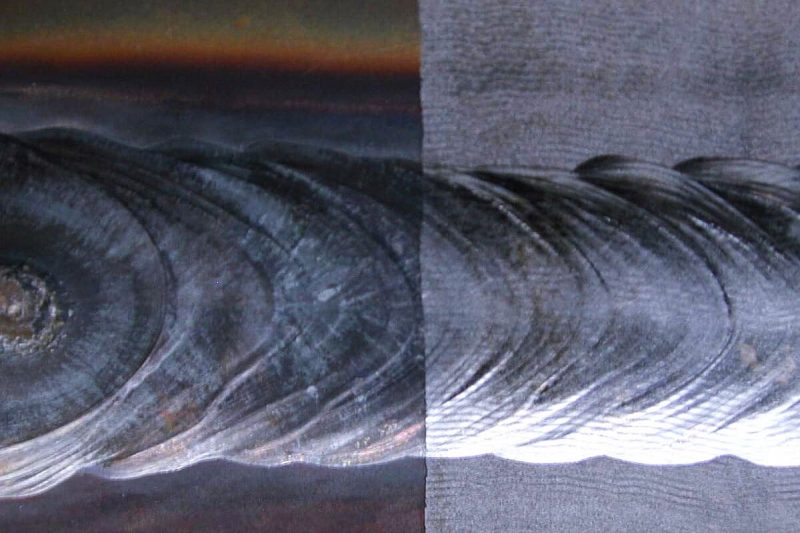
Riassumere
Le prestazioni eccezionali di una macchina per la pulizia laser a impulsi, con prestazioni eccellenti e funzionamento stabile, dipendono non solo dall'elevata qualità del corpo del generatore laser, ma anche dalla pianificazione scientifica e dalla configurazione razionale dell'intero sistema, dall'impostazione all'applicazione. Che si tratti di una pulizia complessa della ruggine metallica, della rimozione dello strato di ossido o del trattamento superficiale di stampi ad alta precisione, per ottenere effetti di pulizia efficienti, sicuri e controllabili, è necessario garantire che tutte le fasi del processo siano eseguite rigorosamente:
Dalla valutazione iniziale delle condizioni di pulizia (inclusi tipo di materiale, caratteristiche dei contaminanti e target di pulizia), alla selezione del tipo di generatore laser e dei parametri di potenza appropriati, all'abbinamento del sistema di raffreddamento e dell'apparecchiatura di depurazione dei gas di scarico appropriati, fino al successivo allineamento del raggio laser, al debug dei parametri, alla calibrazione del sistema e alla protezione di sicurezza, ecc., ogni passaggio influirà direttamente sull'efficienza operativa, sulla precisione di pulizia e sulla durata utile dell'apparecchiatura. Un processo di impostazione scientifico può non solo migliorare l'uniformità della pulizia, ma anche ridurre significativamente i costi operativi e la frequenza di manutenzione, il che è fondamentale per garantire il funzionamento efficiente e a lungo termine dell'azienda.
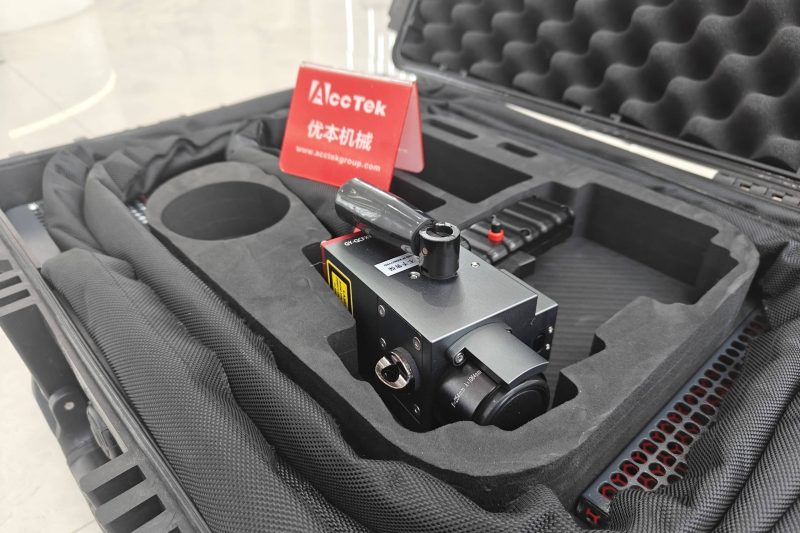
Ottieni soluzioni laser
Se stai cercando una soluzione di trattamento superficiale laser davvero performante, intelligente e adattabile, Laser AccTek Sarà la vostra scelta ideale. Ci impegniamo a fornire ai clienti globali sistemi di pulizia laser pulsata che coprono molteplici settori e scenari. Le apparecchiature coprono una varietà di livelli di potenza da 50 W a 500 W, adatti ad applicazioni in tutte le condizioni, dalla pulizia di macchie leggere alla rimozione di ruggine da inquinamento intenso. Ancora più importante, supportiamo anche servizi personalizzati per l'intero processo e possiamo configurare in modo flessibile dispositivi esclusivi, sistemi di automazione e interfacce operative in base alla forma del pezzo, alle esigenze di pulizia e all'ambiente della linea di produzione.
Inoltre, disponiamo di un team di ingegneri tecnici esperti in grado di fornire ai clienti una valutazione pre-vendita personalizzata delle condizioni, assistenza all'installazione da remoto, formazione operativa e supporto tecnico continuo per garantire un utilizzo fluido, efficiente e senza preoccupazioni in ogni fase del processo. Scegliere noi significa scegliere professionalità, efficienza e valore a lungo termine. Benvenuti a Contattaci per soluzioni di test gratuite o consulenze personalizzate.
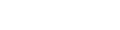
Informazioni sui contatti
- [email protected]
- [email protected]
- +86-19963414011
- N. 3 Zona A, zona industriale di Lunzhen, città di Yucheng, provincia di Shandong.
Ottieni soluzioni laser