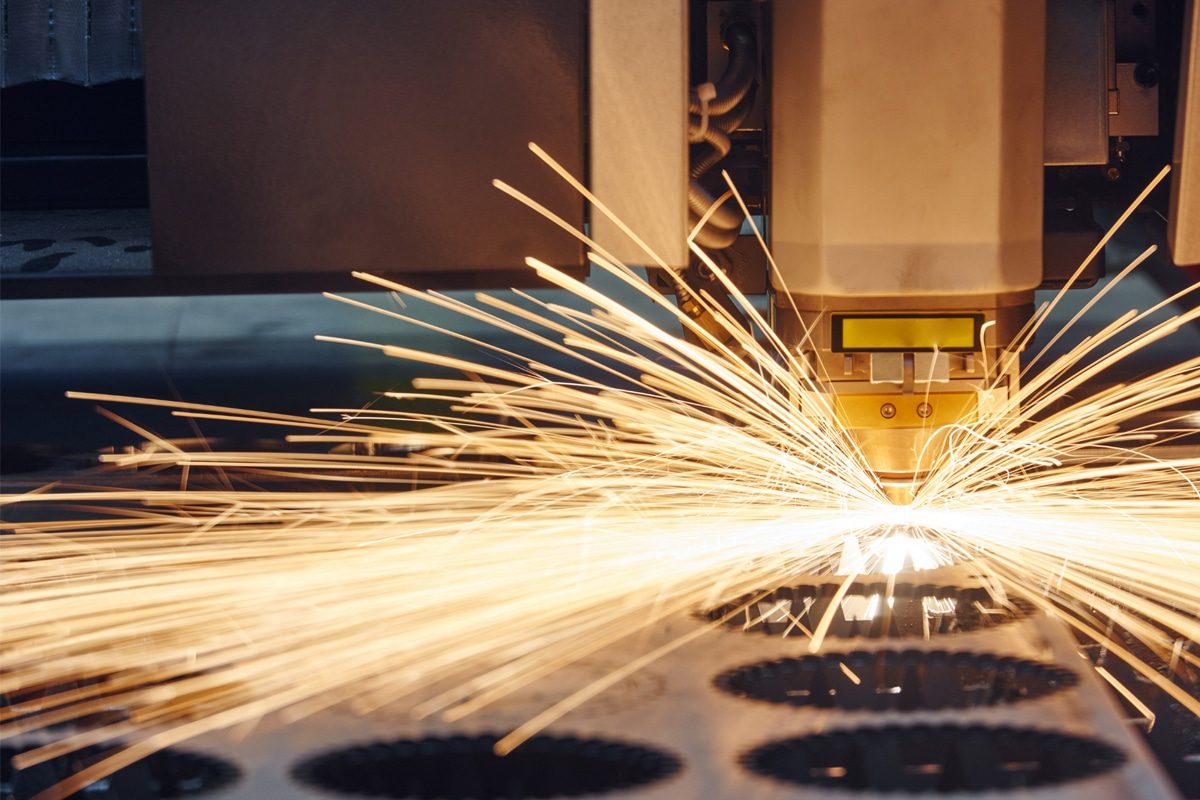
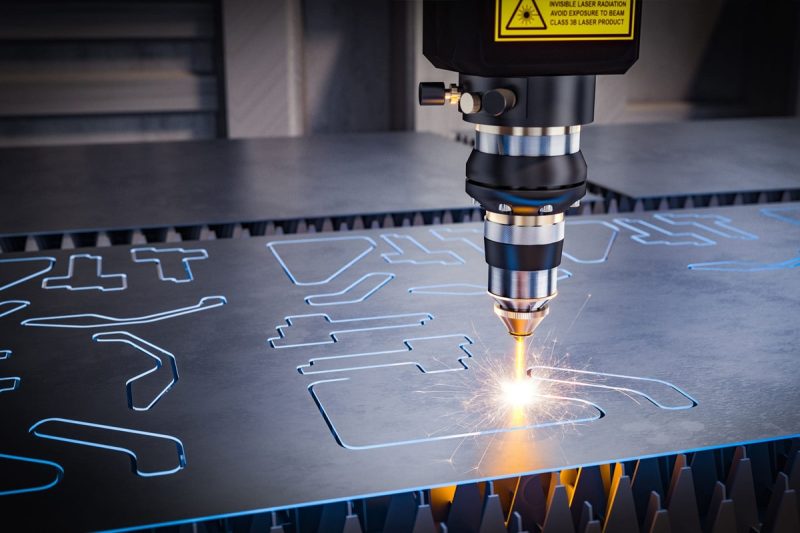
Introduction to Laser and Plasma Cutting
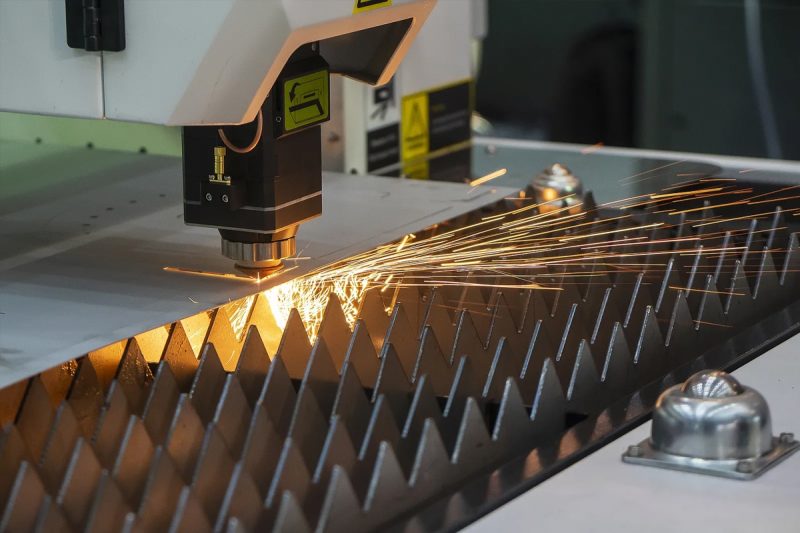
Working Principle: Laser Cutting VS Plasma Cutting
Laser Cutting Working Principle
Laser cutting utilizes a high-powered, focused beam of light to cut or engrave materials with exceptional precision. The term “LASER” stands for Light Amplification by Stimulated Emission of Radiation. Here’s how the process works:
- Laser Generation: A laser source, such as a fiber laser or CO2laser, generates a coherent beam of monochromatic light. This light is produced by exciting atoms in a lasing medium, causing them to release photons in unison.
- Beam Focusing: The laser beam is directed through a series of mirrors and lenses that focus it onto a very small, precise point on the material’s surface. The focusing mechanism concentrates the beam to a diameter as small as 0.1 mm, increasing its intensity.
- Material Interaction: When the focused laser beam strikes the material, its energy is absorbed, causing the material to heat up rapidly. Depending on the laser’s power and the material’s properties, this can lead to:
- Melting: The material melts due to the high temperature.
- Vaporization: The material vaporizes if the temperature exceeds its boiling point.
- Burning: In some cases, especially with non-metals, the material may combust.
- Assist Gas: An assist gas, such as oxygen, nitrogen, or compressed air, is blown coaxially with the laser beam through a nozzle. The gas serves multiple purposes:
- Ejection of Molten Material: It blows away the molten or vaporized material from the kerf (cutting gap).
- Enhancing Cutting Speed: Oxygen can react exothermically with the material, increasing the cutting speed.
- Protecting the Lens: It prevents fumes and particles from contaminating the focusing lens.
- Controlled Movement: CNC (Computer Numerical Control) systems guide the laser cutting head over the material following the programmed design, ensuring precise cuts and intricate shapes.
Key Characteristics of Laser Cutting:
- Precision: Capable of cutting with tolerances as tight as ±0.1 mm.
- Edge Quality: Produces smooth, clean edges that often require no further finishing.
- Versatility: Suitable for cutting a wide range of materials, including metals, plastics, wood, and glass (depending on the laser type).
- Minimal Heat-Affected Zone: The focused beam minimizes thermal distortion of the surrounding material.
Plasma Cutting Working Principle
Plasma cutting is a process that cuts through electrically conductive materials using a jet of hot plasma. Here’s a step-by-step explanation of how plasma cutting works:
- Power Supply and Gas: A plasma cutter uses a power supply to generate a direct current (DC) arc and a gas supply (usually compressed air, nitrogen, or oxygen) that will form the plasma.
- Arc Initiation: The plasma cutter starts an arc between an electrode (situated in the torch) and the workpiece. This can be initiated by:
- Contact Start: Touching the torch tip to the workpiece to complete the circuit.
- High-Frequency Start: Using a high-voltage, high-frequency circuit to ionize the gas without contact.
- Plasma Formation: The gas is forced through a narrow nozzle inside the torch at high speed. As the gas passes through the electrical arc, it becomes ionized, transforming into plasma—a hot, electrically conductive gas.
- Material Melting and Removal:
- Melting: The plasma reaches temperatures up to 30,000℃ (54,000℉), instantly melting the metal at the point of contact.
- Blowing Away Molten Metal: The high-velocity plasma stream blows the molten metal away from the cut, creating a kerf.
- Cutting Torch Movement: Similar to laser cutting, CNC systems control the movement of the plasma torch to follow the desired cutting path accurately.
Key Characteristics of Plasma Cutting:
- Cutting Speed: Faster cutting speeds on thicker materials compared to laser cutting.
- Material Thickness: Effective for cutting metal plates up to several inches thick.
- Conductive Materials Only: Can only cut materials that conduct electricity, such as steel, stainless steel, aluminum, brass, and copper.
- Wider Kerf and Heat-Affected Zone: Results in a wider cut width and larger area affected by heat, which may lead to more material waste and potential warping.
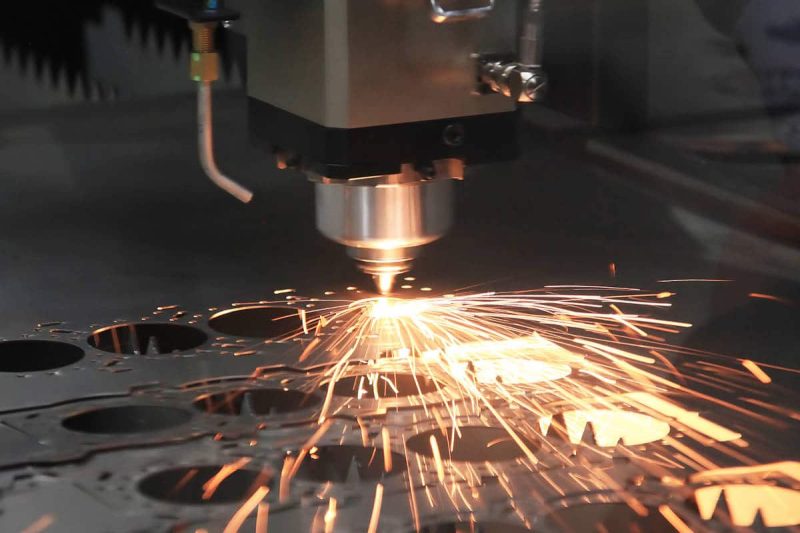
Key Differences Between Laser Cutting and Plasma Cutting
Cutting Mechanism
- Laser Cutting: Laser cutting works by focusing a high-powered laser beam onto the material’s surface, either melting, burning, or vaporizing the material. A stream of assist gas (such as nitrogen, oxygen, or compressed air) helps expel the molten material and create a clean cut. The laser beam is generated from a fiber, or CO2 laser source, depending on the material being cut. Laser cutting offers unmatched precision and is controlled by a CNC (Computer Numerical Control) system, enabling the creation of intricate and complex designs.
- Plasma Cutting: Plasma cutting, in contrast, relies on a jet of hot plasma—created by electrically ionizing a gas like oxygen or nitrogen—to melt through electrically conductive materials such as steel or aluminum. The plasma arc is generated by passing gas through a nozzle while applying an electrical arc, creating a stream hot enough to melt the material. Plasma cutting is effective for thicker metals but does not offer the same level of precision as laser cutting.
Material Compatibility
- Laser Cutting: Laser cutting is highly versatile when it comes to material compatibility. It can cut both metallic and non-metallic materials. Fiber lasers are primarily used for cutting metals like steel, stainless steel, aluminum, brass, and copper. CO2 laser cutting machines, on the other hand, are more suitable for cutting non-metals like wood, plastic, fabric, and glass. However, fiber lasers are most efficient for cutting metals, and they cannot cut materials that are highly reflective, like aluminum, without adjustments to laser power and settings.
- Plasma Cutting: Plasma cutting is limited to electrically conductive materials. This includes metals such as carbon steel, stainless steel, aluminum, brass, copper, and other alloys. It is unable to cut non-conductive materials like plastics, wood, or glass, limiting its application to metalworking industries. For cutting thicker metals, plasma cutting offers a faster, more efficient option.
Cutting Speed
- Laser Cutting: Laser cutting generally excels at cutting thin materials with speed and precision. For metals with a thickness under 6mm, laser cutting is significantly faster than plasma cutting, especially when high-precision cuts are required. However, as the material thickness increases, the cutting speed of laser cutting decreases. Laser cutting is best suited for detailed work where precision is more important than raw speed.
- Plasma Cutting: Plasma cutting, by contrast, is faster than laser cutting when it comes to thicker materials, especially metals over 10mm in thickness. Plasma cutters can cut through these thick materials at high speeds, making them ideal for heavy-duty industrial applications like shipbuilding or construction. For thicker metals, plasma cutting can be more time-efficient than laser cutting.
Cutting Thickness
- Laser Cutting: Laser cutting is highly effective for thin materials, typically up to 30mm in thickness for metals when using high-power fiber lasers. Beyond this thickness, the efficiency and speed of laser cutting decrease, and cutting may become less practical due to power limitations and potential material deformation from heat.
- Plasma Cutting: Plasma cutting excels when cutting thicker materials, often up to 50mm or more depending on the power of the plasma cutter. This makes plasma cutting a better choice for applications where cutting thick metals is required, such as in heavy fabrication industries. For materials over 30mm, plasma cutting is generally faster and more cost-effective than laser cutting.
Precision and Accuracy
- Laser Cutting: One of the main advantages of laser cutting is its precision. The narrow laser beam, combined with CNC controls, allows for highly accurate cuts with tight tolerances, often within ±0.1 mm. This makes laser cutting ideal for intricate designs, detailed components, and applications where high precision is crucial, such as in the aerospace, electronics, and automotive industries. The narrow kerf (cut width) further reduces material waste.
- Plasma Cutting: While plasma cutting is effective for thicker materials, it is less precise than laser cutting. Plasma cutters create a wider kerf, which limits the ability to achieve fine, intricate cuts. Although suitable for many industrial applications, plasma cutting may require post-processing such as grinding or sanding to improve the cut quality and remove burrs, especially for detailed work or thin materials.
Heat-Affected Zone (HAZ)
- Laser Cutting: Laser cutting produces a smaller heat-affected zone (HAZ) compared to plasma cutting. The highly concentrated laser beam melts a small portion of the material without significantly affecting the surrounding area. This minimized HAZ leads to less thermal distortion, reducing the risk of warping or deforming the material, which is especially important for thin or delicate workpieces.
- Plasma Cutting: Plasma cutting generates a much larger heat-affected zone due to the high temperatures of the plasma arc. This larger HAZ increases the likelihood of material warping or distortion, particularly when cutting thinner materials. For thicker metals, the HAZ may be less of an issue, but for precision applications or materials prone to heat damage, laser cutting is the better option.
Edge Quality
- Laser Cutting: Laser cutting produces superior edge quality with smooth, clean cuts that often require no further finishing. The narrow kerf and minimal heat impact result in edges that are burr-free and precise. This is particularly advantageous for applications where aesthetics or a high-quality finish is required.
- Plasma Cutting: Plasma cutting, while fast, often produces rougher edges compared to laser cutting. The wider kerf and greater HAZ can result in dross or slag (residual material) forming on the edges, requiring additional post-processing to achieve a smooth finish. For applications where edge quality is not critical, plasma cutting remains a suitable option.
Conclusion: Key Differences
- Cutting Mechanism: Laser cutting uses a focused beam of light, while plasma cutting relies on an ionized gas (plasma) stream.
- Material Compatibility: Laser cutting can handle both metals and non-metals, while plasma cutting is limited to electrically conductive metals.
- Cutting Speed: Laser cutting is faster for thin materials, whereas plasma cutting excels at cutting thicker metals quickly.
- Cutting Thickness: Laser cutting is more efficient for thinner materials, while plasma cutting handles thick metals more effectively.
- Precision and Accuracy: Laser cutting offers higher precision and accuracy with cleaner cuts, while plasma cutting is less precise and may require post-processing.
- Heat-Affected Zone (HAZ): Laser cutting has a smaller HAZ, reducing thermal distortion, whereas plasma cutting creates a larger HAZ, increasing the risk of warping.
- Edge Quality: Laser cutting delivers smooth, high-quality edges, while plasma cutting may produce rougher edges that require additional finishing.
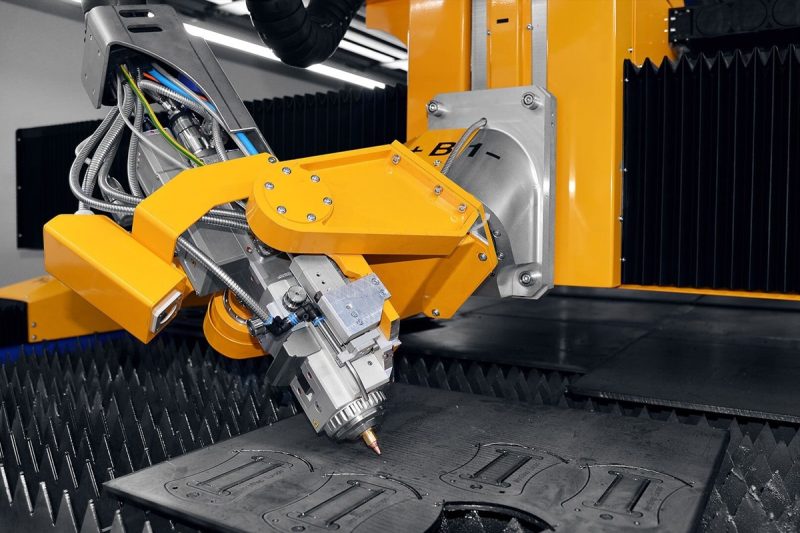
Application: Laser Cutting VS Plasma Cutting
Laser Cutting Applications
Laser cutting is known for its high precision, fine detailing, and clean cuts, making it ideal for industries and applications where accuracy and quality are paramount. Laser cutting is widely used in the following industries:
- Aerospace: In aerospace manufacturing, components must meet extremely high precision standards. Laser cutting is the preferred method for cutting intricate parts made from lightweight metals like titanium and aluminum, as well as for creating small, detailed parts with minimal tolerances.
- Automotive: Laser cutting is widely employed in the automotive industry to cut complex parts, including sheet metal components, dashboard panels, and engine parts. Its precision allows for the creation of customized and detailed pieces that meet the high-performance requirements of modern vehicles.
- Electronics: The electronics industry often requires delicate and intricate cuts for small components like printed circuit boards (PCBs). Laser cutting’s ability to handle thin materials and deliver high-precision cuts with minimal heat damage makes it ideal for these applications.
- Medical Devices: Laser cutting is used to manufacture medical devices such as surgical instruments, implants, and other precision components that require intricate detailing. Its high accuracy ensures that medical devices meet stringent regulatory standards.
- Jewelry and Fashion: Laser cutting is frequently used for cutting and engraving in the jewelry and fashion industries. Whether cutting precious metals for fine jewelry or intricate patterns on fabrics and leather, laser technology provides clean and precise cuts that enhance the aesthetic appeal of products.
- Textile and Fabric Cutting: CO2 lasers are commonly used in the textile industry to cut fabrics, leather, and synthetic materials. Laser cutting allows for fast, accurate, and non-contact cutting, which is crucial for delicate materials that can be easily damaged.
- Signage and Display Manufacturing: Laser cutting is also popular in the signage industry for creating detailed logos, intricate designs, and lettering on materials such as acrylic, plastic, and wood. The clean edges and precise cuts are ideal for visually appealing displays.
Plasma Cutting Applications
Plasma cutting is known for its speed and ability to cut through thick, conductive materials efficiently. It is typically used in heavy-duty industries where precision is not as critical but high-speed, large-scale cutting is required. Plasma cutting is commonly used in the following applications:
- Construction: Plasma cutting is widely used in the construction industry to cut thick steel plates, structural beams, and metal reinforcements. Its ability to cut through thick materials quickly makes it ideal for large-scale projects like bridges, buildings, and other infrastructure.
- Shipbuilding: In the shipbuilding industry, plasma cutting is essential for cutting thick steel plates used in the construction of ships. The speed and cost-effectiveness of plasma cutting make it the go-to method for fabricating large metal components, including hulls and frames.
- Metal Fabrication: Plasma cutting is popular in metal fabrication shops for cutting thick metal sheets, pipes, and frames. Fabricators appreciate the speed and power of plasma cutting, especially for jobs that involve high-strength materials like stainless steel or aluminum.
- Automotive Repair and Customization: While laser cutting is often used in the manufacturing of automotive parts, plasma cutting is ideal for automotive repair shops that need to cut through thick metal quickly. Plasma cutters are frequently used to repair vehicle frames, exhaust systems, and custom metalwork.
- Heavy Equipment Manufacturing: Industries that manufacture heavy machinery, such as mining, agriculture, and industrial equipment, often rely on plasma cutting to handle the thick steel and metal components that make up these machines. Plasma cutting’s ability to work through thick materials makes it highly effective for producing heavy-duty parts.
- Pipeline Construction: In the oil and gas industry, plasma cutting is used to cut and shape thick metal pipes. The ability to cut thick materials at high speeds is essential for industries that require precision in handling large pipes and metal components for transport systems.
Conclusion: Applications
- Laser Cutting is best suited for applications requiring precision, fine detailing, and high-quality finishes. It excels in industries such as aerospace, automotive, electronics, and medical device manufacturing where precision and clean edges are critical.
- Plasma Cutting is ideal for heavy-duty applications that involve cutting thicker materials quickly and efficiently. Industries such as construction, shipbuilding, and metal fabrication benefit from the speed and cost-effectiveness of plasma cutting, especially when precision is less critical.
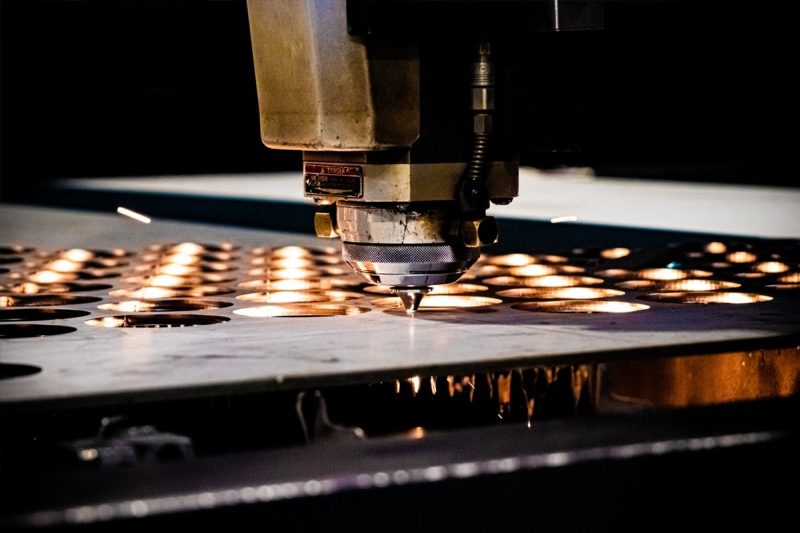
Cost Comparison: Laser Cutting VS Plasma Cutting
Initial Investment
- Laser Cutting: The initial investment for a laser cutting machine is generally higher compared to plasma cutting. Laser cutting machines, particularly fiber lasers, are known for their precision and advanced technology, which comes with a higher price tag. The cost of a fiber laser cutting machine can range from $15,000 to over $500,000 depending on power, features, and custom configurations. For example, a high-power industrial laser cutting system used in metal fabrication can cost significantly more than a basic machine designed for thinner materials or small-scale production.
- Plasma Cutting: Plasma cutting machines, by contrast, have a lower initial cost. A standard plasma cutter typically costs between $15,000 and $100,000, depending on the machine’s power and the size of the materials it can handle. Even high-end plasma cutters are generally more affordable than laser cutters. This lower price makes plasma cutting more accessible for small to medium-sized businesses that need to cut thick metals but don’t require the high precision of laser cutting.
Operational Costs
- Laser Cutting: While the initial cost of laser cutting machines is higher, the operational costs are generally lower over time. Laser cutting consumes less power during operation, especially when using efficient fiber lasers. Consumables such as assist gases (e.g., nitrogen, oxygen, or compressed air) are relatively inexpensive and contribute to the machine’s overall efficiency. Additionally, because laser cutting produces precise, clean cuts, there is often no need for post-processing, reducing labor costs associated with finishing work.
- Plasma Cutting: Plasma cutting machines have higher operational costs compared to laser cutting machines. This is primarily due to the greater energy consumption needed to generate and sustain the plasma arc. Consumables, such as electrodes and nozzles, wear out faster in plasma cutting and need to be replaced more frequently. The use of gases (such as oxygen, nitrogen, or argon) for cutting also adds to the ongoing operational costs. Furthermore, plasma-cut materials often require secondary finishing, such as grinding or sanding, to smooth rough edges, which increases labor costs.
Maintenance Costs
- Laser Cutting: Laser cutting machines require regular maintenance to ensure the longevity of the laser source and other components. Fiber lasers, however, are known for their long life and low maintenance requirements compared to older CO2 lasers. The most common maintenance tasks include cleaning the optics and replacing any worn lenses or mirrors, but these tasks are generally low-cost and infrequent. If maintained properly, fiber lasers can have minimal downtime and relatively low maintenance expenses over their operational lifespan.
- Plasma Cutting: Plasma cutters, while simpler in design, tend to have higher maintenance costs over time. Consumable parts like electrodes, nozzles, and shields need regular replacement due to wear caused by the plasma arc. Additionally, these parts may wear out faster when cutting thicker materials at higher power levels. The frequency of replacement adds to the long-term maintenance costs. While the cost per part may be low, the need for frequent replacements can drive up costs over time.
Energy Consumption
- Laser Cutting: One of the biggest advantages of laser cutting is its energy efficiency. Fiber laser cutting machines, in particular, consume significantly less electricity than plasma cutters, especially when cutting thin materials. The highly focused laser beam allows for efficient cutting without requiring excessive power. For companies looking to reduce their energy footprint and operational costs, laser cutting is often the better choice, especially for long-term usage.
- Plasma Cutting: Plasma cutting machines, while efficient for cutting thick materials, tend to consume more energy. The process of ionizing gas to create a plasma arc requires considerable electrical power, especially when working with high amperage for thicker materials. The energy consumption of a plasma cutting machine can be 2 to 3 times higher than that of a fiber laser cutter, making it more expensive to operate in the long run.
Conclusion: Cost Comparison
- Initial Investment: Laser-cutting machines have a higher upfront cost but offer superior precision and capabilities. Plasma-cutting machines are more affordable initially, making them ideal for businesses focusing on thick materials without the need for extreme precision.
- Operational Costs: Laser cutting has lower operational costs due to fewer consumables, efficient energy use, and minimal post-processing requirements. Plasma cutting, though less expensive to purchase, incurs higher operational costs due to frequent consumable replacement and higher energy consumption.
- Maintenance Costs: Laser cutting generally requires less maintenance, especially with more durable fiber lasers. Plasma cutting, while simple, demands frequent part replacements, leading to higher long-term maintenance costs.
- Energy Consumption: Laser cutting, particularly with fiber lasers, is much more energy-efficient than plasma cutting, which requires more power to operate.
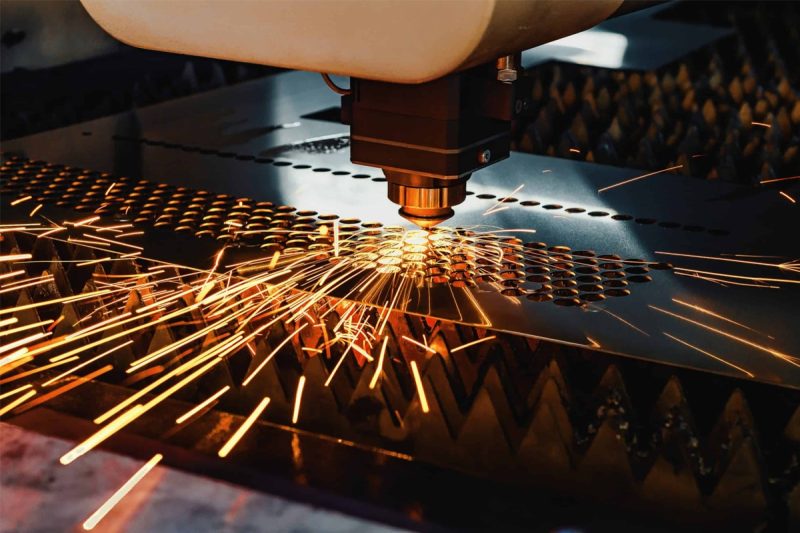
Environmental Impact: Laser Cutting VS Plasma Cutting
Energy Efficiency
- Laser Cutting: Laser cutting, especially fiber lasers, is known for its high energy efficiency. Fiber lasers can convert electrical energy into light with minimal waste, using less power to produce the required cutting force. This reduced energy consumption makes laser cutting more environmentally friendly, particularly when cutting thin to medium-thickness materials. Additionally, the precise and controlled nature of laser cutting reduces material waste, contributing to a more sustainable production process.
- Plasma Cutting: Plasma cutting, while effective for cutting thicker materials, is generally less energy-efficient compared to laser cutting. The process of generating and sustaining the plasma arc consumes a significant amount of electricity, especially when cutting thick metal plates. This higher energy demand results in a larger carbon footprint, making plasma cutting a less eco-friendly option in terms of energy consumption.
Emissions and Air Quality
- Laser Cutting: Laser cutting typically produces fewer harmful emissions during operation. While gases like nitrogen or oxygen are used in the cutting process, they do not emit significant pollutants. Fiber lasers, in particular, have minimal environmental impact in terms of air quality. However, when cutting certain materials, such as plastics or composites, laser cutting may release fumes that require proper ventilation or filtration systems to protect workers and reduce air pollution.
- Plasma Cutting: Plasma cutting emits more pollutants due to the ionization of gases, including oxygen, nitrogen, or argon, during the cutting process. The heat generated by plasma cutting can cause the release of hazardous fumes, especially when cutting coated or treated metals. These fumes may contain harmful particulates and gases, such as nitrogen oxides (NOx), which can contribute to air pollution and pose health risks to operators. Therefore, plasma cutting typically requires more robust ventilation and filtration systems to mitigate its impact on air quality.
Material Waste
- Laser Cutting: One of the key environmental advantages of laser cutting is its ability to produce minimal material waste. The precision of laser cutting allows for tighter tolerances and smaller kerfs (cut widths), meaning less material is lost in the cutting process. This not only reduces the amount of scrap produced but also improves the efficiency of material usage, making laser cutting a more sustainable choice, particularly for expensive materials.
- Plasma Cutting: Plasma cutting tends to produce more material waste due to its wider kerf and the rougher edges it leaves on cut materials. The larger heat-affected zone (HAZ) may also lead to deformation or warping, resulting in additional material waste. Moreover, plasma-cut parts often require post-processing to remove burrs and rough edges, leading to further material losses. This makes plasma cutting less efficient and potentially more wasteful in terms of raw material usage.
Consumables and Resource Use
- Laser Cutting: Laser cutting, particularly with fiber lasers, has relatively low consumable requirements. Fiber lasers do not require frequent replacements of components, such as electrodes or nozzles, making them more environmentally sustainable over time. The assist gases used in laser cutting (nitrogen or oxygen) are also widely available and have a lower environmental impact compared to the gases used in plasma cutting.
- Plasma Cutting: Plasma cutting relies more heavily on consumables, including electrodes, nozzles, and shields, which need regular replacement due to wear and tear. This frequent need for consumable parts not only increases operational costs but also adds to resource consumption and waste production. The disposal of worn components, especially if not properly recycled, contributes to the environmental footprint of plasma cutting.
Noise Pollution
- Laser Cutting: Laser cutting operates relatively quietly compared to other industrial cutting methods. The cutting process produces minimal noise, which contributes to a safer and more pleasant working environment. Reduced noise pollution is also an environmental benefit, particularly in urban or residential areas where noise regulations may be strict.
- Plasma Cutting: Plasma cutting generates more noise, particularly when cutting thicker materials at high power. The noise produced by the plasma arc and the expulsion of molten metal can contribute to noise pollution in the workplace, necessitating hearing protection for operators. Excessive noise levels can also disturb surrounding environments, making plasma cutting less desirable in noise-sensitive areas.
Conclusion: Environmental Impact
- Energy Efficiency: Laser cutting, especially with fiber lasers, is more energy-efficient than plasma cutting, making it a greener option.
- Emissions: Plasma cutting emits more harmful fumes and particulates, particularly when cutting coated or treated metals. Laser cutting produces fewer emissions but may still require proper ventilation for certain materials.
- Material Waste: Laser cutting produces less waste due to its precision, while plasma cutting generates more scrap and may require additional post-processing.
- Consumables: Plasma cutting requires more consumable parts, contributing to higher resource use and waste, while laser cutting uses fewer consumables.
- Noise Pollution: Laser cutting is quieter and produces less noise pollution compared to the louder plasma cutting process.
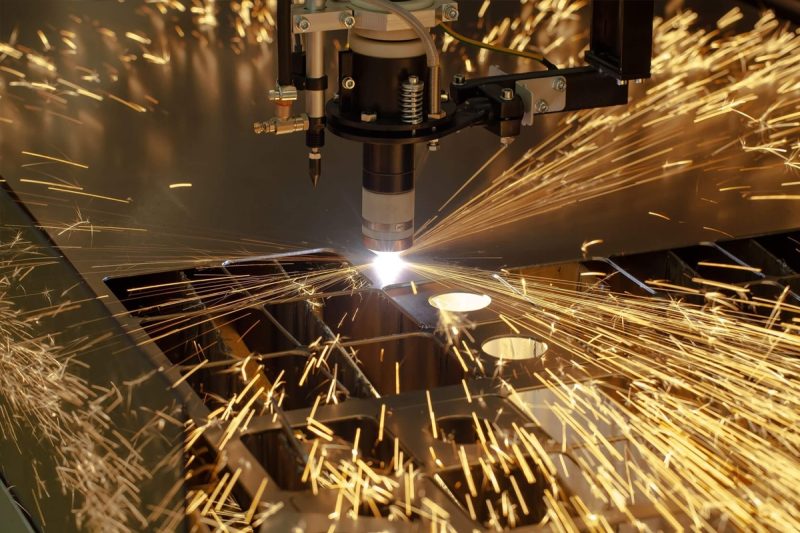
Summary
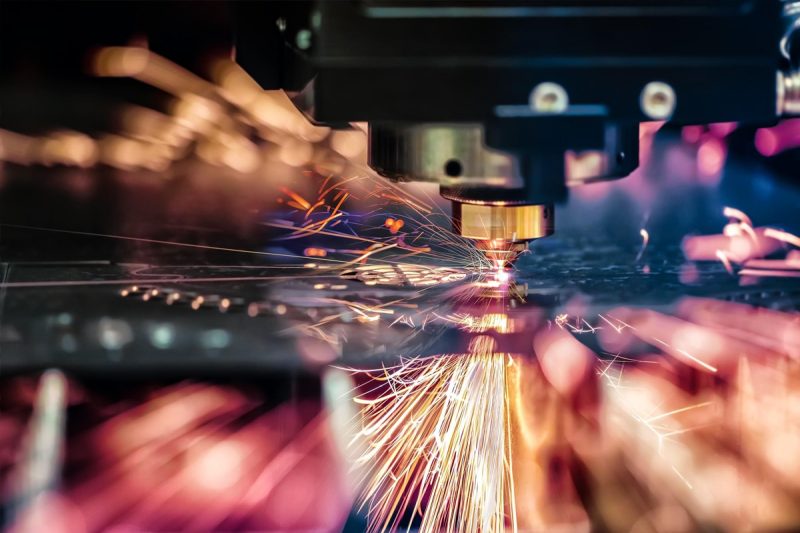
Get Laser Solutions with AccTek Laser
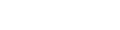
- [email protected]
- [email protected]
- +86-19963414011
- No. 3 Zone A, Lunzhen Industrial Zone,Yucheng City , Shandong Province.