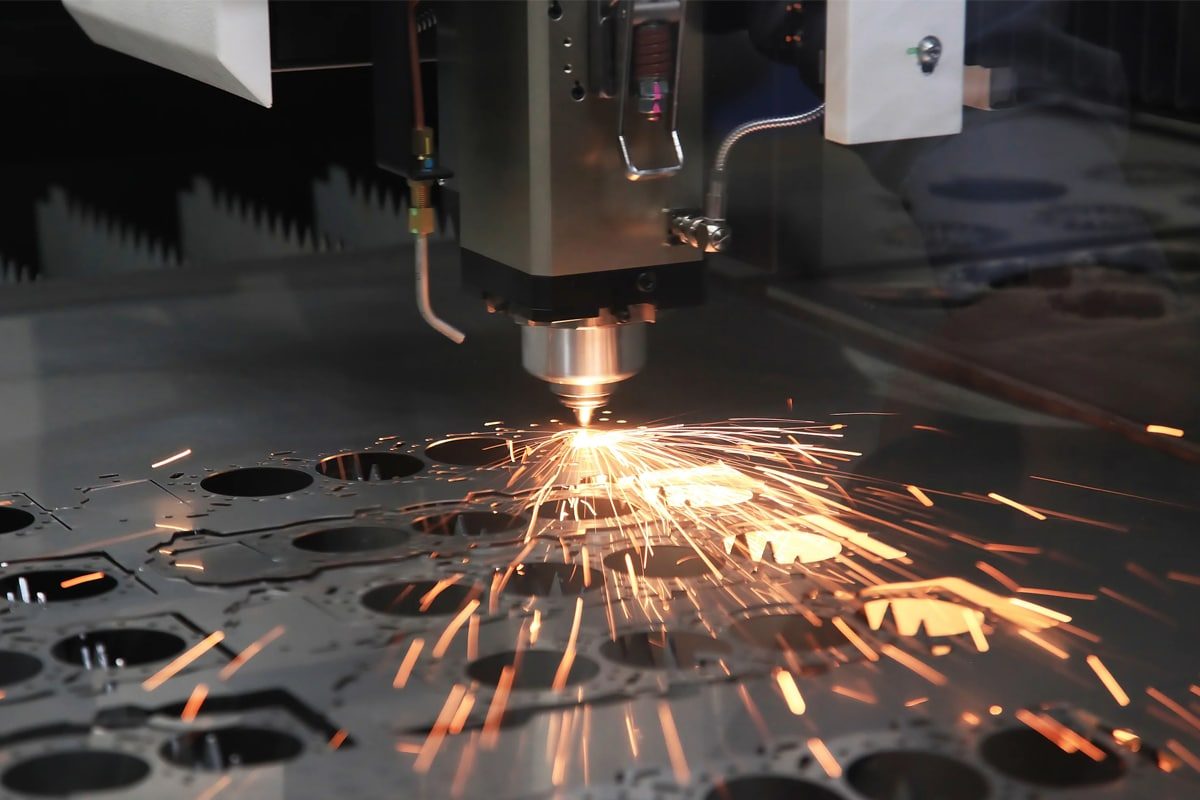
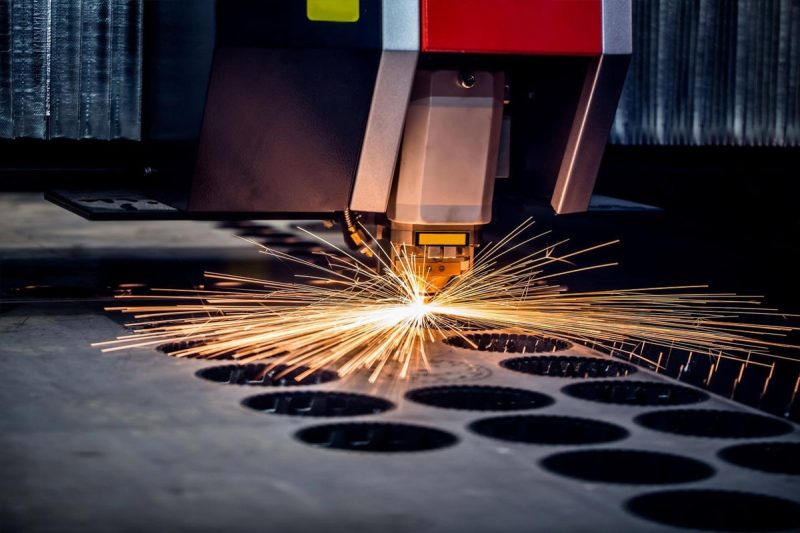
Introduction to Laser Cutting Machines
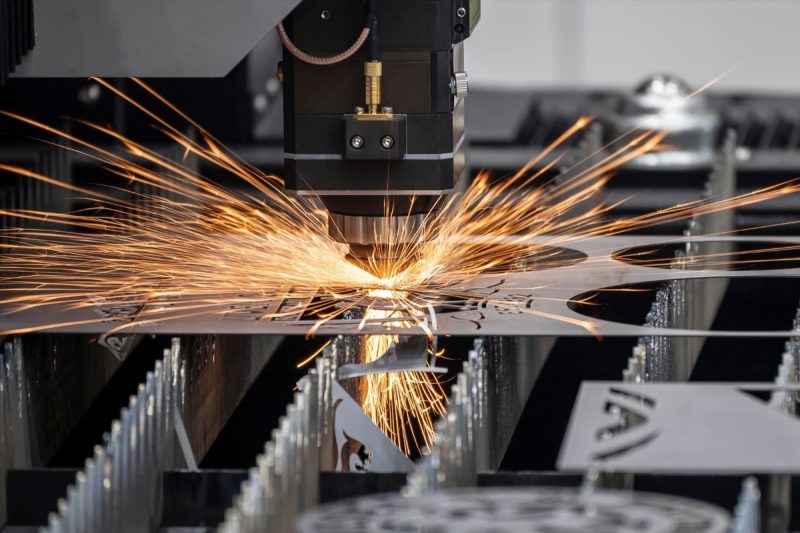
Fiber Laser Cutting Machines
How They Work
Advantages
- High Efficiency and Power: Fiber lasers are known for their high electrical-to-optical efficiency, often exceeding 30%. This efficiency translates into lower operating costs and energy consumption compared to other laser types. The ability to generate high power levels makes fiber lasers suitable for cutting thick materials while maintaining speed and quality.
- Superior Beam Quality: The beam quality of fiber lasers is exceptional, characterized by a small beam divergence and a consistent beam profile. This results in a smaller focal diameter, allowing for finer cuts, higher precision, and reduced heat-affected zones. The superior beam quality also enables fiber lasers to cut reflective materials like aluminum, brass, and copper with minimal risk of back reflections damaging the laser source.
- Low Maintenance and Durability: Fiber lasers have a solid-state design with no moving parts or mirrors in the laser source, reducing the need for maintenance and alignment. The optical fibers are flexible and robust, capable of withstanding harsh industrial environments. This reliability leads to higher machine uptime and lower maintenance costs over the lifespan of the equipment.
- Compact and Flexible Design: The compact size of the fiber laser source allows for a smaller overall machine footprint, saving valuable floor space in manufacturing facilities. The flexibility of the fiber delivery system enables easier integration into various machine designs and configurations, including robotic arms and multi-axis systems.
- Cost-Effective Operation: Due to their high efficiency and low maintenance requirements, fiber laser cutting machines offer cost-effective operation. The reduced energy consumption and minimal need for consumables like laser gas or replacement parts contribute to lower operating expenses.
- Environmental Benefits: Fiber lasers do not require laser gases for operation, eliminating the need for reducing environmental impact. The high efficiency also means less energy is wasted as heat, aligning with sustainability goals and reducing the carbon footprint of manufacturing processes.
Applications
- Metal Fabrication: Fiber laser cutting machines excel in cutting a wide range of metals, making them ideal for metal fabrication industries. They are used to cut steel, stainless steel, aluminum, brass, copper, and other alloys with high precision and speed. Typical applications include the production of metal cabinets, enclosures, frames, and structural components.
- Automotive Industry: In the automotive sector, fiber lasers are utilized for cutting complex parts and components with tight tolerances. They enable manufacturers to produce intricate designs for body panels, chassis parts, exhaust systems, and other critical components efficiently. The speed and precision of fiber lasers contribute to shorter production cycles and improved product quality.
- Aerospace and Aviation: The aerospace industry demands high-precision cutting of materials like titanium and aluminum alloys. Fiber laser cutting machines meet these requirements by providing clean cuts with minimal thermal distortion. Applications include the fabrication of aircraft structural components, engine parts, and intricate assemblies that require strict adherence to design specifications.
- Electronics and Electrical Manufacturing: Fiber lasers are used in the electronics industry for cutting thin metal sheets used in electrical enclosures, circuit boards, and components. The ability to cut fine features without damaging sensitive materials makes fiber lasers suitable for producing intricate parts required in electronic devices and equipment.
- Medical Device Manufacturing: In the medical field, fiber lasers are employed to cut components for medical devices and surgical instruments. The high precision and clean-cutting capabilities ensure that parts meet stringent medical standards. Applications include the production of implants, surgical tools, and diagnostic equipment components.
- Architectural and Artistic Applications: Architects and artists utilize fiber laser cutting machines to produce intricate metalwork for decorative panels, sculptures, and architectural elements. The precision and flexibility of fiber lasers enable the realization of complex designs that would be difficult or impossible with traditional cutting methods.
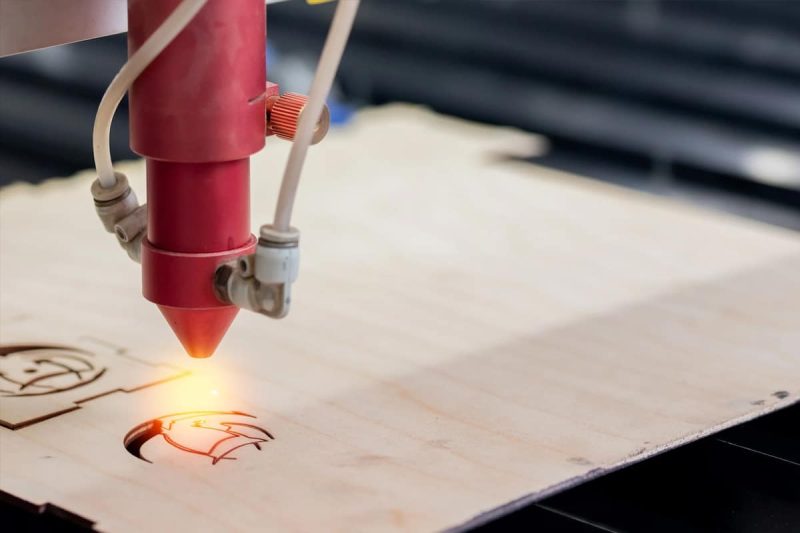
CO2 Laser Cutting Machines
How They Work
Advantages
- Versatility Across Materials: One of the most significant advantages of CO2 laser cutting machines is their ability to process a wide variety of materials. They are exceptionally effective at cutting non-metallic materials such as wood, acrylic, glass, paper, textiles, leather, and certain plastics. With appropriate configurations, they can also cut thin metals, making them highly versatile for different industrial applications.
- High-Quality Edge Finishes: CO2 lasers produce smooth and clean cuts with minimal burring or rough edges, especially on non-metal materials. The laser’s interaction with materials results in a polished finish that often requires little to no post-processing, saving time and reducing labor costs.
- Cost-Effective Operation for Non-Metals: For industries primarily working with non-metal materials, CO2 laser cutting machines offer a cost-effective solution. The initial investment and operational costs are generally lower compared to fiber lasers when processing non-metals. The mature technology and widespread availability of consumables contribute to reduced maintenance expenses.
- Proven and Reliable Technology: CO2 laser technology has been in use for several decades, leading to a well-understood and reliable system. The components and operational principles are well-established, resulting in machines with long lifespans and consistent performance. This reliability translates to reduced downtime and increased productivity.
- Large Cutting Area Capability: CO2 laser cutting machines are available in various sizes, including large-format systems capable of handling oversized materials. This is particularly beneficial for industries requiring the processing of large sheets or rolls of material, such as textiles and signage.
- Multi-Functional Use: Beyond cutting, CO2 lasers are also adept at engraving and marking, adding versatility to their functionality. They can engrave detailed images, text, and patterns onto materials, enabling businesses to offer a broader range of services with a single machine.
Applications
- Advertising and Signage Industry: CO2 laser cutting machines are extensively used in the advertising and signage industry for creating eye-catching displays, signboards, and promotional materials. They can cut and engrave acrylic, wood, and plastics to produce intricate designs, letters, logos, and 3D effects with high precision and clarity.
- Textile and Fashion Industry: In the textile and fashion sectors, CO2 lasers are employed to cut fabrics, leather, and synthetic materials with precision and speed. The non-contact cutting method prevents fraying and distortion of delicate fabrics, allowing for the production of intricate patterns, lacework, and custom designs in garments, accessories, and upholstery.
- Packaging Industry: CO2 laser cutting machines play a vital role in the packaging industry by cutting and scoring materials like cardboard, paper, and thin plastics. They enable the creation of custom packaging solutions with complex designs, perforations, and engravings, enhancing both functionality and aesthetic appeal.
- Arts, Crafts, and Personalized Products: Artists and craftsmen utilize CO2 lasers for creating detailed and precise cuts and engravings on materials like wood, glass, paper, and acrylic. Applications include custom jewelry, decorative items, model making, scrapbooking, and personalized gifts. The ability to reproduce intricate designs makes these machines invaluable for bespoke creations.
- Architectural Modeling and Design: Architects and designers use CO2 laser cutters to produce accurate scale models and prototypes. The machines can cut complex components from materials such as foam board, balsa wood, and acrylic, aiding in visualizing and presenting architectural concepts and interior designs.
- Educational Institutions: Educational facilities employ CO2 laser cutting machines for teaching purposes and research projects. They provide hands-on experience with advanced manufacturing technology, fostering creativity and technical skills in students studying engineering, design, and the arts.
- Medical Device Manufacturing: In the medical field, CO2 lasers are used to cut and engrave components made from plastics and other non-metal materials for medical devices and equipment. Applications include producing parts for diagnostic instruments, surgical tools, and custom prosthetics with high precision and cleanliness standards.
- Rubber Stamp and Seal Making: The ability of CO2 lasers to engrave and cut rubber materials makes them ideal for producing custom rubber stamps and seals. They can create detailed and durable stamp designs for business, educational, or personal use, with quick turnaround times.
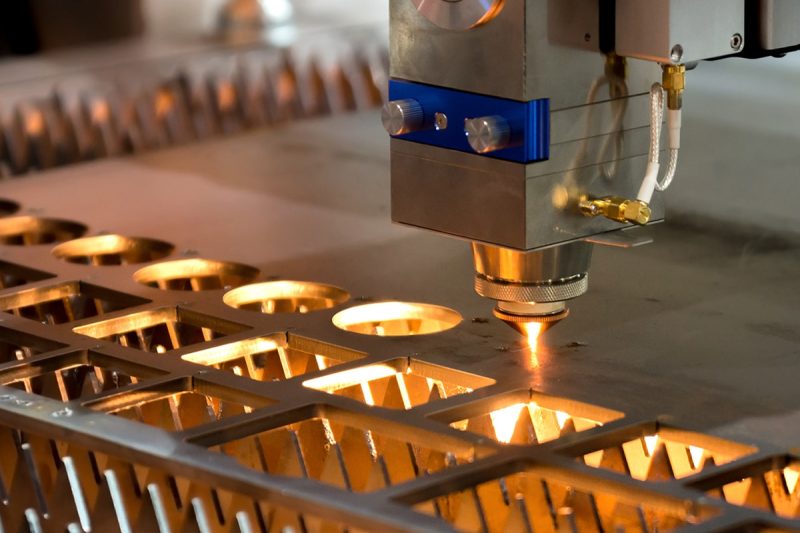
Factors Influencing the Price
Type of Laser Source
The type of laser source is one of the most significant factors influencing the price of a laser-cutting machine. The two main types are fiber lasers and CO2 lasers, each with distinct characteristics and cost implications.
- Fiber Lasers: Generally, fiber laser cutting machines are more expensive upfront compared to CO2 lasers. This is due to their advanced technology, higher efficiency, and superior performance in cutting metals. Fiber lasers have a longer lifespan, lower maintenance requirements, and faster cutting speeds for metal materials, which can justify the higher initial investment for businesses focusing on metal fabrication.
- CO2 Lasers: CO2 laser cutting machines are typically less expensive initially and are highly versatile, capable of cutting a wide range of non-metal materials such as wood, acrylic, glass, textiles, and certain plastics. However, they may have higher operating costs over time due to the need for regular maintenance and consumables like laser gases and mirrors.
Laser Power
Laser power, measured in watts (W), directly affects the machine’s cutting capabilities and is a crucial factor in determining its price.
- Low-Power Machines: Suitable for cutting thin materials like sheet metal or non-metal materials. These machines are generally less expensive and are ideal for small businesses or startups with basic cutting needs.
- Medium Power Machines: Offer greater versatility, allowing for cutting a broader range of material thicknesses. The price increases with higher power due to enhanced cutting capabilities and faster processing speeds.
- High-Power Machines: Capable of cutting thick materials at high speeds, these machines are more expensive due to the advanced technology required to generate and control high-power lasers. They are suitable for large-scale industrial operations with heavy-duty cutting requirements.
Machine Size and Design
The machine size and design impact both functionality and price.
- Work Area Size: Larger machines with bigger worktables can accommodate larger materials, reducing the need for repositioning and increasing productivity. However, they require more materials to build and are more complex, leading to higher costs.
- Compact Designs: Smaller machines are less expensive and take up less floor space but may limit the size and volume of materials you can process. They are suitable for businesses with space constraints or smaller-scale production needs.
- Build Quality: Machines constructed with robust frames, precision components, and high-quality materials offer better performance and longevity but come at a higher price. Enhanced rigidity and stability improve cutting accuracy and consistency.
Configuration and Features
Configuration and additional features enhance a laser cutting machine’s capabilities but also increase its price.
- Cutting Head Technology: Advanced cutting heads with features like auto-focus, height sensing, and anti-collision systems improve cutting quality and efficiency but add to the cost.
- Dual Worktable Changers: Allow for simultaneous loading and unloading of materials, reducing downtime and increasing productivity. This feature is common in higher-end machines and contributes to a higher price.
- Protective Enclosures: Safety features such as fully enclosed designs protect operators from laser radiation and reduce environmental impact from fumes and dust. These enhancements increase manufacturing costs.
- Cooling Systems: High-power lasers require efficient cooling systems, such as water chillers, to maintain optimal operating temperatures, which adds to the overall cost.
- Dust and Fume Extraction Systems: Integrated extraction systems improve the working environment and comply with safety regulations but contribute to the machine’s price.
- Selecting the right configuration and features depends on your specific operational requirements and can significantly impact the machine’s cost.
After-Sales Support and Service
The level of after-sales support and service provided by the manufacturer or supplier is a crucial factor influencing the price.
- Warranty Terms: Extended warranties and comprehensive service packages offer peace of mind but may increase the initial cost. They cover parts and labor for a specified period, protecting your investment.
- Technical Support: Access to expert technical support, including installation assistance, training, and troubleshooting, adds value but can raise the price. Prompt support minimizes downtime and maintains productivity.
- Maintenance Services: Some manufacturers offer scheduled maintenance services or preventive maintenance programs, ensuring the machine operates at peak efficiency. These services may be included or offered at an additional cost.
- Spare Parts Availability: Manufacturers with readily available spare parts reduce downtime in case of component failures. This convenience can influence the initial investment.
Brand and Manufacturer Reputation
The brand and manufacturer’s reputation play a significant role in the pricing of laser cutting machines.
- Established Brands: Manufacturers with a long history and strong reputation often charge premium prices due to their proven track record, reliability, and quality assurance. Their machines are perceived as safer investments.
- Innovation and Technology: Brands that invest in research and development to offer the latest technology may have higher-priced machines reflecting their advanced features and superior performance.
- Global Presence: Companies with a global presence and extensive support networks can provide better service and quicker response times but may have higher costs associated with their products.
- Customer Reviews and Testimonials: Positive feedback from existing customers can indicate a reliable product and excellent customer service, potentially justifying a higher price.
Automation and Software Integration
Automation and software integration enhance efficiency and precision but contribute to the overall cost.
- CNC Control Systems: High-quality CNC systems with advanced capabilities increase precision, improve ease of use, and offer better integration with design software but add to the price.
- Software Compatibility: Machines that integrate seamlessly with CAD/CAM software allow for efficient design and production workflows. Licensing fees and advanced software features can increase the cost.
- Automation Features: Automated loading and unloading systems, material handling solutions, and robotic interfaces improve productivity by reducing manual labor but require additional investment.
- Remote Monitoring and Diagnostics: Features that allow for remote monitoring, diagnostics, and control enhance maintenance and operation but may raise the cost. They enable proactive maintenance and quick response to issues.
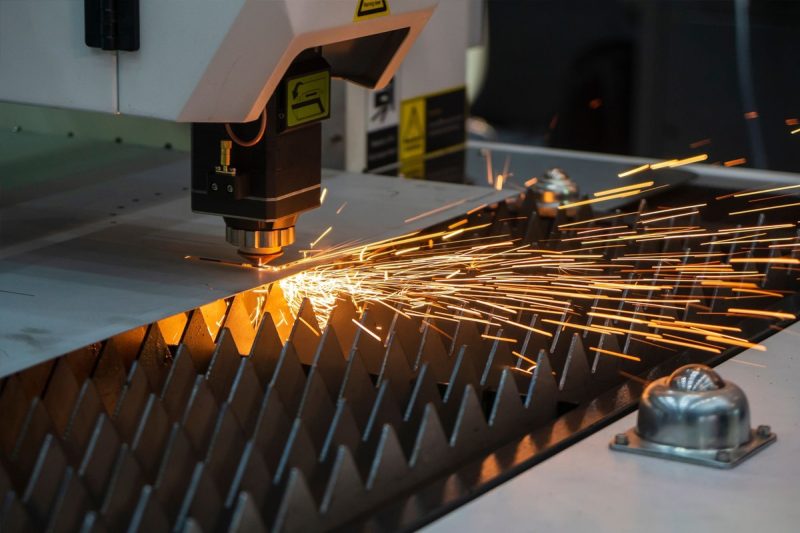
Typical Price Ranges for Fiber and CO2 Laser Cutting Machines
Fiber Laser Cutting Machine Price Ranges
Entry-Level Fiber Laser Cutting Machines ($13,000 - $35,000)
- Laser Power: 1,500W – 3,000W
- Applications: Ideal for cutting thin metal sheets (typically up to 5mm thickness) such as stainless steel, carbon steel, and galvanized sheets.
Features:
- Basic cutting capabilities are suitable for small businesses or startups.
- Standard components with limited automation features.
Considerations:
- Suitable for businesses with lower production volumes.
- May have slower cutting speeds compared to higher-end models.
- Limited in cutting thicker materials or high-reflectivity metals like aluminum or copper.
Mid-Range Fiber Laser Cutting Machines ($25,000 - $70,000)
- Laser Power: 4,000W – 6,000W
- Applications: Capable of cutting medium-thickness metals (up to 10mm), suitable for a variety of industrial applications.
Features:
- Enhanced cutting speeds and precision.
- Additional features such as auto-focus cutting heads, better CNC systems, and improved software integration.
Considerations:
- Balances cost with performance, ideal for growing businesses.
- Offers improved efficiency and the ability to handle a wider range of materials.
- Better suited for moderate production demands.
High-End Fiber Laser Cutting Machines ($60,000 - $250,000+)
- Laser Power: 8,000W – 40,000W
- Applications: Designed for cutting thick metals (over 25mm), high-speed production, and heavy industrial use.
Features:
- Advanced automation features such as dual pallet changers, automatic nozzle changers, and material handling systems.
- High-precision components, top-tier CNC controls, and safety enclosures.
Considerations:
- Significant investment is suitable for large-scale manufacturing operations.
- Maximizes productivity with minimal downtime.
- Capable of cutting a wide variety of metals, including highly reflective materials.
CO2 Laser Cutting Machine Price Ranges
Entry-Level CO2 Laser Cutting Machines ($2,500 - $5,000)
- Laser Power: Up to 150W
- Applications: Suitable for cutting and engraving non-metal materials like wood, acrylic, paper, leather, and fabrics.
Features:
- Basic control systems and software.
- Ideal for hobbyists, small workshops, or educational purposes.
Considerations:
- Limited to non-metal materials or very thin metals with specialized setups.
- Lower cutting speeds and precision compared to higher-end models.
- Minimal automation and additional features.
Mid-Range CO2 Laser Cutting Machines ($6,000 - $10,000)
- Laser Power: 150W – 300W
- Applications: Capable of cutting thicker non-metals and some thin metals (up to 2mm).
Features:
- Improved cutting speeds and accuracy.
- Enhanced software compatibility and user interfaces.
Considerations:
- Suitable for small to medium-sized businesses.
- Offers a balance between cost and functionality.
- May include features like auto-focus and basic safety enclosures.
High-End CO2 Laser Cutting Machines ($15,000 - $50,000+)
- Laser Power: 300W and above
- Applications: Industrial applications require precise cutting of large-format non-metals and certain metals with appropriate setups.
Features:
- Advanced features such as automatic loading/unloading systems, higher precision optics, and comprehensive safety systems.
- Superior control systems with advanced software integration.
Considerations:
- Best suited for large-scale production environments.
- Higher operational costs due to increased maintenance and energy consumption.
- Greater versatility in materials and cutting capabilities.
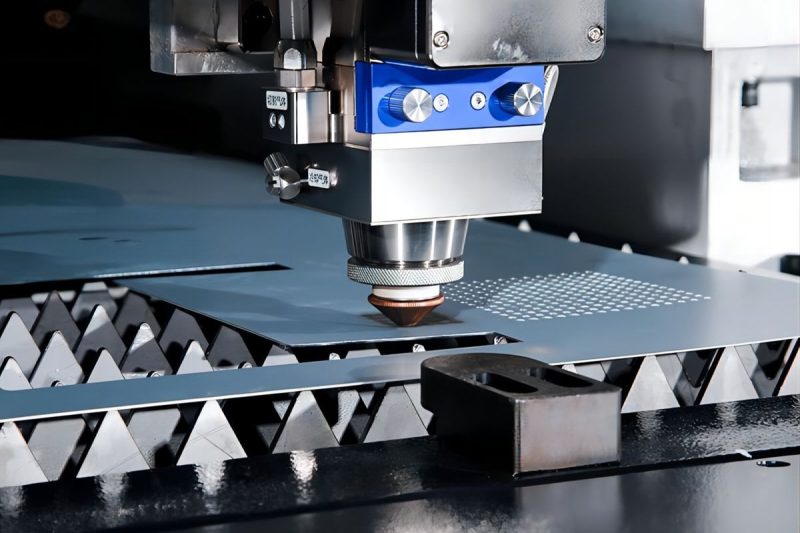
Total Cost of Ownership
Operational Costs
Consumables
- Assist Gases: Both fiber and CO2 laser cutting machines require assist gases like nitrogen, oxygen, or compressed air to aid in the cutting process. The type and volume of gas used depend on the material and thickness being cut.
- Fiber Lasers: Often use nitrogen or compressed air, which can be more cost-effective, especially when cutting stainless steel or aluminum.
- CO2 Lasers: Typically use oxygen for cutting mild steel and nitrogen for stainless steel, potentially increasing gas consumption and costs.
- Laser Gases (CO2 Lasers Only): CO2 lasers require a mixture of gases (carbon dioxide, nitrogen, helium) to generate the laser beam. The consumption of these gases adds to operational expenses and requires regular replenishment.
- Nozzles and Lenses: Regularly replacing the cutting nozzle and protective lens can maintain optimal cutting performance. The frequency of replacement depends on usage intensity and material types.
- Cutting Consumables: Items such as slats on the cutting bed may wear out over time and need replacement.
Labor Costs
- Operator Expertise: Skilled operators can optimize machine performance, reduce waste, and improve efficiency but may command higher wages.
- Training: Initial and ongoing training ensures operators can use the machine effectively and safely. Training costs should be factored into operational expenses.
- Programming and Setup Time: Time spent on programming and setting up jobs affects labor costs. Machines with advanced software integration may reduce setup times.
Software and Licensing
- Software Updates: Keeping the machine’s software up-to-date may involve licensing fees or subscription costs.
- Nesting Software: Advanced nesting software optimizes material usage but may require additional investment.
Waste Management
- Material Waste: Inefficient cutting can lead to increased material waste, affecting overall costs.
- Scrap Handling: Disposing of or recycling scrap materials incurs costs for handling and transportation.
Maintenance Costs
Routine Maintenance
- Scheduled Servicing: Regular maintenance according to the manufacturer’s recommendations can effectively prevent breakdowns and extend the life of the machine. This may include inspections, calibrations, and component replacements.
- Component Wear and Tear: Parts like belts, bearings, and filters will wear out over time and require replacement.
- Optical Components (CO2Lasers): Mirrors and lenses in CO2 lasers need regular cleaning, alignment, and eventual replacement due to contamination and degradation.
- Fiber Delivery System (Fiber Lasers): Fiber lasers have fewer optical components, resulting in lower maintenance requirements.
Unplanned Repairs
- Breakdowns: Unexpected failures can lead to costly repairs and significant downtime.
- Spare Parts Availability: The ease of obtaining replacement parts affects repair costs and downtime duration.
- Technical Support: Access to skilled technicians for troubleshooting and repairs may involve service fees.
Maintenance Agreements
- Service Contracts: Purchasing a maintenance agreement from the manufacturer or a third-party provider can offer predictable maintenance costs and priority service.
- Extended Warranties: Extended warranties may cover certain repairs beyond the standard warranty period but come at an additional cost.
Downtime Costs
- Production Losses: Downtime during maintenance or repairs leads to lost production time, potentially delaying orders and affecting customer satisfaction.
- Backup Equipment: Investing in backup machinery or components can mitigate downtime but adds to overall costs.
Energy Consumption
Electrical Efficiency
- Fiber Lasers: Fiber lasers convert a higher percentage of electrical power into laser light (up to 35% efficiency), reducing electricity consumption. It generates less heat, thus reducing cooling requirements.
- CO2 Lasers: Typically have electrical-to-optical efficiencies of around 10-15%, meaning they consume more power for the same output. Produce more waste heat, increasing the load on cooling systems.
Cooling Systems
- Fiber Lasers: Due to higher efficiency and lower heat generation, cooling systems are less complex and consume less energy.
- CO2Lasers: Require powerful cooling units, such as water chillers, to dissipate heat, increasing energy consumption.
Operating Hours
- Continuous Operation: Machines running multiple shifts will consume more energy, making efficiency an even more critical factor.
- Idle Consumption: Even when not actively cutting, machines consume standby power. Implementing power-saving modes can reduce energy costs.
Facility Considerations
- Electrical Infrastructure: Higher-powered machines may require electrical system upgrades, such as increased amperage circuits or transformers, adding to initial costs.
- Climate Control: Heat generated by the machine can affect the facility’s climate control costs. Excess heat from CO2lasers may increase air conditioning expenses.
Energy Costs
- Local Electricity Rates: Energy costs vary by region, affecting the total operating expenses.
- Peak Demand Charges: High energy consumption during peak hours can lead to additional charges from utility providers.
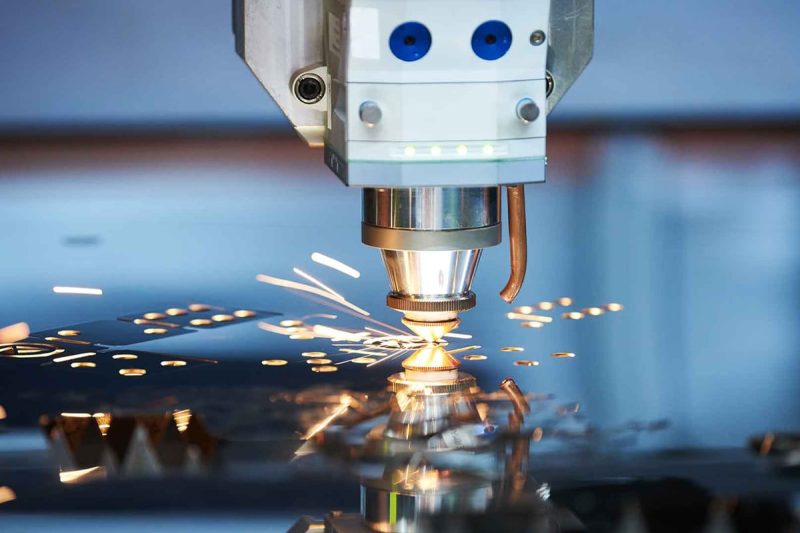
Making the Right Choice
Assessing Your Needs
Material Types and Thickness
- Primary Materials: Identify the materials you will predominantly work with—metals, non-metals, or a combination of both. Fiber lasers excel at cutting metals, while CO2 lasers offer versatility with non-metal materials.
- Material Thickness: Determine the range of material thicknesses you need to process. Higher laser power is required for cutting thicker materials, which influences both the machine’s capabilities and cost.
- Reflective Materials: If you plan to cut highly reflective metals like aluminum, brass, or copper, a fiber laser with appropriate technology is essential to prevent back-reflection damage.
Production Volume and Speed
- Batch Sizes: Consider whether your operations involve large-scale production runs or custom, low-volume jobs. High-volume production may benefit from machines with faster cutting speeds and automation features.
- Cutting Speed Requirements: Evaluate the importance of cutting speed in your production process. Faster machines increase throughput but may come at a higher cost.
- Future Growth: Anticipate future production needs. Investing in a machine that can handle increased demand can save costs in the long run.
Precision and Quality
- Tolerance Levels: Assess the precision requirements of your products. Industries like aerospace and medical devices demand high accuracy, which may necessitate advanced machine features.
- Edge Quality: Determine if superior edge quality is crucial for your applications. Machines with higher precision and better beam quality produce cleaner cuts, reducing the need for secondary processing.
- Complex Designs: If your work involves intricate patterns or fine details, ensure the machine can deliver the required performance.
Workspace and Footprint
- Available Space: Measure your facility to understand the space available for the machine. Larger machines require more floor space and may need special accommodations.
- Accessibility: Consider the ease of integrating the machine into your existing workflow, including material handling and operator access.
- Safety Requirements: Ensure that your workspace can support necessary safety features, such as proper ventilation and protective enclosures.
Budget Considerations
Initial Investment
- Budget Limits: Establish a clear budget for the initial purchase, including any additional costs for installation and training.
- Machine Pricing: Compare different models and configurations within your budget range. Remember that lower-priced machines may lack essential features or capabilities.
- Financing Options: Explore financing solutions such as leases, loans, or payment plans that can make higher-end machines more accessible.
Operating Expenses
- Consumables and Supplies: Calculate the ongoing costs for consumables like assist gases, replacement parts, and maintenance supplies.
- Energy Costs: Factor in the machine’s energy consumption. Fiber lasers are generally more energy-efficient than CO2lasers, potentially reducing utility bills.
- Labor Costs: Consider the level of expertise required to operate and maintain the machine. Advanced machines may require more skilled operators, impacting labor expenses.
Maintenance and Support
- Warranty and Service Agreements: Evaluate the warranty terms and consider purchasing extended service agreements for additional protection.
- Spare Parts Availability: Ensure that replacement parts are readily available and reasonably priced to minimize downtime.
- Technical Support: Access to reliable technical support can save time and money when issues arise. Factor this into your overall budget.
Long-Term Value
Reliability and Durability
- Build Quality: Machines constructed with high-quality materials and components tend to be more durable and reliable, reducing long-term maintenance costs.
- Brand Reputation: Manufacturers like AccTek Laser are known for producing dependable equipment. A reputable brand often signifies better quality and support.
Technological Advancements
- Future-Proofing: Choose a machine that incorporates the latest technology to extend its useful life. Features like software updates, modular components, and compatibility with new technologies can enhance longevity.
- Upgrade Options: Some machines offer the ability to upgrade laser power or add new features as your business grows, providing flexibility and scalability.
Efficiency and Productivity
- Automation Features: Machines with automation capabilities, such as automatic loading and unloading or advanced CNC controls, can increase productivity and reduce labor costs over time.
- Software Integration: Efficient software that integrates with your existing systems can streamline operations and improve workflow efficiency.
Resale Value
- Market Demand: High-quality machines from reputable manufacturers tend to retain their value better, offering potential resale opportunities if your needs change.
- Condition and Maintenance Records: Maintaining the machine properly and keeping detailed service records can enhance its resale value.
Environmental Impact
- Energy Efficiency: More efficient machines not only reduce operating costs but also lessen environmental impact, which can be important for corporate responsibility and compliance with regulations.
- Sustainability: Consider machines that support sustainable practices, such as reduced waste generation and the ability to process recyclable materials.

Summary
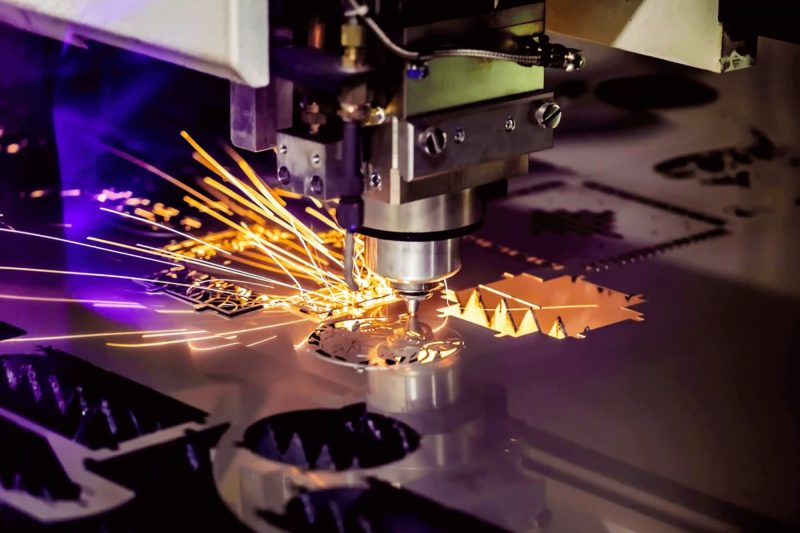
Get Laser Solutions
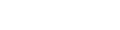
- [email protected]
- [email protected]
- +86-19963414011
- No. 3 Zone A, Lunzhen Industrial Zone,Yucheng City , Shandong Province.