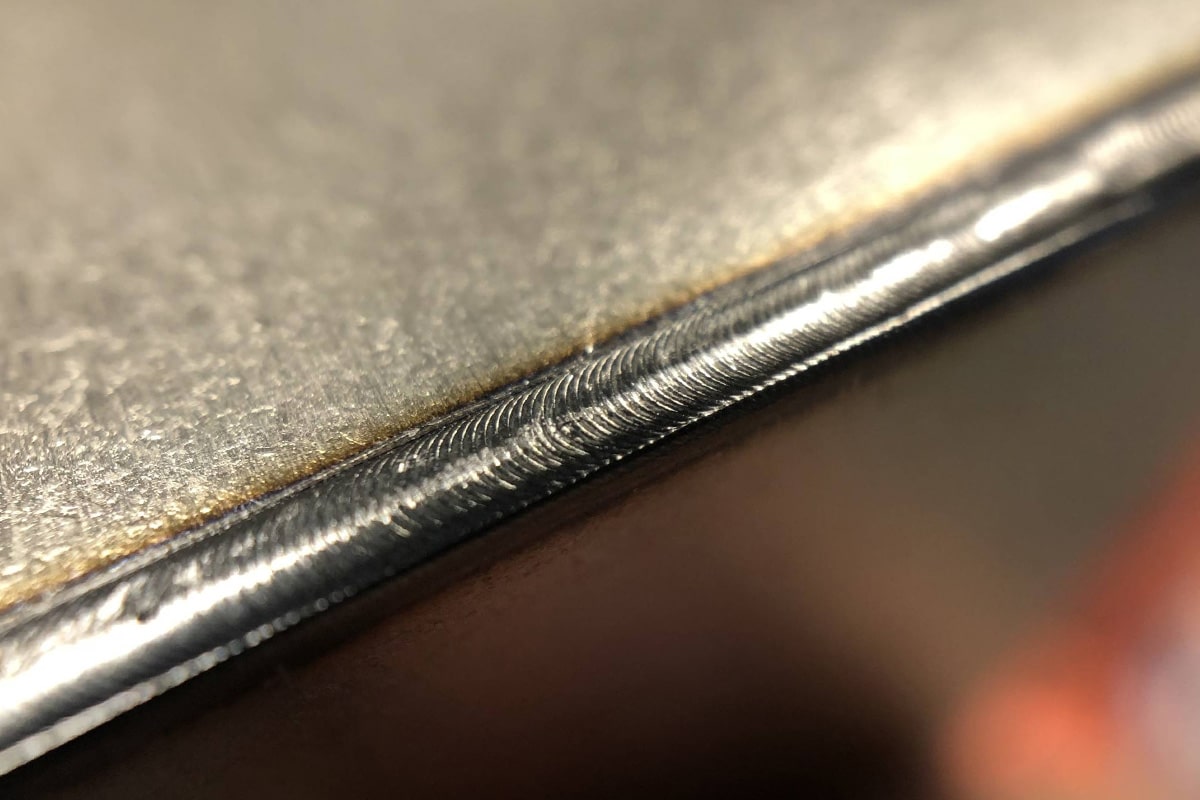
How Does Laser Welding Achieve Deep Melting of Materials?
As an efficient and precise welding technology, laser welding has been widely used in many industries such as automobiles, aerospace, and electronics due to its advantages of high energy density, non-contact processing, and small heat-affected zone. Compared with traditional welding methods, laser welding can complete the connection of complex structures at a faster speed, with less thermal deformation and higher welding strength, and is particularly suitable for precision manufacturing and high-demand industrial production scenarios.
In the laser welding process, achieving deep penetration welding of materials requires comprehensive consideration of multiple factors, such as laser parameters, material properties, and welding process control. This article will deeply explore the basic principles of laser welding, the key factors affecting the penetration depth, and analyze in detail the formation mechanism and optimization strategy of deep penetration, to help enterprises better apply laser welding technology and improve welding quality and production efficiency.
Table of Contents
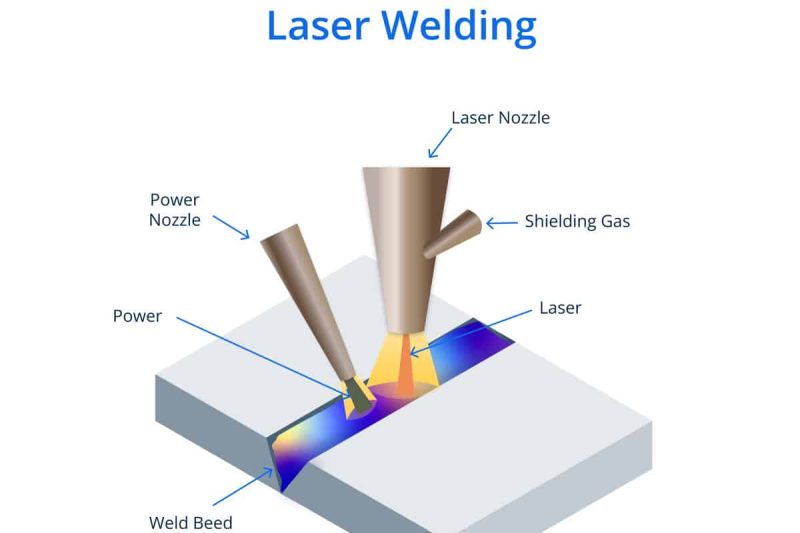
Learn about laser welding
Definition and Rationale
Laser welding is a process that uses a laser beam as a heat source to locally heat the material to the melting point to achieve welding. The laser beam is focused on the welding area, and the high-intensity light energy quickly heats and melts the material to form a molten pool, which forms a strong welded joint after cooling. Laser welding has the characteristics of high energy density, high precision, and high welding speed, and is suitable for welding precision parts.
Laser Welding Process Overview
The laser welding process usually includes the steps of laser beam irradiation, material heating and melting, molten pool formation, cooling and solidification, etc. In these steps, the effective use of laser energy and the interaction of materials determine the welding effect, especially the deep melting ability.
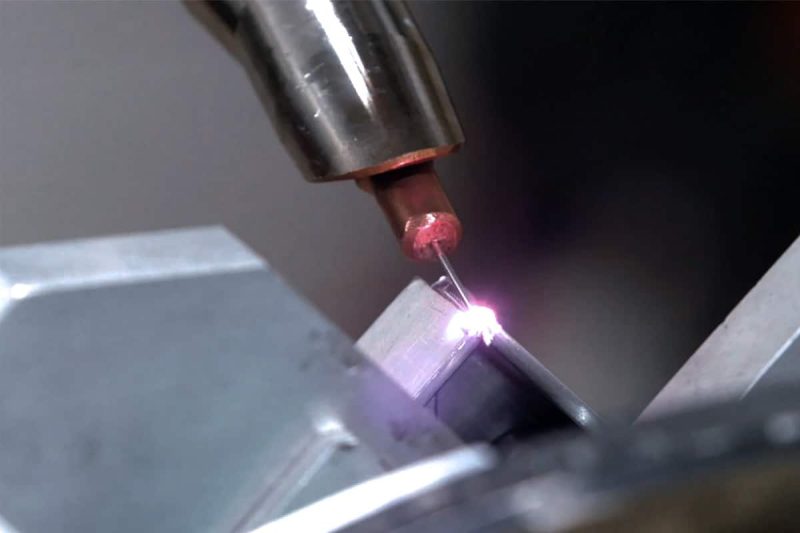
Laser beam interaction with materials
The core of laser welding lies in the interaction between the laser beam and the material, which is the key to achieving efficient and deep-penetration welding. The laser beam is a high-energy-density light source. When it irradiates the surface of a material, it will be partially absorbed, reflected, or transmitted by the material. The absorbed light energy is then converted into heat energy, causing the material to heat up rapidly and enter a molten or vaporized state, thereby completing the welding. The physical properties of different materials, such as absorptivity, thermal conductivity, and melting point, have an important influence on the efficiency and quality of laser welding. Therefore, understanding the material’s absorption of laser energy and the conversion of light energy into heat energy is crucial to optimizing the welding process.
Absorption of laser energy by materials
The performance of a material in laser welding is first affected by its ability to absorb laser energy. Absorption is a key parameter to measure the material’s ability to absorb laser energy, which determines the conversion efficiency of laser energy in the surface area. Different materials have different absorption rates for lasers of different wavelengths. For example, materials such as iron and stainless steel have a high absorption rate for fiber laser generators (near-infrared band), so it is easy to form a stable molten pool. On the other hand, high-reflectivity metals such as aluminum and copper have a low absorption rate, resulting in large energy loss. Higher-power lasers or specialized wavelengths (such as blue or green lasers) are required to improve the absorption rate. In addition, factors such as the oxide layer, roughness, and temperature on the surface of the material will also affect the absorption effect of the laser. Therefore, surface pretreatment is usually required before welding to improve welding stability.
Light energy converted into heat energy
When the laser beam irradiates the surface of the material, the absorbed light energy is quickly converted into heat energy, causing the material temperature to rise rapidly. When the temperature reaches the melting point, the material enters a molten state and forms a molten pool; if the temperature is further increased to the vaporization temperature, part of the material will even evaporate, forming a pinhole effect, thereby achieving deep penetration welding. The conversion efficiency of light energy to heat energy directly determines the depth and quality of welding. If the energy conversion is insufficient, it may result in shallow welds, poor fusion, or even failure to form a stable welding connection. Excessive energy input may cause material overburning, pores, or welding deformation. Therefore, reasonable control of parameters such as laser power, beam mode, and welding speed can effectively optimize the energy conversion process and improve welding quality.
The interaction between the laser beam and the material is the core of laser welding. The key lies in the material’s absorption of laser energy and the efficient conversion of light energy to heat energy. The absorption rate and thermal conductivity characteristics of different materials directly affect the welding effect. By optimizing the laser wavelength, power density, and welding parameters, the utilization rate of light energy can be improved to achieve high-quality deep penetration welding. Understanding the basic principles of these interactions will help optimize the welding process, improve the stability and strength of the weld, and meet the application requirements of different industrial fields.
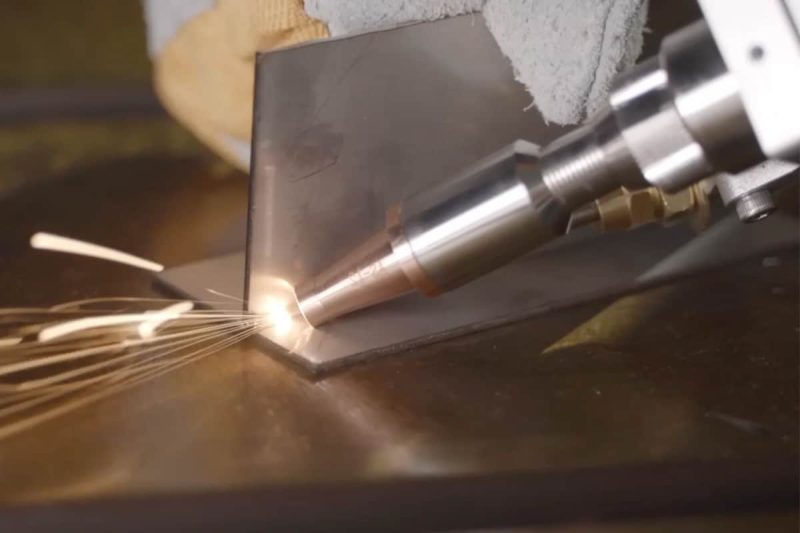
Key factors affecting penetration depth
The deep penetration effect of laser welding is one of the core indicators of welding quality. Its penetration depth directly affects the strength and reliability of the weld. The welding depth is affected by many factors, including laser parameters, material properties, workpiece geometry and assembly, and welding speed. These factors interact to determine the formation and expansion of the molten pool. Reasonable optimization of these parameters can effectively increase the welding depth and ensure the stability and consistency of the weld.
Laser parameters
- Power: Laser power is the main factor affecting welding depth. Higher laser power can provide stronger energy to melt the material at a deeper level. Generally, as the power increases, the welding depth will also increase accordingly, but too high power may cause overburning or welding defects.
- Beam focus and spot size: The size of the laser focus determines the concentration of energy. A smaller focus can provide higher energy density, thereby enhancing the welding depth. Generally, by accurately adjusting the focus position, the best balance between melting depth and melting width can be achieved to meet different welding needs.
- Pulse duration and frequency: For pulsed laser welding, high energy input in a short time helps the material to heat up quickly and penetrate to a deeper level. Reasonable adjustment of pulse parameters can optimize the forming quality of the weld and improve welding stability.
Material properties
- Thermal conductivity: The thermal conductivity of a material affects the propagation of laser energy. High thermal conductivity materials (such as copper and aluminum) lose heat quickly, resulting in a reduced deep melt. Low thermal conductivity materials (such as stainless steel) can concentrate heat more effectively, achieving greater penetration depth.
- Absorption coefficient: The material’s ability to absorb laser light is a key factor in determining deep penetration. A higher absorption coefficient can improve energy utilization, thereby enhancing welding results. For highly reflective materials, it is usually necessary to use a laser of a specific wavelength or pre-treat the surface to increase absorption.
Workpiece geometry and assembly
The shape and assembly method of the workpiece also have a direct impact on the deep melting effect of laser welding. Complex geometric shapes may make it difficult for the laser beam to accurately irradiate the target area, affecting the melting depth. In addition, if the assembly gap of the workpiece is too large or the positioning is inaccurate, it may cause uneven welding and reduce the welding quality. Therefore, precise assembly and positioning are required before welding to ensure that the laser beam can stably act on the welding area.
Welding speed
The welding speed determines the time the material absorbs the laser energy, thus affecting the formation of the molten pool. Slower welding speeds usually increase heat input, giving the material enough time to melt, and thereby increasing the penetration depth. However, if the speed is too slow, it may cause overheating or weld deformation. Conversely, faster welding speeds may reduce the penetration depth and make the weld joint weak. Therefore, in actual operation, the welding speed needs to be optimized according to the material properties and welding requirements to achieve the best weld quality.
The penetration depth of laser welding is affected by many factors, among which laser parameters, material properties, workpiece geometry, and welding speed are the key factors in determining the welding effect. Reasonable control of parameters such as laser power, focus position, welding speed, and optimization combined with material characteristics can effectively improve the stability and quality of deep penetration welding. Through the comprehensive regulation of these factors, the welding process can be ensured to be stable and reliable, meeting the needs of different industrial application scenarios.
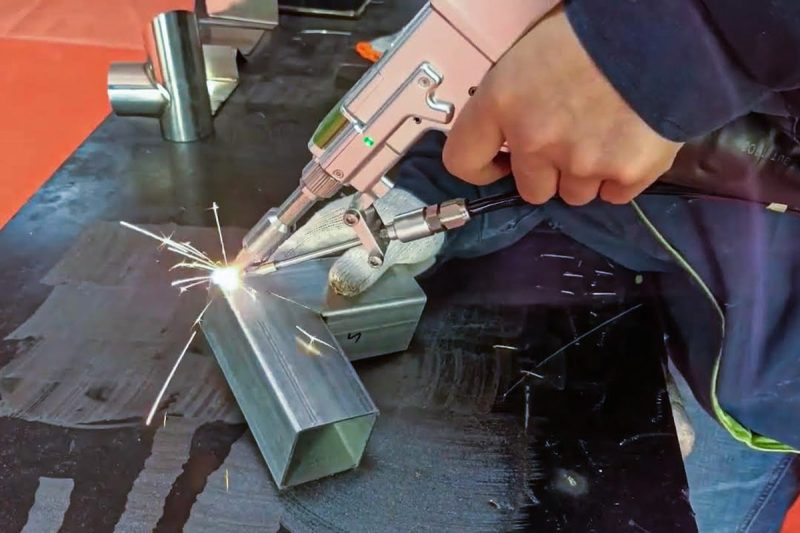
Deep penetration control strategy
In the laser welding process, it is crucial to achieve stable and consistent deep penetration. Since welding depth is affected by many factors, such as laser power, focus position, material properties, and welding speed, strategies such as optimizing laser parameters and real-time monitoring and feedback are needed to ensure welding quality and consistency. These control strategies can not only improve weld strength but also reduce welding defects and improve production efficiency.
Laser parameter optimization
Precise control of laser parameters is crucial for deep penetration welding. The main optimized parameters include:
Laser power:
- Higher power can provide greater energy input, causing the material to melt deeper, thereby increasing the welding depth.
- Too high power may cause excessive melting or evaporation of the material, forming welding defects such as pores or cracks.
- Too low power may result in insufficient penetration and affect the strength of the weld.
Focus size and position:
- Small focus diameter increases energy density, allowing the laser to penetrate the material more effectively, thereby increasing the depth of penetration.
- Optimizing the focus position ensures that the energy is effectively concentrated in the weld area, avoiding excessive energy dispersion or causing surface melting without sufficient depth.
Pulse duration and frequency (for pulsed laser welding):
- Short pulse time combined with high frequency can reduce the heat-affected zone while ensuring sufficient penetration.
- Longer pulse time helps deeper energy penetration but may increase the heat-affected zone, thus affecting welding accuracy.
Through experiments and computer simulation, the optimal combination of laser parameters can be found for different materials and welding requirements to ensure that the depth and quality of welding reach the best level.
Real-time monitoring and feedback
To maintain consistent penetration during the welding process, real-time monitoring and feedback systems are required to adjust welding parameters. These systems usually include optical sensors, thermal imagers, laser power monitors, etc., which can detect the response of the material during the welding process and automatically adjust the welding parameters based on the data.
Key parameters to monitor:
- Molten pool temperature: Through an infrared camera or spectral analysis, the molten pool temperature can be measured in real-time to ensure that the heat input remains within a reasonable range.
- Molten pool morphology: The shape and dynamic changes of the molten pool are monitored through a high-speed camera to ensure uniform and stable welding.
- Laser power fluctuation: Automatically detect and adjust the laser power to prevent fluctuations in welding quality due to equipment instability.
Feedback Mechanism:
- The intelligent control system can automatically adjust the laser parameters based on the monitoring data to compensate for possible deviations. For example, when the sensor detects insufficient penetration, the system can automatically increase the laser power or adjust the focus position.
- Manual adjustment: In high-precision application scenarios, operators can manually fine-tune welding parameters based on monitoring data to ensure that the weld quality meets the requirements.
To ensure the deep melting effect of laser welding, laser parameter optimization and real-time monitoring and feedback strategies are required. By reasonably adjusting parameters such as laser power, focal size, and pulse duration, the welding depth can be effectively improved. At the same time, with the help of advanced monitoring systems, key parameters can be detected and adjusted in real-time during the welding process to ensure the stability and consistency of the melting depth. These control strategies can not only improve welding quality but also reduce welding defects and improve production efficiency, making laser welding technology more reliable and efficient in industrial manufacturing.
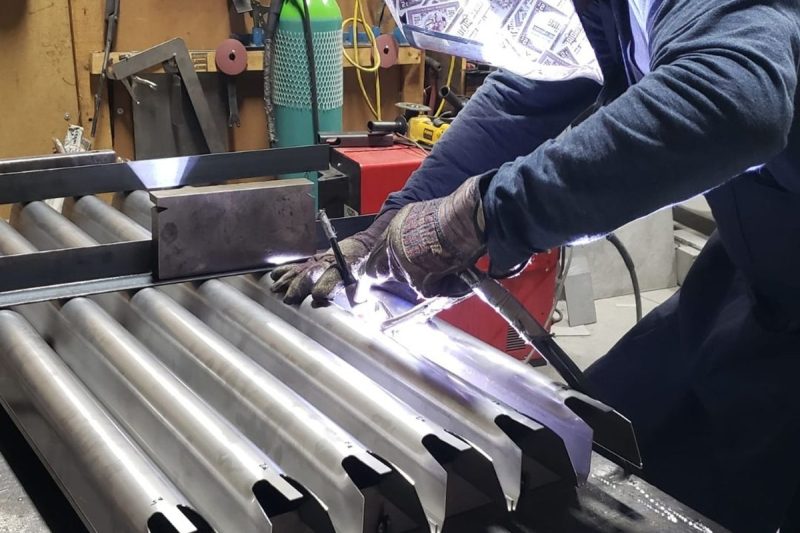
Applications and Industries
Laser welding technology has been widely used in many industries due to its high precision, high efficiency, and adaptability to complex materials, especially in those fields with extremely high requirements for welding quality and depth. The advantages of laser welding make it an ideal choice to solve the needs that traditional welding technology cannot meet. The following are some typical industries and application fields that demonstrate the importance and wide application of laser welding technology in modern industry.
auto industry
Laser welding is widely used in automobile manufacturing, especially in the welding of high-strength steel and aluminum alloy body structural parts. Laser welding can provide deep welding penetration, ensure the strength of the body, and reduce deformation. Efficient laser welding is also suitable for automated production lines to improve production efficiency.
- High-strength steel: Laser welding can perform deep welding on high-strength steel to ensure the strength and safety of the car body while reducing the amount of material used, which is conducive to lightweight design.
- Aluminum alloy welding: Aluminum alloy is a commonly used lightweight material in modern automobile manufacturing. Laser welding technology can achieve efficient deep welding of aluminum alloy due to its precise energy control ability, ensuring the strength and stability of the connection.
- Automated production line: The high speed and high precision of laser welding make it suitable for automated production lines, which improves production efficiency and reduces manual intervention, meeting the needs of large-scale production.
Aerospace
In the aerospace industry, laser welding is used for precision welding of lightweight alloys and composite materials. Due to its deep welding capability and high precision, laser welding has become an ideal welding method for alloy materials and structural components, ensuring the reliability of components under extreme conditions.
- Alloy materials: In aerospace applications, alloy materials (such as titanium alloys, aluminum alloys, etc.) are widely used to manufacture structural components. Laser welding can provide a deeper molten pool and stronger welding strength to ensure the reliability of components under extreme working conditions.
- Composite material welding: Composite materials are widely used in the aerospace field due to their lightweight and high strength. Laser welding can achieve precise welding of these materials to ensure the integrity of the structure.
- High precision and high-quality requirements: The welding of aerospace parts requires extremely high precision and quality. Laser welding can effectively avoid the heat-affected zone and welding deformation that may occur in traditional welding methods, ensuring the strength and durability of the welded parts.
Electronics Industry
Small components in electronic devices are often precisely welded by laser welding to ensure the high reliability and stability of the components. Laser welding can provide high-precision deep welding to avoid damaging other components, making it suitable for the production of microelectronic components.
- Microelectronic components: Laser welding is often used for welding microelectronic components, such as sensors, batteries, integrated circuits, etc. These components have very high requirements for welding quality, and laser welding can provide precise heat input to avoid thermal damage and component deformation.
- Precision welding: In the electronics industry, laser welding technology can complete very precise small component connections without damaging surrounding sensitive components.
- Improve product reliability: Laser welding can provide strong and stable welded joints, ensuring the reliability and durability of electronic products during long-term use.
Laser welding technology has been widely used in many industries, such as automobile, aerospace, electronics, medical, precision tools, etc., due to its high precision, high efficiency, and adaptability to complex materials. With the advancement of science and technology, laser welding will play an important role in more fields, meet the needs of modern industry for high-quality and high-precision welding, and promote the development of manufacturing technology in various industries.
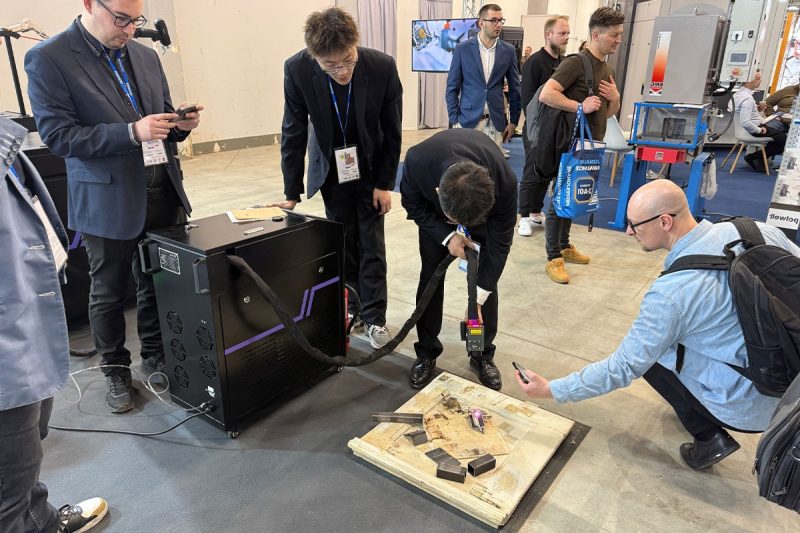
Summarize
The process of achieving deep penetration by laser welding is complex and precise, involving the interaction between laser and material, the optimization and control of multiple key factors, and multiple mechanisms of deep penetration. Through precise control of laser parameters and real-time monitoring, deep welding can be achieved without compromising material quality. This technology has been widely used in many industries, especially in high-precision fields such as automobiles, aerospace, and electronics. With the continuous development of technology, laser welding will play its unique advantages in more industries.
In the above content, we have deeply analyzed the principles and processes of laser welding, focusing on how to achieve deep melting and key control strategies. As an industry leader, AccTek Laser is committed to providing efficient laser welding solutions. Our laser welding machines can meet the high-precision and high-quality welding needs of various industries. If you have any questions or needs, please contact us for more professional advice and services on laser welding.
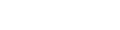
Contact information
- [email protected]
- [email protected]
- +86-19963414011
- No. 3 Zone A, Lunzhen Industrial Zone,Yucheng City , Shandong Province.
Get Laser Solutions