Aluminum Laser Welding Machine
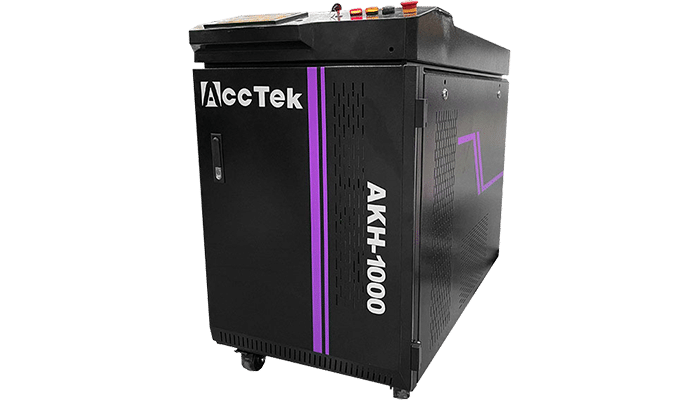
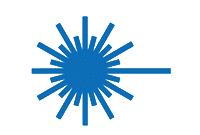
Photoelectric Technology
AccTek Laser focus on designing and manufacturing photoelectric-related system. We provide accurate and exquisite processing quality with leading R&D capability.
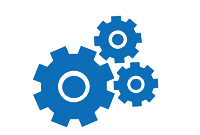
Integration Ability & Experienced
With an experienced, completed, and elite R&D team, customized such as automated, integrated with the robot, system integration, etc. are all available.
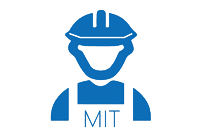
Professional Service
AccTek Laser's laser welding machine is a professional laser welding machine designed and manufactured in China. Our elite engineering team provides related service support.
Equipment Features
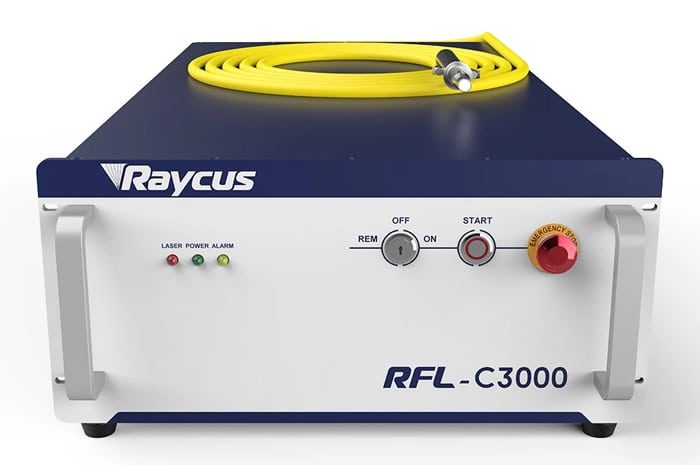
Powerful Laser Generator
Our laser welding machines are equipped with high-quality laser generators that ensure excellent beam quality, providing small and focused spot sizes for precise and efficient welding. With power output options from 1000w to 3000w, our laser welding machines can meet a variety of welding needs, ensuring optimum productivity without compromising quality.
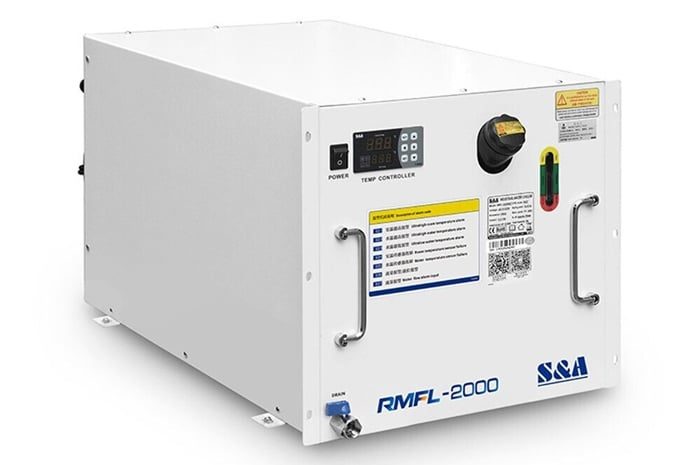
Advanced Cooling System
Designed with reliability in mind, our laser welding machines feature an efficient water cooling system to ensure consistent performance and extend the life of the laser generator. With advanced water cooling technology, we can guarantee stable and reliable welding results even during long-term operation.
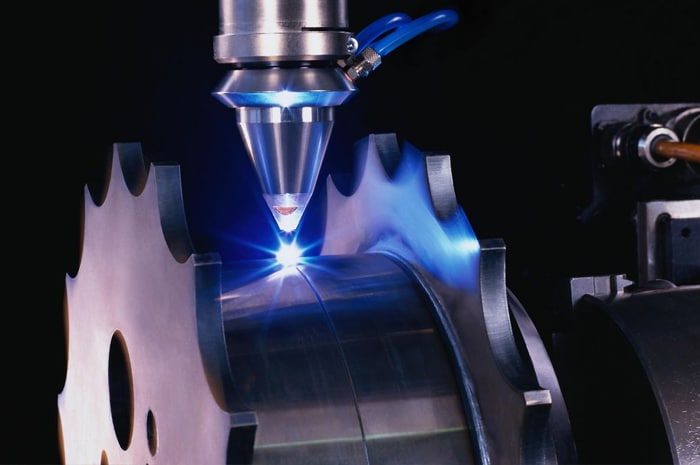
Excellent Beam Quality
Our laser welding machines have excellent beam quality, producing a focused and precise laser spot. This feature enables high-precision and efficient welding of different materials and thicknesses, reducing spatter and minimizing the heat-affected zone.
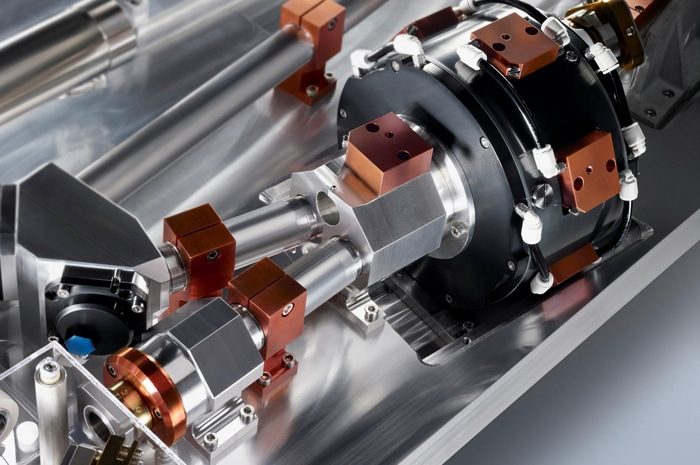
Precision Beam Delivery System
The beam delivery system of our laser welding machines utilizes flexible and flexible fiber optic cables, which can be easily integrated into automated production lines or robotic systems, enabling you to flexibly and easily adapt to different welding tasks. This flexibility increases workflow efficiency and seamlessly adapts to various manufacturing settings.
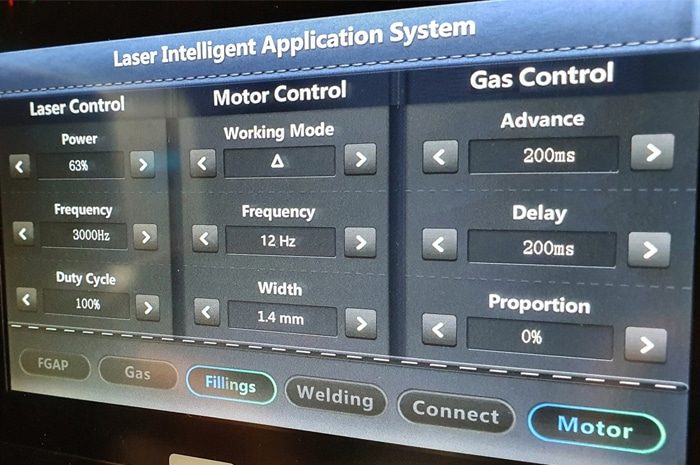
Intuitive Control Interface
Our laser welding machines feature a user-friendly control interface that gives you complete control over your welding process. Easily adjust and program welding parameters such as power, pulse duration, welding speed, and focus position to obtain the best results for your specific welding requirements.
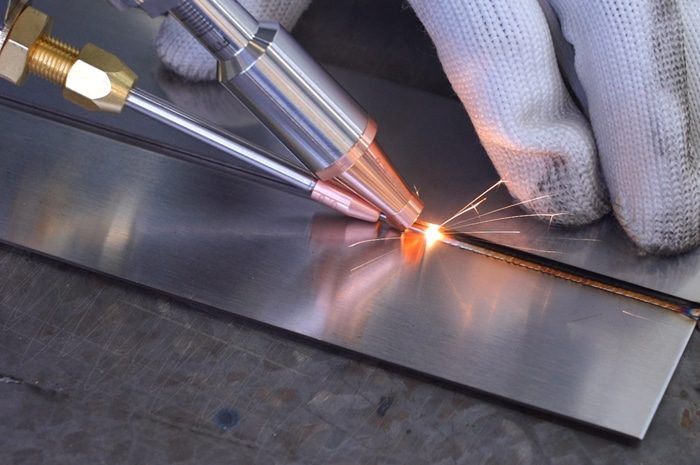
Comprehensive Security Features
Our laser welding machines are equipped with comprehensive safety features including enclosures, interlock systems, and safety sensors. These measures protect your operators from potential exposure to the laser beam, creating a safe work environment.
Technical Specifications
Model | AKH-1000 | AKH-1500 | AKH-2000 | AKH-3000 |
---|---|---|---|---|
Laser Power | 1000W | 1500W | 2000W | 3000W |
Laser Type | Fiber laser | |||
Range of Adjustable Power | 1-100% | |||
Laser Wavelength | 1064nm | |||
Way of Workinging | Continuous/Modulation | |||
Speed Range | 0-120mm/s | |||
Repeat Precision | ±0.01mm | |||
Welding Gap Requirements | ≤0.5mm | |||
Cooling Water | Industrial thermostatic water tank |
Laser Welding Capacity
Laser Power (W) | Material Type | Welding Form | Thickness (mm) | Welding Speed (mm/s) | Defocus Amount | Protective Gas | Blowing Method | Flow (L/min) | Welding Effect |
---|---|---|---|---|---|---|---|---|---|
1000 | 1-3 Series Aluminum Alloys | Butt Welding | 0.5 | 70~80 | -1~1 | Ar | Coaxial/Paraaxial | 5~10 | Welded Completely |
Butt Welding | 1 | 50~60 | -1~1 | Ar | Coaxial/Paraaxial | 5~10 | Welded Completely | ||
Butt Welding | 1.5 | 30~40 | -1~1 | Ar | Coaxial/Paraaxial | 5~10 | Welded Completely | ||
Butt Welding | 2 | 20~30 | -1~1 | Ar | Coaxial/Paraaxial | 5~10 | Welded Completely | ||
4-7 Series Aluminum Alloys | Butt Welding | 0.5 | 45~55 | -1~1 | Ar | Coaxial/Paraaxial | 5~10 | Welded Completely | |
Butt Welding | 1 | 35~45 | -1~1 | Ar | Coaxial/Paraaxial | 5~10 | Welded Completely | ||
Butt Welding | 1.5 | 20~30 | -1~1 | Ar | Coaxial/Paraaxial | 5~10 | Welded Completely | ||
1500 | 1-3 Series Aluminum Alloys | Butt Welding | 0.5 | 80~90 | -1~1 | Ar | Coaxial/Paraaxial | 5~10 | Welded Completely |
Butt Welding | 1 | 70~80 | -1~1 | Ar | Coaxial/Paraaxial | 5~10 | Welded Completely | ||
Butt Welding | 1.5 | 50~60 | -1~1 | Ar | Coaxial/Paraaxial | 5~10 | Welded Completely | ||
Butt Welding | 2 | 30~40 | -1~1 | Ar | Coaxial/Paraaxial | 5~10 | Welded Completely | ||
Butt Welding | 3 | 10~20 | -1~1 | Ar | Coaxial/Paraaxial | 5~10 | Welded Completely | ||
4-7 Series Aluminum Alloys | Butt Welding | 0.5 | 60~65 | -1~1 | Ar | Coaxial/Paraaxial | 5~10 | Welded Completely | |
Butt Welding | 1 | 40~50 | -1~1 | Ar | Coaxial/Paraaxial | 5~10 | Welded Completely | ||
Butt Welding | 1.5 | 30~40 | -1~1 | Ar | Coaxial/Paraaxial | 5~10 | Welded Completely | ||
Butt Welding | 2 | 20~30 | -1~1 | Ar | Coaxial/Paraaxial | 5~10 | Welded Completely | ||
2000 | 1-3 Series Aluminum Alloys | Butt Welding | 0.5 | 90~100 | -1~1 | Ar | Coaxial/Paraaxial | 5~10 | Welded Completely |
Butt Welding | 1 | 80~90 | -1~1 | Ar | Coaxial/Paraaxial | 5~10 | Welded Completely | ||
Butt Welding | 1.5 | 70~80 | -1~1 | Ar | Coaxial/Paraaxial | 5~10 | Welded Completely | ||
Butt Welding | 2 | 40~50 | -1~1 | Ar | Coaxial/Paraaxial | 5~10 | Welded Completely | ||
Butt Welding | 3 | 20~30 | -1~1 | Ar | Coaxial/Paraaxial | 5~10 | Welded Completely | ||
4-7 Series Aluminum Alloys | Butt Welding | 0.5 | 70~80 | -1~1 | Ar | Coaxial/Paraaxial | 5~10 | Welded Completely | |
Butt Welding | 1 | 60~70 | -1~1 | Ar | Coaxial/Paraaxial | 5~10 | Welded Completely | ||
Butt Welding | 1.5 | 40~50 | -1~1 | Ar | Coaxial/Paraaxial | 5~10 | Welded Completely | ||
Butt Welding | 2 | 30~40 | -1~1 | Ar | Coaxial/Paraaxial | 5~10 | Welded Completely | ||
3000 | 1-3 Series Aluminum Alloys | Butt Welding | 0.5 | 100~110 | -1~1 | Ar | Coaxial/Paraaxial | 5~10 | Welded Completely |
Butt Welding | 1 | 90~100 | -1~1 | Ar | Coaxial/Paraaxial | 5~10 | Welded Completely | ||
Butt Welding | 1.5 | 80~90 | -1~1 | Ar | Coaxial/Paraaxial | 5~10 | Welded Completely | ||
Butt Welding | 2 | 70~80 | -1~1 | Ar | Coaxial/Paraaxial | 5~10 | Welded Completely | ||
Butt Welding | 3 | 40~50 | -1~1 | Ar | Coaxial/Paraaxial | 5~10 | Welded Completely | ||
Butt Welding | 4 | 20~30 | -1~1 | Ar | Coaxial/Paraaxial | 5~10 | Welded Completely | ||
4-7 Series Aluminum Alloys | Butt Welding | 0.5 | 80~90 | -1~1 | Ar | Coaxial/Paraaxial | 5~10 | Welded Completely | |
Butt Welding | 1 | 70~80 | -1~1 | Ar | Coaxial/Paraaxial | 5~10 | Welded Completely | ||
Butt Welding | 1.5 | 60~70 | -1~1 | Ar | Coaxial/Paraaxial | 5~10 | Welded Completely | ||
Butt Welding | 2 | 40~50 | -1~1 | Ar | Coaxial/Paraaxial | 5~10 | Welded Completely | ||
Butt Welding | 3 | 30~40 | -1~1 | Ar | Coaxial/Paraaxial | 5~10 | Welded Completely |
- In the welding data, the core diameter of the 1000w, 1500w, 2000w, and 3000w laser output fiber is 50 microns.
- This welding data adopts the Raytools welding head, and the optical ratio is 100/200 (collimator/focus lens focal length).
- The welding shielding gas: Argon (purity 99.99%).
- The welding material is brass.
- Due to the differences in equipment configuration and welding process used by different customers, this data is for reference only.
Comparison of Different Welding Methods
Welding Method | Laser Welding | TIG Welding | MIG Welding |
---|---|---|---|
Heat Source | High-intensity laser beam | Non-consumable tungsten electrode | Consumable wire electrode |
Gas Shielding | Generally not required, but can use inert gas | Inert gas (Argon) | Inert gas (Argon) |
Welding Speed | High speed | Moderate speed | High speed |
Precision | Very high | High | Moderate |
Skill Level | Requires high precision and expertise | Requires moderate to high skill | Relatively easy to learn |
Weld Quality | High-quality welds, minimal distortion | High-quality welds, low distortion | Good welds, moderate distortion |
Thickness Range | Thin to medium thicknesses | Thin to thick sections | Thin to thick sections |
Joint Types | Suited for precision joints | Suited for various joint types | Suited for various joint types |
Filler Material | Generally not required, but can be used | Requires filler rod | Requires filler wire |
Welding Cost | Expensive equipment and operation | Moderate equipment and operation cost | Cost-effective |
Applications | Aerospace, electronics, precision welding | Automotive, general fabrication | General fabrication, construction |
Product Features
- The machine is equipped with a high-power fiber laser generator, which has the characteristics of high energy efficiency, excellent beam quality, and precise control of laser beam parameters. Fiber laser generators are capable of delivering high-powered, focused laser energy, making them ideal for welding aluminum.
- The machine provides excellent beam quality, ensuring that the laser beam is focused and stable, resulting in precise, high-quality welding results.
- The machine can precisely control the laser power and pulse duration, so as to make the best adjustment according to the specific welding requirements of aluminum materials. This precise control ensures consistent and high-quality welds.
- The intuitive and user-friendly interface makes it easier for the operator to set welding parameters, monitor the welding process and adjust settings as needed.
- The machine has an efficient cooling system, which can maintain the best working temperature of the laser generator and prevent overheating during long-term use.
- The machine provides a variety of laser power options to meet different aluminum thicknesses and welding requirements.
- The machine selects a high-quality beam transmission system, which can effectively transmit the laser beam from the laser generator to the welding area, ensuring the stability, accuracy, and consistency of the laser beam during the welding process.
- The machine is easy to maintain and maintain, with features such as easy access to key components, diagnostic tools, and remote monitoring functions to ensure smooth operation and minimize downtime.
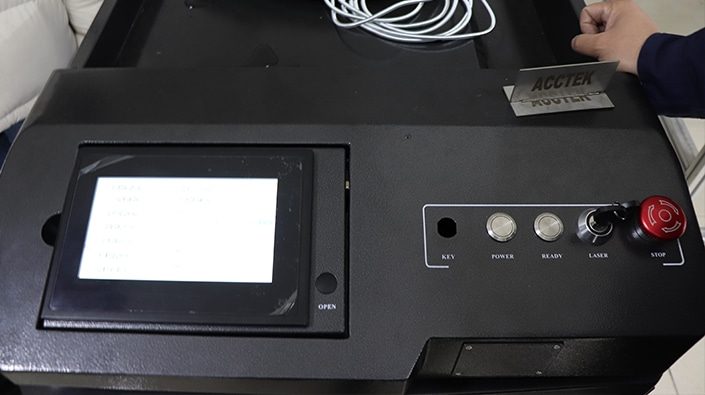
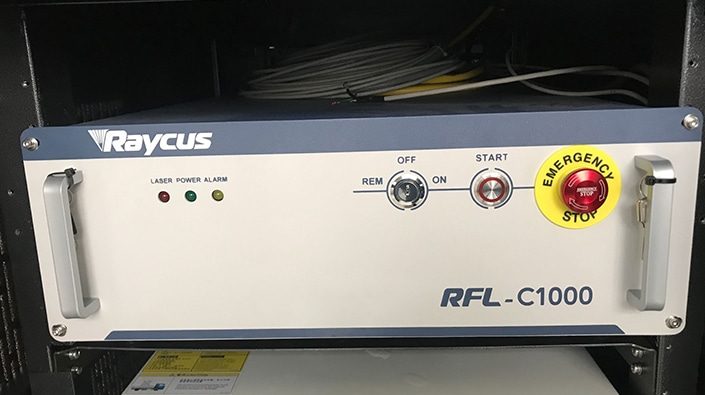
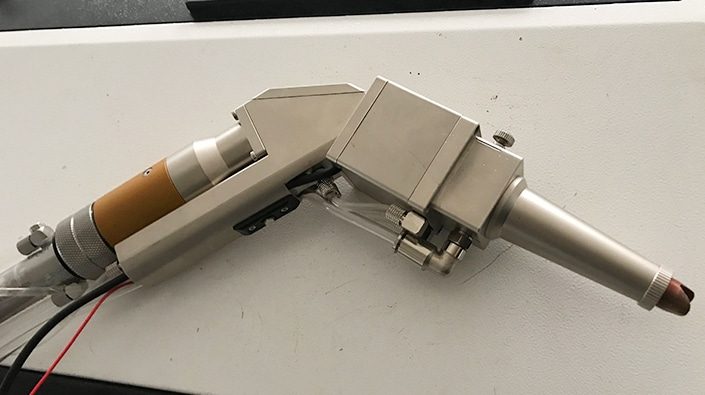
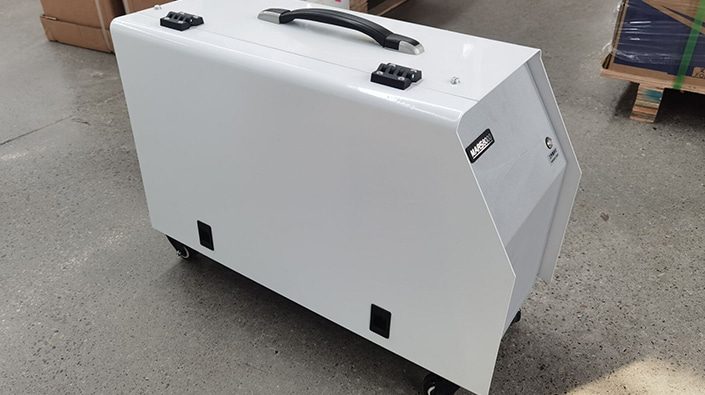
Product Application
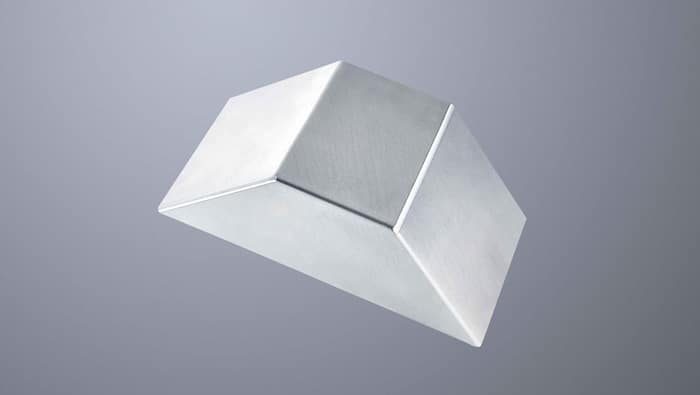
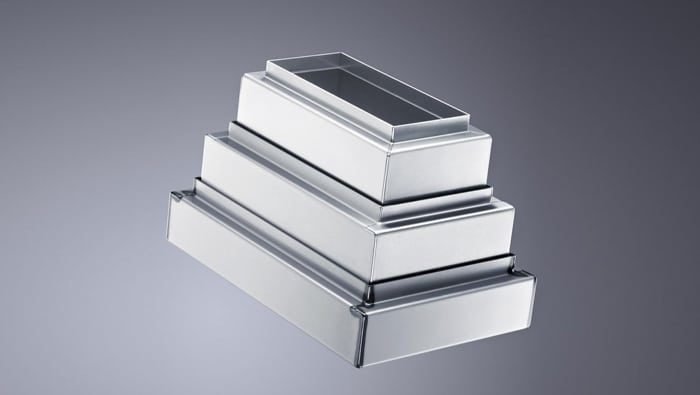
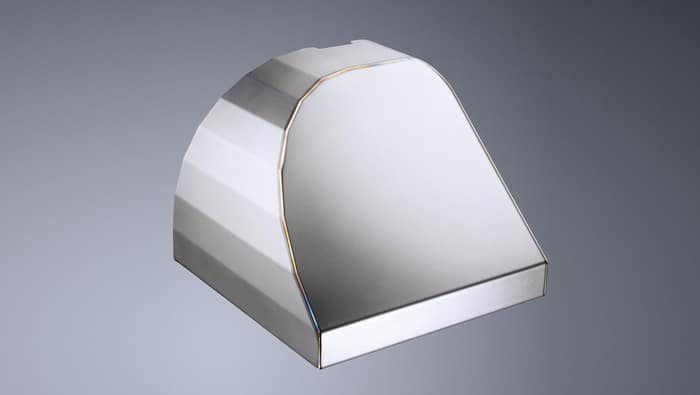
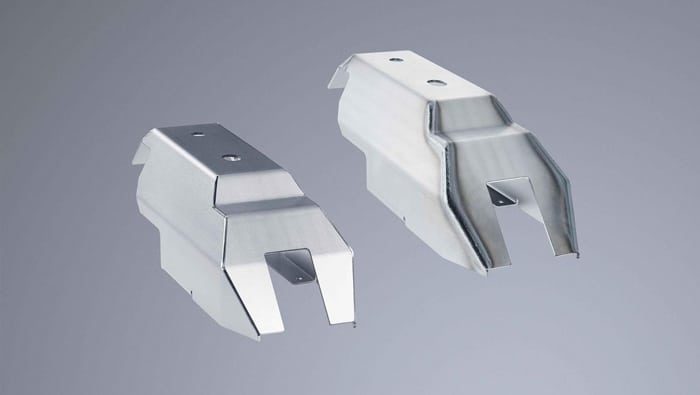
Equipment Selection
High-Configuration Fiber Laser Welding Machine
Portable Fiber Laser Welding Machine
Fiber Laser Welding Machine With Double Wobble
Fiber Laser Welding Machine With Automatic Wire Feeder
3 In 1 Fiber Laser Welding Cutting Cleaning Machine
Laser Welding Robot
Portable Air-Cooled Laser Welding Machine
Why Choose AccTek?
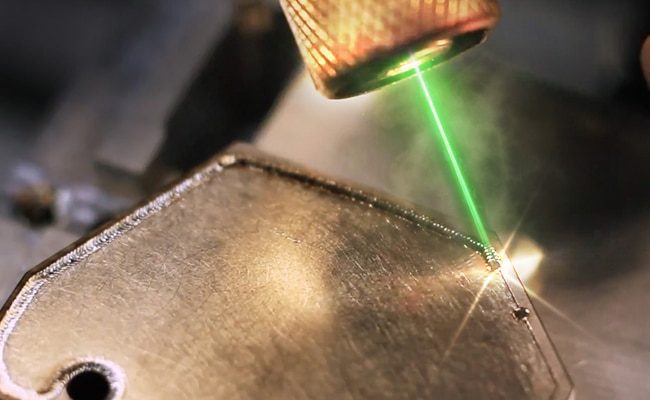
Unparalleled Expertise
Comprehensive Support And Service
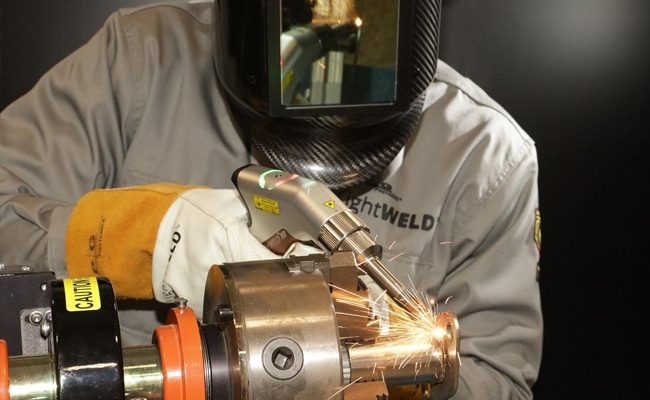
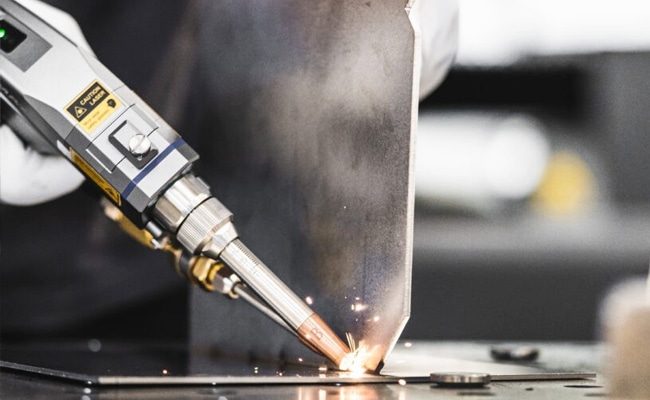
Strict Quality Control
Cost-Effective Solution
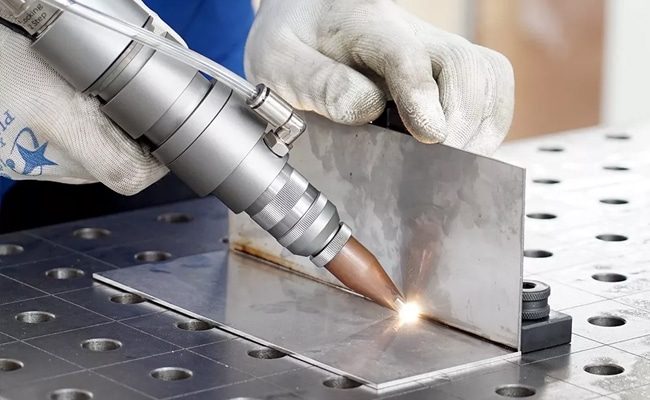
Frequently Asked Questions
- Intermediate Layer: In some cases, a thin layer of compatible material such as copper can be used as an intermediate layer between aluminum and steel to help facilitate the welding process and increase the strength of the joint.
- Beam Characteristics: Laser beam parameters (including power, focus, and spot size) are carefully controlled to achieve the proper balance between melting the two materials and ensuring adequate penetration and bonding.
- Preheating: Preheating the material before welding helps reduce thermal gradients between aluminum and steel, making the welding process more manageable.
- Filler Material Selection: The choice of filler material helps to achieve a strong and reliable connection between aluminum and steel. Whenever possible, choose a dedicated filler material that is compatible with aluminum and steel to facilitate the bonding process.
- Surface Preparation: Proper preparation of the welding surface is critical. Aluminum and steel surfaces should be thoroughly cleaned and free of contaminants such as oil, grease, or oxides that could hinder the Seager process.
- Preparation And Joint Design: Proper preparation and joint design are also important. Joints may require bevels or specific geometries to enhance weld strength and reduce potential problems caused by different material properties.
- Process Parameters: Fine-tuning laser power, welding speed, and other process parameters can help find the best balance between ensuring a good weld joint and minimizing material distortion.
- Pulsed Laser Welding: The use of pulsed laser welding can help manage heat input and reduce the risk of aluminum overheating during welding.
- Alloy 5052: This alloy is known for its excellent weldability and high corrosion resistance. It is commonly used in marine applications as well as sheet metal fabrication and automotive components.
- Alloy 5083: 5083 is a highly weldable aluminum alloy that has exceptional strength and is commonly used in shipbuilding and structural components that withstand harsh environments.
- Alloy 6061: This versatile alloy has good weldability, high strength, and excellent corrosion resistance. It is commonly used in aerospace, automotive, and general engineering applications.
- Alloy 6063: Similar to 6061, 6063 also has good weldability and is commonly used in architectural and structural applications as well as in the fabrication of aluminum framing.
- Alloy 6082: 6082 has excellent weldability and high strength and is often used in structural applications, especially in the construction and transportation industries.