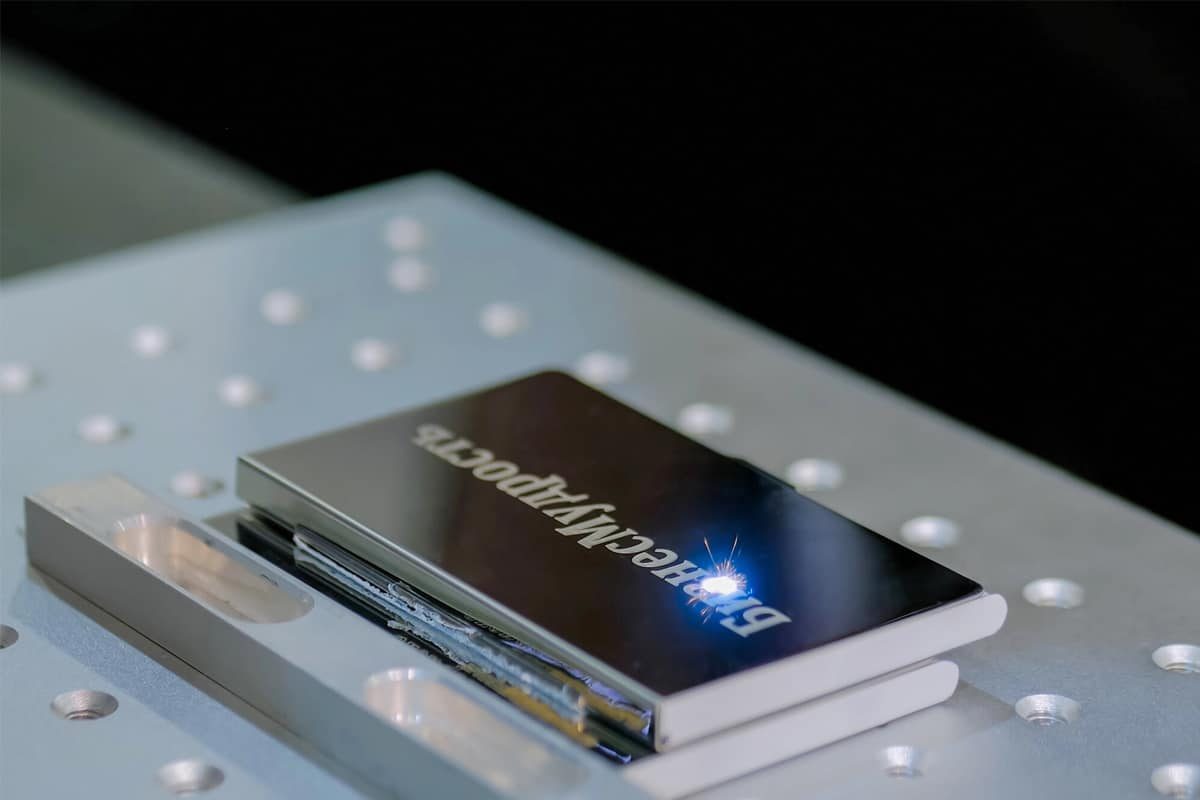
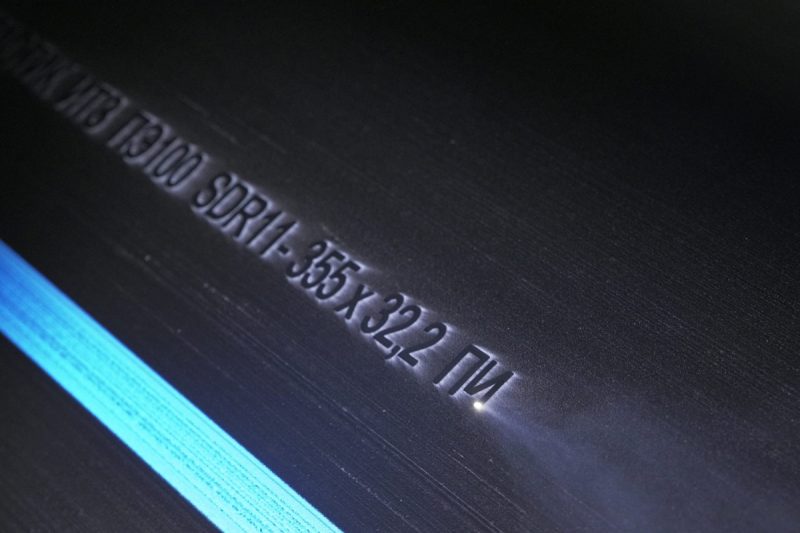
Introduction to Laser Marking
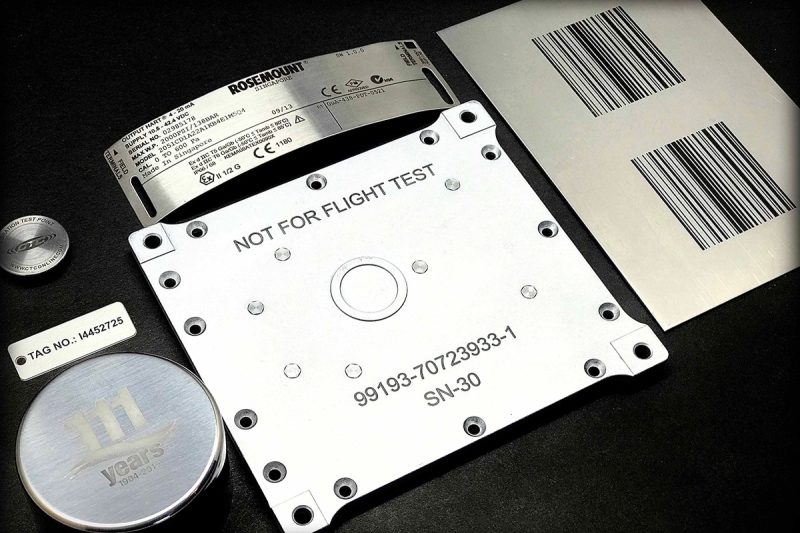
How Does Laser Marking Work
Laser marking is a precise and efficient method of permanently marking or engraving materials using a concentrated beam of light—namely, a laser. The fundamental principle involves directing this laser beam onto the surface of a material to alter its appearance or properties without physical contact or the use of inks and chemicals. Here’s a breakdown of how the process works:
- Laser Generation: The laser marking machine generates a high-intensity light beam through a gain medium, which can be a gas, liquid, or solid-state material. This beam has a single wavelength and is highly focused.
- Beam Focusing: Lenses or mirrors are used to focus the laser beam to a very small spot size, increasing its energy density. This concentrated energy allows the laser to interact effectively with the material’s surface.
- Material Interaction: When the focused laser beam strikes the material, it induces a reaction depending on the laser’s wavelength, power, and the material’s properties.
- Computer Control: The entire process is controlled by specialized software that directs the laser beam’s movement using galvanometer scanners or CNC systems. This allows for the precise reproduction of complex designs, text, barcodes, and serial numbers.
- Non-Contact Process: Since laser marking is a non-contact method, there is minimal wear on the equipment, and the risk of contaminating or deforming the material is significantly reduced.
- Versatility: Laser parameters such as wavelength, pulse duration, and power can be adjusted to suit different materials and desired effects. This makes laser marking suitable for a wide range of substrates including metals, plastics, ceramics, glass, and more.
Key Steps in the Laser Marking Process
- Design Creation: The desired marking design is created or imported into the laser marking software.
- Parameter Setting: Laser settings are configured based on the material type and the required marking effect.
- Material Placement: The workpiece is positioned on the machine’s worktable, and focus adjustments are made to ensure optimal laser interaction.
- Marking Execution: The laser marking machine executes the marking process as per the programmed design.
- Quality Inspection: The finished workpiece is inspected to verify the quality, accuracy, and durability of the mark.
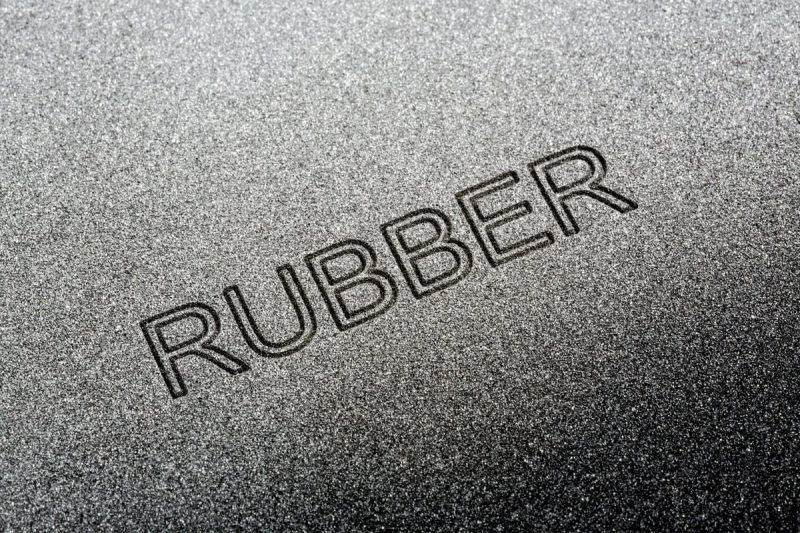
Types of Laser Marking Technology
Laser marking encompasses a range of techniques that alter the appearance or properties of a material’s surface using a focused laser beam. Each method offers unique advantages and is suitable for different applications and materials. Below are the primary types of laser marking technologies:
- Laser Engraving: Laser engraving is a process where the laser beam removes material from the surface to create a cavity that reveals an image or text. The laser vaporizes the material to a specified depth, resulting in a permanent, deep mark. This method is ideal for producing durable marks that are resistant to wear and tear. Laser engraving is commonly used on metals, plastics, wood, and glass.
- Laser Etching: Laser etching is a subset of laser engraving that melts the surface of the material to create a raised mark. The laser’s heat causes the material to expand slightly, forming a bump on the surface. This technique requires less energy than engraving and is suitable for marking metals, ceramics, and polymers. Laser etching is often used for adding barcodes, serial numbers, and logos to products.
- Laser Annealing: Laser annealing is primarily used on metals like stainless steel and titanium. In this process, the laser heats the metal below its melting point, causing oxidation and a change in the material’s color. The result is a smooth, high-contrast mark without any surface disruption. Laser annealing is ideal for applications that require corrosion-resistant markings, such as medical devices and surgical instruments.
- Laser Ablation: Laser ablation involves removing layers of material from a substrate through irradiation with a laser beam. This process can precisely remove coatings, paints, or other surface treatments without damaging the underlying material. Laser ablation is commonly used in industries like electronics for circuit board manufacturing and automotive sectors for removing paint layers.
- Foaming: Foaming is a laser marking technique used mainly on plastics and certain metals. The laser melts the material, creating gas bubbles that get trapped as the material cools. This results in raised marks that are lighter in color than the surrounding material. Foaming provides high-contrast markings on dark surfaces and is often used for aesthetic purposes or for adding functional information to plastic components.
- Carbonization: Carbonization uses the laser to heat organic materials such as wood, paper, or leather, causing them to darken due to the formation of carbon. The process results in dark, high-contrast marks that stand out against lighter backgrounds. Carbonization is widely used for decorative engraving, personalized gifts, and branding on organic materials.
- Removal (Laser Removing): Also known as laser stripping, this technique involves using the laser to remove a top layer of material or coating, revealing a different underlying material or color. Removal is effective for marking anodized aluminum, coated metals, and painted surfaces. It creates clear, high-contrast marks without affecting the integrity of the base material.
- Discoloration: Discoloration is a laser marking method where the laser induces a chemical reaction or structural change in the material, leading to a change in color without engraving or etching the surface. This technique is particularly useful for plastics, where the laser can produce dark or light marks depending on the material composition. Discoloration is ideal for applications requiring high-contrast markings without altering the material’s texture.
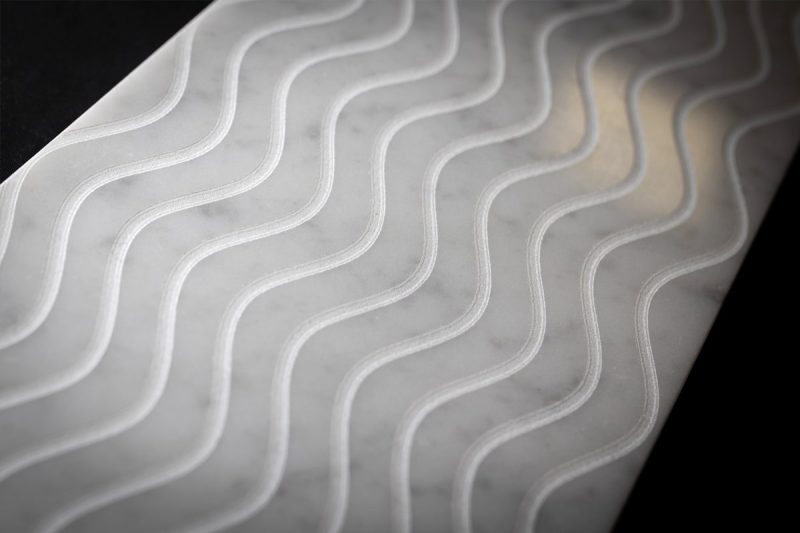
Types of Laser Marking Machines
Fiber Laser Marking Machine
Applications
- Materials: Metals (steel, aluminum, copper, gold, silver), hard plastics, and some ceramics.
- Industries: Aerospace, automotive, electronics, medical devices, jewelry, and tooling.
Advantages
- High Precision: Capable of producing fine, detailed markings with excellent resolution.
- Durability: Marks are permanent and resistant to wear, heat, and chemicals.
- Efficiency: Fast marking speeds enhance productivity.
- Low Maintenance: Solid-state design with minimal moving parts leads to long service life.
Features
- Non-Contact Process: Prevents mechanical stress or damage to the workpiece.
- Versatility: Suitable for various marking techniques, including engraving, annealing, and etching.
- Integration: Easily incorporated into existing production lines for automated marking.
CO2 Laser Marking Machine
Applications
- Materials: Wood, glass, paper, leather, plastics, textiles, rubber, and acrylics.
- Industries: Packaging, textiles, woodworking, crafts, and advertising.
Advantages
- Versatility: Capable of marking, engraving, and cutting a wide range of non-metallic materials.
- Cost-Effective: Generally lower initial investment compared to other laser types.
- Quality Marks: Produces clean and precise markings without physical contact.
- Versatility: Capable of marking, engraving, and cutting a wide range of non-metallic materials.
- Cost-Effective: Generally lower initial investment compared to other laser types.
- Quality Marks: Produces clean and precise markings without physical contact.
Features
- Adjustable Power: Allows control over depth and intensity for various materials.
- Large Working Area: Suitable for processing bigger workpieces.
- User-Friendly: Simple operation with intuitive software interfaces.
UV Laser Marking Machine
Applications
- Materials: Heat-sensitive materials like glass, certain plastics, silicon wafers, ceramics, and thin metals.
- Industries: Electronics, semiconductor manufacturing, medical devices, pharmaceuticals, and cosmetic packaging.
Advantages
- Cold Marking: Reduces the risk of material damage or deformation due to minimal heat generation.
- High Precision: Ideal for micro-marking with extremely fine details and small characters.
- Excellent Contrast: Produces clear and legible marks, even on transparent or translucent materials.
Features
- Non-Contact and Non-Damaging: Preserves the integrity of delicate and sensitive materials.
- High Absorption Rate: UV light is efficiently absorbed by a wide variety of materials.
- Micro-Machining Capability: Suitable for intricate designs and complex patterns.
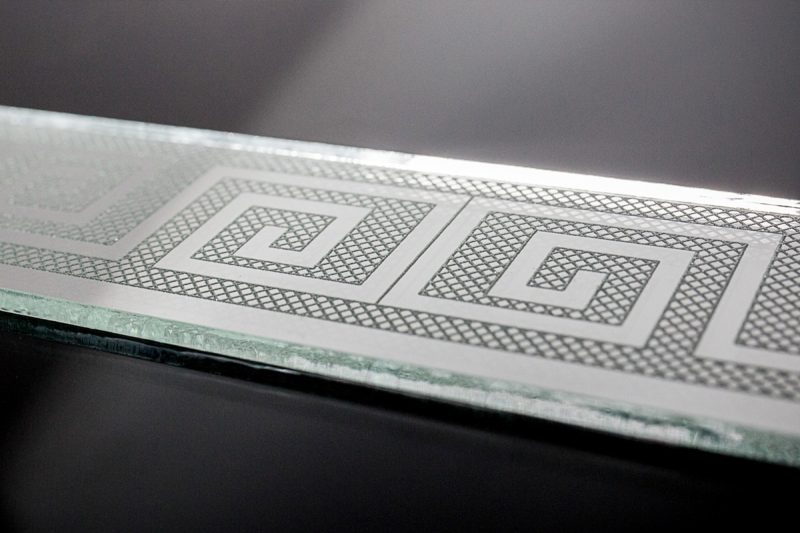
Materials Suitable for Laser Marking
Metals
Common Metals
- Stainless steel
- Aluminum
- Brass
- Copper
- Titanium
- Gold and silver
- Alloys
Applications
- Serial numbers and barcodes for traceability
- Logos and branding
- Component identification
- Decorative engravingsv
Techniques Used
- Laser Engraving: Removes material to create deep, durable marks.
- Laser Annealing: Alters the metal’s surface color without engraving.
- Laser Etching: Melts the surface to form raised marks.
- Carbon Migration: Darkens the metal by bringing carbon to the surface.
Advantages
- Durability: Marks are resistant to wear, heat, and corrosion.
- Precision: High-resolution markings suitable for small components.
- Non-Contact Process: Preserves the integrity of delicate parts.
Plastics
Common Plastics
- ABS
- Polycarbonate
- Polyethylene
- Polypropylene
- PVC
- Acrylic
Applications
- Keypads and buttons
- Electronic housings
- Medical instruments
- Packaging and labeling
Techniques Used
- Foaming: Creates raised, lighter-colored marks.
- Carbonization: Produces dark marks by heating the plastic.
- Color Change (Discoloration): Alters the molecular structure for contrast.
- Laser Etching: Melts the surface for raised markings.
Advantages
- High Contrast Marks: Enhances readability without additional inks.
- Customization: Easily adapts to complex designs and variable data.
- Efficiency: Suitable for high-volume production with rapid processing times.
Wood
Common Woods
- Maple
- Oak
- Cherry
- Walnut
- Plywood
- MDF (Medium-Density Fiberboard)
Applications
- Furniture customization
- Decorative items and artwork
- Musical instruments
- Packaging crates and pallets
Techniques Used
- Laser Engraving: Removes material for deep, textured marks.
- Carbonization: Darkens the wood surface for contrast.
Advantages
- Aesthetic Quality: Produces intricate designs with high detail.
- Versatility: Suitable for various wood types and composites.
- Environmental Friendliness: Eliminates the need for chemicals or inks.
Ceramics
Common Ceramics
- Ceramic tiles
- Porcelain
- Technical ceramics used in electronics and aerospace
Applications
- Branding and logos on tiles
- Component identification in electronic devices
- Marking medical implants
Techniques Used
- Laser Etching: Creates shallow marks by melting the surface.
- Laser Ablation: Removes thin layers for precise markings.
- Discoloration: Changes the color without altering the surface texture.
Advantages
- Permanent Marks: Resistant to high temperatures and abrasion.
- Clean Process: Generates minimal residue or dust.
- Precision: Allows for detailed markings on small or complex shapes.
Glass
Applications
- Bottles and Drinkware
- Laboratory equipment
- Automotive glass components
- Decorative items and awards
Techniques Used
- Laser Etching: Engraves the surface to create frosted marks.
- Internal Laser Marking: Creates marks within the glass without surface disruption.
- Laser Engraving: Removes material for deeper marks.
Advantages
- Non-Contact Process: Reduces the risk of cracks or damage.
- Customization: Ideal for intricate designs, logos, and text.
- Durability: Marks are resistant to chemicals and environmental factors.
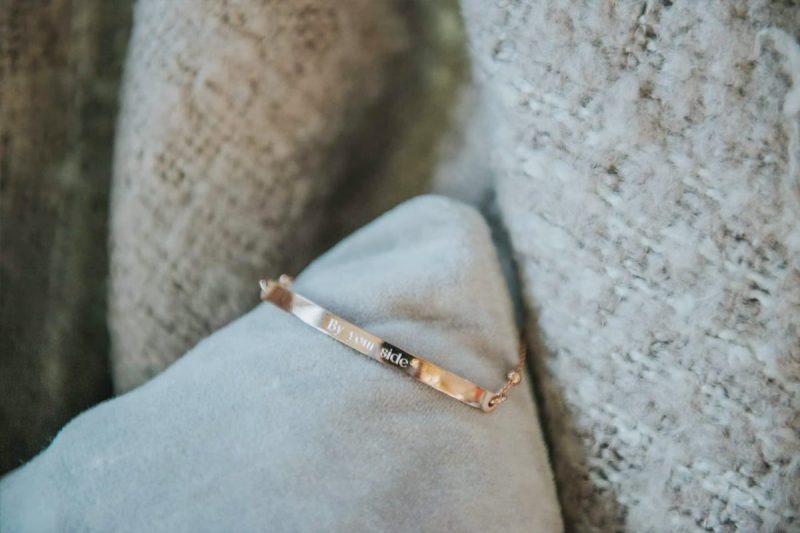
Benefits of Laser Marking
Precision and Accuracy
Laser marking provides exceptional precision and accuracy, enabling the creation of high-resolution marks with intricate details. The focused laser beam can produce extremely fine lines and complex patterns that are clear and legible, even on small or irregularly shaped items.
- High Resolution: Capable of marking at micrometer-level precision.
- Consistency: Ensures uniformity across large production runs.
- Complex Designs: Allows for detailed graphics, logos, and text.
Permanence
Laser marking produces permanent marks that are resistant to wear, heat, chemicals, and other environmental factors. This durability ensures that critical information such as serial numbers, barcodes, and logos remain intact throughout the product’s lifecycle.
- Wear Resistance: Marks do not fade or erode over time.
- Chemical Resistance: Withstands exposure to acids, solvents, and other corrosive substances.
- Heat Resistance: Maintains integrity even under high-temperature conditions.
Non-Contact Process
Laser marking is a non-contact method, meaning the laser beam interacts with the material without physical touch.
- Material Integrity: Reduces the risk of damaging or deforming the workpiece.
- No Tool Wear: Eliminates mechanical wear and tear on equipment.
- Clean Process: Minimizes contamination since there is no direct contact.
High-Speed
Laser marking systems operate at high speeds, significantly enhancing production efficiency. They can quickly apply complex markings without sacrificing quality.
- Fast Processing: Capable of marking hundreds of characters per second.
- Reduced Downtime: Increases throughput and minimizes bottlenecks.
- Automation Compatible: Easily integrated into automated production lines.
Environmental Friendliness
Laser marking is an eco-friendly technology that reduces environmental impact.
- No Consumables: Eliminates the need for inks, chemicals, or solvents.
- Energy Efficient: Modern lasers consume less power compared to traditional methods.
- Minimal Waste: Generates negligible amounts of waste or pollutants.
Versatility
Laser marking is highly versatile, accommodating a wide range of materials and applications.
- Material Compatibility: Effective on metals, plastics, wood, ceramics, glass, and more.
- Various Techniques: Supports engraving, etching, annealing, ablation, foaming, and discoloration.
- Customization: Easily adjusted for different marking depths, sizes, and styles.
Cost-Effectiveness
While not listed explicitly, it’s important to note that laser marking offers significant cost benefits.
- Low Operating Costs: Reduced need for consumables and maintenance.
- Long Lifespan: Durable equipment with extended operational life.
- Reduced Labor Costs: Automation capabilities decrease the need for manual intervention.
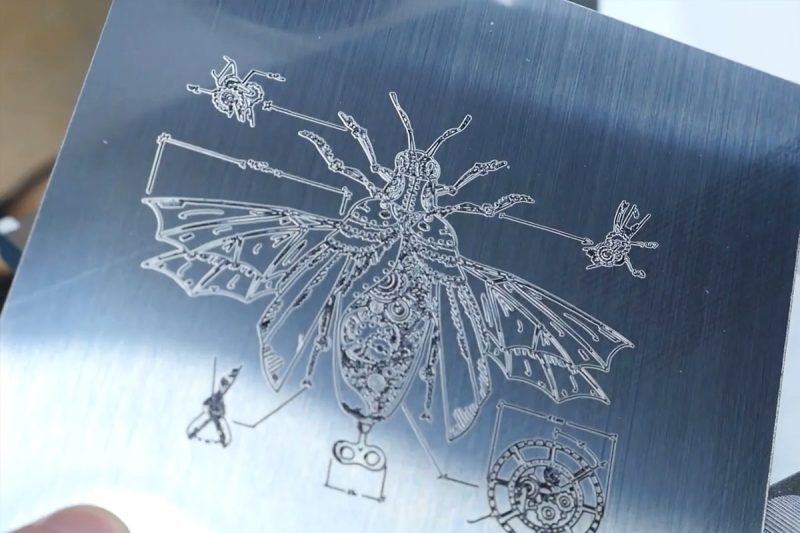
Factors Influencing Laser Marking Quality
Material Properties
The characteristics of the material being marked play a crucial role in the quality of the laser marking. Different materials interact with laser energy in various ways due to their physical and chemical properties.
- Absorption Rate: Materials absorb laser wavelengths differently. Metals, plastics, wood, ceramics, and glass each have unique absorption spectra. Matching the laser type (fiber, CO₂, UV) to the material ensures efficient energy absorption and optimal marking quality.
- Thermal Conductivity: Materials with high thermal conductivity, like metals, dissipate heat quickly, which can affect marking depth and contrast. Adjusting laser power and speed can compensate for these differences.
- Reflectivity: Highly reflective materials, such as aluminum or copper, can reflect a significant portion of the laser energy, reducing marking efficiency. Surface treatments or using lasers with appropriate wavelengths can mitigate this issue.
- Material Composition: Additives, coatings, or alloys in the material can influence how it reacts to laser energy. For example, certain plastics contain additives that improve laser absorption, resulting in better contrast and clarity.
- Surface Condition: The cleanliness, roughness, and finish of the material’s surface can impact marking quality. Contaminants like oil, dust, or rust can hinder the laser’s interaction with the material. Pre-cleaning the surface ensures consistent results.
Laser Parameters
Adjusting the laser’s settings can help achieve the desired mark quality. The laser parameters determine how the laser interacts with the material.
- Laser Power: Higher power increases the energy delivered to the material, affecting marking depth and speed. However, excessive power can cause unwanted melting or damage.
- Pulse Frequency and Duration: The frequency and duration of laser pulses influence the heat input and marking precision. Shorter pulses with higher frequencies can produce finer details without overheating the material.
- Scanning Speed: The speed at which the laser beam moves across the material affects the exposure time. Slower speeds allow more energy absorption, resulting in deeper marks, while faster speeds produce shallower marks.
- Beam Quality (M² Value): A laser with a higher beam quality can be focused to a smaller spot size, enabling finer and more precise markings.
- Wavelength: Different laser wavelengths are absorbed differently by materials. Selecting the correct wavelength (e.g., 1064 nm for fiber lasers, 10.6 μm for CO₂ lasers, 355 nm for UV lasers) ensures efficient marking.
Focus and Alignment
Proper focusing and alignment of the laser beam help to achieve clear and accurate marking.
- Focus Position: The laser must be correctly focused on the material’s surface to maximize energy density. An out-of-focus beam results in reduced power density and blurred markings.
- Spot Size: The diameter of the laser beam at the focal point determines the resolution of the marking. A smaller spot size allows for higher detail but requires precise focusing.
- Beam Alignment: Misalignment of optical components can cause distortions or inconsistencies in the marking pattern. Regular maintenance and calibration ensure the laser beam is correctly aligned.
- Workpiece Positioning: The material must be accurately positioned relative to the laser. Variations in distance can affect focus and marking consistency, especially on curved or uneven surfaces.
Ambient Conditions
Environmental factors in the workspace can influence laser marking quality.
- Temperature: Extreme temperatures can affect both the laser system and the material. High temperatures may alter material properties, while low temperatures can affect laser performance. Maintaining a stable room temperature is advisable.
- Humidity: Excessive humidity can lead to condensation on optical components or the material surface, disrupting the laser beam and causing inconsistent markings.
- Dust and Contaminants: Particulate matter in the air can settle on lenses, mirrors, or the material, scattering the laser beam and reducing marking quality. A clean environment minimizes this risk.
- Vibration: External vibrations from nearby machinery or movement can cause misalignment or movement of the laser or workpiece, leading to distorted markings. Vibration isolation measures can help maintain stability.
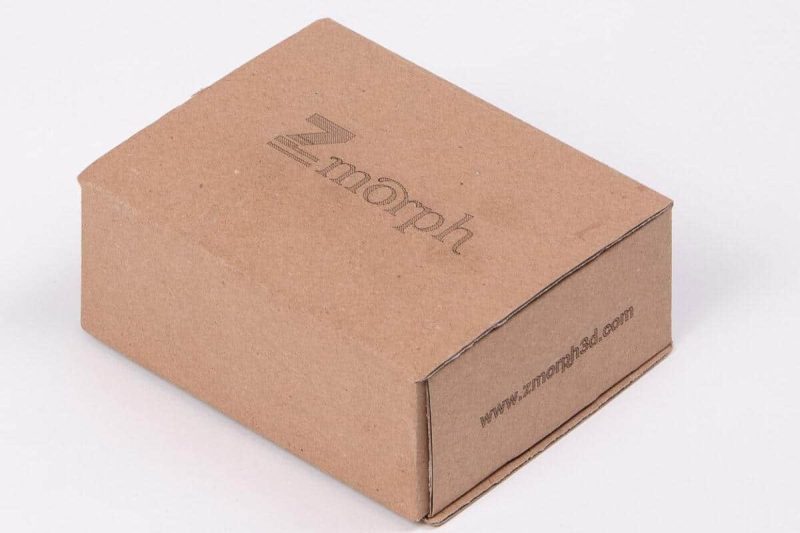
How to Choose the Right Laser Marking Machine
Identify the Material to Be Marked
Understanding the material you intend to mark is the first step in selecting the right machine.
- Metals: For marking metals such as stainless steel, aluminum, brass, and titanium, a Fiber Laser Marking Machine is ideal due to its high efficiency and precision with metallic materials.
- Non-Metals: If you plan to mark non-metallic materials like wood, glass, ceramics, textiles, or certain plastics, a CO2 Laser Marking Machine is more suitable because of its longer wavelength, which is better absorbed by organic materials.
- Heat-Sensitive Materials: For materials that are sensitive to heat, such as some plastics, electronic components, or medical devices, a UV Laser Marking Machine is the best choice. Its “cold marking” process minimizes thermal stress, preventing damage to the material.
Determine Your Application Requirements
Consider the specific needs of your marking application.
- Marking Depth and Type: Decide whether you require deep engraving, surface etching, annealing, or color change marking.
- Precision and Detail: For applications requiring high precision and intricate details, such as micro-marking or complex designs, select a machine with excellent beam quality and fine spot size.
- Marking Speed: If you have high-volume production needs, choose a machine capable of high-speed marking without compromising quality.
- Contrast and Readability: Ensure the machine can produce marks with the desired contrast, especially important for barcodes and QR codes that need to be easily scanned.
Evaluate Machine Specifications
Review the technical specifications to ensure they align with your requirements.
- Laser Power: Higher power lasers can mark deeper and faster but may be unnecessary for certain applications. Match the laser power to your specific needs.
- Work Area Size: Ensure the machine’s worktable or marking area can accommodate the size of your components.
- Machine Footprint: Consider the available space in your facility and choose a machine that fits comfortably.
- Cooling System: Machines may use air or water cooling. Air-cooled systems are typically more compact and require less maintenance.
Consider Software and Control Systems
The software interface plays a significant role in the ease of operation.
- User-Friendly Interface: Look for software that is intuitive and easy to learn, reducing the training time for operators.
- Compatibility: Ensure the software supports various file formats (e.g., DXF, PLT, AI) and can integrate with your existing systems.
- Features: Advanced features like real-time monitoring, barcode generation, and serialization can enhance productivity.
Assess Quality and Reliability
Investing in a high-quality machine ensures long-term performance and durability.
- Build Quality: Machines constructed with high-quality materials and components will offer better longevity and stability.
- Laser Source Lifespan: Check the expected operational hours of the laser source. Fiber lasers typically offer longer lifespans (up to 100,000 hours).
- Warranty and Support: A comprehensive warranty and responsive customer support are indicators of a reliable manufacturer.
Factor in Cost and Budget
Balance your budget with the features and capabilities you require.
- Initial Investment: While it’s important to stay within budget, consider the total cost of ownership, including maintenance and operating costs.
- Operating Costs: Evaluate energy consumption, consumables (if any), and potential downtime costs.
- Return on Investment: A more expensive machine with higher efficiency and lower maintenance may offer better long-term value.
Examine After-Sales Support and Service
Reliable support is essential for uninterrupted operations.
- Technical Support: Ensure the manufacturer provides prompt and effective technical assistance.
- Training and Installation: Look for companies that offer comprehensive training programs and support during installation.
- Spare Parts Availability: Quick access to spare parts minimizes downtime in case of repairs.
Ensure Compliance with Safety and Regulatory Standards
Compliance with industry standards is crucial for legal and safety reasons.
- Safety Features: Machines should have safety enclosures, and emergency stop functions, and comply with laser safety regulations.
- Certifications: Check for certifications such as CE, FDA, or other relevant industry-specific approvals.
Plan for Future Needs
Consider the scalability and adaptability of the machine.
- Modularity: Machines that allow for upgrades or modifications can adapt to changing needs.
- Versatility: A machine capable of handling multiple materials or applications offers greater flexibility.
Choosing the right laser marking machine involves careful consideration of your materials, application requirements, machine specifications, and long-term operational needs. By evaluating these factors and partnering with a reputable manufacturer like AccTek Laser, you can select a machine that enhances your production capabilities, ensures high-quality markings, and supports your business growth.
By making an informed decision, you’ll benefit from the efficiencies and advantages that laser marking technology offers, positioning your business for success in a competitive market.
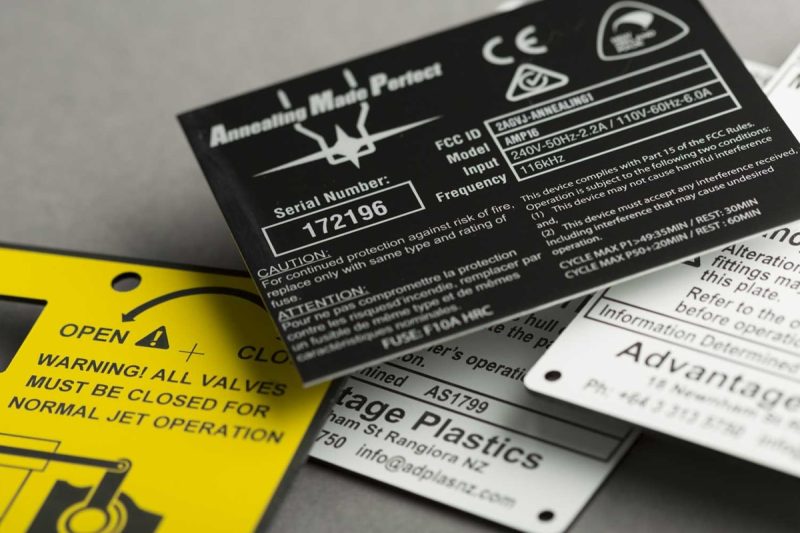
Summary
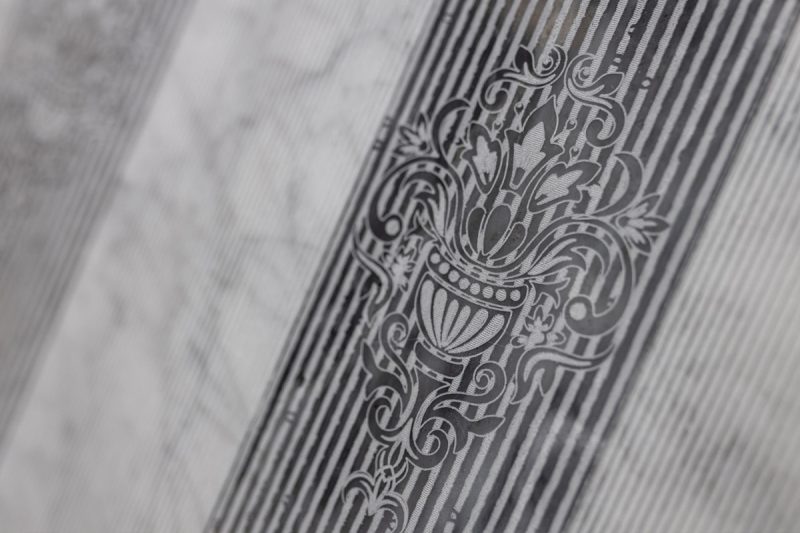
Get Laser Solutions
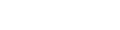
- [email protected]
- [email protected]
- +86-19963414011
- No. 3 Zone A, Lunzhen Industrial Zone,Yucheng City , Shandong Province.