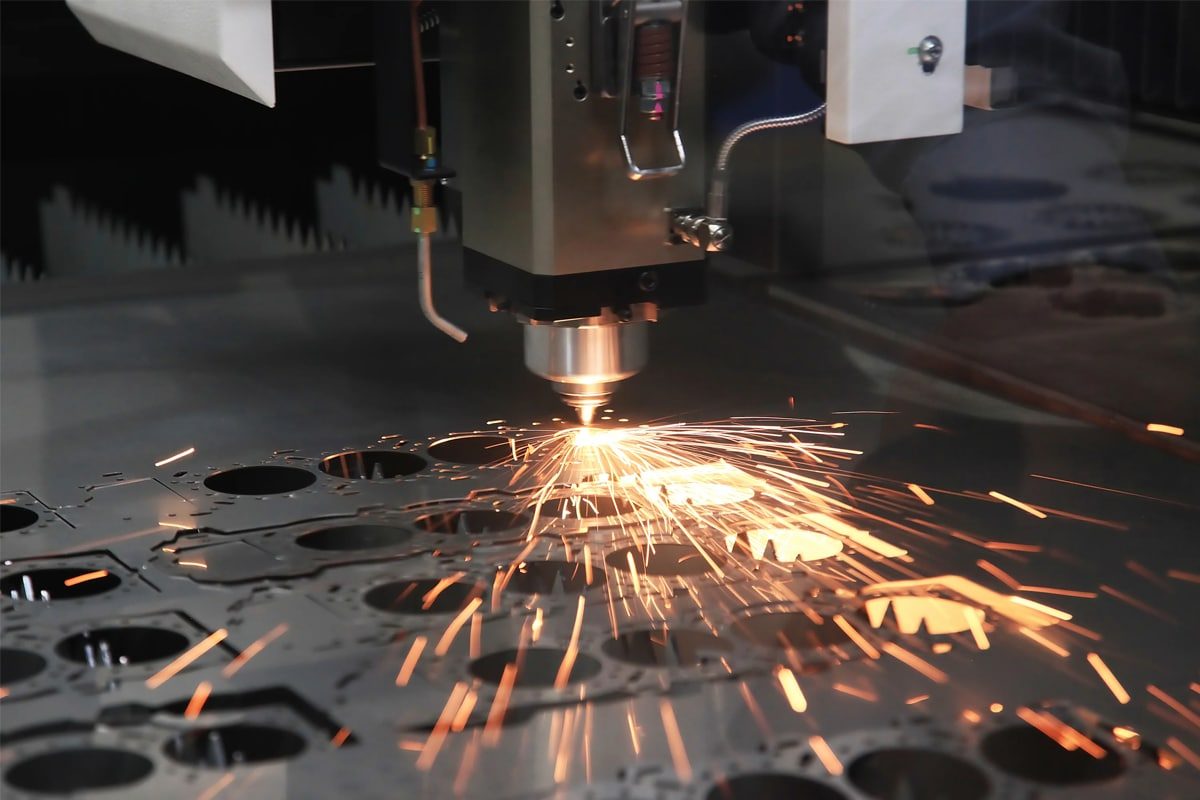
Fiber Laser Cutting VS CO2 Laser Cutting
In today’s manufacturing industry, laser cutting technology plays a crucial role in enabling precise, efficient, and versatile processing across multiple sectors. Among the most widely used laser technologies are fiber laser cutting and CO2 laser cutting, each offering unique benefits and capabilities. Fiber lasers excel in cutting metals, including reflective materials like aluminum and copper, thanks to their shorter wavelength and high energy efficiency. In contrast, CO2 lasers provide excellent versatility, cutting both metals and non-metals such as wood, acrylic, and textiles, making them a preferred choice for industries requiring diverse material processing. However, because there are differences in speed, material compatibility, maintenance, and operating costs, choosing the right laser technology can help companies achieve their production goals. This article provides a detailed comparison of fiber laser cutting versus CO2 laser cutting, helping manufacturers understand the advantages and limitations of each and make an informed decision based on their specific requirements.
Table of Contents
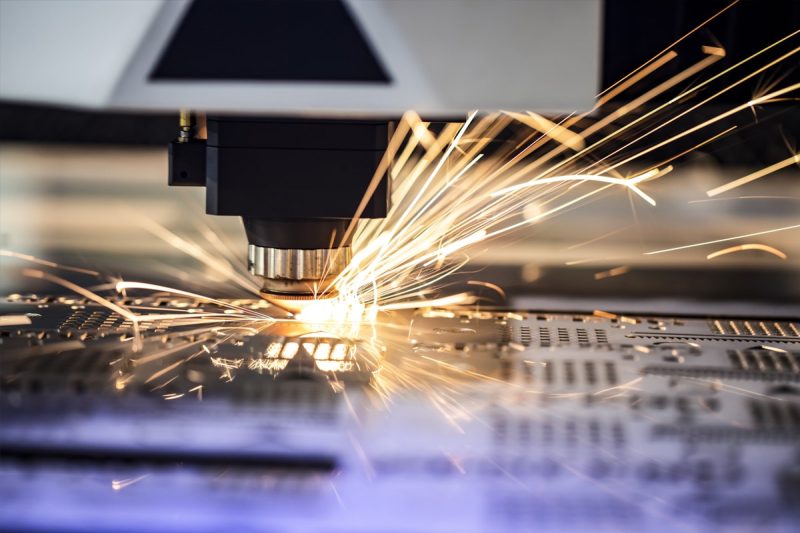
Understanding Laser Cutting Technology
Laser cutting is a precise and versatile technology used in various industries to cut materials by focusing a high-powered laser beam onto the surface of the workpiece. The concentrated beam melts, burns, or vaporizes the material, creating clean and accurate cuts. The popularity of laser cutting stems from its ability to handle complex designs with high precision and its efficiency in mass production.
There are different types of laser technologies, but fiber lasers and CO2 lasers are the most prominent in industrial applications. Each operates on different principles and is suitable for different types of materials and cutting processes.
Fiber Laser Cutting uses optical fibers doped with rare-earth elements, such as ytterbium, to generate and amplify the laser beam. This technology produces a wavelength of around 1.06 micrometers (μm), which is highly effective for cutting metals, especially reflective materials like aluminum, brass, and copper. Fiber lasers are also known for their high energy efficiency, speed, and low maintenance requirements.
CO2 Laser Cutting, on the other hand, utilizes a gas mixture—primarily carbon dioxide, nitrogen, and helium—to generate the laser beam with a wavelength of approximately 10.6 μm. This technology is highly versatile and is widely used for cutting non-metal materials such as wood, acrylic, glass, and textiles. CO2 lasers also perform well when cutting thicker metal materials, although they tend to have higher energy consumption and maintenance requirements compared to fiber lasers.
Both fiber and CO2 laser technologies have their specific strengths and applications, and understanding the differences between them is crucial for manufacturers seeking to optimize production efficiency and material compatibility. This knowledge can help in selecting the most suitable laser-cutting technology based on the material type, thickness, production volume, and operational costs.
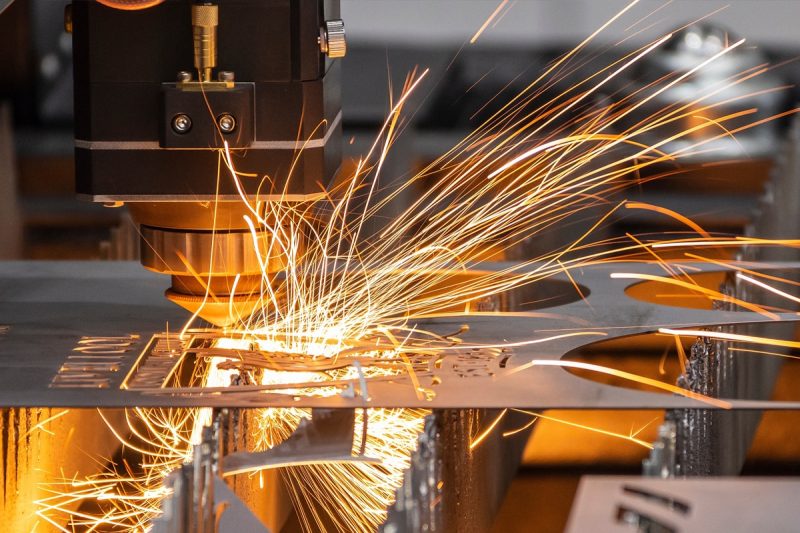
Overview of Fiber Laser Cutting
Principles of Fiber Laser Cutting
Fiber laser cutting utilizes a solid-state laser that generates light through an optical fiber doped with rare-earth elements, typically ytterbium. The laser beam, with a wavelength of approximately 1.06 micrometers (μm), is transmitted through a fiber cable to the cutting head. This beam is highly focused, producing intense heat that melts or vaporizes the material in the path of the laser. Fiber lasers are known for their excellent beam quality, with a smaller spot size that enables precise and clean cuts. Additionally, the shorter wavelength allows the beam to be efficiently absorbed by metals, including reflective ones, without back-reflection risks.
The entire cutting process is aided by auxiliary gases such as nitrogen or oxygen, which assist in blowing away molten material and creating smoother edges. The high power density of fiber lasers ensures rapid cutting, even on thin or reflective materials, making them a preferred solution in various industries.
Advantages of Fiber Laser Cutting
- High Speed and Efficiency: Fiber lasers can cut thin materials, such as stainless steel or aluminum, up to three times faster than CO2 lasers, ensuring high production efficiency.
- Energy Efficiency: Fiber lasers consume significantly less energy, with about one-third the power requirements of CO2 lasers, reducing operational costs.
- Low Maintenance Requirements: The solid-state construction eliminates the need for mirrors or gas refills, resulting in low maintenance and long service life. The laser modules have a lifespan exceeding 100,000 hours.
- Ability to Cut Reflective Metals: Fiber lasers can handle reflective materials like copper and brass without back-reflection issues, which makes them ideal for industries working with a variety of metals.
- High Precision: With a smaller spot size and excellent beam quality, fiber lasers enable intricate cuts and produce minimal burrs, enhancing overall product quality.
- Versatility in Automation: Fiber lasers are compatible with automated systems, enabling seamless integration with robotic arms or other automated manufacturing processes.
Disadvantages of Fiber Laser Cutting
- Limited Performance on Non-Metal Materials: The shorter wavelength of fiber lasers makes them less effective on non-metal materials, such as wood, glass, or acrylic, limiting their versatility.
- Edge Quality on Thick Metals: While fiber lasers excel at cutting thin to medium-thickness metals, they may struggle with edge smoothness on thicker materials compared to CO2 lasers.
- Higher Initial Investment: Fiber laser cutting machines tend to have a higher upfront cost compared to CO2 laser systems, making the initial investment significant for some businesses.
Applications of Fiber Laser Cutting
- Automotive Industry: Fiber laser cutting is widely used for manufacturing vehicle components, including thin metal panels, exhaust systems, and intricate brackets.
- Aerospace Industry: The precision and speed of fiber lasers make them ideal for cutting lightweight metals used in aircraft and spacecraft manufacturing.
- Metal Fabrication and Sheet Metal Processing: Fiber lasers are commonly employed in the metalworking industry for high-speed cutting of stainless steel, aluminum, and other metals.
- Electronics Industry: Precision cutting of small metal parts, including connectors and housings for electronics, is efficiently handled by fiber laser machines.
- Medical Industry: Fiber laser cutting plays a crucial role in producing surgical instruments and medical devices made from metals like stainless steel and titanium.
- Jewelry Manufacturing: The precision and ability to cut reflective materials make fiber lasers ideal for creating intricate designs in gold, silver, and other metals used in jewelry.
Fiber laser cutting is a highly efficient and precise technology, particularly suited for industries that require high-speed processing of metal materials. While it may have some limitations regarding non-metal materials, its advantages in speed, energy efficiency, and minimal maintenance make it an optimal choice for metal-intensive applications.
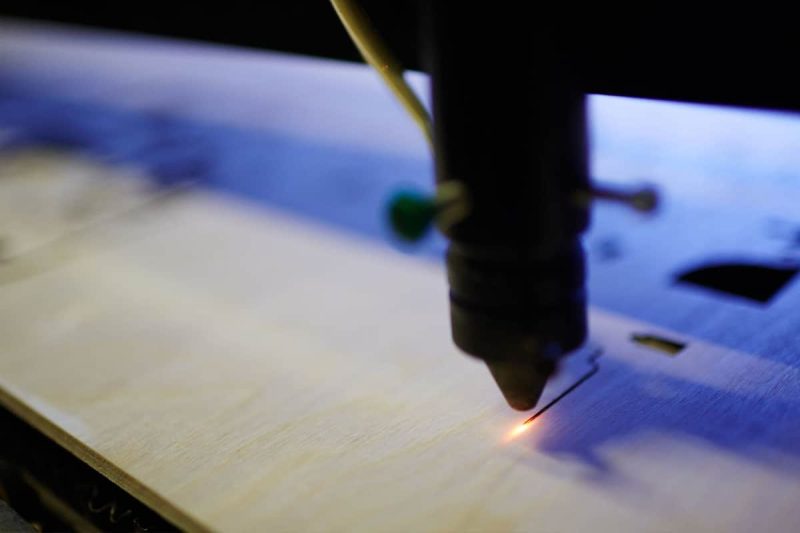
Overview of CO2 Laser Cutting
Principles of CO2 Laser Cutting
CO2 laser cutting relies on a gas mixture—mainly carbon dioxide (CO2), nitrogen, and helium—as the lasing medium. When an electric current excites the gas molecules, they emit photons that are reflected through mirrors inside the laser resonator, amplifying the light into a powerful laser beam. This beam has a wavelength of 10.6 micrometers (μm), which is in the far-infrared spectrum.
The laser beam is directed through a series of mirrors and focused onto the material surface, generating enough heat to melt, vaporize, or burn the material. Auxiliary gases, such as oxygen or nitrogen, assist in removing molten material from the cut and help maintain a clean edge.
CO2 lasers are highly versatile and can cut a wide range of materials, including metals and non-metals, making them a popular choice for applications that require more than just metal cutting.
Advantages of CO2 Laser Cutting
- Versatile Material Processing: CO2 lasers can cut both metals and non-metals, including wood, plastics, glass, acrylic, textiles, and leather, making them a preferred option for industries with diverse material requirements.
- High Edge Quality on Thicker Materials: CO2 lasers offer smooth and clean edge finishes, especially on thicker metals and organic materials, minimizing the need for post-processing.
- Better Performance on Non-Metals: With a longer wavelength, CO2 lasers are more effective at cutting non-metal materials compared to fiber lasers, making them suitable for signage, textile, and woodworking industries.
- Availability and Maturity: CO2 laser technology has been around for decades, leading to widespread availability, reliability, and well-understood operation.
- Cost-Effective for Certain Applications: In scenarios where non-metals need to be cut in high volumes, CO2 lasers are often more cost-effective compared to fiber lasers, especially for thicker non-metal materials.
Disadvantages of CO2 Laser Cutting
- Higher Energy Consumption: CO2 lasers require more power to operate compared to fiber lasers, leading to higher operational costs, especially in large-scale production.
- Increased Maintenance Requirements: The laser beam is delivered using mirrors, which require frequent cleaning, alignment, and maintenance. Additionally, the gas mixture needs to be replaced periodically.
- Difficulty Cutting Reflective Metals: CO2 lasers struggle with reflective metals like aluminum, copper, and brass due to the risk of back-reflection, which can damage the laser optics.
- Slower Cutting Speeds on Thin Metals: For thinner metals, CO2 lasers are slower than fiber lasers, making them less efficient for high-speed production environments focused on metal cutting.
- Shorter Lifespan of Optical Components: The optics, including mirrors and lenses, are subject to wear and tear, requiring regular replacements and increasing maintenance costs over time.
Applications of CO2 Laser Cutting
- Signage and Advertising: CO2 lasers are widely used for cutting and engraving acrylics, plastics, and other non-metal materials for high-quality signs and displays.
- Textile and Fashion Industry: CO2 laser cutting provides precise and intricate patterns on fabrics, leather, and textiles, helping manufacturers create customized designs efficiently.
- Woodworking and Furniture Production: CO2 lasers excel in cutting and engraving wood, MDF, and plywood, making them ideal for decorative woodworking and furniture production.
- Packaging and Printing Industry: Paper, cardboard, and other packaging materials are easily cut or engraved with CO2 lasers for customized packaging solutions.
- Glass and Ceramics Processing: CO2 lasers can engrave intricate designs on glass surfaces and process ceramics, making them valuable for decorative applications.
- Metal Fabrication: While CO2 lasers are not as effective as fiber lasers for reflective metals, they are still widely used to cut carbon steel and stainless steel, especially in thicker gauges.
CO2 laser cutting remains a versatile and reliable technology for industries that require the processing of non-metal materials and thicker metal sheets. Although they may require more maintenance and consume more energy, CO2 lasers excel in applications where smooth edge quality, material versatility, and the ability to cut non-metals are essential. This makes them a valuable option for sectors such as woodworking, signage, textiles, and packaging, where a wide range of materials needs to be handled efficiently.
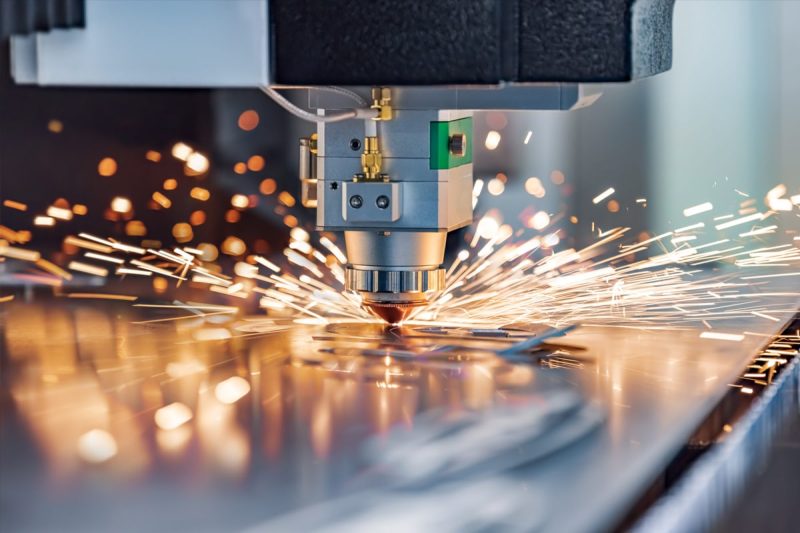
Detailed Comparison Between Fiber Laser and CO2 Laser Cutting
Cutting Speed and Efficiency
- Fiber Laser Cutting is generally faster than CO2 laser cutting, particularly for thin metals. The shorter wavelength of fiber lasers (around 1.06 μm) allows for better absorption in metals, enabling higher energy density and faster cutting speeds, particularly on materials like stainless steel, aluminum, and brass. Fiber lasers can be up to three times faster than CO2 lasers when cutting thin metals, which makes them ideal for high-volume production environments.
- CO2 Laser Cutting, while slower on thin metals, is more efficient when cutting thicker materials or non-metals. The longer wavelength (10.6 μm) is less effective for metals but works well for a wider range of materials, including wood, acrylic, and glass. In thicker materials, CO2 lasers provide consistent cutting performance, though at slower speeds compared to fiber lasers.
Material Compatibility
- Fiber Laser Cutting is specifically suited for cutting metals. It excels in cutting highly reflective metals, such as aluminum, copper, and brass, without back-reflection issues. However, fiber lasers are less effective at cutting non-metallic materials due to their short wavelength, which is not readily absorbed by non-metals like wood or plastic.
- CO2 Laser Cutting is far more versatile in terms of material compatibility. It can cut metals but is particularly effective for non-metals like wood, plastic, acrylic, textiles, glass, and even some ceramics. This versatility makes CO2 lasers an excellent choice for industries that need to process a wide variety of materials. However, CO2 lasers struggle with reflective metals like aluminum and brass.
Thickness of Materials
- Fiber Laser Cutting performs exceptionally well on thin to medium-thickness metals (up to 20 mm for steel). Beyond these thicknesses, the efficiency and cut quality may decline, and fiber lasers may require higher power levels to maintain performance. Thicker materials can be cut with fiber lasers, but the cut quality, particularly the edge finish, can diminish.
- CO2 Laser Cutting tends to excel when cutting thicker materials, both metals and non-metals. CO2 lasers can handle thicker sheets of metal more effectively than fiber lasers, particularly for non-metals. For metals, CO2 lasers can achieve clean cuts in thicker sections (up to 25 mm for steel) with a smoother edge quality compared to fiber lasers.
Operating Costs
- Fiber Laser Cutting generally has lower operating costs. Fiber lasers are solid-state machines that require fewer consumables, and their energy-efficient design keeps running costs down. They do not need regular gas refills or frequent component replacement, which reduces ongoing expenses.
- CO2 Laser Cutting, by comparison, has higher operating costs due to the need for consumables such as gas mixtures (CO2, nitrogen, helium) and more frequent maintenance of mirrors and lenses. The higher energy consumption of CO2 lasers also contributes to increased operational costs, particularly in large-scale production.
Maintenance Requirements
- Fiber Laser Cutting requires minimal maintenance. Since fiber lasers use fiber optics to deliver the laser beam, they eliminate the need for mirrors or other optical components that require alignment. The solid-state design of fiber lasers also means fewer parts that can wear out over time, making them low-maintenance.
- CO2 Laser Cutting, in contrast, requires more frequent maintenance. CO2 lasers use mirrors and lenses to direct the laser beam, which needs regular cleaning, alignment, and replacement. Additionally, the gas mixture used in the laser requires periodic refilling or replacement, adding to the machine’s maintenance burden.
Energy Efficiency
- Fiber Laser Cutting is significantly more energy-efficient compared to CO2 lasers. Fiber lasers use approximately one-third of the energy that a CO2 laser would require for the same cutting task. This efficiency is particularly evident when cutting thin metals, making fiber lasers a more eco-friendly option with lower energy bills over time.
- CO2 Laser Cutting consumes more energy due to its reliance on electrically excited gas molecules. The overall energy efficiency of CO2 lasers is lower, which can lead to higher electricity costs, particularly for heavy industrial applications requiring continuous use.
Beam Quality
- Fiber Laser Cutting offers superior beam quality, producing a smaller focused spot size. This allows for more precise and cleaner cuts, making fiber lasers ideal for applications requiring intricate designs and tight tolerances.
- CO2 Laser Cutting also provides good beam quality, but the larger spot size compared to fiber lasers means it may not be as precise, particularly when cutting very thin materials or performing detailed work. However, CO2 lasers are known for their ability to deliver high-quality cuts on non-metal materials.
Edge Quality and Finish
- Fiber Laser Cutting excels at producing clean, burr-free edges, particularly on thin metals. The smaller spot size and focused heat distribution allow for fine detailing and minimal post-processing. However, when cutting thicker metals, the edge quality may not be as smooth as CO2 lasers, often requiring additional finishing work.
- CO2 Laser Cutting generally provides superior edge quality on thicker materials and non-metals. For metals, the edge smoothness is often better compared to fiber lasers when cutting thicker gauges. CO2 lasers also produce excellent edge finishes on non-metals like acrylic and wood, making them suitable for industries where surface finish is critical.
Initial Investment
- Fiber Laser Cutting typically has a higher initial investment cost compared to CO2 laser cutting systems. The advanced technology and components of fiber lasers, particularly the laser source and optical fiber delivery system, contribute to a higher upfront price. However, the lower operating costs and reduced maintenance often offset this initial expense over time.
- CO2 Laser Cutting systems generally have a lower initial investment cost, making them more accessible to businesses with budget constraints. Despite this lower cost, the higher operational expenses and maintenance requirements can make CO2 lasers more expensive in the long run.
Footprint and Installation
- Fiber Laser Cutting systems tend to have a more compact design, requiring less space for installation. Their solid-state configuration means fewer moving parts and components, which reduces the overall footprint of the machine. This makes fiber lasers ideal for smaller workshops or production facilities with limited space.
- CO2 Laser Cutting machines are typically larger due to the gas supply system, mirrors, and lenses. They often require more space and a carefully controlled environment to ensure optimal performance, which can be a disadvantage for businesses with limited floor space.
Environmental Considerations
- Fiber Laser Cutting is more environmentally friendly due to its higher energy efficiency and fewer consumables. Fiber lasers do not rely on gas mixtures or frequent replacements of optical components, which reduces waste. Additionally, lower energy consumption means a reduced carbon footprint, making fiber lasers the more sustainable option.
- CO2 Laser Cutting, while effective, has a higher environmental impact. The use of gas mixtures and frequent maintenance contributes to more waste, and the higher energy consumption results in a larger carbon footprint. In applications requiring long-term sustainability, fiber lasers are generally the preferred choice.
Safety Considerations
- Fiber Laser Cutting operates at a shorter wavelength (1.06 μm), which is more hazardous to the eyes and skin. Therefore, strict safety protocols are necessary, including enclosures and protective eyewear, to prevent accidents. Due to the intensity of the laser, exposure risks are higher, particularly in open workspaces.
- CO2 Laser Cutting, with its longer wavelength (10.6 μm), is somewhat less penetrative but still requires safety precautions, especially regarding eye and skin exposure. The risk of back-reflection damage is lower in CO2 systems, but safety measures, including proper protective equipment, are still necessary to ensure operator safety.
Both fiber laser cutting and CO2 laser cutting have unique strengths and weaknesses. Fiber lasers offer higher speed, energy efficiency, and precision, especially for metals, but come with higher upfront costs. CO2 lasers excel in material versatility, cutting thicker materials and non-metals effectively, although they require more maintenance and higher operational costs. Understanding these differences allows manufacturers to select the appropriate technology based on material type, production volume, and budgetary constraints.
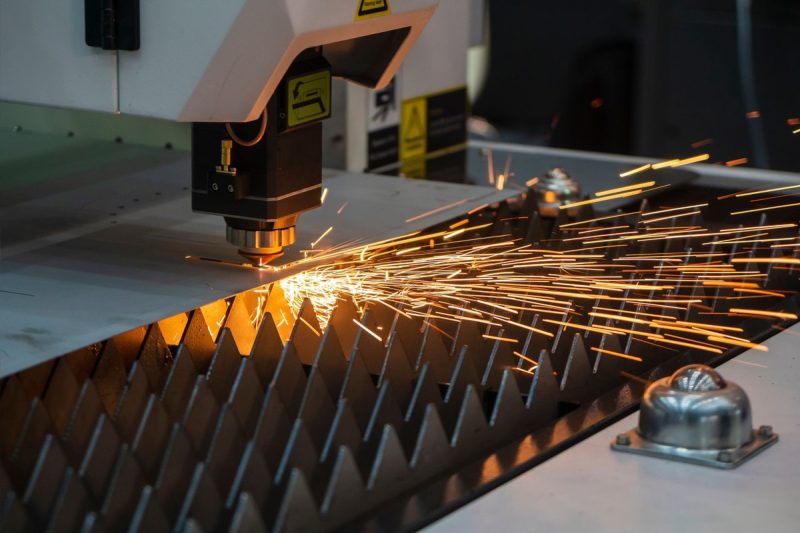
Choosing the Right Laser Cutting Technology
Selecting the right laser-cutting technology depends on several factors, including the materials being processed, production volume, operational costs, and the specific requirements of your application. Both fiber laser cutting and CO2 laser cutting offer unique benefits and limitations. By carefully evaluating your business needs, you can determine which technology is better suited for your operations. Below are key considerations to guide you in making an informed choice.
Material Type and Compatibility
- Fiber Laser Cutting: Best for metal-focused applications. It handles a wide range of metals, including reflective materials like aluminum, copper, and brass, without the risk of damaging the laser. If your business primarily processes metals, fiber laser cutting is the optimal choice.
- CO2 Laser Cutting: More versatile for non-metal materials. If you need to work with wood, acrylic, glass, textiles, or other organic materials, CO2 lasers are more effective. They also perform well on thicker metal sheets but may struggle with highly reflective metals.
Recommendation:
- Choose fiber laser cutting if your primary focus is metal cutting.
- Opt for CO2 laser cutting if your operations require non-metal processing or a variety of material types.
Cutting Thickness Requirements
- Fiber Laser Cutting: Ideal for thin to medium-thickness metals (up to 50 mm). It offers faster cutting speeds for thin materials but may require higher power to maintain quality on thicker metals.
- CO2 Laser Cutting: Performs better on thicker materials and can handle both thick metals and non-metals effectively. If you need to cut process thicker non-metals, CO2 technology is preferable.
Recommendation:
- Use fiber laser cutting for thin to moderately thick metals.
- Opt for CO2 laser cutting for thicker materials or diverse material thicknesses.
Production Speed and Volume
- Fiber Laser Cutting: Faster on thin metals, making it suitable for high-volume production and industries requiring rapid turnaround, such as automotive and electronics manufacturing.
- CO2 Laser Cutting: While it excels in thicker materials, CO2 laser cutting is generally slower for thin metals, which may affect productivity in high-speed manufacturing environments.
Recommendation:
- Choose fiber laser cutting for fast, high-volume production.
- Opt for CO2 laser cutting if speed is not a primary concern and versatility is more critical.
Operational Costs and Energy Efficiency
- Fiber Laser Cutting: More energy-efficient, consuming about one-third of the power required by CO2 lasers for similar tasks. Solid-state construction means lower maintenance and fewer consumables, reducing long-term operating costs.
- CO2 Laser Cutting: Higher operational costs due to greater energy consumption, gas requirements, and more frequent maintenance, including mirror and lens replacements.
Recommendation:
- Use fiber laser cutting if you prioritize energy savings and want to minimize operational costs.
- Choose CO2 laser cutting if the initial savings on equipment are more critical than long-term efficiency.
Maintenance and Machine Longevity
- Fiber Laser Cutting: Requires less maintenance with fewer consumable components. It offers a long service life, with laser modules typically lasting over 100,000 hours.
- CO2 Laser Cutting: Demands more frequent maintenance, including the replacement of optics and gas mixtures, which can lead to increased downtime and operational disruptions.
Recommendation:
- Choose fiber laser cutting if low maintenance and uptime are essential for your operations.
- Opt for CO2 laser cutting if your business can manage regular maintenance.
Budget and Initial Investment
- Fiber Laser Cutting: Involves a higher initial investment due to the advanced technology and components. However, lower operational costs and minimal maintenance can result in better long-term ROI.
- CO2 Laser Cutting: Requires a lower upfront cost, making it more accessible for smaller businesses or those with limited budgets. However, the higher operational costs over time may offset the initial savings.
Recommendation:
- Invest in fiber laser cutting if you are looking for long-term cost savings.
- Opt for CO2 laser cutting if you need a lower-cost entry point.
Space and Installation Requirements
- Fiber Laser Cutting: Compact design with fewer components, making it easier to install in smaller spaces or workshops.
- CO2 Laser Cutting: Larger footprint due to the gas system and optical components, requiring more floor space and careful installation.
Recommendation:
- Choose fiber laser cutting for facilities with limited space.
- Opt for CO2 laser cutting if you have sufficient room for installation.
Environmental and Safety Considerations
- Fiber Laser Cutting: More environmentally friendly due to lower energy consumption and fewer consumables. However, it requires strict safety protocols to manage the risks associated with the shorter wavelength, which can cause severe eye and skin injuries.
- CO2 Laser Cutting: While it consumes more energy, the longer wavelength poses a slightly lower risk to operators. However, safety measures are still necessary to prevent burns or other injuries.
Recommendation:
- Choose fiber laser cutting if environmental sustainability and energy efficiency are priorities.
- Opt for CO2 laser cutting if your focus is on non-metal processing, but ensure safety measures are in place for both technologies.
Choosing between fiber laser cutting and CO2 laser cutting depends on your specific production needs, materials, budget, and long-term goals. Fiber laser cutting is the ideal choice for businesses focusing on high-speed metal processing with minimal maintenance and energy costs. On the other hand, CO2 laser cutting offers greater versatility for non-metal applications and thicker materials, though at the cost of higher energy consumption and more frequent maintenance.
Ultimately, the right laser-cutting technology is the one that aligns with your production requirements and business strategy. By carefully considering the factors outlined above, you can make an informed decision and select the technology that will optimize your production efficiency and profitability.
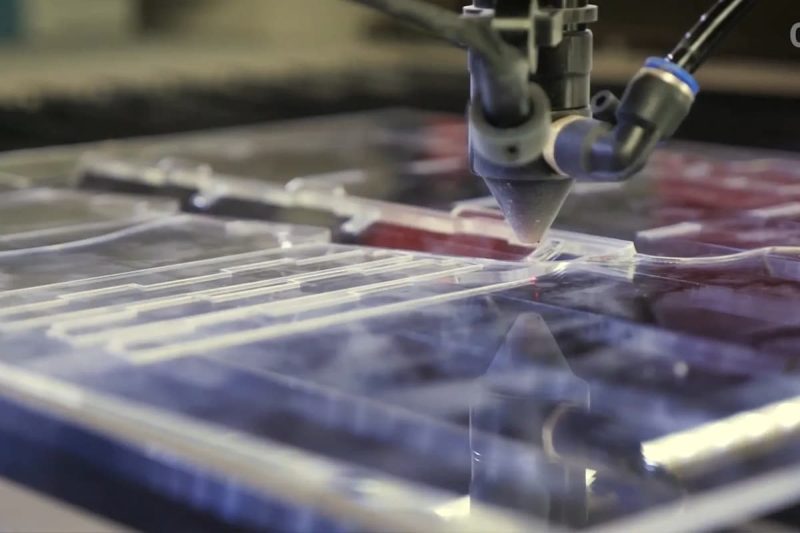
Summary
Both fiber laser cutting and CO2 laser cutting offer unique advantages, making them suitable for different applications. Fiber lasers excel in cutting metals, especially thin and reflective materials like aluminum, copper, and brass, with high speed, precision, and energy efficiency. They are ideal for industries that focus on metal fabrication, automotive parts, and electronics, where high productivity and low maintenance are essential. In contrast, CO2 lasers are highly versatile and capable of cutting both metals and non-metals, including wood, acrylic, glass, and textiles. They provide excellent edge quality on thicker materials and are preferred for industries like signage, packaging, and woodworking.
Choosing the right technology depends on your specific needs. Fiber lasers offer better performance for metal-intensive applications, lower operational costs, and minimal maintenance. CO2 lasers, with their ability to handle a wider range of materials, are better suited for businesses requiring material flexibility. Both technologies have distinct strengths, and selecting the right one ensures optimized performance, efficiency, and cost-effectiveness in your operations.
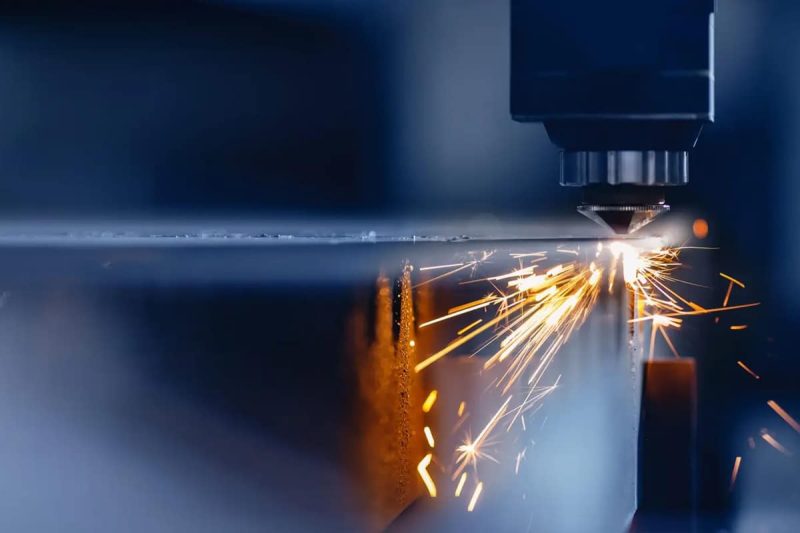
Get Laser Cutting Solutions
Choosing the right laser-cutting technology can achieve the best efficiency and precision in production. Whether you need the speed and metal-cutting prowess of fiber lasers or the material versatility of CO2 lasers, AccTek Laser offers comprehensive solutions tailored to your specific needs. As a professional manufacturer of laser cutting machines, we provide state-of-the-art equipment designed for reliability, precision, and cost-efficiency.
Our fiber laser cutting machines are ideal for industries focusing on metal processing, including automotive, aerospace, and electronics. For businesses requiring diverse material processing, our CO2 laser cutting machines excel in handling non-metals like wood, acrylic, and textiles. AccTek Laser also offers expert consultation to help you select the right machine and configuration for your operations.
With AccTek’s advanced laser technology, responsive technical support, and commitment to quality, you can enhance your production capabilities and achieve superior results. Contact us today to find the perfect laser-cutting solution for your business.
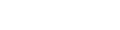
Contact information
- [email protected]
- [email protected]
- +86-19963414011
- No. 3 Zone A, Lunzhen Industrial Zone,Yucheng City , Shandong Province.
Get Laser Solutions