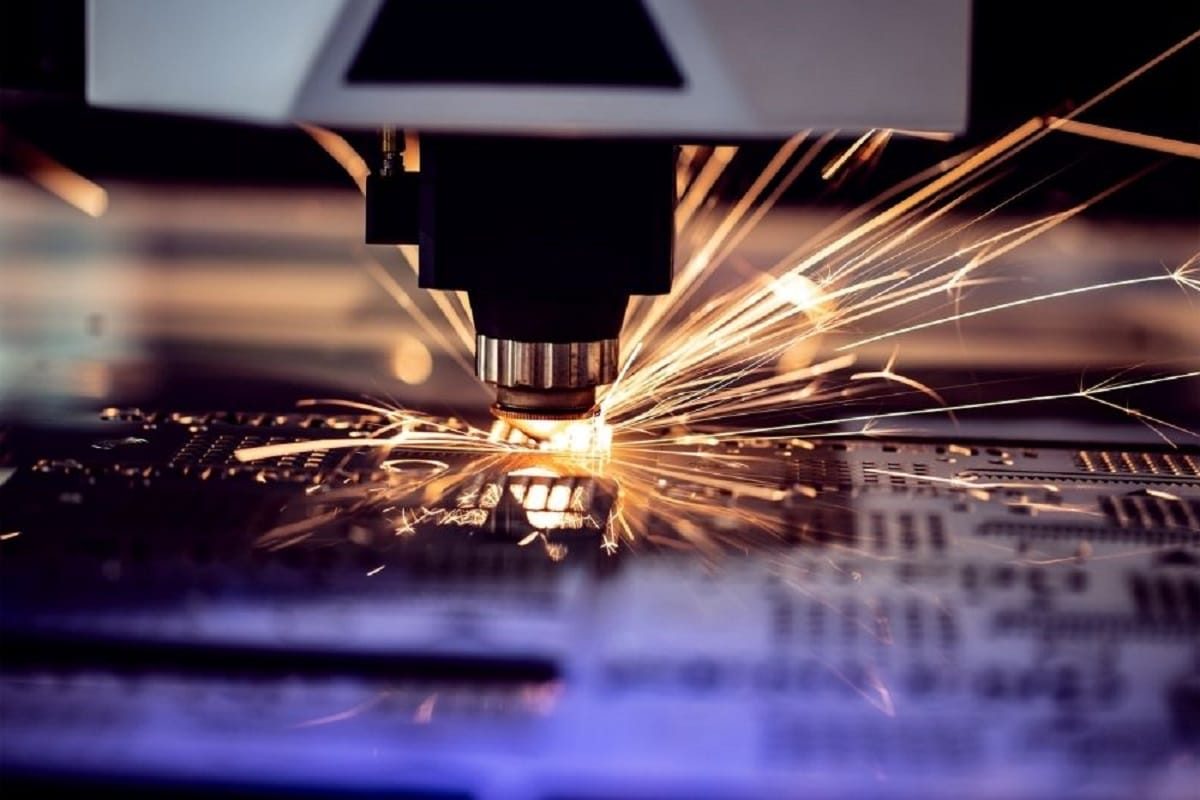
Design Considerations For Laser Cutting
Laser cutting has become a versatile and precise technology with applications spanning industries from manufacturing to art and design. At the same time, its ability to create intricate patterns, detailed cuts, and clean edges makes it the first choice for many projects. However, like any process, laser cutting has its own set of design considerations and limitations that designers and engineers must overcome to achieve the desired cutting results. In this article, we explore these design factors in detail.
Table of Contents
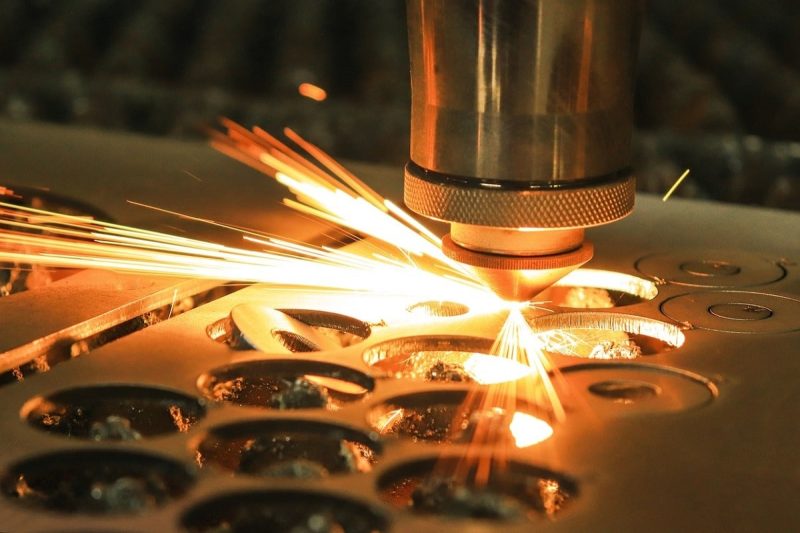
Interior Design Considerations
Interior design considerations using laser cutting technology focus on the specific features, shapes, and characteristics of the design itself. These considerations help ensure that your design is well suited for laser cutting technology and may impact the success of the cutting process and the quality of the final product. The following are key interior design considerations when using laser cutting:
Closed shapes and perforations
- Laser cutting is most efficient when working with closed shapes or contours. Because these shapes keep the material stable during the cutting process and make it easier for the laser to follow accurately.
- When perforations (holes) are included in the design, you need to make sure they are spaced sufficiently apart and are large enough to avoid deformation of the material or difficulty cutting. Consider the thickness of the material and the capabilities of the laser generator.
Feature dimensions and tolerances
Design features should be consistent with the functionality of the laser generator and the thickness of the material used. The following aspects need to be focused on:
- Feature Dimensions: Pay close attention to features in your design, such as holes, slots, and cuts. Make sure they are sized appropriately for the material thickness and laser capabilities. Performance characteristics may not be achievable or may require specialized laser equipment.
- Tolerances: Incorporate appropriate tolerances into your design to account for the width of the laser beam (kerf) and any potential material variations. Proper tolerances help ensure parts fit together accurately after cutting.
Sharp corners and inner radii
- Extremely sharp corners in the design can create challenges for laser cutting. Since the laser beam has a limited diameter, it tends to produce slight rounding.
- To improve cutting accuracy, consider adding small fillets or rounded corners to your design. Make sure the inner radius is designed to fit the laser beam diameter to avoid unintended cuts or material removal.
Material compatibility
- Make sure the materials you choose for your project are compatible with the laser-cutting process. Different materials have different absorptive properties and cutting capabilities.
- Understand how your chosen materials perform under laser-cutting conditions so you can optimize your designs accordingly.
Design complexity
- Laser cutting is great for intricate designs and you can take advantage of this feature by designing detailed and precise patterns.
- However, achieving extremely fine details with laser cutting, especially those smaller than the diameter of the laser beam (kerf), can be challenging.
Cutting compensation
- Consider the width of the laser beam (kerf) to adjust your design, which may involve cutting the line slightly inward to get the desired part size.
Nesting considerations
- If you plan to nest multiple parts or patterns on a single sheet of material, design in a way that optimizes material use while ensuring there is enough spacing between parts to avoid interference during cutting.
Material thickness
- Design features should be consistent with the thickness of the material used. If your design includes different material thicknesses, make sure your laser cutting machineis set up appropriately to handle these variations.
Material grain direction
- Consider the grain direction of the material, especially materials like wood or certain metals. Adjust your design to align with or adapt to the grain direction for better results.
Internal features and cavities
- Laser cutting machines may not be able to access internal features or cavities in materials, so plan your design accordingly and consider alternative manufacturing methods if internal cuts are required.
By addressing these internal design considerations, you can optimize your laser cutting design, increase the efficiency and accuracy of the cutting process, and ensure that the final cut part meets the project’s requirements. Working with an experienced laser-cutting service provider or engineer can provide valuable guidance on your design and material selection.

External Design Considerations
Exterior design considerations for laser cutting focus on factors outside of the design itself, but are critical to the success of the cutting process and the overall quality of the result. These considerations include factors related to overall process, material handling, and machine operation. The following are key exterior design considerations when using laser cutting:
Material support
- Properly support materials on the cutting table to prevent warping, vibration, or material deformation during cutting. Insufficient support can cause inaccurate cuts and reduce cut quality.
Material handling and alignment
- Properly load and align the material on the cutting table to ensure it remains flat, stable, and securely positioned during the cutting process.
- Misaligned or unstable materials can cause inaccurate cuts and reduce cut quality.
Ventilation and airflow
- Depending on the material being cut, laser cutting can produce smoke and gases. Make sure your design allows for proper ventilation and scheduling to eliminate these by-products in the cutting area.
- Adequate airflow helps clear debris from the cutting area and maintains a clear-cutting path. It is recommended to consult your laser cutting machinemanufacturer to determine the appropriate gas flow rate and type for your materials.
Lead-in and lead-out wires
- Incorporate lead-in and lead-out paths into your design. These paths are the entrance and exit points for the laser beam, helping to ensure that the cutting process starts and stops smoothly.
- Lead-in and lead-out lines can prevent unnecessary marks or defects at the beginning and end of the cutting, thereby improving cutting quality.
Avoid overcuts and undercuts
- Overcut occurs when the laser beam extends slightly beyond the intended cutting path, resulting in excessive material removal.
- Undercutting occurs when the laser beam does not reach the intended cutting path, potentially leaving uncut material.
- These issues can be minimized by fine-tuning the design, optimizing cutting parameters, and ensuring that the laser cutting machineis well-maintained.
External support structure
- If your design includes delicate or thin parts that may move easily during the cutting process, consider adding external support structures or tabs to hold the parts in place until the cutting process is complete.
- These support structures can be removed after the cut is complete.
Nozzle positioning and focus
- Make sure the laser cutting nozzle is positioned correctly and focused on the material being cut. Proper nozzle alignment and focus are critical to achieving precise cuts.
Machine safety measures
- Implement safety measures when handling materials and operating laser-cutting equipment. Follow safety guidelines, use appropriate personal protective equipment (PPE), and provide adequate ventilation to protect the operator and maintain a safe work environment.
Machine maintenance
- Regularly maintain and calibrate your laser cutting machine to ensure optimal performance. Proper maintenance can help prevent problems such as beam misalignment or power fluctuations that can affect cut quality.
Laser beam focusing and power adjustment
- Depending on the material and thickness, adjust the focus and power settings of the laser beam to optimize the cutting process. It may take some experimentation and testing to find the ideal settings.
Nozzle cleaning and maintenance
- Clean and maintain your laser cutting nozzle regularly to ensure optimal performance. Clean nozzles help maintain consistent cut quality and accuracy.
Waste management
- Develop a waste management plan to deal with scraps and waste generated during the cutting process. Proper waste disposal helps maintain a clean and safe workspace.
By addressing these external design considerations, you can contribute to the successful execution of the laser cutting process, minimize potential problems or defects, and help ensure that the final cut part meets the required quality standards. Working with an experienced laser-cutting service provider or operator can also provide valuable guidance on optimizing external factors for your laser-cutting project.
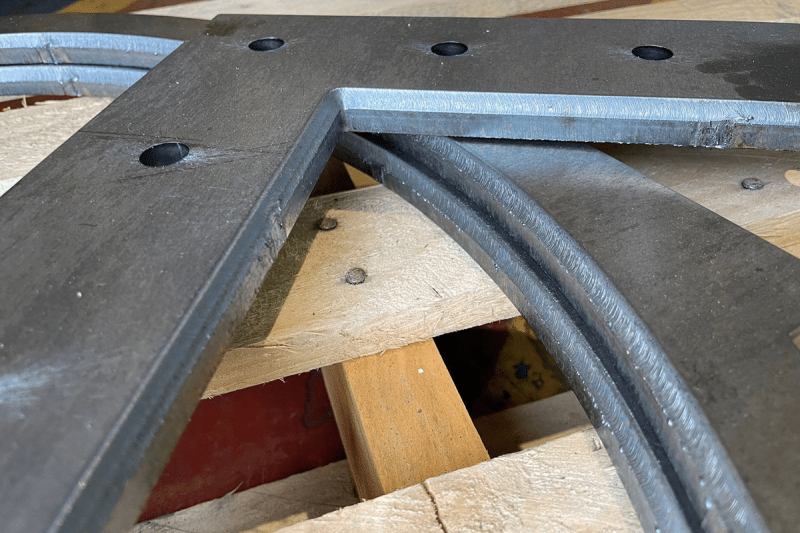
Nested Optimization
Nesting optimization design in laser cutting arranges parts or patterns on the material sheet in the most efficient way to minimize waste and maximize material utilization. Correct nesting can result in significant cost savings, reduced material waste and increased production efficiency. For best results in nested optimization for laser cutting, consider the following key considerations:
Part geometry and orientation
- Analyze part geometry and select appropriate nesting to maximize space utilization and minimize material waste.
- Optimize part orientation to reduce material movement during cutting and minimize laser head travel time.
Optimal panel size selection
- Choose a material sheet size that closely matches the part or pattern dimensions. Using appropriately sized boards minimizes waste and maximizes material utilization. Avoid using boards that are much larger than necessary.
Nesting software
- Take advantage of features in specialized nesting software or design software to automate the nesting process. These tools analyze your design, material sheet dimensions, and cutting parameters to automatically optimize nesting.
Material efficiency
- Prioritize efficient material utilization by placing parts closely together without overlapping. Avoiding excessive spacing between parts helps reduce waste and lower production costs.
Avoid overlapping cuts
- Make sure the cutting paths for different parts do not overlap. Overlapping cuts can cause irregular edges and waste material. Nesting software can be used to automatically arrange parts to avoid overlap.
Material thickness consistency
- Make sure the thickness of the material is consistent throughout the sheet to maintain uniform cut quality and avoid variations that could affect nesting. Additionally, variations in material thickness can lead to inconsistent cutting results.
Optimize panel utilization
- Using nesting software, you can calculate the most efficient way to arrange parts on a sheet of material, taking into account irregular shapes and material properties. Some software can even rotate parts to minimize waste.
- In some cases, manually arranging parts according to your specific requirements may produce better results than relying solely on automated nesting software. Experiment with different arrangements to find the one that works best.
Part cutting order priority
- Consider the order in which parts are cut to minimize the risk of material deformation or interference between parts. Cutting smaller or internal features first helps maintain material stability.
Contour nesting
- Use contour nesting technology to nest parts with similar shapes closely together, further reducing waste and optimizing material use.
Dynamic nesting
- Some advanced nesting software can dynamically adjust the arrangement of parts in real time based on changes in design or available materials. This flexibility optimizes material use for custom or on-demand manufacturing.
Waste management
- Develop strategies for managing and reusing waste wherever possible. Smaller remnants from previous cuts may still have usable sections for smaller parts.
Summarize
Laser cutting offers unparalleled precision and flexibility, but realizing its full potential requires a deep understanding of design considerations and limitations. By choosing the right materials, optimizing designs, and respecting the capabilities of laser cutting technology, designers and engineers can unleash the power of this transformative manufacturing process while avoiding potential pitfalls. Working with an experienced laser-cutting machine manufacturer or professional can provide valuable insights tailored to specific project requirements, ensuring a successful laser-cutting job.
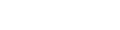
Contact information
- [email protected]
- [email protected]
- +86-19963414011
- No. 3 Zone A, Lunzhen Industrial Zone,Yucheng City , Shandong Province.
Get Laser Solutions