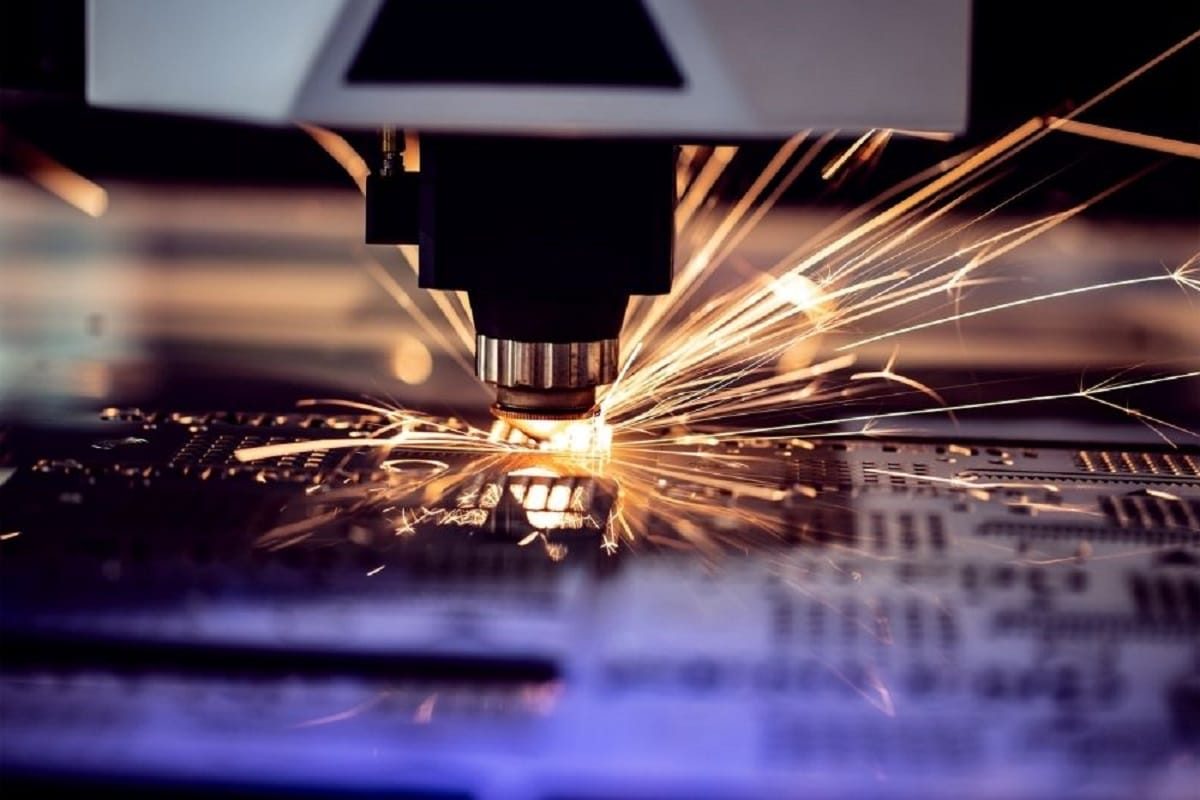
Designüberlegungen für das Laserschneiden
Laser schneiden hat sich zu einer vielseitigen und präzisen Technologie entwickelt, deren Anwendungen branchenübergreifend von der Fertigung bis hin zu Kunst und Design reichen. Gleichzeitig ist es aufgrund seiner Fähigkeit, komplizierte Muster, detaillierte Schnitte und saubere Kanten zu erstellen, die erste Wahl für viele Projekte. Allerdings unterliegt das Laserschneiden wie jeder Prozess seinen eigenen Designüberlegungen und Einschränkungen, die Designer und Ingenieure überwinden müssen, um die gewünschten Schneidergebnisse zu erzielen. In diesem Artikel untersuchen wir diese Designfaktoren im Detail.
Inhaltsverzeichnis
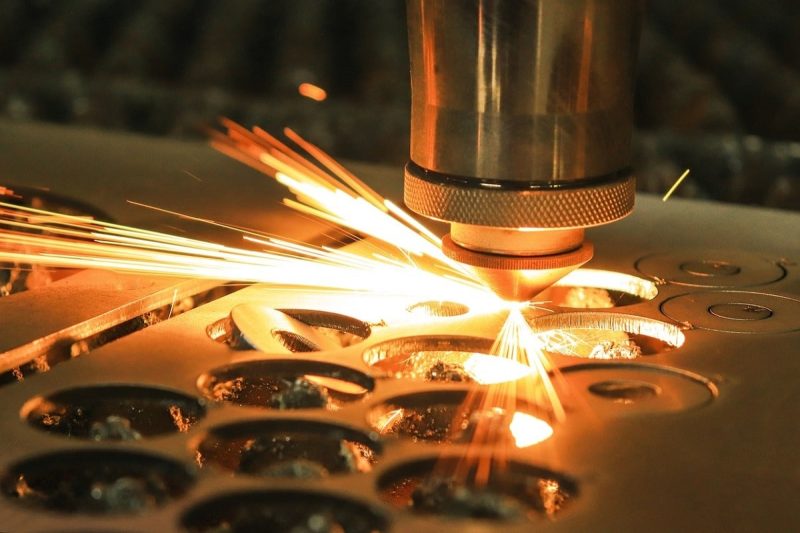
Überlegungen zur Innenarchitektur
Überlegungen zur Innenarchitektur mithilfe der Laserschneidtechnologie konzentrieren sich auf die spezifischen Merkmale, Formen und Eigenschaften des Designs selbst. Diese Überlegungen tragen dazu bei, dass Ihr Design für die Laserschneidtechnologie gut geeignet ist und können sich auf den Erfolg des Schneidprozesses und die Qualität des Endprodukts auswirken. Im Folgenden sind wichtige Überlegungen zur Innenarchitektur beim Laserschneiden aufgeführt:
Geschlossene Formen und Perforationen
- Das Laserschneiden ist am effizientesten, wenn mit geschlossenen Formen oder Konturen gearbeitet wird. Denn diese Formen halten das Material während des Schneidvorgangs stabil und erleichtern dem Laser die genaue Verfolgung.
- Wenn Perforationen (Löcher) in das Design einbezogen werden, müssen Sie sicherstellen, dass sie einen ausreichenden Abstand voneinander haben und groß genug sind, um eine Verformung des Materials oder Schwierigkeiten beim Schneiden zu vermeiden. Berücksichtigen Sie die Materialstärke und die Leistungsfähigkeit des Lasergenerators.
Merkmalsabmessungen und Toleranzen
Die Designmerkmale sollten mit der Funktionalität des Lasergenerators und der Dicke des verwendeten Materials übereinstimmen. Folgende Aspekte müssen im Fokus stehen:
- Merkmalsabmessungen: Achten Sie genau auf Merkmale in Ihrem Design, wie Löcher, Schlitze und Schnitte. Stellen Sie sicher, dass sie für die Materialstärke und die Laserfähigkeiten geeignet sind. Leistungsmerkmale sind möglicherweise nicht erreichbar oder erfordern möglicherweise spezielle Laserausrüstung.
- Toleranzen: Integrieren Sie entsprechende Toleranzen in Ihr Design, um die Breite des Laserstrahls (Schnittfuge) und mögliche Materialabweichungen zu berücksichtigen. Richtige Toleranzen tragen dazu bei, dass die Teile nach dem Schneiden genau zusammenpassen.
Scharfe Ecken und Innenradien
- Extrem scharfe Ecken im Design können beim Laserschneiden zu Herausforderungen führen. Da der Laserstrahl einen begrenzten Durchmesser hat, neigt er dazu, leichte Rundungen zu erzeugen.
- Um die Schnittgenauigkeit zu verbessern, sollten Sie in Erwägung ziehen, Ihrem Design kleine Verrundungen oder abgerundete Ecken hinzuzufügen. Stellen Sie sicher, dass der Innenradius auf den Durchmesser des Laserstrahls abgestimmt ist, um unbeabsichtigte Schnitte oder Materialabtrag zu vermeiden.
Materialverträglichkeit
- Stellen Sie sicher, dass die Materialien, die Sie für Ihr Projekt auswählen, mit dem Laserschneidverfahren kompatibel sind. Verschiedene Materialien haben unterschiedliche Absorptionseigenschaften und Schneidfähigkeiten.
- Verstehen Sie, wie sich die von Ihnen ausgewählten Materialien unter Laserschneidbedingungen verhalten, damit Sie Ihre Designs entsprechend optimieren können.
Designkomplexität
- Das Laserschneiden eignet sich hervorragend für komplizierte Designs und Sie können diese Funktion nutzen, indem Sie detaillierte und präzise Muster entwerfen.
- Allerdings kann es eine Herausforderung sein, beim Laserschneiden extrem feine Details zu erzielen, insbesondere solche, die kleiner als der Durchmesser des Laserstrahls (Schnittfuge) sind.
Schnittkompensation
- Berücksichtigen Sie die Breite des Laserstrahls (Schnittfuge), um Ihr Design anzupassen. Dazu muss die Linie möglicherweise leicht nach innen geschnitten werden, um die gewünschte Teilgröße zu erhalten.
Überlegungen zur Verschachtelung
- Wenn Sie planen, mehrere Teile oder Muster auf einer einzigen Materialplatte zu verschachteln, entwerfen Sie so, dass der Materialverbrauch optimiert wird und gleichzeitig sichergestellt wird, dass zwischen den Teilen ausreichend Abstand vorhanden ist, um Störungen beim Schneiden zu vermeiden.
Materialstärke
- Die Designmerkmale sollten mit der Dicke des verwendeten Materials übereinstimmen. Wenn Ihr Design unterschiedliche Materialstärken umfasst, stellen Sie sicher, dass Ihre Laserschneidmaschine entsprechend eingerichtet ist, um diese Variationen zu bewältigen.
Materialkornrichtung
- Berücksichtigen Sie die Faserrichtung des Materials, insbesondere von Materialien wie Holz oder bestimmten Metallen. Passen Sie Ihr Design an die Faserrichtung an, um bessere Ergebnisse zu erzielen.
Interne Merkmale und Hohlräume
- Laserschneidmaschinen können möglicherweise nicht auf interne Merkmale oder Hohlräume in Materialien zugreifen. Planen Sie daher Ihr Design entsprechend und ziehen Sie alternative Herstellungsmethoden in Betracht, wenn interne Schnitte erforderlich sind.
Durch die Berücksichtigung dieser internen Designüberlegungen können Sie Ihr Laserschneiddesign optimieren, die Effizienz und Genauigkeit des Schneidprozesses steigern und sicherstellen, dass das endgültig geschnittene Teil den Projektanforderungen entspricht. Die Zusammenarbeit mit einem erfahrenen Laserschneiddienstleister oder Ingenieur kann Ihnen wertvolle Hinweise zu Ihrem Design und Ihrer Materialauswahl geben.

Überlegungen zum externen Design
Überlegungen zum Außendesign beim Laserschneiden konzentrieren sich auf Faktoren außerhalb des Designs selbst, sind jedoch entscheidend für den Erfolg des Schneidprozesses und die Gesamtqualität des Ergebnisses. Diese Überlegungen umfassen Faktoren im Zusammenhang mit dem Gesamtprozess, der Materialhandhabung und dem Maschinenbetrieb. Im Folgenden sind wichtige Überlegungen zur Außengestaltung beim Laserschneiden aufgeführt:
Materielle Unterstützung
- Stützen Sie die Materialien ordnungsgemäß auf dem Schneidetisch ab, um Verformungen, Vibrationen oder Materialverformungen während des Schneidens zu vermeiden. Eine unzureichende Unterstützung kann zu ungenauen Schnitten führen und die Schnittqualität beeinträchtigen.
Materialhandhabung und Ausrichtung
- Laden Sie das Material ordnungsgemäß auf den Schneidtisch und richten Sie es richtig aus, um sicherzustellen, dass es während des Schneidvorgangs flach, stabil und sicher positioniert bleibt.
- Falsch ausgerichtete oder instabile Materialien können zu ungenauen Schnitten führen und die Schnittqualität beeinträchtigen.
Belüftung und Luftstrom
- Abhängig vom zu schneidenden Material können beim Laserschneiden Rauch und Gase entstehen. Stellen Sie sicher, dass Ihr Design eine ordnungsgemäße Belüftung und Planung ermöglicht, um diese Nebenprodukte im Schneidbereich zu beseitigen.
- Ein ausreichender Luftstrom hilft dabei, Schmutz aus dem Schnittbereich zu entfernen und sorgt für einen sauberen Schnittweg. Es wird empfohlen, den Hersteller Ihrer Laserschneidmaschine zu konsultieren, um die geeignete Gasdurchflussrate und -art für Ihre Materialien zu ermitteln.
Zu- und Ableitungskabel
- Integrieren Sie Ein- und Auslaufpfade in Ihr Design. Diese Pfade sind die Eintritts- und Austrittspunkte für den Laserstrahl und tragen dazu bei, dass der Schneidvorgang reibungslos beginnt und endet.
- Ein- und Auslauflinien können unnötige Markierungen oder Defekte am Anfang und Ende des Schnitts verhindern und so die Schnittqualität verbessern.
Vermeiden Sie Über- und Unterschnitte
- Ein Überschnitt tritt auf, wenn der Laserstrahl geringfügig über den vorgesehenen Schnittpfad hinausragt, was zu einem übermäßigen Materialabtrag führt.
- Eine Unterschneidung entsteht, wenn der Laserstrahl den vorgesehenen Schnittpfad nicht erreicht und möglicherweise ungeschnittenes Material zurückbleibt.
- Diese Probleme können durch eine Feinabstimmung des Designs, die Optimierung der Schnittparameter und die Gewährleistung einer guten Wartung der Laserschneidmaschine minimiert werden.
Externe Stützstruktur
- Wenn Ihr Design empfindliche oder dünne Teile enthält, die sich während des Schneidvorgangs leicht bewegen können, sollten Sie in Erwägung ziehen, externe Stützstrukturen oder Laschen hinzuzufügen, um die Teile an Ort und Stelle zu halten, bis der Schneidvorgang abgeschlossen ist.
- Diese Stützstrukturen können nach Abschluss des Schnitts entfernt werden.
Düsenpositionierung und Fokus
- Stellen Sie sicher, dass die Laserschneiddüse richtig positioniert und auf das zu schneidende Material ausgerichtet ist. Die richtige Düsenausrichtung und -fokussierung sind entscheidend für präzise Schnitte.
Maschinensicherheitsmaßnahmen
- Treffen Sie Sicherheitsmaßnahmen beim Umgang mit Materialien und beim Betrieb von Laserschneidgeräten. Befolgen Sie die Sicherheitsrichtlinien, verwenden Sie geeignete persönliche Schutzausrüstung (PSA) und sorgen Sie für ausreichende Belüftung, um den Bediener zu schützen und eine sichere Arbeitsumgebung aufrechtzuerhalten.
Maschinenwartung
- Warten und kalibrieren Sie Ihre Laserschneidmaschine regelmäßig, um eine optimale Leistung zu gewährleisten. Eine ordnungsgemäße Wartung kann dazu beitragen, Probleme wie eine Fehlausrichtung des Strahls oder Leistungsschwankungen zu vermeiden, die sich auf die Schnittqualität auswirken können.
Laserstrahlfokussierung und Leistungsanpassung
- Passen Sie je nach Material und Dicke die Fokus- und Leistungseinstellungen des Laserstrahls an, um den Schneidprozess zu optimieren. Es kann einige Experimente und Tests erfordern, um die idealen Einstellungen zu finden.
Düsenreinigung und Wartung
- Reinigen und warten Sie Ihre Laserschneiddüse regelmäßig, um eine optimale Leistung zu gewährleisten. Saubere Düsen sorgen für eine gleichbleibende Schnittqualität und -genauigkeit.
Abfallmanagement
- Entwickeln Sie einen Abfallmanagementplan, um mit Abfällen und Abfällen umzugehen, die während des Schneidprozesses entstehen. Die ordnungsgemäße Abfallentsorgung trägt dazu bei, einen sauberen und sicheren Arbeitsplatz zu gewährleisten.
Indem Sie diese externen Designüberlegungen berücksichtigen, können Sie zur erfolgreichen Durchführung des Laserschneidprozesses beitragen, potenzielle Probleme oder Mängel minimieren und sicherstellen, dass das endgültige Schnittteil die erforderlichen Qualitätsstandards erfüllt. Die Zusammenarbeit mit einem erfahrenen Laserschneiddienstleister oder -bediener kann auch wertvolle Hinweise zur Optimierung externer Faktoren für Ihr Laserschneidprojekt liefern.
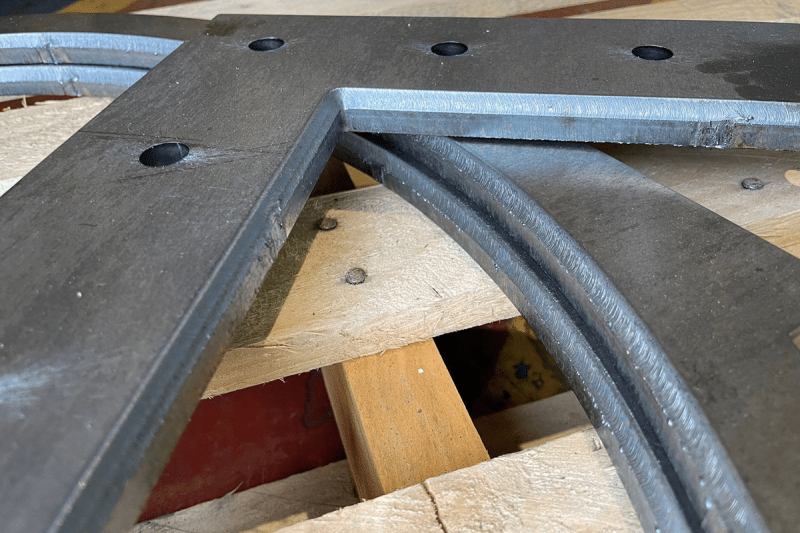
Verschachtelte Optimierung
Das Nesting-Optimierungsdesign beim Laserschneiden ordnet Teile oder Muster auf der Materialplatte auf die effizienteste Weise an, um Abfall zu minimieren und die Materialausnutzung zu maximieren. Eine korrekte Verschachtelung kann zu erheblichen Kosteneinsparungen, weniger Materialverschwendung und einer höheren Produktionseffizienz führen. Um die besten Ergebnisse bei der verschachtelten Optimierung für das Laserschneiden zu erzielen, sollten Sie die folgenden wichtigen Überlegungen berücksichtigen:
Teilegeometrie und Ausrichtung
- Analysieren Sie die Teilegeometrie und wählen Sie die geeignete Verschachtelung aus, um die Raumnutzung zu maximieren und Materialverschwendung zu minimieren.
- Optimieren Sie die Teileausrichtung, um die Materialbewegung während des Schneidens zu reduzieren und die Verfahrzeit des Laserkopfs zu minimieren.
Optimale Auswahl der Panelgröße
- Wählen Sie eine Materialblattgröße, die den Abmessungen des Teils oder Musters möglichst genau entspricht. Die Verwendung von Brettern geeigneter Größe minimiert den Abfall und maximiert die Materialausnutzung. Vermeiden Sie die Verwendung von Brettern, die viel größer als nötig sind.
Nesting-Software
- Nutzen Sie die Funktionen spezieller Verschachtelungssoftware oder Designsoftware, um den Verschachtelungsprozess zu automatisieren. Diese Tools analysieren Ihr Design, die Abmessungen der Materialplatten und die Schnittparameter, um die Verschachtelung automatisch zu optimieren.
Materialeffizienz
- Priorisieren Sie eine effiziente Materialausnutzung, indem Sie Teile eng aneinander platzieren, ohne sich zu überlappen. Die Vermeidung übermäßiger Abstände zwischen den Teilen trägt dazu bei, Abfall zu reduzieren und die Produktionskosten zu senken.
Vermeiden Sie überlappende Schnitte
- Stellen Sie sicher, dass sich die Schnittpfade für verschiedene Teile nicht überschneiden. Überlappende Schnitte können zu unregelmäßigen Kanten und Materialabfall führen. Mithilfe von Nesting-Software können Teile automatisch so angeordnet werden, dass Überlappungen vermieden werden.
Konsistenz der Materialstärke
- Stellen Sie sicher, dass die Dicke des Materials im gesamten Blech gleichmäßig ist, um eine gleichmäßige Schnittqualität zu gewährleisten und Abweichungen zu vermeiden, die sich auf die Verschachtelung auswirken könnten. Darüber hinaus können Schwankungen in der Materialstärke zu inkonsistenten Schnittergebnissen führen.
Optimieren Sie die Panelauslastung
- Mithilfe einer Verschachtelungssoftware können Sie unter Berücksichtigung unregelmäßiger Formen und Materialeigenschaften die effizienteste Methode zum Anordnen von Teilen auf einer Materialplatte berechnen. Einige Softwareprogramme können sogar Teile drehen, um Abfall zu minimieren.
- In manchen Fällen kann die manuelle Anordnung von Teilen gemäß Ihren spezifischen Anforderungen zu besseren Ergebnissen führen, als sich ausschließlich auf automatisierte Verschachtelungssoftware zu verlassen. Experimentieren Sie mit verschiedenen Anordnungen, um diejenige zu finden, die am besten funktioniert.
Priorität der Teileschneidereihenfolge
- Berücksichtigen Sie die Reihenfolge, in der die Teile geschnitten werden, um das Risiko einer Materialverformung oder einer Interferenz zwischen den Teilen zu minimieren. Das vorherige Schneiden kleinerer oder interner Merkmale trägt zur Aufrechterhaltung der Materialstabilität bei.
Konturverschachtelung
- Nutzen Sie die Konturschachtelungstechnologie, um Teile mit ähnlichen Formen eng aneinander zu schachteln, was den Abfall weiter reduziert und den Materialverbrauch optimiert.
Dynamische Verschachtelung
- Einige fortschrittliche Verschachtelungssoftware kann die Anordnung von Teilen in Echtzeit basierend auf Änderungen im Design oder verfügbaren Materialien dynamisch anpassen. Diese Flexibilität optimiert den Materialeinsatz für kundenspezifische oder On-Demand-Fertigungen.
Abfallmanagement
- Entwickeln Sie Strategien zur Bewirtschaftung und Wiederverwendung von Abfällen, wo immer dies möglich ist. Kleinere Reste früherer Schnitte können noch nutzbare Abschnitte für kleinere Teile aufweisen.
Zusammenfassen
Laserschneiden bietet beispiellose Präzision und Flexibilität, doch um sein volles Potenzial auszuschöpfen, ist ein tiefes Verständnis der Designüberlegungen und -beschränkungen erforderlich. Durch die Auswahl der richtigen Materialien, die Optimierung des Designs und die Berücksichtigung der Möglichkeiten der Laserschneidtechnologie können Designer und Ingenieure die Leistung dieses transformativen Herstellungsprozesses freisetzen und gleichzeitig potenzielle Fallstricke vermeiden. Die Zusammenarbeit mit einem erfahrenen Hersteller oder Fachmann für Laserschneidmaschinen kann wertvolle, auf die spezifischen Projektanforderungen zugeschnittene Erkenntnisse liefern und so einen erfolgreichen Laserschneidauftrag gewährleisten.
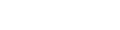
Kontaktinformationen
- [email protected]
- [email protected]
- +86-19963414011
- Nr. 3 Zone A, Industriegebiet Lunzhen, Stadt Yucheng, Provinz Shandong.
Holen Sie sich Laserlösungen