
レーザー溶接機は正確で精密な溶接能力を提供しますか?
現代の製造業では、精度と正確さが極めて重要です。産業界がより効率的で信頼性の高い材料接合方法を模索する中、レーザー溶接が有望なソリューションとして浮上しています。 レーザー溶接機 レーザー溶接は、高濃度のエネルギービームを利用して、金属やその他の材料を比類のない精度で溶接します。しかし、この技術は本当に精密溶接機能の約束を果たすことができるのでしょうか? この記事では、レーザー溶接技術に関連する利点と課題を詳しく検討し、さまざまな産業用途で精密溶接を実現する可能性を検討します。レーザー溶接の能力と限界を包括的に理解することで、レーザー溶接の誇張された精度と精密さの背後にある真実を明らかにします。

レーザー溶接技術について学ぶ
この問題を解決するには、まずレーザー溶接の基本原理を理解する必要があります。電流や炎を利用して熱を発生させる従来の溶接方法とは異なり、レーザー溶接では集中したコヒーレント光線を利用して材料を溶かして融合させます。基本原理は次のとおりです。
- レーザービーム生成:レーザー溶接は、高エネルギーレーザービームを生成することから始まります。このプロセスでは通常、固体レーザー発生器、ファイバーレーザー発生器、CO2 レーザー発生器などのレーザー源が使用されます。これらのレーザー発生器は、誘導放出プロセスを通じて光を放射し、正確な特性を持つコヒーレントで集中した光線を生成します。
- 集束光学系:レーザービームは、生成されると、ミラーやレンズなどの一連の集束光学系を通過します。これらの光学系はレーザービームを整形して集中させ、その強度と焦点を正確に制御できるようにします。集束光学系の位置と方向を調整することで、オペレーターは溶接アプリケーションの特定の要件に合わせてレーザービームを調整できます。
- 材料の相互作用:焦点を絞ったレーザービームが溶接する材料と相互作用すると、いくつかの重要なプロセスが発生します。レーザーエネルギーは材料の表面によって吸収され、急速に加熱されて融点に達します。この局所的な加熱により、溶接接合部に溶融池が形成され、材料が融合して強力な結合が形成されます。
- 制御システム:制御システムはレーザー溶接プロセスの動作を制御し、正確で一貫した結果を保証します。このシステムは、レーザー出力、ビーム径、パルス持続時間、移動速度などのさまざまなパラメータを監視および調整し、特定のアプリケーションごとに溶接プロセスを最適化します。高度な制御システムには、センサーやカメラなどのフィードバック メカニズムが組み込まれ、溶接パラメータのリアルタイム監視と調整を行うこともできます。
レーザー溶接技術の基本原理と手順を習得することで、メーカーはレーザー溶接技術の能力を活用して、幅広い材料や用途で高精度で高品質の溶接を実現できます。自動車や航空宇宙の部品から医療機器や電子機器まで、レーザー溶接は現代の製造プロセスにおける革新と卓越性を推進し続けています。

レーザー溶接の精度と正確さ
精度と正確さは、現代の製造プロセスにとって重要なベンチマークであり、最終製品の品質と信頼性を決定します。レーザー溶接技術は、高度に集中した光線を利用して、材料を接合する際に比類のない精度を提供します。レーザー溶接技術が優れた精度と正確さを実現する仕組みを探ってみましょう。
制御されたエネルギー供給
レーザー溶接は、制御されたエネルギー供給によって精度と正確性を実現します。幅広い熱源に依存する従来の溶接方法とは異なり、レーザー ビームは正確に焦点を合わせて溶接ジョイントに向けることができます。この集中したエネルギーによって熱の分散が最小限に抑えられ、溶接プロセスを正確に制御できるため、歪みが最小限で正確な溶接が実現します。
最小限の熱影響部(HAZ)
レーザー溶接は、溶接領域を囲む熱影響部 (HAZ) のサイズを最小限に抑えます。レーザー溶接は、熱を非常に局所的に伝達することで、熱変形のリスクを軽減し、母材の機械的特性を維持します。熱の適用におけるこの精度により、溶接された部品の構造的完全性と寸法精度が維持されます。
パラメータの微調整
レーザー溶接システムでは、レーザー出力、ビーム径、パルス持続時間、移動速度など、さまざまな溶接パラメータを細かく制御できます。オペレーターは、各溶接アプリケーションの特定の要件に合わせてこれらのパラメータを調整できるため、正確で一貫した結果が保証されます。このレベルの制御により、溶接プロセスで厳しい許容範囲と高い再現性が実現され、変動が最小限の正確な溶接が可能になります。
高解像度と高精度な位置決め
レーザー溶接機には、高度な動作制御システムと高解像度の位置決め装置が組み込まれていることがよくあります。これらのシステムにより、ワークピースに対するレーザー ビームの正確な移動と位置決めが可能になり、溶接が最高の精度で施されることが保証されます。複雑な形状や複雑なコンポーネントを溶接する場合でも、レーザー溶接技術により、ミクロン レベルの精度で正確な溶接配置を実現できます。
リアルタイムの監視とフィードバック
最新のレーザー溶接システムの多くは、リアルタイムの監視およびフィードバック メカニズムを備えています。センサー、カメラ、自動検査システムが溶接プロセスを継続的に監視し、制御システムに即時のフィードバックを提供します。このリアルタイム フィードバックにより、溶接パラメータをオンザフライで調整できるため、プロセス全体を通じて溶接品質が一貫して正確になります。
結論として、制御されたエネルギー供給、細かいパラメータ制御、高解像度の位置決め、リアルタイムの監視により、レーザー溶接システムは歪みやばらつきを最小限に抑えた精密な溶接を実現できます。業界ではより高いレベルの精度と信頼性が求められており、レーザー溶接は現代の製造業の礎となり、材料接合プロセスにおける革新と卓越性を推進しています。

精密用途におけるレーザー溶接の利点
レーザー溶接技術 レーザー溶接は現代の製造業において精度と卓越性の代名詞となり、精密用途に無数の利点をもたらしています。精密用途におけるレーザー溶接の主な利点を見てみましょう。
レーザー溶接技術は現代の製造業において精度と卓越性の代名詞となり、精密用途に無数の利点をもたらしています。精密用途におけるレーザー溶接の主な利点を見てみましょう。
高い溶接品質
レーザー溶接技術は、欠陥が最小限で、強力で均一な溶接を特徴とする優れた溶接品質を提供します。エネルギー供給と溶接パラメータを正確に制御することで、一貫した融合と冶金学的完全性が保証され、優れた機械的特性を持つ高品質の接合部が得られます。このレベルの溶接品質は、信頼性と性能が重要となる精密用途にとって非常に重要です。
多彩な溶接機能
レーザー溶接は、さまざまな材料や部品形状を接合できる汎用性を備えています。異種金属、薄板、複雑な部品の溶接を問わず、レーザー溶接技術はさまざまな用途の要件を満たすのに優れています。この汎用性により、レーザー溶接は自動車、航空宇宙、電子機器、医療機器製造など、さまざまな業界の精密用途に最適です。
溶接幅が狭い
レーザー溶接の主な利点の 1 つは、高アスペクト比の狭い溶接部を生成できることです。レーザー ビームを集中させることで、熱影響部を正確に制御できるため、最小限の幅と優れた溶け込みの溶接部が得られます。この狭い溶接幅は、スペースの制約や美観上の配慮により厳しい許容誤差と細かいディテールが求められる精密用途に特に有利です。
溶接後の処理が最小限
レーザー溶接は、歪みを最小限に抑え、スパッタのないきれいな溶接を実現し、溶接後の大がかりな処理の必要性を最小限に抑えます。正確な熱入力と制御されたエネルギー供給により、材料の変形や変色のリスクが軽減され、時間のかかる研削、研磨、表面仕上げ作業が不要になります。これにより、精密製造プロセスで大幅な時間とコストの節約が可能になります。
熱影響部(HAZ)の削減
レーザー溶接技術は、溶接部周辺の熱影響部 (HAZ) のサイズを最小限に抑え、母材の機械的特性を維持します。集中した熱入力と急速な冷却速度により、熱変形と金属組織の変化が最小限に抑えられ、溶接部品の完全性が維持されます。寸法精度と材料性能が重要となる精密用途では、熱影響部を縮小することが非常に重要です。
要約すると、レーザー溶接技術は精密用途に数多くの利点をもたらします。高い溶接品質と多様な溶接機能から、狭い溶接幅と最小限の溶接後処理要件まで、レーザー溶接は精密製造のあらゆる面で優れています。

溶接の品質と精度に影響を与える要因
レーザー溶接技術は、材料を接合するための高度に制御された多用途の方法を提供しますが、溶接プロセスの品質と精度に影響を与える要因がいくつかあります。レーザー溶接アプリケーションにおける溶接の品質と精度に影響を与える主な要因を見てみましょう。
レーザービームの品質と焦点
レーザー ビームの品質と焦点は、溶接の品質と精度を決定する上で重要な役割を果たします。ビームの形状、強度分布、発散角などの要素は、レーザー ビームのエネルギー分布と浸透深度に影響します。高品質のビーム プロファイルと正確な焦点を維持することで、一貫した熱伝達と溶接形状が確保され、欠陥が最小限に抑えられ、正確な溶接が保証されます。
溶接パラメータと制御
レーザー出力、パルス持続時間、ビーム径、移動速度などの溶接パラメータは、溶接プロセスの品質と精度に直接影響します。これらのパラメータを正確に制御することで、最適な溶け込み、融合、溶接形態が実現します。高度な制御システムは、溶接パラメータをリアルタイムで監視および調整し、プロセス全体の正確な制御と一貫した溶接品質を保証します。
保護ガス
シールドガスは、レーザー溶接中に溶接プールと周囲の領域を大気汚染から保護するために使用されます。シールドガスの組成と流量の選択は、溶接ビードの形状、多孔性、スパッタ形成に影響し、溶接品質に影響します。シールドガスパラメータを適切に選択して制御することで、最適な冶金特性を持つ高品質で欠陥のない溶接が可能になります。
素材の種類と厚さ
溶接される材料の種類と厚さは、溶接の品質と精度に大きく影響します。材料によって熱特性、吸収係数、融点が異なり、レーザーと材料の相互作用や溶接形成プロセスに影響します。さらに、材料の厚さが変化すると、熱放散、浸透、接合強度に影響する可能性があるため、最適な結果を得るには溶接パラメータの調整が必要になります。
環境要因
周囲温度、湿度、空気清浄度などの環境要因は、溶接の品質と精度に影響を与える可能性があります。温度変動と湿度レベルは、レーザー性能、ビーム安定性、材料特性に影響を与え、溶接品質の変化をもたらします。溶接エリア内の環境条件を管理することで、プロセスの不安定性のリスクを最小限に抑え、一貫した溶接品質を確保できます。
システムの安定性
レーザー溶接システムの安定性と信頼性により、一貫した溶接品質と精度が確保されます。機械的な振動、光学的なずれ、電力の変動はすべて、ビームの伝達と溶接性能に悪影響を及ぼす可能性があります。溶接システムの定期的なメンテナンス、校正、監視により、安定性と信頼性が確保され、溶接品質の変動が最小限に抑えられます。
したがって、これらの要素を制御および最適化することで、製造業者は現代の製造プロセスの厳しい要件を満たす高品質で高精度の溶接を実現できます。

レーザー溶接機のメンテナンスと校正
製造工程中の一貫した溶接品質と信頼性は、主にレーザー溶接機の最適な性能と精度を維持することによって達成されます。定期的なメンテナンスとキャリブレーションは、レーザー溶接システムの効率と機能を維持する上で重要な要素です。レーザー溶接機に影響を与える主要なメンテナンスとキャリブレーションの実践について見てみましょう。
定期的な清掃と点検
レーザー溶接機の定期的な清掃と検査は、汚染の防止、機能の維持、機器の寿命の延長に重要な役割を果たします。オペレーターは、ビームの品質と性能に影響を与える可能性のあるほこり、破片、残留物を取り除くために、定期的に光学系、レンズ、ミラーを清掃する必要があります。さらに、徹底した検査は、溶接品質やシステムの信頼性に影響を与える前に潜在的な問題を特定して解決するのに役立ちます。
キャリブレーションとアライメント
キャリブレーションとアライメントの手順により、レーザー溶接システムが最適なパフォーマンスと精度で動作することが保証されます。レーザー ビームのアライメント、焦点調整、溶接パラメータのキャリブレーションは、一貫した溶接品質と形状を実現するための重要な前提条件です。定期的なキャリブレーション チェックと調整により、システムの整合性と精度が維持され、溶接品質のエラーや偏差のリスクが軽減されます。
システムのアップグレードとアップデート
システムのアップグレードとソフトウェアの更新により、レーザー溶接機は最新の技術の進歩と改善を維持することができます。メーカーは、システムのパフォーマンス、信頼性、および機能性を向上させるために、ファームウェアの更新、ソフトウェア パッチ、およびハードウェアのアップグレードを頻繁にリリースしています。定期的なシステムのアップグレードと更新を実施することで、レーザー溶接機の競争力と効率性を維持し、変化する業界のニーズに対応できるようになります。
トレーニングと教育
オペレーターとメンテナンス担当者の適切なトレーニングと教育は、レーザー溶接機の性能と耐用年数を最適化するために不可欠です。包括的なトレーニング プログラムには、機器の操作、メンテナンス手順、安全プロトコル、トラブルシューティング手法が含まれます。十分なトレーニングを受けた担当者は、日常的なメンテナンス作業の実行、潜在的な問題の特定、課題への効果的な対応をより適切に実行できるため、ダウンタイムを最小限に抑え、生産性を最大化できます。
予防保守計画
潜在的な問題に積極的に対処し、レーザー溶接機の予期しないダウンタイムを最小限に抑える予防保守プログラムを導入することが重要です。潤滑、部品の交換、システム検査などの定期的な保守作業は、機器の故障を防ぎ、耐用年数を延ばし、一貫したパフォーマンスを確保するのに役立ちます。定期的な保守スケジュールを順守することで、コストのかかる修理や生産の遅延の可能性を減らすことができます。
要約すると、メンテナンスとキャリブレーションは、レーザー溶接機の効率、精度、信頼性を維持する上で重要な要素です。予防的なメンテナンス手順を実施し、オペレーターのトレーニングに投資することで、メーカーはレーザー溶接機が最高のパフォーマンスで動作し、製造プロセス全体を通じて一貫して効率的に高品質の溶接を実現できることを保証できます。
要約する
急速に発展する製造業では、製品の品質と効率を確保するために、精度と正確さが基本要件となります。レーザー溶接機は、さまざまな材料や用途で精密な溶接を提供できることから、長い間高く評価されてきました。業界がイノベーションの限界を押し広げ、より高いレベルの精度を要求し続ける中、レーザー溶接技術はこれらの課題に対応するために進化しています。効率、柔軟性、新興技術の統合が進み、レーザー溶接が精密製造の礎としてさらに確固たる地位を築くことが期待されます。
これらの要素を深く理解することで、レーザー溶接機市場をより深く理解し、情報に基づいた購入決定を下すことができます。メーカーでもエンドユーザーでも、ぜひ当社をご検討ください。 AccTek レーザー 特定のニーズと予算に合ったレーザー溶接機を購入する際にご利用ください。
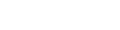
連絡先
- 電子メール:[email protected]
- Skype:[email protected]
- 微信: +86-19963414011
校正資料送付先
- No. 3 ゾーン A、Lunzhen 工業地帯、玉城市、山東省。
関連ブログ
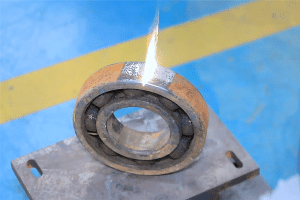
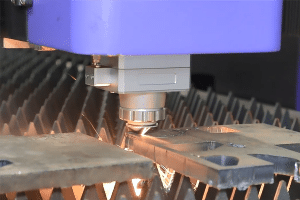
レーザー切断は製造の効率と生産性をどのように向上させるのでしょうか?
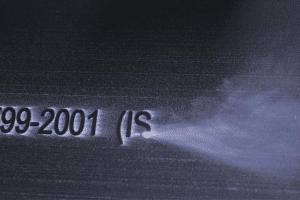
レーザーマーキングを行う際にはどのような安全上の注意が必要ですか?
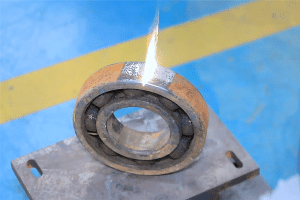
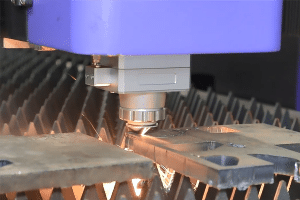
レーザー切断は製造の効率と生産性をどのように向上させるのでしょうか?
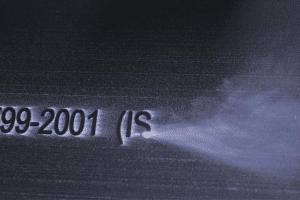
レーザーマーキングを行う際にはどのような安全上の注意が必要ですか?