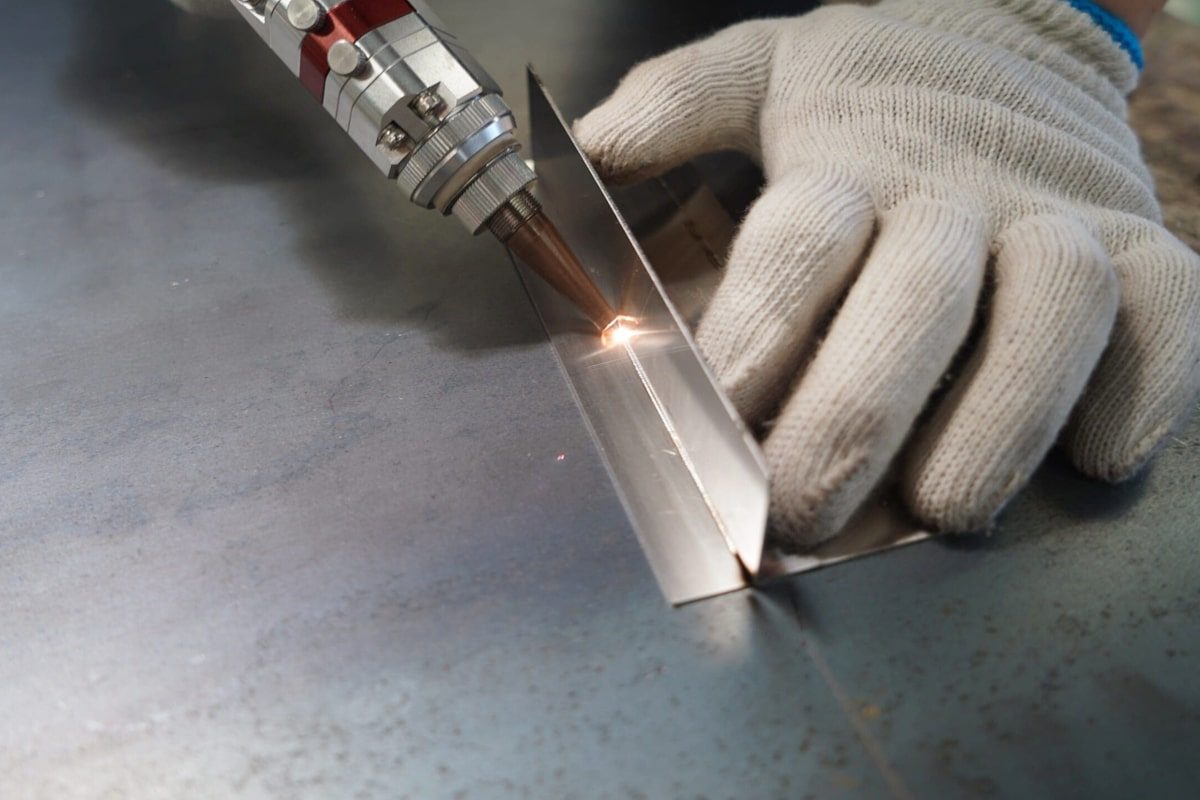
Quali fattori influenzano la saldabilità della saldatura laser?
La saldatura laser ha rivoluzionato la produzione moderna, offrendo elevata precisione, minima distorsione termica e la capacità di unire materiali altrimenti difficili da saldare con metodi tradizionali. Settori come aerospaziale, automobilistico, dispositivi medici ed elettronica fanno molto affidamento sulla saldatura laser per la sua velocità e capacità di fornire giunzioni di alta qualità e resistenti con un trattamento post-saldatura minimo. Nonostante i numerosi vantaggi della saldatura laser, ottenere una saldabilità ottimale non è sempre semplice. Il successo di una saldatura laser è determinato da una serie di fattori (proprietà dei materiali, parametri laser, configurazione delle apparecchiature, condizioni ambientali e trattamenti post-saldatura), tutti attentamente controllati per garantire la produzione di una saldatura resistente, durevole e priva di difetti.
In questo articolo esploreremo in modo approfondito i vari fattori che influenzano la saldabilità dei materiali nella saldatura laser. Questi fattori includono la composizione del materiale di base, la geometria del giunto, la potenza laser, la velocità e la qualità del raggio, nonché fattori ambientali esterni come temperatura e contaminanti. Esamineremo anche le sfide comuni incontrate nella saldatura laser e come possono essere mitigate per ottenere la massima qualità di saldatura possibile. Entro la fine di questo articolo, i lettori avranno una comprensione completa delle molteplici variabili coinvolte nella saldatura laser e come ottimizzare questi fattori per risultati di saldatura superiori.
Sommario
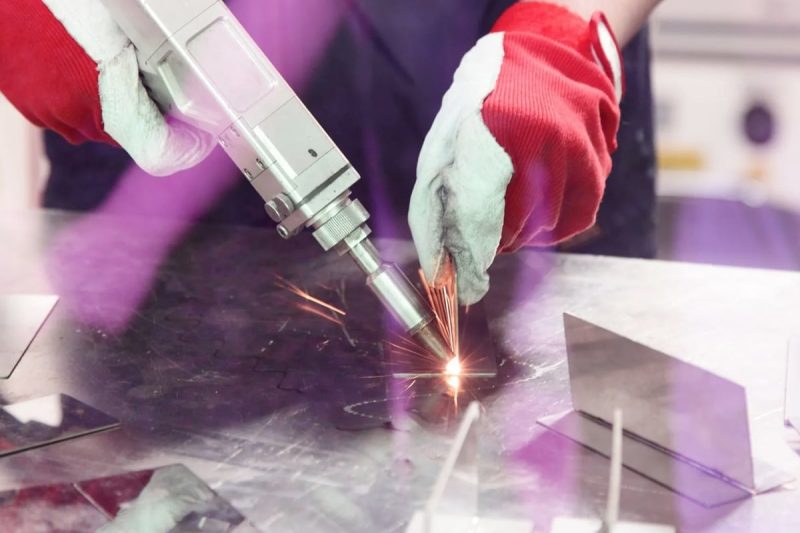
Introduzione alla saldatura laser
Definizione e panoramica
La saldatura laser è una tecnica di saldatura di precisione che utilizza un raggio laser altamente concentrato per fondere e fondere materiali, in genere metalli o termoplastici. Il raggio laser, generato da una sorgente laser, dirige l'energia focalizzata sul materiale, creando una zona di calore localizzata che fonde il materiale di base all'interfaccia del giunto. Quando il materiale fuso si solidifica, forma una saldatura. Questo processo può essere eseguito utilizzando laser a onda continua (CW), che forniscono calore costante, o laser pulsati, che forniscono energia in brevi raffiche, spesso per prevenire il surriscaldamento e per fornire una penetrazione controllata.
La saldatura laser è altamente versatile e può essere utilizzata per una vasta gamma di tipi di materiali e spessori. Offre numerosi vantaggi, tra cui elevate velocità di saldatura, zone termiche alterate (HAZ) strette, minima distorsione del materiale e la capacità di automatizzare il processo, il che porta a una maggiore efficienza produttiva. La precisione del raggio laser consente la saldatura in spazi ristretti e su componenti delicati, rendendo la saldatura laser ideale per applicazioni ad alta precisione, tra cui i settori aerospaziale ed elettronico.
Importanza della saldabilità nella saldatura laser
La saldabilità nella saldatura laser si riferisce alla capacità di un materiale di formare un giunto resistente e privo di difetti quando sottoposto al processo di saldatura laser. Il raggiungimento della saldabilità dipende da diversi fattori correlati, come la composizione chimica del materiale, le proprietà termiche, la progettazione del giunto e il modo in cui risponde all'apporto di calore localizzato dal raggio laser. Se questi fattori non sono ottimizzati, il giunto saldato potrebbe essere soggetto a difetti come porosità, crepe, distorsioni o debole legame.
Il concetto di saldabilità è particolarmente cruciale nella saldatura laser perché l'elevata concentrazione di energia del raggio laser può avere un impatto significativo sulla microstruttura e sulle proprietà meccaniche del materiale. Ad esempio, rapidi cicli di riscaldamento e raffreddamento possono portare a problemi come stress residuo, cricche o trasformazioni di fase indesiderate in determinati materiali. Per superare queste sfide, i produttori devono selezionare e controllare attentamente i vari parametri coinvolti nella saldatura laser.
Confronto con i metodi di saldatura tradizionali
Sebbene la saldatura laser sia nota per la sua precisione ed efficienza, differisce in modo significativo dai metodi di saldatura tradizionali come la saldatura MIG (Metal Inert Gas) o la saldatura TIG (Tungsten Inert Gas) in diversi modi importanti. I metodi di saldatura tradizionali utilizzano archi elettrici per generare calore, che riscalda un'area più ampia del materiale e generalmente si traduce in zone termicamente alterate più ampie. Questi metodi tendono anche a comportare velocità di saldatura più lente e una maggiore distorsione del materiale. D'altro canto, la saldatura laser è caratterizzata da un fascio di energia altamente concentrato, che consente velocità di saldatura più elevate, zone termicamente alterate più strette e una distorsione minima.
Tuttavia, la saldatura laser è più sensibile alle modifiche nelle proprietà dei materiali, nella progettazione dei giunti e nelle impostazioni laser rispetto ai metodi tradizionali. Ad esempio, i metodi tradizionali possono essere più indulgenti quando si saldano materiali più spessi o giunti con geometrie irregolari, mentre la saldatura laser richiede un controllo più preciso di parametri quali potenza laser, messa a fuoco del raggio e velocità di saldatura. Pertanto, la saldatura laser potrebbe non essere la soluzione ideale per tutte le applicazioni, in particolare quando si ha a che fare con materiali o geometrie che sono difficili per il processo.
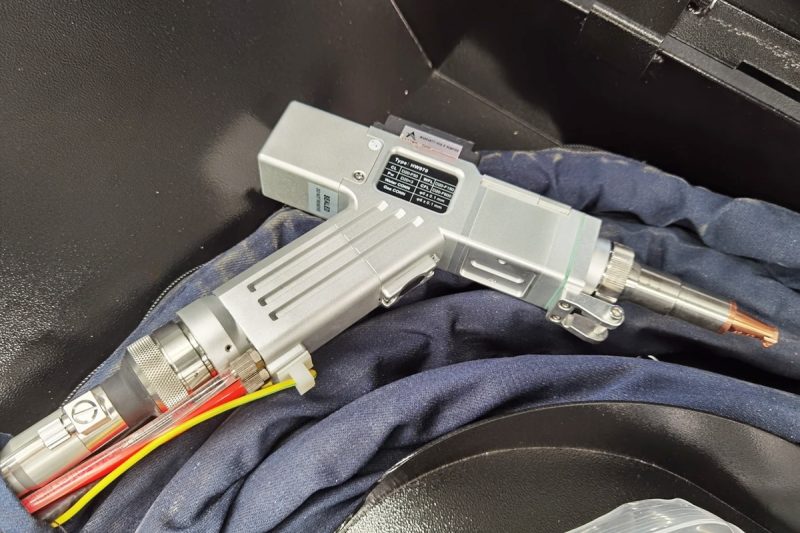
Proprietà dei materiali
Il materiale da saldare gioca un ruolo significativo nel successo di un'operazione di saldatura laser. Le principali proprietà del materiale che influenzano la saldabilità includono la composizione del materiale di base, lo spessore e la geometria, il punto di fusione, la conduttività termica e la presenza di elementi di lega o additivi.
Composizione del materiale di base
La composizione chimica del materiale di base è uno dei fattori più importanti che influenzano la saldabilità. Materiali diversi hanno punti di fusione, conduttività termica e comportamenti di solidificazione diversi, tutti fattori che influenzano il processo di saldatura laser. Ad esempio, gli acciai ad alto tenore di carbonio tendono a formare fasi dure e fragili durante il raffreddamento, aumentando la probabilità di cricche nella saldatura. Analogamente, i materiali con alti livelli di determinati elementi di lega come cromo, nichel o molibdeno possono essere più suscettibili alle trasformazioni di fase, che potrebbero portare a difetti di saldatura o proprietà meccaniche ridotte.
Alcuni materiali, come alluminio E rame, sono particolarmente difficili da saldare con la saldatura laser a causa della loro elevata conduttività termica e dei bassi punti di fusione. Questi materiali richiedono una maggiore potenza laser per ottenere una penetrazione adeguata, ma anche il rischio di bruciatura è molto più elevato. I materiali con un elevato coefficiente di espansione, come le leghe di titanio, possono subire distorsioni termiche durante la saldatura, richiedendo un controllo preciso dei parametri laser.
Comprendere la composizione del materiale da saldare è essenziale per determinare i parametri laser ottimali. Gli elementi di lega e le impurità nel materiale possono influenzare il modo in cui il materiale risponde al calore e alla formazione della saldatura, rendendo necessario regolare parametri come potenza laser, messa a fuoco del fascio e gas di protezione.
Spessore e geometria
Lo spessore del materiale e la geometria del giunto influenzano direttamente l'energia richiesta per la saldatura e la distribuzione del calore all'interno del materiale. Per materiali sottili, una potenza laser inferiore è generalmente sufficiente, ma è necessario un controllo attento per evitare un apporto di calore eccessivo che potrebbe causare bruciature. Per materiali più spessi, sono necessarie una potenza laser maggiore e velocità di saldatura più lente per garantire una penetrazione completa e una saldatura solida.
Anche la geometria del giunto influenza il modo in cui il laser interagisce con il materiale. I semplici giunti a testa sono relativamente facili da saldare perché forniscono una connessione diretta tra le due superfici. Tuttavia, giunti più complessi, come giunti a T, giunti a filetto o giunti a sovrapposizione, potrebbero richiedere un'attenzione speciale. L'angolazione e l'allineamento del giunto influenzeranno la capacità del laser di penetrare e fondere correttamente i materiali.
I materiali con geometrie complesse possono anche introdurre ulteriori sfide per la saldatura laser a causa delle difficoltà nell'allineamento del raggio con il giunto e delle variazioni di spessore lungo il giunto. Ottimizzare la progettazione del giunto e garantire il corretto allineamento del raggio laser sono passaggi critici per ottenere saldature resistenti e di alta qualità.
Punto di fusione e conduttività termica
Il punto di fusione di un materiale determina quanta energia è necessaria per fonderlo. Materiali con punti di fusione elevati, come tungsteno, titanio o acciai altolegati, richiedono molta più energia per raggiungere il loro punto di fusione e richiedono un'attenta gestione della potenza del laser. D'altro canto, materiali con punti di fusione bassi, come alluminio o zinco, possono fondersi troppo facilmente sotto un raggio laser e potrebbero richiedere velocità di saldatura elevate o tecniche laser pulsate per evitare un'eccessiva fusione.
La conduttività termica, ovvero la capacità di un materiale di condurre calore, ha un impatto anche sulla saldabilità. I materiali con elevata conduttività termica, come il rame, dissipano rapidamente il calore, il che significa che il raggio laser deve fornire energia sufficiente per superare questa perdita di calore e ottenere una penetrazione adeguata. Al contrario, i materiali a bassa conduttività termica, come acciaio inossidabile, trattengono il calore in modo più efficace, il che può portare a una zona termicamente alterata (HAZ) più ampia e a potenziali distorsioni termiche se non gestito correttamente.
Elementi di lega e additivi
La presenza di elementi di lega e additivi può avere un profondo impatto sulla saldabilità di un materiale. Elementi di lega comuni come manganese, silicio e cromo possono migliorare le proprietà meccaniche di un materiale, ma possono anche introdurre delle sfide durante la saldatura. Ad esempio, il manganese può rendere la saldatura più suscettibile alle cricche, mentre un eccesso di silicio può portare alla formazione di fasi fragili nella zona di saldatura.
Additivi come il flusso possono essere utilizzati per migliorare la saldatura superficiale, prevenire l'ossidazione o modificare il comportamento del bagno di saldatura. La selezione del flusso e di altri additivi deve essere effettuata con attenzione, poiché possono influenzare la qualità finale e le proprietà meccaniche della saldatura.
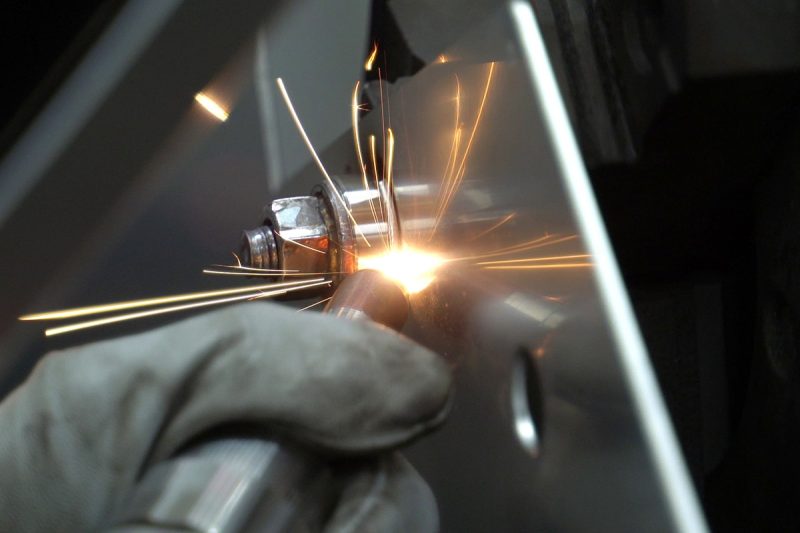
Parametri laser
I parametri laser, tra cui potenza laser, messa a fuoco, velocità, qualità del raggio e altri, sono fondamentali per la saldabilità dei materiali. Questi parametri controllano il modo in cui il raggio laser interagisce con il materiale, l'energia erogata al bagno di saldatura e la velocità di solidificazione.
Potenza laser
La potenza laser influenza direttamente la profondità di penetrazione, la velocità di saldatura e la quantità di calore generato durante il processo. Una potenza laser più elevata porta a una penetrazione più profonda, ma aumenta anche il rischio di bruciature o zone eccessivamente colpite dal calore. Impostazioni di potenza inferiori potrebbero non fornire energia sufficiente per ottenere una penetrazione completa in materiali più spessi, con conseguenti giunzioni deboli o fusione incompleta.
L'impostazione ottimale della potenza laser dipende dal materiale da saldare, dal suo spessore e dalle caratteristiche di saldatura desiderate. In generale, è necessario trovare un equilibrio tra potenza sufficiente a fondere il materiale ed evitare calore in eccesso che potrebbe deformare il pezzo in lavorazione.
Messa a fuoco laser
La messa a fuoco laser controlla la dimensione e l'intensità del raggio laser. Un raggio ben focalizzato produce un piccolo punto ad alta energia sul materiale, che consente una penetrazione più profonda e saldature più strette. Tuttavia, una messa a fuoco troppo stretta può aumentare il rischio di bruciatura, soprattutto con materiali più sottili. Al contrario, un raggio defocalizzato distribuirà l'energia su un'area più ampia, riducendo il rischio di bruciatura ma determinando anche una penetrazione più superficiale e saldature più ampie.
La messa a fuoco ottimale dipende dal materiale, dallo spessore e dalla geometria del giunto. Per un controllo preciso, i sistemi laser solitamente presentano una messa a fuoco regolabile, consentendo agli operatori di mettere a punto il raggio in base a requisiti di saldatura specifici.
Durata dell'impulso
Nella saldatura laser pulsata, il raggio laser viene erogato in brevi e intense scariche di energia. La durata di questi impulsi, la durata dell'impulso, può avere un impatto significativo sulla profondità di penetrazione, sulla velocità di raffreddamento e sulla qualità complessiva della saldatura. Impulsi più brevi consentono un apporto di energia più controllato e possono aiutare a prevenire il surriscaldamento, mentre impulsi più lunghi forniscono più energia per una penetrazione più profonda.
La durata dell'impulso deve essere attentamente regolata in base al materiale e allo spessore da saldare. Impulsi più lunghi sono solitamente utilizzati per materiali più spessi, mentre impulsi più brevi sono utilizzati per materiali sottili per evitare distorsioni termiche.
Qualità del raggio
La qualità del raggio si riferisce alla distribuzione dell'energia all'interno del raggio laser ed è un fattore essenziale per determinare l'efficacia con cui il laser può concentrarsi sul materiale. Un raggio di alta qualità ha un profilo energetico uniforme, consentendo un'erogazione di energia costante e una saldatura più stabile. I raggi di bassa qualità, d'altro canto, possono portare a una distribuzione di energia non uniforme, con conseguente scarsa qualità della saldatura e formazione di giunti incoerenti.
I sistemi di saldatura laser con elevata qualità del fascio solitamente producono saldature più pulite e precise, con meno difetti.
Velocità di saldatura
La velocità di saldatura influisce sul tempo durante il quale il laser viene applicato al materiale. Velocità di saldatura più elevate in genere comportano un apporto di calore inferiore, con conseguenti zone termicamente alterate più piccole e una distorsione ridotta. Tuttavia, se la velocità è troppo elevata, potrebbe non esserci abbastanza tempo per una penetrazione corretta, con conseguenti giunti deboli. Velocità più basse possono aumentare l'apporto di calore, con conseguenti zone termicamente alterate più grandi e potenzialmente una maggiore distorsione, ma potrebbero essere necessarie per la saldatura di materiali più spessi.
La velocità di saldatura ottimale è determinata dal tipo di materiale, dallo spessore e dalle caratteristiche di saldatura desiderate.
Gas di protezione
Il gas di protezione viene utilizzato nella saldatura laser per proteggere il bagno di saldatura dalla contaminazione dell'atmosfera circostante, che potrebbe causare ossidazione o altri difetti. Il tipo di gas di protezione utilizzato, come argon, azoto o una miscela di gas, può influenzare la qualità della saldatura, tra cui la sua resistenza, l'aspetto e la resistenza alla corrosione. Inoltre, il gas di protezione può influenzare la dissipazione del calore e la velocità di raffreddamento del bagno di saldatura, che a sua volta influenza la microstruttura della saldatura.
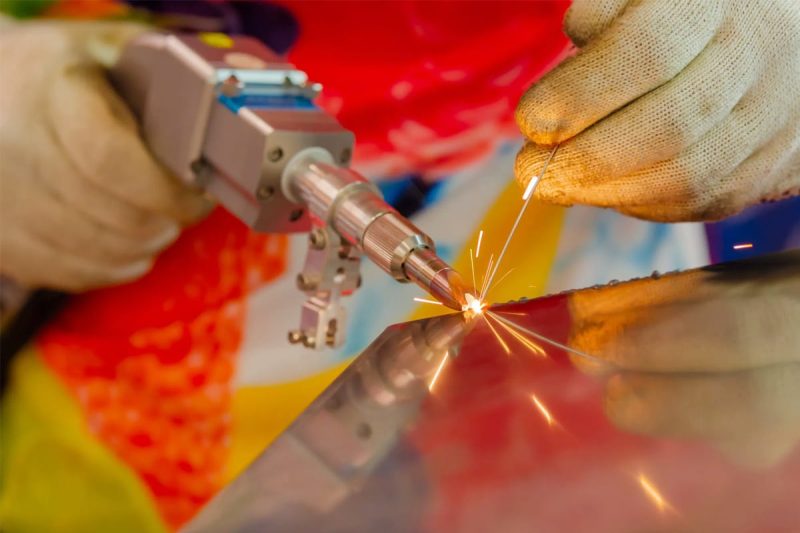
Spessore del materiale e progettazione del giunto
Nella saldatura laser, lo spessore del materiale e la geometria del giunto hanno un impatto significativo sul processo di saldatura, sull'energia richiesta e, in ultima analisi, sulla qualità della saldatura. Una profonda comprensione di questi fattori è fondamentale per ottenere saldature ottimali con difetti minimi.
Spessore materiale
Lo spessore del materiale da saldare ha un impatto diretto sul processo di saldatura laser. I materiali più spessi richiedono una potenza laser maggiore per ottenere una penetrazione completa e creare un legame forte. Quando si saldano materiali più spessi, è necessario gestire attentamente l'apporto di calore per evitare surriscaldamento e distorsione. Un'impostazione di potenza più elevata consente una penetrazione più profonda ma può anche aumentare le dimensioni della zona termicamente alterata (HAZ), che può influenzare le proprietà meccaniche del materiale di base.
Per i materiali sottili, si usa solitamente una potenza laser inferiore per evitare la bruciatura, poiché questi materiali richiedono meno energia per fondersi. La sfida principale nella saldatura di materiali sottili con un laser è bilanciare la potenza laser per evitare un apporto di calore eccessivo, ottenendo comunque una penetrazione sufficiente senza danneggiare il materiale. La velocità di raffreddamento rapida della saldatura laser aiuta a ridurre al minimo la zona interessata dal calore per i materiali più sottili.
Geometria del giunto
La geometria del giunto, come giunti di testa, giunti a T, giunti a sovrapposizione e giunti a filetto, svolge un ruolo cruciale nel successo di una saldatura laser. La saldatura laser in genere funziona meglio con giunti di testa, poiché l'allineamento diretto dei bordi del materiale garantisce un bagno di saldatura uniforme. Tuttavia, giunti più complessi come giunti a sovrapposizione o giunti a T richiedono un attento allineamento del raggio, poiché il laser deve garantire la penetrazione su tutti i lati del giunto, compresi eventuali spazi vuoti che possono esistere tra i materiali.
Quando la geometria del giunto comporta forme complesse o variazioni nello spessore del materiale, sono necessarie regolazioni dei parametri di saldatura. Ad esempio, i giunti a sovrapposizione richiedono un controllo preciso della messa a fuoco laser e dell'angolo del fascio per garantire che il materiale superiore si fonda efficacemente con quello inferiore. Le saldature d'angolo richiedono anche un attento controllo dell'interazione del fascio laser con le superfici del giunto, poiché gli angoli e la prossimità del materiale possono influenzare la distribuzione del calore.
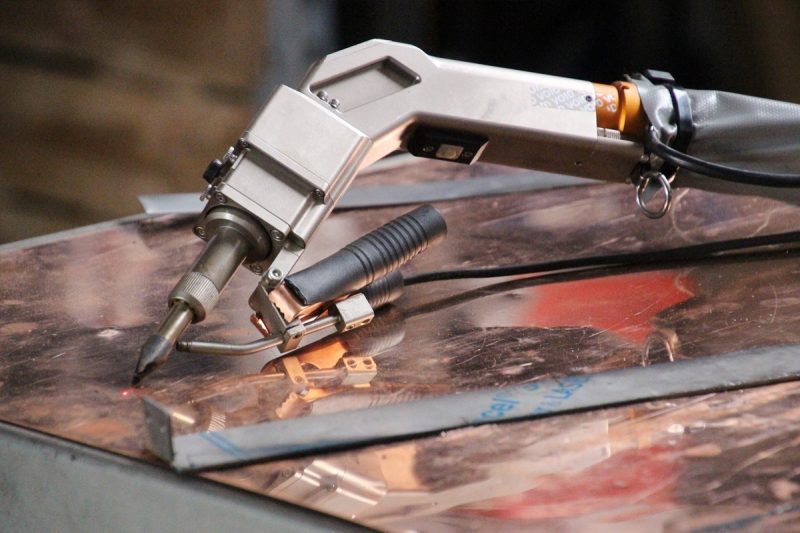
Gestione del calore e velocità di raffreddamento
Una gestione efficace del calore è fondamentale nella saldatura laser per controllare le proprietà dei materiali, ridurre al minimo la distorsione e prevenire difetti di saldatura. Gli aspetti chiave della gestione del calore includono la zona termicamente alterata (HAZ) e la velocità di raffreddamento.
Zona termicamente alterata (ZTA)
La zona termicamente alterata (HAZ) è la regione del materiale che non è fusa ma subisce un cambiamento nella microstruttura a causa delle alte temperature durante la saldatura. Le dimensioni e l'estensione della HAZ sono determinate dalla potenza del laser, dalla velocità di saldatura e dal tipo di materiale. Nella saldatura laser, la HAZ tende a essere più piccola rispetto ai metodi di saldatura tradizionali a causa del calore concentrato del raggio laser. Tuttavia, anche una piccola HAZ può avere un impatto sulle proprietà del materiale, specialmente per acciai ad alta resistenza o materiali sensibili ai cicli termici.
Per alcuni materiali, come ad esempio acciai ad alto tenore di carbonio o leghe di titanio, una ZTA più grande può portare a proprietà meccaniche ridotte, come comportamento fragile o cricche da corrosione sotto sforzo. Di conseguenza, un attento controllo dei parametri laser, in particolare potenza e velocità, è essenziale per ridurre al minimo la ZTA pur ottenendo una fusione adeguata all'interfaccia del giunto.
Velocità di raffreddamento
La velocità di raffreddamento, ovvero la velocità alla quale il bagno di saldatura fuso si solidifica, è un fattore critico per determinare la microstruttura finale e le proprietà meccaniche della saldatura. La saldatura laser in genere determina velocità di raffreddamento molto elevate a causa della piccola zona interessata dal calore e della rapida solidificazione del bagno fuso. Velocità di raffreddamento più elevate possono determinare una microstruttura più fine, che può migliorare la resistenza della saldatura. Tuttavia, questo rapido raffreddamento può anche introdurre tensioni residue, che potenzialmente portano a cricche o distorsioni in determinati materiali, in particolare quelli con elevata temprabilità, come gli acciai ad alto tenore di carbonio.
Una velocità di raffreddamento più lenta può ridurre il rischio di cricche, ma può causare la formazione di grani più grandi, che possono ridurre la resistenza complessiva della saldatura. Gestire la velocità di raffreddamento è fondamentale per bilanciare questi fattori. Tecniche come il trattamento termico post-saldatura (ad esempio, ricottura) possono essere impiegate per alleviare le tensioni residue e migliorare le proprietà finali del materiale.
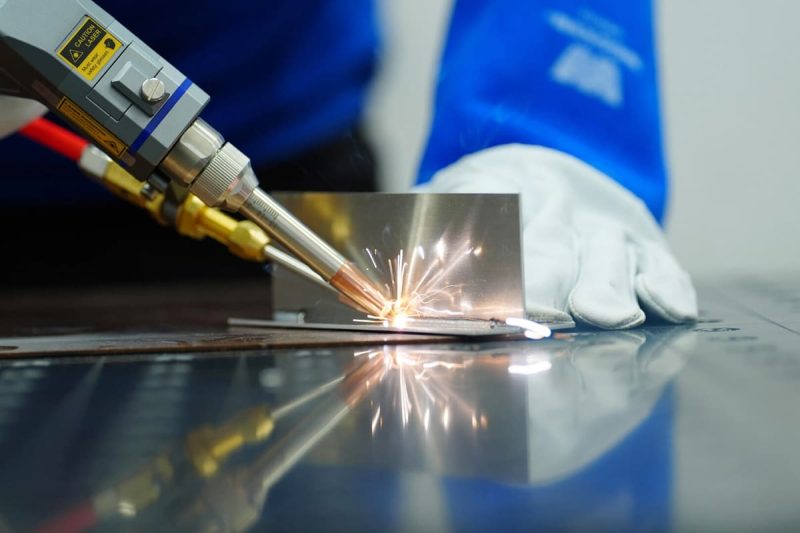
Attrezzatura e configurazione per saldatura laser
La qualità della saldatura laser è fortemente influenzata dal tipo e dalla configurazione dell'attrezzatura per la saldatura laser. I componenti chiave dell'attrezzatura includono la sorgente laser, la lente di messa a fuoco, l'ottica e la testa di saldatura.
Tipo di sorgente laser
Il tipo di laser utilizzato nel processo di saldatura influisce su diversi aspetti dell'operazione, tra cui la qualità del raggio, la potenza e la messa a fuoco. I tipi di laser comuni per la saldatura includono laser CO2, laser a fibra e laser a disco:
- Laser CO2: sono i laser più ampiamente utilizzati nella saldatura industriale grazie alla loro elevata potenza e versatilità. I laser CO2 sono ideali per saldare materiali più spessi e forniscono una qualità del fascio stabile.
- Laser a fibra: questi laser sono noti per la loro elevata qualità del fascio e per l'efficienza, rendendoli particolarmente efficaci per la saldatura di lamiere sottili. I laser a fibra offrono velocità di saldatura più elevate e possono raggiungere una precisione maggiore rispetto ai laser a CO2, in particolare su materiali con bassa conduttività termica.
La scelta della sorgente laser giusta dipende dal tipo di materiale, dallo spessore e dai requisiti dell'applicazione.
Lente di messa a fuoco e ottica
Il raggio laser deve essere focalizzato sul pezzo in lavorazione per ottenere la dimensione di saldatura e la penetrazione desiderate. La qualità e l'allineamento della lente di messa a fuoco e dell'ottica svolgono un ruolo fondamentale nella precisione del raggio e nella qualità della saldatura. Un sistema ottico di alta qualità assicura che il raggio laser rimanga stabile e focalizzato, il che è particolarmente importante per le applicazioni ad alta precisione.
La lunghezza focale della lente, la dimensione dell'apertura e il posizionamento della lente possono tutti influenzare il modo in cui l'energia viene distribuita sulla superficie del materiale. Ottiche mal allineate possono portare a sfocatura, che si traduce in un'erogazione di energia incoerente e potenzialmente saldature deboli o difettose.
Testa di saldatura e ottica di messa a fuoco
La testa di saldatura è responsabile della direzione del raggio laser sul materiale. L'impostazione della testa di saldatura, inclusa la sua posizione, inclinazione e movimento, influisce sull'uniformità e sulla qualità della saldatura. La testa di saldatura deve essere allineata con precisione con il materiale per garantire che il raggio laser rimanga focalizzato sul giunto durante tutto il processo di saldatura.
Oltre alla testa di saldatura, anche l'ottica di focalizzazione, che modella e dirige il fascio, deve essere sottoposta a manutenzione e calibrazione adeguate. Qualsiasi disallineamento o degradazione di queste ottiche può portare a un'erogazione del fascio non uniforme e a una scarsa qualità della saldatura.
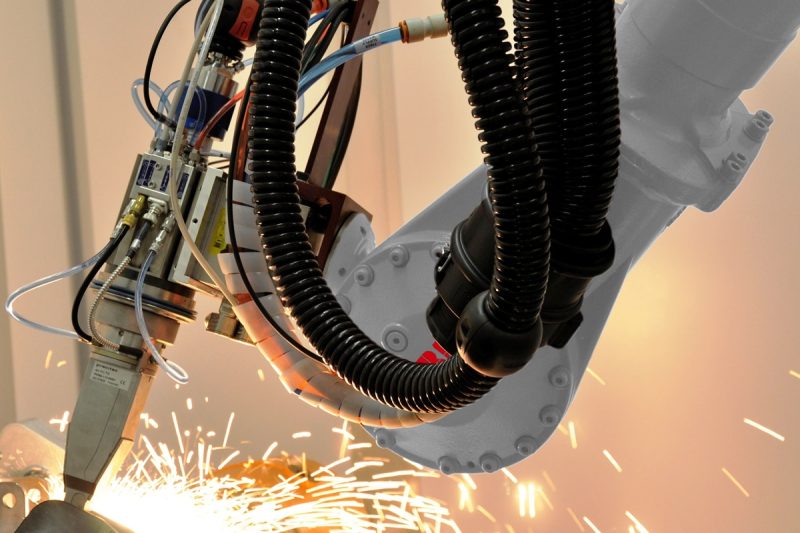
Condizioni ambientali
Le condizioni ambientali in cui avviene la saldatura laser possono avere un effetto significativo sulla qualità e la consistenza della saldatura. I principali fattori ambientali da considerare includono la temperatura ambiente e il flusso d'aria.
Temperatura ambiente
Le temperature estreme possono influenzare la risposta del materiale al processo di saldatura laser. Ad esempio, i materiali possono diventare fragili a basse temperature, il che può aumentare la probabilità di cricche durante la saldatura. Al contrario, temperature ambiente elevate possono portare a un'eccessiva distorsione del materiale o a un'espansione termica, che può influenzare l'allineamento del giunto e la consistenza della saldatura. Mantenere una temperatura ambiente stabile è fondamentale per garantire che il materiale risponda in modo prevedibile al processo di saldatura.
Flusso d'aria e contaminanti
La presenza di contaminanti come polvere, olio, umidità o fumi può influenzare il processo di saldatura in diversi modi. I contaminanti nell'aria possono assorbire parte dell'energia laser, riducendo l'efficienza del processo. Inoltre, le impurità sulla superficie del materiale possono causare ossidazione, corrosione o altri difetti che compromettono la qualità della saldatura.
Il controllo dell'ambiente di saldatura tramite un'adeguata ventilazione, superfici pulite e una camera di saldatura chiusa può aiutare a ridurre il rischio di contaminazione e garantire saldature più uniformi.

Trattamento Post Saldatura
Una volta completato il processo di saldatura laser, potrebbero essere necessari trattamenti post-saldatura per migliorare le proprietà meccaniche, alleviare le sollecitazioni residue e garantire che la saldatura soddisfi le specifiche richieste.
Ricottura
La ricottura è un processo di trattamento termico in cui il materiale saldato viene riscaldato a una temperatura specifica e poi raffreddato lentamente. Questo processo viene utilizzato per alleviare le tensioni residue che potrebbero essere state introdotte durante le rapide fasi di riscaldamento e raffreddamento del processo di saldatura. La ricottura aiuta a ripristinare la duttilità del materiale e a ridurre il rischio di cricche.
Nella saldatura laser, i materiali che subiscono rapide velocità di raffreddamento potrebbero richiedere la ricottura per prevenire l'infragilimento e migliorare la tenacità della saldatura. La temperatura e la durata esatte della ricottura dipendono dal tipo di materiale e dai requisiti specifici della saldatura.
Finitura superficiale e pulizia
Dopo la saldatura, la superficie della saldatura potrebbe presentare ossidazione, incrostazioni o altri contaminanti che devono essere rimossi. La pulizia e la finitura della superficie della saldatura sono essenziali per garantire un aspetto liscio e privo di difetti e per migliorare la resistenza alla corrosione dell'area saldata.
La pulizia può comprendere tecniche quali lucidatura meccanica, decapaggio chimico o sabbiatura abrasiva. Una finitura superficiale adeguata è particolarmente importante nei settori in cui l'estetica della saldatura e l'integrità del materiale sono fondamentali, come nei dispositivi medici o nell'elettronica di consumo.
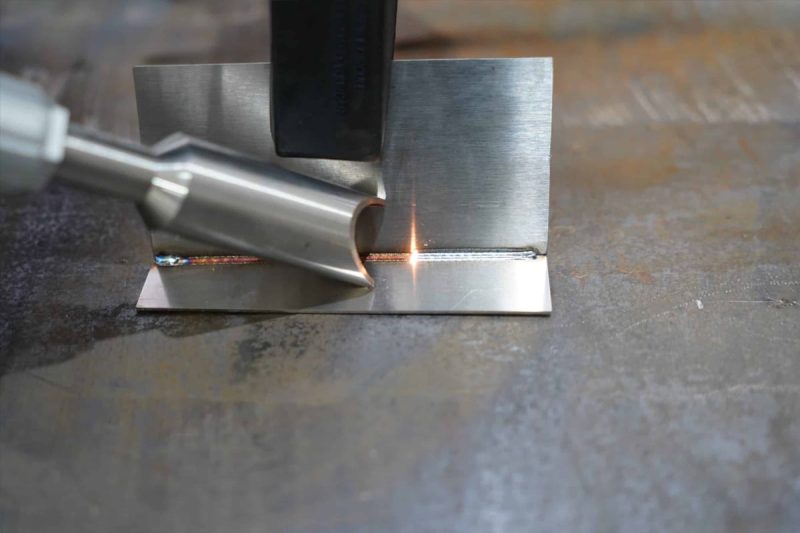
Sfide nella saldatura laser
Sebbene la saldatura laser offra molti vantaggi, presenta anche una serie di sfide. I problemi comuni includono porosità, crepe, distorsioni e qualità di saldatura incoerente.
Porosità
La porosità si verifica quando si formano sacche di gas all'interno del bagno di saldatura, causando vuoti nella saldatura. Ciò è spesso causato da gas intrappolati come azoto o ossigeno che rimangono intrappolati durante il processo di solidificazione. La porosità può indebolire la saldatura e influenzarne le prestazioni. Un gas di protezione appropriato, un controllo attento dei parametri di saldatura e la garanzia di superfici pulite prima della saldatura possono aiutare a ridurre al minimo la porosità.
Cracking e distorsione
La formazione di crepe è un problema significativo nella saldatura laser, in particolare nei materiali con elevato contenuto di carbonio o bassa duttilità. Le rapide velocità di raffreddamento della saldatura laser possono creare elevate sollecitazioni residue, che possono portare alla formazione di crepe, in particolare nella zona interessata dal calore.
La distorsione può verificarsi anche a causa di riscaldamento e raffreddamento non uniformi, che causano la deformazione o la deformazione del materiale. Gestire l'apporto di calore tramite parametri laser ottimali e utilizzare tecniche di serraggio può aiutare a ridurre la distorsione.
Incoerenza nella qualità della saldatura
Una qualità di saldatura incoerente può derivare da variazioni nelle proprietà dei materiali, nei parametri laser o nei fattori ambientali. Fluttuazioni nella potenza o nella messa a fuoco del laser, disallineamenti dei giunti o cambiamenti nel flusso del gas di protezione possono tutti contribuire a saldature incoerenti. Per ridurre al minimo queste incoerenze, è essenziale mantenere uno stretto controllo sul processo di saldatura e calibrare regolarmente l'attrezzatura per garantire uniformità in tutte le saldature.
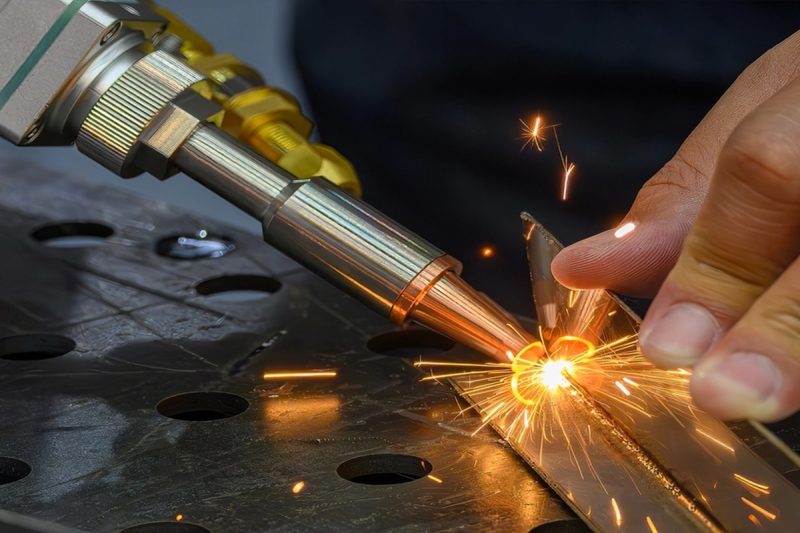
Riepilogo
Nella saldatura laser, la saldabilità dei materiali dipende da un'ampia gamma di fattori, dalla composizione e dallo spessore del materiale ai parametri laser e alle condizioni ambientali esterne. Comprendendo questi fattori e ottimizzandoli, i produttori possono produrre saldature di alta qualità che soddisfano rigorosi requisiti di resistenza, durata e aspetto. Mentre sfide come porosità, crepe e distorsioni possono sorgere durante il processo di saldatura, un attento controllo e selezione dei parametri di saldatura, delle attrezzature e dei trattamenti post-saldatura possono mitigare questi problemi e migliorare la coerenza e l'affidabilità della saldatura laser su una varietà di materiali e applicazioni.
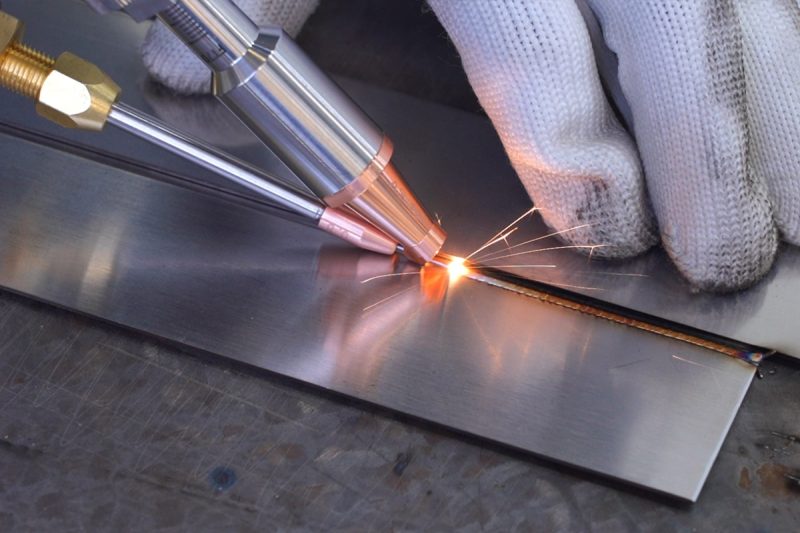
Ottieni soluzioni di saldatura laser
Per le aziende che cercano saldature affidabili e di alta qualità, AccTek Laser offre soluzioni di saldatura laser all'avanguardia progettate per soddisfare diverse esigenze industriali. Come produttore professionale di macchine per taglio, saldatura, pulizia e marcatura laser, AccTek Laser fornisce attrezzature all'avanguardia su misura per ottimizzare la saldabilità. Che tu stia lavorando con metalli, materie plastiche o compositi, le nostre macchine per saldatura laser offrono precisione, velocità ed efficienza anche per le applicazioni più impegnative.
Laser AccTek saldatrici laser sono progettati per gestire vari materiali e spessori, con impostazioni personalizzabili per potenza laser, durata impulso, messa a fuoco e velocità di saldatura, assicurando che le tue saldature soddisfino gli standard più elevati. Il nostro team di esperti può aiutarti a selezionare l'attrezzatura giusta, configurare il sistema per le tue esigenze specifiche e offrire supporto continuo per garantire prestazioni ottimali durante tutto il processo di produzione.
Scegliendo AccTek Laser, avrai accesso a una tecnologia avanzata e a un partner impegnato a migliorare la qualità e la produttività della tua saldatura, aiutandoti a ottenere saldature impeccabili e durature ogni volta.
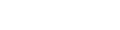
Informazioni sui contatti
- [email protected]
- [email protected]
- +86-19963414011
- N. 3 Zona A, zona industriale di Lunzhen, città di Yucheng, provincia di Shandong.
Ottieni soluzioni laser