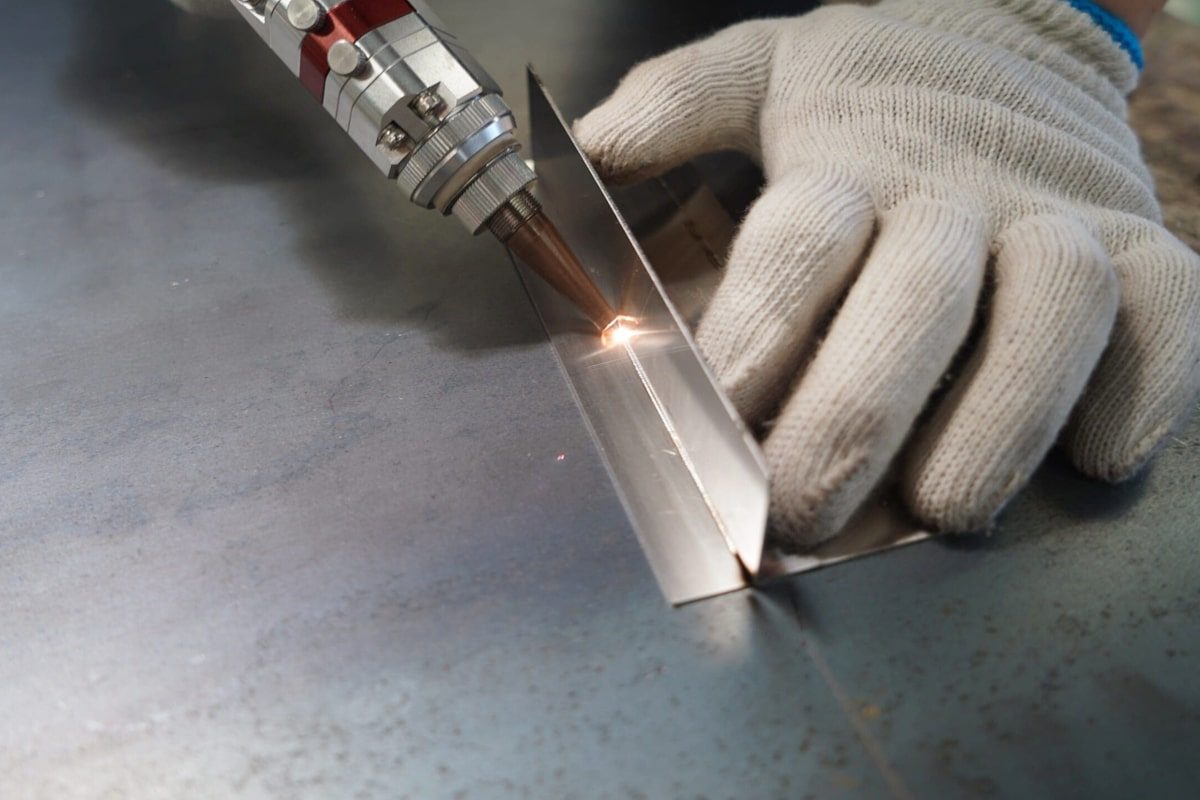
Jakie czynniki wpływają na spawalność spawania laserowego?
Spawanie laserowe zrewolucjonizowało nowoczesną produkcję, oferując wysoką precyzję, minimalne odkształcenia cieplne i możliwość łączenia materiałów, które w innym przypadku trudno spawać tradycyjnymi metodami. Branże takie jak lotnictwo, motoryzacja, urządzenia medyczne i elektronika w dużym stopniu polegają na spawaniu laserowym ze względu na jego szybkość i zdolność do dostarczania wysokiej jakości, mocnych połączeń przy minimalnej obróbce po spawaniu. Pomimo licznych zalet spawania laserowego, osiągnięcie optymalnej spawalności nie zawsze jest proste. Sukces spawania laserowego zależy od wielu czynników — właściwości materiału, parametrów lasera, konfiguracji sprzętu, warunków środowiskowych i obróbki po spawaniu — z których wszystkie muszą być starannie kontrolowane, aby zapewnić produkcję mocnego, trwałego i wolnego od wad spoiny.
W tym artykule szczegółowo przeanalizujemy różne czynniki wpływające na spawalność materiałów w spawaniu laserowym. Czynniki te obejmują skład materiału bazowego, geometrię połączenia, moc lasera, prędkość i jakość wiązki, a także zewnętrzne czynniki środowiskowe, takie jak temperatura i zanieczyszczenia. Przeanalizujemy również typowe wyzwania napotykane w spawaniu laserowym i sposoby ich łagodzenia w celu uzyskania najwyższej możliwej jakości spoiny. Pod koniec tego artykułu czytelnicy będą mieli kompleksowe zrozumienie wielu zmiennych zaangażowanych w spawanie laserowe i jak zoptymalizować te czynniki w celu uzyskania lepszych wyników spawania.
Spis treści
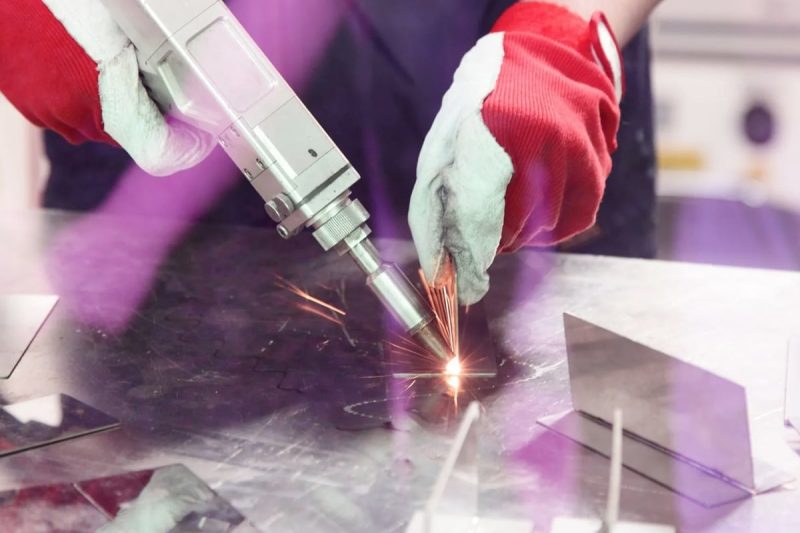
Wprowadzenie do spawania laserowego
Definicja i przegląd
Spawanie laserowe to precyzyjna technika spawania, która wykorzystuje silnie skoncentrowaną wiązkę lasera do topienia i łączenia materiałów, zazwyczaj metali lub tworzyw termoplastycznych. Wiązka lasera, która jest generowana przez źródło laserowe, kieruje skupioną energię na materiał, tworząc zlokalizowaną strefę ciepła, która topi materiał bazowy na styku złącza. Gdy stopiony materiał krzepnie, tworzy spoinę. Proces ten można wykonać przy użyciu laserów o fali ciągłej (CW), które zapewniają stałe ciepło, lub laserów impulsowych, które dostarczają energię w krótkich seriach, często w celu zapobiegania przegrzaniu i zapewnienia kontrolowanej penetracji.
Spawanie laserowe jest niezwykle wszechstronne i może być stosowane do różnych typów i grubości materiałów. Oferuje liczne zalety, w tym wysokie prędkości spawania, wąskie strefy wpływu ciepła (HAZ), minimalne odkształcenia materiału i możliwość automatyzacji procesu, co prowadzi do zwiększenia wydajności produkcji. Precyzja wiązki laserowej umożliwia spawanie w ciasnych przestrzeniach i delikatnych podzespołach, dzięki czemu spawanie laserowe jest idealne do zastosowań wymagających wysokiej precyzji, w tym w przemyśle lotniczym i elektronicznym.
Znaczenie spawalności w spawaniu laserowym
Spawalność w spawaniu laserowym odnosi się do zdolności materiału do tworzenia mocnego, wolnego od wad połączenia, gdy jest poddawany procesowi spawania laserowego. Osiągnięcie spawalności zależy od kilku powiązanych ze sobą czynników, takich jak skład chemiczny materiału, właściwości termiczne, konstrukcja połączenia i sposób, w jaki reaguje on na lokalne ciepło dopływające z wiązki laserowej. Jeśli czynniki te nie zostaną zoptymalizowane, połączenie spawane może być podatne na wady, takie jak porowatość, pękanie, odkształcenie lub słabe wiązanie.
Pojęcie spawalności jest szczególnie istotne w spawaniu laserowym, ponieważ wysokie stężenie energii wiązki laserowej może mieć znaczący wpływ na mikrostrukturę materiału i właściwości mechaniczne. Na przykład szybkie cykle nagrzewania i chłodzenia mogą prowadzić do problemów, takich jak naprężenia szczątkowe, pęknięcia lub niepożądane przemiany fazowe w niektórych materiałach. Aby sprostać tym wyzwaniom, producenci muszą starannie wybierać i kontrolować różne parametry związane ze spawaniem laserowym.
Porównanie z tradycyjnymi metodami spawania
Chociaż spawanie laserowe jest znane ze swojej precyzji i wydajności, różni się ono znacząco od tradycyjnych metod spawania, takich jak spawanie MIG (Metal Inert Gas) lub spawanie TIG (Tungsten Inert Gas) na kilka ważnych sposobów. Tradycyjne metody spawania wykorzystują łuki elektryczne do generowania ciepła, które nagrzewają większą powierzchnię materiału i generalnie powodują szersze strefy wpływu ciepła. Metody te mają również tendencję do stosowania wolniejszych prędkości spawania i większych odkształceń materiału. Z drugiej strony spawanie laserowe charakteryzuje się silnie skoncentrowaną wiązką energii, co pozwala na szybsze prędkości spawania, węższe strefy wpływu ciepła i minimalne odkształcenia.
Jednak spawanie laserowe jest bardziej wrażliwe na zmiany właściwości materiału, konstrukcji złącza i ustawień lasera niż tradycyjne metody. Na przykład tradycyjne metody mogą być bardziej wyrozumiałe podczas spawania grubszych materiałów lub złączy o nieregularnej geometrii, podczas gdy spawanie laserowe wymaga bardziej precyzyjnej kontroli parametrów, takich jak moc lasera, ogniskowanie wiązki i prędkość spawania. W związku z tym spawanie laserowe może nie być idealnym rozwiązaniem dla wszystkich zastosowań, szczególnie w przypadku materiałów lub geometrii, które są trudne dla procesu.
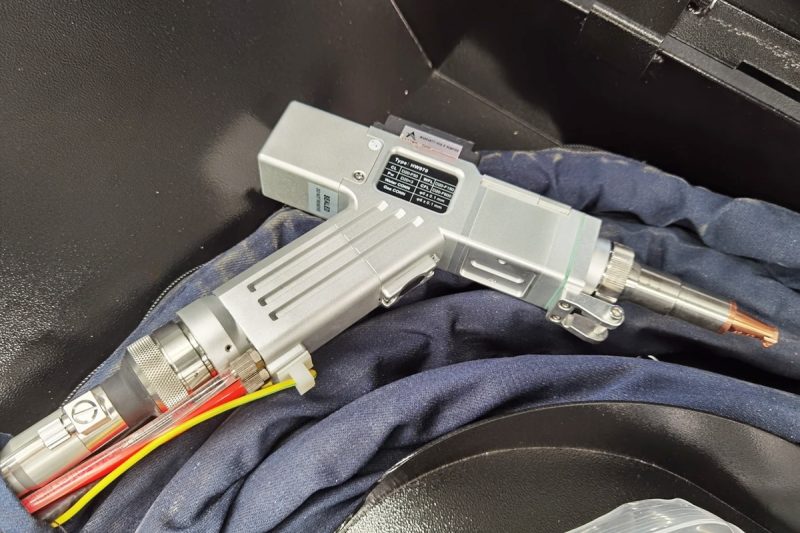
Właściwości materiału
Materiał, który jest spawany, odgrywa znaczącą rolę w powodzeniu operacji spawania laserowego. Kluczowe właściwości materiału, które wpływają na spawalność, obejmują skład materiału bazowego, grubość i geometrię, temperaturę topnienia, przewodność cieplną oraz obecność pierwiastków stopowych lub dodatków.
Skład materiału bazowego
Skład chemiczny materiału bazowego jest jednym z najważniejszych czynników wpływających na spawalność. Różne materiały mają różne temperatury topnienia, przewodnictwo cieplne i zachowania krzepnięcia, które wpływają na proces spawania laserowego. Na przykład stale wysokowęglowe mają tendencję do tworzenia twardych i kruchych faz podczas chłodzenia, co zwiększa prawdopodobieństwo pękania spoiny. Podobnie materiały o wysokim poziomie niektórych pierwiastków stopowych, takich jak chrom, nikiel lub molibden, mogą być bardziej podatne na przemiany fazowe, co może prowadzić do wad spoiny lub obniżenia właściwości mechanicznych.
Niektóre materiały, takie jak aluminium I miedź, są szczególnie trudne do spawania laserowego ze względu na wysoką przewodność cieplną i niskie temperatury topnienia. Materiały te wymagają większej mocy lasera, aby osiągnąć odpowiednią penetrację, ale ryzyko przepalenia jest również znacznie wyższe. Materiały o wysokim współczynniku rozszerzalności, takie jak stopy tytanu, mogą ulegać odkształceniom cieplnym podczas spawania, co wymaga precyzyjnej kontroli parametrów lasera.
Zrozumienie składu spawanego materiału jest niezbędne do określenia optymalnych parametrów lasera. Elementy stopowe i zanieczyszczenia w materiale mogą wpływać na sposób, w jaki materiał reaguje na ciepło i tworzenie spoiny, co sprawia, że konieczne jest dostosowanie parametrów, takich jak moc lasera, ogniskowanie wiązki i gaz osłonowy.
Grubość i geometria
Grubość materiału i geometria spoiny bezpośrednio wpływają na energię wymaganą do spawania i rozkład ciepła w materiale. W przypadku cienkich materiałów zazwyczaj wystarczająca jest niższa moc lasera, ale konieczna jest staranna kontrola, aby uniknąć nadmiernego wprowadzania ciepła, które mogłoby spowodować przepalenie. W przypadku grubszych materiałów konieczna jest wyższa moc lasera i wolniejsze prędkości spawania, aby zapewnić pełne wtopienie i solidne spoiny.
Geometria połączenia wpływa również na interakcję lasera z materiałem. Proste połączenia czołowe są stosunkowo łatwe do spawania, ponieważ zapewniają bezpośrednie połączenie między dwiema powierzchniami. Jednak bardziej złożone połączenia, takie jak połączenia T, połączenia pachwinowe lub połączenia zakładkowe, mogą wymagać szczególnej uwagi. Kąt i ustawienie połączenia będą miały wpływ na zdolność lasera do prawidłowej penetracji i łączenia materiałów.
Materiały o złożonej geometrii mogą również stwarzać dodatkowe wyzwania dla spawania laserowego ze względu na trudności w wyrównaniu wiązki ze złączem i różnice w grubości wzdłuż złącza. Optymalizacja projektu złącza i zapewnienie prawidłowego wyrównania wiązki laserowej to kluczowe kroki w celu uzyskania mocnych, wysokiej jakości spoin.
Temperatura topnienia i przewodność cieplna
Temperatura topnienia materiału określa, ile energii jest potrzebne do jego stopienia. Materiały o wysokiej temperaturze topnienia, takie jak wolfram, tytan lub stale wysokostopowe, wymagają znacznie więcej energii, aby osiągnąć temperaturę topnienia i wymagają ostrożnego zarządzania mocą lasera. Z drugiej strony materiały o niskiej temperaturze topnienia, takie jak aluminium lub cynk, mogą stopić się zbyt łatwo pod wpływem wiązki laserowej i mogą wymagać szybkich prędkości spawania lub technik lasera impulsowego, aby zapobiec nadmiernemu przetopieniu.
Przewodność cieplna — zdolność materiału do przewodzenia ciepła — również wpływa na spawalność. Materiały o wysokiej przewodności cieplnej, takie jak miedź, szybko rozpraszają ciepło, co oznacza, że wiązka lasera musi dostarczać wystarczającą energię, aby pokonać tę utratę ciepła i osiągnąć odpowiednią penetrację. Z kolei materiały o niskiej przewodności cieplnej, takie jak Stal nierdzewna, skuteczniej zatrzymują ciepło, co może prowadzić do zwiększenia strefy wpływu ciepła (HAZ) i potencjalnych odkształceń termicznych, jeśli nie będzie odpowiednio zarządzane.
Elementy stopowe i dodatki
Obecność pierwiastków stopowych i dodatków może mieć głęboki wpływ na spawalność materiału. Powszechne pierwiastki stopowe, takie jak mangan, krzem i chrom, mogą poprawić właściwości mechaniczne materiału, ale mogą również stwarzać problemy podczas spawania. Na przykład mangan może sprawić, że spoina będzie bardziej podatna na pękanie, podczas gdy nadmiar krzemu może prowadzić do tworzenia się kruchych faz w strefie spoiny.
Dodatki takie jak topnik mogą być używane w celu zwiększenia wiązania powierzchni, zapobiegania utlenianiu lub modyfikowania zachowania jeziorka spawalniczego. Wybór topnika i innych dodatków powinien być dokonany ostrożnie, ponieważ mogą one wpływać na końcową jakość i właściwości mechaniczne spoiny.
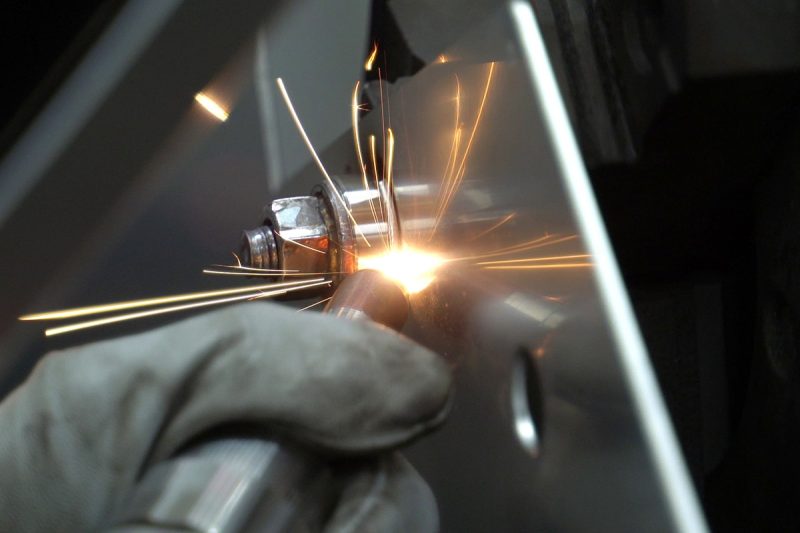
Parametry lasera
Parametry lasera, w tym moc lasera, ogniskowanie, prędkość, jakość wiązki i inne, są fundamentalne dla spawalności materiałów. Parametry te kontrolują interakcję wiązki lasera z materiałem, energię dostarczaną do jeziorka spawalniczego i szybkość krzepnięcia.
Moc lasera
Moc lasera bezpośrednio wpływa na głębokość penetracji, szybkość spawania i ilość ciepła wytwarzanego podczas procesu. Większa moc lasera prowadzi do głębszej penetracji, ale zwiększa również ryzyko przepalenia lub stref nadmiernego wpływu ciepła. Niższe ustawienia mocy mogą nie zapewniać wystarczającej energii do osiągnięcia pełnej penetracji w grubszych materiałach, co skutkuje słabymi połączeniami lub niepełnym stopieniem.
Optymalne ustawienie mocy lasera zależy od spawanego materiału, jego grubości i pożądanych właściwości spoiny. Zasadniczo należy znaleźć równowagę między wystarczającą mocą do stopienia materiału a unikaniem nadmiaru ciepła, które mogłoby zniekształcić obrabiany przedmiot.
Skupienie laserowe
Ogniskowanie laserowe kontroluje rozmiar i intensywność wiązki laserowej. Mocno skupiona wiązka powoduje powstanie małego, wysokoenergetycznego punktu na materiale, co pozwala na głębszą penetrację i węższe spoiny. Jednak zbyt ciasne skupienie może zwiększyć ryzyko przepalenia, szczególnie w przypadku cieńszych materiałów. Natomiast rozogniskowana wiązka rozproszy energię na większym obszarze, zmniejszając ryzyko przepalenia, ale również prowadząc do płytszej penetracji i szerszych spoin.
Optymalna ostrość zależy od materiału, grubości i geometrii połączenia. Aby zapewnić precyzyjną kontrolę, systemy laserowe zazwyczaj mają regulowaną ostrość, co pozwala operatorom na dokładne dostrojenie wiązki zgodnie ze szczególnymi wymaganiami spawania.
Czas trwania impulsu
W spawaniu laserowym impulsowym wiązka lasera jest dostarczana w krótkich, intensywnych seriach energii. Czas trwania tych impulsów — czas trwania impulsu — może znacząco wpłynąć na głębokość penetracji, szybkość chłodzenia i ogólną jakość spoiny. Krótsze impulsy umożliwiają bardziej kontrolowane wprowadzanie energii i mogą pomóc zapobiec przegrzaniu, podczas gdy dłuższe impulsy zapewniają więcej energii do głębszej penetracji.
Czas trwania impulsu musi być starannie dostosowany do materiału i grubości spawanego materiału. Dłuższe impulsy są zazwyczaj używane do grubszych materiałów, podczas gdy krótsze impulsy są używane do cienkich materiałów, aby uniknąć zniekształceń termicznych.
Jakość wiązki
Jakość wiązki odnosi się do rozkładu energii w wiązce lasera i jest istotnym czynnikiem w określaniu, jak skutecznie laser może skupić się na materiale. Wysokiej jakości wiązka ma jednolity profil energetyczny, co umożliwia spójną dostawę energii i bardziej stabilne spawanie. Z drugiej strony wiązki niskiej jakości mogą prowadzić do nierównomiernego rozkładu energii, co skutkuje słabą jakością spoiny i niespójnym tworzeniem spoiny.
Systemy spawania laserowego o wysokiej jakości wiązki zazwyczaj zapewniają czystsze, bardziej precyzyjne spoiny z mniejszą liczbą wad.
Prędkość spawania
Prędkość spawania wpływa na czas, w którym laser jest stosowany do materiału. Większe prędkości spawania zazwyczaj skutkują mniejszym dopływem ciepła, co prowadzi do mniejszych stref wpływu ciepła i zmniejszonych odkształceń. Jednak jeśli prędkość jest zbyt wysoka, może nie być wystarczająco dużo czasu na właściwą penetrację, co skutkuje słabymi połączeniami. Mniejsze prędkości mogą zwiększyć dopływ ciepła, co prowadzi do większych stref wpływu ciepła i potencjalnie większych odkształceń, ale mogą być konieczne do spawania grubszych materiałów.
Optymalna prędkość spawania zależy od rodzaju materiału, jego grubości i pożądanych właściwości spoiny.
Gaz osłonowy
Gaz osłonowy jest używany w spawaniu laserowym w celu ochrony jeziorka spawalniczego przed zanieczyszczeniem przez otaczającą atmosferę, co może prowadzić do utleniania lub innych wad. Rodzaj użytego gazu osłonowego, takiego jak argon, azot lub mieszanina gazów, może mieć wpływ na jakość spoiny, w tym jej wytrzymałość, wygląd i odporność na korozję. Ponadto gaz osłonowy może wpływać na rozpraszanie ciepła i szybkość chłodzenia jeziorka spawalniczego, co z kolei wpływa na mikrostrukturę spoiny.
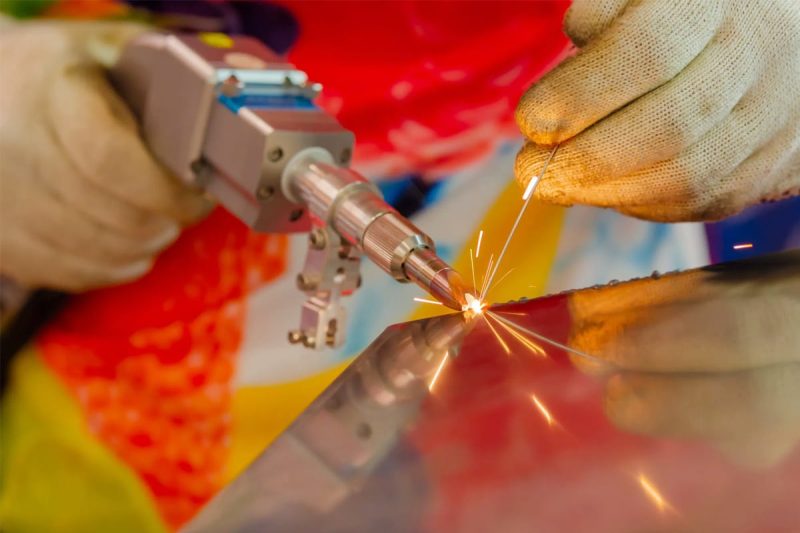
Grubość materiału i konstrukcja połączenia
W spawaniu laserowym grubość materiału i geometria spoiny znacząco wpływają na proces spawania, wymaganą energię i ostatecznie na jakość spoiny. Głębokie zrozumienie tych czynników jest kluczowe dla uzyskania optymalnych spoin z minimalną liczbą defektów.
Grubość materiału
Grubość spawanego materiału ma bezpośredni wpływ na proces spawania laserowego. Grubsze materiały wymagają większej mocy lasera, aby osiągnąć pełną penetrację i stworzyć mocne wiązanie. Podczas spawania grubszych materiałów konieczne jest ostrożne zarządzanie ciepłem wejściowym, aby zapobiec przegrzaniu i odkształceniom. Wyższe ustawienie mocy umożliwia głębszą penetrację, ale może również zwiększyć rozmiar strefy wpływu ciepła (HAZ), co może mieć wpływ na właściwości mechaniczne materiału bazowego.
W przypadku cienkich materiałów zwykle stosuje się niższą moc lasera, aby uniknąć przepalenia, ponieważ materiały te wymagają mniej energii do stopienia. Kluczowym wyzwaniem w spawaniu cienkich materiałów za pomocą lasera jest zrównoważenie mocy lasera w celu uniknięcia nadmiernego wprowadzania ciepła, przy jednoczesnym osiągnięciu wystarczającej penetracji bez uszkodzenia materiału. Szybkie tempo chłodzenia spawania laserowego pomaga zminimalizować strefę wpływu ciepła w przypadku cieńszych materiałów.
Geometria stawowa
Geometria połączenia — takiego jak połączenia czołowe, połączenia typu T, połączenia zakładkowe i połączenia pachwinowe — odgrywa kluczową rolę w powodzeniu spawania laserowego. Spawanie laserowe zazwyczaj najlepiej sprawdza się w przypadku połączeń czołowych, ponieważ bezpośrednie wyrównanie krawędzi materiału zapewnia spójny jeziorko spawalnicze. Jednak bardziej złożone połączenia, takie jak połączenia zakładkowe lub połączenia typu T, wymagają starannego wyrównania wiązki, ponieważ laser musi zapewnić penetrację ze wszystkich stron połączenia, w tym wszelkich szczelin, które mogą występować między materiałami.
Gdy geometria połączenia obejmuje złożone kształty lub zmiany grubości materiału, konieczne są zmiany parametrów spawania. Na przykład połączenia zakładkowe wymagają precyzyjnej kontroli ogniska lasera i kąta wiązki, aby zapewnić skuteczne połączenie górnego materiału z dolnym materiałem. Spoiny pachwinowe wymagają również starannej kontroli interakcji wiązki lasera z powierzchniami połączenia, ponieważ kąty i bliskość materiału mogą wpływać na dystrybucję ciepła.
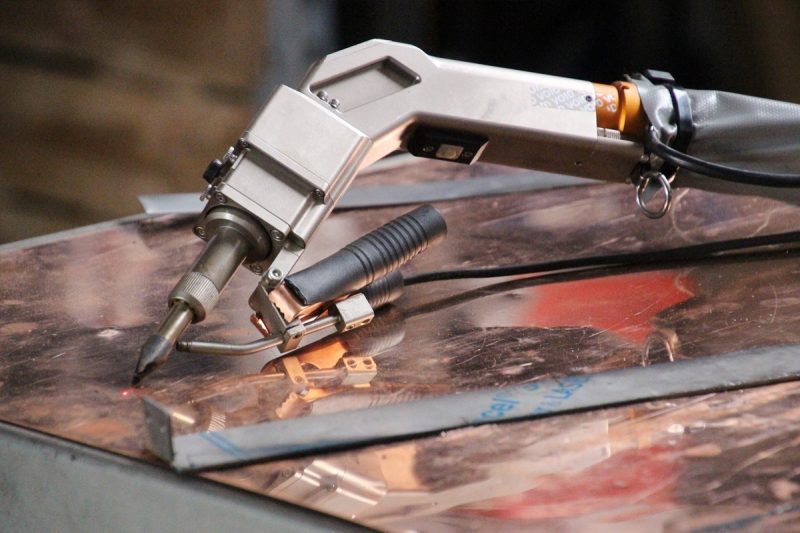
Zarządzanie ciepłem i szybkość chłodzenia
Efektywne zarządzanie ciepłem jest kluczowe w spawaniu laserowym, aby kontrolować właściwości materiału, minimalizować odkształcenia i zapobiegać wadom spoin. Kluczowe aspekty zarządzania ciepłem obejmują strefę wpływu ciepła (HAZ) i szybkość chłodzenia.
Strefa wpływu ciepła (HAZ)
Strefa wpływu ciepła (HAZ) to obszar materiału, który nie jest topiony, ale doświadcza zmiany mikrostruktury z powodu wysokich temperatur podczas spawania. Rozmiar i zasięg HAZ są określane przez moc lasera, prędkość spawania i rodzaj materiału. W spawaniu laserowym HAZ jest zwykle mniejszy w porównaniu do tradycyjnych metod spawania z powodu skoncentrowanego ciepła wiązki laserowej. Jednak nawet mała HAZ może mieć wpływ na właściwości materiału, szczególnie w przypadku stali o wysokiej wytrzymałości lub materiałów wrażliwych na cykle termiczne.
W przypadku niektórych materiałów, takich jak: stale wysokowęglowe lub stopów tytanu, większa strefa HAZ może prowadzić do obniżenia właściwości mechanicznych, takich jak kruche zachowanie lub pękanie korozyjne naprężeniowe. W rezultacie, staranna kontrola parametrów lasera, zwłaszcza mocy i prędkości, jest niezbędna do zminimalizowania strefy HAZ przy jednoczesnym osiągnięciu odpowiedniego stopienia na styku złącza.
Szybkość chłodzenia
Szybkość chłodzenia, czyli prędkość, z jaką krzepnie roztopione jeziorko spawalnicze, jest kluczowym czynnikiem decydującym o ostatecznej mikrostrukturze i właściwościach mechanicznych spoiny. Spawanie laserowe zazwyczaj skutkuje bardzo szybkimi szybkościami chłodzenia ze względu na małą strefę wpływu ciepła i szybkie krzepnięcie roztopionego jeziorka. Szybsze szybkości chłodzenia mogą skutkować drobniejszą mikrostrukturą, co może poprawić wytrzymałość spoiny. Jednak to szybkie chłodzenie może również wprowadzać naprężenia szczątkowe, potencjalnie prowadząc do pękania lub odkształceń w niektórych materiałach, zwłaszcza tych o wysokiej hartowności, takich jak stale wysokowęglowe.
Wolniejsze tempo chłodzenia może zmniejszyć ryzyko pękania, ale może skutkować tworzeniem się większych ziaren, co może zmniejszyć ogólną wytrzymałość spoiny. Zarządzanie tempem chłodzenia jest kluczowe dla zrównoważenia tych czynników. Techniki takie jak obróbka cieplna po spawaniu (np. wyżarzanie) mogą być stosowane w celu złagodzenia naprężeń szczątkowych i poprawy końcowych właściwości materiału.
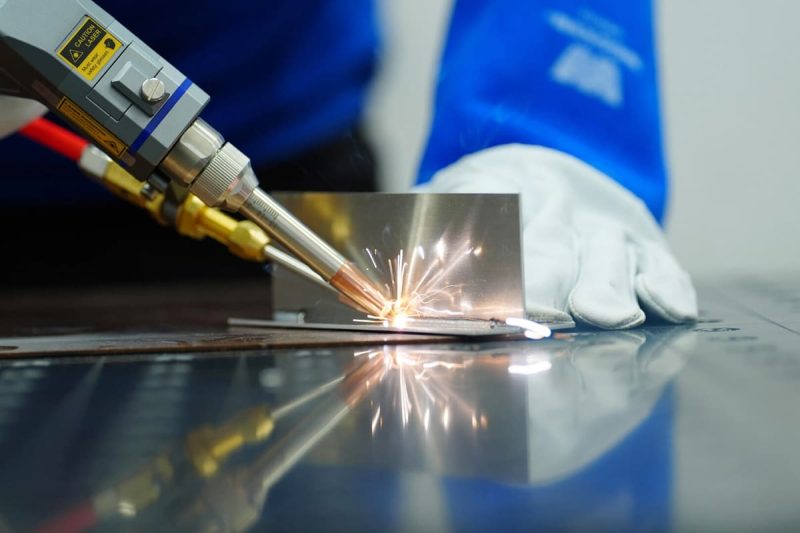
Sprzęt do spawania laserowego i jego konfiguracja
Jakość spoiny laserowej jest w dużym stopniu uzależniona od rodzaju i konfiguracji sprzętu do spawania laserowego. Kluczowe elementy sprzętu obejmują źródło lasera, soczewkę skupiającą, optykę i głowicę spawalniczą.
Typ źródła laserowego
Rodzaj lasera używanego w procesie spawania wpływa na kilka aspektów operacji, w tym jakość wiązki, moc i ostrość. Typowe rodzaje laserów do spawania obejmują lasery CO2, lasery światłowodowe i lasery dyskowe:
- Lasery CO2: Są to najczęściej używane lasery w spawalnictwie przemysłowym ze względu na ich wysoką moc i wszechstronność. Lasery CO2 są idealne do spawania grubszych materiałów i zapewniają stabilną jakość wiązki.
- Lasery światłowodowe: Te lasery są znane z wysokiej jakości wiązki i wydajności, co czyni je szczególnie skutecznymi w spawaniu cienkich blach. Lasery światłowodowe oferują szybsze prędkości spawania i mogą osiągnąć wyższą precyzję niż lasery CO2, szczególnie w przypadku materiałów o niskiej przewodności cieplnej.
Wybór właściwego źródła lasera zależy od rodzaju materiału, jego grubości i wymagań zastosowania.
Soczewka skupiająca i optyka
Wiązka lasera musi być skupiona na obrabianym przedmiocie, aby uzyskać pożądany rozmiar spoiny i penetrację. Jakość i ustawienie soczewki skupiającej i optyki odgrywają kluczową rolę w dokładności wiązki i jakości spoiny. Wysokiej jakości układ optyczny zapewnia, że wiązka lasera pozostaje stabilna i skupiona, co jest szczególnie ważne w przypadku zastosowań wymagających wysokiej precyzji.
Ogniskowa soczewki, rozmiar apertury i położenie soczewki mogą mieć wpływ na sposób rozprowadzania energii na powierzchni materiału. Źle wyrównana optyka może prowadzić do rozogniskowania, co skutkuje niespójnym dostarczaniem energii i potencjalnie słabymi lub wadliwymi spoinami.
Głowica spawalnicza i optyka skupiająca
Głowica spawalnicza odpowiada za kierowanie wiązki lasera na materiał. Ustawienie głowicy spawalniczej, w tym jej położenie, nachylenie i ruch, wpływa na jednorodność i jakość spoiny. Głowica spawalnicza musi być precyzyjnie wyrównana z materiałem, aby zapewnić, że wiązka lasera pozostanie skupiona na połączeniu przez cały proces spawania.
Oprócz głowicy spawalniczej, optyka skupiająca, która kształtuje i kieruje wiązkę, musi być odpowiednio konserwowana i kalibrowana. Wszelkie rozbieżności lub degradacja tej optyki może prowadzić do niespójnego dostarczania wiązki i złej jakości spoiny.
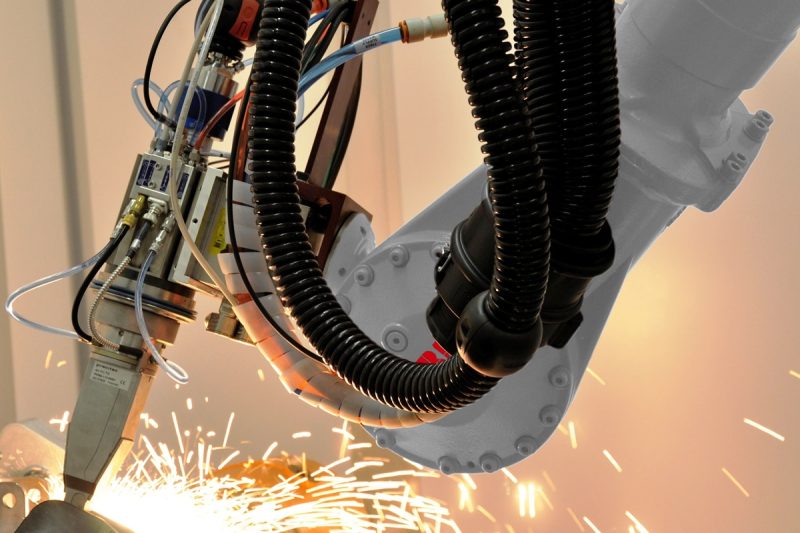
Warunki środowiska
Warunki środowiskowe, w których odbywa się spawanie laserowe, mogą mieć znaczący wpływ na jakość i spójność spoiny. Kluczowe czynniki środowiskowe, które należy wziąć pod uwagę, to temperatura otoczenia i przepływ powietrza.
Temperatura otoczenia
Ekstremalne temperatury mogą wpływać na reakcję materiału na proces spawania laserowego. Na przykład materiały mogą stać się kruche w niskich temperaturach, co może zwiększyć prawdopodobieństwo pękania podczas spawania. Z drugiej strony, wysokie temperatury otoczenia mogą prowadzić do nadmiernego odkształcenia materiału lub rozszerzalności cieplnej, co może mieć wpływ na wyrównanie spoin i spójność spoin. Utrzymanie stabilnej temperatury otoczenia jest kluczowe dla zapewnienia przewidywalnej reakcji materiału na proces spawania.
Przepływ powietrza i zanieczyszczenia
Obecność zanieczyszczeń, takich jak kurz, olej, wilgoć lub opary, może wpływać na proces spawania na kilka sposobów. Zanieczyszczenia w powietrzu mogą absorbować część energii lasera, zmniejszając wydajność procesu. Ponadto zanieczyszczenia na powierzchni materiału mogą prowadzić do utleniania, korozji lub innych wad, które obniżają jakość spoiny.
Kontrola środowiska spawania poprzez odpowiednią wentylację, czyste powierzchnie i zamkniętą komorę spawalniczą może pomóc zredukować ryzyko skażenia i zagwarantować bardziej spójne spoiny.

Obróbka po spawaniu
Po zakończeniu procesu spawania laserowego może być konieczne przeprowadzenie dodatkowej obróbki w celu poprawy właściwości mechanicznych, usunięcia naprężeń szczątkowych i zapewnienia, że spoina spełnia wymagane specyfikacje.
Wyżarzanie
Wyżarzanie to proces obróbki cieplnej, w którym spawany materiał jest podgrzewany do określonej temperatury, a następnie powoli chłodzony. Proces ten jest stosowany w celu złagodzenia naprężeń szczątkowych, które mogły zostać wprowadzone podczas szybkich faz nagrzewania i chłodzenia procesu spawania. Wyżarzanie pomaga przywrócić ciągliwość materiału i zmniejszyć ryzyko pękania.
W spawaniu laserowym materiały, które podlegają szybkim szybkościom chłodzenia, mogą wymagać wyżarzania w celu zapobiegania kruchości i poprawy wytrzymałości spoiny. Dokładna temperatura i czas wyżarzania zależą od rodzaju materiału i konkretnych wymagań spoiny.
Wykończenie powierzchni i czyszczenie
Po spawaniu powierzchnia spoiny może mieć ślady utleniania, zgorzeliny lub inne zanieczyszczenia, które należy usunąć. Czyszczenie i wykańczanie powierzchni spoiny jest niezbędne, aby zapewnić gładki wygląd bez wad i zwiększyć odporność na korozję spawanego obszaru.
Czyszczenie może obejmować techniki takie jak polerowanie mechaniczne, trawienie chemiczne lub obróbka strumieniowo-ścierna. Prawidłowe wykończenie powierzchni jest szczególnie ważne w branżach, w których estetyka spoin i integralność materiału są najważniejsze, np. w urządzeniach medycznych lub elektronice użytkowej.
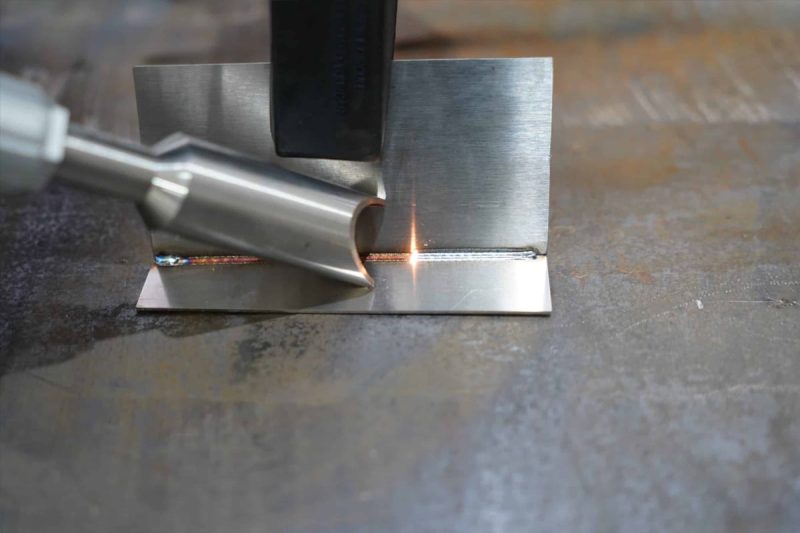
Wyzwania w spawaniu laserowym
Spawanie laserowe oferuje wiele zalet, ale wiąże się również z własnym zestawem wyzwań. Typowe problemy obejmują porowatość, pękanie, odkształcenie i niespójną jakość spoiny.
Porowatość
Porowatość występuje, gdy kieszenie gazowe tworzą się w jeziorku spawalniczym, co prowadzi do powstania pustych przestrzeni w spoinie. Często jest to spowodowane uwięzionymi gazami, takimi jak azot lub tlen, które zostają uwięzione podczas procesu krzepnięcia. Porowatość może osłabić spoinę i wpłynąć na jej wydajność. Prawidłowy gaz osłonowy, staranna kontrola parametrów spawania i zapewnienie czystych powierzchni przed spawaniem mogą pomóc zminimalizować porowatość.
Pękanie i zniekształcenie
Pękanie jest poważnym problemem w spawaniu laserowym, szczególnie w materiałach o wysokiej zawartości węgla lub niskiej ciągliwości. Szybkie tempo chłodzenia podczas spawania laserowego może powodować wysokie naprężenia szczątkowe, które mogą prowadzić do pękania, szczególnie w strefie wpływu ciepła.
Zniekształcenie może również wystąpić z powodu nierównomiernego ogrzewania i chłodzenia, co powoduje odkształcenie lub deformację materiału. Zarządzanie ciepłem wejściowym za pomocą optymalnych parametrów lasera i stosowanie technik zaciskania może pomóc w zmniejszeniu zniekształcenia.
Niespójność w jakości spoin
Niespójna jakość spoiny może wynikać ze zmian właściwości materiału, parametrów lasera lub czynników środowiskowych. Wahania mocy lasera lub ogniska, nieprawidłowe ustawienie połączeń lub zmiany przepływu gazu osłonowego mogą przyczyniać się do niespójnych spoin. Aby zminimalizować te niespójności, konieczne jest zachowanie ścisłej kontroli nad procesem spawania i regularna kalibracja sprzętu w celu zapewnienia jednorodności wszystkich spoin.
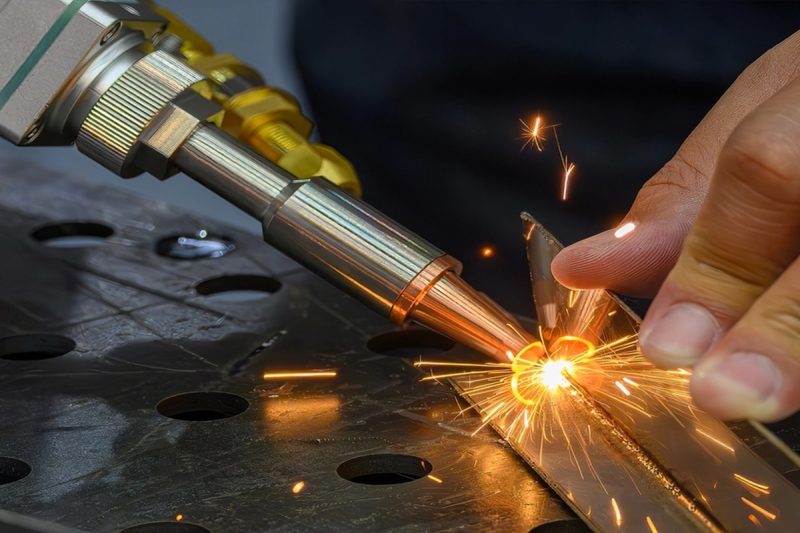
Streszczenie
W spawaniu laserowym spawalność materiałów zależy od szerokiego zakresu czynników, od składu i grubości materiału po parametry lasera i zewnętrzne warunki środowiskowe. Dzięki zrozumieniu tych czynników i ich optymalizacji producenci mogą wytwarzać wysokiej jakości spoiny, które spełniają rygorystyczne wymagania dotyczące wytrzymałości, trwałości i wyglądu. Podczas gdy wyzwania, takie jak porowatość, pękanie i odkształcenia mogą pojawić się podczas procesu spawania, staranna kontrola i dobór parametrów spawania, sprzętu i obróbki po spawaniu mogą złagodzić te problemy i poprawić spójność i niezawodność spawania laserowego w różnych materiałach i zastosowaniach.
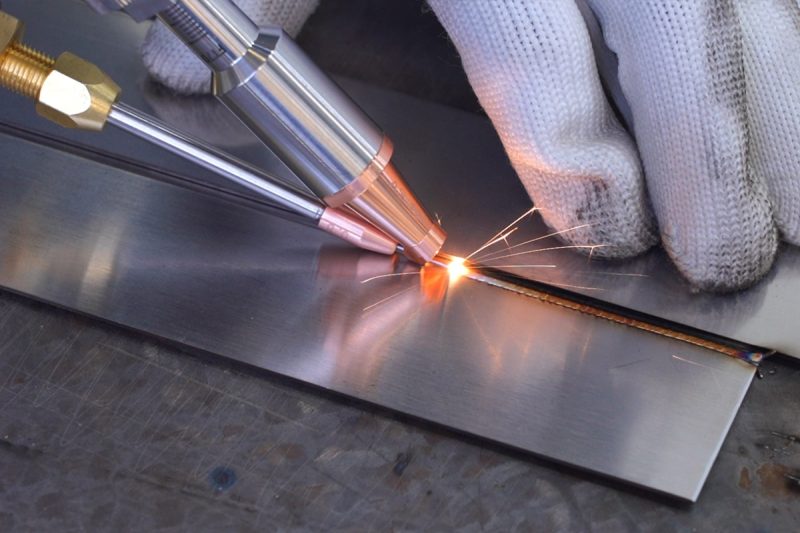
Uzyskaj rozwiązania w zakresie spawania laserowego
Dla firm poszukujących wysokiej jakości, niezawodnych spoin, AccTek Laser oferuje najnowocześniejsze rozwiązania w zakresie spawania laserowego zaprojektowane tak, aby sprostać różnorodnym potrzebom przemysłowym. Jako profesjonalny producent maszyn do cięcia, spawania, czyszczenia i znakowania laserowego, AccTek Laser dostarcza najnowocześniejszy sprzęt dostosowany do optymalizacji spawalności. Niezależnie od tego, czy pracujesz z metalami, tworzywami sztucznymi czy kompozytami, nasze maszyny do spawania laserowego oferują precyzję, szybkość i wydajność nawet w przypadku najbardziej wymagających zastosowań.
Lasery AccTek spawarki laserowe są zaprojektowane do obsługi różnych materiałów i grubości, z konfigurowalnymi ustawieniami mocy lasera, czasu trwania impulsu, ostrości i prędkości spawania, zapewniając, że Twoje spoiny spełniają najwyższe standardy. Nasz zespół ekspertów może pomóc Ci wybrać odpowiedni sprzęt, skonfigurować system zgodnie z Twoimi konkretnymi potrzebami i zaoferować stałe wsparcie, aby zapewnić optymalną wydajność w całym procesie produkcyjnym.
Wybierając AccTek Laser, zyskujesz dostęp do zaawansowanej technologii i partnera, którego celem jest poprawa jakości i wydajności spawania, co ostatecznie pomoże Ci za każdym razem uzyskać idealne, trwałe spoiny.
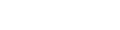
Informacje kontaktowe
- [email protected]
- [email protected]
- +86-19963414011
- Nr 3 Strefa A, strefa przemysłowa Lunzhen, miasto Yucheng, prowincja Shandong.
Uzyskaj rozwiązania laserowe