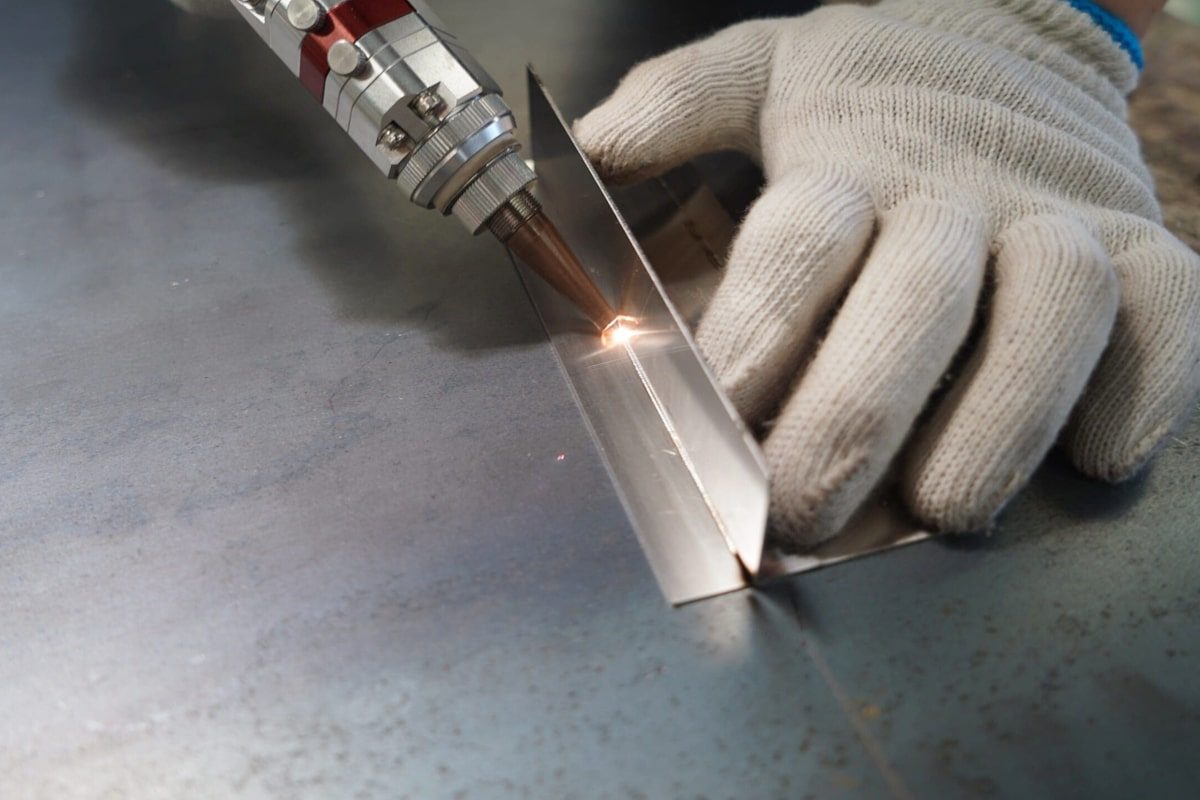
Welche Faktoren beeinflussen die Schweißbarkeit des Laserschweißens?
Das Laserschweißen hat die moderne Fertigung revolutioniert. Es bietet hohe Präzision, minimale Wärmeverformung und die Möglichkeit, Materialien zu verbinden, die mit herkömmlichen Methoden sonst nur schwer zu schweißen sind. Branchen wie die Luft- und Raumfahrt, die Automobilindustrie, die Medizintechnik und die Elektronik verlassen sich stark auf das Laserschweißen, da es schnell ist und hochwertige, starke Verbindungen mit minimaler Nachbehandlung liefert. Trotz der zahlreichen Vorteile des Laserschweißens ist das Erreichen optimaler Schweißbarkeit nicht immer einfach. Der Erfolg einer Laserschweißung wird von einer Vielzahl von Faktoren bestimmt – Materialeigenschaften, Laserparameter, Gerätekonfiguration, Umgebungsbedingungen und Nachbehandlung – die alle sorgfältig kontrolliert werden müssen, um die Herstellung einer starken, langlebigen und fehlerfreien Schweißnaht zu gewährleisten.
In diesem Artikel untersuchen wir ausführlich die verschiedenen Faktoren, die die Schweißbarkeit von Materialien beim Laserschweißen beeinflussen. Zu diesen Faktoren gehören die Zusammensetzung des Grundmaterials, die Geometrie der Verbindung, die Laserleistung, Geschwindigkeit und Strahlqualität sowie externe Umgebungsfaktoren wie Temperatur und Verunreinigungen. Wir untersuchen auch häufige Herausforderungen beim Laserschweißen und wie diese gemildert werden können, um die höchstmögliche Schweißqualität zu erzielen. Am Ende dieses Artikels verfügen die Leser über ein umfassendes Verständnis der zahlreichen Variablen beim Laserschweißen und wissen, wie diese Faktoren für hervorragende Schweißergebnisse optimiert werden können.
Inhaltsverzeichnis
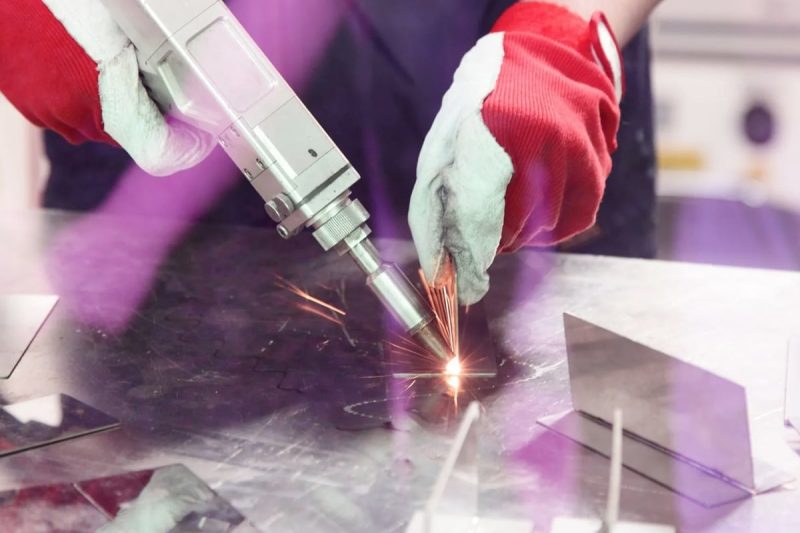
Einführung in das Laserschweißen
Definition und Übersicht
Laserschweißen ist eine Präzisionsschweißtechnik, bei der ein hochkonzentrierter Laserstrahl zum Schmelzen und Verschmelzen von Materialien, normalerweise Metallen oder Thermoplasten, verwendet wird. Der von einer Laserquelle erzeugte Laserstrahl richtet fokussierte Energie auf das Material und erzeugt eine lokalisierte Wärmezone, die das Grundmaterial an der Verbindungsstelle schmilzt. Wenn das geschmolzene Material erstarrt, bildet es eine Schweißnaht. Dieser Prozess kann entweder mit Dauerstrichlasern (CW) durchgeführt werden, die gleichmäßige Wärme liefern, oder mit gepulsten Lasern, die Energie in kurzen Stößen abgeben, oft um eine Überhitzung zu verhindern und ein kontrolliertes Eindringen zu gewährleisten.
Laserschweißen ist äußerst vielseitig und kann für eine Reihe von Materialarten und -stärken verwendet werden. Es bietet zahlreiche Vorteile, darunter hohe Schweißgeschwindigkeiten, schmale Wärmeeinflusszonen (WEZ), minimale Materialverzerrungen und die Möglichkeit, den Prozess zu automatisieren, was zu einer höheren Produktionseffizienz führt. Die Präzision des Laserstrahls ermöglicht das Schweißen in engen Räumen und an empfindlichen Bauteilen, wodurch sich das Laserschweißen ideal für hochpräzise Anwendungen eignet, einschließlich der Luft- und Raumfahrt- und Elektronikindustrie.
Bedeutung der Schweißbarkeit beim Laserschweißen
Schweißbarkeit beim Laserschweißen bezeichnet die Fähigkeit eines Materials, beim Laserschweißen eine feste, fehlerfreie Verbindung zu bilden. Das Erreichen der Schweißbarkeit hängt von mehreren miteinander verbundenen Faktoren ab, wie etwa der chemischen Zusammensetzung des Materials, den thermischen Eigenschaften, der Verbindungskonstruktion und seiner Reaktion auf die lokale Wärmezufuhr durch den Laserstrahl. Wenn diese Faktoren nicht optimiert werden, kann die Schweißverbindung anfällig für Fehler wie Porosität, Rissbildung, Verformung oder schwache Bindung sein.
Das Konzept der Schweißbarkeit ist beim Laserschweißen besonders wichtig, da die hohe Energiekonzentration des Laserstrahls erhebliche Auswirkungen auf die Mikrostruktur und die mechanischen Eigenschaften des Materials haben kann. So können beispielsweise schnelle Heiz- und Kühlzyklen bei bestimmten Materialien zu Problemen wie Eigenspannungen, Rissbildung oder unerwünschten Phasenumwandlungen führen. Um diese Herausforderungen zu bewältigen, müssen Hersteller die verschiedenen beim Laserschweißen beteiligten Parameter sorgfältig auswählen und kontrollieren.
Vergleich mit herkömmlichen Schweißverfahren
Obwohl das Laserschweißen für seine Präzision und Effizienz bekannt ist, unterscheidet es sich in mehreren wichtigen Punkten erheblich von herkömmlichen Schweißverfahren wie MIG-Schweißen (Metall-Inertgasschweißen) oder WIG-Schweißen (Wolfram-Inertgasschweißen). Bei herkömmlichen Schweißverfahren wird Wärme durch Lichtbögen erzeugt, wodurch ein größerer Bereich des Materials erhitzt wird und im Allgemeinen breitere Wärmeeinflusszonen entstehen. Diese Verfahren führen außerdem tendenziell zu langsameren Schweißgeschwindigkeiten und stärkerer Materialverzerrung. Das Laserschweißen hingegen zeichnet sich durch einen hochkonzentrierten Energiestrahl aus, der schnellere Schweißgeschwindigkeiten, schmalere Wärmeeinflusszonen und minimale Verzerrungen ermöglicht.
Allerdings reagiert das Laserschweißen empfindlicher auf Änderungen der Materialeigenschaften, der Fugenkonstruktion und der Lasereinstellungen als herkömmliche Verfahren. Beispielsweise können herkömmliche Verfahren beim Schweißen dickerer Materialien oder von Fugen mit unregelmäßiger Geometrie nachsichtiger sein, während beim Laserschweißen eine präzisere Kontrolle von Parametern wie Laserleistung, Strahlfokus und Schweißgeschwindigkeit erforderlich ist. Daher ist das Laserschweißen möglicherweise nicht für alle Anwendungen die ideale Lösung, insbesondere bei Materialien oder Geometrien, die für den Prozess eine Herausforderung darstellen.
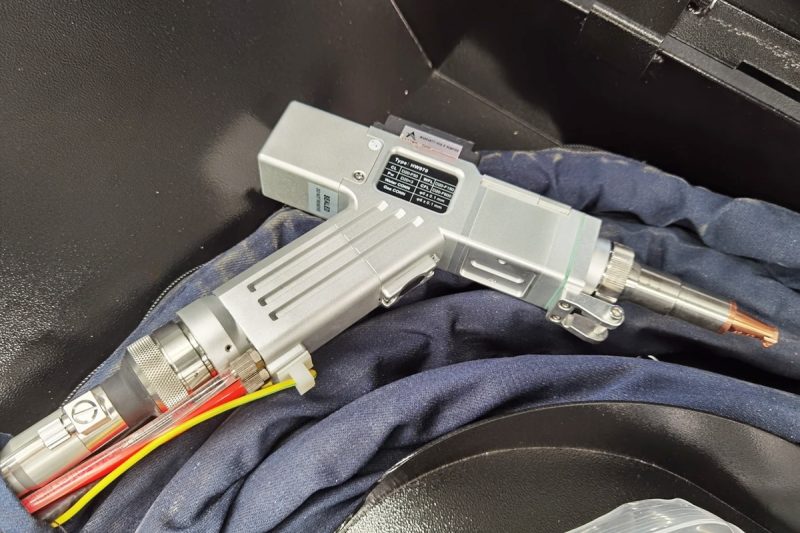
Materialeigenschaften
Das zu schweißende Material spielt eine entscheidende Rolle für den Erfolg eines Laserschweißvorgangs. Wichtige Materialeigenschaften, die die Schweißbarkeit beeinflussen, sind die Zusammensetzung des Grundmaterials, Dicke und Geometrie, Schmelzpunkt, Wärmeleitfähigkeit und das Vorhandensein von Legierungselementen oder Zusatzstoffen.
Zusammensetzung des Grundmaterials
Die chemische Zusammensetzung des Grundmaterials ist einer der wichtigsten Faktoren, die die Schweißbarkeit beeinflussen. Unterschiedliche Materialien haben unterschiedliche Schmelzpunkte, Wärmeleitfähigkeiten und Erstarrungsverhalten, die alle den Laserschweißprozess beeinflussen. Beispielsweise neigen kohlenstoffreiche Stähle dazu, beim Abkühlen harte und spröde Phasen zu bilden, was die Wahrscheinlichkeit von Rissen in der Schweißnaht erhöht. Ebenso können Materialien mit hohen Anteilen bestimmter Legierungselemente wie Chrom, Nickel oder Molybdän anfälliger für Phasenumwandlungen sein, die zu Schweißfehlern oder verminderten mechanischen Eigenschaften führen können.
Einige Materialien, wie beispielsweise Aluminium Und Kupfer, sind aufgrund ihrer hohen Wärmeleitfähigkeit und niedrigen Schmelzpunkte besonders schwierig mit dem Laserschweißen zu schweißen. Diese Materialien erfordern eine höhere Laserleistung, um eine ausreichende Durchdringung zu erreichen, aber auch das Risiko eines Durchbrennens ist viel höher. Materialien mit einem hohen Ausdehnungskoeffizienten, wie Titanlegierungen, können beim Schweißen thermische Verformungen aufweisen, was eine genaue Kontrolle der Laserparameter erfordert.
Um die optimalen Laserparameter bestimmen zu können, ist es wichtig, die Zusammensetzung des zu schweißenden Materials zu kennen. Die Legierungselemente und Verunreinigungen im Material können Einfluss darauf haben, wie das Material auf Hitze reagiert und wie sich die Schweißnaht bildet. Daher müssen Parameter wie Laserleistung, Strahlfokus und Schutzgas angepasst werden.
Dicke und Geometrie
Materialdicke und Fugengeometrie wirken sich direkt auf die zum Schweißen erforderliche Energie und die Wärmeverteilung im Material aus. Bei dünnen Materialien reicht im Allgemeinen eine geringere Laserleistung aus, es ist jedoch eine sorgfältige Kontrolle erforderlich, um eine übermäßige Wärmezufuhr zu vermeiden, die zu einem Durchbrennen führen könnte. Bei dickeren Materialien sind eine höhere Laserleistung und langsamere Schweißgeschwindigkeiten erforderlich, um eine vollständige Durchdringung und eine einwandfreie Schweißnaht zu gewährleisten.
Auch die Geometrie der Verbindung beeinflusst, wie der Laser mit dem Material interagiert. Einfache Stumpfstöße sind relativ leicht zu schweißen, da sie eine direkte Verbindung zwischen den beiden Oberflächen herstellen. Komplexere Verbindungen wie T-Stöße, Kehlnähte oder Überlappstöße erfordern jedoch möglicherweise besondere Aufmerksamkeit. Der Winkel und die Ausrichtung der Verbindung beeinflussen die Fähigkeit des Lasers, die Materialien richtig zu durchdringen und zu verschmelzen.
Materialien mit komplexen Geometrien können beim Laserschweißen zusätzliche Herausforderungen mit sich bringen, da es schwierig ist, den Strahl auf die Verbindung auszurichten, und es entlang der Verbindung zu Dickenunterschieden kommt. Die Optimierung des Verbindungsdesigns und die Sicherstellung der richtigen Ausrichtung des Laserstrahls sind entscheidende Schritte zum Erreichen starker, qualitativ hochwertiger Schweißnähte.
Schmelzpunkt und Wärmeleitfähigkeit
Der Schmelzpunkt eines Materials bestimmt, wie viel Energie zum Schmelzen erforderlich ist. Materialien mit hohen Schmelzpunkten, wie Wolfram, Titan oder hochlegierte Stähle, benötigen erheblich mehr Energie, um ihren Schmelzpunkt zu erreichen, und erfordern eine sorgfältige Steuerung der Laserleistung. Materialien mit niedrigen Schmelzpunkten, wie Aluminium oder Zink, können dagegen unter einem Laserstrahl zu leicht schmelzen und erfordern möglicherweise hohe Schweißgeschwindigkeiten oder gepulste Lasertechniken, um ein übermäßiges Durchschmelzen zu verhindern.
Die Wärmeleitfähigkeit – die Fähigkeit eines Materials, Wärme zu leiten – beeinflusst auch die Schweißbarkeit. Materialien mit hoher Wärmeleitfähigkeit, wie Kupfer, leiten Wärme schnell ab, was bedeutet, dass der Laserstrahl ausreichend Energie liefern muss, um diesen Wärmeverlust auszugleichen und eine ausreichende Durchdringung zu erreichen. Materialien mit geringer Wärmeleitfähigkeit, wie z. B. Edelstahl, speichern Wärme effektiver, was bei unsachgemäßer Handhabung zu einer größeren Wärmeeinflusszone (WEZ) und potenzieller thermischer Verzerrung führen kann.
Legierungselemente und Additive
Das Vorhandensein von Legierungselementen und Zusatzstoffen kann die Schweißbarkeit eines Materials erheblich beeinflussen. Gängige Legierungselemente wie Mangan, Silizium und Chrom können die mechanischen Eigenschaften eines Materials verbessern, können aber beim Schweißen auch Probleme bereiten. Beispielsweise kann Mangan die Schweißnaht anfälliger für Risse machen, während übermäßiges Silizium zur Bildung spröder Phasen in der Schweißzone führen kann.
Additive wie Flussmittel können verwendet werden, um die Oberflächenhaftung zu verbessern, Oxidation zu verhindern oder das Verhalten des Schweißbads zu verändern. Die Auswahl von Flussmitteln und anderen Additiven sollte sorgfältig erfolgen, da sie die endgültige Qualität und die mechanischen Eigenschaften der Schweißnaht beeinflussen können.
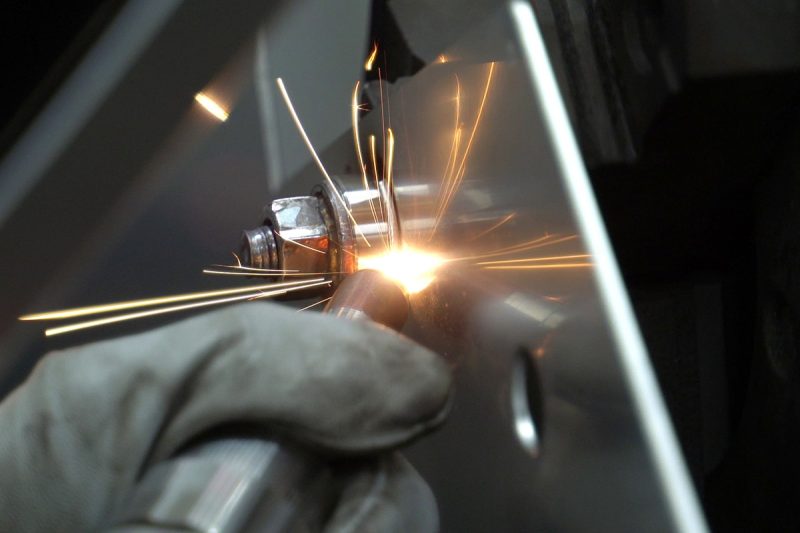
Laserparameter
Die Laserparameter, darunter Laserleistung, Fokus, Geschwindigkeit, Strahlqualität und andere, sind für die Schweißbarkeit von Materialien von grundlegender Bedeutung. Diese Parameter steuern, wie der Laserstrahl mit dem Material interagiert, welche Energie in das Schweißbad abgegeben wird und wie schnell das Material erstarrt.
Laserleistung
Die Laserleistung beeinflusst direkt die Eindringtiefe, die Schweißgeschwindigkeit und die während des Prozesses erzeugte Wärmemenge. Eine höhere Laserleistung führt zu einer tieferen Eindringtiefe, erhöht jedoch auch das Risiko von Durchbrennungen oder übermäßig wärmebeeinflussten Zonen. Niedrigere Leistungseinstellungen liefern möglicherweise nicht genügend Energie, um bei dickeren Materialien eine vollständige Eindringtiefe zu erreichen, was zu schwachen Verbindungen oder unvollständiger Verschmelzung führt.
Die optimale Laserleistungseinstellung hängt vom zu schweißenden Material, seiner Dicke und den gewünschten Schweißeigenschaften ab. Generell muss ein Gleichgewicht zwischen ausreichender Leistung zum Schmelzen des Materials und der Vermeidung übermäßiger Hitze, die das Werkstück verformen könnte, gefunden werden.
Laserfokus
Der Laserfokus steuert die Größe und Intensität des Laserstrahls. Ein eng fokussierter Strahl erzeugt einen kleinen, energiereichen Punkt auf dem Material, der eine tiefere Durchdringung und schmalere Schweißnähte ermöglicht. Ein zu enger Fokus kann jedoch das Risiko eines Durchbrennens erhöhen, insbesondere bei dünneren Materialien. Im Gegensatz dazu verteilt ein defokussierter Strahl die Energie über einen größeren Bereich, wodurch das Risiko eines Durchbrennens verringert wird, aber auch eine flachere Durchdringung und breitere Schweißnähte entstehen.
Der optimale Fokus hängt vom Material, der Dicke und der Geometrie der Verbindung ab. Zur präzisen Steuerung verfügen Lasersysteme normalerweise über einen einstellbaren Fokus, sodass der Bediener den Strahl entsprechend den spezifischen Schweißanforderungen fein abstimmen kann.
Impulsdauer
Beim gepulsten Laserschweißen wird der Laserstrahl in kurzen, intensiven Energiestößen abgegeben. Die Dauer dieser Impulse – die Impulsdauer – kann die Eindringtiefe, die Abkühlrate und die Gesamtqualität der Schweißnaht erheblich beeinflussen. Kürzere Impulse ermöglichen eine kontrolliertere Energiezufuhr und können dazu beitragen, eine Überhitzung zu verhindern, während längere Impulse mehr Energie für eine tiefere Durchdringung liefern.
Die Impulsdauer muss sorgfältig auf das zu schweißende Material und die Schweißdicke abgestimmt werden. Längere Impulse werden typischerweise für dickere Materialien verwendet, während kürzere Impulse für dünne Materialien verwendet werden, um thermische Verformungen zu vermeiden.
Strahlqualität
Die Strahlqualität bezeichnet die Energieverteilung innerhalb des Laserstrahls und ist ein wesentlicher Faktor, der bestimmt, wie effektiv der Laser auf das Material fokussiert werden kann. Ein qualitativ hochwertiger Strahl hat ein gleichmäßiges Energieprofil, was eine konstante Energieabgabe und eine stabilere Schweißnaht ermöglicht. Strahlen von geringer Qualität hingegen können zu einer ungleichmäßigen Energieverteilung führen, was wiederum eine schlechte Schweißnahtqualität und eine inkonsistente Fugenbildung zur Folge hat.
Laserschweißsysteme mit hoher Strahlqualität erzeugen typischerweise sauberere, präzisere Schweißnähte mit weniger Defekten.
Schweißgeschwindigkeit
Die Schweißgeschwindigkeit beeinflusst die Zeit, in der der Laser auf das Material einwirkt. Schnellere Schweißgeschwindigkeiten führen normalerweise zu einer geringeren Wärmezufuhr, was zu kleineren Wärmeeinflusszonen und geringerer Verformung führt. Wenn die Geschwindigkeit jedoch zu hoch ist, bleibt möglicherweise nicht genügend Zeit für eine ordnungsgemäße Durchdringung, was zu schwachen Verbindungen führt. Niedrigere Geschwindigkeiten können die Wärmezufuhr erhöhen, was zu größeren Wärmeeinflusszonen und möglicherweise mehr Verformung führt, sie können jedoch zum Schweißen dickerer Materialien erforderlich sein.
Die optimale Schweißgeschwindigkeit wird durch Materialart, Dicke und gewünschte Schweißeigenschaften bestimmt.
Schutzgas
Schutzgas wird beim Laserschweißen verwendet, um das Schweißbad vor Verunreinigungen durch die umgebende Atmosphäre zu schützen, die zu Oxidation oder anderen Defekten führen könnten. Die Art des verwendeten Schutzgases, beispielsweise Argon, Stickstoff oder eine Gasmischung, kann die Qualität der Schweißnaht, einschließlich ihrer Festigkeit, ihres Aussehens und ihrer Korrosionsbeständigkeit, beeinflussen. Darüber hinaus kann Schutzgas die Wärmeableitung und Abkühlungsrate des Schweißbades beeinflussen, was wiederum die Mikrostruktur der Schweißnaht beeinflusst.
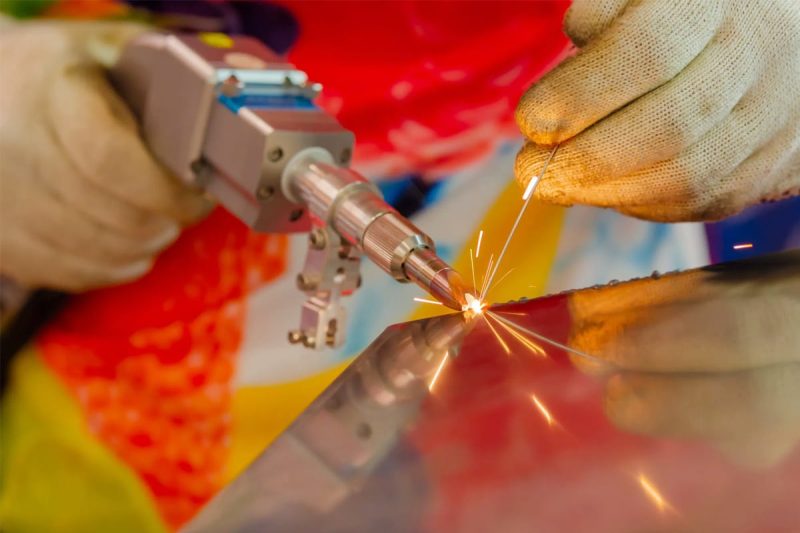
Materialstärke und Fugengestaltung
Beim Laserschweißen haben Materialdicke und Fugengeometrie erhebliche Auswirkungen auf den Schweißprozess, den Energiebedarf und letztlich auf die Qualität der Schweißnaht. Ein tiefes Verständnis dieser Faktoren ist entscheidend, um optimale Schweißnähte mit minimalen Defekten zu erzielen.
Materialstärke
Die Dicke des zu schweißenden Materials hat direkte Auswirkungen auf den Laserschweißprozess. Dickere Materialien erfordern eine höhere Laserleistung, um eine vollständige Durchdringung zu erreichen und eine starke Verbindung herzustellen. Beim Schweißen dickerer Materialien muss die Wärmezufuhr sorgfältig gesteuert werden, um Überhitzung und Verformung zu vermeiden. Eine höhere Leistungseinstellung ermöglicht eine tiefere Durchdringung, kann aber auch die Größe der Wärmeeinflusszone (WEZ) vergrößern, was die mechanischen Eigenschaften des Grundmaterials beeinträchtigen kann.
Bei dünnen Materialien wird normalerweise eine geringere Laserleistung verwendet, um ein Durchbrennen zu vermeiden, da diese Materialien weniger Energie zum Schmelzen benötigen. Die größte Herausforderung beim Schweißen dünner Materialien mit einem Laser besteht darin, die Laserleistung so auszubalancieren, dass eine übermäßige Wärmezufuhr vermieden wird und gleichzeitig eine ausreichende Durchdringung erreicht wird, ohne das Material zu beschädigen. Die schnelle Abkühlrate beim Laserschweißen trägt dazu bei, die Wärmeeinflusszone bei dünneren Materialien zu minimieren.
Gelenkgeometrie
Die Geometrie der Verbindung – wie Stumpfstöße, T-Stöße, Überlappstöße und Kehlnähte – spielt eine entscheidende Rolle für den Erfolg einer Laserschweißung. Laserschweißen funktioniert normalerweise am besten mit Stumpfstößen, da die direkte Ausrichtung der Materialkanten ein gleichmäßiges Schweißbad gewährleistet. Komplexere Verbindungen wie Überlappstöße oder T-Stöße erfordern jedoch eine sorgfältige Strahlausrichtung, da der Laser eine Durchdringung auf allen Seiten der Verbindung sicherstellen muss, einschließlich aller Lücken, die zwischen den Materialien vorhanden sein können.
Wenn die Verbindungsgeometrie komplexe Formen oder Unterschiede in der Materialstärke aufweist, müssen die Schweißparameter angepasst werden. Überlappverbindungen erfordern beispielsweise eine präzise Steuerung des Laserfokus und des Strahlwinkels, um sicherzustellen, dass das obere Material effektiv mit dem unteren Material verschmilzt. Bei Kehlnähten muss die Wechselwirkung des Laserstrahls mit den Verbindungsoberflächen ebenfalls sorgfältig kontrolliert werden, da Winkel und Materialnähe die Wärmeverteilung beeinflussen können.
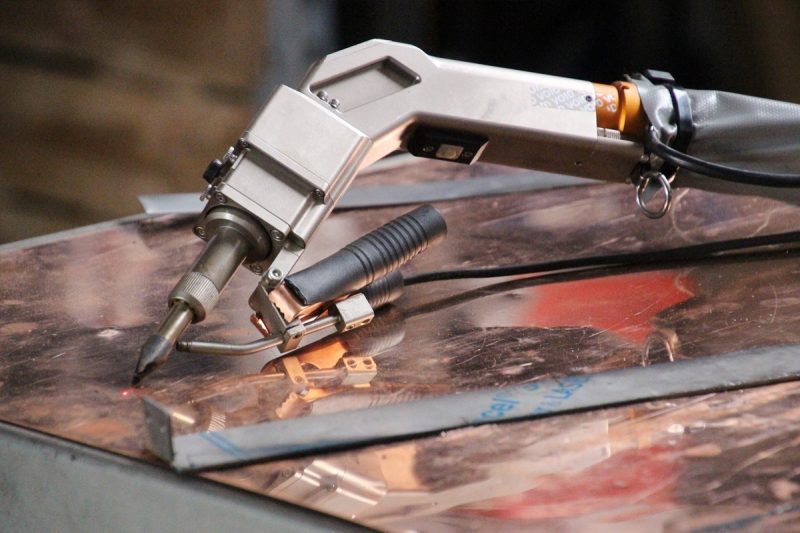
Wärmemanagement und Kühlrate
Effektives Wärmemanagement ist beim Laserschweißen entscheidend, um Materialeigenschaften zu kontrollieren, Verformungen zu minimieren und Schweißfehler zu vermeiden. Wichtige Aspekte des Wärmemanagements sind die Wärmeeinflusszone (WEZ) und die Abkühlrate.
Wärmeeinflusszone (HAZ)
Die Wärmeeinflusszone (WEZ) ist der Bereich des Materials, der nicht schmilzt, dessen Mikrostruktur sich jedoch aufgrund der hohen Temperaturen beim Schweißen ändert. Größe und Ausmaß der WEZ werden durch Laserleistung, Schweißgeschwindigkeit und Materialart bestimmt. Beim Laserschweißen ist die WEZ im Vergleich zu herkömmlichen Schweißverfahren aufgrund der konzentrierten Hitze des Laserstrahls tendenziell kleiner. Selbst eine kleine WEZ kann jedoch die Materialeigenschaften beeinträchtigen, insbesondere bei hochfestem Stahl oder Materialien, die empfindlich auf thermische Zyklen reagieren.
Für bestimmte Materialien, wie z. B. Kohlenstoffstähle oder Titanlegierungen kann eine größere WEZ zu verringerten mechanischen Eigenschaften wie Sprödigkeit oder Spannungsrisskorrosion führen. Daher ist eine sorgfältige Kontrolle der Laserparameter, insbesondere der Leistung und Geschwindigkeit, unerlässlich, um die WEZ zu minimieren und dennoch eine ausreichende Verschmelzung an der Verbindungsstelle zu erreichen.
Abkühlungsrate
Die Abkühlrate, also die Geschwindigkeit, mit der das geschmolzene Schweißbad erstarrt, ist ein entscheidender Faktor für die endgültige Mikrostruktur und die mechanischen Eigenschaften der Schweißnaht. Beim Laserschweißen sind die Abkühlraten aufgrund der kleinen Wärmeeinflusszone und der schnellen Erstarrung des geschmolzenen Bades normalerweise sehr hoch. Schnellere Abkühlraten können zu einer feineren Mikrostruktur führen, die die Festigkeit der Schweißnaht verbessern kann. Diese schnelle Abkühlung kann jedoch auch zu Eigenspannungen führen, die möglicherweise zu Rissen oder Verformungen bei bestimmten Materialien führen, insbesondere bei solchen mit hoher Härtbarkeit, wie z. B. Kohlenstoffstählen.
Eine langsamere Abkühlgeschwindigkeit kann zwar das Rissrisiko verringern, kann aber zur Bildung größerer Körner führen, die die Gesamtfestigkeit der Schweißnaht verringern können. Die Steuerung der Abkühlgeschwindigkeit ist für die Balance dieser Faktoren von entscheidender Bedeutung. Techniken wie Wärmebehandlung nach dem Schweißen (z. B. Glühen) können eingesetzt werden, um Restspannungen abzubauen und die endgültigen Materialeigenschaften zu verbessern.
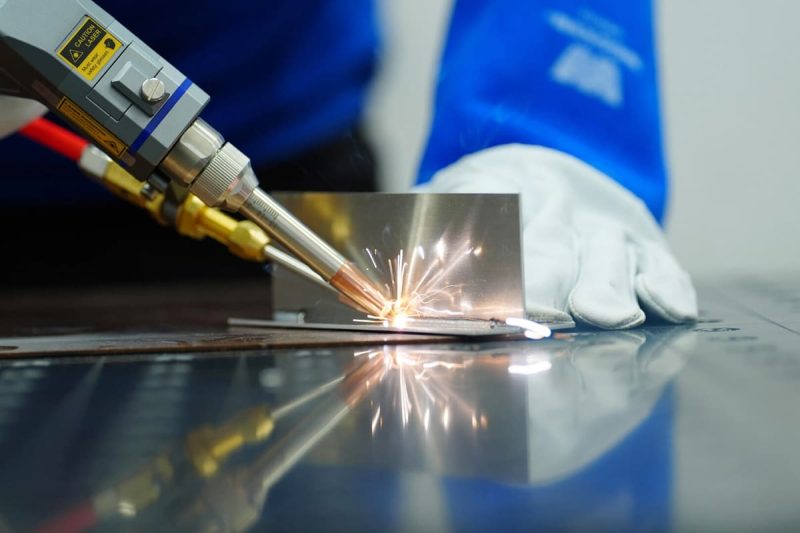
Laserschweißausrüstung und -einrichtung
Die Qualität der Laserschweißung wird stark von der Art und Konfiguration der Laserschweißanlage beeinflusst. Zu den wichtigsten Komponenten der Anlage gehören die Laserquelle, die Fokussierlinse, die Optik und der Schweißkopf.
Laserquellentyp
Der beim Schweißen verwendete Lasertyp beeinflusst mehrere Aspekte des Vorgangs, darunter Strahlqualität, Leistung und Fokus. Zu den üblichen Lasertypen zum Schweißen gehören CO2-Laser, Faserlaser und Scheibenlaser:
- CO2-Laser: Aufgrund ihrer hohen Leistung und Vielseitigkeit sind dies die am häufigsten verwendeten Laser beim industriellen Schweißen. CO2-Laser sind ideal zum Schweißen dickerer Materialien und bieten eine stabile Strahlqualität.
- Faserlaser: Diese Laser sind für ihre hohe Strahlqualität und Effizienz bekannt, was sie besonders effektiv für das Schweißen dünner Bleche macht. Faserlaser bieten höhere Schweißgeschwindigkeiten und können eine höhere Präzision als CO2-Laser erreichen, insbesondere bei Materialien mit geringer Wärmeleitfähigkeit.
Die Wahl der richtigen Laserquelle hängt von Materialart, Dicke und Anwendungsanforderungen ab.
Fokussierlinse und Optik
Der Laserstrahl muss auf das Werkstück fokussiert werden, um die gewünschte Schweißnahtgröße und -durchdringung zu erreichen. Die Qualität und Ausrichtung der Fokussierlinse und der Optik spielen eine entscheidende Rolle für die Strahlgenauigkeit und Schweißnahtqualität. Ein hochwertiges optisches System stellt sicher, dass der Laserstrahl stabil und fokussiert bleibt, was besonders bei hochpräzisen Anwendungen wichtig ist.
Die Brennweite der Linse, die Blendengröße und die Positionierung der Linse können Einfluss darauf haben, wie die Energie über die Oberfläche des Materials verteilt wird. Eine schlecht ausgerichtete Optik kann zu einer Defokussierung führen, was wiederum eine ungleichmäßige Energieabgabe und möglicherweise schwache oder fehlerhafte Schweißnähte zur Folge hat.
Schweißkopf und Fokussieroptik
Der Schweißkopf ist dafür verantwortlich, den Laserstrahl auf das Material zu richten. Die Einstellung des Schweißkopfes, einschließlich seiner Position, Neigung und Bewegung, wirkt sich auf die Gleichmäßigkeit und Qualität der Schweißnaht aus. Der Schweißkopf muss präzise auf das Material ausgerichtet sein, um sicherzustellen, dass der Laserstrahl während des gesamten Schweißvorgangs auf die Verbindung fokussiert bleibt.
Neben dem Schweißkopf muss auch die Fokussieroptik, die den Strahl formt und lenkt, ordnungsgemäß gewartet und kalibriert werden. Jede Fehlausrichtung oder Verschlechterung dieser Optik kann zu einer inkonsistenten Strahlabgabe und schlechter Schweißqualität führen.
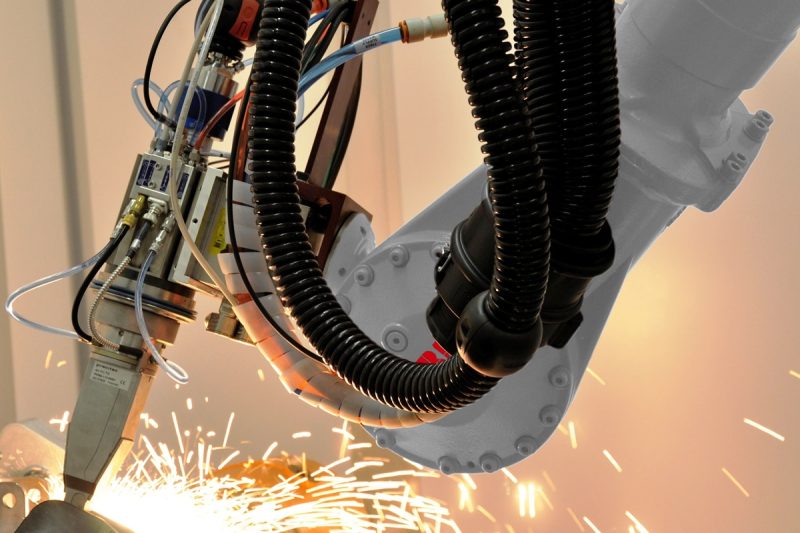
Umweltbedingungen
Die Umgebungsbedingungen, unter denen das Laserschweißen stattfindet, können einen erheblichen Einfluss auf die Qualität und Konsistenz der Schweißnaht haben. Zu den wichtigsten zu berücksichtigenden Umgebungsfaktoren gehören Umgebungstemperatur und Luftstrom.
Umgebungstemperatur
Extreme Temperaturen können die Reaktion des Materials auf den Laserschweißprozess beeinflussen. Beispielsweise können Materialien bei niedrigen Temperaturen spröde werden, was die Wahrscheinlichkeit von Rissen während des Schweißens erhöhen kann. Umgekehrt können hohe Umgebungstemperaturen zu übermäßiger Materialverformung oder Wärmeausdehnung führen, was die Fugenausrichtung und die Schweißnahtkonsistenz beeinträchtigen kann. Die Aufrechterhaltung einer stabilen Umgebungstemperatur ist entscheidend, um sicherzustellen, dass das Material vorhersehbar auf den Schweißprozess reagiert.
Luftstrom und Schadstoffe
Das Vorhandensein von Verunreinigungen wie Staub, Öl, Feuchtigkeit oder Rauch kann den Schweißprozess auf verschiedene Weise beeinträchtigen. Verunreinigungen in der Luft können einen Teil der Laserenergie absorbieren und so die Effizienz des Prozesses verringern. Darüber hinaus können Verunreinigungen auf der Materialoberfläche zu Oxidation, Korrosion oder anderen Defekten führen, die die Qualität der Schweißnaht beeinträchtigen.
Die Kontrolle der Schweißumgebung durch entsprechende Belüftung, saubere Oberflächen und eine geschlossene Schweißkammer kann dazu beitragen, das Kontaminationsrisiko zu verringern und gleichmäßigere Schweißnähte sicherzustellen.

Nachbehandlung nach dem Schweißen
Sobald der Laserschweißvorgang abgeschlossen ist, können Nachbehandlungen erforderlich sein, um die mechanischen Eigenschaften zu verbessern, Restspannungen abzubauen und sicherzustellen, dass die Schweißnaht den erforderlichen Spezifikationen entspricht.
Glühen
Glühen ist ein Wärmebehandlungsprozess, bei dem das geschweißte Material auf eine bestimmte Temperatur erhitzt und dann langsam abgekühlt wird. Dieser Prozess wird verwendet, um Restspannungen abzubauen, die während der schnellen Aufheiz- und Abkühlphasen des Schweißprozesses entstanden sein können. Durch das Glühen wird die Duktilität des Materials wiederhergestellt und das Risiko von Rissen verringert.
Beim Laserschweißen müssen Materialien, die schnell abkühlen, möglicherweise geglüht werden, um Versprödung zu verhindern und die Schweißzähigkeit zu verbessern. Die genaue Glühtemperatur und -dauer hängen vom Materialtyp und den spezifischen Anforderungen der Schweißnaht ab.
Oberflächenbeschaffenheit und Reinigung
Nach dem Schweißen kann die Oberfläche der Schweißnaht Oxidation, Zunder oder andere Verunreinigungen aufweisen, die entfernt werden müssen. Das Reinigen und Nachbearbeiten der Schweißnahtoberfläche ist wichtig, um ein glattes, fehlerfreies Erscheinungsbild zu gewährleisten und die Korrosionsbeständigkeit des Schweißbereichs zu verbessern.
Zum Reinigen können Techniken wie mechanisches Polieren, chemisches Beizen oder Strahlen verwendet werden. Eine gute Oberflächenbeschaffenheit ist besonders in Branchen wichtig, in denen die Ästhetik der Schweißnähte und die Materialintegrität von größter Bedeutung sind, wie etwa bei medizinischen Geräten oder Unterhaltungselektronik.
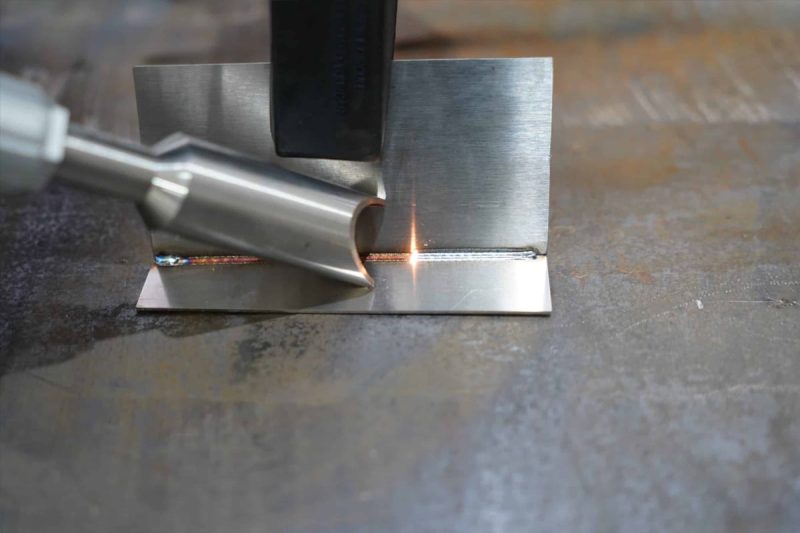
Herausforderungen beim Laserschweißen
Obwohl das Laserschweißen viele Vorteile bietet, bringt es auch seine eigenen Herausforderungen mit sich. Häufige Probleme sind Porosität, Risse, Verformungen und inkonsistente Schweißqualität.
Porosität
Porosität entsteht, wenn sich im Schweißbad Gaseinschlüsse bilden, die zu Hohlräumen in der Schweißnaht führen. Dies wird häufig durch eingeschlossene Gase wie Stickstoff oder Sauerstoff verursacht, die während des Erstarrungsprozesses eingeschlossen werden. Porosität kann die Schweißnaht schwächen und ihre Leistung beeinträchtigen. Das richtige Schutzgas, die sorgfältige Kontrolle der Schweißparameter und die Gewährleistung sauberer Oberflächen vor dem Schweißen können dazu beitragen, Porosität zu minimieren.
Rissbildung und Verformung
Rissbildung ist ein erhebliches Problem beim Laserschweißen, insbesondere bei Materialien mit hohem Kohlenstoffgehalt oder geringer Duktilität. Die schnellen Abkühlungsraten beim Laserschweißen können hohe Eigenspannungen erzeugen, die insbesondere in der Wärmeeinflusszone zu Rissbildung führen können.
Auch durch ungleichmäßiges Erhitzen und Abkühlen kann es zu Verformungen kommen, die das Material verziehen oder deformieren. Die Steuerung der Wärmezufuhr durch optimale Laserparameter und den Einsatz von Klemmtechniken kann zur Reduzierung von Verformungen beitragen.
Inkonsistenz der Schweißqualität
Eine inkonsistente Schweißqualität kann durch Abweichungen bei Materialeigenschaften, Laserparametern oder Umgebungsfaktoren entstehen. Schwankungen bei Laserleistung oder Fokus, Fehlausrichtung der Schweißnaht oder Änderungen im Schutzgasfluss können zu inkonsistenten Schweißnähten beitragen. Um diese Inkonsistenzen zu minimieren, ist es wichtig, den Schweißprozess streng zu kontrollieren und die Ausrüstung regelmäßig zu kalibrieren, um eine einheitliche Qualität aller Schweißnähte sicherzustellen.
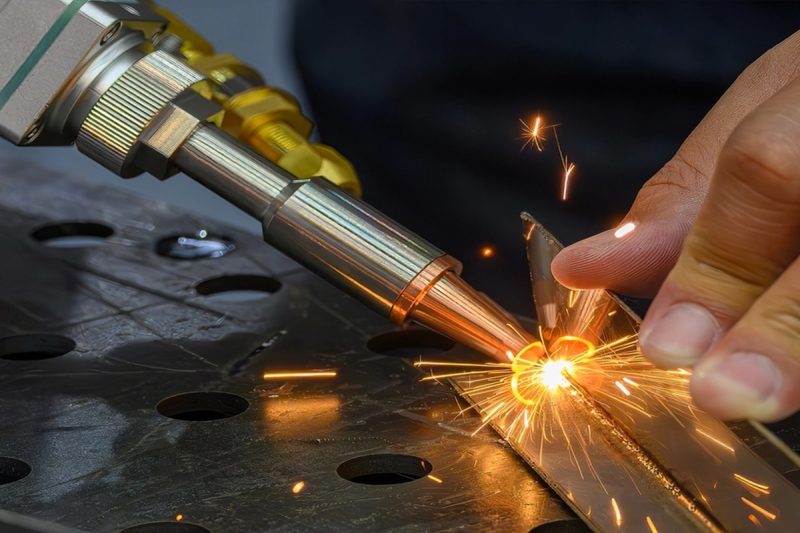
Zusammenfassung
Beim Laserschweißen hängt die Schweißbarkeit von Materialien von einer Vielzahl von Faktoren ab, von der Materialzusammensetzung und -dicke bis hin zu Laserparametern und äußeren Umgebungsbedingungen. Durch das Verständnis und die Optimierung dieser Faktoren können Hersteller hochwertige Schweißnähte herstellen, die strenge Anforderungen an Festigkeit, Haltbarkeit und Aussehen erfüllen. Während des Schweißprozesses können zwar Probleme wie Porosität, Rissbildung und Verformung auftreten, aber eine sorgfältige Kontrolle und Auswahl der Schweißparameter, der Ausrüstung und der Nachbehandlungen nach dem Schweißen kann diese Probleme mildern und die Konsistenz und Zuverlässigkeit des Laserschweißens bei einer Vielzahl von Materialien und Anwendungen verbessern.
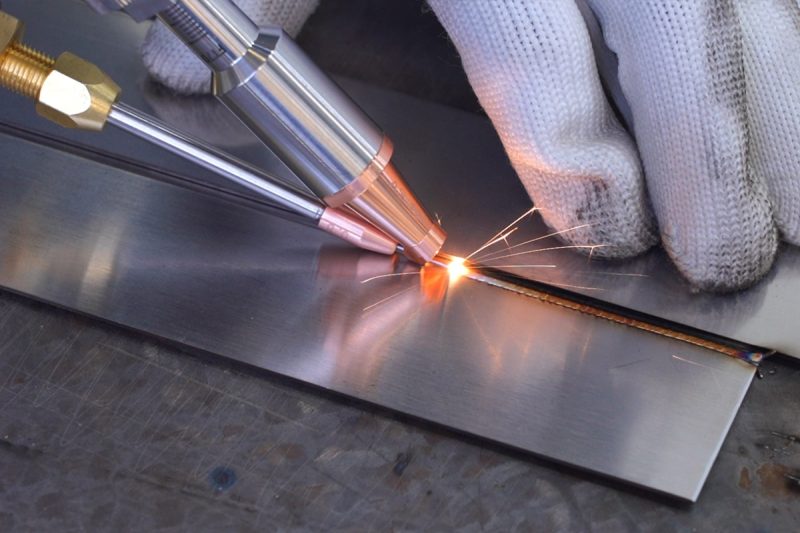
Holen Sie sich Laserschweißlösungen
Für Unternehmen, die hochwertige, zuverlässige Schweißnähte suchen, bietet AccTek Laser hochmoderne Laserschweißlösungen, die auf die unterschiedlichsten industriellen Anforderungen zugeschnitten sind. Als professioneller Hersteller von Laserschneid-, Schweiß-, Reinigungs- und Markierungsmaschinen bietet AccTek Laser hochmoderne Geräte, die auf optimale Schweißbarkeit zugeschnitten sind. Egal, ob Sie mit Metallen, Kunststoffen oder Verbundwerkstoffen arbeiten, unsere Laserschweißmaschinen bieten Präzision, Geschwindigkeit und Effizienz selbst für die anspruchsvollsten Anwendungen.
AccTek Lasers Laserschweißmaschinen sind für die Verarbeitung verschiedener Materialien und Stärken ausgelegt und verfügen über anpassbare Einstellungen für Laserleistung, Pulsdauer, Fokus und Schweißgeschwindigkeit, um sicherzustellen, dass Ihre Schweißnähte den höchsten Standards entsprechen. Unser Expertenteam kann Ihnen bei der Auswahl der richtigen Ausrüstung helfen, das System für Ihre spezifischen Anforderungen konfigurieren und fortlaufende Unterstützung bieten, um während des gesamten Produktionsprozesses eine optimale Leistung sicherzustellen.
Wenn Sie sich für AccTek Laser entscheiden, erhalten Sie Zugriff auf fortschrittliche Technologie und einen Partner, der sich für die Verbesserung Ihrer Schweißqualität und Produktivität einsetzt und Ihnen letztendlich dabei hilft, jedes Mal einwandfreie und langlebige Schweißnähte zu erzielen.
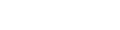
Kontaktinformationen
- [email protected]
- [email protected]
- +86-19963414011
- Nr. 3 Zone A, Industriegebiet Lunzhen, Stadt Yucheng, Provinz Shandong.
Holen Sie sich Laserlösungen