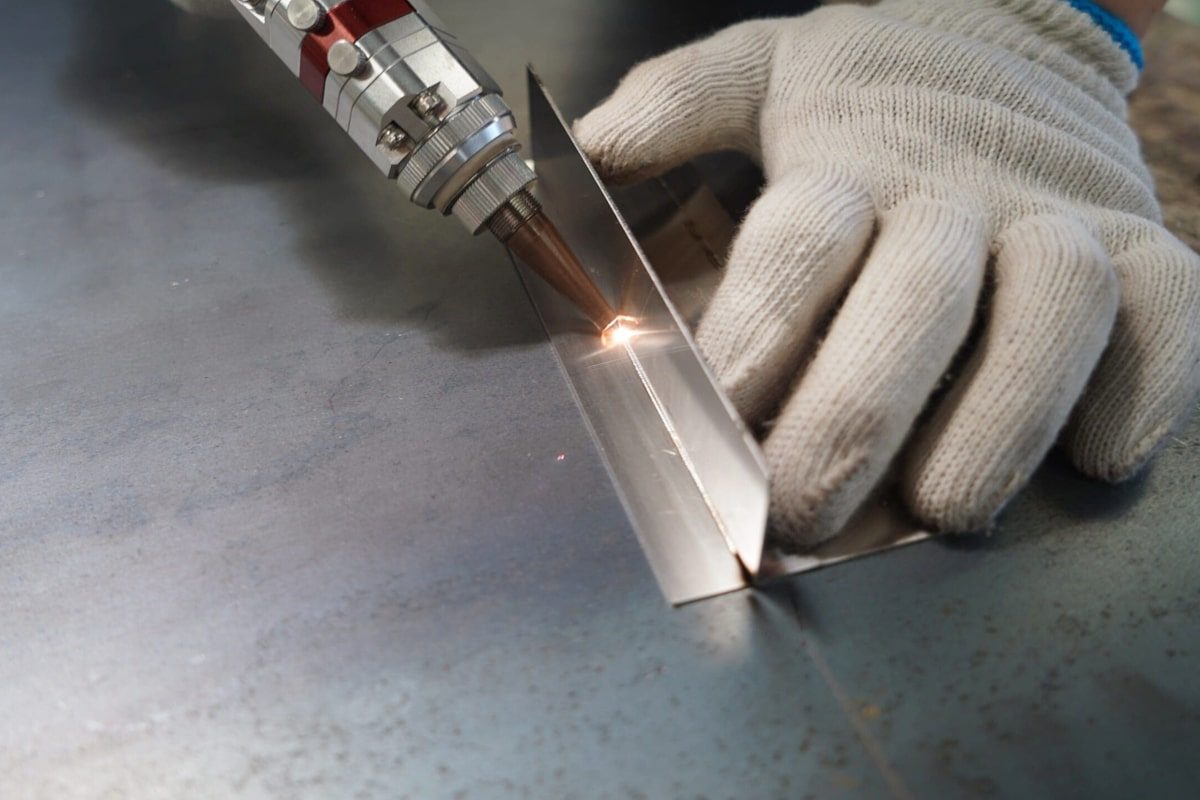
Quais fatores afetam a soldabilidade da soldagem a laser?
A soldagem a laser revolucionou a fabricação moderna, oferecendo alta precisão, distorção mínima de calor e a capacidade de unir materiais que, de outra forma, seriam difíceis de soldar usando métodos tradicionais. Indústrias como aeroespacial, automotiva, dispositivos médicos e eletrônicos dependem muito da soldagem a laser por sua velocidade e capacidade de fornecer juntas fortes e de alta qualidade com tratamento pós-soldagem mínimo. Apesar das inúmeras vantagens da soldagem a laser, atingir a soldabilidade ideal nem sempre é simples. O sucesso de uma soldagem a laser é determinado por uma variedade de fatores — propriedades do material, parâmetros do laser, configuração do equipamento, condições ambientais e tratamentos pós-soldagem — todos os quais devem ser cuidadosamente controlados para garantir a produção de uma solda forte, durável e sem defeitos.
Neste artigo, exploraremos em profundidade os vários fatores que influenciam a soldabilidade de materiais na soldagem a laser. Esses fatores incluem a composição do material base, a geometria da junta, a potência do laser, a velocidade e a qualidade do feixe, bem como fatores ambientais externos, como temperatura e contaminantes. Também examinaremos os desafios comuns encontrados na soldagem a laser e como eles podem ser mitigados para atingir a mais alta qualidade de solda possível. Ao final deste artigo, os leitores terão uma compreensão abrangente das múltiplas variáveis envolvidas na soldagem a laser e como otimizar esses fatores para resultados de soldagem superiores.
Índice
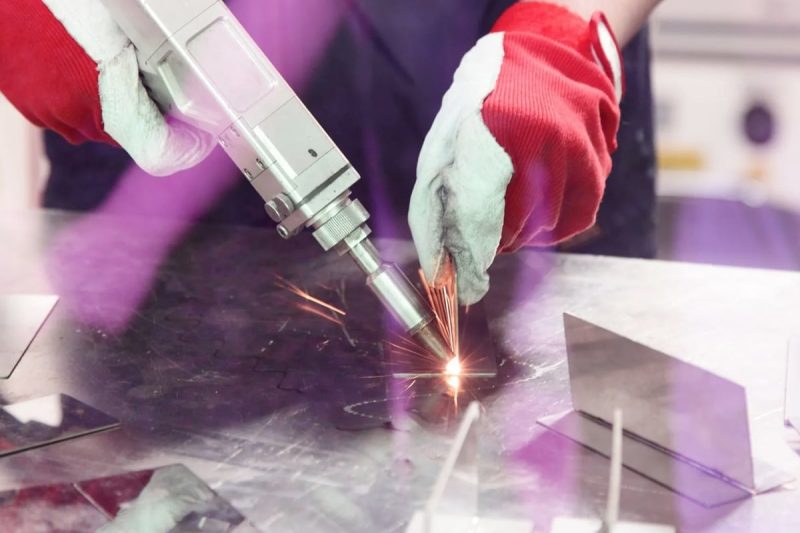
Introdução à soldagem a laser
Definição e Visão Geral
Soldagem a laser é uma técnica de soldagem de precisão que usa um feixe de laser altamente concentrado para derreter e fundir materiais, normalmente metais ou termoplásticos. O feixe de laser, que é gerado por uma fonte de laser, direciona energia focada no material, criando uma zona de calor localizada que derrete o material base na interface da junta. À medida que o material fundido se solidifica, ele forma uma solda. Este processo pode ser feito usando lasers de onda contínua (CW), que fornecem calor constante, ou lasers pulsados, que fornecem energia em rajadas curtas, geralmente para evitar superaquecimento e fornecer penetração controlada.
A soldagem a laser é altamente versátil e pode ser usada para uma variedade de tipos e espessuras de materiais. Ela oferece inúmeras vantagens, incluindo altas velocidades de soldagem, zonas afetadas pelo calor (HAZ) estreitas, distorção mínima do material e a capacidade de automatizar o processo, o que leva ao aumento da eficiência da produção. A precisão do feixe de laser permite a soldagem em espaços apertados e em componentes delicados, tornando a soldagem a laser ideal para aplicações de alta precisão, incluindo as indústrias aeroespacial e eletrônica.
Importância da soldabilidade na soldagem a laser
Soldabilidade na soldagem a laser refere-se à capacidade de um material de formar uma junta forte e sem defeitos quando submetido ao processo de soldagem a laser. Alcançar a soldabilidade depende de vários fatores inter-relacionados, como a composição química do material, propriedades térmicas, design da junta e como ele responde à entrada de calor localizada do feixe de laser. Se esses fatores não forem otimizados, a junta soldada pode estar propensa a defeitos como porosidade, rachaduras, distorções ou ligação fraca.
O conceito de soldabilidade é particularmente crucial na soldagem a laser porque a alta concentração de energia do feixe de laser pode ter um impacto significativo na microestrutura e nas propriedades mecânicas do material. Por exemplo, ciclos rápidos de aquecimento e resfriamento podem levar a problemas como tensão residual, rachaduras ou transformações de fase indesejáveis em certos materiais. Para superar esses desafios, os fabricantes devem selecionar e controlar cuidadosamente os vários parâmetros envolvidos na soldagem a laser.
Comparação com métodos tradicionais de soldagem
Embora a soldagem a laser seja conhecida por sua precisão e eficiência, ela difere significativamente dos métodos de soldagem tradicionais, como soldagem MIG (Metal Inert Gas) ou soldagem TIG (Tungsten Inert Gas) em várias maneiras importantes. Os métodos de soldagem tradicionais usam arcos elétricos para gerar calor, o que aquece uma área maior do material e geralmente resulta em zonas afetadas pelo calor mais amplas. Esses métodos também tendem a envolver velocidades de soldagem mais lentas e maior distorção do material. Por outro lado, a soldagem a laser é caracterizada por um feixe de energia altamente concentrado, o que permite velocidades de soldagem mais rápidas, zonas afetadas pelo calor mais estreitas e distorção mínima.
No entanto, a soldagem a laser é mais sensível a mudanças nas propriedades do material, design da junta e configurações do laser do que os métodos tradicionais. Por exemplo, os métodos tradicionais podem ser mais tolerantes ao soldar materiais mais espessos ou juntas com geometrias irregulares, enquanto a soldagem a laser requer um controle mais preciso de parâmetros como potência do laser, foco do feixe e velocidade de soldagem. Como tal, a soldagem a laser pode não ser a solução ideal para todas as aplicações, particularmente ao lidar com materiais ou geometrias que são desafiadores para o processo.
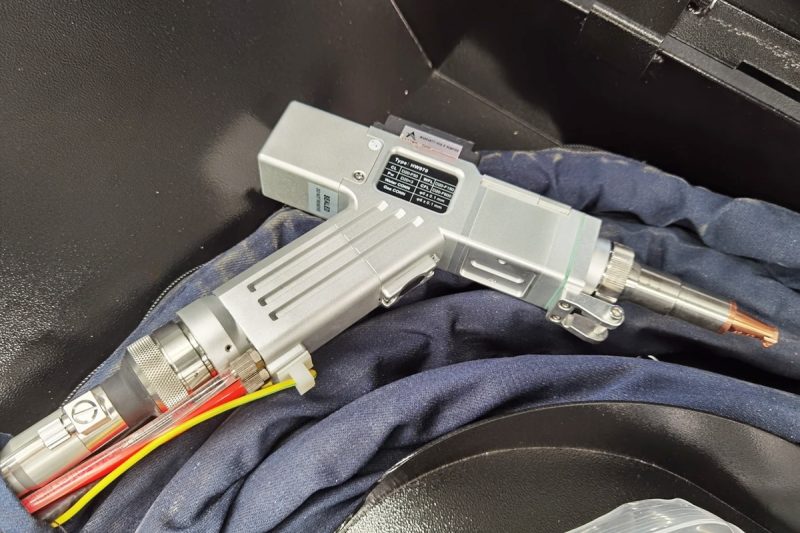
Propriedades do Material
O material que está sendo soldado desempenha um papel significativo no sucesso de uma operação de soldagem a laser. Propriedades-chave do material que influenciam a soldabilidade incluem composição do material base, espessura e geometria, ponto de fusão, condutividade térmica e a presença de elementos de liga ou aditivos.
Composição do material base
A composição química do material base é um dos fatores mais importantes que afetam a soldabilidade. Diferentes materiais têm diferentes pontos de fusão, condutividades térmicas e comportamentos de solidificação, todos os quais influenciam o processo de soldagem a laser. Por exemplo, aços de alto carbono tendem a formar fases duras e quebradiças durante o resfriamento, aumentando a probabilidade de rachaduras na solda. Da mesma forma, materiais com altos níveis de certos elementos de liga, como cromo, níquel ou molibdênio, podem ser mais suscetíveis a transformações de fase, o que pode levar a defeitos de solda ou propriedades mecânicas reduzidas.
Alguns materiais, como alumínio e cobre, são particularmente desafiadores para soldar usando soldagem a laser devido à sua alta condutividade térmica e baixos pontos de fusão. Esses materiais exigem maior potência do laser para atingir penetração adequada, mas o risco de queima também é muito maior. Materiais com alto coeficiente de expansão, como ligas de titânio, podem sofrer distorção térmica durante a soldagem, exigindo controle preciso dos parâmetros do laser.
Entender a composição do material que está sendo soldado é essencial para determinar os parâmetros ideais do laser. Os elementos de liga e impurezas no material podem influenciar como o material responde ao calor e à formação da solda, tornando necessário ajustar parâmetros como potência do laser, foco do feixe e gás de proteção.
Espessura e Geometria
A espessura do material e a geometria da junta afetam diretamente a energia necessária para a soldagem e a distribuição de calor dentro do material. Para materiais finos, uma potência de laser menor é geralmente suficiente, mas é necessário um controle cuidadoso para evitar entrada excessiva de calor que pode causar queimadura. Para materiais mais espessos, uma potência de laser maior e velocidades de soldagem mais lentas são necessárias para garantir penetração total e uma solda sólida.
A geometria da junta também influencia como o laser interage com o material. Juntas de topo simples são relativamente fáceis de soldar porque fornecem uma conexão direta entre as duas superfícies. No entanto, juntas mais complexas, como juntas em T, juntas de filete ou juntas de sobreposição, podem exigir atenção especial. O ângulo e o alinhamento da junta influenciarão a capacidade do laser de penetrar e fundir adequadamente os materiais.
Materiais com geometrias complexas também podem introduzir desafios adicionais para soldagem a laser devido a dificuldades em alinhar o feixe com a junta e variações na espessura ao longo da junta. Otimizar o design da junta e garantir o alinhamento adequado do feixe de laser são etapas críticas para obter soldas fortes e de alta qualidade.
Ponto de fusão e condutividade térmica
O ponto de fusão de um material determina quanta energia é necessária para derretê-lo. Materiais com altos pontos de fusão, como tungstênio, titânio ou aços de alta liga, requerem significativamente mais energia para atingir seu ponto de fusão e exigem gerenciamento cuidadoso da potência do laser. Por outro lado, materiais com baixos pontos de fusão, como alumínio ou zinco, podem derreter muito facilmente sob um feixe de laser e podem exigir velocidades de soldagem rápidas ou técnicas de laser pulsado para evitar derretimento excessivo.
Condutividade térmica — a capacidade de um material de conduzir calor — também impacta a soldabilidade. Materiais com alta condutividade térmica, como cobre, dissipam calor rapidamente, o que significa que o feixe de laser deve fornecer energia suficiente para superar essa perda de calor e atingir a penetração adequada. Por outro lado, materiais de baixa condutividade térmica, como aço inoxidável, retêm o calor de forma mais eficaz, o que pode levar a uma zona afetada pelo calor (ZTA) maior e potencial distorção térmica se não for gerenciado adequadamente.
Elementos de Liga e Aditivos
A presença de elementos de liga e aditivos pode ter um impacto profundo na soldabilidade de um material. Elementos de liga comuns como manganês, silício e cromo podem melhorar as propriedades mecânicas de um material, mas também podem introduzir desafios durante a soldagem. Por exemplo, o manganês pode tornar a solda mais suscetível a rachaduras, enquanto o silício excessivo pode levar à formação de fases quebradiças na zona de solda.
Aditivos como fluxo podem ser usados para melhorar a ligação da superfície, evitar oxidação ou modificar o comportamento da poça de solda. A seleção de fluxo e outros aditivos deve ser feita com cuidado, pois eles podem influenciar a qualidade final e as propriedades mecânicas da solda.
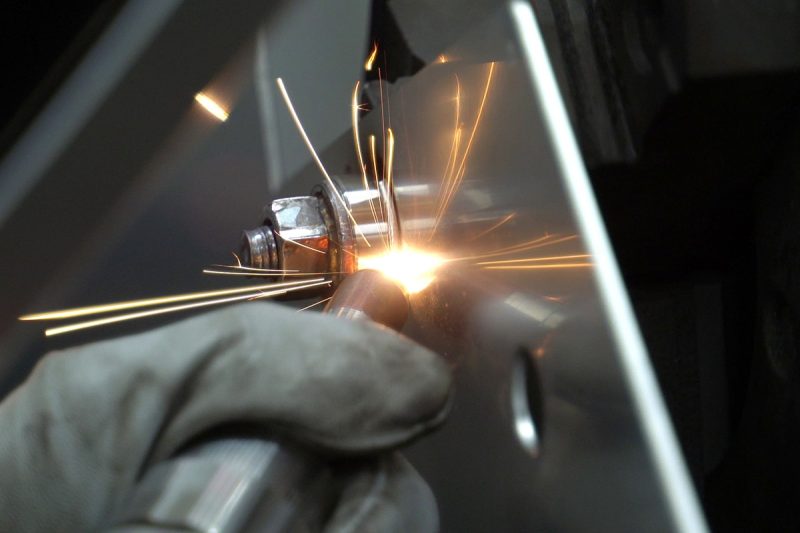
Parâmetros de laser
Os parâmetros do laser, incluindo potência do laser, foco, velocidade, qualidade do feixe e outros, são fundamentais para a soldabilidade dos materiais. Esses parâmetros controlam como o feixe de laser interage com o material, a energia entregue à poça de solda e a taxa de solidificação.
Potência do Laser
A potência do laser influencia diretamente a profundidade da penetração, a velocidade da soldagem e a quantidade de calor gerada durante o processo. Maior potência do laser leva a uma penetração mais profunda, mas também aumenta o risco de queimaduras ou zonas afetadas pelo calor excessivo. Configurações de potência mais baixas podem não fornecer energia suficiente para atingir a penetração total em materiais mais espessos, resultando em juntas fracas ou fusão incompleta.
A configuração ideal de potência do laser depende do material a ser soldado, sua espessura e as características de solda desejadas. Em geral, deve-se atingir um equilíbrio entre potência suficiente para derreter o material e evitar excesso de calor que poderia distorcer a peça de trabalho.
Foco Laser
O foco do laser controla o tamanho e a intensidade do feixe de laser. Um feixe fortemente focado resulta em um ponto pequeno e de alta energia no material, o que permite uma penetração mais profunda e soldas mais estreitas. No entanto, um foco muito apertado pode aumentar o risco de queimadura, especialmente com materiais mais finos. Em contraste, um feixe desfocado espalhará a energia por uma área maior, reduzindo o risco de queimadura, mas também levando a uma penetração mais rasa e soldas mais largas.
O foco ideal depende do material, espessura e geometria da junta. Para controle preciso, os sistemas de laser normalmente apresentam foco ajustável, permitindo que os operadores ajustem o feixe de acordo com requisitos específicos de soldagem.
Duração do pulso
Na soldagem a laser pulsado, o feixe de laser é entregue em rajadas curtas e intensas de energia. A duração desses pulsos — duração do pulso — pode impactar significativamente a profundidade de penetração, a taxa de resfriamento e a qualidade geral da solda. Pulsos mais curtos permitem uma entrada de energia mais controlada e podem ajudar a evitar o superaquecimento, enquanto pulsos mais longos fornecem mais energia para uma penetração mais profunda.
A duração do pulso deve ser cuidadosamente ajustada com base no material e na espessura que estão sendo soldados. Pulsos mais longos são normalmente usados para materiais mais espessos, enquanto pulsos mais curtos são usados para materiais finos para evitar distorção térmica.
Qualidade do feixe
A qualidade do feixe se refere à distribuição de energia dentro do feixe de laser e é um fator essencial para determinar quão efetivamente o laser pode focar no material. Um feixe de alta qualidade tem um perfil de energia uniforme, permitindo uma entrega de energia consistente e uma solda mais estável. Feixes de baixa qualidade, por outro lado, podem levar a uma distribuição desigual de energia, resultando em baixa qualidade de solda e formação de junta inconsistente.
Sistemas de soldagem a laser com alta qualidade de feixe geralmente produzem soldas mais limpas e precisas, com menos defeitos.
Velocidade de soldagem
A velocidade de soldagem afeta o tempo durante o qual o laser é aplicado ao material. Velocidades de soldagem mais rápidas normalmente resultam em menor entrada de calor, levando a zonas menores afetadas pelo calor e distorção reduzida. No entanto, se a velocidade for muito alta, pode não haver tempo suficiente para a penetração adequada, resultando em juntas fracas. Velocidades mais lentas podem aumentar a entrada de calor, levando a zonas maiores afetadas pelo calor e potencialmente mais distorção, mas podem ser necessárias para soldar materiais mais espessos.
A velocidade ideal de soldagem é determinada pelo tipo de material, espessura e características de solda desejadas.
Gás de proteção
O gás de proteção é usado na soldagem a laser para proteger a poça de solda da contaminação pela atmosfera ao redor, o que pode levar à oxidação ou outros defeitos. O tipo de gás de proteção usado, como argônio, nitrogênio ou uma mistura de gases, pode afetar a qualidade da solda, incluindo sua resistência, aparência e resistência à corrosão. Além disso, o gás de proteção pode influenciar a dissipação de calor e a taxa de resfriamento da poça de solda, o que por sua vez afeta a microestrutura da solda.
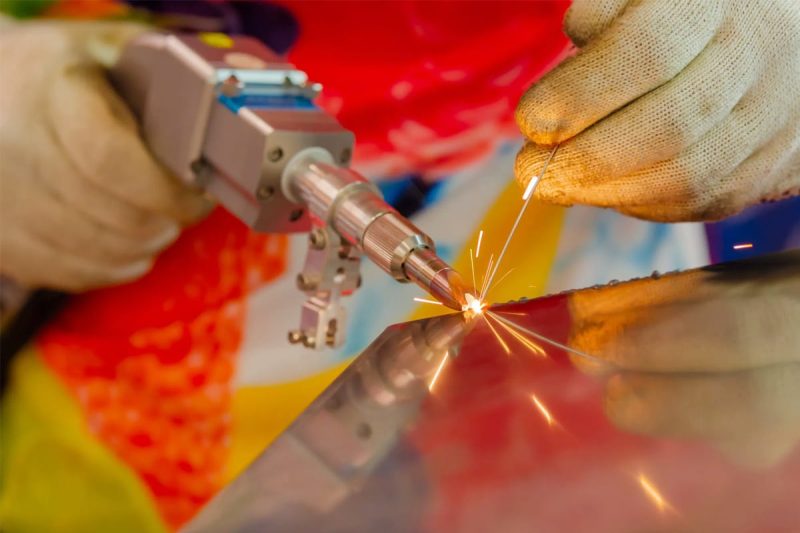
Espessura do material e projeto da junta
Na soldagem a laser, a espessura do material e a geometria da junta impactam significativamente o processo de soldagem, a energia necessária e, finalmente, a qualidade da solda. Uma compreensão profunda desses fatores é crítica para atingir soldas ótimas com defeitos mínimos.
Espessura do material
A espessura do material que está sendo soldado tem um impacto direto no processo de soldagem a laser. Materiais mais espessos exigem maior potência do laser para atingir penetração total e criar uma ligação forte. Ao soldar materiais mais espessos, é necessário gerenciar a entrada de calor cuidadosamente para evitar superaquecimento e distorção. Uma configuração de potência mais alta permite penetração mais profunda, mas também pode aumentar o tamanho da zona afetada pelo calor (HAZ), o que pode afetar as propriedades mecânicas do material base.
Para materiais finos, uma potência de laser menor é normalmente usada para evitar a queima, pois esses materiais exigem menos energia para derreter. O principal desafio na soldagem de materiais finos com um laser é equilibrar a potência do laser para evitar entrada excessiva de calor, enquanto ainda atinge penetração suficiente sem danificar o material. A rápida taxa de resfriamento da soldagem a laser ajuda a minimizar a zona afetada pelo calor para materiais mais finos.
Geometria das juntas
A geometria da junta — como juntas de topo, juntas em T, juntas sobrepostas e juntas de filete — desempenha um papel crucial no sucesso de uma solda a laser. A soldagem a laser normalmente funciona melhor com juntas de topo, pois o alinhamento direto das bordas do material garante uma poça de solda consistente. No entanto, juntas mais complexas, como juntas sobrepostas ou juntas em T, exigem alinhamento cuidadoso do feixe, pois o laser precisa garantir a penetração em todos os lados da junta, incluindo quaisquer lacunas que possam existir entre os materiais.
Quando a geometria da junta envolve formas complexas ou variações na espessura do material, são necessários ajustes nos parâmetros de soldagem. Por exemplo, juntas sobrepostas exigem controle preciso do foco do laser e do ângulo do feixe para garantir que o material superior se funda efetivamente com o material inferior. Soldas de filete também exigem controle cuidadoso da interação do feixe de laser com as superfícies da junta, pois os ângulos e a proximidade do material podem influenciar a distribuição de calor.
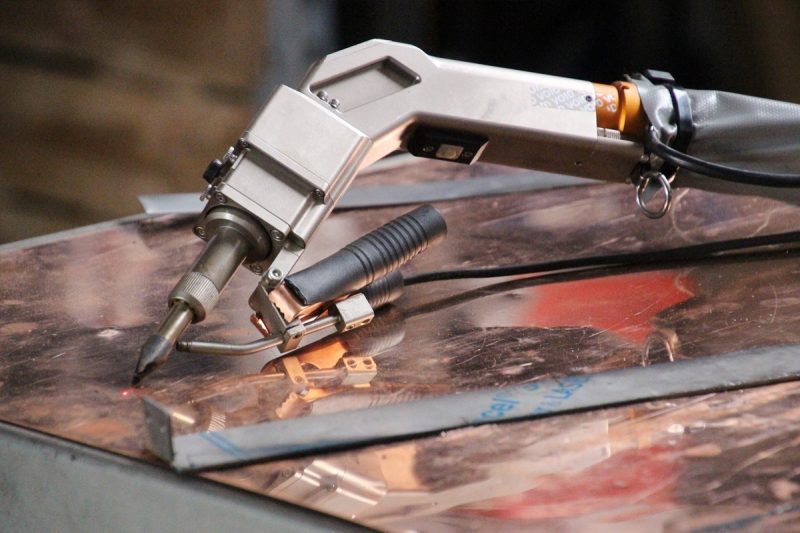
Gestão de calor e taxa de resfriamento
O gerenciamento eficaz do calor é crucial na soldagem a laser para controlar as propriedades do material, minimizar a distorção e evitar defeitos de solda. Aspectos-chave do gerenciamento do calor incluem a zona afetada pelo calor (HAZ) e a taxa de resfriamento.
Zona Afetada pelo Calor (HAZ)
A zona afetada pelo calor (ZTA) é a região do material que não é derretida, mas sofre uma mudança na microestrutura devido às altas temperaturas durante a soldagem. O tamanho e a extensão da ZTA são determinados pela potência do laser, velocidade de soldagem e tipo de material. Na soldagem a laser, a ZTA tende a ser menor em comparação aos métodos tradicionais de soldagem devido ao calor concentrado do feixe de laser. No entanto, mesmo uma ZTA pequena pode impactar as propriedades do material, especialmente para aços de alta resistência ou materiais que são sensíveis a ciclos térmicos.
Para certos materiais, como aços de alto carbono ou ligas de titânio, uma HAZ maior pode levar a propriedades mecânicas reduzidas, como comportamento quebradiço ou corrosão sob tensão. Como resultado, o controle cuidadoso dos parâmetros do laser, especialmente a potência e a velocidade, é essencial para minimizar a HAZ e ainda atingir a fusão adequada na interface da junta.
Taxa de resfriamento
A taxa de resfriamento, ou a velocidade na qual a poça de solda fundida se solidifica, é um fator crítico na determinação da microestrutura final e das propriedades mecânicas da solda. A soldagem a laser normalmente resulta em taxas de resfriamento muito rápidas devido à pequena zona afetada pelo calor e à rápida solidificação da poça de solda fundida. Taxas de resfriamento mais rápidas podem resultar em uma microestrutura mais fina, o que pode melhorar a resistência da solda. No entanto, esse resfriamento rápido também pode introduzir tensões residuais, potencialmente levando a rachaduras ou distorções em certos materiais, especialmente aqueles com alta temperabilidade, como aços de alto carbono.
Uma taxa de resfriamento mais lenta pode reduzir o risco de rachaduras, mas pode resultar na formação de grãos maiores, o que pode reduzir a resistência geral da solda. Gerenciar a taxa de resfriamento é vital para equilibrar esses fatores. Técnicas como tratamento térmico pós-soldagem (por exemplo, recozimento) podem ser empregadas para aliviar tensões residuais e melhorar as propriedades finais do material.
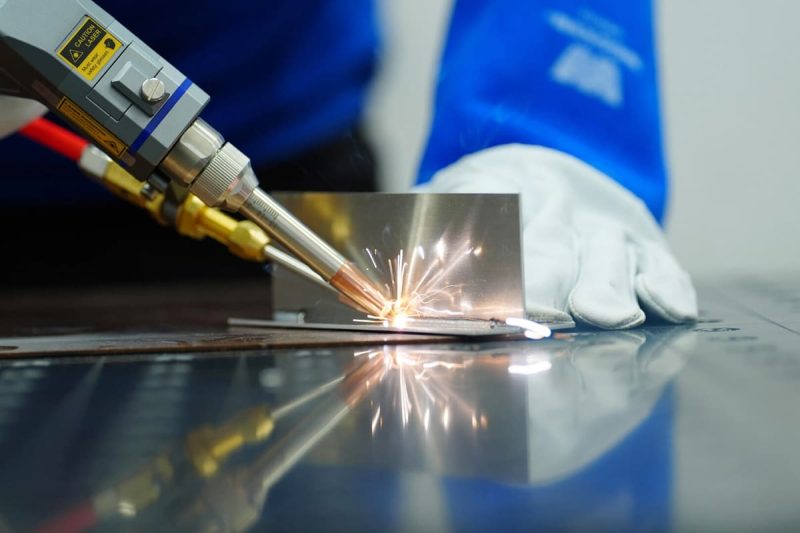
Equipamento e configuração de soldagem a laser
A qualidade da solda a laser é fortemente influenciada pelo tipo e configuração do equipamento de solda a laser. Os principais componentes do equipamento incluem a fonte de laser, lente de foco, óptica e cabeça de solda.
Tipo de fonte de laser
O tipo de laser usado no processo de soldagem afeta vários aspectos da operação, incluindo qualidade do feixe, potência e foco. Os tipos comuns de laser para soldagem incluem lasers de CO2, lasers de fibra e lasers de disco:
- Lasers de CO2: Esses são os lasers mais amplamente utilizados em soldagem industrial devido à sua alta potência e versatilidade. Os lasers de CO2 são ideais para soldar materiais mais espessos e fornecem uma qualidade de feixe estável.
- Lasers de fibra: Esses lasers são conhecidos por sua alta qualidade de feixe e eficiência, tornando-os particularmente eficazes para soldagem de chapas finas. Os lasers de fibra oferecem velocidades de soldagem mais rápidas e podem atingir maior precisão do que os lasers de CO2, especialmente em materiais com baixa condutividade térmica.
A escolha da fonte de laser correta depende do tipo de material, da espessura e dos requisitos da aplicação.
Lente de Foco e Óptica
O feixe de laser deve ser focado na peça de trabalho para atingir o tamanho e a penetração de solda desejados. A qualidade e o alinhamento da lente de foco e da óptica desempenham um papel crítico na precisão do feixe e na qualidade da solda. Um sistema óptico de alta qualidade garante que o feixe de laser permaneça estável e focado, o que é particularmente importante para aplicações de alta precisão.
A distância focal da lente, o tamanho da abertura e o posicionamento da lente podem influenciar como a energia é distribuída sobre a superfície do material. Ópticas mal alinhadas podem levar ao desfoque, o que resulta em entrega de energia inconsistente e soldas potencialmente fracas ou defeituosas.
Cabeça de soldagem e óptica de foco
A cabeça de soldagem é responsável por direcionar o feixe de laser para o material. A configuração da cabeça de soldagem, incluindo sua posição, inclinação e movimento, afeta a uniformidade e a qualidade da solda. A cabeça de soldagem deve ser alinhada precisamente com o material para garantir que o feixe de laser permaneça focado na junta durante todo o processo de soldagem.
Além da cabeça de soldagem, a óptica de foco, que molda e direciona o feixe, precisa ser mantida e calibrada adequadamente. Qualquer desalinhamento ou degradação nessas ópticas pode levar à entrega inconsistente do feixe e à má qualidade da solda.
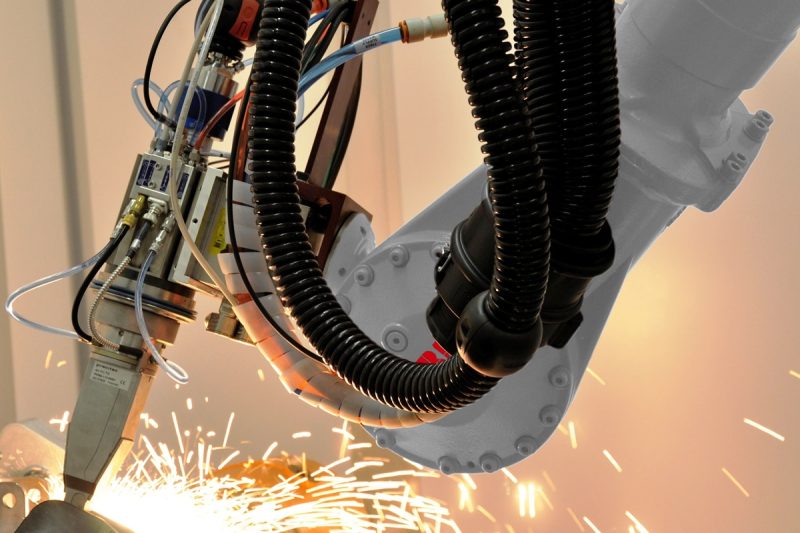
Condições ambientais
As condições ambientais sob as quais a soldagem a laser ocorre podem ter um efeito significativo na qualidade e consistência da solda. Fatores ambientais importantes a serem considerados incluem temperatura ambiente e fluxo de ar.
Temperatura ambiente
Temperaturas extremas podem afetar a resposta do material ao processo de soldagem a laser. Por exemplo, os materiais podem se tornar quebradiços em baixas temperaturas, o que pode aumentar a probabilidade de rachaduras durante a soldagem. Por outro lado, altas temperaturas ambientes podem levar à distorção excessiva do material ou expansão térmica, o que pode afetar o alinhamento da junta e a consistência da solda. Manter uma temperatura ambiente estável é crucial para garantir que o material responda previsivelmente ao processo de soldagem.
Fluxo de ar e contaminantes
A presença de contaminantes como poeira, óleo, umidade ou fumaça pode afetar o processo de soldagem de várias maneiras. Contaminantes no ar podem absorver parte da energia do laser, reduzindo a eficiência do processo. Além disso, impurezas na superfície do material podem levar à oxidação, corrosão ou outros defeitos que comprometem a qualidade da solda.
Controlar o ambiente de soldagem por meio de ventilação adequada, superfícies limpas e uma câmara de soldagem fechada pode ajudar a reduzir o risco de contaminação e garantir soldas mais consistentes.

Tratamento Pós-Soldagem
Após a conclusão do processo de soldagem a laser, tratamentos pós-soldagem podem ser necessários para melhorar as propriedades mecânicas, aliviar tensões residuais e garantir que a solda atenda às especificações exigidas.
anelamento
O recozimento é um processo de tratamento térmico em que o material soldado é aquecido a uma temperatura específica e, então, resfriado lentamente. Este processo é usado para aliviar tensões residuais que podem ter sido introduzidas durante as fases de aquecimento e resfriamento rápido do processo de soldagem. O recozimento ajuda a restaurar a ductilidade do material e a reduzir o risco de rachaduras.
Na soldagem a laser, materiais que passam por taxas de resfriamento rápidas podem exigir recozimento para evitar fragilização e melhorar a tenacidade da solda. A temperatura e a duração exatas do recozimento dependem do tipo de material e dos requisitos específicos da solda.
Acabamento e limpeza de superfície
Após a soldagem, a superfície da solda pode apresentar oxidação, incrustações ou outros contaminantes que precisam ser removidos. A limpeza e o acabamento da superfície da solda são essenciais para garantir uma aparência lisa e sem defeitos e para aumentar a resistência à corrosão da área soldada.
A limpeza pode envolver técnicas como polimento mecânico, decapagem química ou jateamento abrasivo. O acabamento de superfície adequado é particularmente importante em indústrias onde a estética da solda e a integridade do material são primordiais, como em dispositivos médicos ou eletrônicos de consumo.
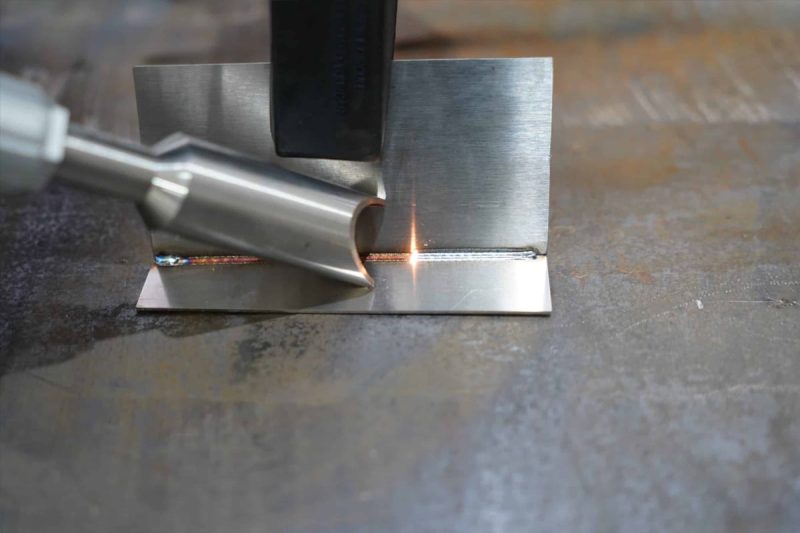
Desafios na soldagem a laser
Embora a soldagem a laser ofereça muitas vantagens, ela também vem com seu próprio conjunto de desafios. Problemas comuns incluem porosidade, rachaduras, distorção e qualidade de solda inconsistente.
Porosidade
A porosidade ocorre quando bolsas de gás se formam dentro da poça de solda, levando a vazios na solda. Isso geralmente é causado por gases presos, como nitrogênio ou oxigênio, que ficam presos durante o processo de solidificação. A porosidade pode enfraquecer a solda e afetar seu desempenho. Gás de proteção adequado, controle cuidadoso dos parâmetros de soldagem e garantia de superfícies limpas antes da soldagem podem ajudar a minimizar a porosidade.
Rachaduras e Distorções
Rachaduras são um problema significativo na soldagem a laser, particularmente em materiais com alto teor de carbono ou baixa ductilidade. As rápidas taxas de resfriamento da soldagem a laser podem criar altas tensões residuais, o que pode levar a rachaduras, especialmente na zona afetada pelo calor.
A distorção também pode ocorrer devido ao aquecimento e resfriamento desiguais, o que faz com que o material se deforme ou entorte. Gerenciar a entrada de calor por meio de parâmetros de laser ideais e usar técnicas de fixação pode ajudar a reduzir a distorção.
Inconsistência na qualidade da solda
A qualidade inconsistente da solda pode surgir de variações nas propriedades do material, parâmetros do laser ou fatores ambientais. Flutuações na potência ou foco do laser, desalinhamento da junta ou mudanças no fluxo do gás de proteção podem contribuir para soldas inconsistentes. Para minimizar essas inconsistências, é essencial manter um controle rígido sobre o processo de soldagem e calibrar regularmente o equipamento para garantir uniformidade em todas as soldas.
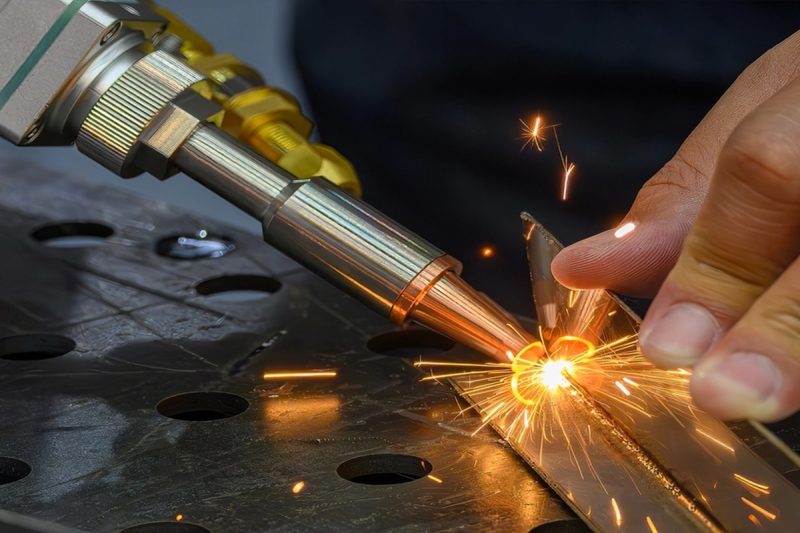
Resumo
Na soldagem a laser, a soldabilidade dos materiais depende de uma ampla gama de fatores, desde a composição e espessura do material até os parâmetros do laser e condições ambientais externas. Ao entender esses fatores e otimizá-los, os fabricantes podem produzir soldas de alta qualidade que atendem a requisitos rigorosos de resistência, durabilidade e aparência. Embora desafios como porosidade, rachaduras e distorções possam surgir durante o processo de soldagem, o controle cuidadoso e a seleção de parâmetros de soldagem, equipamentos e tratamentos pós-soldagem podem mitigar esses problemas e melhorar a consistência e a confiabilidade da soldagem a laser em uma variedade de materiais e aplicações.
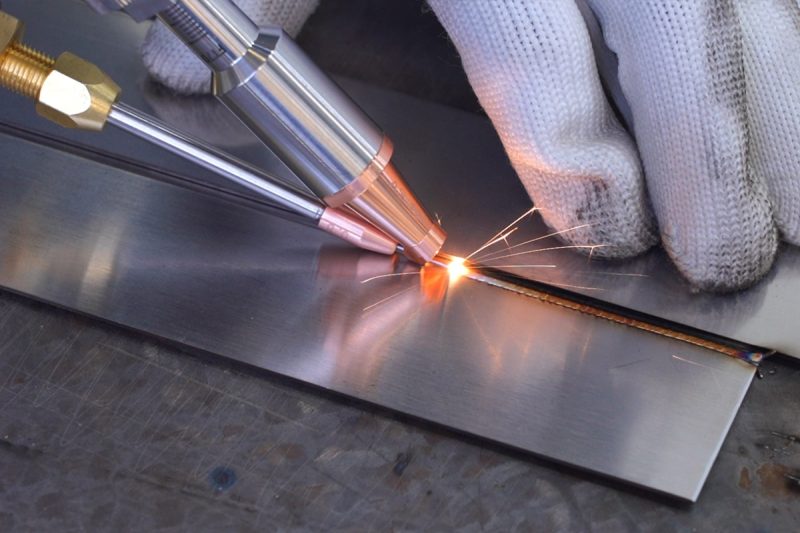
Obtenha soluções de soldagem a laser
Para empresas que buscam soldas confiáveis e de alta qualidade, a AccTek Laser oferece soluções de soldagem a laser de ponta, projetadas para atender a diversas necessidades industriais. Como fabricante profissional de máquinas de corte, soldagem, limpeza e marcação a laser, a AccTek Laser fornece equipamentos de última geração, personalizados para otimizar a soldabilidade. Não importa se você está trabalhando com metais, plásticos ou compostos, nossas máquinas de soldagem a laser oferecem precisão, velocidade e eficiência até mesmo para as aplicações mais desafiadoras.
Lasers AccTek máquinas de solda a laser são projetados para lidar com vários materiais e espessuras, com configurações personalizáveis para potência do laser, duração do pulso, foco e velocidade de soldagem, garantindo que suas soldas atendam aos mais altos padrões. Nossa equipe de especialistas pode ajudá-lo a selecionar o equipamento certo, configurar o sistema para suas necessidades específicas e oferecer suporte contínuo para garantir o desempenho ideal durante todo o processo de produção.
Ao escolher a AccTek Laser, você ganha acesso a tecnologia avançada e a um parceiro comprometido em melhorar a qualidade e a produtividade da sua soldagem, ajudando você a obter soldas perfeitas e duráveis sempre.
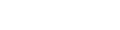
Informações de contato
- [email protected]
- [email protected]
- +86-19963414011
- No. 3 Zona A, Zona Industrial de Lunzhen, Cidade de Yucheng, Província de Shandong.
Obtenha soluções a laser