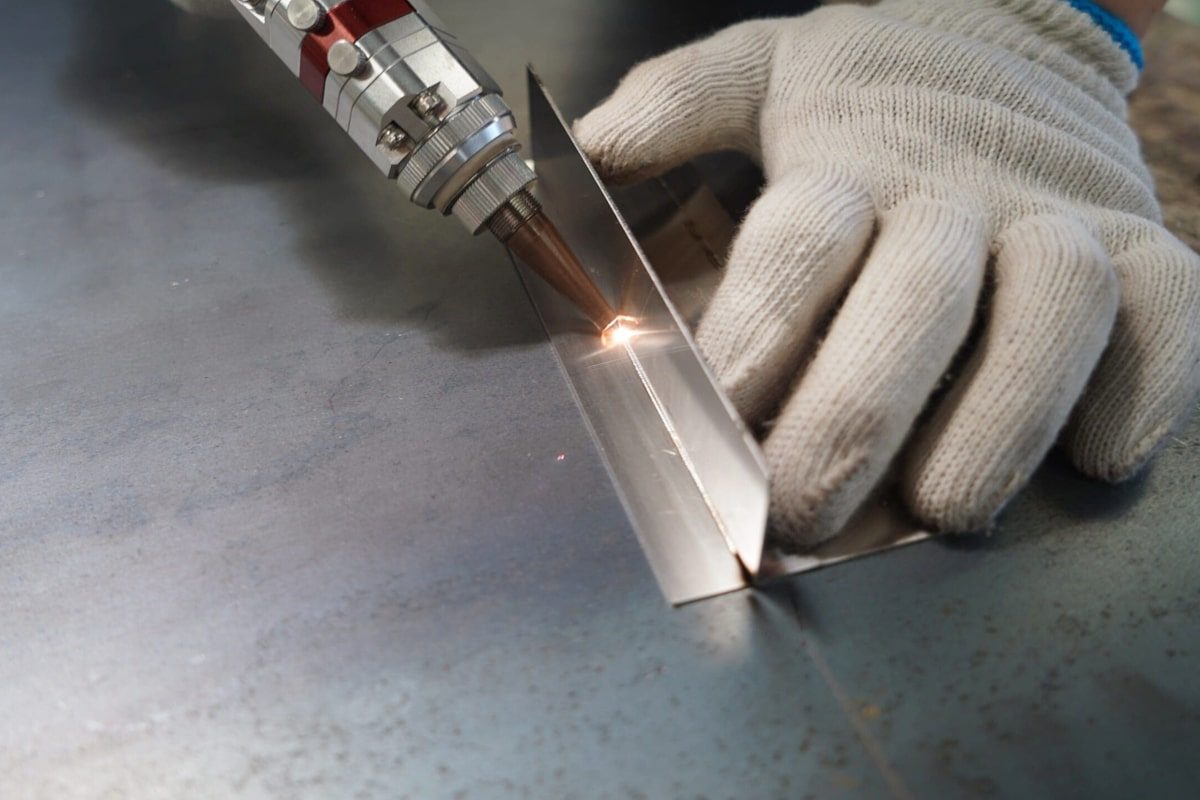
¿Qué factores afectan la soldabilidad de la soldadura láser?
La soldadura láser ha revolucionado la fabricación moderna, ofreciendo alta precisión, mínima distorsión térmica y la capacidad de unir materiales que de otro modo serían difíciles de soldar con los métodos tradicionales. Industrias como la aeroespacial, la automotriz, los dispositivos médicos y la electrónica dependen en gran medida de la soldadura láser por su velocidad y su capacidad para ofrecer uniones resistentes y de alta calidad con un mínimo tratamiento posterior a la soldadura. A pesar de las numerosas ventajas de la soldadura láser, lograr una soldabilidad óptima no siempre es sencillo. El éxito de una soldadura láser está determinado por una variedad de factores (propiedades del material, parámetros del láser, configuración del equipo, condiciones ambientales y tratamientos posteriores a la soldadura), todos los cuales deben controlarse cuidadosamente para garantizar la producción de una soldadura resistente, duradera y sin defectos.
En este artículo, exploraremos en profundidad los diversos factores que influyen en la soldabilidad de los materiales en la soldadura láser. Estos factores incluyen la composición del material base, la geometría de la unión, la potencia del láser, la velocidad y la calidad del haz, así como factores ambientales externos como la temperatura y los contaminantes. También examinaremos los desafíos comunes que se encuentran en la soldadura láser y cómo se pueden mitigar para lograr la mayor calidad de soldadura posible. Al final de este artículo, los lectores tendrán una comprensión integral de las múltiples variables involucradas en la soldadura láser y cómo optimizar estos factores para obtener resultados de soldadura superiores.
Tabla de contenido
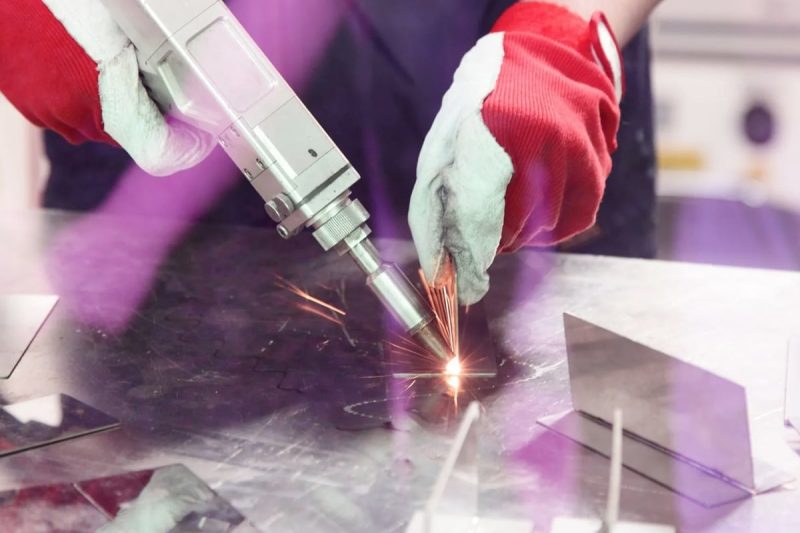
Introducción a la soldadura láser
Definición y descripción general
La soldadura láser es una técnica de soldadura de precisión que utiliza un haz láser altamente concentrado para fundir y fusionar materiales, generalmente metales o termoplásticos. El haz láser, que se genera mediante una fuente láser, dirige energía enfocada hacia el material, creando una zona de calor localizada que funde el material base en la interfaz de unión. A medida que el material fundido se solidifica, forma una soldadura. Este proceso se puede realizar utilizando láseres de onda continua (CW), que proporcionan calor constante, o láseres pulsados, que entregan energía en ráfagas cortas, a menudo para evitar el sobrecalentamiento y proporcionar una penetración controlada.
La soldadura láser es muy versátil y se puede utilizar para una amplia gama de tipos y espesores de materiales. Ofrece numerosas ventajas, entre las que se incluyen altas velocidades de soldadura, zonas afectadas por el calor (ZAT) estrechas, mínima distorsión del material y la capacidad de automatizar el proceso, lo que conduce a una mayor eficiencia de producción. La precisión del rayo láser permite soldar en espacios reducidos y en componentes delicados, lo que hace que la soldadura láser sea ideal para aplicaciones de alta precisión, incluidas las industrias aeroespacial y electrónica.
Importancia de la soldabilidad en la soldadura láser
La soldabilidad en la soldadura láser se refiere a la capacidad de un material para formar una unión fuerte y libre de defectos cuando se somete al proceso de soldadura láser. Lograr la soldabilidad depende de varios factores interrelacionados, como la composición química del material, las propiedades térmicas, el diseño de la unión y cómo responde al calor localizado que aporta el rayo láser. Si estos factores no se optimizan, la unión soldada puede ser propensa a defectos como porosidad, agrietamiento, distorsión o unión débil.
El concepto de soldabilidad es particularmente crucial en la soldadura láser porque la alta concentración de energía del haz láser puede tener un impacto significativo en la microestructura y las propiedades mecánicas del material. Por ejemplo, los ciclos rápidos de calentamiento y enfriamiento pueden generar problemas como tensión residual, agrietamiento o transformaciones de fase no deseadas en ciertos materiales. Para superar estos desafíos, los fabricantes deben seleccionar y controlar cuidadosamente los diversos parámetros que intervienen en la soldadura láser.
Comparación con los métodos de soldadura tradicionales
Si bien la soldadura láser es conocida por su precisión y eficiencia, difiere significativamente de los métodos de soldadura tradicionales, como la soldadura MIG (gas inerte metálico) o la soldadura TIG (gas inerte de tungsteno), en varios aspectos importantes. Los métodos de soldadura tradicionales utilizan arcos eléctricos para generar calor, lo que calienta un área más grande del material y generalmente da como resultado zonas afectadas por el calor más amplias. Estos métodos también tienden a implicar velocidades de soldadura más lentas y una mayor distorsión del material. Por otro lado, la soldadura láser se caracteriza por un haz de energía altamente concentrado, lo que permite velocidades de soldadura más rápidas, zonas afectadas por el calor más estrechas y una distorsión mínima.
Sin embargo, la soldadura láser es más sensible a los cambios en las propiedades del material, el diseño de la unión y los ajustes del láser que los métodos tradicionales. Por ejemplo, los métodos tradicionales pueden ser más tolerantes al soldar materiales más gruesos o uniones con geometrías irregulares, mientras que la soldadura láser requiere un control más preciso de parámetros como la potencia del láser, el enfoque del haz y la velocidad de soldadura. Por lo tanto, la soldadura láser puede no ser la solución ideal para todas las aplicaciones, en particular cuando se trata de materiales o geometrías que suponen un desafío para el proceso.
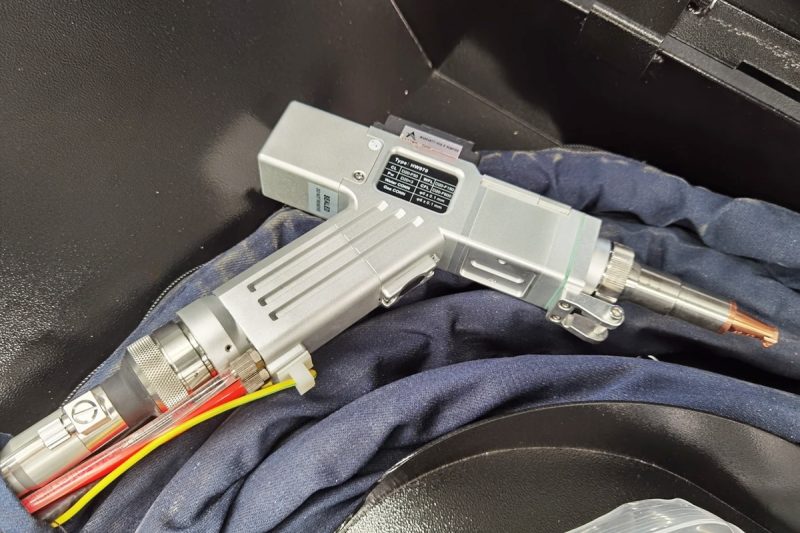
Propiedades materiales
El material que se suelda desempeña un papel importante en el éxito de una operación de soldadura láser. Las propiedades clave del material que influyen en la soldabilidad incluyen la composición del material base, el espesor y la geometría, el punto de fusión, la conductividad térmica y la presencia de elementos de aleación o aditivos.
Composición del material base
La composición química del material base es uno de los factores más importantes que afectan la soldabilidad. Los distintos materiales tienen diferentes puntos de fusión, conductividades térmicas y comportamientos de solidificación, todo lo cual influye en el proceso de soldadura láser. Por ejemplo, los aceros con alto contenido de carbono tienden a formar fases duras y frágiles durante el enfriamiento, lo que aumenta la probabilidad de que se produzcan grietas en la soldadura. De manera similar, los materiales con altos niveles de ciertos elementos de aleación, como el cromo, el níquel o el molibdeno, pueden ser más susceptibles a las transformaciones de fase, lo que podría provocar defectos de soldadura o una reducción de las propiedades mecánicas.
Algunos materiales, como aluminio y cobre, son particularmente difíciles de soldar con láser debido a su alta conductividad térmica y bajos puntos de fusión. Estos materiales requieren una mayor potencia del láser para lograr una penetración adecuada, pero el riesgo de que se quemen también es mucho mayor. Los materiales con un alto coeficiente de expansión, como las aleaciones de titanio, pueden experimentar distorsión térmica durante la soldadura, lo que requiere un control preciso de los parámetros del láser.
Comprender la composición del material que se va a soldar es esencial para determinar los parámetros láser óptimos. Los elementos de aleación y las impurezas del material pueden influir en la forma en que el material responde al calor y en la formación de la soldadura, lo que hace necesario ajustar parámetros como la potencia del láser, el enfoque del haz y el gas de protección.
Espesor y geometría
El espesor del material y la geometría de la unión afectan directamente la energía necesaria para la soldadura y la distribución del calor dentro del material. Para materiales delgados, una potencia láser menor suele ser suficiente, pero se necesita un control cuidadoso para evitar una entrada de calor excesiva que podría causar quemaduras. Para materiales más gruesos, se necesita una potencia láser mayor y velocidades de soldadura más lentas para garantizar una penetración completa y una soldadura sólida.
La geometría de la unión también influye en la forma en que el láser interactúa con el material. Las uniones a tope simples son relativamente fáciles de soldar porque proporcionan una conexión directa entre las dos superficies. Sin embargo, las uniones más complejas, como las uniones en T, las uniones en ángulo o las uniones traslapadas, pueden requerir una atención especial. El ángulo y la alineación de la unión influirán en la capacidad del láser para penetrar y fusionar correctamente los materiales.
Los materiales con geometrías complejas también pueden presentar desafíos adicionales para la soldadura láser debido a las dificultades para alinear el haz con la junta y las variaciones de espesor a lo largo de la junta. Optimizar el diseño de la junta y garantizar la alineación adecuada del haz láser son pasos fundamentales para lograr soldaduras resistentes y de alta calidad.
Punto de fusión y conductividad térmica
El punto de fusión de un material determina la cantidad de energía necesaria para fundirlo. Los materiales con puntos de fusión altos, como el tungsteno, el titanio o los aceros de alta aleación, requieren mucha más energía para alcanzar su punto de fusión y requieren una gestión cuidadosa de la potencia del láser. Por otro lado, los materiales con puntos de fusión bajos, como el aluminio o el zinc, pueden fundirse con demasiada facilidad bajo un rayo láser y pueden requerir velocidades de soldadura rápidas o técnicas de láser pulsado para evitar una fusión excesiva.
La conductividad térmica (la capacidad de un material para conducir el calor) también afecta la soldabilidad. Los materiales con alta conductividad térmica, como el cobre, disipan el calor rápidamente, lo que significa que el rayo láser debe proporcionar suficiente energía para superar esta pérdida de calor y lograr una penetración adecuada. Por el contrario, los materiales de baja conductividad térmica, como el cobre, acero inoxidable, retienen el calor de manera más efectiva, lo que puede generar una zona afectada por el calor (ZAT) más grande y una posible distorsión térmica si no se gestiona adecuadamente.
Elementos de aleación y aditivos
La presencia de elementos de aleación y aditivos puede tener un profundo impacto en la soldabilidad de un material. Los elementos de aleación comunes, como el manganeso, el silicio y el cromo, pueden mejorar las propiedades mecánicas de un material, pero también pueden presentar desafíos durante la soldadura. Por ejemplo, el manganeso puede hacer que la soldadura sea más susceptible a las grietas, mientras que el exceso de silicio puede provocar la formación de fases frágiles en la zona de soldadura.
Se pueden utilizar aditivos como el fundente para mejorar la unión de las superficies, evitar la oxidación o modificar el comportamiento del baño de soldadura. La selección del fundente y otros aditivos debe hacerse con cuidado, ya que pueden influir en la calidad final y las propiedades mecánicas de la soldadura.
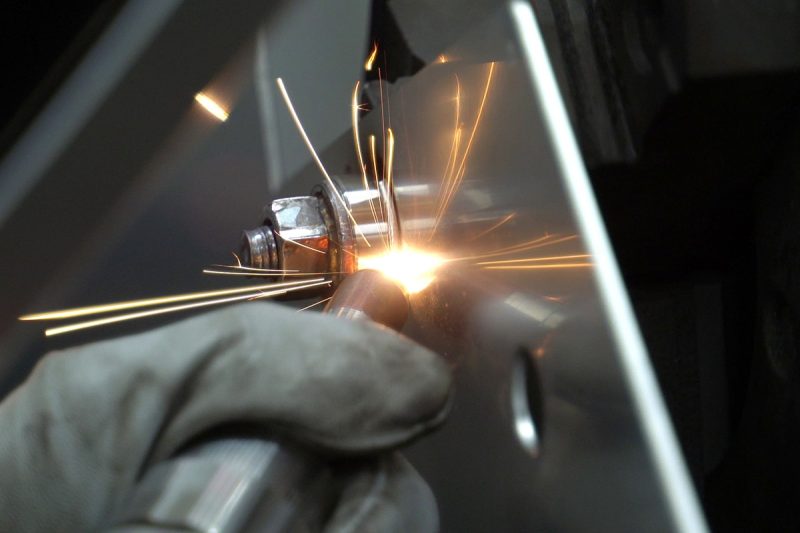
Parámetros del láser
Los parámetros del láser, como la potencia, el enfoque, la velocidad, la calidad del haz y otros, son fundamentales para la soldabilidad de los materiales. Estos parámetros controlan la forma en que el haz láser interactúa con el material, la energía que se entrega al baño de soldadura y la velocidad de solidificación.
Potencia láser
La potencia del láser influye directamente en la profundidad de penetración, la velocidad de soldadura y la cantidad de calor generado durante el proceso. Una mayor potencia del láser produce una penetración más profunda, pero también aumenta el riesgo de quemaduras o de zonas afectadas por el calor excesivo. Es posible que los ajustes de potencia más bajos no proporcionen la energía suficiente para lograr una penetración completa en materiales más gruesos, lo que da como resultado uniones débiles o una fusión incompleta.
La potencia óptima del láser depende del material que se va a soldar, su espesor y las características de soldadura deseadas. En general, se debe lograr un equilibrio entre la potencia suficiente para fundir el material y evitar el exceso de calor que podría distorsionar la pieza de trabajo.
Enfoque láser
El enfoque del láser controla el tamaño y la intensidad del haz láser. Un haz muy enfocado produce un punto pequeño y de alta energía en el material, lo que permite una penetración más profunda y soldaduras más estrechas. Sin embargo, un enfoque demasiado estrecho puede aumentar el riesgo de perforación, especialmente con materiales más delgados. Por el contrario, un haz desenfocado distribuirá la energía sobre un área más grande, lo que reduce el riesgo de perforación, pero también produce una penetración más superficial y soldaduras más anchas.
El enfoque óptimo depende del material, el grosor y la geometría de la junta. Para un control preciso, los sistemas láser suelen tener un enfoque ajustable, lo que permite a los operadores ajustar el haz de acuerdo con los requisitos específicos de la soldadura.
Duración del pulso
En la soldadura láser pulsada, el haz láser se emite en ráfagas de energía cortas e intensas. La duración de estos pulsos (duración del pulso) puede afectar significativamente la profundidad de penetración, la velocidad de enfriamiento y la calidad general de la soldadura. Los pulsos más cortos permiten una entrada de energía más controlada y pueden ayudar a prevenir el sobrecalentamiento, mientras que los pulsos más largos proporcionan más energía para una penetración más profunda.
La duración del pulso debe ajustarse cuidadosamente en función del material y el espesor que se va a soldar. Los pulsos más largos se utilizan normalmente para materiales más gruesos, mientras que los pulsos más cortos se utilizan para materiales delgados para evitar la distorsión térmica.
Calidad del haz
La calidad del haz se refiere a la distribución de energía dentro del haz láser y es un factor esencial para determinar la eficacia con la que el láser puede enfocarse en el material. Un haz de alta calidad tiene un perfil de energía uniforme, lo que permite una entrega de energía constante y una soldadura más estable. Por otro lado, los haces de baja calidad pueden generar una distribución de energía desigual, lo que da como resultado una mala calidad de la soldadura y una formación de juntas inconsistente.
Los sistemas de soldadura láser con haz de alta calidad generalmente producen soldaduras más limpias, precisas y con menos defectos.
Velocidad de soldadura
La velocidad de soldadura afecta el tiempo durante el cual se aplica el láser al material. Las velocidades de soldadura más rápidas generalmente dan como resultado un menor aporte de calor, lo que genera zonas afectadas por el calor más pequeñas y una menor distorsión. Sin embargo, si la velocidad es demasiado alta, es posible que no haya tiempo suficiente para una penetración adecuada, lo que da como resultado uniones débiles. Las velocidades más lentas pueden aumentar el aporte de calor, lo que genera zonas afectadas por el calor más grandes y potencialmente más distorsión, pero pueden ser necesarias para soldar materiales más gruesos.
La velocidad de soldadura óptima está determinada por el tipo de material, el espesor y las características de soldadura deseadas.
Gas protector
El gas de protección se utiliza en la soldadura láser para proteger el baño de soldadura de la contaminación de la atmósfera circundante, que podría provocar oxidación u otros defectos. El tipo de gas de protección utilizado, como argón, nitrógeno o una mezcla de gases, puede afectar la calidad de la soldadura, incluida su resistencia, apariencia y resistencia a la corrosión. Además, el gas de protección puede influir en la disipación de calor y la velocidad de enfriamiento del baño de soldadura, lo que a su vez afecta la microestructura de la soldadura.
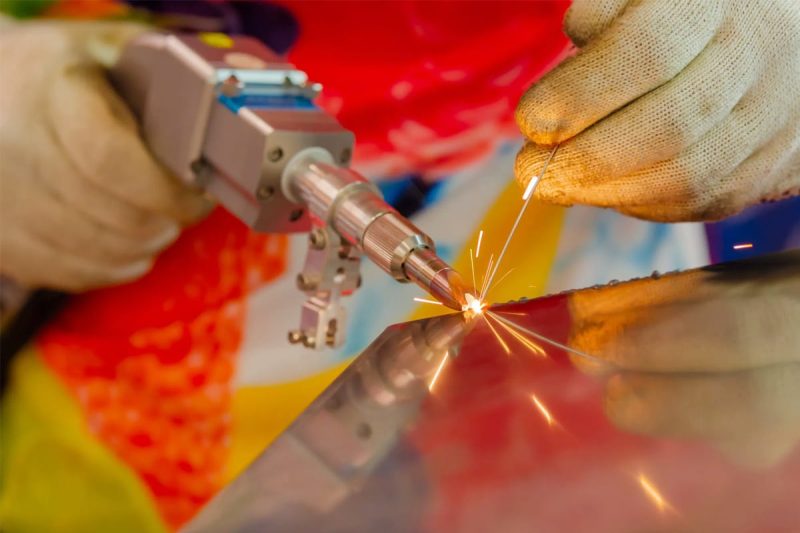
Espesor del material y diseño de juntas
En la soldadura láser, el espesor del material y la geometría de la unión afectan significativamente el proceso de soldadura, la energía requerida y, en última instancia, la calidad de la soldadura. Una comprensión profunda de estos factores es fundamental para lograr soldaduras óptimas con defectos mínimos.
Espesor del material
El espesor del material que se suelda tiene un impacto directo en el proceso de soldadura láser. Los materiales más gruesos requieren una mayor potencia del láser para lograr una penetración completa y crear una unión fuerte. Al soldar materiales más gruesos, es necesario controlar con cuidado la entrada de calor para evitar el sobrecalentamiento y la distorsión. Una configuración de mayor potencia permite una penetración más profunda, pero también puede aumentar el tamaño de la zona afectada por el calor (ZAT), lo que puede afectar las propiedades mecánicas del material base.
En el caso de materiales delgados, se suele utilizar una potencia láser menor para evitar que se quemen, ya que estos materiales requieren menos energía para fundirse. El principal desafío al soldar materiales delgados con láser es equilibrar la potencia del láser para evitar una entrada excesiva de calor y, al mismo tiempo, lograr una penetración suficiente sin dañar el material. La rápida velocidad de enfriamiento de la soldadura láser ayuda a minimizar la zona afectada por el calor en el caso de materiales más delgados.
Geometría de la articulación
La geometría de la unión (como las uniones a tope, las uniones en T, las uniones traslapadas y las uniones en ángulo) desempeña un papel crucial en el éxito de una soldadura láser. La soldadura láser suele funcionar mejor con las uniones a tope, ya que la alineación directa de los bordes del material garantiza un baño de soldadura uniforme. Sin embargo, las uniones más complejas, como las uniones traslapadas o las uniones en T, requieren una alineación cuidadosa del haz, ya que el láser debe garantizar la penetración en todos los lados de la unión, incluidos los espacios que puedan existir entre los materiales.
Cuando la geometría de la unión implica formas complejas o variaciones en el espesor del material, es necesario realizar ajustes en los parámetros de soldadura. Por ejemplo, las uniones a solape requieren un control preciso del enfoque del láser y del ángulo del haz para garantizar que el material superior se fusione de manera efectiva con el material inferior. Las soldaduras de filete también requieren un control cuidadoso de la interacción del haz láser con las superficies de la unión, ya que los ángulos y la proximidad del material pueden influir en la distribución del calor.
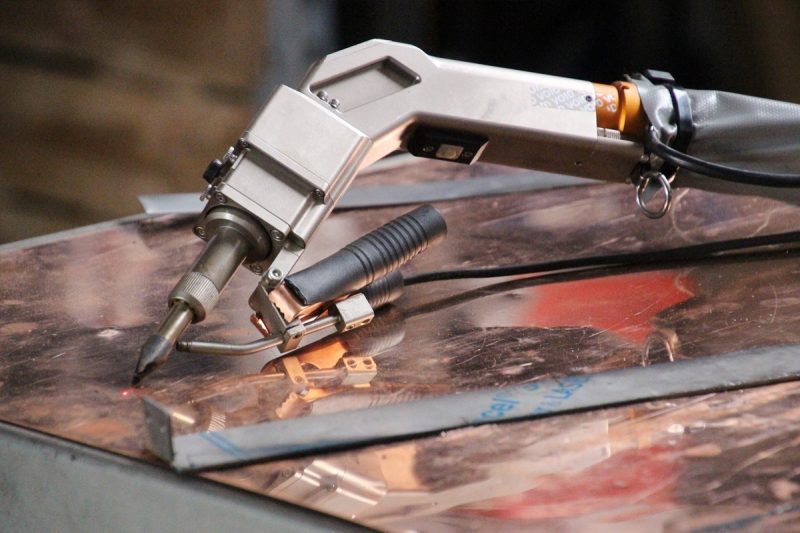
Gestión del calor y velocidad de enfriamiento
La gestión eficaz del calor es fundamental en la soldadura láser para controlar las propiedades del material, minimizar la distorsión y evitar defectos en la soldadura. Los aspectos clave de la gestión del calor incluyen la zona afectada por el calor (ZAT) y la velocidad de enfriamiento.
Zona Afectada por el Calor (HAZ)
La zona afectada por el calor (ZAT) es la región del material que no se funde pero que experimenta un cambio en la microestructura debido a las altas temperaturas durante la soldadura. El tamaño y la extensión de la ZAT están determinados por la potencia del láser, la velocidad de soldadura y el tipo de material. En la soldadura láser, la ZAT tiende a ser más pequeña en comparación con los métodos de soldadura tradicionales debido al calor concentrado del haz láser. Sin embargo, incluso una ZAT pequeña puede afectar las propiedades del material, especialmente en el caso de aceros de alta resistencia o materiales que son sensibles a los ciclos térmicos.
Para ciertos materiales, como aceros con alto contenido de carbono En el caso de las aleaciones de titanio o de titanio, una ZAT más grande puede provocar una reducción de las propiedades mecánicas, como un comportamiento frágil o un agrietamiento por corrosión bajo tensión. Como resultado, es esencial controlar cuidadosamente los parámetros del láser, especialmente la potencia y la velocidad, para minimizar la ZAT y, al mismo tiempo, lograr una fusión adecuada en la interfaz de la unión.
Velocidad de enfriamiento
La velocidad de enfriamiento, o la velocidad a la que se solidifica el baño de soldadura fundida, es un factor crítico para determinar la microestructura final y las propiedades mecánicas de la soldadura. La soldadura láser generalmente da como resultado velocidades de enfriamiento muy rápidas debido a la pequeña zona afectada por el calor y la solidificación rápida del baño de soldadura fundida. Las velocidades de enfriamiento más rápidas pueden dar como resultado una microestructura más fina, lo que puede mejorar la resistencia de la soldadura. Sin embargo, este enfriamiento rápido también puede introducir tensiones residuales, lo que puede provocar grietas o distorsión en ciertos materiales, especialmente aquellos con alta templabilidad, como los aceros con alto contenido de carbono.
Una velocidad de enfriamiento más lenta puede reducir el riesgo de agrietamiento, pero puede dar lugar a la formación de granos más grandes, lo que puede reducir la resistencia general de la soldadura. Controlar la velocidad de enfriamiento es vital para equilibrar estos factores. Se pueden emplear técnicas como el tratamiento térmico posterior a la soldadura (por ejemplo, recocido) para aliviar las tensiones residuales y mejorar las propiedades finales del material.
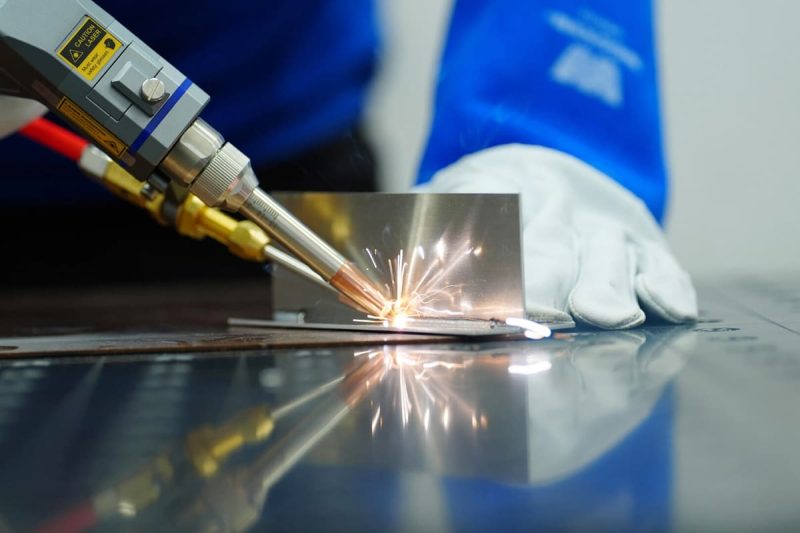
Equipos y configuración de soldadura láser
La calidad de la soldadura láser está muy influenciada por el tipo y la configuración del equipo de soldadura láser. Los componentes clave del equipo incluyen la fuente láser, la lente de enfoque, la óptica y el cabezal de soldadura.
Tipo de fuente láser
El tipo de láser utilizado en el proceso de soldadura afecta a varios aspectos de la operación, como la calidad del haz, la potencia y el enfoque. Los tipos de láser más comunes para soldadura incluyen láseres de CO2, láseres de fibra y láseres de disco:
- Láseres de CO2: Son los láseres más utilizados en soldadura industrial por su alta potencia y versatilidad. Los láseres de CO2 son ideales para soldar materiales de mayor espesor y proporcionan una calidad de haz estable.
- Láseres de fibra: estos láseres son conocidos por la alta calidad y eficiencia de su haz, lo que los hace especialmente eficaces para la soldadura de chapa fina. Los láseres de fibra ofrecen velocidades de soldadura más rápidas y pueden lograr una mayor precisión que los láseres de CO2, especialmente en materiales con baja conductividad térmica.
La elección de la fuente láser adecuada depende del tipo de material, el grosor y los requisitos de la aplicación.
Lentes de enfoque y ópticas
El haz láser debe enfocarse sobre la pieza de trabajo para lograr el tamaño de soldadura y la penetración deseados. La calidad y la alineación de la lente de enfoque y la óptica desempeñan un papel fundamental en la precisión del haz y la calidad de la soldadura. Un sistema óptico de alta calidad garantiza que el haz láser se mantenga estable y enfocado, lo que es especialmente importante para aplicaciones de alta precisión.
La distancia focal de la lente, el tamaño de la apertura y la posición de la lente pueden influir en la forma en que se distribuye la energía sobre la superficie del material. Una óptica mal alineada puede provocar desenfoque, lo que da como resultado una entrega de energía inconsistente y soldaduras potencialmente débiles o defectuosas.
Cabezal de soldadura y óptica de enfoque
El cabezal de soldadura es el encargado de dirigir el haz láser sobre el material. La configuración del cabezal de soldadura, incluida su posición, inclinación y movimiento, afecta la uniformidad y la calidad de la soldadura. El cabezal de soldadura debe estar alineado con precisión con el material para garantizar que el haz láser permanezca enfocado en la unión durante todo el proceso de soldadura.
Además del cabezal de soldadura, las ópticas de enfoque, que dan forma y dirigen el haz, necesitan un mantenimiento y una calibración adecuados. Cualquier desalineación o degradación en estas ópticas puede provocar una entrega inconsistente del haz y una mala calidad de la soldadura.
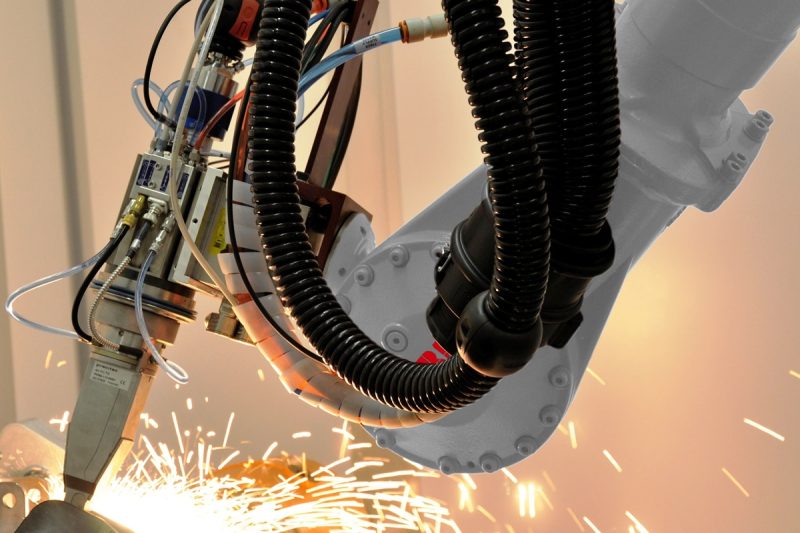
Condiciones ambientales
Las condiciones ambientales en las que se realiza la soldadura láser pueden tener un efecto significativo en la calidad y la consistencia de la soldadura. Los factores ambientales clave que se deben tener en cuenta incluyen la temperatura ambiente y el flujo de aire.
Temperatura ambiente
Las temperaturas extremas pueden afectar la respuesta del material al proceso de soldadura láser. Por ejemplo, los materiales pueden volverse quebradizos a bajas temperaturas, lo que puede aumentar la probabilidad de que se agrieten durante la soldadura. Por el contrario, las temperaturas ambientales altas pueden provocar una distorsión excesiva del material o una expansión térmica, lo que puede afectar la alineación de la unión y la consistencia de la soldadura. Mantener una temperatura ambiente estable es crucial para garantizar que el material responda de manera predecible al proceso de soldadura.
Flujo de aire y contaminantes
La presencia de contaminantes como polvo, aceite, humedad o humos puede afectar el proceso de soldadura de varias maneras. Los contaminantes en el aire pueden absorber parte de la energía del láser, lo que reduce la eficiencia del proceso. Además, las impurezas en la superficie del material pueden provocar oxidación, corrosión u otros defectos que comprometan la calidad de la soldadura.
Controlar el entorno de soldadura a través de una ventilación adecuada, superficies limpias y una cámara de soldadura cerrada puede ayudar a reducir el riesgo de contaminación y garantizar soldaduras más consistentes.

Tratamiento post-soldadura
Una vez completado el proceso de soldadura láser, pueden ser necesarios tratamientos posteriores a la soldadura para mejorar las propiedades mecánicas, aliviar tensiones residuales y garantizar que la soldadura cumpla con las especificaciones requeridas.
Recocido
El recocido es un proceso de tratamiento térmico en el que el material soldado se calienta a una temperatura específica y luego se enfría lentamente. Este proceso se utiliza para aliviar las tensiones residuales que pueden haberse introducido durante las fases rápidas de calentamiento y enfriamiento del proceso de soldadura. El recocido ayuda a restaurar la ductilidad del material y a reducir el riesgo de agrietamiento.
En la soldadura láser, los materiales que experimentan velocidades de enfriamiento rápidas pueden requerir un recocido para evitar la fragilización y mejorar la tenacidad de la soldadura. La temperatura exacta del recocido y su duración dependen del tipo de material y de los requisitos específicos de la soldadura.
Acabado y limpieza de superficies
Después de soldar, la superficie de la soldadura puede presentar oxidación, sarro u otros contaminantes que deben eliminarse. La limpieza y el acabado de la superficie de la soldadura son esenciales para garantizar una apariencia lisa y sin defectos y para mejorar la resistencia a la corrosión del área soldada.
La limpieza puede implicar técnicas como pulido mecánico, decapado químico o limpieza con chorro abrasivo. El acabado adecuado de la superficie es particularmente importante en industrias donde la estética de la soldadura y la integridad del material son primordiales, como en los dispositivos médicos o los productos electrónicos de consumo.
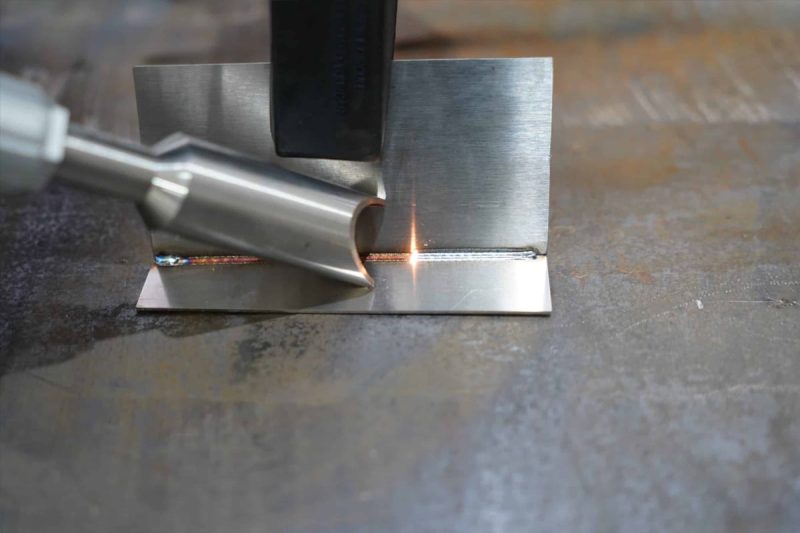
Desafíos en la soldadura láser
Si bien la soldadura láser ofrece muchas ventajas, también conlleva sus propios desafíos. Los problemas más comunes incluyen porosidad, grietas, distorsión y calidad de soldadura inconsistente.
Porosidad
La porosidad se produce cuando se forman bolsas de gas dentro del baño de soldadura, lo que genera espacios vacíos en la soldadura. Esto suele deberse a gases atrapados, como nitrógeno u oxígeno, que quedan atrapados durante el proceso de solidificación. La porosidad puede debilitar la soldadura y afectar su rendimiento. El uso de gas de protección adecuado, un control cuidadoso de los parámetros de soldadura y la garantía de que las superficies estén limpias antes de soldar pueden ayudar a minimizar la porosidad.
Agrietamiento y distorsión
El agrietamiento es un problema importante en la soldadura láser, en particular en materiales con alto contenido de carbono o baja ductilidad. Las rápidas velocidades de enfriamiento de la soldadura láser pueden crear altas tensiones residuales, que pueden provocar agrietamiento, especialmente en la zona afectada por el calor.
La distorsión también puede producirse debido a un calentamiento y enfriamiento desiguales, que provocan que el material se deforme o se deforme. La gestión del aporte de calor mediante parámetros láser óptimos y el uso de técnicas de sujeción pueden ayudar a reducir la distorsión.
Inconsistencia en la calidad de la soldadura
La calidad inconsistente de la soldadura puede surgir de variaciones en las propiedades del material, los parámetros del láser o factores ambientales. Las fluctuaciones en la potencia o el enfoque del láser, la desalineación de las uniones o los cambios en el flujo del gas de protección pueden contribuir a la formación de soldaduras inconsistentes. Para minimizar estas inconsistencias, es esencial mantener un control estricto sobre el proceso de soldadura y calibrar regularmente el equipo para garantizar la uniformidad en todas las soldaduras.
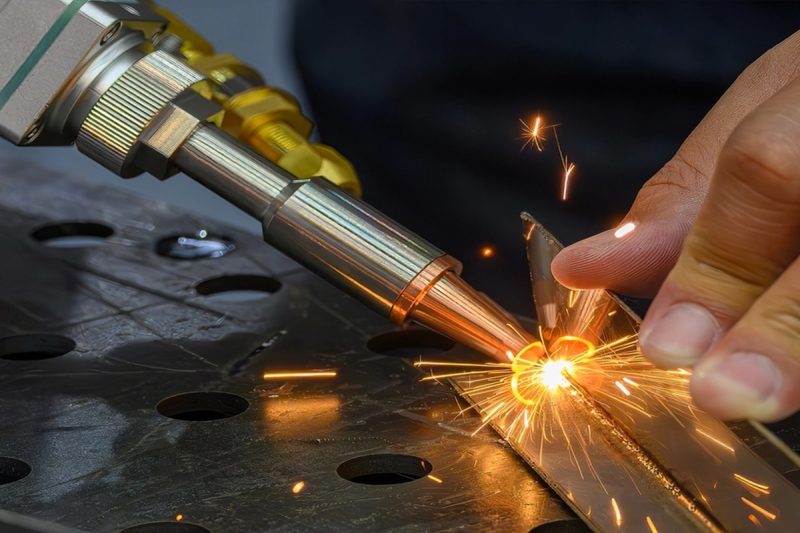
Resumen
En la soldadura láser, la soldabilidad de los materiales depende de una amplia gama de factores, desde la composición y el espesor del material hasta los parámetros del láser y las condiciones ambientales externas. Al comprender estos factores y optimizarlos, los fabricantes pueden producir soldaduras de alta calidad que cumplan con los estrictos requisitos de resistencia, durabilidad y apariencia. Si bien pueden surgir problemas como porosidad, agrietamiento y distorsión durante el proceso de soldadura, un control y una selección cuidadosos de los parámetros de soldadura, el equipo y los tratamientos posteriores a la soldadura pueden mitigar estos problemas y mejorar la consistencia y confiabilidad de la soldadura láser en una variedad de materiales y aplicaciones.
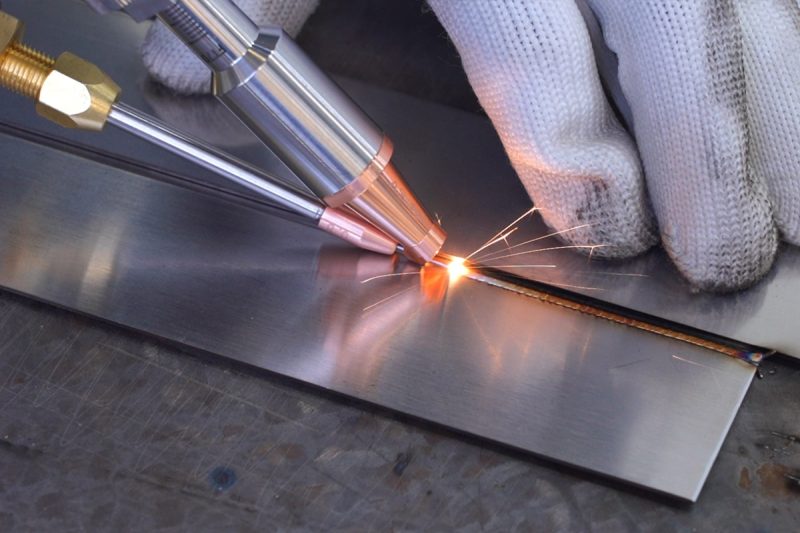
Obtenga soluciones de soldadura láser
Para las empresas que buscan soldaduras confiables y de alta calidad, AccTek Laser ofrece soluciones de soldadura láser de vanguardia diseñadas para satisfacer diversas necesidades industriales. Como fabricante profesional de máquinas de corte, soldadura, limpieza y marcado láser, AccTek Laser ofrece equipos de última generación diseñados para optimizar la soldabilidad. Ya sea que trabaje con metales, plásticos o compuestos, nuestras máquinas de soldadura láser ofrecen precisión, velocidad y eficiencia incluso para las aplicaciones más desafiantes.
Láser AccTek máquinas de soldadura láser Están diseñados para manejar diversos materiales y espesores, con configuraciones personalizables para potencia del láser, duración del pulso, enfoque y velocidad de soldadura, lo que garantiza que sus soldaduras cumplan con los estándares más altos. Nuestro equipo de expertos puede ayudarlo a seleccionar el equipo adecuado, configurar el sistema para sus necesidades específicas y ofrecer soporte continuo para garantizar un rendimiento óptimo durante todo el proceso de producción.
Al elegir AccTek Laser, obtiene acceso a tecnología avanzada y a un socio comprometido a mejorar su calidad y productividad de soldadura, lo que en última instancia lo ayudará a lograr soldaduras impecables y duraderas en todo momento.
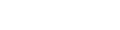
Información del contacto
- [email protected]
- [email protected]
- +86-19963414011
- No. 3 Zona A, Zona Industrial de Lunzhen, Ciudad de Yucheng, Provincia de Shandong.
Obtenga soluciones láser