Laser Welding Machine
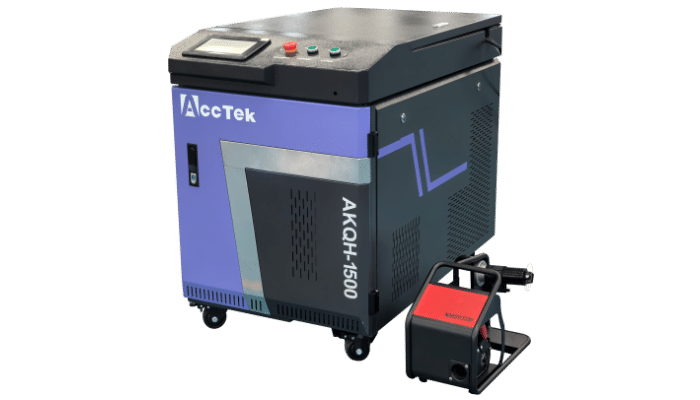
Product Range
-
Handheld Laser Welding Machine
Rated 5.00 out of 5$3,200.00 – $6,400.00 Select options This product has multiple variants. The options may be chosen on the product page -
Portable Laser Welding Machine
Rated 4.75 out of 5$3,100.00 – $7,500.00 Select options This product has multiple variants. The options may be chosen on the product page -
Double Wobble Laser Welding Machine
Rated 4.75 out of 5$3,700.00 – $6,900.00 Select options This product has multiple variants. The options may be chosen on the product page -
Automatic Wire Feeder Laser Welding Machine
Rated 4.75 out of 5$3,200.00 – $6,400.00 Select options This product has multiple variants. The options may be chosen on the product page -
Portable Air-Cooled Laser Welding Machine
Rated 5.00 out of 5$4,500.00 – $6,200.00 Select options This product has multiple variants. The options may be chosen on the product page -
3 In 1 Laser Welding Cutting Cleaning Machine
Rated 4.75 out of 5$3,200.00 – $6,400.00 Select options This product has multiple variants. The options may be chosen on the product page -
Laser Welding Robot
Rated 4.75 out of 5$12,900.00 – $16,600.00 Select options This product has multiple variants. The options may be chosen on the product page
Optional Laser Welding Machine Power
Materials That Can Be Welded
Laser Welding VS. Other Methods
Laser Welding vs. MIG Welding
MIG welding is fast and cost-effective for thicker materials, but it generates more heat, which can cause material distortion and require additional post-processing. Laser welding, on the other hand, provides more precise control with minimal heat, resulting in cleaner, stronger welds and less need for finishing, even on delicate or thin materials.
Laser Welding vs. TIG Welding
TIG welding is known for its high-quality welds, especially in thin materials. However, it is slower and requires skilled operators. Laser welding, in comparison, offers faster processing times, higher automation, and improved precision, making it ideal for high-volume production with complex joint designs while reducing operator skill dependency.
Laser Welding vs. Spot Welding
Spot welding is commonly used for joining thin metal sheets, but it can struggle with thicker materials and lacks precision in controlling weld depth. Laser welding provides greater versatility, capable of welding a wider range of materials and thicknesses, with superior precision and minimal heat distortion, making it ideal for high-strength and intricate welds.
Why Choose AccTek Laser
Industry-Leading Technology
We use the latest laser technology to ensure our machines deliver unmatched precision, speed, and efficiency. AccTek Laser welding machines are built to provide high-quality results, minimizing heat distortion and maximizing weld strength for a wide range of materials.
Customizable Solutions
Our laser welding machines offer customizable power settings, laser types, and control systems, allowing you to tailor the equipment to your specific needs. Whether you're working with delicate components or heavy-duty applications, we provide flexible solutions for every project.
Exceptional Build Quality
AccTek Laser machines are engineered for durability and long-lasting performance. Built with high-quality materials and advanced engineering, our machines are designed to withstand rigorous production environments, ensuring reliable operation with minimal maintenance.
Precision and Accuracy
AccTek Laser welding machines are known for their exceptional precision, ensuring clean, accurate welds every time. Our advanced control systems allow you to achieve tight tolerances and complex weld geometries with ease, even on delicate or intricate materials.
Excellent Customer Support
We pride ourselves on offering outstanding customer support, from initial consultation to installation and after-sales service. Our team of experts is available to assist with machine setup, training, and troubleshooting, ensuring you get the most out of your investment.
Competitive Pricing
At AccTek Laser, we offer high-performance laser welding machines at competitive prices. We understand the need for cost-effective solutions without compromising on quality, making our machines an excellent value for businesses of all sizes.
Frequently Asked Questions
What Are Laser Welding Machines?
Does Laser Welding Machines Use Welding Wire?
- Filling Gaps: If there is a significant gap between the parts being welded, filler wire can be added to help fill the joint and ensure a stronger bond.
- Welding Thin Materials: When welding very thin materials or delicate components, welding wire might be used to add more control and improve the strength of the joint.
- Special Alloys: Some advanced materials or alloys may require filler material to ensure the weld’s structural integrity or compatibility with the base material.
What Are The Operating Costs of Laser Welding Machines?
- Electricity Consumption: Laser welding machines require electricity to power the laser generator, cooling system, and other components. Energy consumption may vary depending on factors such as the laser generator’s power output, duty cycle, and operating duration.
- Laser Consumables: While laser welding typically does not require consumables such as filler materials, certain components within the laser system may require periodic replacement, such as laser optics, protective windows, or gas components in some types of lasers.
- Maintenance and Upkeep: Regular maintenance and upkeep can keep your laser welding machine running efficiently and ensure its service life. This may include cleaning optics, replacing worn parts, aligning the laser beam, and repairing the cooling system. Maintenance costs may vary depending on the frequency of use and complexity of the machine.
- Gas Consumption: Some laser welding processes may require the use of a shielding gas, such as argon or helium, to protect the weld pool from atmospheric contamination. The cost of these gases may impact overall operating expenses.
- Operator Training and Labor Costs: Operators need to be properly trained to use laser welding machines efficiently and safely. Consideration should be given to the labor costs associated with operating the machine and any additional labor required for set-up, programming, and quality control.
- Facility Cost: Operating laser welding machines requires a suitable facility with proper ventilation, safety measures, and environmental controls. Facility costs such as rent, utilities, and insurance make up overall operating expenses.
- Consumable Materials: Depending on the application, additional consumable materials such as filler wire or flux may be required, increasing operating costs.
- Depreciation and Amortization: Your laser welding machine depreciates over time, and calculating depreciation and amortization can give you an idea of the true cost of ownership.
What Are The Disadvantages of Laser Welding Machines?
- Initial Cost: Laser welding machines tend to have higher upfront costs compared to traditional welding equipment. The initial investment includes the purchase of the machine itself, installation, and potential training of the operator.
- Material Limitations: Laser welding is most effective on metals with good optical absorption properties, such as steel, aluminum, and titanium. Welding certain materials, such as highly reflective metals or non-metallic materials, using laser welding can be challenging or impractical.
- Joint Accessibility: Laser welding requires a line of sight into the welding area, which may limit its suitability for joining complex or closed geometries. Access restrictions can make it challenging to weld certain parts without additional fixing or manipulation.
- Thermal Sensitivity: Laser welding generates intense heat in localized areas, which can cause thermal deformation, especially on thin materials or parts with heat-sensitive components nearby. Proper thermal management techniques such as pulse welding or the use of filler materials may be required to mitigate this problem.
- Skills and Training Requirements: Operating laser welding machines requires specialized training and expertise due to the complex setup, programming, and safety considerations involved. Skilled operators achieve high-quality welds and maximize equipment efficiency.
- Maintenance and Downtime: Laser welding machines require regular maintenance to ensure optimal performance and reliability. Downtime for maintenance or repairs may impact production schedules, and alternate welding methods may be required to maintain workflow continuity.
- Safety Issues: Laser welding involves the use of high-energy laser beams, which can pose safety risks to operators if used incorrectly. To minimize the risk of accident or injury, protective measures such as safety fencing, laser safety glasses, and proper training must be taken.
- Welding Speed: While laser welding is often faster than traditional welding methods in some applications, it may not always be the fastest option, especially for thick materials or large parts. Achieving deep penetration in thick materials may require multiple passes, which increases cycle time.
Does Laser Welding Need Gas?
- Gas Shielding: In some laser welding processes, particularly those involving metals, shielding gas may be used to protect the weld pool from atmospheric contamination. Common shielding gases include argon, helium, nitrogen, or a mixture of these gases. The choice of shielding gas depends on factors such as the material being welded and the desired welding characteristics.
- Gas Assist: In laser welding of certain materials, such as plastics or ceramics, gas may be used as an assist gas to help improve the quality of the weld. The assist gas can help remove debris, control heat dissipation, or enhance the penetration depth, depending on the specific requirements of the welding process.
- No Gas Option: However, there are laser welding processes where gas is not required. For example, in laser welding of certain plastics or some specialized metal welding applications, gas may not be necessary or may even be detrimental to the process.
How Do Laser Welding Machines Create The Smallest Heat-Affected Zone?
- High Energy Density: Laser welding concentrates a high amount of energy into a small spot size, resulting in a very high energy density at the weld point. This intense heat rapidly heats and melts the material in the weld zone while minimizing heat transfer to the surrounding areas.
- Short Interaction Time: The duration of laser heating is extremely brief, typically on the order of milliseconds. This short interaction time means that only a small volume of material is subjected to the intense heat, resulting in minimal thermal diffusion into the adjacent regions.
- Precise Control: Laser welding machines offer precise control over parameters such as laser power, pulse duration, pulse frequency, and beam focusing. Operators can adjust these parameters to optimize energy delivery to the weld zone, ensuring sufficient penetration depth while minimizing excessive heating of the surrounding material.
- Focused Beam: Laser beams can be tightly focused using optical components such as lenses or mirrors. By focusing the laser beam onto a small spot size, the energy is concentrated, allowing for deep penetration into the workpiece while limiting the spread of heat to adjacent areas.
- Non-Contact Process: Laser welding is a non-contact process, meaning there is no physical contact between the heat source (laser beam) and the workpiece. This eliminates the need for a heat-affected zone to accommodate heat-affected regions caused by direct contact, as seen in processes like gas metal arc welding (GMAW) or shielded metal arc welding (SMAW).
- Minimal Energy Input: Laser welding delivers energy to the workpiece in a highly controlled manner, with minimal heat input compared to traditional welding methods. This reduces the overall thermal effects on the material, resulting in a smaller heat-affected zone.
Is Laser Welding Safe?
- Eye Protection: Direct exposure to the intense light produced by laser beams may cause eye injury, including retinal damage and blindness. The operator and anyone near the laser welding area must wear appropriate laser safety glasses with the correct optical density to block the specific wavelengths emitted by the laser.
- Skin Protection: Skin exposure to laser beams may cause burns and tissue damage. Operators should wear appropriate protective clothing, including long-sleeved garments made of non-flammable materials, gloves, and aprons, to minimize the risk of skin injury.
- Ventilation and Fume Extraction: Laser welding can produce smoke, gases, and vapors, depending on the materials being welded. Adequate ventilation and fume extraction systems should be provided to remove airborne contaminants from the welding area and prevent their accumulation, ensuring a safe working environment for operators.
- Fire Safety: Laser welding generates heat that can cause a fire, especially when working with flammable materials or in an environment containing flammable substances. Fire prevention measures such as the use of fire barriers, fire extinguishers, and appropriate housekeeping measures should be taken to reduce the risk of fire incidents.
- Electrical Safety: Laser welding machines require electricity to operate, and precautions should be taken to prevent electrical hazards such as electric shock or electrocution. Machines should be properly grounded and electrical connections should be checked regularly for signs of damage or wear.
- Training and Supervision: Operators should receive comprehensive training in laser safety procedures, including proper operation of equipment, handling of laser hazards, and emergency response protocols. Supervision by trained personnel ensures that safe laser welding practices are always followed.
- Controls: Engineering controls, administrative controls, and personal protective equipment (PPE) should be implemented to minimize laser hazards. This may include safety interlocks on the equipment, restricting access to the laser area, and using barriers or enclosures to contain laser radiation.
What Maintenance Is Required For Laser Welding Machines?
- Cleaning Optics: Laser optics, including lenses and mirrors, should be cleaned regularly to remove dust, dirt, and other contaminants that may affect beam quality and efficiency. Cleaning should be done carefully using appropriate cleaning solutions and lint-free materials to avoid scratching or damaging the optics.
- Check Beam Alignment: Regularly checking beam alignment ensures that the laser beam is properly focused and directed onto the workpiece. Misalignment can result in reduced weld quality and efficiency. If a deviation is detected, adjustments may be needed to realign the beam.
- Cooling System Maintenance: Laser welding machines usually have a cooling system to dissipate the heat generated during operation. Regular maintenance of cooling components such as pumps, filters, and heat exchangers can prevent overheating and ensure proper cooling performance.
- Inspect and Replace Consumable Parts: Certain components within a laser system, such as laser optics, protective windows, and gas filters, may wear out over time and require replacement. Regular inspections should be performed to identify worn or damaged parts and replace them as necessary to maintain optimal performance.
- Check the Gas Delivery System: If the laser welding process requires the use of shielding or auxiliary gases, the gas delivery system should be checked regularly for leaks, blockages, or other problems. Gas flow rates and pressures should be adjusted as needed to maintain optimal welding conditions.
- Check the Beam Quality: Monitoring and evaluating the beam quality of the laser output can detect any deviations or anomalies that may indicate problems with the laser system. Beam quality checks should be performed regularly using appropriate diagnostic tools and procedures
- Software Updates and Calibration: Laser welding machines may be equipped with software to control welding parameters and monitor performance. Regular software updates and calibration checks help ensure accurate operation and compatibility with evolving industry standards.
- Safety Inspections: Safety inspections should be conducted regularly to ensure compliance with safety standards and regulations. This includes checking emergency stop systems, interlocks, safety fences, and other safety features to prevent accidents and protect operators.
Related Resources
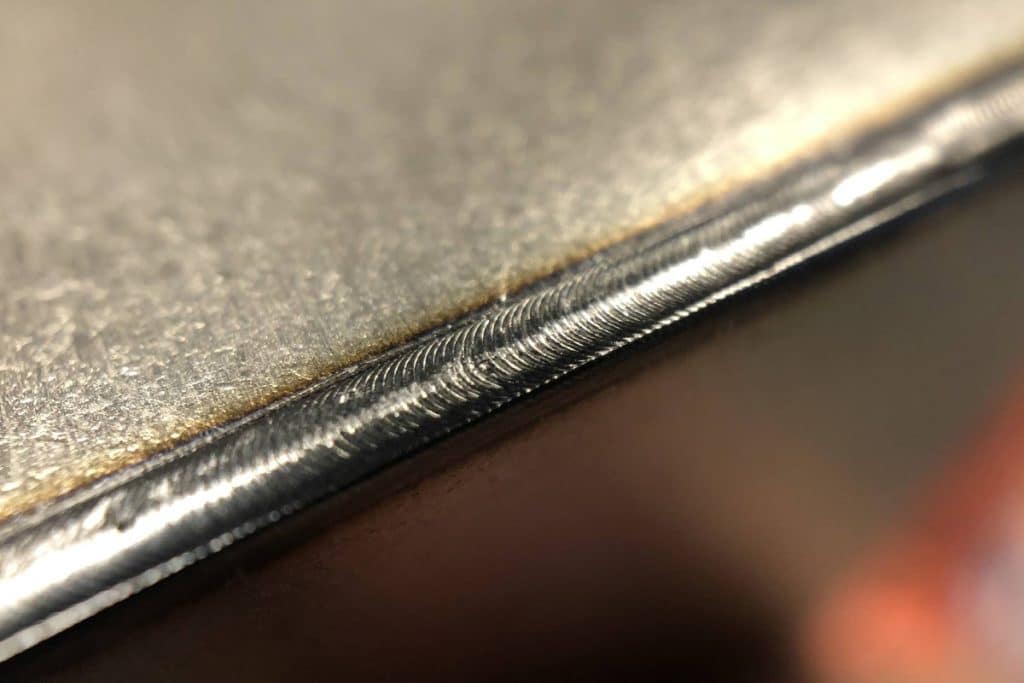
How Does Laser Welding Achieve Deep Melting of Materials?
This article mainly discusses how laser welding can achieve deep melting of materials, including its basic principles, key factors affecting penetration depth, the formation mechanism of deep penetration, and optimization
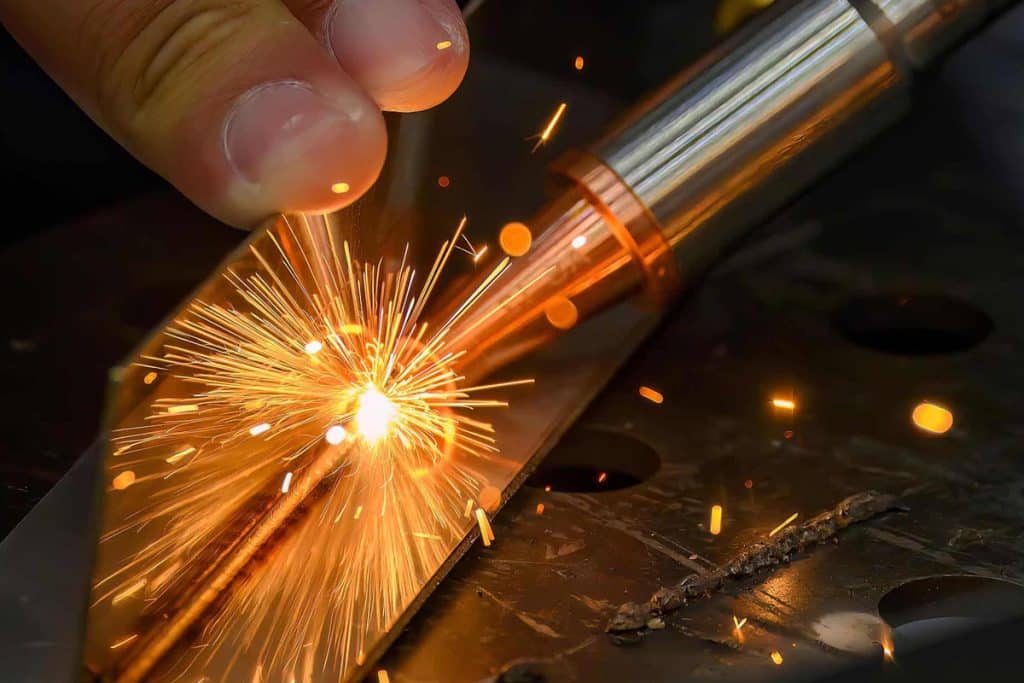
What Are the Challenges of Laser Welding Thin Materials?
This article will explore the challenges and response strategies of thin materials laser welding to help manufacturers master this technology and improve production efficiency and product quality.

Laser Welding Joint Design
This paper mainly discusses the basic principles, influencing factors, and optimization strategies of laser welding joint design to improve welding quality, optimize production efficiency, and ensure the integrity and strength