
Руководство по устранению неполадок станка для лазерной резки CO2
В современном промышленном производстве Станок для лазерной резки CO2 служит эффективным и точным режущим инструментом. Он широко используется при обработке различных материалов, в том числе металла, пластика и дерева. Однако, как и любое механическое оборудование, станки для лазерной резки CO2 иногда выходят из строя, что влияет на эффективность производства и качество резки. Чтобы помочь пользователям лучше понять и решить эти проблемы, в этой статье представлено руководство по устранению неполадок станка для лазерной резки CO2, в котором описаны распространенные неисправности и их решения для обеспечения нормальной работы и производственной эффективности оборудования.
В этой статье мы углубимся в распространенные неисправности станков для лазерной резки CO2, в том числе объясним важность устранения неисправностей станков для лазерной резки CO2, типичные явления неисправностей и возможные причины, шаги по устранению неполадок и решения, а также эффективные профилактические меры и рекомендации по техническому обслуживанию. . Помогите пользователям быстро и точно устранять возникающие проблемы, обеспечивая тем самым непрерывность производства и стабильность качества.

Важность устранения неисправностей станков для лазерной резки CO2
Станки для лазерной резки CO2 играют жизненно важную роль в современном промышленном производстве, и устранение неисправностей имеет большое значение для обеспечения их нормальной работы и эффективности производства. Вот несколько ключевых моментов, касающихся важности устранения неполадок:
- Гарантия эффективности производства: отказ станка для лазерной резки CO2 может привести к остановке производственной линии, что приведет к снижению эффективности производства. Своевременное и эффективное устранение неполадок может сократить время простоя производства и обеспечить ход производства и соблюдение сроков поставки.
- Экономия средств. Устранение неполадок может снизить производственные затраты, избегая ненужных задержек производства и простоев. Длительные простои приводят не только к потерям производства, но также могут потребовать дополнительных затрат на ремонт и техническое обслуживание.
- Гарантия качества продукции: Выход из строя станка для лазерной резки CO2 может привести к снижению качества резки и получению бракованной продукции. Своевременное устранение неполадок позволяет обеспечить стабильность и постоянство качества продукции, а также повысить удовлетворенность клиентов.
- Продление срока службы оборудования. Регулярное устранение неисправностей позволяет вовремя обнаружить и устранить потенциальные проблемы, избежать дальнейшего ухудшения состояния неисправностей и продлить срок службы станка для лазерной резки CO2.
- Гарантия безопасности: некоторые неисправности могут создать угрозу безопасности операторов и оборудования. Благодаря устранению неполадок можно вовремя устранить угрозы безопасности, чтобы обеспечить безопасность операторов и оборудования.
Таким образом, важность устранения неисправностей станков для лазерной резки CO2 очевидна. Только путем своевременного и эффективного устранения неисправностей можно обеспечить нормальную работу оборудования, повысить эффективность производства, обеспечить качество продукции, продлить срок эксплуатации оборудования.

Типичные неисправности и возможные причины
Станки для лазерной резки CO2 часто сталкиваются с различными сбоями в процессе резки различных материалов. Эти неисправности могут привести к снижению качества резки, снижению эффективности производства и даже повлиять на срок службы и безопасность оборудования. Ниже будут описаны распространенные явления неисправностей и возможные причины машин для лазерной резки CO2:
Снижение качества резки
Явление неисправности:
- Появляются подгоревшие или зазубренные края.
- Режущая поверхность неровная, гофрированная или неровная.
Возможные причины:
- Оптическая линза загрязнена или изношена: Оптическая линза является ключевым компонентом, фокусирующим лазерный луч на поверхности заготовки. Когда поверхность линзы подвержена воздействию пыли, масла или износа, это влияет на эффект фокусировки лазерного луча, что приводит к снижению качества резки.
- Скорость резки слишком высокая или слишком медленная: Скорость резки зависит от типа и толщины материала. Если скорость слишком высокая, материал может не расплавиться полностью, а если скорость слишком низкая, качество режущей поверхности ухудшится.
- Неточная фокусировка лазерного луча. Если фокусировка лазерного луча неточная, плотность энергии в точке резки будет неравномерной, что приведет к неровности режущей поверхности или обгоранию краев.
Нестабильная скорость резания.
Явление неисправности:
- Внезапные изменения или колебания скорости резания.
- Линии разреза прерывистые или имеют скачки.
Возможные причины:
- Нестабильный источник питания: станки для лазерной резки CO2 предъявляют высокие требования к стабильному источнику питания. Колебания источника питания или нестабильность напряжения напрямую влияют на выходную мощность лазера, что приводит к нестабильной скорости резки.
- Повреждение оптических компонентов: К оптическим компонентам относятся зеркала и линзы. Если какой-либо из них поврежден или испачкан, это повлияет на передачу и фокусировку лазерного луча, что приведет к нестабильной скорости резки.
- Отказ системы управления. Отказ системы управления может привести к неточной или неправильной регулировке скорости резания, что потребует повторной калибровки или замены неисправных деталей.
Детали режущей головки повреждены
Явление неисправности:
- Детали режущей головки сильно изношены.
- Линзы треснули или отвалились
Возможные причины:
- Износ компонентов режущей головки: Компоненты режущей головки изнашиваются при длительной интенсивной работе, особенно сопло режущего газа и защитная накладка. Сильный износ повлияет на качество и эффективность резки.
- Линза сломана или отсоединена: Линза является важной частью оптической линзы. Если он поврежден или отсоединен, он напрямую повлияет на передачу и фокусировку лазерного луча, что приведет к снижению качества резки.
Проблемы с газоснабжением
Явление неисправности:
- Снижение качества резки
- Скорость резания нестабильна.
Возможные причины:
- Нестабильный поток газа: во время процесса резки поток газа, впрыскиваемый газовым соплом, должен оставаться стабильным, иначе качество резки пострадает.
- Ненормальное давление газа. Ненормальное давление в системе подачи газа приведет к нестабильному потоку газа и повлияет на качество и скорость резки.
- Перечисленное выше — это лишь некоторые из распространенных неисправностей станков для лазерной резки CO2. Для операторов своевременное выявление и устранение неисправностей являются ключом к обеспечению стабильной работы оборудования и эффективности производства. Поэтому понимание возможных причин неисправности и соответствующих решений имеет решающее значение для поддержания нормальной работы станка для лазерной резки CO2.
Станки для лазерной резки CO2 часто сталкиваются с различными сбоями в процессе резки различных материалов. Эти неисправности могут привести к снижению качества резки, снижению эффективности производства и даже повлиять на срок службы и безопасность оборудования. Ниже будут описаны распространенные явления неисправностей и возможные причины машин для лазерной резки CO2:

Действия по устранению неполадок и общие решения
После выхода из строя станка для лазерной резки CO2 своевременное устранение неисправностей является залогом обеспечения нормальной работы оборудования. Чтобы как можно быстрее восстановить работу вашего устройства, выполните следующие действия и решения по устранению неполадок:
Подтвердите явление отказа и его влияние
- Наблюдайте за явлением неисправности: подробно рассмотрите конкретное явление неисправности, например, снижение качества резки, нестабильную скорость и т. д.
- Оценить степень влияния: Определить степень влияния неисправности на эффективность производства и качество продукции, чтобы сформулировать соответствующие планы реагирования.
Проверить рабочее состояние оборудования
- Проверьте систему электропитания и подачи газа: Убедитесь, что электропитание устройства стабильно и подача газа в норме.
- Проверьте механические компоненты: проверьте, нет ли каких-либо неисправностей в механических компонентах, таких как режущие головки, направляющие и системы трансмиссии.
Проверить оптику
- Проверьте оптическую линзу: Очистите поверхность оптической линзы, чтобы убедиться, что она не загрязнена и не изношена.
- Проверьте отражатель: проверьте, не поврежден ли отражатель и не загрязнен ли он, чтобы обеспечить качество передачи лазерного луча.
Отрегулируйте параметры резки
- Отрегулируйте скорость и мощность резки: в зависимости от различных характеристик и толщины материала отрегулируйте скорость резки и параметры мощности, чтобы оптимизировать эффект резки.
- Отрегулируйте фокус: убедитесь, что фокус лазерного луча отрегулирован правильно, чтобы обеспечить качество и скорость резки.
Проверьте систему управления
- Проверьте управляющее программное обеспечение: убедитесь, что управляющее программное обеспечение настроено правильно и в программе резки нет ошибок.
- Проверьте соединение цепи: проверьте, хорошее ли соединение цепи системы управления, чтобы избежать сбоев, вызванных проблемами с подключением.
Замените поврежденные детали
- Замените изношенные детали: такие как детали режущей головки, оптические линзы и т. д., чтобы обеспечить нормальную работу оборудования.
- Замените поврежденные электронные компоненты: такие как модули питания, контроллеры и т. д., чтобы убедиться в правильной работе электрической системы оборудования.
Выполнять тестирование и отладку
- Проведите испытание на холостом ходу: перед фактической резкой проведите испытание на холостом ходу, чтобы проверить, все ли функции оборудования в норме.
- Отладка параметров резки: в соответствии с результатами испытаний отрегулируйте параметры резки, чтобы оптимизировать эффект резки.
Запись и обратная связь
- Запишите информацию о неисправности: запишите подробную информацию о неисправности, действиях по устранению неполадок и решениях для дальнейшего использования.
- Обратная связь с соответствующими отделами: верните информацию о неисправностях в отдел технического обслуживания оборудования или производителю для дальнейшего отслеживания и решения потенциальных проблем.
С помощью вышеуказанных шагов и решений по устранению неполадок можно быстро и эффективно устранить неисправности станка для лазерной резки CO2, а также обеспечить нормальную работу и производственную эффективность оборудования. В то же время регулярное техническое обслуживание и обучение операторов также являются важными мерами предотвращения сбоев.

Профилактические меры и рекомендации по техническому обслуживанию
Профилактические меры и рекомендации по техническому обслуживанию необходимы для обеспечения бесперебойной работы станка для лазерной резки CO2 и продления срока службы оборудования. Вот некоторые общие меры предосторожности и рекомендации по техническому обслуживанию:
Регулярная чистка и уход
- Очистите оптические компоненты. Регулярно очищайте оптические линзы и отражатели, чтобы пыль, масло или грязь не влияли на качество передачи лазерного луча.
- Очистите рабочую зону: поддерживайте рабочую зону в чистоте, чтобы предотвратить попадание пыли, посторонних предметов и т. д. в оборудование и повлиять на качество резки и срок службы оборудования.
- Смазывайте механические компоненты. Регулярно смазывайте и обслуживайте механические компоненты, такие как режущие головки, направляющие и системы трансмиссии, чтобы уменьшить трение и износ.
Регулярная проверка и калибровка
- Проверьте систему электропитания и газоснабжения: Регулярно проверяйте систему электропитания и газоснабжения, чтобы обеспечить стабильную подачу электроэнергии и газа.
- Калибровка параметров резки. Регулярно проверяйте и калибруйте параметры резки, такие как скорость резки, мощность, фокусное расстояние и т. д., чтобы обеспечить качество и эффективность резки.
- Проверка системы управления: регулярно проверяйте программное и аппаратное обеспечение системы управления, чтобы обеспечить нормальную работу, а также своевременно выявлять и решать потенциальные проблемы.
Обучение операторов
- Обеспечьте обучение: обеспечьте профессиональную подготовку операторов, включая эксплуатацию оборудования, техническое обслуживание, безопасную эксплуатацию и т. д., чтобы улучшить их уровень квалификации и эксплуатационные характеристики.
- Установите рабочие процедуры: установите стандартизированные рабочие процедуры и стандартные рабочие процедуры, чтобы гарантировать, что операторы управляют оборудованием правильно в соответствии с процедурами, и уменьшить количество сбоев, вызванных человеческим фактором.
Обратите внимание на безопасную эксплуатацию
- Соблюдайте правила техники безопасности: строго соблюдайте правила эксплуатации оборудования, чтобы обеспечить безопасность операторов и оборудования.
- Носите защитное оборудование. Операторы должны носить соответствующие защитные средства, такие как очки, перчатки и т. д., чтобы снизить вероятность случайных травм.
Обновления и улучшения оборудования
- Своевременное обновление оборудования: в соответствии с фактическими производственными потребностями и технологическим развитием, своевременное обновление оборудования для повышения эффективности производства и качества резки.
- Рассмотрите варианты модернизации. Рассмотрите варианты модернизации оборудования, такие как добавление функций автоматизации, повышение точности резки и т. д., чтобы соответствовать меняющимся требованиям рынка.
Благодаря вышеуказанным профилактическим мерам и предложениям по техническому обслуживанию можно эффективно снизить частоту отказов станков для лазерной резки CO2 и гарантировать нормальную работу и производственную эффективность оборудования.
Подведем итог
Подводя итог, можно сказать, что общие проблемы устранения неполадок и решения для станков лазерной резки CO2 затрагивают различные аспекты, и необходимо всесторонне учитывать механические, оптоэлектронные, электрические и другие факторы оборудования. Только создав полный механизм и команду устранения неполадок, а также укрепив спецификации по техническому обслуживанию и эксплуатации оборудования, мы сможем обеспечить нормальную работу и эффективность производства. Станок для лазерной резки CO2 и удовлетворить меняющиеся производственные потребности. Мы надеемся, что руководство по устранению неполадок, представленное в этой статье, поможет пользователям, когда они сталкиваются с сбоями в реальном производстве, чтобы оборудование всегда поддерживало свое наилучшее состояние и обеспечивало стабильную и надежную поддержку производства.
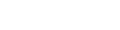
Контактная информация
- Электронная почта: [email protected]
- Скайп:[email protected]
- Вичат: +86-19963414011
Адрес для отправки контрольных материалов
- Зона № 3 А, промышленная зона Лунчжэнь, город Юйчэн, провинция Шаньдун.
Связанный блог