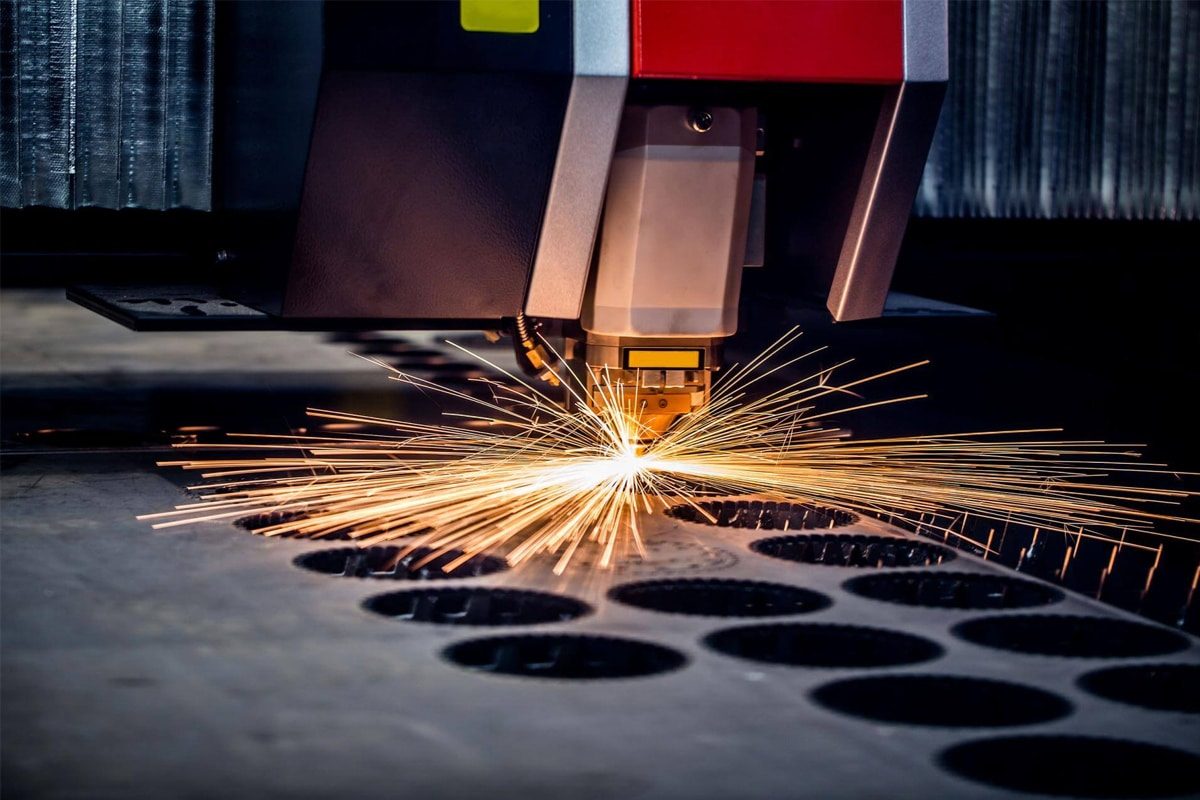
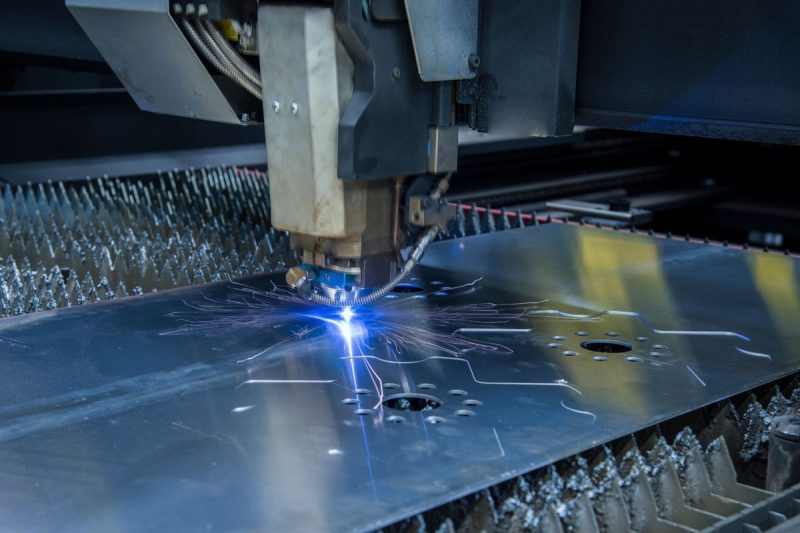
Factors Affecting the Service Life
Quality of Components
Laser Source
The laser source is the heart of the cutting machine, providing the beam used for material processing. Factors affecting its longevity include:
- Type of Laser: Fiber lasers typically outlast CO2 lasers due to their robust construction and fewer consumable parts.
- Power Stability: Fluctuating power levels can degrade the laser source, reducing efficiency and output quality.
- Cooling Requirements: Overheating is a major risk for laser sources. An efficient cooling system can effectively extend its service life.
Optical Components
Optics, including lenses and mirrors, direct and focus the laser beam. Their lifespan depends on:
- Material Quality: Optics made of high-quality materials, such as zinc selenide for CO2 lasers, last longer.
- Protective Coatings: Anti-reflective and protective coatings minimize damage from intense laser beams and contaminants.
- Cleaning Practices: Regular cleaning with appropriate tools prevents the buildup of dirt and residues, which can cause overheating and distortion.
Mechanical Components
Mechanical parts endure constant wear and tear due to motion and material handling. Key components include:
- Linear Guides and Ball Screws: Precision components ensure smooth and accurate movement. Regular lubrication reduces wear.
- Motors: High-quality servo or stepper motors improve durability and minimize vibrations.
- Chassis and Frame: A rigid and stable structure reduces vibrations, protecting both the machine and the quality of the cut.
Operating Environment
Temperature
- Optimal Range: Most laser cutting machines operate best within 15℃ to 35℃ (59℉ to 95℉). Extreme temperatures can cause thermal stress, leading to premature failure of electronic and mechanical parts.
- Impact of Overheating: Prolonged exposure to high temperatures can damage the laser source, optics, and control systems.
Humidity
- Condensation Risk: High humidity can lead to condensation on electronic and optical components, causing corrosion or short circuits.
- Dehumidifiers: In regions with high humidity, dehumidifiers are essential to maintain a safe environment.
Dust and Contaminants
- Generated Dust: Cutting operations often generate dust and fumes, which can settle on optics, filters, and moving parts.
- Extraction Systems: Installing effective dust and fume extraction systems prevents contamination and extends component life.
Vibration and Shock
- External Vibrations: Nearby machinery or unstable installations can transmit vibrations, misaligning critical components.
- Damping Solutions: Using vibration-isolating mounts or installing the machine on a stable foundation minimizes external shocks.
Maintenance Practices
Regular Cleaning
- Optics: Clean lenses and mirrors to prevent buildup that can distort the laser beam.
- Machine Surfaces: Wipe down external surfaces and ensure moving parts are free of debris.
- Filters: Clean air filters to maintain effective cooling and airflow.
Lubrication
- Lubrication Points: Bearings, linear guides, and ball screws require regular lubrication to reduce friction.
- Lubricant Quality: Using the manufacturer-recommended lubricant ensures compatibility and effectiveness.
Calibration
- Beam Alignment: Misaligned beams can damage internal components and reduce cutting precision.
- Focus Adjustment: Regularly calibrating the focus ensures consistent cutting quality.
Scheduled Maintenance
- Inspection Schedules: Periodically inspect key components for wear and tear.
- Consumables Replacement: Replace worn nozzles, filters, and protective windows to prevent cascading failures.
Usage Patterns
Operating Hours
- Continuous Operation: Excessive use without breaks causes overheating and increased wear. Adhering to the recommended duty cycle is essential.
- Cooling Breaks: Allowing time for the machine to cool down between operations prevents thermal stress.
Load and Stress
- Overloading: Running the machine at maximum capacity for extended periods can damage components. Moderating load reduces mechanical stress.
- Optimal Speed and Power: Using excessive speed or power settings unnecessarily strain the machine.
Material Types and Thickness
- Thick Materials: Cutting thick or dense materials requires more power, increasing stress on the laser source and optics.
- Reflective Materials: Materials like aluminum or brass reflect the laser beam, potentially damaging internal components. Using anti-reflective optics mitigates this risk.
Cutting Parameters
- Incorrect Settings: Poorly adjusted speed, power, or gas pressure can lead to uneven cuts and increased wear.
- Parameter Optimization: Tailoring parameters for specific materials ensures efficient operation and minimizes stress.
Electrical Supply
Voltage Stability
- Fluctuations: Voltage spikes or drops can damage electronic components. Voltage stabilizers protect against these issues.
- UPS Systems: Uninterruptible power supplies (UPS) prevent outages and safeguard the system during power fluctuations.
Power Quality
- Interference: Electrical noise can disrupt machine operation. Filters and surge protectors improve power quality.
Cooling System
Water Quality
- Impurities: Contaminated water can corrode cooling channels and reduce efficiency. Use distilled or deionized water as recommended.
- Regular Replacement: Changing the coolant at regular intervals prevents sediment buildup.
Temperature Control
- Optimal Range: Maintaining the coolant temperature within the specified range prevents thermal stress.
- Chiller Maintenance: Ensure chillers and cooling pumps are functioning correctly for consistent cooling performance.
Software and Control System
Updates and Upgrades
- System Updates: Regular updates fix bugs, improve performance, and enhance compatibility with new materials.
- Hardware Compatibility: Ensure updates align with the machine’s hardware to avoid malfunctions.
User Training
- Proper Usage: Operators must understand machine capabilities and limitations to avoid misuse.
- Error Prevention: Training minimizes errors that can cause unnecessary strain on components.
Installation and Setup
Proper Installation
- Stable Foundation: Installing the machine on a vibration-free surface prevents misalignment and wear.
- Environmental Considerations: Ensure proper ventilation and protection from dust and contaminants.
Alignment
- Initial Setup: Accurate alignment of the laser beam, optics, and motion systems ensures optimal cutting quality.
- Periodic Adjustments: Regular realignment compensates for wear and maintains precision.

Extending the Service Life
Best Practices for Maintenance
Regular and thorough maintenance is the cornerstone of extending the lifespan of laser-cutting machines. Establishing a consistent maintenance routine helps prevent minor issues from escalating into major problems.
- Daily Cleaning: Remove dust, debris, and residue from the machine’s optics, cutting head, and filters to prevent contamination and ensure precision.
- Lubrication of Moving Parts: Apply manufacturer-recommended lubricants to linear guides, ball screws, and other mechanical components at regular intervals to reduce friction and wear.
- Optics Maintenance: Clean lenses and mirrors using appropriate materials and solvents to maintain laser beam quality. Replace them if scratches or residues impair performance.
- Cooling System Checks: Inspect coolant levels, flow rates, and temperature control systems to prevent overheating of the laser source and electronics.
- Gas Supply Management: Ensure assist gas filters are clean and gas lines are free of leaks to maintain consistent cutting performance.
Training for Operators
Well-trained operators play a pivotal role in preserving the health of laser-cutting machines. Proper training minimizes operational errors and ensures the machine is used within its designed parameters.
- Understanding Machine Limits: Operators should be aware of the machine’s maximum cutting speed, power capacity, and material compatibility to avoid overloading.
- Error Recognition: Train operators to identify warning signs, such as unusual noises, inconsistent cuts, or error messages, and take immediate corrective action.
- Software Proficiency: Familiarity with the machine’s control system and software ensures efficient operation and reduces the risk of programming errors.
- Safety Protocols: Teach operators to follow safety measures, such as using protective gear, maintaining a clean workspace, and adhering to startup and shutdown procedures.
Use of High-Quality Consumables
Using high-quality consumables enhances machine performance and prevents unnecessary wear and tear on critical components.
- Nozzles and Lenses: Choose consumables made from durable materials with precise manufacturing standards to maintain consistent cutting quality.
- Protective Windows: Replace protective covers over lenses and mirrors when they show signs of wear or contamination to safeguard internal optics.
- Assist Gas: Use clean, high-purity gases to ensure optimal cutting conditions and prevent residue buildup on components.
- Coolant: Ensure the coolant is of the recommended quality and change it at the specified intervals to avoid corrosion and blockages in the cooling system.
Environmental Controls
Creating a controlled operating environment significantly impacts the service life of laser-cutting machines. Adverse environmental conditions can lead to premature wear, misalignment, and electrical failures.
- Temperature and Humidity: Maintain an ambient temperature within the manufacturer’s specified range (typically 15℃ to 35℃) and control humidity levels to prevent condensation on sensitive components.
- Dust and Fume Extraction: Install effective dust and fume extraction systems to keep the workspace clean and reduce contamination of optics, filters, and mechanical parts.
- Vibration Mitigation: Place the machine on a stable foundation to minimize the effects of external vibrations and shocks, which can misalign components.
- Clean Workspace: Keep the surrounding area free from debris and clutter to prevent accidents and ensure smooth material handling.
Scheduled Inspections
Routine inspections are essential for identifying potential issues before they lead to costly downtime or component failure. A structured inspection schedule ensures the machine operates at peak performance.
- Visual Inspections: Check for visible signs of wear, such as frayed cables, loose screws, or rust on metal components.
- Performance Tests: Periodically test the machine’s cutting accuracy and speed to identify calibration needs or potential alignment issues.
- Component Checks: Inspect critical components such as the laser source, optics, motion system, and cooling system for wear or degradation.
- Consumables Review: Evaluate the condition of consumables like nozzles, lenses, and filters, replacing them as necessary.
- Service Logs: Maintain detailed records of inspections, repairs, and parts replacements to track trends and anticipate future maintenance needs.
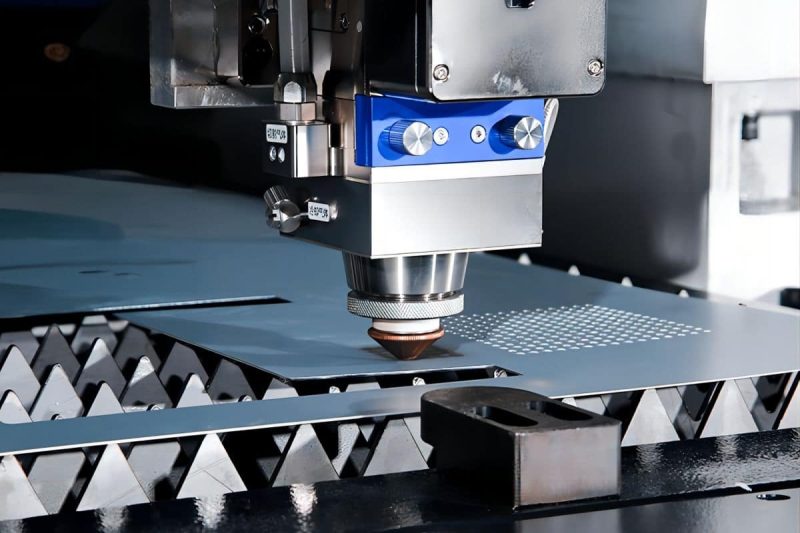
Common Mistakes That Shorten the Service Life
Ignoring Maintenance Schedules
Regular maintenance is critical for the proper functioning of any laser-cutting machine. Neglecting scheduled maintenance can have severe consequences:
- Dust and Debris Accumulation: Allowing dust, residue, or contaminants to build up on optics, filters, and mechanical components can lead to overheating, misalignment, and reduced cutting precision.
- Unlubricated Parts: Failure to lubricate moving parts, such as linear guides and ball screws, increases friction, resulting in accelerated wear and potential damage to the motion system.
- Worn-Out Consumables: Neglecting to replace consumables like nozzles, lenses, and protective covers on time can compromise cutting quality and strain other components.
- Cooling System Neglect: Ignoring coolant quality or flow issues can lead to overheating of the laser source and other critical components.
- Establish a strict maintenance schedule and adhere to the manufacturer’s recommendations to address these issues before they escalate.
Using Low-Quality Materials
The materials used in the cutting process significantly impact the machine’s performance and longevity. Low-quality materials can have the following adverse effects:
- Contaminated Materials: Impurities such as oil, dirt, or rust on materials can produce excessive fumes and residues, contaminating optics and filters.
- Poor Material Compatibility: Attempting to cut materials that are not suited for the machine (e.g., overly reflective metals without anti-reflective optics) can damage internal components.
- Inconsistent Thickness: Low-grade materials with uneven thickness may result in improper cutting parameters, increasing strain on the laser source and cutting head.
- Use high-quality, clean materials that are compatible with the machine’s capabilities, and ensure they are free of contaminants before processing.
Overloading the Machine
Pushing the machine beyond its intended capabilities is a common mistake that can lead to severe wear and damage over time.
- Exceeding Duty Cycle: Running the machine continuously without adequate cooling periods can overheat components, reducing their efficiency and service life.
- Maximum Power and Speed Settings: Consistently using maximum power and speed settings can strain the laser source, optics, and motion systems.
- Excessive Material Thickness: Cutting materials beyond the machine’s recommended thickness limit can result in poor-quality cuts and stress on the laser source.
- Operate the machine within its specified capacity and adhere to the recommended duty cycle to prevent unnecessary stress.
Poor Handling and Operation
Improper handling and lack of operator expertise can significantly impact the machine’s longevity.
- Incorrect Parameter Settings: Using inappropriate settings for laser power, cutting speed, or assist gas pressure can lead to poor-quality cuts and excessive wear on components.
- Improper Material Loading: Mishandling materials during loading can cause misalignment, damage to the worktable, or collisions with the laser head.
- Neglecting Safety Features: Disabling safety interlocks or ignoring system warnings can result in accidents and damage to the machine.
- Rough Operation: Abrupt starting, stopping, or handling of the machine can introduce unnecessary strain on moving parts and electronics.
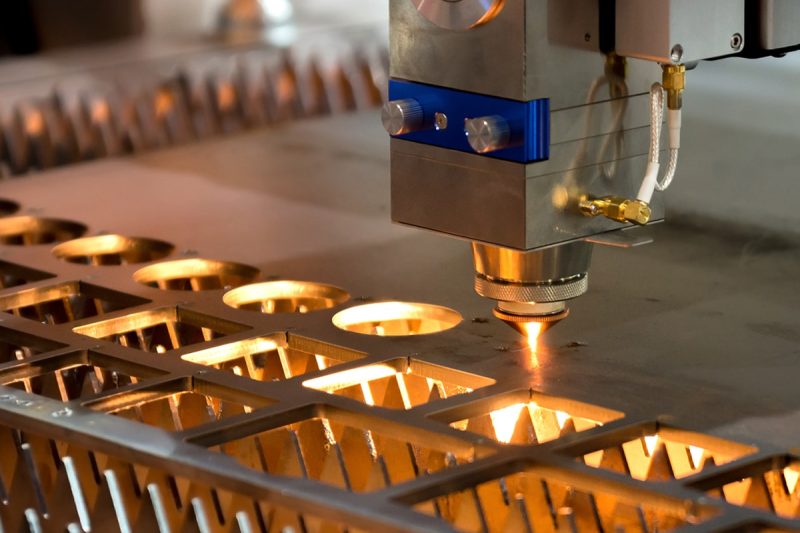
Importance of OEM Support
Access to Original Spare Parts
Using genuine spare parts from the OEM is essential for preserving the performance and integrity of laser-cutting machines.
- Compatibility and Quality: OEM spare parts are designed specifically for the machine, ensuring perfect fit and optimal performance. Using non-OEM parts may compromise functionality and cause further damage.
- Durability: Original parts are manufactured to the highest quality standards, which helps minimize wear and tear, reducing the frequency of replacements.
- Risk Mitigation: Inferior or incompatible parts can lead to mechanical failures, misalignments, or electrical issues. Relying on OEM parts mitigates these risks.
Technical Support
Comprehensive technical support from the OEM is a critical factor in troubleshooting issues and maintaining machine health.
- Expert Guidance: OEM technicians have in-depth knowledge of the machine’s design and functionality, enabling them to provide accurate diagnoses and solutions.
- Remote Assistance: Many OEMs, including AccTek Laser, offer remote support to address operational challenges, minimizing downtime.
- Training Resources: Access to training programs, user manuals, and instructional videos ensures operators are well-equipped to use the machine effectively.
- Preventive Maintenance Recommendations: OEMs provide detailed maintenance guidelines tailored to the machine, helping users proactively address potential issues.
Software Updates
Software is the backbone of a laser cutting machine’s control system, and keeping it updated is crucial for maintaining efficiency and extending service life.
- Enhanced Functionality: Software updates often include new features and tools that improve performance, reduce wear on components, and enhance cutting quality.
- Bug Fixes and Stability: Updates address software glitches and improve system stability, reducing the risk of errors during operation.
- Material Compatibility: As new materials and cutting techniques emerge, OEMs release software updates to optimize machine settings for these advancements.
- Security Improvements: Regular updates also address cybersecurity concerns, protecting the machine’s control system from potential threats.
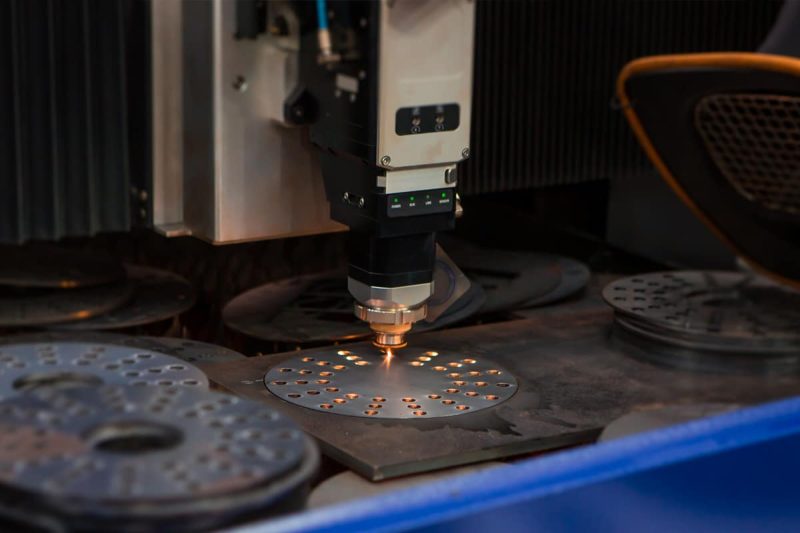
Summary
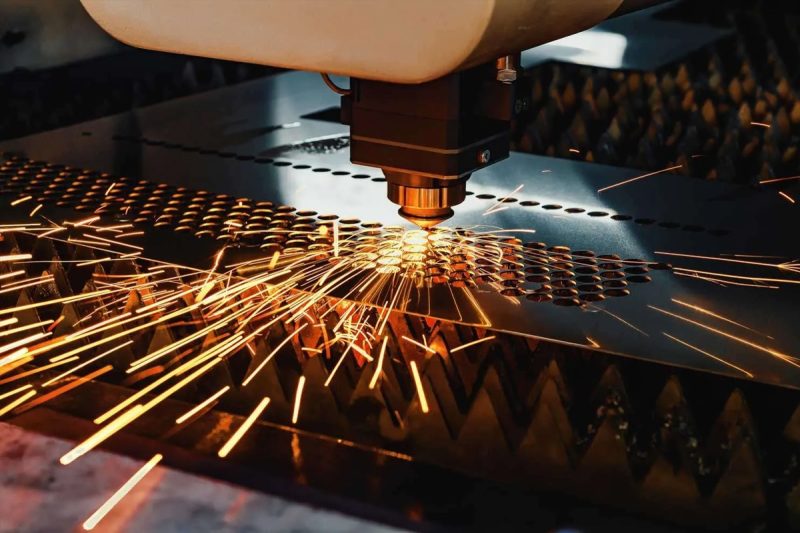
Get Laser Cutting Solutions
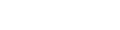
- [email protected]
- [email protected]
- +86-19963414011
- No. 3 Zone A, Lunzhen Industrial Zone,Yucheng City , Shandong Province.