3000W Laser Welding Machine
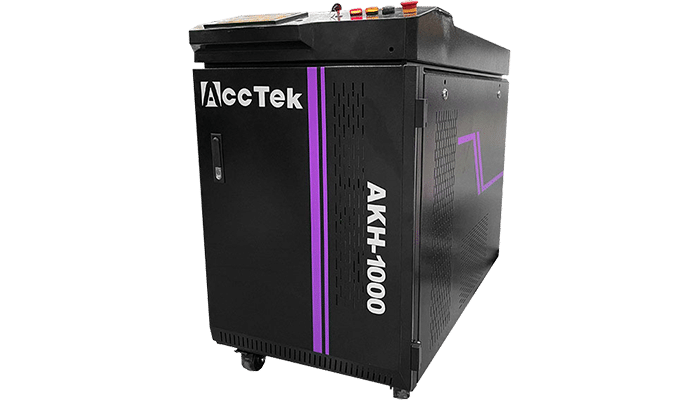
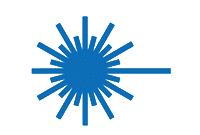
Photoelectric Technology
AccTek Laser focus on designing and manufacturing photoelectric-related system. We provide accurate and exquisite processing quality with leading R&D capability.
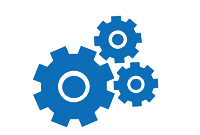
Integration Ability & Experienced
With an experienced, completed, and elite R&D team, customized such as automated, integrated with the robot, system integration, etc. are all available.
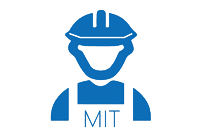
Professional Service
AccTek Laser's laser welding machine is a professional laser welding machine designed and manufactured in China. Our elite engineering team provides related service support.
Equipment Features
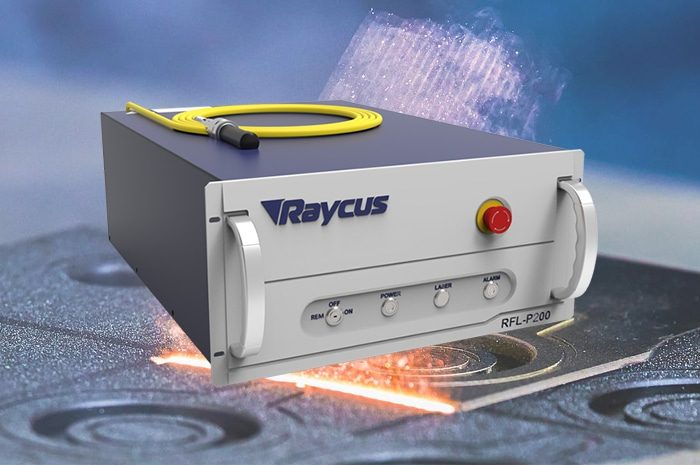
Famous Laser Generator
Using well-known brand laser generators (Raycus / JPT / Reci / Max / IPG), a high photoelectric conversion rate ensures the laser power and makes the welding effect better. AccTek can design different configurations to meet customer needs.
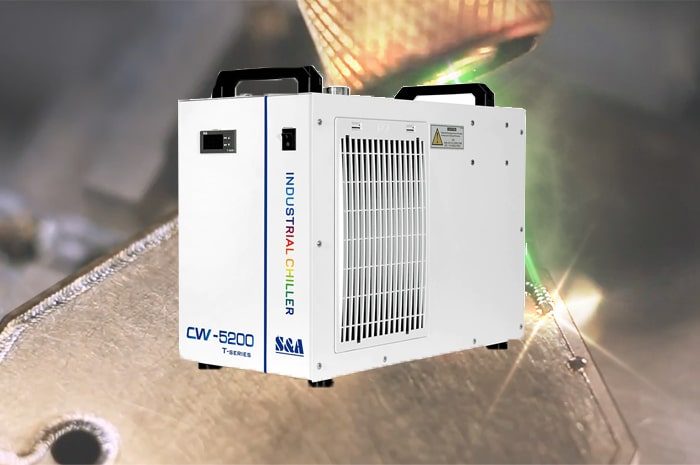
Industrial Water Chiller
The industrial water cooler ensures the heat dissipation of the core optical path components, allowing the welding machine to provide consistent welding quality and helping to improve the overall quality of the weld itself. It can also increase welding output by reducing the downtime of fiber laser welding machines. In addition, an excellent industrial water cooler can also prolong the service life of the laser welding machine.
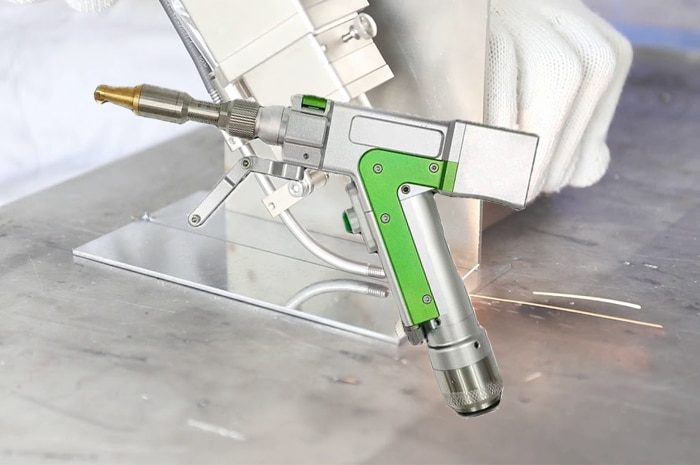
Laser Welding Gun
The laser welding gun is ergonomically designed, light in shape, comfortable to hold, and easy to control and operate. The hand-held welding gun is easy to hold and can be operated at any angle, making welding more convenient and flexible.
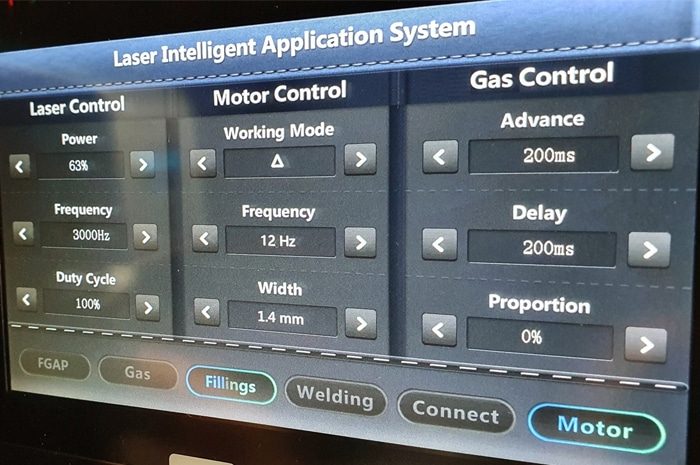
Interactive Touch Screen Control System
AccTek provides high-performance, intuitive, and easy-to-use operating systems. It expands the tolerance range and weld width of machined parts and provides better weld formation results. The operating system supports Chinese, English, Korean, Russian, Vietnamese, and other languages.
Technical Specifications
Model | AKH-1000 | AKH-1500 | AKH-2000 | AKH-3000 |
---|---|---|---|---|
Laser Power | 1000W | 1500W | 2000W | 3000W |
Laser Type | Fiber laser | |||
Range of Adjustable Power | 1-100% | |||
Laser Wavelength | 1064nm | |||
Way of Workinging | Continuous/Modulation | |||
Speed Range | 0-120mm/s | |||
Repeat Precision | ±0.01mm | |||
Welding Gap Requirements | ≤0.5mm | |||
Cooling Water | Industrial thermostatic water tank |
Laser Welding Capacity
Material Type | Welding Form | Thickness (mm) | Laser Power (W) | Welding Speed (mm/s) | Defocus Amount | Protective Gas | Blowing Method | Flow (L/min) | Welding Effect |
---|---|---|---|---|---|---|---|---|---|
Carbon Steel (Q235B) | Butt Welding | 0.5 | 3000 | 100~110 | -1~1 | Ar | Coaxial/Paraaxial | 5~10 | Welded Completely |
Butt Welding | 1 | 3000 | 90~100 | -1~1 | Ar | Coaxial/Paraaxial | 5~10 | Welded Completely | |
Butt Welding | 1.5 | 3000 | 70~80 | -1~1 | Ar | Coaxial/Paraaxial | 5~10 | Welded Completely | |
Butt Welding | 2 | 3000 | 60~70 | -1~1 | Ar | Coaxial/Paraaxial | 5~10 | Welded Completely | |
Butt Welding | 3 | 3000 | 50~60 | -1~1 | Ar | Coaxial/Paraaxial | 5~10 | Welded Completely | |
Butt Welding | 4 | 3000 | 40~50 | -1~1 | Ar | Coaxial/Paraaxial | 5~10 | Welded Completely | |
Butt Welding | 5 | 3000 | 30~40 | -1~1 | Ar | Coaxial/Paraaxial | 5~10 | Welded Completely | |
Butt Welding | 6 | 3000 | 20~30 | -1~1 | Ar | Coaxial/Paraaxial | 5~10 | Welded Completely | |
Stainless Steel (SUS304) | Butt Welding | 0.5 | 3000 | 110~120 | -1~1 | Ar | Coaxial/Paraaxial | 5~10 | Welded Completely |
Butt Welding | 1 | 3000 | 100~110 | -1~1 | Ar | Coaxial/Paraaxial | 5~10 | Welded Completely | |
Butt Welding | 1.5 | 3000 | 90~100 | -1~1 | Ar | Coaxial/Paraaxial | 5~10 | Welded Completely | |
Butt Welding | 2 | 3000 | 80~90 | -1~1 | Ar | Coaxial/Paraaxial | 5~10 | Welded Completely | |
Butt Welding | 3 | 3000 | 70~80 | -1~1 | Ar | Coaxial/Paraaxial | 5~10 | Welded Completely | |
Butt Welding | 4 | 3000 | 60~70 | -1~1 | Ar | Coaxial/Paraaxial | 5~10 | Welded Completely | |
Butt Welding | 5 | 3000 | 40~50 | -1~1 | Ar | Coaxial/Paraaxial | 5~10 | Welded Completely | |
Butt Welding | 6 | 3000 | 30~40 | -1~1 | Ar | Coaxial/Paraaxial | 5~10 | Welded Completely | |
Brass | Butt Welding | 0.5 | 3000 | 90~100 | -1~1 | Ar | Coaxial/Paraaxial | 5~10 | Welded Completely |
Butt Welding | 1 | 3000 | 80~90 | -1~1 | Ar | Coaxial/Paraaxial | 5~10 | Welded Completely | |
Butt Welding | 1.5 | 3000 | 70~80 | -1~1 | Ar | Coaxial/Paraaxial | 5~10 | Welded Completely | |
Butt Welding | 2 | 3000 | 60~70 | -1~1 | Ar | Coaxial/Paraaxial | 5~10 | Welded Completely | |
Butt Welding | 3 | 3000 | 50~60 | -1~1 | Ar | Coaxial/Paraaxial | 5~10 | Welded Completely | |
Butt Welding | 4 | 3000 | 30~40 | -1~1 | Ar | Coaxial/Paraaxial | 5~10 | Welded Completely | |
Butt Welding | 5 | 3000 | 20~30 | -1~1 | Ar | Coaxial/Paraaxial | 5~10 | Welded Completely | |
1-3 Series Aluminum Alloys | Butt Welding | 0.5 | 3000 | 100~110 | -1~1 | Ar | Coaxial/Paraaxial | 5~10 | Welded Completely |
Butt Welding | 1 | 3000 | 90~100 | -1~1 | Ar | Coaxial/Paraaxial | 5~10 | Welded Completely | |
Butt Welding | 1.5 | 3000 | 80~90 | -1~1 | Ar | Coaxial/Paraaxial | 5~10 | Welded Completely | |
Butt Welding | 2 | 3000 | 70~80 | -1~1 | Ar | Coaxial/Paraaxial | 5~10 | Welded Completely | |
Butt Welding | 3 | 3000 | 40~50 | -1~1 | Ar | Coaxial/Paraaxial | 5~10 | Welded Completely | |
Butt Welding | 4 | 3000 | 20~30 | -1~1 | Ar | Coaxial/Paraaxial | 5~10 | Welded Completely | |
4-7 Series Aluminum Alloys | Butt Welding | 0.5 | 3000 | 80~90 | -1~1 | Ar | Coaxial/Paraaxial | 5~10 | Welded Completely |
Butt Welding | 1 | 3000 | 70~80 | -1~1 | Ar | Coaxial/Paraaxial | 5~10 | Welded Completely | |
Butt Welding | 1.5 | 3000 | 60~70 | -1~1 | Ar | Coaxial/Paraaxial | 5~10 | Welded Completely | |
Butt Welding | 2 | 3000 | 40~50 | -1~1 | Ar | Coaxial/Paraaxial | 5~10 | Welded Completely | |
Butt Welding | 3 | 3000 | 30~40 | -1~1 | Ar | Coaxial/Paraaxial | 5~10 | Welded Completely | |
Copper | Butt Welding | 0.5 | 3000 | 60~70 | -1~1 | Ar | Coaxial/Paraaxial | 5~10 | Welded Completely |
Butt Welding | 1 | 3000 | 40~50 | -1~1 | Ar | Coaxial/Paraaxial | 5~10 | Welded Completely | |
Butt Welding | 1.5 | 3000 | 30~40 | -1~1 | Ar | Coaxial/Paraaxial | 5~10 | Welded Completely | |
Butt Welding | 2 | 3000 | 20~30 | -1~1 | Ar | Coaxial/Paraaxial | 5~10 | Welded Completely |
- In the welding data, the core diameter of the 3000W laser output fiber is 50 microns.
- This welding data adopts a Raytools welding head (swing welding head is used for copper welding), and the optical ratio is 100/200 (collimation/focus lens focal length).
- Welding shielding gas: Argon (purity 99.99%).
- Due to the differences in equipment configuration and welding process used by different customers, this data is for reference only.
Product Features
- The operation is simple and easy to learn, and the weld seam is not deformed.
- The laser output is stable, ensuring the consistency of the weld.
- High power density after laser focusing.
- The welding seam is smooth and beautiful, the welding workpiece will not be deformed, and the welding is firm without a subsequent grinding process, saving time and cost.
- 360-degree micro-welding without dead angle. After the laser beam is focused, a small spot can be obtained, which can be precisely positioned and used for the welding of small and small workpieces and can realize mass production.
- The welding speed is fast and the operation is simple, which is 2-10 times faster than the traditional welding speed.
- Long service life, providing a safer and more environmentally friendly welding method.
- High energy density, low heat input, small thermal deformation, narrow and deep melting zone, and heat-affected zone.
- The cooling speed is fast, the fine weld structure can be welded, and the joint performance is good.
- Compared with the contact welding method, laser welding saves electrodes, reduces daily maintenance costs, and greatly improves production efficiency.
- The welding seam is thin, the penetration depth is large, the taper is small, the precision is high, and the appearance is smooth and beautiful.
- No consumables, small size, flexible processing, low operation, and maintenance costs.
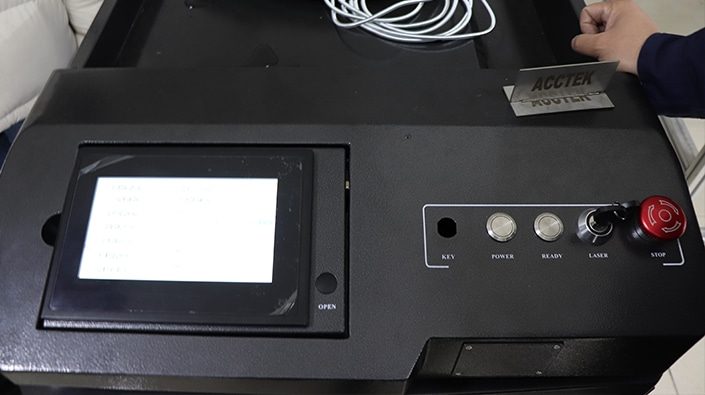
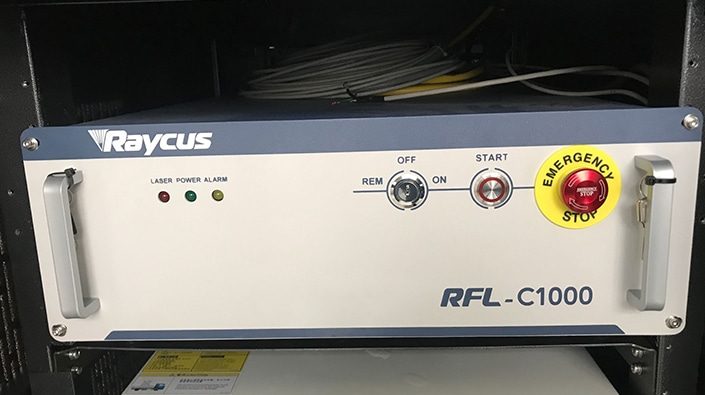
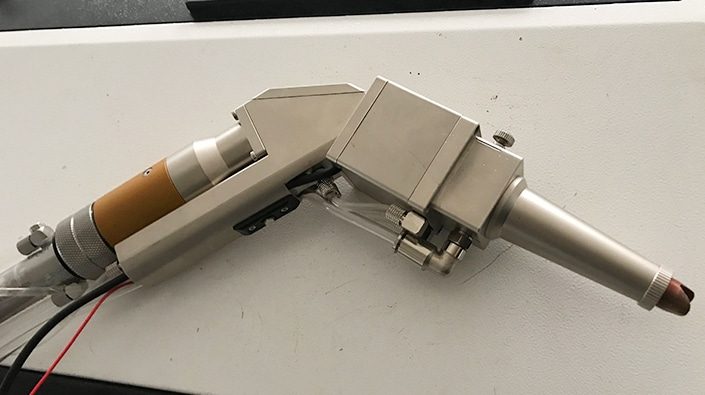
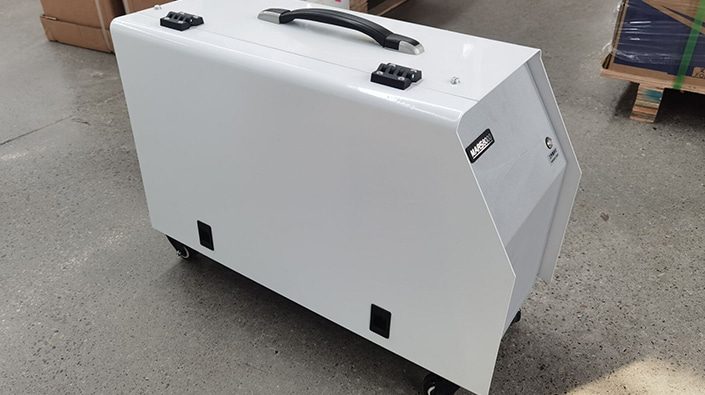
Product Application
Frequently Asked Questions
- Laser Optics: Laser optics, such as lenses and mirrors, degrade over time due to exposure to high-intensity laser beams. These parts may require periodic cleaning, calibration, or replacement to maintain optimum performance. The frequency and cost of replacing laser optics can vary depending on factors such as laser power, operating conditions, and maintenance time.
- Gas Consumption: Some laser welding processes require the use of shielding gases, such as argon or nitrogen, to protect the weld area from oxidation and improve weld quality. Ongoing costs should include purchasing or refilling cylinders.
- Cooling System Maintenance: Laser welding machines usually use a cooling system to dissipate the heat generated during operation. This may involve the use of coolant or the use of water circulation systems. Ongoing costs may include scheduled maintenance, coolant replenishment, and occasional repairs or replacements of cooling system components.
- Power Consumption: Using a 3000w laser welding machine requires a lot of power. Ongoing costs will include the electricity consumption associated with running the machine. It is recommended to consider energy-saving models and optimize the operation plan to minimize electricity costs.
- Electrical Components: Over time, electrical components within a laser welding machine may require maintenance or replacement. These components can include power supplies, control boards, sensors, and other related parts. The cost and frequency of replacing these components may vary depending on their reliability and condition of use.
- Laser Consumables: Depending on the welding process and application, additional consumable accessories such as filler wire or shielding gas may be required. The frequency of replacement or replenishment of these consumables will vary depending on usage and specific welding requirements.
- Brands And Manufacturers: Different brands and manufacturers offer laser welding machines that vary in quality, features, and reputation. Well-known brands often command higher prices because of their proven track record, advanced technology, and customer support.
- Machine Features And Capabilities: The features and capabilities of a laser welding machine can significantly affect its cost. Higher-end models may offer advanced features such as enhanced control systems, improved beam quality, faster processing speeds, larger work areas, or integrated automation, which may result in a higher price.
- Laser Generator: The brand of laser generator used in the machine will also affect the price. Different laser generator brands have different levels of efficiency, reliability, and maintenance requirements. In addition, factors such as laser power output and beam quality also affect the price.
- Build Quality And Durability: The build quality, materials used, and overall durability of a laser welding machine can affect its price. Machines built with high-quality components and durable materials may have a higher initial cost but may offer better performance, longevity, and reliability.
- Service And Support: The level of support and service provided by the manufacturer or distributor also affects the initial cost. Companies that offer comprehensive warranties, training programs, responsive customer support, and maintenance services may have higher initial costs due to the added value offered.
- Additional Equipment And Accessories: Additional equipment and accessories can also affect the overall price. This may include items such as cooling units, fume extraction systems, safety enclosures, workpiece fixtures, etc. These accessories are often critical to ensuring safe and efficient operation but may require additional investment.
- Control System And Software: The control system and software used in a laser welding machine also affect the initial cost of the machine. Advanced control systems with user-friendly interfaces, programming options, and monitoring capabilities can result in higher initial costs.
- Stainless Steel: Laser welding is often used for stainless steel applications due to its high precision and ability to produce clean and aesthetically pleasing welds. It is suitable for welding different grades of stainless steel such as austenitic, ferritic, and duplex stainless steel.
- Carbon Steel: Laser welding is also widely used in carbon steel applications, and can weld low-carbon steel, medium-carbon steel, and high-carbon steel. Laser welding allows for excellent control of heat input, resulting in precise and strong welds.
- Aluminum: Laser welding is ideal for welding aluminum and its alloys, including common grades such as 6061 and 7075. Due to aluminum’s high thermal conductivity, it can be challenging to weld using traditional welding methods, but laser welding allows precise control of heat input for successful aluminum welding.
- Copper: Laser welding can effectively weld copper and its alloys, such as brass and bronze. Copper is highly reflective of laser light, so laser welding of copper requires specific techniques and laser parameters to overcome these challenges.
- Titanium: Laser welding is commonly used to weld titanium and its alloys, known for their high strength-to-weight ratio and corrosion resistance. Welding titanium requires precise control of laser energy to avoid contamination and achieve strong, high-quality welds.
- Nickel-Based Alloys: Laser welding can be applied to weld a variety of nickel-based alloys, including Inconel, Monel, and Hastelloy. These alloys are often used in high-temperature and corrosive environments, and laser welding can provide precise and high-quality welds.
- Copper-Nickel Alloys: Laser welding can effectively join copper-nickel alloys. Copper-nickel alloys are often used in marine and offshore applications due to their excellent corrosion resistance in seawater.
- Precious Metals: Laser welding is also suitable for welding precious metals such as gold, silver, and platinum. The jewelry and dental industries often use laser welding machines for precise and intricate welding of these materials.
- Laser Beam Characteristics: The beam quality and focusing ability of a laser play an important role in determining the maximum material thickness. A high-quality laser beam with good focusing capabilities enables deeper penetration and better control of the welding process. A well-focused beam concentrates energy efficiently, allowing thicker materials to be welded.
- Material Type: Different materials have different thermal properties, reflectivity, and absorption of laser energy, which can affect the laser welding process. Some materials, such as carbon steel and stainless steel, have a higher absorption rate of laser energy, allowing greater thicknesses to be welded more efficiently. Conversely, materials with low absorption may require higher laser power or different welding techniques to achieve comparable results.
- Material Reflectivity: Emissive materials such as copper or highly polished surfaces tend to reflect most of the laser energy, reducing the energy available for welding, which limits the achievable weld thickness. In this case, additional measures may be required, such as the use of special coatings or welding parameters.
- Welding Speed: Welding speed also affects the maximum material thickness that can be effectively welded. Higher welding speeds may result in reduced weld penetration and poor weld quality in thicker materials. Adjusting welding parameters such as laser power and travel speed helps to optimize the welding process for different material thicknesses.
- Laser Welding Parameters: Specific welding parameters, such as laser power, welding speed, focus position, and beam diameter, need to be optimized for each material and thickness combination. Finding the right combination of parameters can achieve satisfactory welding results. Typically process development and parameter optimization are required to determine the maximum weld thickness for a given material.
- Weld Design And Preparation: The design and preparation of the weld affect the achievable weld thickness. Factors such as joint access, fit and joint configuration (e.g., butt joints, lap joints) affect the welding process and can impose limitations on the maximum material thickness that can be effectively welded.
- Beam Delivery System: The beam delivery system, including optics and delivery components, also affects welding performance. Proper beam shaping and alignment ensure optimum power density and focus at the soldering point. Efficient beam delivery enhances welding capabilities for thicker materials.
- Laser Safety Training: Laser safety training is usually a basic requirement for anyone operating a laser welding machine. It typically covers topics such as laser hazards, safety precautions, personal protective equipment (PPE), safe operating practices, and emergency procedures. This training ensures that operators are aware of the potential risks associated with laser radiation and know how to mitigate them.
- Machine-Specific Training: In addition to laser safety, operators should receive machine-specific training from the manufacturer or authorized training provider. This training typically includes machine operation, control system navigation, parameter setting, loading and unloading workpieces, and basic troubleshooting. It ensures that the operator is familiar with the features and functions of the machine and can use it safely and efficiently.
- Welding Techniques And Parameters: Laser welding requires knowledge of various welding techniques and parameters specific to the materials being welded. Understanding concepts such as laser power settings, focal length, weld speed, assist gas selection, and joint preparation can help achieve high-quality welds. A training program may cover these topics to ensure operators have the necessary skills to optimize the welding process.
- Certification Programs: In some cases, certain industries or applications may require specific certifications or qualifications. For example, the aerospace or automotive industries may have additional requirements to meet their quality standards or regulatory compliance. These certifications typically involve practical assessments to demonstrate proficiency in laser welding techniques and adherence to industry-specific guidelines.
- Material Specific Training: Depending on the material being welded, additional material-specific training may be required. This training can cover topics such as material properties, weldability considerations, pre-weld preparation, and post-weld handling requirements. It ensures operators understand the unique characteristics and challenges associated with welding specific materials.
- Power Supply: 3000w laser welding machine needs a dedicated power supply that can provide the necessary power output. The power requirements of the machine may vary depending on the specific model but generally run on three-phase power. Voltage and frequency specifications will depend on the design of the machine and the electrical codes in your area.
- Power Capacity: Laser welding machines consume a lot of power due to their high laser power output. You need to ensure that the power supply has sufficient capacity to support the power consumption of the machine and any other devices or accessories that may be connected. The electrical capacity in the facility needs to be assessed to ensure it can support the electrical needs of the machines.
- Electrical Wiring And Connections: Proper electrical wiring and connections help ensure the safe and reliable operation of the laser welding machine. Be sure to follow the manufacturer’s guidelines and electrical codes to ensure proper wiring, grounding, and electrical protection are in place.
- Power Supply Stability: Laser welding machines require a stable and reliable power supply to maintain consistent laser output and ensure reliable and precise welding results. Electrical fluctuations, voltage dips, or power surges can adversely affect the performance of the machine and cause inconsistent weld quality. The stability and quality of the power supply within the facility should be considered to ensure proper operation.